EEE435_RIE_Lab_v5
pdf
keyboard_arrow_up
School
Arizona State University *
*We aren’t endorsed by this school
Course
MISC
Subject
Chemistry
Date
Nov 24, 2024
Type
Pages
3
Uploaded by galil43
EEE435/591 Fundamentals of CMOS and MEMS Processing
1
RIE Laboratory (Revision 5)
Module 6 Laboratory
–
Reactive Ion Etching
Objective
: This lab provides an introduction to
reactive ion etching (RIE) using a PlasmaTherm 790
tool, see Fig. I. You will use the PT790 to etch an oxide
covered wafer and will measure the oxide thickness
before and after the etch step using the Filmetrics
F40. Based on these measurements you will
determine the etch rate of silicon dioxide (SiO2) as
well as the etch uniformity across the wafer.
Background
: Reactive ion etching is a plasma
technology that is widely used in semiconductor
manufacturing to etch metals, semiconductors, and
dielectric insulators such as silicon dioxide and silicon
nitride. RIE is a dry etch process that combines
chemical etching reactions with physical ion
bombardment. The dry etch process can be used to
produce an isotropic or anisotropic etch profile,
depending on the processing pressure and chemistry.
Figure II shows the differences between anisotropic
and isotropic etch profiles. The anisotropic etch
profile produces similar size transfer (W
initial
W
final
)
and the isotropic etch profile widens open features
(W
initial
< W
final
). The goal of most RIE processes is to
achieve highly anisotropic etching as this enables high
resolution transfer of patterns in the photoresist
masking layer into the underlying substrate material.
Dry etching does, however, have some disadvantages.
For example, the energetic ions used for the dry etch
processing can damage materials and adversely affect
the properties of the etched layers. This damage
includes crystal defects, implanted impurities,
damage due to ultraviolet radiation generated in the
plasma, and defects due to electrical charging of the
sample. Loading effects, or the dependence of etch
rate on feature size and local geometry, are also a
problem in dry etching. Furthermore, low etch
selectivity (e.g. erosion of the photoresist layer) is
also a problem. Resists that can withstand dry etch
processes by design or by treatment are often
difficult to remove after the dry etch process has
completed.
Figure I: ASU NanoFab PlasmaTherm 790
RIE tool for fluorine based etch chemistry.
Figure II: Anisotropic etch and isotropic
etch profiles.
EEE435/591 Fundamentals of CMOS and MEMS Processing
2
RIE Laboratory (Revision 5)
Typical RIE equipment is built around a vacuum chamber with two electrodes that create an
electric field which accelerates ions toward the substrate surface. The plasma is initiated by
applying RF power at 13.56 MHz to the cathode, whereas the anode is grounded. The electric
field ionizes the gas molecules, creating the plasma. A DC bias voltage, that forms on the
bottom RF-
powered electrode, extracts ions from the “bulk” plasma and energizes them. The
ions possess energies ranging from tens to hundreds of eV. The charged ions react with the
material’s surface to aid the chemical etch processes.
Experiment
: This lab will be divided into two stations: the Filmetrics and the PT790. Start by
measuring the thickness of the oxide prior to the etch step using the Filmetrics. Work with the
TA to r
ecord the initial ‘pre
-
etch’ oxide thickness at each of the locations shown in table of
Figure III below. Next perform a 2 minute etch of the oxide layer using the PT790. Record the
RIE process conditions in the table below being sure to include the correct units. Finally,
measure the oxide thickness after the etch and record the ‘post
-
etch’ valu
es. The TA will take
the measurements and post them on the Module 6 Canvas page.
Figure III: Table for recording the pre- and post-etch oxide thickness data at the locations shown across the wafer.
CHF
3
gas
flow
O
2
gas flow
Chamber
base
pressure
Chamber
process
pressure
RF Power
Anisotropic
SiO
2
etch
conditions
Units
Table for recording the PlasmaTherm 790 oxide etch recipe conditions.
