learning resource answer guide
docx
keyboard_arrow_up
School
Oxford University *
*We aren’t endorsed by this school
Course
433
Subject
Mechanical Engineering
Date
Nov 24, 2024
Type
docx
Pages
22
Uploaded by CorporalWorldFish31
Student workbook
Answer Guide Topics 1-5
BSBWHS518
Manage WHS hazards associated with
maintenance and use of plant
Contents
Feedback: Topic 1
......................................................................................................................
4
Activity 1.1: Identify how to access sources of WHS information
........................................
4
Activity 1.2: identify how to inspect items of plant and identify how they are to be used.5
Activity 1.3: Determine WHS hazards
...................................................................................
7
Activity 1.4: Forum: Consult with others to confirm hazard identification
..........................
8
Activity 1.5: Identify how to record and report identified hazards
......................................
9
Feedback: Topic 2
....................................................................................................................
11
Activity 2.1: Identify how to access sources of information, data and advice
...................
11
Activity 2.2: Identify how to consult with others to inform WHS risk assessment
............
11
Activity 2.3: Identify how to record and report on WHS risk assessment
.........................
13
Feedback: Topic 3
....................................................................................................................
14
Activity 3.1: Identify how to access sources of information, data
.....................................
14
Activity 3.2: Identify how to develop risk controls
.............................................................
14
Activity 3.3: Forum: Identify how to consult with internal and specialist personnel
........
15
Activity 3.4: Identify how to communicate rights, obligations and duties of workplace
personnel
............................................................................................................................
16
Activity 3.5: Identify how to monitor the effectiveness of implemented risk controls
.....
18
Activity 3.6: Identify how to record and report on implemented risk controls
.................
19
Feedback: Topic 4
....................................................................................................................
20
Activity 4.1: Identify types of plant requiring registration and tasks requiring operator
licensing
..............................................................................................................................
20
Activity 4.2: Identify how to document registration, licensing and certification
requirements
......................................................................................................................
21
Activity 4.3: Identify how to monitor and report compliance with WHS regulatory
requirements
......................................................................................................................
21
Feedback: Topic 5
....................................................................................................................
23
Activity 5.1: Identify WHS-related training needs and identify skill gaps
..........................
23
Activity 5.2: Identify how to ensure training is undertaken and completed
......................
24
Image attributions
...................................................................................................................
25
Page 2 of 22
Feedback: Topic 1
Activity 1.1: Identify how to access sources of WHS
information
For two different items of plant used at your organisation, or in your business industry,
access WHS information and research how you can work safely with these items.
Document your findings using MS Word or similar and provide a one A4 page summary of
your findings; as a minimum, you must include:
•
three WHS requirements or recommendations for each item of plant and
•
provide a reference of your information sources (stating the name of the source and
where you obtained this from).
Note: Information must be sourced from trusted/authoritative sources; this may include
WHS legislation, codes of practice, manufacturer information and WHS legal advice sources.
You will need to attach your document to this workbook, labelled with your name and
activity reference number.
Feedback
You must access WHS information and research on how to work safely with two different items of
plant that are used at your organisation or in your business industry. You must provide a reference
for your information sources with your written summary.
Items of plant may vary, depending on your business industry; plant may include:
•
pressure equipment
•
cranes
•
hoists
•
lifts, escalators and moving walkways
•
manufacturing machines
•
printing machines
•
scaffolding
•
amusement devices.
Working safely may relate to:
•
using machine guards
•
using PPE
•
setting-up plant
•
working in isolation from others
•
working with a colleague
•
performing maintenance and machine care
Page 3 of 22
Your preview ends here
Eager to read complete document? Join bartleby learn and gain access to the full version
- Access to all documents
- Unlimited textbook solutions
- 24/7 expert homework help
•
checking plant readings or machine parts
•
having isolation controls to turn off energy sources
•
having emergency stops to shut-down machinery
•
having alarms and lights to warn of plant use.
Activity 1.2: identify how to inspect items of plant and
identify how they are to be used
Resources and equipment required to complete this activity:
•
A real or simulated work environment
•
Policy and procedures for inspecting plant (from your workplace or you may use
Appendix A at the end of this workbook).
•
Two items of workplace plant (as relevant to your business industry).
You are required to inspect two items of workplace plant and record what they are and how
they are to be used. You should include any relevant notes relating to health and safety, such
as wear and tear of plant, emergency stop functions or machine guards.
You may include photographs to support your findings. Attach to this workbook with a
reference to the activity number in the file name.
