Final. WBA DBM 623 OPERATIONS MANAGEMENT JULY-DECEMBER 2023 (1)
docx
School
Health Services Academy *
*We aren’t endorsed by this school
Course
2
Subject
Management
Date
Nov 24, 2024
Type
docx
Pages
8
Uploaded by BrigadierFlagPigeon17
WORK BASED ASSIGNMENET
ADMISSION NUMBER IN FULL:e.g:KIM/110000/19
SEMESTER: e.g. OCTOBER-MARCH 2023
UNIT/SUBJECT: e.g., BUSINESS MATHEMATICS
UNIT CODE: e.g. CCM 413
LECTURER:……………………………………………………………
DATE OF SUBMISSION:………………………………………….…..
NB:
WBA should be
handwritten
and detailed. Should be handed over during cat sitting time
without fail.
QUESTION ONE
1.
a) Discuss in details the emerging trends and issues in operation management.
One prominent trend is the growing adoption of advanced technologies like artificial intelligence, IoT,
and data analytics to optimize processes, enhance decision-making, and enable predictive maintenance.
Additionally, sustainability and environmental concerns have become integral, driving the focus
on green
operations and circular economy practices. The rise of e-commerce and customer expectations
for fast delivery has led to a surge in demand for efficient last-mile logistics. The shift towards remote
work has also necessitated flexible operational models. Lastly, the volatile global landscape and supply
chain disruptions have underscored the importance of risk management and resilience.
b)
Elaborate challenges and opportunities posed by the emerging trends and issues in
operation management.
The emerging trends and issues in operations management bring both challenges and
opportunities. Implementing new technologies can be costly and require upskilling the
workforce. Moreover, the complexity of data management and ensuring data privacy pose
challenges. Green operations entail redesigning processes, which might lead to initial costs but
offer long-term sustainability gains. Addressing last-mile logistics demands efficiency and
innovative delivery solutions. Remote work presents opportunities for cost reduction and talent
acquisition but can hinder collaboration. Supply chain disruptions highlight the need for robust
risk mitigation strategies.
c)
Discuss approaches you would employ to cope with opportunities and manage
challenges posed by the emerging issue and trends in operation s management.
To capitalize on opportunities and manage challenges, a multifaceted approach is necessary.
Embracing advanced technologies requires investment in training and infrastructure, and
partnering with tech providers can accelerate integration. Green operations demand collaboration
with suppliers and innovative process redesign while educating customers about sustainability
benefits. Enhancing last-mile logistics involves route optimization software, alternative delivery
methods like drones, and leveraging local distribution centers. For remote work, fostering a
virtual collaboration culture and using communication tools effectively is crucial. Addressing
supply chain disruptions necessitates diversification, dual sourcing, and building agile networks
to ensure uninterrupted supply.
d)
Differentiate between value engineering and value analysis in relation to product
and services analysis.
Value engineering and value analysis are distinct but related concepts in product and service
analysis. Value engineering focuses on improving the value of a product or service by optimizing
costs without compromising quality, often through re-evaluating materials, processes, or designs.
Value analysis, on the other hand, delves into existing products or services to identify
components or features that might not be necessary, aiming to eliminate waste and reduce costs.
Both approaches seek efficiency and cost-effectiveness, but value engineering involves broader
reimagining, while value analysis is more about incremental improvements.
e)
Expound on contributions of supply chain management in product and service
design.
Supply chain management significantly contributes to product and service design. It involves
collaboration with suppliers during the design phase to integrate their expertise and capabilities.
Early supplier involvement ensures manufacturability, cost efficiency, and access to innovative
components. Supply chain insights help in identifying potential risks and devising mitigation
strategies. Moreover, a well-structured supply chain enhances responsiveness to market
demands, reducing lead times and enabling quick adjustments in design. Effective supply chain
Your preview ends here
Eager to read complete document? Join bartleby learn and gain access to the full version
- Access to all documents
- Unlimited textbook solutions
- 24/7 expert homework help
management, therefore, fosters seamless integration between design, production, and
distribution, ultimately resulting in optimized products and services.
