Chapter 2 Reading
pdf
keyboard_arrow_up
School
Washington State University *
*We aren’t endorsed by this school
Course
338
Subject
Accounting
Date
Nov 24, 2024
Type
Pages
30
Uploaded by AgentGalaxy781
Chapter Introduction
The study of cost accounting and cost management requires an understanding of fundamental
cost concepts, terms, and the associated information systems that produce them
We need a basic framework to help us make sense of the variety of topics that appear in the
field of cost accounting and cost management
A systems perspective provides a useful framework for achieving this objective
But what is an
information system?
Are there different systems for different
purposes? Similarly, what is meant by
cost?
Are there different costs for
different purposes?
This chapter addresses these basic questions and provides the necessary
foundation for the study of the rest of the text
In providing this foundation, we make no attempt to be exhaustive
in our coverage of different systems and costs
Other system and cost concepts will be discussed in later
chapters
However, a thorough understanding of the concepts
presented in this chapter is essential for success with
later chapters
–
◊
□
○
-
2-1 A Systems Framework
A system is a set of interrelated parts that performs one or more processes to accomplish specific
objectives
Consider a home theater system
This system has a number of interrelated parts such as the speakers, the receiver, the
amplifier, the television, and the DVD player
The most obvious process (or series of actions designed to accomplish an
objective) is the playing of a movie; another is the delivery of surround sound
throughout the room
The primary objective of the system is to provide a theater-quality
experience while watching a movie
Notice that each part of the system is critical for achievement of the
overall objective
For example, if the speakers were missing, the amplifier and
receiver would not be able to provide theater-quality sound
even if the other parts were present and functional
◊
□
○
-
A system works by using processes to transform inputs into outputs that satisfy the system’s
objectives
Consider the movie-playing process
This process requires inputs such as a movie (typically on Blu-ray or DVD), a Blu-ray or
DVD player, a television set, and electricity
The inputs are transformed into the replay of the movie, an output of this
process
The output of the process, delivery of surround sound, is obviously critical
to achieving the overall objective of the system
The encoded sound on the DVD, the amplifier, and the speakers
become inputs to the delivery process
This process transforms the inputs so that tracks of sound are
delivered to each of the speakers throughout the room
In this way, the theater experience is reproduced at
–
◊
□
○
-
Chapter 2: Basic Cost Management Concepts
Saturday, November 4, 2023
9:44 PM
Week 1 Page 1
In this way, the theater experience is reproduced at
home (minus, of course, the people on cell phones or
the sticky floors that are all too often part of the theater
experience)
The operational model for the home theater
experience is shown in Exhibit 2.1
–
Exhibit 2.1 Operational Model of the Home Theater System
○
-
2-1a Accounting Information Systems
An information system is designed to provide information to people in the company who might
need it
For example, the human resource (HR) information system and materials requirements
planning (MRP) system are both information systems
The HR system tracks people as they are hired. It includes data on date of hire, entry-
level title and salary/wages, and any information needed for determining employee
benefits
The MRP is a computerized system that keeps track of the purchase and use of raw
materials used in manufacturing
These systems may also have subsystems
For example, a subsystem of the HR system is the payroll system
This is a transaction processing system
The payroll system uses information from the HR database along
with information on taxes and benefits needed to pay the
employees and to remit appropriate amounts to various
governmental agencies, in order to process periodic payroll
transactions
◊
□
○
-
An accounting information system is one that consists of interrelated manual and computer parts
and uses processes such as collecting, classifying, summarizing, analyzing, and managing data to
provide information to users
-
Week 1 Page 2
provide information to users
Like any system, an accounting information system has objectives, interrelated parts,
processes, and outputs
The overall objective of an accounting information system is to provide information to
users
The interrelated parts include database(s) and database management programs
The databases are simply collections of data or information, usually in
digital form
The database management system is needed to control, maintain,
and use a given database
For accounting purposes, databases are formed to keep track
of orders, sales, and other transactions
◊
The database management system allows the company to handle billing,
accounts receivable and cash receipts, inventory, general ledger, and cost
accounting
Each of these interrelated parts is itself a system and is therefore
referred to as a
subsystem
of the accounting information system
Processes of the database management system may include
collecting, classifying, summarizing, and managing data
Some processes may also be formal decision models—
models that use inputs and provide recommended
decisions as the information output
The outputs are data and reports that provide
needed information for users.