Site
SiO2 Pre-Etch
Thickness (Å)
SiO2 Post-Etch
Thickness (Å)
Flat
Site 2
Site 3
Site 4
Site 5
Site 6
Site 7
Site 8
Site 9
Site 10
Site 11
Site 12
Site 13
Site 14
Site 15
Site 16
Site 17
Site 18
Site 19
Opposite
flat
EEE435/591 Fundamentals of CMOS and MEMS Processing
3
RIE Laboratory (Revision 5)
Writing-Up the Report
Executive Summary: A short paragraph that summarizes what you did and your
main findings. Think of this as the only part your busy manager might read before
you meet to explain the details.
[10 points]
Description of RIE Process: Describe how the etch is performed. How was the
wafer loaded into the etch tool? Explain the pump down sequence and the etch
‘recipe’ and gas chemistry used to etch the wafer. (1
-2 pages)
[40 points]
Analysis of the Etch Data: Calculate the mean etch rate and standard deviation
across the wafer for each RIE data set. Discuss the uniformity of the etching. In
particular, plot a graph of etch rate across the wafer look for systematic variations
across the wafer.
Describe what is meant by the RIE ‘bullseye effect’. Does your
plot show evidence for the bullseye effect? (2-4 pages)
[60 points]
Oxidised Wafer Etch: Based on the average etch rate calculate the time required
to etch a 200nm thick layer of wet oxide. Estimate the uncertainty in this time. (1-
2 pages)
[30 points]
Over Etch:
Explain why you need to include an ‘over etch’ to make sure all
the
oxide layer has cleared? Based on the measured data how long should the over
etch be to ensure that all the 200nm thick wet oxide has been removed? (<1
page)
[50 points]
Conclusions: This should be a short summary of the main results you achieved.
Again, think of your busy manager skipping through the report to the end to
confirm the main findings after he or she has read the executive summary.
[10 points]
Your preview ends here
Eager to read complete document? Join bartleby learn and gain access to the full version
- Access to all documents
- Unlimited textbook solutions
- 24/7 expert homework help
Related Documents
Related Questions
1. Pt is a face centered cubic metal with lattice parameter = 3.91Å. A bulk terminated
(100) surface is exposed to oxygen molecules which adsorb onto the surface, dissociate
into oxygen atoms and form the surface reconstruction shown below.
O Pt
a) Identify two ways of naming this reconstruction using Wood's notations.
b) What are the magnitudes of the reconstruction lattice parameters in each case?
arrow_forward
Readion Cone, Nay S0, Cine HCI|Ab. 1 | Rabe
I1.3085840
65.56796607
Cone, Nagd, 03
ATme (5)
0.10 M
·30M 04563164 |0.028 F09 13
,15 M 12267196|0.01870913
30M |1.5360817 0.300349
O.10 M
3
0.050 M
5. 11431671
4
0.025 M
0:30M
1.3686611
1,358380874
1.007568
3. What is the overall order of the reaction? Write the complete rate law for this reaction.
arrow_forward
What other method besides conductivity can be used to determine CMC (critical micelle concentration)?
arrow_forward
Bradford assay was used to determine bovine serum albumin (BSA) concentrations. The method works by binding
Coomassie Brilliant Blue dye to protein standards and unknown, leading to a shift in the absorbance maximum of the dye.
A stock solution of BSA is available (10 mg/ml) from which the protein standards were prepared. Bradford reagent, 290 ul,
was pipetted into a transparent 96-well microplate. 10 ul of the protein dilution was added followed by mixing in the wells.
After 5 min of incubation at room temperature, the plate was read in spectrum mode with the absorbance spectrometer of
the microplate reader. The spectrum of the dye not bound to protein was also determined. Create a standard curve or
regression equation that related the protein concentration and absorbance. An unknown BSA sample was prepared the
same way as the standard and the OD was 0.35. determine the original concentration of the protein solution.
The measurements can be seen below.
0.0625
Protein
Concentration…
arrow_forward
calculate the theoretical reciprocal linear dispersion of an echelle grating with a focal growth of 0.85m, a groove density of 120 grooves/mm, and a diffracion angle of 61 16 when the diffraction order is 30 and 90
arrow_forward
6.) An unknown polymer sample is fractionated, and the following molar fractions are
obtained. Calculate Mn and Mw and the dispersity. Fill out the table to show your work.
