Lab_4
docx
keyboard_arrow_up
School
New Jersey Institute Of Technology *
*We aren’t endorsed by this school
Course
215
Subject
Mechanical Engineering
Date
Feb 20, 2024
Type
docx
Pages
33
Uploaded by GeneralOxideLeopard44
Department Of Mechanical And Industrial Engineering
Measurement And
Visualization Of Flow
By
Kisei Mano
Team 1
1.
Kisei Mano
2.
Clair Wagner
3.
Courage Lahban
4.
Elijah Smith
Date of Experiment: 6-7-2023 & 6-8-2023
Instructor: B. S. Mani
ME343-011, MECHANICAL LAB-1
Summer 2023
1
Table of Contents
Cover Page………………………………………………………………………………………………………………………… Page 1
Table of Contents………………………………………………………………………………………………………………. Page 2
Grading Citaria………………………………………………………………………………………………………………….. Page 3
Table of Tables…………………………………………………………………………………………………………………… Page 5
Table of Figures…………………………………………………………………………………………………………………. Page 5
Abstract…………………………………………………………………………………………………………………………….. Page 6
Introduction………………………………………………………………………………………………………………………. Page 7
Experimental systems……………………………………………………………………………………………………….. Page 8
o
Equipment……………………………………………………………………………………………………………. Page 8
o
Experimental description…………………………………………………………………………………... Page 12
Data and Result………………………………………………………………………………………………………………. Page 15
Discussion……..………………………………………………………………………………………………………………… Page 23
Conclusion………………………………………………………………………………………………………………………. Page 25
Bibliography……………………………………………………………………………………………………………………. Page 26
Appendix………………………………………………………………………………………………………………………… Page 27
Bonus Points…………………………………………………………………………………………………………………… Page 35
2
MEASUREMENT OF Flow Through Pipes
Grading Criteria for Lab Report 3
(Maximum Possible 50 points
)
1.
General Format
(
12.5 points
)
Cover page
Grading Criteria
Table of Contents
Abstract
Introduction
Theory (See details given at 2 below) (
12.5 points
)
Methodology
Experimental system (See details below given separately) (
12.5 points
)
Sample Analysis (See details given at 4 below AND include this section in appendix) (
12.5 points
)
Results and discussions (See details below given separately)
Conclusion
Nomenlecture
Appendices
Original data
Data conversion with sample analysis
2.
Theory (
12.5 points
)
Methods based on Bernoulli equations
Flow rate equation for venturi and orifice (with discharge coefficient)
Local velocity equation for Pitot’s tube (with inclined manometer)
3.
Experimental Systems (
12.5 points
)
Flow rate measurement system – Flow Stand
Schematic diagram of experimental system
Photograph of the system and its key components
Photograph of the system and its key components
3
Your preview ends here
Eager to read complete document? Join bartleby learn and gain access to the full version
- Access to all documents
- Unlimited textbook solutions
- 24/7 expert homework help
Schematic diagram of experimental system
Photograph of the system and its key components
4.
Sample Analysis (include this section in the appendix) (12.5 points)
Theoretical flow rate calculation (venturi & orifice)
Jet velocity calculation (Pitot tube)
5.
Results and Discussions
:
Calibration of flow rate
Calibration of rotameter (Plot flow rate vs float height)
Calibration of venturi, comparison against theory and determination of discharge coefficient
Calibration of orifice, comparison against theory and determination of discharge coefficient
Determination of jet boundary - Plot the three velocity profiles on the
same graph Normalize, and determine the jet entrapment in pitot’s tube experiment.
4
Table of Figures
Figure #
Description
Page #
1
Flow measurement Workbench
9
2
Digital Flow rate Annunciator
10
3
Venturi and Orifice Devices
10
4
Flow measurements – apparatus and components
10
5
Monometer
11
6
Rotameter
11
7
Control Valves
12
8
Compressed air inlet
12
9
Pitot Tube Jet Flow
12
10
Air Jet nozzle
13
11
Manometers
13
12
Pitot Tube Adjustment Apparatus
14
13
Work bench schematic
14
14
Pitot Tube Schematic
15
15
Graph of rotameter 17
16
Graph of Orifice
19
17
Graph for Venturi
19
18
Jet Flow Measurement (Pitot Tube)
21
19
Normalized Jet Flow measurements
22
Table of Tables
Table #
Page #
1
16
2
15
3
15
4
16
5
17
6
17
5
Abstract
The abstract of this lab was based on how the fluid streams. To understand how the flow behaves we used many kinds of devices like Venturi tube, orifice tube and a turbine. We obtained the measurements by reading the pressure difference when the fluid would come in and out of a specific device. Another method was the use of pitot tube to determine the pressure differences. Even though both methods were very similar, measuring the flow of two different materials; air and water, this experiment showed that both were behaving in similar ways. After we acquired the important data, we had a better understanding of how pressure reacts during a steady flow process and how they are measured.
6
Your preview ends here
Eager to read complete document? Join bartleby learn and gain access to the full version
- Access to all documents
- Unlimited textbook solutions
- 24/7 expert homework help
Introduction
The importance of experiments in the engineering society is to understand how the pressure and velocities of the liquid through
pipelines are measured. One of the ways is the use of Bernoulli’s equation a fundamental principle in fluid dynamics that relates the pressure, velocity, and height of a fluid in a streamline. This equation is mainly used in aerodynamics, hydrodynamics, plumbing, and the design of fluid flow systems. For this experiment
we used water for the liquid flowing through the two measuring devices. The first one is called the Flow Measurement Workbench, this is used for the calibration, testing, and evaluation of flow meters and flow measurement devices. Another is called the Pitot’s Tube Jet Nozzle; this uses a jet stream of air to measure fluid
flow velocity. Eventually after this experiment we were able to acquire the experimental measurement of the flow and velocity as well as the calculation of the theoretical values.
