ENME317_Lab_2_Tension_Test_Updated
pdf
keyboard_arrow_up
School
University of California, Los Angeles *
*We aren’t endorsed by this school
Course
ME439
Subject
Mechanical Engineering
Date
Nov 24, 2024
Type
Pages
9
Uploaded by ProfKnowledge26820
S
CHULICH
S
CHOOL OF
E
NGINEERING
Department of Mechanical and Manufacturing Engineering
ENME317
M
ECHANICS OF
D
EFORMABLE
S
OLIDS
I
L
ABORATORY
#2:
T
ENSION
T
EST
I
NTRODUCTION AND
O
BJECTIVES
:
The term tension test is usually taken to refer to a test in which a prepared specimen is
subjected to gradually increasing uniaxial (along one axis) load until failure occurs. In the test, a
sample of material to be tested is placed between the grips of a load frame that pulls the
sample apart.
During the load application, the load, and the corresponding elongation of the
sample in a direction parallel to the applied load are recorded.
A tension test is the most fundamental test conducted in stress analysis since its results are
critical in mechanical component design.
That is, the load-elongation results can be analyzed to
determine the mechanical properties, such as the strength and stiffness, of the material being
tested.
In fact, tension test procedures have been standardized so that the results obtained for
different materials, from different laboratories can be compared.
The American Society of
Testing and Materials (ASTM) provides details of tension testing procedures in their standard
ASTM E8.
The objectives of this lab are to gain experience with conducting tension tests and analyzing the
results to determine the mechanical behavior of three different materials.
B
ACKGROUND
:
T
HE
S
TRESS
-S
TRAIN
C
URVE AND THE
M
ECHANICAL
P
ROPERTIES OF
M
ATERIALS
:
The tension test will give us a force versus displacement (elongation) curve for the specimen
tested.
The average normal true stress in an axially loaded member (ie. The lab sample) as the
load P increases can determined from:
,
(1)
where A is the cross-sectional area of the member at load level P.
Although the area A changes
with the test, if the deformations within the sample are small, engineering stress is often used.
Engineering stress references the initial cross-sectional area, A
o
and it is defined by:
.
(2)
P
A
s
=
0
P
A
s
=
Engineering stress therefore changes only with the applied load.
At any given load P, the
elongation of the sample from its initial length,
D
l
can be calculated using:
,
(3)
where
l
o
is the initial gauge length and
l
is the gauge length at load level P.
At any given load level P, the average normal engineering strain,
e
in the loading direction can
be found by dividing original length of the sample, or:
.
(4)
The plot of the stress vs. strain, as defined by Eqns. (2) an (4) is called the engineering stress-
strain curve of the material being tested.
Different materials exhibit different stress-strain curves.
Ductile materials are those materials
that undergo significant permanent deformations before failure.
A typical stress strain curve
for a ductile material is shown below.
Figure 1:
Engineering Stress-Strain Curves for a ductile material (adapted from Hibbeler)
There are four main regions of the engineering stress strain curve.
These regions are labelled in
Figure 1, and described below.
o
D
=
-
l
l
l
o
D
e
=
l
l
Region 1:
Elastic Region:
•
Sample returns to its original shape after load is removed.
•
Linearly Elastic Behavior (material is linear in the elastic region)
•
Hooke’s Law:
relation between stress and strain in the elastic region:
•
E: “Young’s Modulus” / “Elastic Modulus”/ “Modulus of Elasticity”
Ø
Slope of
s
-
e
curve in the elastic region
Ø
It is a material constant
Ø
Same units as stress (Pa or psi)
Region 2:
Yielding:
•
Elastic region continued until the yield stress,
s
y
, is reached.
•
Plateau in plot represents a region where the material slips, ie with no increase
in load, the strain increases.
•
If load is removed after the yield stress is reached, the sample will NOT return to
its original configuration.
The deformation is called plastic deformation.
Region 3:
Strain Hardening:
•
Slippage stops and further load can be applied (curve rises but becomes flatter)
•
Unloading along linear line parallel to the elastic curve.
•
Reloading – yields at a value greater than original yield stress
•
Cross-sectional area decreases uniformly.
