HELP_MEM05015__100__.docx
pdf
keyboard_arrow_up
School
Swinburne University of Technology *
*We aren’t endorsed by this school
Course
ANALYTICAL
Subject
Mechanical Engineering
Date
Nov 24, 2024
Type
Pages
57
Uploaded by ajayinder2509
WORKSHEET
MEM05015
Weld using manual metal arc welding
process
Baxter Institute| MEM05015
Weld using manual metal arc welding
process
Student Name:
___________________________________
Student ID:
______________________________________
P a g e
|
2
MEM05015
Worksheet v1.1
Baxter Institute| MEM05015
Weld using manual metal arc welding
process
Learning Activity
1
-
Review Question
SECTION
1
–
WHAT IS MANUAL METAL ARC WELDING?
1.
What is
Describe
manual metal arc welding
(MMAW)
?
Manual metal arc welding is a type of welding that uses a welding power supply to create an electric arc
between an electrode and the base material to melt the metals at the welding point. They can use either
direct current (DC+/-) or alternating (AC) current, and the electrode is consumed.
2.
List some manual metal arc welding machine manufactures?
Some of the leading manufactures are listed below:
CIGWELD
LINCLON
MILLER
FORONIUS
BOC
3.
What things should be taken into consideration when choosing amperage for a MMAW
machine?
As a rule, on manual metal arc welding machines voltage is set and not adjustable, where
amperage can be adjusted. Things to be taken into consideration when selecting amperage are:
•Welding position
•Material thickness
•Type of material, low alloy, stainless steel etc
•Electrode diameter
•Manufacture’s recommendations (including AC/DC+/-)
•Type of electrode
4.
List some functions of the flux?
Flux is the coating of core metal that forms an electrode, the functions of the flux are:
•Protect the molten metal from atmospheric contamination
•Form a protective slag coating during the cooling process
•Control the chemical and mechanical properties by replacing lost elements, adding elements as
required
•Control arc stability, penetration, and surface finish of the weld
•Act as a cleanser by dissolving some surface rust of other impurities
•Control the weld bead shape
P a g e
|
3
MEM05015
Worksheet v1.1
Your preview ends here
Eager to read complete document? Join bartleby learn and gain access to the full version
- Access to all documents
- Unlimited textbook solutions
- 24/7 expert homework help
Baxter Institute| MEM05015
Weld using manual metal arc welding
process
5.
List some factors that may affect your choice when choosing an electrode?
Electrode selection also depends not only on the type of material, but also the Weld-ability
group number. In particular when welding stainless steel, it is important that a compatible
Weld-ability group number is used to weld the metal together.
You chose the size of the electrode depending on certain factors that affect the final weld:
(amperage takes in similar considerations)
-Plate thickness
-Material thickness/type
-Weld preparation
-Welding position
6.
Where should
an
the
electrode be stored
according to safety pro
safely
cedure
?
Electrode storage is critical to the proper operation of the electrode. You should never open a
packet of electrodes until you are ready to use them. In particular, once you open a packet of
low hydrogen electrodes you should place them in a hot box for approximately 1 hour at 100
°
c
to ensure that there is no moisture in the electrodes.
P a g e
|
4
MEM05015
Worksheet v1.1
Baxter Institute| MEM05015
Weld using manual metal arc welding
process
Learning Activity
2
– Review Question
s
SECTION
2
–
WELDING MACHINE SETUP
1.
What
possible
currents can be used for a welding machine?
You have three possible combinations:
1.Alternating current
2.Direct current electrode positive (reverse polarity)
3.Direct current electrode negative (straight polarity)
The terms "straight" and "reverse" polarity are used around the shop. They may also be
expressed as "electrode-negative" and "electrode-positive" polarity.
2.
Draw
Sketch
the MMAW process
?
P a g e
|
5
MEM05015
Worksheet v1.1
Baxter Institute| MEM05015
Weld using manual metal arc welding
process
P a g e
|
6
MEM05015
Worksheet v1.1
Your preview ends here
Eager to read complete document? Join bartleby learn and gain access to the full version
- Access to all documents
- Unlimited textbook solutions
- 24/7 expert homework help
Baxter Institute| MEM05015
Weld using manual metal arc welding
process
Learning Activity
3
– Review Question
s
SECTION
3
–
MATERIAL PREPARATION AND JOINT
PREPARATION
1.
What should we do to
How can you
ensure that the selected
welding
material
s
are
is
clean?
After selecting the material that you require for welding, ensure that the material is clean.
Remove all oil, grease, dirt, paint, scale, etc.; failure to remove these contaminants may result in
arc instability or contaminated welds. This also results in costly repairs and time overruns.
The metal can be prepared by the following processes:
-Grinding
-Gouging
-Filing
-Machining
-Nibblers
Etc
The key is to ensure that after you have done the preparation, there is no contaminates left on
the metal before you start tacking and welding.
2.
Which processes can be used for preparing metal
for welding
?
In the process of selecting a suitable butt weld joint preparation for thick plate (greater
than 1 in), the most apparent consideration is unquestionably the joint economy – the practice
of minimizing the volume of weld metal required to fill the joint. This desire to keep costs low is
certainly understandable, as a fabricator would not want to deposit any more weld metal than
is absolutely necessary so that profitability can be assured.
3.
According to
AS/NZS 1554 – Part 1 Welding
of Steel Structures (Table 6.2.2)
What is the
required
alignment for metal components
according to
AS/NZS 1554 – Part 1
Welding
of Steel Structures (Table 6.2.2)
welding standard AS1554.1:2011
?
Clause 5.2.2 of AS1554.1 state that plates of equal thickness shall not be out of alignment
by the lesser of: a)3mm, or b)10% of the thickness of the plates, unless otherwise approved by
the principal.
P a g e
|
7
MEM05015
Worksheet v1.1
Baxter Institute| MEM05015
Weld using manual metal arc welding
process
4.
What is the require
d
ment
of
the
filler metal when preparing material for
a
welding
process
?
The filler metal must be compatible with the parent metal, if not this may result in a weld
that is not up to the specifications as laid down in AS1554.1
_______________________________________________________________________
P a g e
|
8
MEM05015
Worksheet v1.1
Baxter Institute| MEM05015
Weld using manual metal arc welding
process
Learning Activity
4
–
Review Question
s
SECTION
4
–
TYPES OF WELDS
1.
Draw
a
fillet weld and describe
its
elements
.
included
P a g e
|
9
MEM05015
Worksheet v1.1
Your preview ends here
Eager to read complete document? Join bartleby learn and gain access to the full version
- Access to all documents
- Unlimited textbook solutions
- 24/7 expert homework help
Baxter Institute| MEM05015
Weld using manual metal arc welding
process
Fillet welds are approximately triangular in shape and are defined by their leg length.
1.Toe
2.Weld metal
3.Weld face
4.Reinforcement
5.Weld zone
6.Root (of weld)
7.Parent metal
8.Depth
9.Heat affect zone (HAZ)
10.Design throat thickness
11.Leg length
•For all fillets welds shaped by plates placed at right angles, the throat thickness should be
approximately 70% of the leg length.
•For a fillet weld with a length of 10mm, the throat thickness should be 7mm.
P a g e
|
10
MEM05015
Worksheet v1.1
Baxter Institute| MEM05015
Weld using manual metal arc welding
process
2.
3.
4.
5.
6.
7.
8.
9.
10.
11.
12.
13.
14.
15.
16.
17.
18.
19.
20.
Draw
a
butt weld and describe
its
elements
included
P a g e
|
11
MEM05015
Worksheet v1.1
Baxter Institute| MEM05015
Weld using manual metal arc welding
process
A weld in which the metal lies substantially within the extension of the planes of the surfaces of
the parts being joined is known as a butt weld.
1.Toe
2.Weld metal
3.Weld face
4.Reinforcement
5.Weld zone
6.Root (of weld)
7.Parent metal
8.Depth of fusion
9.Heat affected zone (HAZ)
10.Design throat thickness
P a g e
|
12
MEM05015
Worksheet v1.1
Your preview ends here
Eager to read complete document? Join bartleby learn and gain access to the full version
- Access to all documents
- Unlimited textbook solutions
- 24/7 expert homework help
Baxter Institute| MEM05015
Weld using manual metal arc welding
process
The terms below are used to define the setup of a butt weld; the actual dimensions are
determined either by the engineering or are taken from the pre-defined weld preparation in
AS/NZS 1554 - Part 1: Welding of Steel Structures
P a g e
|
13
MEM05015
Worksheet v1.1
Baxter Institute| MEM05015
Weld using manual metal arc welding
process
P a g e
|
14
MEM05015
Worksheet v1.1
Baxter Institute| MEM05015
Weld using manual metal arc welding
process
Learning Activity
5
– Review Question
s
SECTION
5
–
DISTORTION
1.
What is
Define
distortion
and
list
? List
some
of
the common
types of distortion.
Distortion is a major problem when welding metal. Metals such as stainless steel tend to
distort at a rate 50% greater than steel. Distortion should be considered when welding, but
even more so welding metals such as stainless steel. The reason why stainless steels are more
susceptible is it has a greater thermal expansion and lower thermal conductivity than carbon
steels. Thinner material is more susceptible, as it has less stiffness.
Types of Distortion:
•
Transverse
•Longitudinal
•Angular
•Bowing
2.
How
c
w
an
ould
the
distortion
be
prevent
ed
ion be achieved
?
Distortion prevention is almost impossible to prevent completely all the time. It is a case
of distortion minimisation that you try to achieve. Adopting the following assembly techniques
will help to control distortion:
•
Pre-set parts so that welding distortion will achieve overall alignment and dimensional control with
minimum residual stress.
•Pre-bend joint edges to counteract distortion and achieve alignment and dimensional control with
minimum residual stress.
•Apply restraint during welding by using jigs and fixtures, flexible clamps, strong-backs and tack welding
but consider the risk of cracking which can be quite significant, especially for fully welded strong-backs.
•Use an approved procedure for welding and removal of welds for restraint techniques which may need
preheating to avoid forming imperfections in the component surface.