7
Theory and Methology
1. Flow Rate Equation
a) Venturi
With the equation: ρ
∗
A
A
v
A
=
ρ
∗
A
B
v
B
We were able to get:
Q
=
A
B
v
B
=
A
B
(
(
2
g
1
−
(
A
B
A
A
)
2
)
∗
(
P
A
−
P
B
pg
)
)
1
2
b) Orifice
Basically it’s similar to the venturi equation.
Q
=
A
F
v
F
=
C A
F
(
(
2
g
1
−
(
A
F
A
E
)
)
∗
(
P
E
−
P
F
pg
)
)
1
2
The discharge coefficient (C) is a dimensionless factor that accounts for the efficiency of the flow through a particular device or constriction. It takes into consideration various factors such as the shape, design, and condition of the flow element, as well as any flow disturbances or losses. The Discharge Coefficient, C, is
determined by the two-flow rate theoretical discharge rate: C
=
Q
actual
Q
ideal
.
Local velocity Equation for Pitot’s Tube:
V
=
√
2
(
P
1
−
P
2
)
ρ
air
8
This is true when taking the pressure difference in the pipeline.
Experimental systems
Equipment and Description:
Figure 1: Flow Measurement Workbench
Flow Measurement Workbench:
This workbench produces a specific flow rate that’s being passed through the tubes. We could control the flow of the water in the tubes using the control valve that is connected to layout pipes. By using the flow rate annunciator, we were able to digitally read how much flow rate could be passed through the pipes. The volume flow rate changes depending on the size of the piping. It is an essential tool in industries where accurate flow measurement is
crucial, such as oil and gas, chemical processing, water management, and manufacturing.
9
Your preview ends here
Eager to read complete document? Join bartleby learn and gain access to the full version
- Access to all documents
- Unlimited textbook solutions
- 24/7 expert homework help
Figure 2: Digital flow rate annunciator
Digital flow rate annunciator:
This device can display the amount of volume flow rate in L/sec and L/min.
Figure 3: Venturi & orifice devices
Figure 4: Flow measurements – apparatus and components
10
Monometer: This is a device used to measure pressure, typically in a fluid system of the workbench. This is connected to the Venturi and Orifice tube. The pressure at various points in the workbench can be read on the monometers. The manometer operates based on the principle of hydrostatic pressure, which reads on the manometer changes depending on volume flow rate at the given point.
Figure 5: Monometer
Figure 6: Rotamter
Rotameter:
This device is used to measure the height of how high the float rises from the initial height to the final height.
11
Figure 7: Control valves
Figure 8: Compressed air inlet (used for purging)
Figure 10: Pitot Tube Jet Flow 12
Your preview ends here
Eager to read complete document? Join bartleby learn and gain access to the full version
- Access to all documents
- Unlimited textbook solutions
- 24/7 expert homework help
Pitot Tube Jet Flow
: This is a device that is used to measure fluid flow velocity, particularly in applications involving gases or liquids. It works based on the principle of Bernoulli's equation, which relates fluid velocity to pressure changes. A fluid jet refers to a stream of fluid (liquid or gas) being discharged from a nozzle or an orifice at a high velocity. It is often used in applications such as water jets, hydraulic systems, propulsion systems, and aerodynamics.
Figure 9: Air jet nozzel
Figure 10: Manometers
13
Figure 12: Pitot Tube Adjustment Appartus
Equipment and Description:
Figure 13: Schematic of Workbench
As you can see in the diagram above, as the control valve ejects water it goes through the venturi and Orifice tube eventually leading through the rotameter. The tube is connected to the manometer.
14
Figure 14: schematic diagram of using thermistor.
As you can see in the diagram above as the Jet flow Nozzle releases air, some of them go into the apparatus though the pipe eventually leading to the manometer.
15
Your preview ends here
Eager to read complete document? Join bartleby learn and gain access to the full version
- Access to all documents
- Unlimited textbook solutions
- 24/7 expert homework help
Sample Analysis
Theoretical Flow Rate Calculation for Venturi:
Q
=
A
B
v
B
=
A
B
(
(
2
g
1
−
(
A
B
A
A
)
2
)
∗
(
P
A
−
P
B
pg
)
)
1
2
¿
(
530.9291585
)
∗
(
(
2
1
−
(
530.9291585
201.0619298
)
2
)
∗
(
242
−
250
0.000000997
)
)
1
2
¿
870274.6904
L
(
mm
)
3
Theoretical Flow Rate Calculation for Orifice:
Q
=
A
E
v
E
=
A
E
(
(
2
g
1
−
(
A
E
A
F
)
2
)
∗
(
P
E
−
P
F
pg
)
)
1
2
¿
(
530.9291585
)
∗
(
(
2
1
−
(
314.2
2115.6
)
2
)
∗
(
250
−
238
0.000000997
)
)
1
2
¿
1343027.9
L
(
mm
)
3
Results And Discussion
16
1.
Rotameter
Table 1: Rotameter Data
#
Flow Rate
(L/m)
Flow Rate
(L/S)
Height
(mm)
B
(mm)
C
(mm
)
D
(mm)
E
(mm
)
F
(mm)
H
(mm)
1
6.06
0.101
29
242
250
250
238
243
142
2
7.2
0.12
39
244
256
256
240
246
146
3
8.58
0.143
49
248
268
268
244
250
150
4
9.96
0.166
59
252
276
278
246
252
152
5
11.28
0.188
69
254
286
294
248
254
154
6
12.78
0.213
79
256
298
332
248
256
156
7
14.52
0.242
89
258
314
356
248
260
160
8
15.72
0.262
99
264
326
368
264
264
164
9
17.1
0.285
109
272
348
382
270
272
172
10
18.6
0.31
119
280
372
400
288
282
182
0.05
0.1
0.15
0.2
0.25
0.3
0.35
0
20
40
60
80
100
120
140
f(x) = 424.37 x − 12.15
R² = 1
Rotameter (experimental)
Flow Rate (L/s)
Height (mm)
Figure 13: Graph of Rotermeter Flow rate (L/s) vs Height (mm)
2.
