WBA DBM 624
docx
keyboard_arrow_up
School
Health Services Academy *
*We aren’t endorsed by this school
Course
5113
Subject
Management
Date
Nov 24, 2024
Type
docx
Pages
8
Uploaded by BrigadierFlagPigeon17
Q1. To prepare the process I and process II accounts, we need to calculate the following:
Calculate the cost of materials, labor, and overhead for each process.
Calculate the cost per unit for each process.
Calculate the normal loss for each process.
Calculate the cost of abnormal loss and abnormal gain for each process.
Calculate the total cost of production for each process.
Prepare the process accounts.
Let's start with Process I:
Process I Account for August 2019
Particulars
Amount (Sh)
Particulars
Amount (Sh)
Materials
Labor
Opening WIP
0
Opening WIP
0
Purchase
6,000 kg * 50
Direct Wages
24 hours * 200
Total Cost
300,000
Total Cost
4,800
Overheads (Absorbed)
71,400
Normal Loss
400 kg * 50
(80% of input)
-20,000
Closing WIP (4,600 kg)
?
Abnormal Loss
?
(6,000 kg - 4,600 kg)
?
Total Cost of Production
?
Total Cost of Abnormal Loss
?
To calculate the closing WIP and abnormal loss cost for Process I, we need to find the cost per unit (CPU) for both materials and labor. Then, we can calculate the closing WIP cost and abnormal loss cost.
Cost per Unit for Process I
Materials CPU = Total Materials Cost / Total Input Materials CPU = 300,000 Sh / 6,000 kg = 50 Sh/kg
Labor CPU = Total Labor Cost / Total Labor Hours Labor CPU = 4,800 Sh / 24 hours = 200 Sh/hour
Closing WIP for Process I
Closing WIP (in kg) = Input - Normal Loss Closing WIP (in kg) = 6,000 kg - 400 kg = 5,600 kg
Closing WIP Cost = (Closing WIP in kg) * (Materials CPU + Labor CPU) Closing WIP Cost = 5,600 kg * (50 Sh/kg + 200 Sh/hour) = 1,120,000 Sh
Abnormal Loss for Process I
Abnormal Loss (in kg) = Input - Closing WIP Abnormal Loss (in kg) = 6,000 kg - 5,600 kg = 400 kg
Abnormal Loss Cost = Abnormal Loss (in kg) * Materials CPU Abnormal Loss Cost = 400 kg * 50 Sh/kg = 20,000 Sh
Now, let's prepare the Process I Account:
Process I Account for August 2019
Particulars
Amount (Sh)
Particulars
Amount (Sh)
Materials
300,000
Labor
4,800
Opening WIP
0
Opening WIP
0
Purchase
300,000
Direct Wages
4,800
Total Cost
300,000
Total Cost
4,800
Overheads (Absorbed)
71,400
Normal Loss
-20,000
(80% of input)
Closing WIP (5,600 kg)
1,120,000
Abnormal Loss
20,000
(6,000 kg - 5,600 kg)
Total Cost of Production
1,491,400
Total Cost of Abnormal Loss
20,000
Now, let's move on to Process II:
Process II Account for August 2019
Particulars
Amount (Sh)
Particulars
Amount (Sh)
Materials
Labor
Opening WIP
0
Opening WIP
0
Purchase
4,000 kg * 80
Direct Wages
40 hours * 270
Total Cost
320,000
Total Cost
10,800
Overheads (Absorbed)
71,400
Normal Loss
600 kg * 80
(90% of input)
-48,000
Closing WIP (8,000 kg)
?
Abnormal Loss
?
(4,000 kg - 8,000 kg)
?
Total Cost of Production
?
Total Cost of Abnormal Loss
?
To calculate the closing WIP and abnormal loss cost for Process II, we need to find the cost per unit (CPU) for both materials and labor. Then, we can calculate the closing WIP cost and abnormal loss cost.
