Module 2- Assigment
pdf
keyboard_arrow_up
School
Montclair State University *
*We aren’t endorsed by this school
Course
204
Subject
Management
Date
Apr 3, 2024
Type
Pages
4
Uploaded by Jaliaax3_
Your preview ends here
Eager to read complete document? Join bartleby learn and gain access to the full version
- Access to all documents
- Unlimited textbook solutions
- 24/7 expert homework help
Recommended textbooks for you
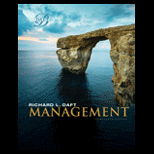
Management, Loose-Leaf Version
Management
ISBN:9781305969308
Author:Richard L. Daft
Publisher:South-Western College Pub
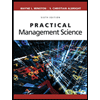
Practical Management Science
Operations Management
ISBN:9781337406659
Author:WINSTON, Wayne L.
Publisher:Cengage,
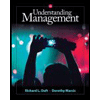
Understanding Management (MindTap Course List)
Management
ISBN:9781305502215
Author:Richard L. Daft, Dorothy Marcic
Publisher:Cengage Learning
Recommended textbooks for you
- Management, Loose-Leaf VersionManagementISBN:9781305969308Author:Richard L. DaftPublisher:South-Western College PubPractical Management ScienceOperations ManagementISBN:9781337406659Author:WINSTON, Wayne L.Publisher:Cengage,Understanding Management (MindTap Course List)ManagementISBN:9781305502215Author:Richard L. Daft, Dorothy MarcicPublisher:Cengage Learning
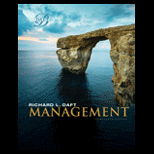
Management, Loose-Leaf Version
Management
ISBN:9781305969308
Author:Richard L. Daft
Publisher:South-Western College Pub
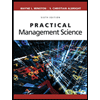
Practical Management Science
Operations Management
ISBN:9781337406659
Author:WINSTON, Wayne L.
Publisher:Cengage,
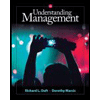
Understanding Management (MindTap Course List)
Management
ISBN:9781305502215
Author:Richard L. Daft, Dorothy Marcic
Publisher:Cengage Learning