Quality Manual
docx
keyboard_arrow_up
School
Colorado Technical University *
*We aren’t endorsed by this school
Course
370-1802A-
Subject
Management
Date
Jan 9, 2024
Type
docx
Pages
14
Uploaded by GeneralStork3157
Quality Control Manual
Brittany Shoff
Colorado Technical University
BADM370: Quality Management
Johnny Maddox
08/20/2023
1
Quality Control Manual
Table of Contents
Week 1: Introduction
o
History of the quality management evolution……………………………………………. Pg.3-4
o
Why it is needed…………………………………………………………………………………………. Pg.4
Week 2: The Role of Leadership
o
Why it is a strategic issue……………………………………………………………………………. Pg.5
o
Management as a role model………………………………………………………………….…. Pg.6
o
New kinds of metrics…………………………………………………………………………….……. Pg.7
Week 3: General Quality Strategies and Tools
o
Establishing customer expectations……………………………………………………………. Pg.7, 8-9
o
Designing quality in……………………………………………………………………………………. Pg.7, 9-10
o
Defining metrics…………………………………………………………………………………………. Pg.8, 9-10
o
Mistake-proofing….……………………………………………………………………………………. Pg.8, 10
o
Kaizen…………………………………………………………………………………………………………. Pg.8, 10
o
Six Sigma……………………………………………………………………………………………………. Pg.8, 10-11
Week 4: Quality Tactics and the Logistics and Supply Chain Functions
o
What tools are applicable internally……………………………………………………………. Pg. 11
o
What tools are applicable externally with vendors………………………………………. Pg. 11-12
o
References………………………………………………………………..…………………………………. Pg. 13-14
Week 5: Roll-out
o
Strategic plan……
..........................
…………………….…………………………………………. Pg. 2
Quality Control Manual
Introduction
History of Quality Management Evolution We can date quality management back to the late 13th century when craftsmen began to organize unions
called guilds. Guilds took the responsibility for creating strict rules for product and service quality. They would have
inspection committees enforce these rules by giving the product of decent quality a special marking.
In the early 19
th
century is when we started to head into the industrial revolution. In these early years of
manufacturing in an industrialized word continued to follow the craftsmanship model. As the 1800s there was a
break from the craftsmen’s model in the United States practices for quality had evolved as changes to were made
to the predominant production methods. These changes began to happen as the divide from craftsmen trade to
specialized task. This would late be called the factory system. This would force craftsmen to become factory
workers and those that owned shops to be production supervisors. This also marked the decline in one’s sense of
empowerment in the workplace. This system ensures that skilled laborer’s quality would be done by audits or
inspections any defect to be found would either be reworked or scrapped.
Towards the late 19th century, the United States moved away from the European system and adopted an
innovative approach. This innovative approach was developed by Frederick W. Taylor with the goal to increase
productivity without being in more skilled craftsmen. Taylor was able to achieve this by giving factory planning to
specialize engineers, used the craftsmen as inspectors and those in management were to execute the engineers
plans. This would soon be known as The Taylor System. Even though the Taylor System led to a rise in productivity
it also led to more quality defects. To ensure that products of decent quality only reached the customer managers
instilled inspection departments to look for products that were defective.
As time move on, we come up to sometime after the United States joins World War II. During this time
quality was critical for the wars efforts and was an important safety issue. No one wanted unsafe military
equipment therefore measure was taken with every part of the equipment with inspection before they came to
the full unit. These inspected need a huge amount of people who were competent, but the armed forces had
3
Your preview ends here
Eager to read complete document? Join bartleby learn and gain access to the full version
- Access to all documents
- Unlimited textbook solutions
- 24/7 expert homework help
Quality Control Manual
difficulties recruiting and retaining the personnel. To help avoid this issue the armed forces began using sample
inspections to replace unit by unit inspection. The inspection we led by industrial consultants such as Bell
Laboratories, which were then adapted and published as military standards known as Mil-Std-105. Those who had
contracts with the military were expected to follow these standards. The armed forces helped Their supplies by
conducting training courses in Walter Shewharts SQC techniques to improve on quality. Now Shewharts recognized
that the industrial processes yelled data and with the data he could use it to analyze the processes to see whether
it’s stable or in need to be fixed. This laid out a foundation for Control chart and quality tools. After World War II engineers Deming and Juran would go onto collaborate with Japanese manufacturers
and come up with the concept of Total Quality. This focused on all the processes that were responsible for
production quality. Total Quality concept was applied to all over Japan. In America as they saw that the total
quality control concept for making leaps and bounds over in Japan around the 1980s American manufacturers
began to recognize total quality head started to apply it to their manufacturers. From there quality management
has been transformed to meet the needs of a changing marketplace that includes various factors including
globalization.