Fraction #
1
2
3
4
5
6
n₁ (mol)
0.004
0.011
0.009
0.003
0.017
0.008
M; (g/mol)
10,400
12,080
13,950
16,700
18,150
20,000
n¡Mi
n;M;²
arrow_forward
If light machinery oil has a viscosity of 5E-2 Pa-s and density of 970 kg/m³ at 25°C, how long will it take for a sample to pass through a viscometer if water under this condition takes 1 min? Density of water is 1000 kg/m³ and its viscosity is 8.9E-4 Pa-s.A. 36.5 minB. 47.7 minC. 57.9 minD. 64.4 min
arrow_forward
No need guideline answer if u provide guideline answer I will dislike ok
Module Code & Title: CHM9011M Chromatography and Sep Sciences
Description of Assessment Task and Purpose:
To prepare an SOP for the GC-MS Instrument
arrow_forward
22-30. (a) The mean free path is the average distance a molecule
travels before colliding with another molecule. The mean free
path, A, is given by A = kT/(V20P), where k is Boltzmann’s
constant, T is temperature (K), P is pressure (Pa), and o is the
collision cross section. For a molecule with a diameter d, the col-
lision cross section is nd. The collision cross section is the area
swept out by the molecule within which it will strike any other
molecule it encounters. The magnetic sector mass spectrometer is
maintained at a pressure of ~103 Pa so that ions do not collide
with (and deflect) one another as they travel through the mass
analyzer. What is the mean free path of a molecule with a diam-
eter of 1 nm at 300 K in the mass analyzer?
arrow_forward
Calculate the composite modulus for polyester reinforced with 30 vol % Al2O3 whiskers under isostrain conditions. (For polyester, E = 6900 MPa. For Al2O3 whiskers E= 430 × 10³ MPa.)
Express your answer to three significant digits.
15| ΑΣΦ
The composite modulus is
Submit Request Answer
vec
6
?
MPa.
arrow_forward
Do not give handwriting solution
Using 0.901 g/cm3 for density of tri - isopropylsilanol (i-C3H7)3SiOH and assuming spherical shape of the molecule, determine its molecular cross section and the maximal grafting density for these molecules supported on a flat silica surface.
arrow_forward
SEE MORE QUESTIONS
Recommended textbooks for you
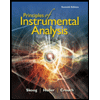
Principles of Instrumental Analysis
Chemistry
ISBN:9781305577213
Author:Douglas A. Skoog, F. James Holler, Stanley R. Crouch
Publisher:Cengage Learning
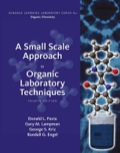
EBK A SMALL SCALE APPROACH TO ORGANIC L
Chemistry
ISBN:9781305446021
Author:Lampman
Publisher:CENGAGE LEARNING - CONSIGNMENT
Related Questions
- 1. Pt is a face centered cubic metal with lattice parameter = 3.91Å. A bulk terminated (100) surface is exposed to oxygen molecules which adsorb onto the surface, dissociate into oxygen atoms and form the surface reconstruction shown below. O Pt a) Identify two ways of naming this reconstruction using Wood's notations. b) What are the magnitudes of the reconstruction lattice parameters in each case?arrow_forwardReadion Cone, Nay S0, Cine HCI|Ab. 1 | Rabe I1.3085840 65.56796607 Cone, Nagd, 03 ATme (5) 0.10 M ·30M 04563164 |0.028 F09 13 ,15 M 12267196|0.01870913 30M |1.5360817 0.300349 O.10 M 3 0.050 M 5. 11431671 4 0.025 M 0:30M 1.3686611 1,358380874 1.007568 3. What is the overall order of the reaction? Write the complete rate law for this reaction.arrow_forwardWhat other method besides conductivity can be used to determine CMC (critical micelle concentration)?arrow_forward