Feedback
Plant
How is it used
WHS
considerations
Existing
controls
The saw is
operated by a
person who
stands in front
and pulls the
handle down
to apply
pressure from
the blade onto
the metal to
be cut.
Steel is loaded
onto the roller
bed prior to
cutting.
PPS
requirements,
glasses and or
face shield,
gloves.
Rotating
machinery
poses a risk of
entanglement,
particularly loose
clothing and long
hair.
Manual handling
of heavy lengths
of steel.
Guard is in place
over the blade.
Existing
controls include
the safe
operating
procedure and
PPE provided
for the
operator.
Forklift for
heavy lifting, or
use of other
people to carry
out a team lift
as specified in
the safe
operating
procedure.
Plant
How is it used
WHS
Existing
Page 4 of 22
considerations
controls
No existing
emergency stop is
installed.
Hydraulic
Press is
operated by an
individual
using control
levers.
Work item to
be pressed is
loaded onto
the bed of the
press in the
desired
position. Press
is operated
until the work
item is in the
desired. state
Work item is
removed from
the press bed.
Crush injury of
the operator is
holding the work
item.
Flying objects if
the work item is
not positioned
safely and
securely.
Hydraulic
injection injury if
the hoses or
fittings fail.
No guarding is in
place.
No emergency
stop is installed.
A competent
person
regularly
services the
press.
Safe Operating
Procedure in
place and
personnel
trained before
use.
Activity 1.3: Determine WHS hazards
Following on from
Activity 1.2: identify how to inspect items of plant and identify how they
are to be used
, as relevant to your work environment, document the hazards that are
associated with using the two items of plant, their condition, their suitability for the
workplace, their potential location in the workplace and any potential abnormal situations
that may exist.
Feedback
You must refer to Activity 1.2, and the inspections carried out. You must document your conclusions
found from the assessment of your inspections.
You must identify any hazards with:
Plant 1 – Cut-off saw
Plant 2 – Hydraulic press
Page 5 of 22
Using the plant
Plant operation requires the operator to
place and clamp the steel to be cut in
position, turn on the saw and use the
handle to pull the saw down and cut
through the steel.
When the steel has been cut, the handle
is raised, and the plant turned off.
Plant operation requires the operator to
place the item to be "pressed" onto the
bed of the press in a suitable position.
The operator will need to select a
suitable "dolly" for the pressing
application and hold or secure it in place
while operating a lever to extend the
ram until it contacts the dolly. At this
point, the operator can let go of the
dolly and operate the levers to finish the
process.
The condition of
the plant
The saw is old, though well maintained
and serviceable.
The table it operates on is well made
and fitted with rollers to make the
operation easier.
The press is old, functional and in good
order, though lacks the relevant
engineering approval. If anything it is
over-engineered for its "pressing
capacity", though this has not been
formally assessed.
Their
suitability for
the workplace
Both items of plant are suitable for use
in this workplace. They are well
constructed, robust and well
serviced/maintained. The lack of
engineering certification on the press is
a concern which needs to be addressed.
This is something that can be corrected.
Both items of plant are suitable for use
in this workplace. They are well
constructed, robust and well
serviced/maintained. The lack of
engineering certification on the press is
a concern which needs to be addressed.
This is something that can be corrected.
Plant 1 – Cut-off saw
Plant 2 – Hydraulic press
Their potential
location in the
workplace
Both items of plant are in a suitable
location for their intended use. The saw
has been placed so that lengths of steel
can be fed into it without pre-cutting,
and the wall modified so that long
pieces can be cut off and removed
without obstruction. The press is located
outside, under a skillion roof which
provides a level of separation from
other staff at the worksite should
something o wrong during the process.
Both items of plant are in a suitable
location for their intended use. The saw
has been placed so that lengths of steel
can be fed into it without pre-cutting,
and the wall modified so that long
pieces can be cut off and removed
without obstruction. The press is located
outside, under a skillion roof which
provides a level of separation from
other staff at the worksite should
something o wrong during the process.
Any abnormal
situations that
may exist with
the plant.
The normal operation of the saw
requires a pre-start checklist to be
completed which will highlight any
issues with the operation of the saw.
The main area of concern is damage to
the saw blade.
There are no abnormal situations that
may exist with the plant. It is
particularly hazardous if used
incorrectly.