–
◊
□
○
Two key features of the accounting information system distinguish it from other information
systems
First, an accounting information system’s inputs are usually economic events
○
Second, the operational model of an accounting information system is critically involved
with the user of information, since the output of the information system influences users
and may serve as the basis for action
This is particularly true for tactical and strategic decisions but less true for day-to-day
decisions
In other cases, the output may serve to confirm that the actions taken had the
intended effects
Another possible output is feedback, which becomes an input for subsequent
operational system performance
The operational model for an accounting information system is illustrated
in Exhibit 2.2
Examples of the inputs, processes, and outputs are provided in the
exhibit
(The list is not intended to be exhaustive.)
Notice that personal communication is an information
output
Often, users may not wish to wait for formal
reports and can obtain needed information on a
timelier basis by communicating directly with
accountants
–
◊
□
○
-
Exhibit 2.2 Operational Model of an Accounting Information System
-
Week 1 Page 3
Your preview ends here
Eager to read complete document? Join bartleby learn and gain access to the full version
- Access to all documents
- Unlimited textbook solutions
- 24/7 expert homework help
○
The accounting information system can be divided into two major subsystems: (1) the
financial
accounting information system
and (2) the
cost management information system
While we emphasize the second, it should be noted that the two systems need not be
independent
Ideally, the two systems should be integrated and have linked databases
Output of each of the two systems can be used as input for the other system.
□
○
-
Financial Accounting Information System
The financial accounting information system is primarily concerned with producing outputs
for
external
users
It uses well-specified economic events (e.g., payment of wages, purchases of
materials) as inputs, and its processes follow certain rules and conventions
For financial accounting, the nature of the inputs and the rules and conventions
governing processes are defined by the Securities and Exchange Commission
(SEC), the Financial Accounting Standards Board (FASB), and potentially the
International Accounting Standards Board (IASB)
Among its outputs are financial statements such as the balance sheet,
income statement, and statement of cash flows for external users
(investors, creditors, government agencies, and other outside users)
Financial accounting information is used for investment decisions,
stewardship evaluation, activity monitoring, and regulatory
measures
◊
□
○
-
The Cost Management Information System
The cost management information system is primarily concerned with producing outputs
for
internal
users using inputs and processes needed to satisfy management objectives
The cost management information system is not bound by externally imposed criteria
that define inputs and processes
Instead, the criteria that govern the inputs and processes are set by people in
the company
The cost management information system provides information for three
broad objectives:
Costing services, products, and other objects of interest to
management
1.
Planning and control
2.
Decision making
3.
□
○
How much does a product or service cost?
That depends on the reason why management wants to know the cost
For example, product costs calculated in accordance with GAAP (Generally
Accepted Accounting Principles) are needed to value inventories for the balance
sheet and to calculate the cost of goods sold expense on the income statement
These product costs include the cost of materials, labor, and overhead
□
In other cases, managers may want to know all costs that are associated with a service
for purposes of tactical and strategic profitability analysis
For example, a bank might want to know the costs and revenues associated with
providing small business loans
□
○
-
Week 1 Page 4
providing small business loans
Then additional cost information may be needed concerning service
provision, the cost of funds, collection costs, and so on
Cost information is also needed for planning and control.