2.
a) Discuss how you’ll apply forecasting techniques in making operations projections
and decisions.
Forecasting techniques are crucial for making accurate operations projections and decisions by using
historical data and statistical methods to predict future trends. These techniques involve analyzing
patterns, seasonality, and other relevant factors to anticipate demand, resource requirements, and potential
challenges. By applying methods like time series analysis, moving averages, exponential smoothing, and
regression analysis, operations managers can make informed decisions regarding production levels,
inventory management, staffing, and capacity planning.
b)
Explain your understanding of forecasting as used in operations management.
Forecasting in operations management refers to the process of predicting future demand,
resource needs, and market trends to facilitate effective decision-making. It involves using
historical data and various quantitative and qualitative techniques to estimate the future state of a
business. By making accurate forecasts, operations managers can optimize inventory levels,
allocate resources efficiently, and enhance overall supply chain management.
c)
Explain elements of good forecast.
A good forecast encompasses several key elements, including accuracy, reliability, relevance,
timeliness, and clarity. Accuracy ensures that the forecast aligns closely with actual outcomes,
while reliability signifies consistent performance across different situations. Relevance involves
considering factors that directly impact the forecasted variable. Timeliness is crucial for timely
decision-making, and clarity ensures that the forecast's presentation and communication are
easily understandable by stakeholders.
d)
Discuss the two main types of forecasting methods in operations management
(qualitative and quantitative techniques). Giving well explained examples of each.
Operations management employs two main types of forecasting methods: qualitative and
quantitative. Qualitative techniques rely on expert judgment, market research, and subjective
insights. For instance, the Delphi method gathers opinions from experts to reach a consensus on
future trends. Quantitative techniques, on the other hand, involve numerical data analysis, such
as time series methods like moving averages and exponential smoothing. For example, a retail
store might use quantitative forecasting to predict future sales based on historical sales data and
trends.
e)
Discuss the steps in forecasting in operations management.
Forecasting in operations management follows a series of steps: data collection, data analysis,
choosing a forecasting method, generating a forecast, implementing the forecast, and monitoring
its accuracy. The process begins with collecting relevant historical data and conducting thorough
analysis to identify patterns and trends. Based on this analysis, an appropriate forecasting method
is selected and applied to generate predictions. Once implemented, regular monitoring of forecast
accuracy allows for adjustments and improvements as needed.
f)
How will you ensure accuracy and control of forecast in operations management?
Ensuring accuracy and control of forecasts in operations management involves continuous
validation and refinement. This can be achieved by comparing forecasted values with actual
outcomes and adjusting the methods accordingly. Using multiple forecasting techniques and
incorporating feedback from stakeholders can also enhance accuracy. Regularly updating
forecasts with new data and adjusting for changes in market conditions helps maintain control
and relevance.
g)
Expound on management of forecast.
The management of forecasts involves not only creating accurate predictions but also effectively
communicating and using those predictions for decision-making. This includes setting up a
structured process for data collection, analysis, and validation. Clear communication of forecast
assumptions, limitations, and risks is vital for guiding organizational decisions. Additionally,
forecasting management includes the establishment of accountability for forecast accuracy and
the ability to adapt strategies based on changing circumstances.
h)
Discuss both roles and application of forecasting in operations management.
Forecasting plays dual roles in operations management: strategic and operational. Strategically,
forecasting helps organizations plan for the future by identifying long-term trends and potential
opportunities or threats. Operationally, forecasting supports day-to-day decisions by predicting
short-term demand, enabling efficient resource allocation, production scheduling, and inventory
management. It aids in achieving a balance between meeting customer demands and avoiding
overstock or stockouts, ultimately contributing to optimized operational performance.
3.
a) Explain your understanding of benchmarking as used in operations management.