Why is it Needed?
Companies need to embrace the concept of quality management due to many reasons. First, they need
this concept to ensure that they are meeting the needs and to satisfy their customers this also will help in more of
a loyal customer base. Secondly, quality management helps with the preventing and minimizing of damages in a
company by ensuring greater levels of productivity. When a company has high level products, they’re more able to
satisfy. Lastly, quality management is there to help encourage the engagement of staff. This is the help give the
staff empowerment that they're being involved the decision-making process with doing so this gives them the
empowerment and the accountability for their actions. So also help Ensure that as products are leaving the line the
staff members are ensuring that the quality of said product is up to standards. Therefore, without the evolution of
quality management we as consumers would be left with low level quality products coming from Craftsman that
would only have been done in a local setting. With the evolution of quality management, we are given higher level
products at a global scale. (Week 1)
4
Quality Control Manual
The Role of Leadership
Why is it Strategic Issue?
Total Quality Management can help create a strategic focus within the whole business. This focus
is based on a continuous improvement that gives the customer what they need. Senior Management must
leave their employees to achieve the business goals and objectives. They help perform critical roles like
role models, instigators, cheerleading, resource providers, decision making, and facilitators. The Senior
managers are the role models for improvements, they use the data that they get from customers to help
guide them to the decision-making process. Employees look up to the managers for critical decision
making and before managers and those of higher-level management make any improvements and quality
at it any programs, they need to appoint an instigator. Instigators help in the developing and
implementing of strategies. By consulting with HR and creating trading programs for Quality
improvements. Once all is said and done the Senior Management well then act as the facilitators by
recognizing and rewarding the employees for the efforts that they put in to improving the quality.
Now let's look at an example of a company going through quality improvements. The Ritz-Carlton
hotel company set a clear path for continuous improvements, the developed a pyramid concept. Their
mission “To be the premier worldwide provider of luxury travel and hospitality products and services”
(
The Ritz-Carlton Hotel Company, L.L.C. NIST. 2022, May 19). The management team to the
opportunities in making improvements in a more systematic of their total quality management
system. They have also made more efforts in reducing employee turnovers and to improve their
morale. Their improvements got them the acknowledgment of the Baldrige Award that they won in
1992.
5
Quality Control Manual
Management as a Role Model
Management takes on the role of leaders the employees look up to for guidance and reassurance. Leaders
expect their employees to accomplish their assignments and manager are also there for the employees to confide in. In an organization, senior management is responsible to establish programs of strategic quality programs. They must also accurately collect data from customers to enable the organization to make quality improvements through performance measure such as failure statistics, customer surveys, complaints, lost in sales, returns, etc. Management needs to create an atmosphere that helps promote teamwork and promotes all the member of the team to make healthy decisions and better communications between them. Managers top responsibility is to assign the roles and responsibilities to personnel that will assist them in the development of total quality management. They must be able to isolate and identify the key issues during the decision making as well as to be able to formulate risk solutions. They can apply statistical methods to help with problem solving and use programs like statistical process control that will help improve all efforts in quality based on facts and data. If you think about
it Senior Management can be summed up as; promulgate the idea of total quality, set the standard for zero failure,
keep an eye on quality performance and to introduce programs on quality systems on prevention and not detection as well as processes for control methods.
Majority of firm’s adopt decision making roles for performance improvements. Decision making management will establish plans that include to improve the performance of employees and to develop reachable goals that they can attain. Once this Senior management decision making roles are established it will give the employees a better understanding on fact-based decision-making based on the performance management system. If these roles are not filled it leave an organization open to more problematic decision that can result in performance failures and quality issues.