It should help managers decide what should be done, why it should be done, how it
should be done, and how well it is being done
For example, pharmaceutical companies may want to consider life cycle costing
of individual drugs or drug families
The expected revenues and costs may cover the entire life of the new
product
Thus, projected costs of research, development, testing, production,
marketing, distribution, and servicing would be essential
information
These costs form the basis of the value chain
◊
□
○
The value chain is the set of activities required to design, develop, produce, market, deliver,
and provide post-sales service for the products and services sold to customers
Exhibit 2.3 illustrates the business processes of the value chain
Emphasizing customer value forces managers to determine which activities in
the value chain are important to customers
The cost management information system should track information about
the wide variety of activities that span the value chain
Consider, for example, the delivery segment
Timely delivery of a product or service is part of the total
product and, thus, is of value to the customer
Customer value can be increased by increasing the
speed of delivery and response
Federal Express exploited this part of the value
chain and successfully developed a service that
was not being offered by the U.S. Postal Service
Today, many customers believe that
delivery delayed is delivery denied
This indicates that a good cost
management information system
ought to develop and measure
indicators of customer satisfaction
–
◊
□
○
Exhibit 2.3 The Value Chain
-
Week 1 Page 5
○
Companies have internal customers as well
For example, the procurement process acquires and delivers parts and materials to
producing departments
Providing high-quality parts on a timely basis to managers of producing departments
is just as vital for procurement as it is for the company as a whole to provide high-
quality goods to external customers
The emphasis on managing the internal value chain and servicing internal
customers has revealed the importance of a cross-functional perspective
□
○
-
Finally, cost information is important for many managerial decisions
For example, a manager may need to decide whether to continue making a component in-
house or to buy it from an external supplier
In this case, the manager would need to know the cost of materials, labor, and other
productive resources associated with the manufacture of the component and which of
these costs would disappear if the product were no longer produced
Also needed is information about the cost of purchasing the component,
including any increase in cost for internal activities such as receiving and storing
goods
□
○
-
2-1b Relationship to Other Operational Systems and Functions
The cost information produced by the cost management information system benefits the whole
organization and should have an organization-wide perspective
Managers in many different areas of a business require cost information
For example, an engineering manager must make strategic decisions concerning
product design
Later costs of production, marketing, and servicing can vary widely, depending
on the design
An engineer at Hewlett-Packard once told us that 70 percent of eventual
product costs are “locked in” during the design process
□
To provide accurate cost information for the different design options, the cost
management system must not only interact with the design and development system
but also with the production, marketing, and customer service systems
Cost information for tactical decision making is also important
For example, a sales manager needs reliable and accurate cost
information when faced with a decision concerning an order that may be
□
○
-
Week 1 Page 6
Your preview ends here
Eager to read complete document? Join bartleby learn and gain access to the full version
- Access to all documents
- Unlimited textbook solutions
- 24/7 expert homework help
information when faced with a decision concerning an order that may be
sold for less than the normal selling price
Such a sale may only be feasible if the production system has idle
capacity. In this case, a sound decision requires interaction among
the cost management system, the marketing and distribution
system, and the production system
◊
These two examples illustrate that the cost management system should have an
organization-wide perspective and that it must be properly integrated with the
nonfinancial functions and systems within an organization
In the past, little effort was made to integrate the cost management system
with other operational systems
The current competitive environment, however, dictates that companies
pay much greater attention to cost management in all functional areas
□
An integrated cost management system receives information from and provides information to all
operational systems
To the extent possible, the cost management system should be integrated with the
organization’s operational systems
Integration reduces redundant storage and use of data, improves the timeliness of
information, and increases the efficiency of producing reliable and accurate
information
One way of accomplishing this is to implement an enterprise resource planning
(ERP) system
ERP systems are integrative, cross-functional systems that coordinate
information to facilitate timely and accurate reporting and decision
making
Ideally, in an ERP system, data must be input only once; then it is
available to people across the company for whatever purpose it
may serve.