Page 6 of 22
Your preview ends here
Eager to read complete document? Join bartleby learn and gain access to the full version
- Access to all documents
- Unlimited textbook solutions
- 24/7 expert homework help
Activity 1.4: Forum: Consult with others to confirm hazard
identification
Go to the Forum and post the hazards that you found in
Activity 1.3: Determine WHS
hazards.
Thencomment on the potential harm that may be caused by their occurrence.
Post your response in the 'Consult with others to confirm hazard identification' forum.
After you have posted your answers, review the replies of other students and, where
appropriate, provide feedback on others' responses.
Feedback
You must post your answers in the forum, review the replies of other students and, where
appropriate, provide feedback on others' responses. You must comment on what you confirm and
identify the potential harm that may be caused by each one.
For example, hazards and their harm may include:
•
Exposed moving parts – operators may become caught in machinery.
•
Hot temperature of plant – operators and passers-by may suffer burns if touching hot parts.
•
Noisy machinery – operators may not hear other people or noises around them, making them
unaware of what is happening around them.
Activity 1.5: Identify how to record and report identified
hazards
Refer to Case study: Policies and procedures for recording and reporting hazards.
Case study: Policies and procedures for recording and reporting hazards
Recording and reporting hazards policy
WHS hazards that are identified must be documented and communicated to all relevant
personnel; they must be acted upon to prevent risks from occurring or for risks to be
controlled to a safe level.
Records of hazards must identify the hazard, where this is found, and the persons who
are affected by the hazard. Reports should be made to the officer (as soon as it is
possible to do so), so hazard/risk management can take place.
Recording and reporting hazards procedures
Records of hazards must be completed in the following way:
Page 7 of 22
•
be written clearly and in a permanent form (that is, permanent ink on paper or
saved in organisational electronic records)
•
state the hazard and where this is found
•
state the individuals and/or parties who are at risk from the hazard
•
include the name of the person making the record and the date this was made.
Reporting hazards must be completed in the following way:
•
reports must be made to the officer (in person or writing)
•
report must be made as soon after identification of the hazard, as is possible •
reports must be an accurate account of the hazard record that is made and
be addressed to 'The Officer'.
1.Record your confirmed hazards from
Activity 1.4: Consult with others to confirm hazard
identification
, following the policy and procedures provided.
Feedback
You must follow the guidance provided in the case study to record your confirmed hazards from
Activity 1.4. This must be written clearly and permanently, state the hazards and where they are
found, state the individuals or parties who are at risk and include their name and the date the report
was made.
2.Using the record, you have made, create a short report to inform the officer of the hazards
that have been found.
For this activity, you may use a suitable report template, create your own using MS Word
or similar. Your report should be at least 1 x A4 page.
Please ensure you attach a copy to this workbook referencing the activity number.
Feedback
You must follow the guidance provided in Case study A to report the hazards to the officer in writing.
This must be an accurate account of the hazard record that has been made in activity question one.
This report will be similar to the record but must be addressed to 'The Officer'.
For example:
Dear John,
During our recent Plant Inspection at the workshop, a number of items of plant were
targeted as part of our in-depth study process. This included a metal cut-off saw and a
hydraulic press.
The Saw was a fairly normal example of this type of plant. It was not in new condition,
though it has clearly been well maintained and serviced. The blade was in good order with
Page 8 of 22
no signs of premature failure. The area where the saw was set up is serviceable and
functional.
The Hydraulic Press is in good operational condition and has been well maintained. It is quite
old, though it has had a number of components replaced. While there are no major concerns
with this piece of plant from an operational perspective, it does lack the required engineering
certification or load rating. This needs to be rectified ASAP.
Corrective actions from this process include:
•
Review the Safe Operating procedures for both items of plant
•
Engage a suitably qualified engineer to calculate the safe working load of the press
and install a placard.
Your assistance with any financial approval is appreciated.
Regards,
Worker Bill.
Feedback: Topic 2
Activity 2.1: Identify how to access sources of information,
data and advice
Following on from
Activity 1.4: Consult with others to confirm hazard identification;
for
three of the plant hazards that you identified, access reputable sources of information, data
and/or advice to help you assess the risks to health and safety.
List your three hazards, your information sources, and what you have found.
Feedback
You must access sources of information, data or advice to help them assess the risks to three hazards
found with the plant from Activity 1.4.
The information, data or advice must come from recognised and authoritative sources.
You must write down three hazards and associated risks; must identify what you have found through
the information, data or advice that has been received.
For example, risks may relate to:
•
injury or fatality
•
damage to the workplace
•
loss of work production.