Venturi and Orifice
17
d
1
=
16
mm
A
1
=
201.0619298
m m
2
d
2
=
26
mm
A
2
=
530.9291585
m m
2
Table 2: Thermocouple Data for Close Device
Rotameter
Venturi
Orifice
Flow
Rate
(L/S)
Height
(mm)
B: P1
(mm)
C: P2
(mm)
Flow rate
Q
thoretical
Flow rate
*10^-6
Coefficient
of discharge
©
E: P1
(mm)
F: P2
(mm)
Flow rate
(theoretical)
0.101
29
242
250
870274.6
904
0.0870
0.862
250
238
1343027.9
0.12
39
244
256
1065864.
464
0.1066
0.888
256
240
1598601.3
0.143
49
248
268
1376025.
106
0.1376
0.962
268
244
2121071.8
0.166
59
252
276
1507359.
98
0.1507
0.908
278
246
2311230.8
0.188
69
254
286
1740549.
381
0.1741
0.926
294
248
2825314.9
0.213
79
256
298
1994049.
822
0.1994
0.936
332
248
3860606.0
0.242
89
258
314
2302530.
403
0.2303
0.952
356
248
4448988.9
0.262
99
264
326
2422742.
204
0.2423
0.925
368
264
4243087.8
0.285
109
272
348
2682366.
744
0.2682
0.941
382
270
4481689.3
0.31
119
280
372
2951245.
063
0.2951
0.952
400
288
4533274.6
18
Your preview ends here
Eager to read complete document? Join bartleby learn and gain access to the full version
- Access to all documents
- Unlimited textbook solutions
- 24/7 expert homework help
0.05
0.1
0.15
0.2
0.25
0.3
0.35
0.0
500000.0
1000000.0
1500000.0
2000000.0
2500000.0
3000000.0
3500000.0
4000000.0
4500000.0
5000000.0
f(x) = 16786665.83 x − 209441.08
R² = 0.93
Orifice Orifice
Linear (Orifice)
Experimental Flow rate (L/m) Theoretical Flow rate (L/m) Figure 14: Graph of Orifice
4
6
8
10
12
14
16
18
20
0
500000
1000000
1500000
2000000
2500000
3000000
3500000
f(x) = 162704.66 x − 90441.95
R² = 1
Venturi
Flow Rate (L/m)
Linear (Flow Rate (L/m))
Experimental Flowvrate (L/m)
Theoretical Flow rate (L/m)
Figure 15: Graph for Venturi
19
3.
Jet Flow
Table 3 Jet Flow Measurement Data
Y = 50
X(mm)
P1(mm
)
P2
(mm)
Delta
P
V:Y50
V_Norm:
Y50
0.0
135.0
275.0
140.0
15.5
1
5.0
136.0
276.0
140.0
15.5
1
10.0
137.0
277.0
140.0
15.5
1
15.0
138.0
278.0
140.0
15.5
1
20.0
141.0
276.0
135.0
15.2
0.977781629
25.0
182.0
274.0
92.0
12.6
0.76651989
30.0
264.0
269.0
5.0
2.9
0
Y = 200
X
P1(mm
)
P2
(mm)
Delta
P
V:Y200
V_NORM:
Y200
0.0
140.0
275.0
135.0
15.0
1.0
5.0
140.0
276.0
136.0
15.1
1.0
10.0
145.0
275.0
130.0
14.7
1.0
15.0
155.0
275.0
120.0
14.1
0.9
20.0
180.0
273.0
93.0
12.4
0.8
25.0
205.0
271.0
66.0
10.5
0.7
30.0
233.0
270.0
37.0
7.9
0.5
35.0
250.0
269.0
19.0
5.6
0.3
40.0
259.0
268.0
9.0
3.9
0.2
45.0
265.0
267.0
2.0
1.8
0.0
20
Y = 350
X
P1(mm)
P2 (mm)
Delta P
V:Y350
0.0
160.0
275.0
115.0
13.8
5.0
170.0
275.0
105.0
13.2
10.0
180.0
275.0
95.0
12.6
15.0
195.0
273.0
78.0
11.4
20.0
210.0
270.0
60.0
10.0
25.0
220.0
270.0
50.0
9.1
30.0
235.0
269.0
34.0
7.5
35.0
240.0
269.0
29.0
7.0
40.0
250.0
268.0
18.0
5.5
45.0
255.0
268.0
13.0
4.7
50.0
260.0
266.0
6.0
3.2
55.0
265.0
267.0
2.0
1.8
-80.0
-60.0
-40.0
-20.0
0.0
20.0
40.0
60.0
80.0
0.0
2.0
4.0
6.0
8.0
10.0
12.0
14.0
16.0
Jet flow Measurment (Pitot tube)
V_Norm: Y50
Polynomial (V_Norm: Y50)
V_NORM: Y200
Polynomial (V_NORM: Y200)
V_NORM:Y350
Polynomial (V_NORM:Y350)
Distanbce from Center of Jet Flow (mm)
Velocity of Air(mm/s)
Figure 16: Thermistor Temperature vs Resistance
Table 4 – Normalized Jet Flow Measurement Data
Normalized
Distance
Normalized 50
mm jet flow
Normalized
Distance
Normalized 200
mm jet flow
Normalized
Distance
Normalized 350
mm jet flow
-0.54545
0
-0.81818
0
-1
0
-0.45455
0.76651989
-0.72727
0.154745743
-0.90909
0.117208987
-0.36364
0.977781629
-0.63636
0.287351131
-0.81818
0.235384942
-0.27273
1
-0.54545
0.455570852
-0.72727
0.3038186
-0.18182
1
-0.45455
0.654764605
-0.63636
0.42654408
-0.09091
1.0
-0.36364
0.803052885
-0.54545
0.474428789
21
Your preview ends here
Eager to read complete document? Join bartleby learn and gain access to the full version
- Access to all documents
- Unlimited textbook solutions
- 24/7 expert homework help
0
1
-0.27273
0.930964674
-0.45455
0.6076372
0.090909
1
-0.18182
0.974613837
-0.36364
0.680132203
0.181818
1
-0.09091
1
-0.27273
0.796763974
0.272727
1
0
0.995808446
-0.18182
0.895053298
0.363636
0.977781629
0.090909
1
-0.09091
0.948778148
0.454545
0.76651989
0.181818
0.974613837
0
1
0.545455
0
0.272727
0.930964674
0.09091
0.948778148
0.363636