•
Strain hardening continues until the ultimate tensile strength,
s
U
is reached.
Region 4:
Necking:
•
Cross-sectional area decreases in a localized region
•
Smaller area can only carry a decreasing load (downward turn)
•
s
B
= stress level when fracture (Breaking) occurs in the necked region.
Some materials, such as aluminum, do not exhibit a well-defined yield limit.
In such cases, the
0.2% offset method, as depicted in Figure 2 below is used to define the yield strength.
E
s
e
=
Your preview ends here
Eager to read complete document? Join bartleby learn and gain access to the full version
- Access to all documents
- Unlimited textbook solutions
- 24/7 expert homework help
Figure 2:
0.2% Offset Method for Determining Yield Strength.
Brittle materials such as cast iron, glass, or stone do not exhibit significant plastic deformation
prior to fracturing.
A typical stress-strain curve for a brittle material is shown in Figure 3 below.
Figure 3:
Typical Stress-Strain Curve of a Brittle Material
The percentage that a sample elongates prior to fracture is a measurement of the ductility of
the sample.
It can be calculated as:
As a reference, a ductile structural steel has a percentage elongation of around 20%.
B
o
o
% Elongation
x100%
é
ù
-
=
ê
ú
ë
û
l
l
l
E
QUIPMENT
:
Load Frame:
In this lab, tensile tests will be preformed on a Tinius Olsen Model 25 ST universal material
testing machine that is shown below in Figure 4. This electromechanical device has a maximum
load capacity of 25kN and can be operated manually on the attached panel, or remotely using
the Horizon software suite. The associated software, Horizon, will be used to set the test
parameters and collect data. To apply the load, the crosshead pulls up on the sample that is
gripped to the stationary frame base.
The load is recorded along with the displacement of the
crosshead.
It should be noted that although the crosshead displacement is used as a measure
of sample elongation, it is not an exact representation since the stiffness of the machine will
affect the results.
An attempt has been made to isolate the samples stiffness from the
machines in the Horizon software, but associated errors in the elastic modulus may still be
present.
Figure 4: Apparatus Diagram
Samples:
Three different materials, and therefore three different samples will be tested. The three
materials to be tested are designated by the American Iron and Steel Institute (AISI) as: AISI
1018 hot rolled steel (low carbon steel), AISI 1074 Hot Rolled (medium carbon steel), and AISI
6061-T6 (Aluminum).
Figure 5 shows a drawing of the samples to be tested.
These samples have been designed
roughly in accordance with ASTM E8. It should be noted that the area is reduced in the middle
of the sample.
This is to ensure that the samples will fail in this location, where the stress field
is uniform, and not influenced by the grips. WARNING: the samples may have sharp edges, be
careful not to cut yourself or others.
Figure 5: Sample Drawing
P
ROCEDURE
:
SAFETY FIRST!
Keep clear of the machine while tests are running
, or any time the crosshead is moving. Using
the Horizon software interface, there is a no indicator sound while the machine is moving - you
must
communicate with your group so that everyone is aware when the crosshead is moving.
You will know when the test is complete, and the machine will automatically stop. In the event
of a problem, press the red safety stop button on the base of the machine. This is a twist-on
switch (clockwise) that cuts all power to the frame. Before running a test, ensure that this
switch is in the on position (extended).
There is risk of material debris being ejected from the samples during testing, so safety glasses
are required always during the lab. These will be provided however students can bring their
own protective eyewear if they wish, at the discretion of the lab supervisor.
1.5R
Your preview ends here
Eager to read complete document? Join bartleby learn and gain access to the full version
- Access to all documents
- Unlimited textbook solutions
- 24/7 expert homework help
P
ROCEDURE
CONT
’
D
:
The following steps should be executed during the lab.
1.
Mark the initial gauge length
ℓ
0
(as indicated on Figure 5) on the sample using the
marker provided.
2.
Measure the relevant dimensions of the tensile specimen using calipers and record
them in Table 1 below.
Table 1: Sample Dimensions
Dimensions [mm]
AISI 1018 (hot rolled)
low carbon steel
AISI 1074 (hot rolled)
medium carbon steel
6061-T6 Aluminium
Fillet radius (R)
14
12
14
Initial gauge length
ℓ
0
Width (W)
Thickness (T)
3.