Sources of information may include:
•
WHS personnel
Page 9 of 22
Your preview ends here
Eager to read complete document? Join bartleby learn and gain access to the full version
- Access to all documents
- Unlimited textbook solutions
- 24/7 expert homework help
•
WHS regulator
•
WHS/OHS codes of practice
•
WHS authorities, agencies and consultants.
Activity 2.2: Identify how to consult with others to inform
WHS risk assessment
Following on from
Activity 2.1: Identify how to access sources of information, data and
advice,
you will now prepare an email to your manager informing them about the three
hazard and associated risks with the plant.
Your email communication must include relevant details and their impact on others and the
environment. In closing, you will need to seek feedback from your manager that they agree
on their level of impact and severity of the risk.
You may research a suitable template that can be modified or create your own using MS
Word/Outlook or similar program and attach to this workbook referencing the activity
number in the file name.
Feedback
Student responses must cover the key points above. For example:
To: Management
Subject: Plant associated Risks
Body:
Dear Manager,
The WHS Department has recently carried out a workplace inspection and uncovered several
issues associated with some plant in the workshop.
There are two key items of plant which were the focus of risk management activities
following the inspection. These are a metal cut-off saw and a hydraulic press.
A number of risks are evident:
•
Cut-off Saw
o
Flying objects – from the cutting process.
o
Cuts/lacerations – from sharp edges on the cut metal.
o
Entanglement – hair or clothing caught in rotating parts.
•
Hydraulic Press
o
Flying objects – from misaligned "jobs" on
the press bed.
o
Hydraulic injection injury – from poorly maintained hydraulic hoses and
fittings.
Page 10 of 22
o
Structural failure – no Safe Working Load has been established for the press.
The potentially serious nature of injuries, which may occur as a result of these risks requires
immediate attention. I would appreciate your support and agreement that we can take
required action as detailed in the recommendations from the WHS department.
Regards,
WHS Advisor
Activity 2.3: Identify how to record and report on WHS risk
assessment
Referring back to
Activity 2.1: Identify how to access sources of information, data and
advice
and
Activity 2.2: Identify how to consult with others to inform WHS risk
assessment
, create a brief report that identifies the following:
•
your three hazards and the information you found out
•
the outcomes of your consultation on the hazards, risks and impacts.
•
This should be no more than one A4 page in length. You may research a suitable
template that can be modified or create your own using MS Word or similar program
and attach to this workbook referencing the activity number in the file name.
Feedback
Plant – Risk and control
A recent workplace inspection uncovered a number of concerns associated with items of plant in the
workshop. While there is a lot that is being done well, there is a real risk of serious injury associated
with the use of the cut-off saw and the hydraulic press.
It is considered that the following three risks are more serious and require more urgent attention:
•
flying objects from the press
•
flying objects from the saw
•
entanglement in the saw's rotating components.
A series of toolbox talks and safe behaviour observations were undertaken to ensure sufficient
consultation took place with workers who have experience using the equipment. This consultation
uncovered a number of near-miss incidents and minor injuries went unreported over the past 12
months. This new information highlights the seriousness of the risk and uncovered a culture of
nonreporting.
More information is available from the following sources:
•
Code of Practice – Managing the risks of plant in the workplace
•
NOHSC – National Standard for Plant (1994)
•
Australian Standard 4024 – Safety of Machinery
Page 11 of 22
•
SafeWork NSW – Hazard Library
Further work is required to ensure the safety of workers who are using this plant. Following
consultation with workers, there are now other issues which need to be added to the scope of this
project.
Feedback: Topic 3
Activity 3.1: Identify how to access sources of information,
data
Following on from
Activity 2.3: Identify how to record and report on WHS risk
assessment;
concerning the three plant hazards, access health and safety information, data
and/or advice from reputable sources for preliminary research on the development of risk
controls.
Prepare notes or collect the information you find, as preparation for
Activity 3.2: Identify
how to develop risk controls.
Feedback
You must access information data or advice in relation to health and safety for developing risk
controls for your three identified hazards. You should note down or attach what they find, and this
should be from authoritative sources, such as WHS/OHS regulators, local government and WHS
experts.
Information may relate to WHS management of hazards, risk controls or plant-specific information.
Activity 3.2: Identify how to develop risk controls
Following on from
Activity 3.1: Identify how to access sources of information, data;
for your
three hazards, use the hierarchy of risk control measures (identified in section
Develop risk
controls
of the unit) to develop risk controls that eliminate or manage the risks.