Cost per Unit for Process II
Materials CPU = Total Materials Cost / Total Input Materials CPU = 320,000 Sh / 4,000 kg = 80 Sh/kg
Labor CPU = Total Labor Cost / Total Labor Hours Labor CPU = 10,800 Sh / 40 hours = 270 Sh/hour
Closing WIP for Process II
Closing WIP (in kg) = Input - Normal Loss Closing WIP (in kg) = 4,000 kg - 600 kg = 3,400 kg
Closing WIP Cost = (Closing WIP in kg) * (Materials CPU + Labor CPU) Closing WIP Cost = 3,400 kg * (80 Sh/kg + 270 Sh/hour) = 1,248,000 Sh
Abnormal Loss for Process II
Abnormal Loss (in kg) = Input - Closing WIP Abnormal Loss (in kg) = 4,000 kg - 3,400 kg = 600 kg
Abnormal Loss Cost = Abnormal Loss (in kg) * Materials CPU Abnormal Loss Cost = 600 kg * 80 Sh/kg = 48,000 Sh
Now, let's prepare the Process II Account:
Your preview ends here
Eager to read complete document? Join bartleby learn and gain access to the full version
- Access to all documents
- Unlimited textbook solutions
- 24/7 expert homework help
Process II Account for August 2019
Particulars
Amount (Sh)
Particulars
Amount (Sh)
Materials
320,000
Labor
10,800
Opening WIP
0
Opening WIP
0
Purchase
320,000
Direct Wages
10,800
Total Cost
320,000
Total Cost
10,800
Overheads (Absorbed)
71,400
Normal Loss
-48,000
(90% of input)
Closing WIP (3,400 kg)
1,248,000
Abnormal Loss
48,000
(4,000 kg - 3,400 kg)
Total Cost of Production
1,591,400
Total Cost of Abnormal Loss
48,000
Now, we have prepared the Process I and Process II accounts.
Next, we will calculate the Abnormal Loss and Abnormal Gain accounts:
Abnormal Loss Account
Particulars
Amount (Sh)
Particulars
Amount (Sh)
To Process I Account
20,000
By Process II Account
48,000
Total
20,000
Total
48,000
Abnormal Gain Account
Particulars
Amount (Sh)
Particulars
Amount (Sh)
To Process II Account
20,000
By Process I Account
48,000
Total
20,000
Total
48,000
These accounts show the transfer of costs associated with abnormal losses and gains between Process I and Process II
Q2. i) The Balanced Scorecard Approach: The Balanced Scorecard is a strategic performance management framework that helps organizations translate their strategic objectives into a set of
balanced performance measures. It goes beyond traditional financial metrics and includes non-
financial measures related to customers, internal processes, and learning and growth. This approach provides a more comprehensive view of an organization's performance and helps align various departments and employees with the overall strategic goals.
ii) Kaizen Costing: Kaizen is a Japanese term that means continuous improvement. Kaizen costing is a cost management approach that emphasizes continuous cost reduction efforts through
small, incremental improvements in processes and operations. It encourages employees at all levels to identify and implement cost-saving measures, making it a bottom-up approach to cost control.
iii) Target Costing: Target costing is a proactive cost management approach used during the product design and development phase. It involves setting a target cost based on market conditions and customer expectations and then designing the product or service to meet that cost target. It promotes cost-conscious product development and helps companies remain competitive
in pricing.
iv) Lifecycle Costing: Lifecycle costing considers the total cost of a product or service over its entire lifecycle, including design, production, maintenance, and disposal phases. It helps organizations make informed decisions about product or service investments by considering long-term costs and benefits, environmental impact, and sustainability.
v) Benchmarking Cost Accounting: Benchmarking involves comparing an organization's cost and performance metrics against industry or competitor standards. It helps identify areas of improvement and best practices, leading to more effective cost management strategies and performance improvement.
vi) Activity-Based Costing (ABC): ABC is a costing method that allocates indirect and overhead costs to products or services based on the activities that drive those costs. It provides a more accurate and detailed understanding of cost drivers and helps organizations allocate costs more precisely, improving decision-making related to pricing, product mix, and process improvement.
vii) Strategic Cost Management: Strategic cost management focuses on aligning cost management practices with an organization's overall strategic objectives. It involves identifying and managing costs strategically to gain a competitive advantage, such as cost leadership, product differentiation, or market focus.
viii) Theory of Constraints: The Theory of Constraints (TOC) is a management philosophy that identifies and addresses bottlenecks or constraints within a production or operational process. TOC aims to maximize throughput and improve overall system performance by focusing resources on the most critical areas. It involves cost management strategies that prioritize resolving constraints.
ix) Human Resource Accounting: Human Resource Accounting involves quantifying the value of
an organization's human assets, such as skills, knowledge, and experience. It helps organizations assess the return on investment in their workforce and make more informed decisions regarding recruitment, training, and talent management.
x) Just-In-Time Systems: Just-In-Time (JIT) is a production and inventory management approach
that aims to reduce waste by producing and delivering products or components just in time for their use in the production process. It minimizes inventory holding costs, reduces production lead
times, and helps control production costs.