0.803052885
0.18182
0.895053298
0.454545
0.654764605
0.27273
0.796763974
0.545455
0.455570852
0.36364
0.680132203
0.636364
0.287351131
0.45455
0.6076372
0.727273
0.154745743
0.54545
0.474428789
0.818182
0
0.63636
0.42654408
0.72727
0.3038186
0.81818
0.235384942
-1.5
-1
-0.5
0
0.5
1
1.5
0
0.2
0.4
0.6
0.8
1
1.2
Normalized Jet Flow Measurments
Y = 50
Polynomial (Y = 50)
Y = 200
Polynomial (Y = 200)
Y = 350
Polynomial (Y = 350)
Normalized Distance from Center of Jet Flow (x/x_max)
Normalized velocity of Air (U/U_max)
Figure 19: normalized Jet Flow Measurement
Conclusion
In conclusion, we were able to understand how to measure the flow in different types of pipelines. Also, this experiment taught
us how to use the pitot tube, jet nozzle, manometers, rotameters, 22
Your preview ends here
Eager to read complete document? Join bartleby learn and gain access to the full version
- Access to all documents
- Unlimited textbook solutions
- 24/7 expert homework help
various tubing, and other tools. By using Bernoulli’s equation, we were able to calculate the velocity of the flow rate from the Pitot tube and workbench. Eventually with that data we were able to obtain a graph with the use of Excel. In the end we understand that frequencies change and there is a low chance of obtaining the
perfect frequency. Bibliography
Holman, J. Experimental Methods for Engineers 8
th
edition
. Mc Graw Hill. Zhu, C. (2009). Me 343 Laboratory Introduction
.
23
Your preview ends here
Eager to read complete document? Join bartleby learn and gain access to the full version
- Access to all documents
- Unlimited textbook solutions
- 24/7 expert homework help
Appendix
Detailed Sample Calculation
:
24
Your preview ends here
Eager to read complete document? Join bartleby learn and gain access to the full version
- Access to all documents
- Unlimited textbook solutions
- 24/7 expert homework help
Theoretical Flow Rate Calculation for Venturi:
Q
=
A
B
v
B
=
A
B
(
(
2
g
1
−
(
A
B
A
A
)
2
)
∗
(
P
A
−
P
B
pg
)
)
1
2
¿
(
530.9291585
)
∗
(
(
2
1
−
(
530.9291585
201.0619298
)
2
)
∗
(
242
−
250
0.000000997
)
)
1
2
¿
870274.6904
L
(
mm
)
3
Theoretical Flow Rate Calculation Venturi: C
=
0.087027469
0.101
=
0.861658109
Theoretical Flow Rate Calculation for Orifice:
Q
=
A
E
v
E
=
A
E
(
(
2
g
1
−
(
A
E
A
F
)
2
)
∗
(
P
E
−
P
F
pg
)
)
1
2
¿
(
530.9291585
)
∗
(
(
2
1
−
(
314.2
2115.6
)
2
)
∗
(
250
−
238
0.000000997
)
)
1
2
¿
1343027.9
L
(
mm
)
3
Theoretical Flow Rate Calculation Orifice: C
=
0.087027469
0.101
=
0.861658109
Jet Velocity Calculation:
√
2
(
P
1
−
P
2
)
ρ
air
=
√
2
(
135
−
275
)
1.165
=
¿
Nomenclature:
Symbol
Description
y
Height for Jet Flow
25
Your preview ends here
Eager to read complete document? Join bartleby learn and gain access to the full version
- Access to all documents
- Unlimited textbook solutions
- 24/7 expert homework help
P
1
Pressure 1
P
2
Pressure 2
C
Discharge Coefficient
Q
Flow Rate
A
Area
V
Velocity
ρ
Density
ME 343 Laboratory Instructions
26
Your preview ends here
Eager to read complete document? Join bartleby learn and gain access to the full version
- Access to all documents
- Unlimited textbook solutions
- 24/7 expert homework help
Safety Hazards
Instrumentation Laboratory Room 214
HAZARD: Rotating Equipment / Machine Tools
Personal Protective Equipment
: Safety Goggles;
Standing Shields, Sturdy Shoes.
Personal Care
1.
Do not wear loose clothing, Neck Ties/Scarves;
Jewelry (remove).
2.
Tie back long hair.
HAZARD: Heating – Burns
Personal Protective Equipment
: High temperature
gloves; High temperature apron.
HAZARD: Electrical - Burns / Shock
Personal Care:
Take Care while doing electrical
connections, particularly with grounding; do not use
frayed electrical cords.
HAZARD: Water / Slip Hazard
Personal Care:
Clean any spills immediately.
HAZARD: Noise
Personal Protective Equipment:
Ear Plugs
Measurement of Flow & System Uncertainty Analysis
Objectives:
27
Your preview ends here
Eager to read complete document? Join bartleby learn and gain access to the full version
- Access to all documents
- Unlimited textbook solutions
- 24/7 expert homework help
1.