I
t is a matter of selecting the most appropriate method of reducing distortion to suit the task
that you have to perform.
3.
Briefly describe four types of distortion.
Transverse distortion
has contracting forces acting across the line of weld, and this will
pull the sections of parent metal towards each other.
Longitudinal distortion
occurs when the forces act along the length of the weld and will pull the
ends towards each other.
P a g e
|
15
MEM05015
Worksheet v1.1
Your preview ends here
Eager to read complete document? Join bartleby learn and gain access to the full version
- Access to all documents
- Unlimited textbook solutions
- 24/7 expert homework help
Baxter Institute| MEM05015
Weld using manual metal arc welding
process
Angular distortion
occurs when shrinkage forces about the longitudinal axis pull the two parts
towards the same plane.
Bowing distortion
is caused by a combination of transverse and longitudinal forces.
Learning Activity
6
– Review Question
s
SECTION
6
–
WELDING POSITIONS
1.
What
are
welding positions?
Welding positions are covered by AS 3545.
Welding positions indicate to the welder what position the job is to be welded in, whether is
flat, vertical, horizontal or overhead. With this information the welder can determine what
electrode, current and amperage they are going to use.
2.
List some welding positions
?
HORIZONTAL VERTICAL
PB
PF VERTICAL UP
FLAT
PA
HORIZONTAL
PC
PG VERTICAL DOWN
HORIZONTAL OVERHEAD
PC
OVERHEAD
PE
3.
What are possible
welding
positions for fillet welding?
Possible Fillet welding positions
Flat
Horizontal Vertical
Vertical Up/ Down
Overhead
P a g e
|
16
MEM05015
Worksheet v1.1
Baxter Institute| MEM05015
Weld using manual metal arc welding
process
Learning Activity 7
– Review Question
s
Section 7 – TYPES OF WELD DEFECTS
1.
What is weld defect? List some common form
s of
weld defects
A weld defect can be defined as an irregularity, discontinuity, imperfection, or inconsistency that
renders the welded object unsuitable for its intended use.
The integrity of welds is assured through Quality Control programs conducted by highly
educated or trained individuals such as Welding Engineers, Quality Control Engineers,
Metallurgical Technicians, Non-Destructive Test and Mechanical Test Engineers, and Certified
Welding Inspectors.
Some Common Forms are:
Undercutting
Misalignment
Overlap
Cracking
Porosity
2.
What
is
an
undercut
defect??
Undercutting is one of the more severe welding defects. It is essentially an unfilled groove along
the edge of the weld.
3.
What
are
an
undercut defect’s
possible
causes?
The causes are usually associated with incorrect electrode angles, incorrect weaving technique,
excessive current and travel speed. Undercutting can be avoided with careful attention to detail
during preparation of the weld and by improving the welding process. It can be repaired in most
cases by welding up the resultant groove with a smaller electrode.
4.
What is overlap defect??
The protrusion of weld metal beyond the weld toe or weld root. It is caused by poor
welding techniques and can generally be overcome by an improved weld procedure. The
overlap can be repaired by grinding off excess weld metal and surface grinding smoothly to the
base metal.
P a g e
|
17
MEM05015
Worksheet v1.1
Baxter Institute| MEM05015
Weld using manual metal arc welding
process
5.
What is porosity defect??
Porosity is a collective name describing cavities or pores caused by gas and non-metallic
material entrapment in molten metal during solidification. There are many causes which include
contamination, inadequate shielding, unstable arc, arc gap too short and poor welding
technique in general. Porosity can be minimised in many different ways – by the proper
selection of electrodes and/or filler materials, improved welding techniques, more attention to
the work area during weld preparation and a slower speed to allow gases time to escape.
6.
What is
a
welding crack
ing
defect??
Cracks and planar discontinuities are some of the most dangerous especially if they are subject
to fatigue loading conditions. There are several different type of cracks and none are desired.
They must be removed by grinding back or repaired by welding.
7.
What is
a
joint misalignment defect??
This type of geometric defect is generally caused by a setup/fit up problem, assembling parts to
be welded poorly, or trying to join plates of different thickness.
8.
What is
an
incomplete penetration defect??
Incomplete fusion or penetration is an internal planar discontinuity that is difficult to
detect and evaluate, and very dangerous. It occurs when the weld metal does not form a
cohesive bond with the base metal or when the weld metal does not extend into the base metal
to the required depth, resulting in insufficient throat thickness.
9.
How
c
w
ould
an incomplete penetration defect
the defect
be fixed??
These defects are usually caused by incorrect welding condition such as current too low,
insufficient preheating, welding speed too fast, incorrect edge preparation, short arc length,
insufficient electrode size or the arc was not in the centre of the seam. This type of defect can
only be repaired by grinding/gouging out the defective area and re-welding.
_______________________________________________________________________
?
P a g e
|
18
MEM05015
Worksheet v1.1
Your preview ends here
Eager to read complete document? Join bartleby learn and gain access to the full version
- Access to all documents
- Unlimited textbook solutions
- 24/7 expert homework help
Baxter Institute| MEM05015
Weld using manual metal arc welding
process
P a g e
|
19
MEM05015
Worksheet v1.1
Baxter Institute| MEM05015
Weld using manual metal arc welding
process
Learning Activity 8
– Review Question
s
Section 8 – TESTING FOR WELD DEFECTS
1.
What methods can detect internal
weld
defects?
Internal defects can be detected by two methods, destructive and non-destructive
testing.
Listed below are some of the common destructive and non-destructive testing methods.
Destructive Testing ___________________________________________Non-Destructive Testing
MacroVisual
Nick break__________________________________________________________________Radiographic
Fillet break ___________________________________________________________________Ultrasonic
Side bend_______________________________________________________________Magnetic particle
Root bend________________________________________________________________Liquid penetrant
2.
Name some method
s
of
used for
destructive testing?
Some methods used for Destructive testing:
1. Macro
2. Nick Break
3. Fillet Break
4. Side Bend
5. Root Bend
3.
Name some method
s used for
of
non-destructive testing?
Some methods for Non-Destructive Testing:
1. Visual
2. Radiography
3. Ultrasonic
4. Magnetic Particle
5. Liquid Penetration
P a g e
|
20
MEM05015
Worksheet v1.1
Baxter Institute| MEM05015
Weld using manual metal arc welding
process
SECTION 9
PRACTICAL LEARNING ACTIVITY
Practical Activity 1
– Horizontal/Vertical Fillet Welding
You are required to perform a weld using the below task sheet, and fill out the table with the
welding machine settings that you use to complete the task. All welds to conform to AS/NZS
1554.1:2011 GP.
All welds to conform to the latest standard (AS/NZS 1554 - Part 1: Welding of
Steel Structures), a copy of the Australian standards (AS/NZS 1554:1:2014 is available at your
campus).
Welding Procedure Sheet
Manufacturer:
Baxter Institute
Welding code
: 1554.1.2014
Material specification/Grade:
Mild Steel / GR300
To:
Location:
Workshop
Welding Process:
MMAW
Date qualified:
__/__/____
Welded by
: ____________
Welding position
:
2F
Material dimensions:
Welding consumables:
Plate thickness:
10
mm
Shielding gas:________
Flow Rate:________
Material heating:
Joint tolerances:
Pre-heat temperature
n/a
Interpass temperature
(max)
n/a
Check method
n/a
Joint Sketch
Run Sequence
Joint Details
Pre-qual. Joint #
F1
Table
E
3
Include
90
Weld run details
Welding parameters
Electrode/ Filler
Pass
no.
Size
Class
ɸ
mm
Filler Wire
Trade name
Voltage
Amperage
P
olarity
1
Initial cleaning: Inter-run cleaning
Wire brushing before and after(in-between runs)
Test / Requirements:
Visual
examination to specification as set out: TABLE
6.2.2
-General purpose
of AS/NZS 1554.1.2014
Measurement
Break fillet to check for
5
0
% root fusion
Fillet size
10
mm +2 -0
Distortion
0-5
P a g e
|
21
MEM05015
Worksheet v1.1
Your preview ends here
Eager to read complete document? Join bartleby learn and gain access to the full version
- Access to all documents
- Unlimited textbook solutions
- 24/7 expert homework help
Baxter Institute| MEM05015
Weld using manual metal arc welding
process
You are required to perform a weld according to the job instructions detailed in the welding procedure
specification (WPS) below. You must fill out the information for the welding machine settings and the
consumables used to complete the task.
Note, if applicable the weld should conform to the latest
standard (as specified in the WPS), a copy of the Australian standards is available at your campus.
Fill out the Welding Procedure Specification (WPS) above should your trainer pass the weld
For this practical learning activity you are required to use the following Arc welding Consumable:
Cigweld
3.2mm General Purpose (GP) Electrodes.
Welding Procedure Specification
Manufacturer: Baxter Institute
Welding
Standard:1554.1.2014
Material specification/Grade: Mild Steel/ G300
Welded by: ____________Date: __/__/____
Location:
Workshop
Welding Process:
MMAW
Welding position: 2F
Joint type: Tee
Material dimensions:
Welding consumables:
Plate thickness:
10mm
Plate Size:
25 x 180mm (Qtyx1)
50 x 180mm (Qtyx1)
Shielding Gas: N/A
Flow Rate: N/A
Material heating:
Joint tolerances:
Pre-heat temperature
N/A
Inter-pass temperature
(max)
N/A
Check method
N/A
Root face: N/A
Root gap: N/A
Joint Preparation Sketch
Run Sequence
Joint Details
1 Run
Table (Pre-qual Joint): E3
Joint Identification: F1
Include
: 90
Weld run details
Welding parameters
Electrode/ Filler
Polarity
Pass
no.