Ensure no one is touching the controls before placing the sample between the grips and
securing it with 3/8” pins. It may be necessary to jog the crosshead up or down manually
so that the holes line up – this should be done by the person installing the sample. Keep
hands clear at all times while the crosshead is moving.
4.
Ensure that the sample is unloaded and zero the force and position values in the
Horizon software.
5.
Check the parameters for the test in the Horizon software, input geometry as necessary.
6.
Confirm that everyone in the group has protective eyewear on and is clear of the
machine, and perform the test by clicking start (play button next to test) in Horizon. The
load frame will pull the sample to failure and automatically shut off.
7.
Observe the Force - Position (load – elongation) diagram produced during the test by
the software.
Note how the curve changes prior to failure and record your observations
below.
Did the curve give you an indication that failure was about to occur?
Record
these observations in Table 2 below.
Table 2: Observations on the load-elongation plot during the test
AISI 1018 (hot rolled)
low carbon steel
AISI 1074 (hot rolled)
medium carbon steel
6061-T6 Aluminium
8.
When the test is over, output your data to a .csv file.
You may either save the file to a
USB stick or email it to yourself from the lab computer.
9.
Remove both pieces of the sample from the grips.
10.
Observe the failed faces of the test sample and record your observations below.
Specifically, is the fracture face flat?
Is it partially flat but some material is at an angle?
Record your observations in Table 3 below.
Table 2: Observations on the fracture surfaces
AISI 1018 (hot rolled)
low carbon steel
AISI 1074 (hot rolled)
medium carbon steel
6061-T6 Aluminium
11.
Put the two surfaces back together and measure the gauge length at fracture,
ℓ
B
.
ℓ
B
= _________________________ mm
12.
Repeat Steps 1-11 for each sample that your group is testing.
Guidelines for the Preparation of the Laboratory Writeup
Objectives and Procedure
1.
Provide a brief summary of the objectives of the lab and state briefly the procedure.
(max 6 sentences)
Results and Analysis of Results
2.
Include Tables 1-3 from above.
3.
Plot the engineering stress vs. engineering strain separately for each sample.
4.
From your stress-strain curve calculate the yield stress, the elastic modulus, the ultimate
tensile strength, and the percent elongation for each sample. Look in the available
literature for the above reported values. Calculate the percentage difference between
your values and those found in the literature. Present all of these results in the form of a
table.
5.
For each sample, indicate whether you believe that the material is ductile or brittle.
Base your answer on the stress-strain curve produced, your calculated percent
elongation and your observations of the appearance of the fracture faces and during the
test of each sample.
Conclusions
6.
Conclusions: Briefly (in maximum 6 sentences) state your major takeaways from this lab.
Your preview ends here
Eager to read complete document? Join bartleby learn and gain access to the full version
- Access to all documents
- Unlimited textbook solutions
- 24/7 expert homework help
Related Questions
This exercise requires showing the complete scanned strokes and procedures,
adding it to a pdf document with evidence of all the exercises and the honesty letter.
A Titanium specimen with a diameter of 0.8 [in] and 2.5 [in] in length is stretched in
uniaxial tension.
1. What is the maximum elongation (DI) of the material. If the deformation is
completely elastic?
2. What force is being applied
Consider the material properties S_UTS=1205 [MPa]; Sy= 1075 [MPa]; E= 100
[GPa]
in the following space write the values found as follows, do not forget the units
(-0.5 pts if 4d units do not appear):
]; F=
[];
arrow_forward
Which of these statements are correct?
arrow_forward
3. Two specimens with the same dimensions and made from two different materials, A and B, were subjected to tensile testing. The percentage
reduction in the area of the specimen made of material 'A' was calculated 3 times that of the specimen made of material B. In this case,
O A lthe ductility of material A and B is equal
O Bthe material A is brittle and material B is ductile
O Cthe material B is more ductile than material A
O D nhe material A is more ductile than material B
1.
20
O Aramak için buraya yazıin
arrow_forward
QUESTION
The following data were obtained during a tension test of a low carbon steel specimen
having a gauge length of 100 mm.