Q3. To calculate the material price variance, material usage variance, labor rate variance, and labor efficiency variance, you can use the following formulas:
i) Material Price Variance:
Material Price Variance = (Actual Quantity x Actual Price) - (Actual Quantity x Standard Price)
Material Price Variance = [(96,000 meters + 31,500 kg) x (Sh 100/meter for X + Sh 200/kg for Y)] - [(96,000 meters + 31,500 kg) x (Sh 100/meter for X + Sh 200/kg for Y)]
Material Price Variance = [(127,500) x (Sh 100 + Sh 200)] - [(127,500) x (Sh 100 + Sh 200)]
Material Price Variance = [Sh 12,750,000 + Sh 25,500,000] - [Sh 12,750,000 + Sh 25,500,000]
Material Price Variance = Sh 38,250,000 - Sh 38,250,000
Material Price Variance = Sh 0
ii) Material Usage Variance:
Material Usage Variance = (Standard Quantity x Standard Price) - (Actual Quantity x Standard Price)
Your preview ends here
Eager to read complete document? Join bartleby learn and gain access to the full version
- Access to all documents
- Unlimited textbook solutions
- 24/7 expert homework help
Material Usage Variance = [(50 meters x 1,950 units + 20 kg x 1,950 units) x (Sh 100/meter for X + Sh 200/kg for Y)] - [(96,000 meters + 31,500 kg) x (Sh 100/meter for X + Sh 200/kg for Y)]
Material Usage Variance = [(97,500 meters + 39,000 kg) x (Sh 100 + Sh 200)] - [(127,500) x (Sh
100 + Sh 200)]
Material Usage Variance = [Sh 13,950,000 + Sh 7,800,000] - [Sh 12,750,000 + Sh 25,500,000]
Material Usage Variance = Sh 21,750,000 - Sh 38,250,000
Material Usage Variance = -Sh 16,500,000
iii) Labor Rate Variance:
Labor Rate Variance = (Actual Hours x Actual Rate) - (Actual Hours x Standard Rate)
Labor Rate Variance = (31,000 hours x Sh 125/hour) - (31,000 hours x Sh 125/hour)
Labor Rate Variance = Sh 3,875,000 - Sh 3,875,000
Labor Rate Variance = Sh 0
iv) Labor Efficiency Variance:
Labor Efficiency Variance = (Actual Hours x Standard Rate) - (Standard Hours x Standard Rate)
Labor Efficiency Variance = (31,000 hours x Sh 125/hour) - (10 hours x 2,000 units x Sh 125/hour)
Labor Efficiency Variance = Sh 3,875,000 - Sh 2,500,000
Labor Efficiency Variance = Sh 1,375,000
So, the variances are as follows: i) Material Price Variance: Sh 0 ii) Material Usage Variance: -Sh
16,500,000 iii) Labor Rate Variance: Sh 0 iv) Labor Efficiency Variance: Sh 1,375,000
Related Documents
Recommended textbooks for you
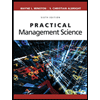
Practical Management Science
Operations Management
ISBN:9781337406659
Author:WINSTON, Wayne L.
Publisher:Cengage,
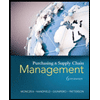
Purchasing and Supply Chain Management
Operations Management
ISBN:9781285869681
Author:Robert M. Monczka, Robert B. Handfield, Larry C. Giunipero, James L. Patterson
Publisher:Cengage Learning
Marketing
Marketing
ISBN:9780357033791
Author:Pride, William M
Publisher:South Western Educational Publishing
Recommended textbooks for you
- Practical Management ScienceOperations ManagementISBN:9781337406659Author:WINSTON, Wayne L.Publisher:Cengage,Purchasing and Supply Chain ManagementOperations ManagementISBN:9781285869681Author:Robert M. Monczka, Robert B. Handfield, Larry C. Giunipero, James L. PattersonPublisher:Cengage LearningMarketingMarketingISBN:9780357033791Author:Pride, William MPublisher:South Western Educational Publishing
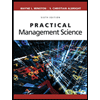
Practical Management Science
Operations Management
ISBN:9781337406659
Author:WINSTON, Wayne L.
Publisher:Cengage,
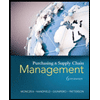
Purchasing and Supply Chain Management
Operations Management
ISBN:9781285869681
Author:Robert M. Monczka, Robert B. Handfield, Larry C. Giunipero, James L. Patterson
Publisher:Cengage Learning
Marketing
Marketing
ISBN:9780357033791
Author:Pride, William M
Publisher:South Western Educational Publishing