- Bradford assay was used to determine bovine serum albumin (BSA) concentrations. The method works by binding Coomassie Brilliant Blue dye to protein standards and unknown, leading to a shift in the absorbance maximum of the dye. A stock solution of BSA is available (10 mg/ml) from which the protein standards were prepared. Bradford reagent, 290 ul, was pipetted into a transparent 96-well microplate. 10 ul of the protein dilution was added followed by mixing in the wells. After 5 min of incubation at room temperature, the plate was read in spectrum mode with the absorbance spectrometer of the microplate reader. The spectrum of the dye not bound to protein was also determined. Create a standard curve or regression equation that related the protein concentration and absorbance. An unknown BSA sample was prepared the same way as the standard and the OD was 0.35. determine the original concentration of the protein solution. The measurements can be seen below. 0.0625 Protein Concentration…arrow_forwardcalculate the theoretical reciprocal linear dispersion of an echelle grating with a focal growth of 0.85m, a groove density of 120 grooves/mm, and a diffracion angle of 61 16 when the diffraction order is 30 and 90arrow_forward6.) An unknown polymer sample is fractionated, and the following molar fractions are obtained. Calculate Mn and Mw and the dispersity. Fill out the table to show your work. Fraction # 1 2 3 4 5 6 n₁ (mol) 0.004 0.011 0.009 0.003 0.017 0.008 M; (g/mol) 10,400 12,080 13,950 16,700 18,150 20,000 n¡Mi n;M;²arrow_forward
- If light machinery oil has a viscosity of 5E-2 Pa-s and density of 970 kg/m³ at 25°C, how long will it take for a sample to pass through a viscometer if water under this condition takes 1 min? Density of water is 1000 kg/m³ and its viscosity is 8.9E-4 Pa-s.A. 36.5 minB. 47.7 minC. 57.9 minD. 64.4 minarrow_forwardNo need guideline answer if u provide guideline answer I will dislike ok Module Code & Title: CHM9011M Chromatography and Sep Sciences Description of Assessment Task and Purpose: To prepare an SOP for the GC-MS Instrumentarrow_forward22-30. (a) The mean free path is the average distance a molecule travels before colliding with another molecule. The mean free path, A, is given by A = kT/(V20P), where k is Boltzmann’s constant, T is temperature (K), P is pressure (Pa), and o is the collision cross section. For a molecule with a diameter d, the col- lision cross section is nd. The collision cross section is the area swept out by the molecule within which it will strike any other molecule it encounters. The magnetic sector mass spectrometer is maintained at a pressure of ~103 Pa so that ions do not collide with (and deflect) one another as they travel through the mass analyzer. What is the mean free path of a molecule with a diam- eter of 1 nm at 300 K in the mass analyzer?arrow_forward
- Calculate the composite modulus for polyester reinforced with 30 vol % Al2O3 whiskers under isostrain conditions. (For polyester, E = 6900 MPa. For Al2O3 whiskers E= 430 × 10³ MPa.) Express your answer to three significant digits. 15| ΑΣΦ The composite modulus is Submit Request Answer vec 6 ? MPa.arrow_forwardDo not give handwriting solution Using 0.901 g/cm3 for density of tri - isopropylsilanol (i-C3H7)3SiOH and assuming spherical shape of the molecule, determine its molecular cross section and the maximal grafting density for these molecules supported on a flat silica surface.arrow_forward
arrow_back_ios
arrow_forward_ios
Recommended textbooks for you
- Principles of Instrumental AnalysisChemistryISBN:9781305577213Author:Douglas A. Skoog, F. James Holler, Stanley R. CrouchPublisher:Cengage LearningEBK A SMALL SCALE APPROACH TO ORGANIC LChemistryISBN:9781305446021Author:LampmanPublisher:CENGAGE LEARNING - CONSIGNMENT
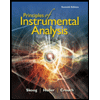
Principles of Instrumental Analysis
Chemistry
ISBN:9781305577213
Author:Douglas A. Skoog, F. James Holler, Stanley R. Crouch
Publisher:Cengage Learning
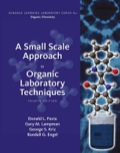
EBK A SMALL SCALE APPROACH TO ORGANIC L
Chemistry
ISBN:9781305446021
Author:Lampman
Publisher:CENGAGE LEARNING - CONSIGNMENT