Side
Class
ɸ mm
Trade Name
Amperage Range
1
Initial cleaning: Wire Brush
Inter-run cleaning: Chip off flux and Wire brush before and after each run
Test / Requirements:
Visual
Examination to specification as set out: TABLE 6.2.2-General
purpose of AS/NZS 1554.1.2014
Measurement
Break fillet to check for 75% root fusion
Fillet size 6mm +2 -0
No Distortion
P a g e
|
22
MEM05015
Worksheet v1.1
Your preview ends here
Eager to read complete document? Join bartleby learn and gain access to the full version
- Access to all documents
- Unlimited textbook solutions
- 24/7 expert homework help
Baxter Institute| MEM05015
Weld using manual metal arc welding
process
Welding Procedure Sheet
Material:
Low Carbon Steel
To
Fabricator
Baxter Institute
Process
MMAW
Welding standard
AS/NZS 1554.1:2011
Edge preparation
Weld ability group#
250
Plate thickness
10mm
PQR #
1
Date qualified
Welded by
Revision
Date
Qualification
Welding position
2F
Pre-heat temperature
n/a
Inter-run temperature
n/a
Check method
n/a
PHWT
n/a
Hold
n/a
Other
n/a
Run sequence
Joint details
Prequel. Joint #
F1
Table
E3
Root gap
n/a
Root face
n/a
Include Ø
90
Backing
n/a
Weld run details
Welding parameters
No
side
Position
ɸ
mm
Trade name
Amperage
Voltage
Current and polarity
Initial cleaning
wire brush
Inter-run cleaning
chipping hammer and
wire brush
Back gouge method
n/a
Test
Visual
examination to specification as set out:
TABLE 6.2.2 of AS/NZS 1554.1.2014
examination to specification as set out on
page 61, TABLE 6.2.2 of GP from AS/NZS
1554.1:2011
Measurement
Fillet size 6mm +2 -0
Break fillet to check for 50% root fusion
Distortion
0-5 Ø
P a g e
|
23
MEM05015
Worksheet v1.1
Your preview ends here
Eager to read complete document? Join bartleby learn and gain access to the full version
- Access to all documents
- Unlimited textbook solutions
- 24/7 expert homework help
Baxter Institute| MEM05015
Weld using manual metal arc welding
process
Practical Activity 2
- Horizontal/Vertical Fillet Welding
You are required to perform a weld using the below task sheet, and fill out the table with the
welding
machine settings that you use to complete the task.
All welds to conform to the latest
standard (AS/NZS 1554 - Part 1: Welding of Steel Structures), a copy of the Australian standards
(AS/NZS 1554:1:2014 is available at your campus).
Welding Procedure Sheet
Manufacturer: Baxter Institute
Welding code: 1554.1.2014
Material specification / Grade: Mild Steel / GR300
To:
Location:
Workshop
Welding Process:
MMAW
Date qualified: __/__/____
Welded by: ____________
Welding position: 2F
Material dimensions:
Welding consumables:
Plate thickness:
10mm
Shielding gas:________
Flow Rate:________
Material heating:
Joint tolerances:
Pre-heat temperature
n/a
Interpass temperature
(max)
n/a
Check method
n/a
Joint Sketch
Run Sequence
Joint Details
3 runs (multi-pass)
Pre-qual. Joint #
F1
Table
E
3
Include
90
Weld run details
Welding parameters
Electrode/
Filler
Pass
Size
Class
ɸ
m
Filler Wire
Voltage
Amperag
Polarity
P a g e
|
24
MEM05015
Worksheet v1.1
Your preview ends here
Eager to read complete document? Join bartleby learn and gain access to the full version
- Access to all documents
- Unlimited textbook solutions
- 24/7 expert homework help
Baxter Institute| MEM05015
Weld using manual metal arc welding
process
no.
m
Trade name
e
1
2
3
Initial
cleaning:
Inter-run
cleaning
Wire brushing before and after(in-between runs)
Test / Requirements:
Visual
examination to specification as set out: TABLE
6.2.2-General purpose of AS/NZS 1554.1.2014
Measurement
Break fillet to check for
5
0
% root
fusion
Fillet size
10
mm +2 -0
Distortion
0-5
All welds to conform to AS/NZS 1554.1:2011 GP.
Welding Procedure Sheet
Material
Low Carbon Steel
To
Fabricator
Baxter Institute
Process
MMAW
Welding standard
AS/NZS 1554.1:2011
Edge preparation
Weldability group #
250
Plate thickness
10mm
PQR #
2
Date qualified
Welded by
Revision
Date
Qualification
Welding position
2F
Pre-heat temperature
n/a
Inter-run temperature
n/a
Check method
n/a
PHWT
n/a
Hold
n/a
Other
n/a
Run sequence
Joint details
Prequel. Joint #
F1
Table
E3
Root gap
n/a
Root face
n/a
Include Ø
90
Backing
n/a
Weld run details
Welding parameters
No
side
Position
ɸ mm
Trade name
amperage
Voltage
Current and polarity
P a g e
|
25
MEM05015
Worksheet v1.1
Your preview ends here
Eager to read complete document? Join bartleby learn and gain access to the full version
- Access to all documents
- Unlimited textbook solutions
- 24/7 expert homework help
Baxter Institute| MEM05015
Weld using manual metal arc welding
process
Initial cleaning
wire brush
Inter-run cleaning
chipping hammer and
wire brush
Back gouge method
n/a
Test
Visual
examination to specification as set out: TABLE
6.2.2 of AS/NZS 1554.1.2014
examination to
specification as set out on page 61, TABLE 6.2.2
of GP from AS/NZS 1554.1:2011
Measurement
Fillet size 10mm +2 -0
Break fillet to check for 50% root fusion
Distortion
0-5 Ø
You are required to perform a weld according to the job instructions detailed in the welding
procedure specification (WPS) below. You must fill out the information for the welding machine
settings and the consumables used to complete the task.
Note, if applicable the weld should
conform to the latest standard (as specified in the WPS), a copy of the Australian standards is
available at your campus.
For this practical learning activity you are required to use the following Arc welding Consumable:
Cigweld 3.2mm General Purpose (GP) Electrodes.
Welding Procedure Specification
Manufacturer: Baxter Institute
Welding
Standard:1554.1.2014
Material specification / Grade: Mild Steel / G300
Welded by: ____________Date: __/__/____
Location:
Workshop
Welding Process:
MMAW
Welding position: 2F
Joint type: Tee
Material dimensions:
Welding consumables:
Plate thickness:
10mm
Plate Size:
25 x 180mm (Qtyx1)
50 x 180mm (Qtyx1)
Shielding Gas: N/A
Flow Rate: N/A
Material heating:
Joint tolerances:
Pre-heat temperature
N/A
Inter-pass temperature
(max)
N/A
Check method
N/A
Root face: N/A
Root gap: N/A
Joint
Preparation Sketch
Run Sequence
Joint Details
3 Runs
Table (Pre-qual Joint): E3
Joint Identification: F1
Include
: 90
Weld run details
Welding parameters
P a g e
|
26
MEM05015
Worksheet v1.1
Your preview ends here
Eager to read complete document? Join bartleby learn and gain access to the full version
- Access to all documents
- Unlimited textbook solutions
- 24/7 expert homework help
Baxter Institute| MEM05015
Weld using manual metal arc welding
process
Electrode/ Filler
Polarity
Pass
no.
Side
Class
ɸ mm
Trade Name
1
2
3
Initial cleaning: Wire Brush
Inter-run cleaning: Chip off flux and Wire brush before and after each run
Test / Requirements:
Visual
Examination to specification as set out: TABLE 6.2.2-General
purpose of AS/NZS 1554.1.2014
Measurement
Break fillet to check for 75% root fusion
Fillet size 10mm +2 -0
No Distortion
P a g e
|
27
MEM05015
Worksheet v1.1
Amperage
Range
Your preview ends here
Eager to read complete document? Join bartleby learn and gain access to the full version
- Access to all documents
- Unlimited textbook solutions
- 24/7 expert homework help
Baxter Institute| MEM05015
Weld using manual metal arc welding
process
Practical Activity 3
- Horizontal/Vertical Fillet Welding
You are required to perform a weld according to the job instructions detailed in the welding
procedure specification (WPS) below. You must fill out the information for the welding machine
settings and the consumables used to complete the task.
Note, if applicable the weld should
conform to the latest standard (as specified in the WPS), a copy of the Australian standards is
available at your campus.
For this practical learning activity you are required to use the following Arc welding Consumable:
Cigweld 3.2mm General Purpose (GP) Electrodes
You are required to perform a weld using the below task sheet, and fill out the table with the
welding machine settings that you use to complete the task.
All welds to conform to the latest
standard (AS/NZS 1554 - Part 1: Welding of Steel Structures), a copy of the Australian standards
(AS/NZS 1554:1:2014 is available at your campus).
All welds to conform to AS/NZS 1554.1:2011
GP.
Welding Procedure Sheet
Manufacturer: Baxter Institute
Welding code: 1554.1.2014
Material specification / Grade: Mild Steel /
GR300
To:
Location:
Workshop
Welding Process:
MMAW
Date qualified: __/__/____
Welded by: ____________
Welding position:
3
F
Material dimensions:
Welding consumables:
Plate thickness:
10mm
Shielding gas:________
Flow Rate:________
Material heating:
Joint tolerances:
Pre-heat temperature
n/a
Interpass temperature
(max)
n/a
Check method
n/a
Joint Sketch
Run Sequence
Joint Details
2
runs (multi-pass)
Pre-qual. Joint #
F1
Table
E3
Include
90
Weld run details
Welding parameters
Electrode/
Filler
Pass
no.