At the point where the stress strain curve deviated from linearity, the load was 35KN, the
gauge length was 102.5 mm and the diameter of the specimen was 1.6 mm. Before necking
began, loads of 45 KN and 55 KN produced gauge lengths of 103.4 mm and 107.7 mm
respectively.
Calculate
(a) The Modulus of elasticity
(b) The Strainhardening exponent
arrow_forward
Hi can you please help me with the attached question?
arrow_forward
please solve part b, this is past paper and just iam studying, mechanical engineering
arrow_forward
The answer is one of the options below please solve carefully and circle the correct option Please write clear .
arrow_forward
6. State your answers to the following questions.Strain Gauge represents the deformation of a material through a change in resistance. If so, explain how temperature will affect the strain gauge in the experimental environment.①:In this experiment, the Strain Gauge measures the strain in micro units. Explain one possible error factor when applying a load by hanging a weight on the material with the strain gauge attached. (Hint: It is easy to shake by hanging the weight using a thread)①:
arrow_forward
Can someone please help me to correctly solve all the following parts of this question. Thank you!
arrow_forward
Detailed steps
arrow_forward
Flag question
You have been given the following test sample data following mechanical testing of 15 test pieces of a modified Alumina.
What is the Weibull modulus of this material?
Would you advise the use of this material over one with a Weibull Modulus of 19.6 and a mean failure stress of 270 MPa, if you
anticipate that the peak stress on the material could be 255 MPa?
Sample
1
2
3
4
5
6
7
8
9
10
11
12
13
14
15
Select one or more:
Failure Stress (MPa)
297
293
270
300
260
286
265
295
4
293
280
288
263
290
298
275
arrow_forward
Using the four-point bending tool, discuss how measurements of transverse
strain using DIC and compare with those from the strain gauge attached at
the centre top of the specimen. In your answer, include the following:
a. A short explanation of how each of the strain measurement techniques
works.
(4 marks)
b. A description of the methodology you have used to make the data that
you discussed from each technique as comparable as possible.
(6 marks)
c. A set of figures (images, graphs and/or tables as necessary) with
appropriate captions demonstrating the comparability of data extracted
from the two strain measurement methods. This should include at least
three different applied loads.
(10 marks)
d. A brief description of the findings.
(5 marks)
arrow_forward
Figure 1 shows the tensile testing results for different materials. All specimens have an initial
diameter of 12 mm and an initial gauge length of 50 mm.
300
250
Low carbon steel
Network polymer
200
Crystalline polymer
150
Amorphous polymer
100
50
5
10
15
20
25
30
Strain (%)
Figure 1: Stress-strain curve
b. Determine the following parameters for each material:
• the tensile strength
the 0.2% offset yield strength
the modulus of elasticity
• the ductility
Stress (MPa)
LO
arrow_forward
The following curve is a result of a tensile test. The gauge length was 2 in, and the specimen diameter was 0.505 in The fracture area was round with a diameter of 0.391 in. Remember to com
20000
Force (pounds force)
15000
10000
5000
0
16. The yield strength is
0 0.2%
O 80,000 pl
O 12.000 p
060,000 pl
85,000 p
0.1
0.2
Extension (inch)
0.3
0.4
arrow_forward
1. A tensile test was conducted on a metal "505" specimen and the following stress-strain curves
were generated, both curves generated from the same set of data. Use the graphs to fill in the
mechanical properties of the material tested in the box below. Don't forget units!
Stress vs Strain
Stress, psi
Stress, psi
80000
70000
60000
50000
40000
30000
20000
10000
0
0.00
80000
70000
60000
50000
40000
30000
20000
10000
0.02
0
0.000 0.002
0.04
0.004
0.06
0.006
0.08
0.10
Strain
Stress vs Strain
0.008
0.12
Elastic Modulus, E:
0.2% Offset Yield Strength, oo:
Tensile Strength, ou:
Breaking Strength, of:
% Elongation:
0.14
0.010 0.012 0.014
Strain
0.16
0.18
0.016 0.018
0.20
0.020
arrow_forward
(d) Following experimental data (TableQ1b) has obtained from the
torsion test for the specimen dimension given in Table Q1a.