Record what these are and how you would implement them in the workplace.
Feedback
You must refer to the hierarchy of risk controls found in section 3.2 of the learning unit; you may also
refer to Safe Work Australia or your own WHS/OHS regulator for this information.
The hierarchy of risk control measures from Safe Work Australia:
•
Level one – eliminate the hazard.
•
Level two – substitute the hazard for something safer, isolate the hazard or reduce risks
through engineering controls.
Page 12 of 22
Your preview ends here
Eager to read complete document? Join bartleby learn and gain access to the full version
- Access to all documents
- Unlimited textbook solutions
- 24/7 expert homework help
•
Level three – reduce exposure to the hazard using administrative actions, or use personal
protective equipment (PPE).
Risk controls for the plant include:
•
machine guards
•
access and egress
•
barriers and signs
•
emergency stops and warning devices
•
supervision and training
•
improved work procedures for plant.
Implementation may refer to producing schedules, prioritising risk controls, and how to carry out
activities. A systematic approach should be used to ensure consistent and safe standards of risk
control management.
Activity 3.3: Forum: Identify how to consult with internal
and specialist personnel
1.Go to the Forum page and post the risk controls you have identified together with details
on how you plan to implement them.
•
Post your response in the 'Identify how to consult with internal and specialist
personnel' forum.
•
After you have posted your response, review the replies of other students and
comment where applicable.
Feedback
You must post your answers in the forum, review the replies of other students and, where
appropriate, provide feedback on others' responses.
Posts will include details of controls devised in Activity 3.2.
2.Following your consultation with other forum members in question one, prepare a brief
report (1 x A4 page) to report the outcomes of the consultation.
For this activity, you may use a suitable template, create your own using MS Word or
similar and attach a copy to this workbook activity number.
Feedback
Student feedback will vary based on previous activities.
Page 13 of 22
The following controls have been proposed following consultation with workers on the three more
serious risks associated with the operation of the cut-off saw and the hydraulic press.
Flying objects from the cut-off saw
•
Proposed controls – cut-off saw:
o
Installation of additional guarding between the saw table and the operator's position
o
Requirement for operators to wear safety glasses and a face shield
o
Requirement
for operators to have long hair tied back
o
Installation of footswitch to keep
operators a safe distance from the saw while operating
o
Requirement for operators
to wear a leather apron while operating the saw
o
Review of SOP and additional
training for all operators.
Flying objects from the hydraulic press
•
Proposed controls – hydraulic press
o
Install mesh guarding around the press
o
Purchase and installation of additional equipment to enable the job to be set-up in
the press and the operator to stand outside the cage.
•
The controls will be scheduled for review at every operation in the first week, followed by
monthly review thereafter. It is anticipated that modification or adjustment to the location of
the footswitch will be required. It is also anticipated that a level of objection will be seen
regarding the use of the cage around the press.
Activity 3.4: Identify how to communicate rights, obligations
and duties of workplace personnel
Your manager has requested that you address with your team the rights, obligations and
duties of workplace personnel for the identified hazards and risk controls from
Activity 3.2:
Identify how to develop risk controls.
You have decided to address this in the next toolbox talk meeting. In preparation, you will
prepare a handout that will be provided to each member. The staff handout needs to
conform to the organisation's style guidelines as this will also be filed with the toolbox talk
briefing notes for company records.
As a minimum your supporting staff handout must include:
•
date of discussion
•
key points to be covered
o
stakeholders
o
the rights, obligations and duties of workplace personnel for the
identified hazards and risk controls
Page 14 of 22
•
how you will accommodate any feedback
•
reminder to staff to acknowledge receipt of the handout in the toolbox talk briefing
document.
For this activity, you may use a suitable template, create your own using MS Word or similar
and attach a copy to this workbook referencing the activity number.
Feedback
Your responses will vary depending on the template used. Content of the prepared document must
include the points above. For example:
Toolbox Talk
27/11/2020
Topic
The main topic for today's toolbox talk is risk associated with plant
Background
Workplace inspection carried out, identified risk associated with the use
of a number of items of plant.
Risks included flying objects from the saw, flying objects from the press
and risk of entanglement in the rotating saw blade
Stakeholders
Any person who uses these items of plant is at risk of injury. This includes
regular workers in the workshop and contractors who may use it from
time to time.
Obligations of workers
As everyone already knows, you have the right to work in a safe
workplace. This right comes with an obligation to work within the
direction given by the PCBU, including policy and procedure and verbal
instruction.