Size
Class
ɸ
mm
Filler Wire
Trade name
Voltage
Amperage
Polarity
1
P a g e
|
28
MEM05015
Worksheet v1.1
Your preview ends here
Eager to read complete document? Join bartleby learn and gain access to the full version
- Access to all documents
- Unlimited textbook solutions
- 24/7 expert homework help
Baxter Institute| MEM05015
Weld using manual metal arc welding
process
2
Initial cleaning: Inter-run cleaning
Wire brushing before and after(in-between runs)
Test / Requirements:
Visual
examination to specification as set out: TABLE
6.2.2-General purpose of AS/NZS 1554.1.2014
Measurement
Break fillet to check for
5
0
% root fusion
Fillet size 10mm +2 -0
Distortion
0-5
P a g e
|
29
MEM05015
Worksheet v1.1
Your preview ends here
Eager to read complete document? Join bartleby learn and gain access to the full version
- Access to all documents
- Unlimited textbook solutions
- 24/7 expert homework help
Baxter Institute| MEM05015
Weld using manual metal arc welding
process
Welding Procedure Sheet
Material
Low Carbon Steel
To
Fabricator
Baxter Institute
Process
MMAW
Welding standard
AS/NZS 1554.1:2011
Edge preparation
Weldability group #
250
Plate thickness
10mm
PQR #
3
Date qualified
Welded by
Revision
Date
Qualification
Welding position
3F
Pre-heat temperature
n/a
Inter-run temperature
n/a
Check method
n/a
PHWT
n/a
Hold
n/a
Other
n/a
Run sequence
Joint details
Prequel. Joint #
F1
Table
E3
Root gap
n/a
Root face
n/a
Include Ø
90
Backing
n/a
Weld run details
Welding parameters
No
sid
e
Positio
n
ɸ mm
Trade name
amperage
Voltage
Current and polarity
Initial cleaning
wire brush
Inter-run cleaning
chipping hammer and
wire brush
Back gouge method
n/a
Test
Visual
examination to specification as set out:
TABLE 6.2.2 of AS/NZS 1554.1.2014
examination to specification as set out on
page 61, TABLE 6.2.2 of GP from AS/NZS
1554.1:2011
Measurement
Fillet size 10mm +2 -0
Break fillet to check for 50% root fusion
Distortion
0-5 Ø
P a g e
|
30
MEM05015
Worksheet v1.1
Your preview ends here
Eager to read complete document? Join bartleby learn and gain access to the full version
- Access to all documents
- Unlimited textbook solutions
- 24/7 expert homework help
Baxter Institute| MEM05015
Weld using manual metal arc welding
process
Practical Activity 4
-
Flat Butt Welding
You are required to perform a weld using the below task sheet, and fill
out the table with the welding machine settings that you use to
complete the task.
All welds to conform to the latest standard
(AS/NZS 1554 - Part 1: Welding of Steel Structures), a copy of the
Australian standards (AS/NZS 1554:1:2014 is available at your
campus).
All welds to conform to AS/NZS 1554.1:2011 GP.
Welding Procedure Sheet
Manufacturer: Baxter Institute
Welding code: 1554.1.2014
Material specification / Grade: Mild
Steel / GR300
To:
Location:
Workshop
Welding Process:
MMAW
Edge preparation:
Bevel cut/Grind
Date qualified: __/__/____
Welded by: ____________
Welding position:
1
G
Material dimensions:
Welding consumables:
Plate thickness:
10
mm
Shielding gas:________
Flow Rate:________
Material heating:
Joint tolerances:
Pre-heat temperature
n/a
Interpass temperature
(max)
n/a
Check method
n/a
Bevel angle: 30 to 350
Root face: 1.5mm (min) to 2.5mm
(max)
Root Gap: 1.5mm (min) to 4mm
(max)
Joint Sketch
Run Sequence
Joint Details
3 - 7 runs
Pre-qual. Joint
#
B-C 2a
Table
E1
Include
90
Weld run details
Welding parameters
P a g e
|
31
MEM05015
Worksheet v1.1
Your preview ends here
Eager to read complete document? Join bartleby learn and gain access to the full version
- Access to all documents
- Unlimited textbook solutions
- 24/7 expert homework help
Baxter Institute| MEM05015
Weld using manual metal arc welding
process
Electrode/
Filler
Pas
s
no
.
Size
Class
ɸ
mm
Filler
Wire
Trade
name
Voltag
e
Amperag
e
Polarity
1
2
3
4
5
6
7
Initial cleaning: Inter-run cleaning
.
Wire brushing before and after(in-between runs)
Test / Requirements:
Visual
examination to specification as set
out: TABLE 6.2.2-General purpose of
AS/NZS 1554.1.2014
Measurement
Inspect weld to check 5
0
%
penetration
Weld Reinforcement: Not Limited
Penetration Reinforcement: Not
limited
Distortion
0-5
P a g e
|
32
MEM05015
Worksheet v1.1
Your preview ends here
Eager to read complete document? Join bartleby learn and gain access to the full version
- Access to all documents
- Unlimited textbook solutions
- 24/7 expert homework help
Baxter Institute| MEM05015
Weld using manual metal arc welding
process
Welding Procedure Sheet
Material
Low Carbon
Steel
To
Fabricator
Baxter Institute
Process
MMAW
Welding standard
AS/NZS
1554.1:2011
Edge preparation
Weldability group #
250
Plate thickness
10mm
PQR #
5
Date qualified
Welded by
Revision
Date
Qualification
Welding position
1G
Pre-heat temperature
n/a
Inter-run temperature
n/a
Check method
n/a
PHWT
n/a
Hold
n/a
Other
n/a
Run sequence
Joint details
Between 4 and 7 runs to
fill
Prequel. Joint #
B-C 2a
Table
E1
Root gap
n/a
Root face
n/a
Include Ø
90
Backing
n/a
Weld run details
Welding parameters
No
sid
e
Positio
n
ɸ
mm
Trade
name
ampera
ge
Voltag
e
Current and polarity
Initial cleaning
wire brush
Inter-run cleaning
chipping
hammer and
wire brush
Back gouge method
n/a
P a g e
|
33
MEM05015
Worksheet v1.1
Your preview ends here
Eager to read complete document? Join bartleby learn and gain access to the full version
- Access to all documents
- Unlimited textbook solutions
- 24/7 expert homework help
Baxter Institute| MEM05015
Weld using manual metal arc welding
process
Test
Visual
examination to specification as set
out: TABLE 6.2.2 of AS/NZS
1554.1.2014
examination to specification as set
out on page 61, TABLE 6.2.2 of GP
from AS/NZS 1554.1:2011
Measurement
Butt weld size 10mm +2 -0
Minimum 50% root fusion
Distortion
0-5 Ø
P a g e
|
34
MEM05015
Worksheet v1.1
Your preview ends here
Eager to read complete document? Join bartleby learn and gain access to the full version
- Access to all documents
- Unlimited textbook solutions
- 24/7 expert homework help
Baxter Institute| MEM05015
Weld using manual metal arc welding
process
Practical Activity 5
-
Horizontal Butt Welding
You are required to perform a weld using the below task sheet, and fill
out the table with the welding machine settings that you use to
complete the task.
All welds to conform to the latest standard
(AS/NZS 1554 - Part 1: Welding of Steel Structures), a copy of the
Australian standards (AS/NZS 1554:1:2014 is available at your
campus).
All welds to conform to AS/NZS 1554.1:2011 GP.
Welding Procedure Sheet
Manufacturer: Baxter Institute
Welding code: 1554.1.2014
Material specification/Grade: Mild
Steel / GR300
To:
Location:
Workshop
Welding Process:
MMAW
Edge preparation:
Bevel cut/Grind
Date qualified: __/__/____
Welded by: ____________
Welding position:
2
G
Material dimensions:
Welding consumables:
Plate thickness:
10mm
Shielding gas:________
Flow Rate:________
Material heating:
Joint tolerances:
Pre-heat temperature
n/a
Interpass temperature
(max)
n/a
Check method
n/a
Bevel angle: 30 to 350
Root face: 1.5mm (min) to 2.5mm
(max)
Root Gap: 1.5mm (min) to 4mm
(max)
Joint Sketch
Run Sequence
Joint
Details
3 - 7
r
uns
Pre-qual. Joint #
B-C 2a
Table
E1
Include
90
Backing: Non-fusible
backing
Weld run details
Welding parameters
P a g e
|
35
MEM05015
Worksheet v1.1
Your preview ends here
Eager to read complete document? Join bartleby learn and gain access to the full version
- Access to all documents
- Unlimited textbook solutions
- 24/7 expert homework help
Baxter Institute| MEM05015
Weld using manual metal arc welding
process
Pas
s
no
.
Electrode/ Filler
Size
Class
ɸ
mm
Filler
Wire
Trade
name
Voltag
e
Amperag
e
Polarity
Current
and polarity
1
2
3
4
5
6
7
Initial cleaning: Inter-run cleaning. Wire brushing before and after(in-
between runs)
Test / Requirements:
Visual
examination to specification as set
out: TABLE 6.2.2-General purpose of
AS/NZS 1554.1.2014
Measurement
Inspect weld to check 5
0
%
penetration
Weld Reinforcement: Not Limited
Penetration Reinforcement: Not
limited
Distortion
0-5
P a g e
|
36
MEM05015
Worksheet v1.1
Your preview ends here
Eager to read complete document? Join bartleby learn and gain access to the full version
- Access to all documents
- Unlimited textbook solutions
- 24/7 expert homework help
Baxter Institute| MEM05015
Weld using manual metal arc welding
process
Welding Procedure Sheet
Material
Low Carbon
Steel
To
Fabricator
Baxter Institute
Process
MMAW
Welding standard
AS/NZS
1554.1:2011
Edge preparation
Weldability group #
Plate thickness
10mm
PQR #
6
Date qualified
Welded by
Revision
Date
Qualification
Welding position
2G
Pre-heat temperature
n/a
Inter-run temperature
n/a
Check method
n/a
PHWT
n/a
Hold
n/a
Other
n/a
Run sequence
Joint details
Between 3 and 7 runs to
fill
Prequel. Joint #
B-C 2a
Table
E1
Root gap
n/a
Root face
n/a
Include Ø
90
Backing
n/a
Weld run details
Welding parameters
No
sid
e
Positio
n
ɸ
mm
Trade
name
ampera
ge
Voltag
e
Current and polarity
Initial cleaning
wire brush
Inter-run cleaning
chipping
hammer and
wire brush
Back gouge method
n/a
Test
P a g e
|
37
MEM05015
Worksheet v1.1
Your preview ends here
Eager to read complete document? Join bartleby learn and gain access to the full version
- Access to all documents
- Unlimited textbook solutions
- 24/7 expert homework help
Baxter Institute| MEM05015
Weld using manual metal arc welding
process
Visual
examination to specification as set
out: TABLE 6.2.2 of AS/NZS
1554.1.2014
examination to
specification as set out on page 61,
TABLE 6.2.2 of GP from AS/NZS
1554.1:2011
Measurement
Butt Weld size 10mm +2 -0
Minimum 50% root fusion
Distortion
0-5 Ø
P a g e
|
38
MEM05015
Worksheet v1.1
Your preview ends here
Eager to read complete document? Join bartleby learn and gain access to the full version
- Access to all documents
- Unlimited textbook solutions
- 24/7 expert homework help
Baxter Institute| MEM05015
Weld using manual metal arc welding
process
Practical Activity
6
- V
6
ertical
B
utt Welding
You are required to perform a weld using the below task sheet, and fill
out the table with the welding machine settings that you use to
complete the task.