Determine the material of a circular bar. (Take the material
Poisson's Ratio as 0.32)
Table Q1a Specimen Dimensions
Dimensions
Material
Diameter (mm)
6
Length (mm)
77.15
TableQ1b Experimental Results from Torsion test
Angular Deflection
Degree
Radian
Torque/Nm
0.5
0.008727
0.06
1
0.017453
0.47
1.5
0.02618
0.76
2
0.034907
1.01
2.5
0.043633
1.32
3
0.05236
1.65
3.5
0.061087
1.99
4
0.069813
2.32
4.5
0.07854
2.66
5
0.087267
3.00
5.5
0.095993
3.33
6
0.10472
3.64
10
0.174533
5.92
20
0.349066
7.74
30
0.523599
8.07
40
0.698132
8.17
50
0.872665
7.93
60
1.047198
8.10
70
1.221731
8.2
80
1.396264
8.4
90
1.570797
8.24
100
1.74533
8.7
110
1.919863
8.7
120
2.094396
8.7
180
3.141594
9.02
240
4.188792
9.11
300
5.23599
9.48
360
6.283188
9.51
420
7.330386
9.71
arrow_forward
SEE MORE QUESTIONS
Recommended textbooks for you
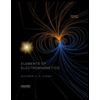
Elements Of Electromagnetics
Mechanical Engineering
ISBN:9780190698614
Author:Sadiku, Matthew N. O.
Publisher:Oxford University Press
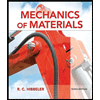
Mechanics of Materials (10th Edition)
Mechanical Engineering
ISBN:9780134319650
Author:Russell C. Hibbeler
Publisher:PEARSON
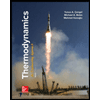
Thermodynamics: An Engineering Approach
Mechanical Engineering
ISBN:9781259822674
Author:Yunus A. Cengel Dr., Michael A. Boles
Publisher:McGraw-Hill Education
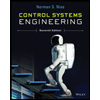
Control Systems Engineering
Mechanical Engineering
ISBN:9781118170519
Author:Norman S. Nise
Publisher:WILEY
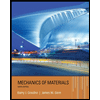
Mechanics of Materials (MindTap Course List)
Mechanical Engineering
ISBN:9781337093347
Author:Barry J. Goodno, James M. Gere
Publisher:Cengage Learning
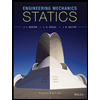
Engineering Mechanics: Statics
Mechanical Engineering
ISBN:9781118807330
Author:James L. Meriam, L. G. Kraige, J. N. Bolton
Publisher:WILEY
Related Questions
- This exercise requires showing the complete scanned strokes and procedures, adding it to a pdf document with evidence of all the exercises and the honesty letter. A Titanium specimen with a diameter of 0.8 [in] and 2.5 [in] in length is stretched in uniaxial tension. 1. What is the maximum elongation (DI) of the material. If the deformation is completely elastic? 2. What force is being applied Consider the material properties S_UTS=1205 [MPa]; Sy= 1075 [MPa]; E= 100 [GPa] in the following space write the values found as follows, do not forget the units (-0.5 pts if 4d units do not appear): ]; F= [];arrow_forwardWhich of these statements are correct?arrow_forward3. Two specimens with the same dimensions and made from two different materials, A and B, were subjected to tensile testing. The percentage reduction in the area of the specimen made of material 'A' was calculated 3 times that of the specimen made of material B. In this case, O A lthe ductility of material A and B is equal O Bthe material A is brittle and material B is ductile O Cthe material B is more ductile than material A O D nhe material A is more ductile than material B 1. 20 O Aramak için buraya yazıinarrow_forward
- QUESTION The following data were obtained during a tension test of a low carbon steel specimen having a gauge length of 100 mm. At the point where the stress strain curve deviated from linearity, the load was 35KN, the gauge length was 102.5 mm and the diameter of the specimen was 1.6 mm. Before necking began, loads of 45 KN and 55 KN produced gauge lengths of 103.4 mm and 107.7 mm respectively. Calculate (a) The Modulus of elasticity (b) The Strainhardening exponentarrow_forwardHi can you please help me with the attached question?arrow_forwardplease solve part b, this is past paper and just iam studying, mechanical engineeringarrow_forward