The existing policies and procedures in place for the operation of plant in
the workshop will be reviewed and refresher training provided.
Additional PPE will be available.
Additional guarding will be installed over the coming week.
Feedback
Ongoing monitoring of the identified risks will be carried out by the WHS
team, though your ongoing feedback and support is appreciated. If you
have concerns, they can be passed on through your supervisor, or the
WHS team.
Reminder
Don't forget to sign the attendance sheet for this Toolbox Talk.
Activity 3.5: Identify how to monitor the effectiveness of
implemented risk controls
1.What activities can you do to monitor risk controls?
Page 15 of 22
Your preview ends here
Eager to read complete document? Join bartleby learn and gain access to the full version
- Access to all documents
- Unlimited textbook solutions
- 24/7 expert homework help
Feedback
•
Monitoring risk controls can take many forms. It can include inspection of a work area, an
audit of compliance with procedures, review of incident data over a period following control,
consultation with workers.
•
Monitoring must consider whether the control has achieved the intended result. In some
cases, the desired outcome, or what we want to achieve, does not actually occur. In some
cases, we actually even create additional issues. This is particularly relevant where
engineering controls are put in place, and other impacts occur.
2.How should you review and evaluate the effectiveness of risk controls? (Answers to be no
more than 100 words).
Feedback
Monitoring activities will depend on the nature of the risk. It may include observation, review of
procedures and risk assessments, discussion with operators or even a combination of those.
Examples might include:
•
Control – Install guarding around plant
o
Review – observe the operation of the plant to see
if the guard allows the worker to operate the plant safely if the guard is being used as
intended if the guard creates additional problems or risk for the operator.
•
Control – updated safe work procedure
o
Review – observe a worker doing the job covered by the procedure and compare the
steps int eh procedure compared to actual steps. Uncover differences and discuss
them with the operator to uncover issues.
Activity 3.6: Identify how to record and report on
implemented risk controls
Refer to
Case study: Implemented risk controls
.
Case study: Implemented risk controls
Organisation ABC has been working with a new manufacturing plant for three months; an
initial hazard and risk assessment was carried out when the plant was installed and made
ready for workers to use. The manager must now check on the implemented risk controls to
see how these are working.
The following information has been gained:
Page 16 of 22
•
Plant training:
Workers have been trained to operate the plant according to their job
roles and to use personal protective equipment; three appointed workers have been trained
to perform maintenance duties.
•
Maintenance and cleaning of plant:
All workers have been given instructions for
regular cleaning of plant that they use; when maintenance is required, they must seek one
of the workers trained to carry out maintenance tasks. This can sometimes hold-up work
production if any of the workers are absent or unable to attend immediately.
•
Specific control measures:
The plant requires guards to minimise the noise that is
emitted from certain functions; these are removable barriers which allow access into a plant
for maintenance and cleaning. It has been noted that on several occasions, the guarding has
not been put back in place, and the plant has been operated in this condition for one or
more days.
Create a short report (1 x A4 page) that identifies the progress of the implemented risk
controls for Organisation ABC. For this activity, you may use a suitable template, create your
own using MS Word or similar and attach a copy to this workbook referencing the activity
number.
Feedback
Answers may vary in wording, but must identify the following information:
•
Plant training has been given to all workers; however, maintenance training has only been
provided to three workers, and this can hold up work production when their assistance is
required.
•
Sound-proof guarding is removed when maintenance and cleaning occur; this is not always
put back in place, causing noise hazards.
Reports must be written objectively (without bias or personal opinion).
Feedback: Topic 4
Activity 4.1: Identify types of plant requiring registration and
tasks requiring operator licensing
1.Provide three examples of plant requiring registration.
Feedback
Answers may vary but must identify three examples of plant requiring registration; this may include:
•
pressure equipment
•
gas cylinders
Page 17 of 22
•
tower cranes
•
mobile cranes with a rated capacity greater than 10 tonnes
•
lifts, escalators and moving walkways
•
prefabricated scaffolding
•
vehicle hoists
•
some amusement devices
•
building maintenance units
•
concrete placing booms.
2.According to work health and safety, list three tasks that require operator licensing and/or
certification in relation to one or two pieces of plant. You may need to perform research
to answer this question.
Feedback
Answers will vary depending on your choice of plant. For example, tasks relating to a tower crane
may include:
•
dismantling and assembling the crane
•
climbing to a significant height for operating the crane
•
lifting and controlling loads at height
•
lifting and controlling moving loads
•
operating the crane remotely.