All welds to conform to the latest standard
(AS/NZS 1554 - Part 1: Welding of Steel Structures), a copy of the
Australian standards (AS/NZS 1554:1:2014 is available at your
campus).
All welds to conform to AS/NZS 1554.1:2011 GP.
Welding Procedure Sheet
Manufacturer: Baxter Institute
Welding code: 1554.1.2014
Material specification / Grade: Mild
Steel / GR300
To:
Location:
Workshop
Welding Process:
MMAW
Edge preparation:
Bevel cut/Grind
Date qualified: __/__/____
Welded by: ____________
Welding position: 3G
Material dimensions:
Welding consumables:
Plate thickness:
10mm
Shielding gas:________
Flow Rate:________
Material heating:
Joint tolerances:
Pre-heat temperature
n/a
Interpass temperature
(max)
n/a
Check method
n/a
Bevel angle: 30 to 350
Root face: 1.5mm (min) to 2.5mm
(max)
Root Gap: 1.5mm (min) to 4mm
(max)
Joint Sketch
Run Sequence
Joint
Details
3 - 6
runs
Pre-qual. Joint #
B-C 2a
Table
E1
(rotated)
Include
90
Weld run details
Welding parameters
P a g e
|
39
MEM05015
Worksheet v1.1
Your preview ends here
Eager to read complete document? Join bartleby learn and gain access to the full version
- Access to all documents
- Unlimited textbook solutions
- 24/7 expert homework help
Baxter Institute| MEM05015
Weld using manual metal arc welding
process
Electrode/
Filler
Pas
s
no
.
Size
Class
ɸ
mm
Filler
Wire
Trade
name
Voltag
e
Amperag
e
Polarity
1
2
3
4
5
6
Initial cleaning: Inter-run cleaning. Wire brushing before and after(in-
between runs)
Test / Requirements:
Visual
examination to specification as set
out: TABLE 6.2.2-General purpose of
AS/NZS 1554.1.2014
Measurement
Inspect weld to check 5
0
%
penetration
Weld Reinforcement: Not Limited
Penetration Reinforcement: Not
limited
Distortion
0-5
P a g e
|
40
MEM05015
Worksheet v1.1
Your preview ends here
Eager to read complete document? Join bartleby learn and gain access to the full version
- Access to all documents
- Unlimited textbook solutions
- 24/7 expert homework help
Baxter Institute| MEM05015
Weld using manual metal arc welding
process
Welding Procedure Sheet
Material
Low Carbon
Steel
To
Fabricator
Baxter Institute
Process
MMAW
Welding standard
AS/NZS
1554.1:2011
Edge preparation
Weldability group #
Plate thickness
10mm
PQR #
7
Date qualified
Welded by
Revision
Date
Qualification
Welding position
3G
Pre-heat temperature
n/a
Inter-run temperature
n/a
Check method
n/a
PHWT
n/a
Hold
n/a
Other
n/a
Run sequence
Joint details
Between 3 and 6 runs to
fill
Prequel. Joint #
B-C 2a
Table
E1
Root gap
n/a
Root face
n/a
Include Ø
90
Backing
n/a
Weld run details
Welding parameters
No
sid
e
Positio
n
ɸ
mm
Trade
name
ampera
ge
Voltag
e
Current and polarity
Initial cleaning
wire brush
Inter-run cleaning
chipping
hammer and
wire brush
Back gouge method
n/a
Test
P a g e
|
41
MEM05015
Worksheet v1.1
Your preview ends here
Eager to read complete document? Join bartleby learn and gain access to the full version
- Access to all documents
- Unlimited textbook solutions
- 24/7 expert homework help
Baxter Institute| MEM05015
Weld using manual metal arc welding
process
Visual
examination to specification as set
out: TABLE 6.2.2 of AS/NZS
1554.1.2014
examination to
specification as set out on page 61,
TABLE 6.2.2 of GP from AS/NZS
1554.1:2011
Measurement
Butt weld size 10mm +2 -0
Minimum 50% root fusion
Distortion
0-5 Ø
Welding Procedure Specification
Manufacturer: Baxter Institute
Welding Standard:1554.1.2014
Material specification / Grade: Mild Steel / G300
Welded by: ____________Date: __/__/____
Location:
Workshop
Welding Process:
MMAW
Welding position: 3F
Joint type: Tee
Material dimensions:
Welding consumables:
Plate thickness:
10mm
Plate size:
50 x 180mm (Qty x 2)
Shielding Gas: N/A
Flow Rate: N/A
Material heating:
Joint tolerances:
Pre-heat temperature
N/A
Inter-pass temperature
(max)
N/A
Check method
N/A
Root face: N/A
Root gap: N/A
Joint
Preparation Sketch
Run Sequence
Joint Details
1 Root Run & 1 Capping Pass
Table (Pre-qual Joint): E3
Joint Identification: F1
Include
: 90
Weld run details
Welding parameters
Electrode/ Filler
Polarity
Pass
no.
Side
Class
ɸ mm
Trade Name
1
2
Initial cleaning: Wire Brush
Inter-run cleaning: Chip off flux and Wire brush before and after each run
Test / Requirements:
Visual
Examination to specification as set out: TABLE 6.2.2-
General purpose of AS/NZS 1554.1.2014
Measurement
Break fillet to check for 75% root fusion
Fillet size 10mm +2 -0
No Distortion
P a g e
|
42
MEM05015
Worksheet v1.1
Side 2
Side 1
Amperage
Range
Your preview ends here
Eager to read complete document? Join bartleby learn and gain access to the full version
- Access to all documents
- Unlimited textbook solutions
- 24/7 expert homework help
Baxter Institute| MEM05015
Weld using manual metal arc welding
process
Practical Activity 4 - Flat Butt Welding
You are required to perform a weld according to the job instructions detailed in the welding
procedure specification (WPS) below. You must fill out the information for the welding machine
settings and the consumables used to complete the task.
Note, if applicable the weld should
conform to the latest standard (as specified in the WPS), a copy of the Australian standards is
available at your campus.
For this practical learning activity you are required to use the following Arc welding Consumable:
Cigweld 3.2mm General Purpose (GP) Electrodes.
Welding Procedure Specification
Manufacturer: Baxter Institute
Welding Standard: 1554.1.2014
Material specification / Grade: Mild Steel / G300
Location:
Workshop
Welding Process:
MMAW
Edge preparation:
Thermal Cut/Grind
Welding position: 1G
Joint Type: Single V
Material dimensions:
Welding consumables:
Plate thickness:
10mm
Plate size:
50 x 180mm (Qty x 2)
Shielding Gas: N/A
Flow Rate: N/A
Material heating:
Joint tolerances:
Pre-heat temperature
N/A
Inter-pass temperature
(max)
N/A
Check method
N/A
Bevel angle: 30
0
Root face: 1.6mm
Root gap: 3.5mm
Joint Preparation Sketch
Run Sequence
Joint Details
5
- 7 Runs
Table (Pre-qual Joint): E1
Joint Identification: B-C 2a
Include
: 60
Weld run details
Welding parameters
Electrode/ Filler
Polarity
Pass
no.
Side
Class
ɸ mm
Trade Name
1
2
3
4
5
6
7
Initial cleaning: Wire Brush
Inter-run cleaning: Chip off flux and Wire brush before and after each run
Test / Requirements:
Visual
Examination to specification as set out: TABLE 6.2.2-
Measurement
Minimum 75% Penetration
P a g e
|
43
MEM05015
Worksheet v1.1
Side 1
Amperage
Range
Your preview ends here
Eager to read complete document? Join bartleby learn and gain access to the full version
- Access to all documents
- Unlimited textbook solutions
- 24/7 expert homework help
Baxter Institute| MEM05015
Weld using manual metal arc welding
process
General purpose of AS/NZS 1554.1.2014
No distortion
Practical Activity 5 - Horizontal Butt Welding
You are required to perform a weld according to the job instructions detailed in the welding
procedure specification (WPS) below. You must fill out the information for the welding machine
settings and the consumables used to complete the task.
Note, if applicable the weld should
conform to the latest standard (as specified in the WPS), a copy of the Australian standards is
available at your campus.
For this practical learning activity you are required to use the following Arc welding Consumable:
Cigweld 3.2mm General Purpose (GP) Electrodes.
Welding Procedure Specification
Manufacturer: Baxter Institute
Welding Standard: 1554.1.2014
Material specification/Grade: Mild Steel / G300
Welded by: ____________Date: __/__/____
Location:
Workshop
Welding Process:
MMAW
Edge preparation:
Thermal Cut/Grind
Welding position: 2G
Joint Type: Single V
Material dimensions:
Welding consumables:
Plate thickness:
10mm
Plate size:
50 x 180mm (Qty x 2)
Shielding Gas: N/A
Flow Rate: N/A
Material heating:
Joint tolerances:
Pre-heat temperature
N/A
Inter-pass temperature
(max)
N/A
Check method
N/A
Bevel angle: 30
0
Root face: 1.6mm
Root gap: 3.5mm
Joint
Preparation Sketch
Run Sequence
Joint Details
5 – 7 Runs
Table (Pre-qual Joint): E1
Joint Identification: B-C 2a
Include
: 60
Weld run details
Welding parameters
Pass
no.