Flow pattern analysis.
2.
Flowrate measurement with Venturi meter and Orifice plate.
3.
Flow velocity profile measurement with Pitot tube.
4.
System Uncertainty Analysis
a.
Flowrate (Orifice Plate) OR Pitot tube
1)
Calibration of Flow-meters
1.
Set the flow rate on the rotameter with the inlet hand valve to a
value of 5.
2.
Record the weight of the tank and close the bypass to the pump so the water goes to the tank for a period of 1 minute for higher flow rate and 2
3.
minutes for lower flow rate.
4.
3. Record the pressure drop ΔPL through the rotameter on the differential
5.
pressure gage by opening valves Q and R.
6.
4. Record the pressure drop ΔPL through the Turbine flow meter on the
7.
differential pressure gage by opening valves A and B.
8.
5. Record the pressure drop ΔPM through the Venturi on the differential
9.
pressure gage by opening valves E and D. Then record the pressure drop
10.
ΔPL through the Venturi on the differential pressure gage by
opening
11.
valves C and F.
12.
6. Record the pressure drop ΔPM through the nozzle on the
differential
13.
pressure gage by opening valves I and H. Then record the pressure drop
14.
ΔPL through the nozzle on the differential pressure gage by opening
15.
valves J and G.
16.
7. Record the pressure drop ΔPM through the orifice on the differential
17.
pressure gage by opening valves M and L. Then record the pressure drop
18.
ΔPL through the orifice on the differential pressure gage by opening valves
19.
N and K.
28
Your preview ends here
Eager to read complete document? Join bartleby learn and gain access to the full version
- Access to all documents
- Unlimited textbook solutions
- 24/7 expert homework help
20.
8. Record the digital output from the counter of Turbine flow meter.
21.
9. Repeat steps 1 through 8 for rotameter settings of 4.5, 4, 3, 2, and 1.5.
22.
C. Zhu, September, 2009 2
23.
ME343 Laboratory Instruction
2)
Measurement of Air Jet Velocity
a.
Adjust the horizontal balance of a fan. Set the Pitot tube in an alignment with the centerline of the jet exit from the fan and record
the axial distance from the jet exit.
b.
Remove the cap from the vertical manometer which is connected to the Pitot tube. Record the initial reading of manometer.
c.
Turn on the power of fan and set the power to maximum. Record the manometer reading. If the variation of manometer readings is within the range of inclined manometer measurement, repeat steps 2 and 3 to use the inclined manometer instead of the vertical manometer.
d.
Recording the manometer reading in both traverse directions for at least 6 points on each side or until the change in manometer reading becomes insignificant.
e.
Repeat steps 1 to 4 for different axial distances (each group measures at least two velocity profiles at different axial distances).
3)
Measurement using Laser Doppler Velocimetry (LDV) (Optional)
Caution: Wear the Laser Safety Goggle!!!
a.
Take off the cap from head of Laser beam tube.
b.
Turn on the Computer, Laser Generator and Processor. Wait until the “Ready” light on Processor turn to Green. Double click “BSA flow” Button to open software on the desktop.
c.
Click on “New Project”, make sure “black Project” in “Project” Tab is highlighted. Click on “ok”.
d.
Click from main menu “File” → “New” to start a new measurement. Highlight “BSA Application” in “Object” Tab. Click on “OK”, then “Connect”, wait until the light “On line” of Processor turns to green.
e.
In BSA Application window, select the Group 1 to edit properties in property window which is located at left side of the window. Set the termination criteria of a data acquisition (max. Samples: 3000 max. Acquisition time100 second).
f.
In BSA Application window, select the LDA 1 to edit properties in property window. Set the Center frequency (0.0 m/s), Bandwidth 29
Your preview ends here
Eager to read complete document? Join bartleby learn and gain access to the full version
- Access to all documents
- Unlimited textbook solutions
- 24/7 expert homework help
(0.23412 m/s), High voltage level (1800V), and Signal gain (28 dB). It is noted that these variables may be reset for different flow measurements.
g.
To monitor the Doppler signals, right click on Processor, Group 1 or LDA 1 in the BSA Application
window, and select System Monitor from the list, click on “File” → “New”→ “Histogram” and . “File” → “New”→ “list” to show the data diagram and list on screen.
h.
Turn the laser block shutte
r from Closed to Open
.
i.
Precisely adjust the laser focus point to the measurement location, using the traversing stage. Move stage up/down and left/right to let laser beam focus at center of cylinder. Move left/right to let focus at right edge of cylinder. Move 5 cycles of stage further to let the focus reach to first measuring location. In this part, a velocity profile in the wake of a cylinder needs to be obtained with at least 6
points at different locations (see below for locations).
30
Your preview ends here
Eager to read complete document? Join bartleby learn and gain access to the full version
- Access to all documents
- Unlimited textbook solutions
- 24/7 expert homework help
31
Your preview ends here
Eager to read complete document? Join bartleby learn and gain access to the full version
- Access to all documents
- Unlimited textbook solutions
- 24/7 expert homework help
32
Your preview ends here
Eager to read complete document? Join bartleby learn and gain access to the full version
- Access to all documents
- Unlimited textbook solutions
- 24/7 expert homework help
33
Your preview ends here
Eager to read complete document? Join bartleby learn and gain access to the full version
- Access to all documents
- Unlimited textbook solutions
- 24/7 expert homework help
Related Questions
True Story! The 1998-1999 Mars Climate Orbiter mission was declared a total loss in1999 as there was a unit conversion mismatch error between Lockheed Martin and NASA. Themismatch was in the thruster force units. NASA used the SI system which called forNewton-Seconds (4.45 times as large) of thrust and Lockheed Martin used Pound-Force Seconds.Calculations placed the Orbiter at 68 miles from the surface as it went into orbit, but it waswithin 57 km of the surface after the breaking maneuver. Any distance from the surface lessthan 50 miles would have caused the Orbiter to crash.a. What was the actual distance of the Orbiter from the surface in miles?b. In percentage, how far off from the calculated 68 miles was the Orbiter?
arrow_forward
I need help solving this problem.
arrow_forward
University of Babylon
Collage of Engineering\Al-Musayab
Department of Automobile
Engineering
Under Grad/Third stage
Notes:
1-Attempt Four Questions.