- The answer is one of the options below please solve carefully and circle the correct option Please write clear .arrow_forward6. State your answers to the following questions.Strain Gauge represents the deformation of a material through a change in resistance. If so, explain how temperature will affect the strain gauge in the experimental environment.①:In this experiment, the Strain Gauge measures the strain in micro units. Explain one possible error factor when applying a load by hanging a weight on the material with the strain gauge attached. (Hint: It is easy to shake by hanging the weight using a thread)①:arrow_forwardCan someone please help me to correctly solve all the following parts of this question. Thank you!arrow_forward
- Detailed stepsarrow_forwardFlag question You have been given the following test sample data following mechanical testing of 15 test pieces of a modified Alumina. What is the Weibull modulus of this material? Would you advise the use of this material over one with a Weibull Modulus of 19.6 and a mean failure stress of 270 MPa, if you anticipate that the peak stress on the material could be 255 MPa? Sample 1 2 3 4 5 6 7 8 9 10 11 12 13 14 15 Select one or more: Failure Stress (MPa) 297 293 270 300 260 286 265 295 4 293 280 288 263 290 298 275arrow_forwardUsing the four-point bending tool, discuss how measurements of transverse strain using DIC and compare with those from the strain gauge attached at the centre top of the specimen. In your answer, include the following: a. A short explanation of how each of the strain measurement techniques works. (4 marks) b. A description of the methodology you have used to make the data that you discussed from each technique as comparable as possible. (6 marks) c. A set of figures (images, graphs and/or tables as necessary) with appropriate captions demonstrating the comparability of data extracted from the two strain measurement methods. This should include at least three different applied loads. (10 marks) d. A brief description of the findings. (5 marks)arrow_forward
arrow_back_ios
SEE MORE QUESTIONS
arrow_forward_ios
Recommended textbooks for you
- Elements Of ElectromagneticsMechanical EngineeringISBN:9780190698614Author:Sadiku, Matthew N. O.Publisher:Oxford University PressMechanics of Materials (10th Edition)Mechanical EngineeringISBN:9780134319650Author:Russell C. HibbelerPublisher:PEARSONThermodynamics: An Engineering ApproachMechanical EngineeringISBN:9781259822674Author:Yunus A. Cengel Dr., Michael A. BolesPublisher:McGraw-Hill Education
- Control Systems EngineeringMechanical EngineeringISBN:9781118170519Author:Norman S. NisePublisher:WILEYMechanics of Materials (MindTap Course List)Mechanical EngineeringISBN:9781337093347Author:Barry J. Goodno, James M. GerePublisher:Cengage LearningEngineering Mechanics: StaticsMechanical EngineeringISBN:9781118807330Author:James L. Meriam, L. G. Kraige, J. N. BoltonPublisher:WILEY
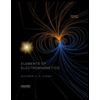
Elements Of Electromagnetics
Mechanical Engineering
ISBN:9780190698614
Author:Sadiku, Matthew N. O.
Publisher:Oxford University Press
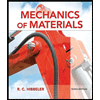
Mechanics of Materials (10th Edition)
Mechanical Engineering
ISBN:9780134319650
Author:Russell C. Hibbeler
Publisher:PEARSON
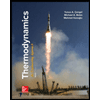
Thermodynamics: An Engineering Approach
Mechanical Engineering
ISBN:9781259822674
Author:Yunus A. Cengel Dr., Michael A. Boles
Publisher:McGraw-Hill Education
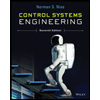
Control Systems Engineering
Mechanical Engineering
ISBN:9781118170519
Author:Norman S. Nise
Publisher:WILEY
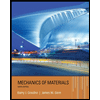
Mechanics of Materials (MindTap Course List)
Mechanical Engineering
ISBN:9781337093347
Author:Barry J. Goodno, James M. Gere
Publisher:Cengage Learning
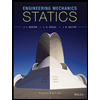
Engineering Mechanics: Statics
Mechanical Engineering
ISBN:9781118807330
Author:James L. Meriam, L. G. Kraige, J. N. Bolton
Publisher:WILEY