Electrode/ Filler
Amperage Range
Polarity
Side
Class
ɸ mm
1
2
3
4
5
6
7
Initial cleaning: Wire Brush
Inter-run cleaning: Chip off flux and Wire brush before and after each run
Test / Requirements:
Visual
Measurement
P a g e
|
44
MEM05015
Worksheet v1.1
Side
Trade Name
Your preview ends here
Eager to read complete document? Join bartleby learn and gain access to the full version
- Access to all documents
- Unlimited textbook solutions
- 24/7 expert homework help
Baxter Institute| MEM05015
Weld using manual metal arc welding
process
Examination to specification as set out: TABLE 6.2.2-
General purpose of AS/NZS 1554.1.2014
Minimum 75% Penetration
No distortion
Practical Activity 6 - Vertical Butt Welding
You are required to perform a weld according to the job instructions detailed in the welding
procedure specification (WPS) below. You must fill out the information for the welding machine
settings and the consumables used to complete the task.
Note, if applicable the weld should
conform to the latest standard (as specified in the WPS), a copy of the Australian standards is
available at your campus.
For this practical learning activity you are required to use the following Arc welding Consumable:
Cigweld 3.2mm General Purpose (GP) Electrodes.
Welding Procedure Specification
Manufacturer: Baxter Institute
Welding Standard: 1554.1.2014
Material specification / Grade: Mild Steel / G300
Welded by: ____________Date: __/__/____
Location:
Workshop
Welding Process:
MMAW
Edge preparation:
Thermal Cut/Grind
Welding position: 3G
Joint Type: Single V
Material dimensions:
Welding consumables:
Plate thickness:
10mm
Plate size:
50 x 180mm (Qty x 2)
Shielding Gas: N/A
Flow Rate: N/A
Material heating:
Joint tolerances:
Pre-heat temperature
N/A
Inter-pass temperature
(max)
N/A
Check method
N/A
Bevel angle: 30
0
Root face: 1.6mm
Root gap: 3.5mm
Joint
Preparation Sketch
Run Sequence
Joint Details
1 Root Run & 1 - 2 Capping Passes
Table (Pre-qual Joint): E1
Joint Identification: B-C 2a
Include
: 60
Weld run details
Welding parameters
Pass
no.
Electrode/ Filler
Amperage Range
Polarity
Side
Class
ɸ mm
Trade Name
1
2
3
Initial cleaning: Wire Brush
Inter-run cleaning: Chip off flux and Wire brush before and after each run
Test / Requirements:
Visual
Examination to specification as set out: TABLE 6.2.2-General
purpose of AS/NZS 1554.1.2014
Measurement
Minimum 75% Penetration
No distortion
P a g e
|
45
MEM05015
Worksheet v1.1
Side 1
Top View:
Your preview ends here
Eager to read complete document? Join bartleby learn and gain access to the full version
- Access to all documents
- Unlimited textbook solutions
- 24/7 expert homework help
Baxter Institute| MEM05015
Weld using manual metal arc welding
process
P a g e
|
46
MEM05015
Worksheet v1.1
Your preview ends here
Eager to read complete document? Join bartleby learn and gain access to the full version
- Access to all documents
- Unlimited textbook solutions
- 24/7 expert homework help
Baxter Institute| MEM05015
Weld using manual metal arc welding
process
Practical Activity 7
- Horizontal/Vertical Fillet Welding
You are required to perform a weld using the below task sheet, and fill out the table with the welding
machine settings that you use to complete the task.
All welds to conform to the latest standard (AS/NZS
1554 - Part 1: Welding of Steel Structures), a copy of the Australian standards (AS/NZS 1554:1:2014 is
available at your campus).
All welds to conform to AS/NZS 1554.1:2011 GP.
Welding Procedure Sheet
Manufacturer: Baxter Institute
Welding code: 1554.1.2014
Material specification / Grade:
Stainless steel / GR304
To:
Location:
Workshop
Welding Process:
MMAW
Date qualified: __/__/____
Welded by: ____________
Welding position: 2F
Material dimensions:
Welding consumables:
Plate thickness:
6
mm
Shielding gas:________
Flow Rate:________
Material heating:
Joint tolerances:
Pre-heat temperature
n/a
Interpass temperature
(max)
n/a
Check method
n/a
Joint Sketch
Run Sequence
Joint Details
Pre-qual. Joint #
F1
Table
E3
Include
90
Weld run details
Welding parameters
Electrode/ Filler
Pass
no.
Size
Class
ɸ
mm
Filler Wire
Trade name
Voltage
Amperage
Polarity
1
Initial cleaning: Inter-run cleaning
Wire brushing before and after(in-between runs)
Test / Requirements:
Visual
examination to specification as set out: TABLE 6.2.2-
General purpose of AS/NZS 1554.1.2014
Measurement
Break fillet to check for
50
% root fusion
Fillet size
4
mm +2 -0
Distortion
0-5
You are required to perform a weld according to the job instructions detailed in the welding
procedure specification (WPS) below. You must fill out the information for the welding machine
settings and the consumables used to complete the task.
Note, if applicable the weld should
conform to the latest standard (as specified in the WPS), a copy of the Australian standards is
available at your campus.
For this practical learning activity you are required to use the following Arc welding Consumable:
P a g e
|
47
MEM05015
Worksheet v1.1
Your preview ends here
Eager to read complete document? Join bartleby learn and gain access to the full version
- Access to all documents
- Unlimited textbook solutions
- 24/7 expert homework help
Baxter Institute| MEM05015
Weld using manual metal arc welding
process
Cigweld 2.5/3.2 ES316L Electrode
Welding Procedure Specification
Manufacturer: Baxter Institute
Welding Standard:
1554.6.2012.
Material specification / Grade:
Stainless steel / G304
Welded by: ____________Date: __/__/____
Location:
Workshop
Welding Process:
MMAW
Welding position: 2F
Joint type: Tee
Material dimensions:
Welding consumables:
Plate thickness:
6mm
Plate size:
50 x 180mm (Qty x 2)
Shielding Gas: N/A
Flow Rate: N/A
Material heating:
Joint tolerances:
Pre-heat temperature
N/A
Inter-pass temperature
(max)
N/A
Check method
N/A
Root face: N/A
Root gap: N/A
Joint
Preparation Sketch
Run Sequence
Joint Details
1 Run
Table (Pre-qual Joint): D3
Joint Identification:
F1
Include
: 90
Weld run details
Welding parameters
Electrode/ Filler
Polarity
Pass
no.
Side
Class
ɸ mm
Trade Name
1
Initial cleaning: Wire Brush
Inter-run cleaning: Chip off flux and Wire brush before and after run
Test / Requirements:
Visual
Examination to specification as set out in Table 6.3.3
of AS NZS 1554.6.2012.
Measurement
Break fillet to check for 75% root fusion
Fillet size 4mm +2 - 0
Surface discolouration (HAZ) - 0 - 3 (max)
No Distortion
P a g e
|
48
MEM05015
Worksheet v1.1
Amperage
Range
Your preview ends here
Eager to read complete document? Join bartleby learn and gain access to the full version
- Access to all documents
- Unlimited textbook solutions
- 24/7 expert homework help
Baxter Institute| MEM05015
Weld using manual metal arc welding
process
Practical Activity 8 -Vertical Fillet Welding
Welding Procedure Sheet
Material
Stainless steel 309
To
Fabricator
Baxter Institute
Process
MMAW
Welding standard
AS/NZS 1554.1:2011
Edge preparation
Weldability group #
250
Plate thickness
5/6mm
PQR #
1
Date qualified
Welded by
Revision
Date
Qualification
Welding position
2F
Pre-heat temperature
n/a
Inter-run temperature
n/a
Check method
n/a
PHWT
n/a
Hold
n/a
Other
n/a
Run sequence
Joint details
Prequel. Joint #
F1
Table
E3
Root gap
n/a
Root face
n/a
Include Ø
90
Backing
n/a
Weld run details
Welding parameters
No
side
Position
ɸ
mm
Trade name
amperage
Voltage
Current and polarity
Initial cleanings/steel wire brush
Inter-run cleaning
chipping hammer and
wire brush
Back gouge method
n/a
Test
Visual
examination to specification as set out: TABLE
6.2.2 of AS/NZS 1554.1.2014
examination to
specification as set out on page 61, TABLE
6.2.2 of GP from AS/NZS 1554.1:2011
Measurement
Fillet size 4mm +2 -0
Break fillet to check for 50% root fusion
Distortion
0-5 Ø
You are required to perform a weld according to the job instructions detailed in the welding
procedure specification (WPS) below. You must fill out the information for the welding machine
settings and the consumables used to complete the task.
Note, if applicable the weld should
P a g e
|
49
MEM05015
Worksheet v1.1
Your preview ends here
Eager to read complete document? Join bartleby learn and gain access to the full version
- Access to all documents
- Unlimited textbook solutions
- 24/7 expert homework help
Baxter Institute| MEM05015
Weld using manual metal arc welding
process
conform to the latest standard (as specified in the WPS), a copy of the Australian standards is
available at your campus.
For this practical learning activity you are required to use the following Arc welding Consumable:
Cigweld 2.5/3.2 ES316L Electrode
.
Welding Procedure Specification
Manufacturer: Baxter Institute
Welding standard:
1554.6.2012.
Material specification/Grade: Stainless steel / G304
Welded by: ____________Date: __/__/____
Location:
Workshop
Welding Process:
MMAW
Edge preparation:
Grind Bevel
Welding position: 2G
Joint Type: Single V
Material dimensions:
Welding consumables:
Plate thickness:
6mm
Plate size:
50 x 180mm (Qty x 2)
Or 25 x 180mm (Qty x 2)
Shielding Gas: N/A
Flow Rate: N/A
Material heating:
Joint tolerances:
Pre-heat temperature
N/A
Inter-pass temperature
(max)
N/A
Check method
N/A
Bevel angle: 30
0
Root face: 1.5mm
Root gap: 3.5mm
Joint
Preparation Sketch
Run Sequence
Joint Details
2 - 3 Runs
Table (Pre-qual Joint): D1
Joint Identification: B-C 2a
Include
: 60
Weld run details
Welding parameters
Electrode/ Filler
Amperage Range
Polarity
Pass
no.