2- Q4 Must be Answered
3-Assume any missing data.
4 تسلم الأسئلة بعد الامتحان مع الدفتر
Subject: Mechanical
Element Design I
Date: 2022\01\25
2022-2023
Time: Three Hours
Course 1
Attempt 1
Q1/ Design a thin cylindrical pressure tank (pressure vessel) with hemispherical ends to the
automotive industry, shown in figure I below. Design for an infinite life by finding the
appropriate thickness of the vessel to carry a sinusoidal pressure varied from {(-0.1) to (6) Mpa}.
The vessel is made from Stainless Steel Alloy-Type 316 sheet annealed. The operating
temperature is 80 C° and the dimeter of the cylinder is 36 cm. use a safety factor of 1.8.
Fig. 1
(15 Marks)
Q2/ Answer the following:
1- Derive the design equation for the direct evaluation of the diameter of a shaft to a desired
fatigue safety factor, if the shaft subjected to both fluctuated…
arrow_forward
Which of these statements are correct?
arrow_forward
answer a & b. Please show all your work!!
arrow_forward
デジタル形式で段階的に解決
ありがとう!!
SOLVE STEP BY STEP IN DIGITAL FORMAT
An object with a mass of 47 kg is moved horizontally at constant
speed by a force of 203 N using a rope that makes an angle of 30
degrees with the horizontal.
a) What is the coefficient of friction?
arrow_forward
O Week 2- 20527 22110L
x a MasteringEngineering Mastering x
M Inbox (10,309) - usmikail@gmail x
a Product Detail Page
a Central Service Technical Manual x
O 21) YouTube
i session.masteringengineering.com/myct/itemView?assignmentProblemiD=12443395&offset=next
KHW 1
Problem 12.3
6 of 16
I Review
A particle travels along a straight line with a velocity
v = (12 – 3t2) m/s, where t is in seconds. When
t = 1 s, the particle is located 10 m to the left of the
origin.
Express your answer to three significant figures and include the appropriate units.
As =
437
Submit
Previous Answers Request Answer
X Incorrect; Try Again; 4 attempts remaining
Part C
Determine the distance the particle travels during the time period given in previous part.
Express your answer to three significant figures and include the appropriate units.
?
ST =
Value
Units
arrow_forward
University Of Babylon
College of Mussayb
Automobile Production
Quiz(2) 2024-205
7. Which classification method considers the
number of independent movements a robot can
make?
0
0
о
a) Classification by Degrees of Freedom
b) Classification by Kinematic Structure
c) Classification by Drive Technology
d) Classification by Workspace Geometry
8. Which classification method focuses on the
arrangement of the robot's joints?
。 a) Classification by Degrees of Freedom
。 b) Classification by Kinematic Structure
° c) Classification by Drive Technology
od) Classification by Motion
Characteristics
9. What is the difference between a robot with 2
Degrees of Freedom (DOF) and one with 6
DOF?
о a) The 6 DOF robot can move faster.
o b) The 6 DOF robot can move more
precisely.
o c) The 6 DOF robot can perform more
complex tasks.
o d) All of the above
10. What are some examples of drive technologies
used in robots?
。 a) Hydraulic, pneumatic, and electric
о
b) Gear, belt, and chain drives
o c) Ball screws,…
arrow_forward
Sensor systems for obstacle detection and avoidance in mobile robots.
• Produce a written report documenting: the choice of sensors, sensor evaluation, the developed processor/measurement system, and overall system performance.
arrow_forward
Statics of Rigid Bodies (S6)
Note: I will report you if you answer this post multiple times so please follow it.Thank you for understanding, Tutor!
Content Covered:
- Friction
Direction: Solve the problem below by giving the complete solution. In return, I will give you a good and high rating. Thank you so much!
Note: Be careful with the calculations in the problem. Kindly double check the solution and answer if there is a deficiency. And also, box the final answer. Thank you so much!
arrow_forward
OBJECTIVE TYPE QUESTIONS
1.
The velocity ratio of two pulleys connected by an open belt or crossed belt is
2.
(a) directly proportional to their diameters
(b) inversely proportional to their diameters
(c) directly proportional to the square of their diameters
(d) inversely proportional to the square of their diameters
Two pulleys of diameters d, and d, and at distance x apart are connected by means of an open belt
drive. The length of the belt is
(a)(d+d₁)+2x+
(d₁+d₂)²
4x
(b)(d₁-d₂)+2x+
(d₁-d₂)²
4x
(c)(d₁+d₂)+ +2x+
(d₁-d₂)²
4x
(d)(d-d₂)+2x+
(d₁ +d₂)²
4x
3.
In a cone pulley, if the sum of radii of the pulleys on the driving and driven shafts is constant, then
(a) open belt drive is recommended
(b) cross belt drive is recommended
(c) both open belt drive and cross belt drive are recommended
(d) the drive is recommended depending upon the torque transmitted
Due to slip of the belt, the velocity ratio of the belt drive
4.
(a) decreases
5.
(b) increases
(c) does not change
When two pulleys…
arrow_forward
Statics and Principles of Moments
A seesaw that weights 45lbs and its 5m long is balanced on the fulcrum in the center.
1- Two children are sitting on opposite sides of each other on the seesaw. One child weights 50lbs and is sitting 0.7m on the left side. Where should the other child sit in order to be balanced on the seesaw if they weigh 42lbs?