6
Your preview ends here
Eager to read complete document? Join bartleby learn and gain access to the full version
- Access to all documents
- Unlimited textbook solutions
- 24/7 expert homework help
Quality Control Manual
New Kinds of Metrics
Senior and middle management should derive the metrics by their own standards and experiences that can provide him the best results. Using group meeting will help management to understand and give the steps to design what metrics are important, this also gets management involved to commit to set the stage for programs like defect management. Management will guide their employees by supervising and communicating new plans and policies. Program that they may want to bring in would be critical metrics. Critical metrics are used to implement more efficient results by comparing benchmarks, best practices, evaluating the efficacy and efficiency of the process and controlling for variances. Effective management can set and achieve goals and to make decisive action in demanding situations. (Week 2)
General Quality Strategies and Tools
Quality Metric Tactic
Definition
Risks
Value
Establishing Customer
Expectations
Are the needs, ideas and
feeling that a customer wants when purchasing a service or product.
This can bring a challenge for any organization to balance between their bottom-
line and what the customer wants.
This is the primary goal of every organization. Meeting the needs of their customers to continue to bring in business to where the customers feel valued in
some sense. Creating a base of loyal customers will help attract more business too.
Designing Quality
A strategic process to ensure the product is preforming as they should.
This looks at the internal
focus and the quality of the product that relies on performance, functionality, and safety.
This gives them the ability to tailor the product to the needs of the customers.
7
Quality Control Manual
Defining Metrics
Help with measuring the
quality of products and determine if they meet customer satisfaction.
This can lead to more resilience and cause a misunderstanding of the
nature of business and culture.
Keeps track of the performance cost through data and figures.
Mistake-proofing
Mistake-proofing is the technology that uses procedures to prevent defects.
The upfront investment in the design for mistake-proofing can cost more than expected and come up with some challenges like resistance from employees or customers.
This is good for reducing
defects and helps create
a better and more reliable end-product.
Kaizen
Is a Japanese term that says change is good or for continuous improvements.
when implemented into an existing system means that change can happen but if an organization don't welcome it can become a hard pillar to overcome.
The goal is quality control, just-in-time deliveries, standardized work, better equipment and reduce in waste and
cost.
Six Sigma
A tool to improve an organization process by reducing defects and errors and by increasing quality and efficiency.
Some of the risk can be a delay, halt, or some type of harm to an organization project.
This is good focus on reducing process and enhancing process control to where they can drive out waste and creates a competitive advantage.
Establishing Customer Expectations
Before an organization can even think about the product, they’re going to be selling they need to understand what kind a customer’s they plan on selling too. When organizations are starting up, they look at everything such as their marketing plan, the financial plan, their customer service plan but they tend to easily overlook their customer expectations and throw the entire plan into disarray. A customer’s expectations could 8
Quality Control Manual
have a huge impact on whether an organization is going to be successful or not. These expectations come in many different forms from quality, Time, the appearance and just about anything else in between. So, establishing customer expectations before any type of client relationship has been developed can prevent any type of buffoonery to happen. Once you have the clientele you really want to stick to your word to keep your customer relationship in high standards because once you can beat those expectations, you'll see that your customer retention rate to climb.
Designing Quality
As consumers we can have high expectations when looking for products so, as a business start the designing process. With this we are designing for a quality product. The are a number of things to consider when designing quality and here are where I find most consumers look at. First, does it perform the way it needed to? A business looked over all the operational characters of the design making sure they fit in with what the customer expects it does. Secondly, is the product reliability? Business needs to ensure that their product can Ensure any real-world conditions. For example: I forgot to remove my cellphone form my pocket before having a water gun battle with my kids. Thanks to the waterproof case it was in there was no water damage to the cellphone. Lastly, the customers experience with the product. This is an intangible element and is solely on how the product makes the customer feel. We can see this experience through survey, customer reviews and through retention rates.
Defining Metrics
Metrics give the company some type of insight into the quality of the product or service being sold. It also gives us an insight on where improvements need to be made whether it be in customer satisfaction or if new quality procedures need to be implemented. Metrics can start pulling data from ratings, customer complaints, defect rates, failure rates and quality control. As were able to see these metrics in real time the air able to provide us with much needed visibility into any issues that arise and can help us prevent any future issues. For any business
metrics are vital the business they help them determine whether they’re meeting not just customer satisfaction standards but also helps measure the quality of products.