Side
Class
ɸ mm
Trade Name
1
2
3
Initial cleaning: Wire Brush
Test / Requirements:
Visual
Examination to specification as set out in Table 6.3.3 of
AS NZS 1554.6.2012.
Measurement
Minimum 75% Penetration
Surface discolouration (HAZ) - 0 - 3 (max)
No Distortion
P a g e
|
50
MEM05015
Worksheet v1.1
Side 1
Inter-run cleaning: Chip off flux and Wire brush before and after each run
Your preview ends here
Eager to read complete document? Join bartleby learn and gain access to the full version
- Access to all documents
- Unlimited textbook solutions
- 24/7 expert homework help
Baxter Institute| MEM05015
Weld using manual metal arc welding
process
P a g e
|
51
MEM05015
Worksheet v1.1
Your preview ends here
Eager to read complete document? Join bartleby learn and gain access to the full version
- Access to all documents
- Unlimited textbook solutions
- 24/7 expert homework help
Baxter Institute| MEM05015
Weld using manual metal arc welding
process
Practical Activity 8
-Vertical Fillet Welding
You are required to perform a weld using the below task sheet, and fill out the table with the welding
machine settings that you use to complete the task.
All welds to conform to the latest standard (AS/NZS
1554 - Part 1: Welding of Steel Structures), a copy of the Australian standards (AS/NZS 1554:1:2014 is
available at your campus).
All welds to conform to AS/NZS 1554.1:2011 GP.
Welding Procedure Sheet
Manufacturer: Baxter Institute
Welding code: 1554.1.2014
Material specification/
Grade: Stainless
steel / GR304
To:
Location:
Workshop
Welding Process:
MMAW
Edge preparation:
Bevel cut/Grind
Date qualified: __/__/____
Welded by: ____________
Welding position: 2G
Material dimensions:
Welding consumables:
Plate thickness:
6mm
Shielding gas:________
Flow Rate:________
Material heating:
Joint tolerances:
Pre-heat temperature
n/a
Interpass temperature
(max)
n/a
Check method
n/a
Bevel angle: 30 to 35
0
Root face: 1.5mm (min) to 2.5mm (max)
Root Gap: 1.5mm (min) to 4mm (max)
Joint Sketch
Run Sequence
Joint Details
3 - 7
runs
Pre-qual. Joint #
B-C 2a
Table
E1
Include
90
Weld run details
Welding parameters
Electrode/ Filler
Pass
no.
Size
Class
ɸ mm
Filler Wire
Trade name
Voltage
Amperage
Polarity
1
2
3
4
5
6
7
Initial cleaning: Inter-run cleaning. Wire brushing before and after(in-between runs)
Test / Requirements:
Visual
examination to specification as set out: TABLE 6.2.2-General
purpose of AS/NZS 1554.1.2014
Measurement
Inspect weld to check 5
0
% penetration
-
Weld Reinforcement
: Not Limited
P a g e
|
52
MEM05015
Worksheet v1.1
Your preview ends here
Eager to read complete document? Join bartleby learn and gain access to the full version
- Access to all documents
- Unlimited textbook solutions
- 24/7 expert homework help
Baxter Institute| MEM05015
Weld using manual metal arc welding
process
-
Penetration Reinforcement
: Not limited
Distortion
0-5
Welding Procedure Sheet
Material
Stainless steel
To
Fabricator
Baxter Institute
Process
MMAW
Welding standard
AS/NZS 1554.1:2011
Edge preparation
Weldability group #
Plate thickness
5/6mm
PQR #
8
Date qualified
Welded by
Revision
Date
Qualification
Welding position
2G
Pre-heat temperature
n/a
Inter-run temperature
n/a
Check method
n/a
PHWT
n/a
Hold
n/a
Other
n/a
Run sequence
Joint details
Between 3 and 7 runs to fill
Prequel. Joint #
B-C 2a
Table
E1
Root gap
n/a
Root face
n/a
Include Ø
90
Backing
n/a
Weld run details
Welding parameters
No
sid
e
Positio
n
ɸ mm
Trade name
amperage
Voltage
Current and polarity
Initial cleanings/steel wire brush
Inter-run cleaning
chipping hammer and
wire brush
Back gouge method
n/a
Test
Visual
examination to specification as set out on
page 61, TABLE 6.2.2 of GP from AS/NZS
1554.1:2011
examination to specification as set out:
TABLE 6.2.2 of AS/NZS 1554.1.2014
Measurement
Butt weld size 10mm +2 -0
Minimum 50% root fusion
Distortion
0-5 Ø
P a g e
|
53
MEM05015
Worksheet v1.1
Your preview ends here
Eager to read complete document? Join bartleby learn and gain access to the full version
- Access to all documents
- Unlimited textbook solutions
- 24/7 expert homework help
Baxter Institute| MEM05015
Weld using manual metal arc welding
process
P a g e
|
54
MEM05015
Worksheet v1.1
Your preview ends here
Eager to read complete document? Join bartleby learn and gain access to the full version
- Access to all documents
- Unlimited textbook solutions
- 24/7 expert homework help
Baxter Institute| MEM05015
Weld using manual metal arc welding
process
Learning Activities Checklist
Student Name:
Student ID:
________________________________
No
Learning Activities
Date
completed
Trainer’s name
and signature
1
C
omplete Learning Activity 1
–
Review Question
on
:
(Read
Section 1 -
Manual Metal Arc Welding (
MMAW
)
and
Complete
Learning Activity 1
)
2
C
omplete Learning Activity
2 –
Review Question
on
Section 2 -
Review Question
(Read Section 2 -
Welding Machine
Setup
and Complete Learning Activity
)
3
C
omplete Learning Activity
3 –
Review Question
on
Section 3 -
Review Question
:
(Read Section 3 -
Material
Preparation
)
and Complete Learning Activity 3
4
C
omplete Learning Activity
4 –
Review Question on
Section 4 -
Review Question
:
(Read Section 4 -
Types of Welds
)
and Complete Learning Activity 4
5
C
omplete Learning Activity
5 –
Review Question
on
Section 5 -
Review Question
:
(Read Section 5 –
Distortion
)
and
Complete Learning Activity 5
6
C
omplete Learning Activity
6 –
Review Question
on
Section 6 -
Review Question
:
(Read Section 6 -
Welding
Positions
)
and Complete Learning Activity 6
7
C
omplete Learning Activity
7 –
Review Question
on
Section 7 -
Review Question
:
(Read Section 7 -
Types of Weld
Defects
)
and Complete Learning Activity 7
8
C
omplete Learning Activity
8 –
Review Question
on
Section 8 -
Review Question
:
(Read Section 8 -
Testing for weld
defects
)
and Complete Learning Activity 8
10
10
Complete practical activity 1 –
Horizontal
/Vertical
Fillet Welding
Section 9
– Practical Activity
Complete practical activity 1
10
11
Complete practical activity 1 –
Horizontal/Vertical Fillet Welding
Complete practical activity 2
11
12
Complete practical activity 2 –
Horizontal/Vertical Fillet Welding
Section 9 – Practical Activity
Complete practical activity 3
12
13
Complete practical activity 3 –
Horizontal/Vertical Fillet Welding
Section 9 – Practical Activity
Complete practical activity 4
13
14
Complete practical activity 4 –
Flat Butt Welding
Section 9 – Practical Activity
Complete practical activity 5
P a g e
|
55
MEM05015
Worksheet v1.1
Your preview ends here
Eager to read complete document? Join bartleby learn and gain access to the full version
- Access to all documents
- Unlimited textbook solutions
- 24/7 expert homework help
Baxter Institute| MEM05015
Weld using manual metal arc welding
process
14
15
Complete practical activity 5 –
Horizontal Butt Welding
Section 9 – Practical Activity
Complete practical activity 6
15
16
Complete practical activity 6 –
Vertical Butt Welding
Section 9 – Practical Activity
Complete practical activity 7
16
17
Complete practical activity 7 –
Horizontal/Vertical Fillet Welding
Section 9 – Practical Activity
Complete practical activity 8
17
Complete practical activity
8
–
Horizontal
Butt
Welding
Section 9 – Practical Activity
Student Signature:
Completion Date:
Congratulations, you have completed all learning activities for
MEM05015
!
Now you can proceed to undertake assessment activities
This page is left blank intentionally
P a g e
|
56
MEM05015
Worksheet v1.1
Your preview ends here
Eager to read complete document? Join bartleby learn and gain access to the full version
- Access to all documents
- Unlimited textbook solutions
- 24/7 expert homework help
Baxter Institute| MEM05015
Weld using manual metal arc welding
process
P a g e
|
57
MEM05015
Worksheet v1.1
Your preview ends here
Eager to read complete document? Join bartleby learn and gain access to the full version
- Access to all documents
- Unlimited textbook solutions
- 24/7 expert homework help
Related Documents
Related Questions
these are shot questions please answer the all questions it's important for me
arrow_forward
5. What is the part’s over all length?_______________________
6. Whatisthe part’s over all height?_______________________
7. Whatisthepart’soveralldepth?_______________________
9. Which line does in the top view represents surface P
arrow_forward
I need parts 8 and 9 answered please and thank you.
arrow_forward
Which among the following is a forming process in which thickness of the metal plate is decreased by increasing its
length.
O a. Rolling
O b. Forging
O c. Drawing
O d. Bending
Which of the following metal forming processes is best suitable for making the cup shaped products?
ENG
08:37
a
US
19/04/20
ho
inse
arrow_forward
It says surface Temperature is not 125.49oC (look at picture I attached). What would be the correct value? Thank you.
arrow_forward
Please can you assist me with the attached question. Many thanks.
arrow_forward
I have three parts that I need answered pertaining to the print provided below.