Activity 4.2: Identify how to document registration, licensing
and certification requirements
Choose an item of plant and, record the registration, licensing and certification requirements
for the item of plant chosen.
Feedback
You must identify the relevant details as provided in the information given to them.
This will include the:
•
item of plant
•
registration requirements
•
licence required for worker operation
•
certification/training requirements.
Page 18 of 22
Your preview ends here
Eager to read complete document? Join bartleby learn and gain access to the full version
- Access to all documents
- Unlimited textbook solutions
- 24/7 expert homework help
Activity 4.3: Identify how to monitor and report compliance
with WHS regulatory requirements
1.Explain how you will need to monitor compliance with WHS regulatory requirements for
registration, licensing and certification.
Feedback
Answers to include the following points:
•
You will need to check on organisational plant registration and records, and employee
licensing and certification records to ensure these are current to organisational operations.
•
You will need to monitor employee or plant changes to ensure records are kept up-to-date,
and registration, licensing or certification requirements are maintained.
2.To report and communicate the plant registration, licensing and certification requirements
from
Activity 4.2: Identify how to document registration, licensing and certification
requirements,
create a simple one page (one side of A4) fact sheet.
For this activity, you may use a suitable template, create your own using MS Word or
similar and attach a copy to this workbook referencing the activity number.
Feedback
You must create and attach a fact sheet that explains the registration, licensing and certification
requirements of the item of plant from Activity 4.2.
This must be clear and logical in format and content, and be legible to read. The fact sheet must
provide accurate details, as sourced from your original information.
For example:
Vehicle Hoist
Registration
Design
The initial design of the vehicle hoist must be
registered with the relevant State/Territory regulator.
The owner of a vehicle hoist must ensure that its
design has been registered – usually indicated by the
installation of a placard on the hoist.
Item
Not required in NSW
Licencing
Not applicable
Certification
Regular inspection by a competent person is required to ensure the
vehicle hoist remains fit for purpose (as per AS2550)
Page 19 of 22
Feedback: Topic 5
Activity 5.1: Identify WHS-related training needs and
identify skill gaps
1.For one item of plant that is used in your business industry, research and identify the WHS
training requirements for using this and the applicable registration, licensing and
certification requirements.
Feedback
Answers will vary; however, you must identify the training requirements for your item of plant along
with the registration, licensing and certification needs.
For example:
Forklift:
•
Forklifts are used in a wide variety of workplaces and remain one of the major sources of
workplace injury. WHS Legislation requires that any person who is required to drive a forklift
must hold a High-Risk Licence of the appropriate class (LF or LO).
•
Forklift licences are nationally recognised and last for 5 years.
•
Forklift licence training is carried out by a registered training organisation.
2.With reference to question one, identify a comparable item of plant, for example, a higher-
grade model or a different manufacturer's model, and determine any skills gaps and
training needs that may apply. Provide a short summary report to record these needs.
Feedback
Answers will vary; you must identify any skills gaps or training requirements from comparing the
second item of plant against that detailed in your answer to question one.
Responses will typically include a reference to improvements in technology or the incorporation of
computerisation in some plant.
For example:
At my workplace, the forklift in operation was very old. It had a gas-powered engine with the
heavy cylinder on the back above the counterweight. The seat was torn and loos in its
mounts, and there was no seatbelt. The forks lifted up and down, and the mast had some
capacity to tile back and forward.
Page 20 of 22
The replacement forklift is diesel-powered which meant different refuelling procedures. It is
fitted with a seatbelt which locks out the ignition, preventing it from starting unless the
operator has the seatbelt connected.
The forks go up and down, and the mast tilts back and forward, though both movements are
considerably faster than on the old forklift. The forks also move sideways on the headboard
to allow easier and more accurate placement of pallets.
The new features of the forklift presented as gaps in existing worker knowledge and required
retraining. Licences were still valid, though the specific operational aspects of the new forklift
needed to be highlighted and workers trained.
Activity 5.2: Identify how to ensure training is undertaken
and completed
1.How can you make sure that training related to plant is carried out?
Feedback
Your responses could include:
•
You should plan training, making sure you prioritise needs (training should support workers'
needs and work production).
•
You should request and obtain a training budget (training must be affordable and agreed
with management).
•
Organise and agree on training schedules (this must be communicated to all parties).
•
Prepare for training (such as providing training details and arrangements, producing
itineraries and training materials, and liaising with trainers).