9
Your preview ends here
Eager to read complete document? Join bartleby learn and gain access to the full version
- Access to all documents
- Unlimited textbook solutions
- 24/7 expert homework help
Quality Control Manual
Mistake-Proofing
Mistake-proofing proofing or poka-yoke which is the Japanese term for error prevention. This is the use of
some type of automatic device or even a method that can help make it impossible for an error to occur or to make it obvious that has occurred. This is only what we can see mistakes happening on humid arrow inside of the business but as well as customer error in using the product incorrectly. For example, if a customer enters a restaurant and the greeter is not there but is placing new customers at their new table or check again on a table, they become unaware that someone is waiting. That is why most businesses place sensors that signal one someone has entered the establishment. This eliminates the possibility of unhappy customers. Business use poka-
yoke to improve their processes to ensure better quality in products and service.
Kaizen Kaizen is the approach to continuous improvements to make positive change within the business. When going through this process of change you must keep the line off communication open and let good of what you thought you knew. This is e ever we start this look at everything from identifying issues to creating fresh solutions. There are seven steps to Kaizen those are getting the employees involved, getting a listen of the problems, finding a solution, evaluating the solution, analyze the results, adapt the solution, and repeat. You can also think of it as plan, do, check, and act. For example: Pixar studios make continuous improvement models in reducing risk to any expensive movie failures by making control checks and alternative processes. Kaizen efforts improve a business problem solving abilities by staying open-minded.
Six Sigma
Six sigma is a set of quality control tools that a business can use to eliminate any type of defects and to improve processes that could help boost their bottom line. This can be achieved by using the structure approach called DMAIC which stands for define, measure, analyze, improve, control. Six sigma is strict and uses data approaches when trying to achieve improvements and minimize defects. The six-sigma process is to identify the 10
Quality Control Manual
problem and solve the problem. Six sigma is a string type of framework that not only focuses on the data but customer satisfaction Through their feedback. This method of quality control is weirdly use in today’s business world. (Week 3)
Quality Tactics and the Logistics and Supply Chain Functions
What tools are applicable internally?
What are internal tools? They are totes of software application that help a business optimize their internal
operations. These tools are to help by increase productivity, efficiency, and can be cost-effective. There are some tools utilized and quality tactics and logistics that can influence quality management. Some of the internal tools that ensure quality management are the state of the machines used, the nature of communication within management, and the understanding the expectations of all shareholders within the organization and that can include transportation as well. Making sure the machinery is up to date and along with the technology software will happen sure that there are no system breakdowns that could lead to the production of unsatisfactory goods going out to the customer. Here are some tools that are beneficial for any business:
Data entry
Report generation
Business and project planning
Customer relationship management(CRM)
If we automate these routine tasks will be able to minimize errors, improve accuracy, and give the employees more important tasks to focus on. Internal tools can also help in identifying inefficiency and bottlenecking in their current process, giving the business the ability to strange at is max efficiency.
What tools are applicable externally with vendors
In our world today businesses are largely more technology driven and will fund at times that they cannot handle the demand that their customers and employees require. The are ways that businesses over chime this and one is by hiring vendors. Vendors can provide a business things like telecommunications, shipping options, and basic minerals. Tools that your vendor management team should use are template resources, risk management 11
Quality Control Manual
framework, vendor risk tools, inventory tracking, and vendor research. These tools help a business by giving them there employment to carry out their responsibilities more proactively and by having good management software for vendors can improve overall productivity.
Roll-Out
References
12
Your preview ends here
Eager to read complete document? Join bartleby learn and gain access to the full version
- Access to all documents
- Unlimited textbook solutions
- 24/7 expert homework help
Quality Control Manual
(
Week 1
)
Chiarini, A. (2011). Japanese total quality control, TQM, Deming’s system of profound knowledge, BPR, Lean and Six Sigma. International Journal of Lean Six Sigma
, 2
(4), 332–355. https://doi.org/10.1108/20401461111189425
Georgiev, S., & Ohtaki, S. (2016). Evolution and implementation of quality management practices in the manufacturing sector in Eastern Europe after the end of communism. International Journal of Quality & Reliability Management
, 33
(6), 804–829. https://doi.org/10.1108/ijqrm-03-2014-0030
Hamid, S. R., Isa, S., Chew, B. C., & Altun, A. (2019). Quality Management Evolution from the Past to Present: Challenges for Tomorrow. Organizacija
, 52
(3), 157–186. https://doi.org/10.2478/orga-2019-0011
(
Week 2
)
The Ritz-Carlton Hotel Company, L.L.C. | NIST. (2022). NIST
. https://www.nist.gov/baldrige/ritz-carlton-hotel-
company-llc
Kuei, C., & Lu, M. (2013). Integrating quality management principles into sustainability management. Total Quality Management & Business Excellence
, 24
(1–2), 62–78. https://doi.org/10.1080/14783363.2012.669536
Todorut, A. V., Cîrnu, D., & Niculescu, G. (2009). THE RELATION AMONG SIX SIGMA AND OTHER MANAGERIAL TECHNIQUES OF IMPROVING THE PERFORMANCES OF THE ORGANIZATIONS. Annals of the University of Petrosani: Economics
, 9
(4), 289–296. https://econpapers.repec.org/RePEc:pet:annals:v:9:i:4:y:2009:p:289-296
(
Week 3
)
Customer Expectations: What They Are and How to Improve Them
. (2023, March 11). https://www.indeed.com/career-advice/career-development/customer-expectations
Atta-Ankomah, R., Kubi, J. A., & Ackah, C. (2021). The Effect of Kaizen on Performance: Evidence from Manufacturing Enterprises in Ghana. The European Journal of Development Research
, 34
(2), 1167–1192. https://doi.org/10.1057/s41287-021-00459-0
What are Metrics and Why are they Important?