In this way, information collected for one need may be used
for others as well
For example, a sales order entered into an ERP system is
used by marketing to update customer records, by
production to schedule the manufacture of the goods
ordered, and by accounting to record the sale
–
◊
□
○
-
2-1c Different Systems for Different Purposes
The financial accounting and cost management systems show us that different systems exist to
satisfy different purposes
As indicated, these two systems are subsystems of the accounting information system
The cost management information system also has two major subsystems: the
cost
accounting information system
and the
operational control information system
The objectives of these two subsystems correspond to the first and second
objectives mentioned earlier for the cost management information system (the
costing, and planning and control objectives)
The output of these two cost systems satisfies the third objective (the
decision-making objective)
□
○
-
The cost accounting information system is a cost management subsystem designed to assign costs
to individual products and services and other objects of interest to managers
For external financial reporting, the cost accounting system must assign costs to products in
order to value inventories and determine cost of sales
Furthermore, these assignments must conform to the rules and conventions set by
the SEC, the FASB, and (potentially) the IASB
These rules and conventions do not require that all costs assigned to individual
products be causally related to the demands of individual products
Thus, using financial accounting principles to define product costs may
□
○
-
Week 1 Page 7
Thus, using financial accounting principles to define product costs may
lead to under- and overstatements of individual product costs
For reporting inventory values and cost of sales, this may not matter
Inventory values and cost of sales are reported in the
aggregate, and the under- and overstatements may wash out
to the extent that the values reported on the financial
statements are reasonably accurate
◊
At the individual product level, however, distorted product costs can cause managers to make
poor decisions
For example, a manager might erroneously deemphasize and overprice a product that is, in
reality, highly profitable at a lower price
○
For decision making, accurate product costs are needed
If possible, the cost accounting system should produce product costs that
simultaneously are accurate and satisfy financial reporting conventions
If not, then the cost system must produce two sets of product costs: one that satisfies
financial reporting criteria and one that satisfies management decision-making needs
○
-
The operational control information system is a cost management subsystem designed to provide
accurate and timely feedback concerning the performance of managers and others relative to
their planning and control of activities
It helps to ensure that the day-to-day activities support the long-range strategic objectives
of the organization
Operational control is concerned with determining what activities should be
performed and assessing how well they are performed
It identifies opportunities for improvement
A good operational control information system provides information that
helps managers engage in a program of continuous improvement of all
aspects of their businesses
□
○
-
While product cost information is important to this process, it is not sufficient
The information needed for planning and control is broader and encompasses the entire
value chain
For example, every profit-making manufacturing and service organization exists to
serve customers
Thus, one objective of an operational control system is to improve the value received
by customers
Products and services should be produced that fit specific customer needs
(Observe how this affects the design and development system in the value
chain.)
Quality, affordable prices, and low post-purchase costs for
operating and maintaining the product are also important to
customers
◊
□
○
-
A second, related objective is to improve profits by providing this value
Well- designed, quality, affordable products can be offered only if they also provide an
acceptable return to company owners
Cost information concerning quality, different product designs, and post-purchase
customer needs is vital for managerial planning and control
○
-
Exhibit 2.4 illustrates the various subsystems of the accounting information system that we have
been discussing
-
Exhibit 2.4 Subsystems of the Accounting Information System
-
Week 1 Page 8
○
2-2 The Growing Importance of Data Analytics within Cost Management
Organizations operate in an increasingly complex and interconnected global business environment
As a result, organizational decisions impact investors and other key stakeholders, such as
employees, customers, suppliers, regulators, and community residents, in increasingly broad
and deep ways
The rapid expansion in the amount of data available to organizations and their
stakeholders presents an important opportunity increasingly used by organizations to
better understand and manage their impacts within this business environment
For example, accounting experts estimate that the size of the digital universe,
including the amounts of traditional business data and rapidly growing machine-
generated data, grows exponentially by doubling every two years
Not surprisingly, organizations increasingly expect accountants to be able
to collect, transform, and incorporate such data—also known as
big
data
—into various cost management analyses to improve organizational
decisions
Data analytics represents the process through which an
organization utilizes various amounts and types of data to help
connect strategy and other key goals to improved decision making
throughout the organization
Developing accounting expertise with data analytics requires
a concerted effort and wide-ranging practice
Therefore, each chapter in this book emphasizes, where
appropriate, the role played by data analytics in various
cost management analyses
–
◊
□
○
-
2-2a A Framework for Understanding the Role of Data Analytics in Cost Management
Exhibit 2.5 presents an overview of the broad role that data analytics plays within various cost
management analyses
Traditionally, data analytics in cost management has been defined rather narrowly by
focusing primarily on the use of analytical methods within various scenario models, such as
relatively simple high-low analyses or more complex regression analyses
Such analytical methods remain important
However, accountants must define data analytics much more broadly in order
to be able to provide value-adding insights to business decision makers
□
○
-
Exhibit 2.5 The Role of Data Analytics in Cost Management
Step
Core
Issue
Question Answered
Cost Management Application Example
1
What
What am I measuring?
The cost of innovating Apple’s product and
-
Week 1 Page 9
Your preview ends here
Eager to read complete document? Join bartleby learn and gain access to the full version
- Access to all documents
- Unlimited textbook solutions
- 24/7 expert homework help
1
What
What am I measuring?
The cost of innovating Apple’s product and
service offerings, including the cost objects
(e.g., research and development) involved with
such innovation efforts.