2.From your own thinking, suggest three ways you can maintain training records to meet
WHS and organisational requirements.
Feedback
Answers may vary but must suggest three suitable ways to maintain training records; this may
include:
•
applying data protection and security to protect workers' personal details
•
using a logical storing/filing system, so records are easily identifiable
•
using a consistent format to record information in training records
•
retaining records for the required period of time (for example, five or seven years).
Page 21 of 22
Your preview ends here
Eager to read complete document? Join bartleby learn and gain access to the full version
- Access to all documents
- Unlimited textbook solutions
- 24/7 expert homework help
Image attributions
Image
Page #
Attribution
Cover
1
© Getty Images copied under licence
Credit: WhataWin Creative #:
1185282377
Page 22 of 22
Your preview ends here
Eager to read complete document? Join bartleby learn and gain access to the full version
- Access to all documents
- Unlimited textbook solutions
- 24/7 expert homework help
Related Documents
Recommended textbooks for you
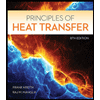
Principles of Heat Transfer (Activate Learning wi...
Mechanical Engineering
ISBN:9781305387102
Author:Kreith, Frank; Manglik, Raj M.
Publisher:Cengage Learning
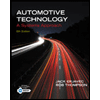
Automotive Technology: A Systems Approach (MindTa...
Mechanical Engineering
ISBN:9781133612315
Author:Jack Erjavec, Rob Thompson
Publisher:Cengage Learning
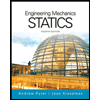
International Edition---engineering Mechanics: St...
Mechanical Engineering
ISBN:9781305501607
Author:Andrew Pytel And Jaan Kiusalaas
Publisher:CENGAGE L
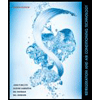
Refrigeration and Air Conditioning Technology (Mi...
Mechanical Engineering
ISBN:9781305578296
Author:John Tomczyk, Eugene Silberstein, Bill Whitman, Bill Johnson
Publisher:Cengage Learning
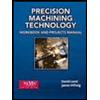
Precision Machining Technology (MindTap Course Li...
Mechanical Engineering
ISBN:9781285444543
Author:Peter J. Hoffman, Eric S. Hopewell, Brian Janes
Publisher:Cengage Learning
Recommended textbooks for you
- Principles of Heat Transfer (Activate Learning wi...Mechanical EngineeringISBN:9781305387102Author:Kreith, Frank; Manglik, Raj M.Publisher:Cengage LearningAutomotive Technology: A Systems Approach (MindTa...Mechanical EngineeringISBN:9781133612315Author:Jack Erjavec, Rob ThompsonPublisher:Cengage LearningInternational Edition---engineering Mechanics: St...Mechanical EngineeringISBN:9781305501607Author:Andrew Pytel And Jaan KiusalaasPublisher:CENGAGE L
- Refrigeration and Air Conditioning Technology (Mi...Mechanical EngineeringISBN:9781305578296Author:John Tomczyk, Eugene Silberstein, Bill Whitman, Bill JohnsonPublisher:Cengage LearningPrecision Machining Technology (MindTap Course Li...Mechanical EngineeringISBN:9781285444543Author:Peter J. Hoffman, Eric S. Hopewell, Brian JanesPublisher:Cengage Learning
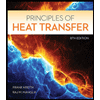
Principles of Heat Transfer (Activate Learning wi...
Mechanical Engineering
ISBN:9781305387102
Author:Kreith, Frank; Manglik, Raj M.
Publisher:Cengage Learning
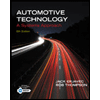
Automotive Technology: A Systems Approach (MindTa...
Mechanical Engineering
ISBN:9781133612315
Author:Jack Erjavec, Rob Thompson
Publisher:Cengage Learning
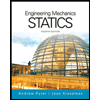
International Edition---engineering Mechanics: St...
Mechanical Engineering
ISBN:9781305501607
Author:Andrew Pytel And Jaan Kiusalaas
Publisher:CENGAGE L
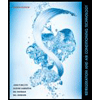
Refrigeration and Air Conditioning Technology (Mi...
Mechanical Engineering
ISBN:9781305578296
Author:John Tomczyk, Eugene Silberstein, Bill Whitman, Bill Johnson
Publisher:Cengage Learning
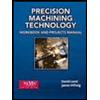
Precision Machining Technology (MindTap Course Li...
Mechanical Engineering
ISBN:9781285444543
Author:Peter J. Hoffman, Eric S. Hopewell, Brian Janes
Publisher:Cengage Learning