(n.d.). https://www.managementstudyguide.com/what-are-
metrics.htm
(
Week 4
)
Heskett, J. L. (2014). Logistics—Essential to Strategy
. https://hbr.org/1977/11/logistics-essential-to-strategy
Supply chain Quality Management
. (n.d.). TraceLink. https://www.tracelink.com/agile-supply-chain/supply-chain-
quality-management
13
Quality Control Manual
Adzija, R. (2022, February 28). Chapter 1 – The Role of Logistics in Supply Chains
. Pressbooks. https://ecampusontario.pressbooks.pub/logistics001oerfc/chapter/chapter-1/
O’Brien, S. (2023). Logistics | RingCentral UK blog. RingCentral UK Blog
. https://www.ringcentral.com/gb/en/blog/definitions/logistics/
Why quality tactics create great corporate strategies
. (n.d.). (C) [Site-date-yyyy] Quality Digest. https://www.qualitydigest.com/inside/statistics-article/why-quality-tactics-create-great-corporate-
strategies-092820.html
Achieving Quality Attributes through Tactics
. (n.d.). BrainKart. https://www.brainkart.com/article/Achieving-
Quality-Attributes-through-Tactics_11278/
14
Related Documents
Recommended textbooks for you
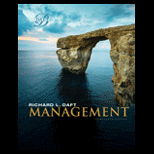
Management, Loose-Leaf Version
Management
ISBN:9781305969308
Author:Richard L. Daft
Publisher:South-Western College Pub
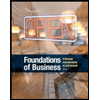
Foundations of Business (MindTap Course List)
Marketing
ISBN:9781337386920
Author:William M. Pride, Robert J. Hughes, Jack R. Kapoor
Publisher:Cengage Learning
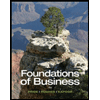
Foundations of Business - Standalone book (MindTa...
Marketing
ISBN:9781285193946
Author:William M. Pride, Robert J. Hughes, Jack R. Kapoor
Publisher:Cengage Learning
Recommended textbooks for you
- Management, Loose-Leaf VersionManagementISBN:9781305969308Author:Richard L. DaftPublisher:South-Western College PubFoundations of Business (MindTap Course List)MarketingISBN:9781337386920Author:William M. Pride, Robert J. Hughes, Jack R. KapoorPublisher:Cengage LearningFoundations of Business - Standalone book (MindTa...MarketingISBN:9781285193946Author:William M. Pride, Robert J. Hughes, Jack R. KapoorPublisher:Cengage Learning
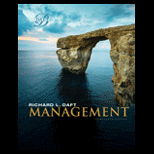
Management, Loose-Leaf Version
Management
ISBN:9781305969308
Author:Richard L. Daft
Publisher:South-Western College Pub
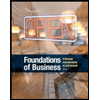
Foundations of Business (MindTap Course List)
Marketing
ISBN:9781337386920
Author:William M. Pride, Robert J. Hughes, Jack R. Kapoor
Publisher:Cengage Learning
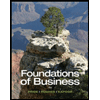
Foundations of Business - Standalone book (MindTa...
Marketing
ISBN:9781285193946
Author:William M. Pride, Robert J. Hughes, Jack R. Kapoor
Publisher:Cengage Learning