What material is specified for this part? (Multiple Choice)a. Cold Drawn Steel CD1040b. Hot Rolled Steelc. Delrin #360d. Brass FM#360
What size paper was used for the original version of this print? (Multiple Choice)ABCD
The two views near the bottom of the print are called detail views. Which one of theviews above (left side, front, or right side) shows the same geometry, but at the normal 1:1scale? (Multiple Choice)a. left sideb. frontc. right side
arrow_forward
I need the answer as soon as possible
arrow_forward
I need answers to questions 4, 5, and 6 pertaining to the print provided.
arrow_forward
The frontal working area of the electrode in an Electrochemical Machining (ECM)
operation is 1000 mm. The applied current is 900 amps and the voltage is 12 volts.
The resistivity of the electi olyte is 140 Q-mm. The material being cut has a valency
of 4 and specific removal rate of 0.0342 mm /A-s. If the process efficiency is 90%,
determine the material remova! rate (MRR) and inter-electrode gap after 30 minutes
of machining when the resistivity of the electrolyte has dropped to 75% of its
original value.
arrow_forward
1. What best describes this print? *
A. Casting
B. Forging
C. Welding
D. Machining
2.
There are GD&T Feature Control Frames on the Print. Check the types that apply. *
Flatness
Parallelism
True Position
3. What company specification number is given to the material for this part?
arrow_forward
The strength in the weld zone of an age-hardening aluminium alloy is often higher than in the heat affect zone (HAZ). Which of the following is NOT a reason for this?
O The maximum temperature is higher in the weld pushing more of the hardening phase into solution.
O Particles that don't dissolve might transform into equilibrium phases instead. This is more likely in the HAZ.
O The greater dissolution of particles in the weld leads to greater solid solution strengthening.
O The increase in solute in the matrix allows more subsequent natural aging to occur in the weld zone.
O Particles in the HAZ tend to dissolve, while those in the weld coarsen. The increase in particle size and spacing reduces the strength of HAZ.
arrow_forward
Please answer correctly thank you
arrow_forward
I have three parts that need to be answered pertaining to the print provided below.
What size paper was used for the original version of this print? (Multiple Choice)ABCD
What is the total quantity of subassemblies required for this assembly? (Multiple Choice)A: twoB: threeC: fourD: five
What term describes the relationship of the axis of the 1/2″ pipe plug with the main,longer axis of the bottom assembly? (Multiple Choice)A: PerpendicularB: ParallelC: VerticalD: X shaped
arrow_forward
24)
arrow_forward
3. SOLDERING, BRAZING and WELDING
Define soldering
Differentiate between the following;
Soft soldering and hard soldering/silver soldering and Electronics soldering
Identify filler rods and fluxes used in each (pg 290)
Describe the process of tinning a bit
4. Describe the following welding processes and sketch and label the tool used
(www.technologystudent.com)
Metal Arc welding
Tungturn Inert Gas welding
Metal Inert Gas welding
Spot welding
5. RIVETS AND RIVETING
Snap head riveting procedure
Pop riveting procedure
6. NUTS and BOLTS
Types of nuts
Types of bolts
Types of washers
7. FITTINGS
Examples and be able to identify by sight and be able to sketch
a) Hinges (butt hinge, backflap,piano hinge, stays, etc)
b)Catches (Magnetic, ball, spring)
c) Locks
arrow_forward
I need answers to questions 13, 14, amd 15 pertaining to the print provided.
arrow_forward
How’s ASTM D2041 related to ASTM D2726 ??
arrow_forward
I need answers for problems 10, 11, and 12 pertaining to the print.
arrow_forward
MENG364 MANUFACTURING TECHNOLOGY
1-Please Put the letter as it is and I will put the student number later
2- Please have to give me the final answer without rounding and with digit number at least 3 digit number should be include and dont forget the Unit
3- please solve the question very quickly
arrow_forward
SEE MORE QUESTIONS
Recommended textbooks for you
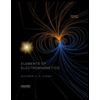
Elements Of Electromagnetics
Mechanical Engineering
ISBN:9780190698614
Author:Sadiku, Matthew N. O.
Publisher:Oxford University Press
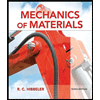
Mechanics of Materials (10th Edition)
Mechanical Engineering
ISBN:9780134319650
Author:Russell C. Hibbeler
Publisher:PEARSON
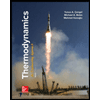
Thermodynamics: An Engineering Approach
Mechanical Engineering
ISBN:9781259822674
Author:Yunus A. Cengel Dr., Michael A. Boles
Publisher:McGraw-Hill Education
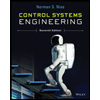
Control Systems Engineering
Mechanical Engineering
ISBN:9781118170519
Author:Norman S. Nise
Publisher:WILEY
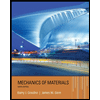
Mechanics of Materials (MindTap Course List)
Mechanical Engineering
ISBN:9781337093347
Author:Barry J. Goodno, James M. Gere
Publisher:Cengage Learning
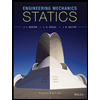
Engineering Mechanics: Statics
Mechanical Engineering
ISBN:9781118807330
Author:James L. Meriam, L. G. Kraige, J. N. Bolton
Publisher:WILEY
Related Questions
- these are shot questions please answer the all questions it's important for mearrow_forward5. What is the part’s over all length?_______________________ 6. Whatisthe part’s over all height?_______________________ 7. Whatisthepart’soveralldepth?_______________________ 9. Which line does in the top view represents surface Parrow_forwardI need parts 8 and 9 answered please and thank you.arrow_forward
- Which among the following is a forming process in which thickness of the metal plate is decreased by increasing its length. O a. Rolling O b. Forging O c. Drawing O d. Bending Which of the following metal forming processes is best suitable for making the cup shaped products? ENG 08:37 a US 19/04/20 ho insearrow_forwardIt says surface Temperature is not 125.49oC (look at picture I attached). What would be the correct value? Thank you.arrow_forwardPlease can you assist me with the attached question. Many thanks.arrow_forward
- I have three parts that I need answered pertaining to the print provided below. What material is specified for this part? (Multiple Choice)a. Cold Drawn Steel CD1040b. Hot Rolled Steelc. Delrin #360d. Brass FM#360 What size paper was used for the original version of this print? (Multiple Choice)ABCD The two views near the bottom of the print are called detail views. Which one of theviews above (left side, front, or right side) shows the same geometry, but at the normal 1:1scale? (Multiple Choice)a. left sideb. frontc. right sidearrow_forwardI need the answer as soon as possiblearrow_forwardI need answers to questions 4, 5, and 6 pertaining to the print provided.arrow_forward
- The frontal working area of the electrode in an Electrochemical Machining (ECM) operation is 1000 mm. The applied current is 900 amps and the voltage is 12 volts. The resistivity of the electi olyte is 140 Q-mm. The material being cut has a valency of 4 and specific removal rate of 0.0342 mm /A-s. If the process efficiency is 90%, determine the material remova! rate (MRR) and inter-electrode gap after 30 minutes of machining when the resistivity of the electrolyte has dropped to 75% of its original value.arrow_forward1. What best describes this print? * A. Casting B. Forging C. Welding D. Machining 2. There are GD&T Feature Control Frames on the Print. Check the types that apply. * Flatness Parallelism True Position 3. What company specification number is given to the material for this part?arrow_forwardThe strength in the weld zone of an age-hardening aluminium alloy is often higher than in the heat affect zone (HAZ). Which of the following is NOT a reason for this? O The maximum temperature is higher in the weld pushing more of the hardening phase into solution. O Particles that don't dissolve might transform into equilibrium phases instead. This is more likely in the HAZ. O The greater dissolution of particles in the weld leads to greater solid solution strengthening. O The increase in solute in the matrix allows more subsequent natural aging to occur in the weld zone. O Particles in the HAZ tend to dissolve, while those in the weld coarsen. The increase in particle size and spacing reduces the strength of HAZ.arrow_forward
arrow_back_ios
SEE MORE QUESTIONS
arrow_forward_ios
Recommended textbooks for you
- Elements Of ElectromagneticsMechanical EngineeringISBN:9780190698614Author:Sadiku, Matthew N. O.Publisher:Oxford University PressMechanics of Materials (10th Edition)Mechanical EngineeringISBN:9780134319650Author:Russell C. HibbelerPublisher:PEARSONThermodynamics: An Engineering ApproachMechanical EngineeringISBN:9781259822674Author:Yunus A. Cengel Dr., Michael A. BolesPublisher:McGraw-Hill Education
- Control Systems EngineeringMechanical EngineeringISBN:9781118170519Author:Norman S. NisePublisher:WILEYMechanics of Materials (MindTap Course List)Mechanical EngineeringISBN:9781337093347Author:Barry J. Goodno, James M. GerePublisher:Cengage LearningEngineering Mechanics: StaticsMechanical EngineeringISBN:9781118807330Author:James L. Meriam, L. G. Kraige, J. N. BoltonPublisher:WILEY
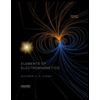
Elements Of Electromagnetics
Mechanical Engineering
ISBN:9780190698614
Author:Sadiku, Matthew N. O.
Publisher:Oxford University Press
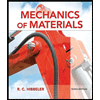
Mechanics of Materials (10th Edition)
Mechanical Engineering
ISBN:9780134319650
Author:Russell C. Hibbeler
Publisher:PEARSON
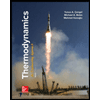
Thermodynamics: An Engineering Approach
Mechanical Engineering
ISBN:9781259822674
Author:Yunus A. Cengel Dr., Michael A. Boles
Publisher:McGraw-Hill Education
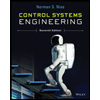
Control Systems Engineering
Mechanical Engineering
ISBN:9781118170519
Author:Norman S. Nise
Publisher:WILEY
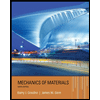
Mechanics of Materials (MindTap Course List)
Mechanical Engineering
ISBN:9781337093347
Author:Barry J. Goodno, James M. Gere
Publisher:Cengage Learning
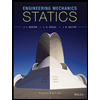
Engineering Mechanics: Statics
Mechanical Engineering
ISBN:9781118807330
Author:James L. Meriam, L. G. Kraige, J. N. Bolton
Publisher:WILEY