2- Now, another child wants to sit on the seesaw and weighs 30lbs and is sitting 1.25m in front of them and is closer to the fulcrum. What are the CW and CCW moment of the seesaw now? What is the net moment and direction?
3- Then, a fourth child wants to play on the seesaw and is on the left side of the plank in order to bring the system to equilibrium. How much does the child weigh (Calculate the pounds of force needed in order for rebalance?)
4- Now the fourth child leaves the other three children sitting on the plank. If the three children are sitting in the same potions as they did in part b, the plank would need to move on the seesaw…
arrow_forward
A Team of Engineers asked for an internal combustion engine to use it in a designed car. Your role is to describe the operation sequence of different types of available engines, explain their mechanical efficiency, and deliver a detailed technical report to show your approach in solving and discussing the following tasks and issues.
You must follow the following steps to help the team:
STEP 1
Describe the operational sequence of four-stroke spark ignition and four-stroke compression ignition engines with the aid of sketches by constructing simple sketch representing the operation and plotting the P-V diagrams for each process during the cycle to show the following:
The input and output heat and net output work
The expansion and compression strokes
The air-fuel mixture intake and exhaust gasses
The spark plug when it is in the active mode
The complete cycle of ideal Otto and Diesel cycles that shows the input and output heat and net output work.
STEP 2
Explain the mechanical…
arrow_forward
SEE MORE QUESTIONS
Recommended textbooks for you
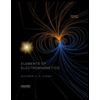
Elements Of Electromagnetics
Mechanical Engineering
ISBN:9780190698614
Author:Sadiku, Matthew N. O.
Publisher:Oxford University Press
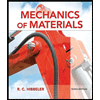
Mechanics of Materials (10th Edition)
Mechanical Engineering
ISBN:9780134319650
Author:Russell C. Hibbeler
Publisher:PEARSON
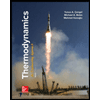
Thermodynamics: An Engineering Approach
Mechanical Engineering
ISBN:9781259822674
Author:Yunus A. Cengel Dr., Michael A. Boles
Publisher:McGraw-Hill Education
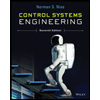
Control Systems Engineering
Mechanical Engineering
ISBN:9781118170519
Author:Norman S. Nise
Publisher:WILEY
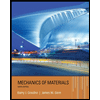
Mechanics of Materials (MindTap Course List)
Mechanical Engineering
ISBN:9781337093347
Author:Barry J. Goodno, James M. Gere
Publisher:Cengage Learning
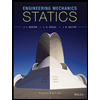
Engineering Mechanics: Statics
Mechanical Engineering
ISBN:9781118807330
Author:James L. Meriam, L. G. Kraige, J. N. Bolton
Publisher:WILEY
Related Questions
- True Story! The 1998-1999 Mars Climate Orbiter mission was declared a total loss in1999 as there was a unit conversion mismatch error between Lockheed Martin and NASA. Themismatch was in the thruster force units. NASA used the SI system which called forNewton-Seconds (4.45 times as large) of thrust and Lockheed Martin used Pound-Force Seconds.Calculations placed the Orbiter at 68 miles from the surface as it went into orbit, but it waswithin 57 km of the surface after the breaking maneuver. Any distance from the surface lessthan 50 miles would have caused the Orbiter to crash.a. What was the actual distance of the Orbiter from the surface in miles?b. In percentage, how far off from the calculated 68 miles was the Orbiter?arrow_forwardI need help solving this problem.arrow_forwardUniversity of Babylon Collage of Engineering\Al-Musayab Department of Automobile Engineering Under Grad/Third stage Notes: 1-Attempt Four Questions. 2- Q4 Must be Answered 3-Assume any missing data. 4 تسلم الأسئلة بعد الامتحان مع الدفتر Subject: Mechanical Element Design I Date: 2022\01\25 2022-2023 Time: Three Hours Course 1 Attempt 1 Q1/ Design a thin cylindrical pressure tank (pressure vessel) with hemispherical ends to the automotive industry, shown in figure I below. Design for an infinite life by finding the appropriate thickness of the vessel to carry a sinusoidal pressure varied from {(-0.1) to (6) Mpa}. The vessel is made from Stainless Steel Alloy-Type 316 sheet annealed. The operating temperature is 80 C° and the dimeter of the cylinder is 36 cm. use a safety factor of 1.8. Fig. 1 (15 Marks) Q2/ Answer the following: 1- Derive the design equation for the direct evaluation of the diameter of a shaft to a desired fatigue safety factor, if the shaft subjected to both fluctuated…arrow_forward
- Which of these statements are correct?arrow_forwardanswer a & b. Please show all your work!!arrow_forwardデジタル形式で段階的に解決 ありがとう!! SOLVE STEP BY STEP IN DIGITAL FORMAT An object with a mass of 47 kg is moved horizontally at constant speed by a force of 203 N using a rope that makes an angle of 30 degrees with the horizontal. a) What is the coefficient of friction?arrow_forward