Benchmarking in operations management refers to the systematic process of comparing an
organization's performance, processes, or practices against those of leading competitors or
industry standards. It involves analyzing key performance indicators and identifying best
practices to understand where improvements can be made within an organization's own
operations.
b)
Discuss the purpose for benchmarking in operations management.
The primary purpose of benchmarking in operations management is to drive continuous
improvement. By comparing an organization's processes and performance to those of industry
leaders or best-in-class companies, organizations can identify areas for enhancement, set realistic
Your preview ends here
Eager to read complete document? Join bartleby learn and gain access to the full version
- Access to all documents
- Unlimited textbook solutions
- 24/7 expert homework help
performance targets, and implement effective strategies to optimize their operations, enhance
efficiency, and stay competitive in the market.
c)
Expound on different types of benchmarking in operations management.
In operations management, various types of benchmarking exist. These include internal
benchmarking, where comparisons are made between different units or departments within the
same organization; competitive benchmarking, which involves evaluating performance against
direct competitors; functional benchmarking, where comparisons extend to similar processes in
different industries; and generic benchmarking, which involves drawing insights from unrelated
industries to spark innovative solutions.
d)
Explain limitations of bench marking in operations management.
Despite its advantages, benchmarking in operations management has limitations. One limitation
is the potential difficulty in obtaining accurate and comparable data from external sources.
Additionally, blindly emulating best practices from other organizations without understanding
the underlying context can lead to suboptimal results. Over-reliance on benchmarking can stifle
innovation, as it encourages conformity rather than encouraging organizations to think outside
the box. Moreover, benchmarking is a snapshot in time and might not consider rapidly changing
market dynamics. Finally, successful benchmarking requires a commitment to change, and if an
organization lacks the necessary resources, expertise, or management support, the benchmarking
efforts may not yield the desired improvements. Despite its advantages, benchmarking in
operations management has limitations. One limitation is the potential difficulty in obtaining
accurate and comparable data from external sources. Additionally, blindly emulating best
practices from other organizations without understanding the underlying context can lead to
suboptimal results. Over-reliance on benchmarking can stifle innovation, as it encourages
conformity rather than encouraging organizations to think outside the box. Moreover,
benchmarking is a snapshot in time and might not consider rapidly changing market dynamics.
Finally, successful benchmarking requires a commitment to change, and if an organization lacks
the necessary resources, expertise, or management support, the benchmarking efforts may not
yield the desired improvements.
NOTE: I realized that some students skips some questions thinking that I won’t notice. Try this at your
own peril.
Charles.
Related Documents
Recommended textbooks for you
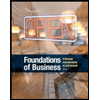
Foundations of Business (MindTap Course List)
Marketing
ISBN:9781337386920
Author:William M. Pride, Robert J. Hughes, Jack R. Kapoor
Publisher:Cengage Learning
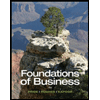
Foundations of Business - Standalone book (MindTa...
Marketing
ISBN:9781285193946
Author:William M. Pride, Robert J. Hughes, Jack R. Kapoor
Publisher:Cengage Learning
Recommended textbooks for you
- Foundations of Business (MindTap Course List)MarketingISBN:9781337386920Author:William M. Pride, Robert J. Hughes, Jack R. KapoorPublisher:Cengage LearningFoundations of Business - Standalone book (MindTa...MarketingISBN:9781285193946Author:William M. Pride, Robert J. Hughes, Jack R. KapoorPublisher:Cengage Learning
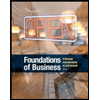
Foundations of Business (MindTap Course List)
Marketing
ISBN:9781337386920
Author:William M. Pride, Robert J. Hughes, Jack R. Kapoor
Publisher:Cengage Learning
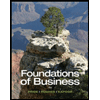
Foundations of Business - Standalone book (MindTa...
Marketing
ISBN:9781285193946
Author:William M. Pride, Robert J. Hughes, Jack R. Kapoor
Publisher:Cengage Learning