- O Week 2- 20527 22110L x a MasteringEngineering Mastering x M Inbox (10,309) - usmikail@gmail x a Product Detail Page a Central Service Technical Manual x O 21) YouTube i session.masteringengineering.com/myct/itemView?assignmentProblemiD=12443395&offset=next KHW 1 Problem 12.3 6 of 16 I Review A particle travels along a straight line with a velocity v = (12 – 3t2) m/s, where t is in seconds. When t = 1 s, the particle is located 10 m to the left of the origin. Express your answer to three significant figures and include the appropriate units. As = 437 Submit Previous Answers Request Answer X Incorrect; Try Again; 4 attempts remaining Part C Determine the distance the particle travels during the time period given in previous part. Express your answer to three significant figures and include the appropriate units. ? ST = Value Unitsarrow_forwardUniversity Of Babylon College of Mussayb Automobile Production Quiz(2) 2024-205 7. Which classification method considers the number of independent movements a robot can make? 0 0 о a) Classification by Degrees of Freedom b) Classification by Kinematic Structure c) Classification by Drive Technology d) Classification by Workspace Geometry 8. Which classification method focuses on the arrangement of the robot's joints? 。 a) Classification by Degrees of Freedom 。 b) Classification by Kinematic Structure ° c) Classification by Drive Technology od) Classification by Motion Characteristics 9. What is the difference between a robot with 2 Degrees of Freedom (DOF) and one with 6 DOF? о a) The 6 DOF robot can move faster. o b) The 6 DOF robot can move more precisely. o c) The 6 DOF robot can perform more complex tasks. o d) All of the above 10. What are some examples of drive technologies used in robots? 。 a) Hydraulic, pneumatic, and electric о b) Gear, belt, and chain drives o c) Ball screws,…arrow_forwardSensor systems for obstacle detection and avoidance in mobile robots. • Produce a written report documenting: the choice of sensors, sensor evaluation, the developed processor/measurement system, and overall system performance.arrow_forward
- Statics of Rigid Bodies (S6) Note: I will report you if you answer this post multiple times so please follow it.Thank you for understanding, Tutor! Content Covered: - Friction Direction: Solve the problem below by giving the complete solution. In return, I will give you a good and high rating. Thank you so much! Note: Be careful with the calculations in the problem. Kindly double check the solution and answer if there is a deficiency. And also, box the final answer. Thank you so much!arrow_forwardOBJECTIVE TYPE QUESTIONS 1. The velocity ratio of two pulleys connected by an open belt or crossed belt is 2. (a) directly proportional to their diameters (b) inversely proportional to their diameters (c) directly proportional to the square of their diameters (d) inversely proportional to the square of their diameters Two pulleys of diameters d, and d, and at distance x apart are connected by means of an open belt drive. The length of the belt is (a)(d+d₁)+2x+ (d₁+d₂)² 4x (b)(d₁-d₂)+2x+ (d₁-d₂)² 4x (c)(d₁+d₂)+ +2x+ (d₁-d₂)² 4x (d)(d-d₂)+2x+ (d₁ +d₂)² 4x 3. In a cone pulley, if the sum of radii of the pulleys on the driving and driven shafts is constant, then (a) open belt drive is recommended (b) cross belt drive is recommended (c) both open belt drive and cross belt drive are recommended (d) the drive is recommended depending upon the torque transmitted Due to slip of the belt, the velocity ratio of the belt drive 4. (a) decreases 5. (b) increases (c) does not change When two pulleys…arrow_forwardStatics and Principles of Moments A seesaw that weights 45lbs and its 5m long is balanced on the fulcrum in the center. 1- Two children are sitting on opposite sides of each other on the seesaw. One child weights 50lbs and is sitting 0.7m on the left side. Where should the other child sit in order to be balanced on the seesaw if they weigh 42lbs? 2- Now, another child wants to sit on the seesaw and weighs 30lbs and is sitting 1.25m in front of them and is closer to the fulcrum. What are the CW and CCW moment of the seesaw now? What is the net moment and direction? 3- Then, a fourth child wants to play on the seesaw and is on the left side of the plank in order to bring the system to equilibrium. How much does the child weigh (Calculate the pounds of force needed in order for rebalance?) 4- Now the fourth child leaves the other three children sitting on the plank. If the three children are sitting in the same potions as they did in part b, the plank would need to move on the seesaw…arrow_forward
arrow_back_ios
SEE MORE QUESTIONS
arrow_forward_ios
Recommended textbooks for you
- Elements Of ElectromagneticsMechanical EngineeringISBN:9780190698614Author:Sadiku, Matthew N. O.Publisher:Oxford University PressMechanics of Materials (10th Edition)Mechanical EngineeringISBN:9780134319650Author:Russell C. HibbelerPublisher:PEARSONThermodynamics: An Engineering ApproachMechanical EngineeringISBN:9781259822674Author:Yunus A. Cengel Dr., Michael A. BolesPublisher:McGraw-Hill Education
- Control Systems EngineeringMechanical EngineeringISBN:9781118170519Author:Norman S. NisePublisher:WILEYMechanics of Materials (MindTap Course List)Mechanical EngineeringISBN:9781337093347Author:Barry J. Goodno, James M. GerePublisher:Cengage LearningEngineering Mechanics: StaticsMechanical EngineeringISBN:9781118807330Author:James L. Meriam, L. G. Kraige, J. N. BoltonPublisher:WILEY
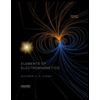
Elements Of Electromagnetics
Mechanical Engineering
ISBN:9780190698614
Author:Sadiku, Matthew N. O.
Publisher:Oxford University Press
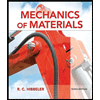
Mechanics of Materials (10th Edition)
Mechanical Engineering
ISBN:9780134319650
Author:Russell C. Hibbeler
Publisher:PEARSON
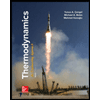
Thermodynamics: An Engineering Approach
Mechanical Engineering
ISBN:9781259822674
Author:Yunus A. Cengel Dr., Michael A. Boles
Publisher:McGraw-Hill Education
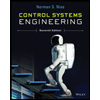
Control Systems Engineering
Mechanical Engineering
ISBN:9781118170519
Author:Norman S. Nise
Publisher:WILEY
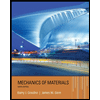
Mechanics of Materials (MindTap Course List)
Mechanical Engineering
ISBN:9781337093347
Author:Barry J. Goodno, James M. Gere
Publisher:Cengage Learning
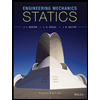
Engineering Mechanics: Statics
Mechanical Engineering
ISBN:9781118807330
Author:James L. Meriam, L. G. Kraige, J. N. Bolton
Publisher:WILEY