2
Why
Why am I measuring
it?
Apple’s strategy requires that it strives for
continuous and industry-leading innovation.
3
How
How am I measuring
it?
Consider the cost drivers (e.g., activities
required by cutting-edge scientists and new
product engineers; laboratory and testing
facilities) for Apple’s continuous innovation cost
objects.
4
Where
Where can I find the
data needed to
conduct my desired
statistical analysis?
Apple can collect and analyze in-house data
regarding the existence and performance of its
new product features as compared to external
data regarding competitors’ product offerings.
5
Which
Which analytical
method should be
employed in my
analysis?
Time-series multiple regression analyses of
Apple’s core innovation activity drivers help
management better understand the
relationship between various research and
development costs and innovation outcomes.
6
When
When is my analysis
complete and ready to
be used in decision
making?
Apple’s newest innovation involves a first-
mover product launch, and thus, the cost
analysis concludes sooner because the profit
margin is wider for mature products that face
more competition.
7
Who
Who in the business
needs to understand
my analysis, and how
should I communicate
its results?
An innovation cost analysis helps sales
personnel better understand which new
product features are more or less costly and
relies on less sophisticated statistical and
accounting terminology as compared to an
analysis intended for product engineers.
Therefore, before crunching numbers using analytical methods, accountants should begin their
data analytic journey by clearly understanding
what
they are trying to measure, as well as
why
it
should be measured
For example, an item should be measured when doing so is expected to provide important
decision insights, such as assessing the success or failure of the company’s strategy
On the contrary, an item should not be measured simply because the underlying data
are available or because other companies measure it
Such unnecessary efforts often waste resources and divert attention away from
potentially more valuable uses of limited data analytic resources
□
○
Finally, understanding the why of data analytics also provides useful insights into how
accurate the measure must be, given the decision it ultimately intends to inform
For example, the framework likely would be employed more intensely to a decision
involving the discontinuation of an entire product line rather than to the
discontinuation of only a product feature
○
-
The next two steps go hand in hand and concern
how
to measure an item and
where
to find the
data for such measurements
One important consideration involves whether the measurement should be quantitative or
qualitative in nature
Quantitative measurement implies the use of data expressed using numerical
quantities, such as a count of the number of new model jet skis sold or a ratio of its
full cost to sales
○
-
Week 1 Page 10
full cost to sales
Also, data used in quantitative measurement usually are structured in nature
and arise from formal sources, such as information systems
□
Qualitative measurement implies the use of data expressed in categories, such as
customer reviews of new model jet skis
Data used in qualitative measurement usually are unstructured in nature and
arise from less formal sources, including various internal business documents,
texts, customer loyalty programs, or focus group transcripts
The challenge of how to measure is particularly strong when the item has
never before been measured
For example, mystery or secret shopper programs were first created
to help accountants assess difficult-to-measure business
environments, such as customer experiences at newly
redesigned Mobil gas station pumps or different Victoria’s
Secret store layouts
◊
□
The how and where steps often present accountants with the greatest challenge across the entire
data analytic framework
For example, appropriate data must be identified (e.g., knowing which data are necessary to
the measurement of interest), obtained (e.g., either internally from existing legacy and new
information systems or externally through licensed access to an industry database), and
transformed into a usable format (e.g., combining data from multiple sources, converting
data into a single usable format, and cleansing data to improve its accuracy)
These efforts—sometimes referred to as “extract, transform, and load”—are
important as some experts estimate the cost of using bad data (i.e., incomplete,
poorly defined, or inaccurate) to be as high as 15 to 25 percent of a company’s
revenue
While these steps can be outsourced to third parties, accountants must be sure
to understand them sufficiently so that the resulting data are used appropriately
throughout the data analytic framework
Interestingly, creativity becomes particularly valuable in these steps
because accountants often do not have access to the data they most
prefer and, instead, must find a way to utilize the data to which they do
have access in a manner that ultimately provides the needed decision
insights
□
○
-
Deciding
which
analytical method to employ in the analysis represents the next step. An analytical
method (e.g., a quantitative or qualitative model) includes any method that converts raw data into
useful information with decision insights
Examples of analytical methods in cost management include models for costing, linear
programming, net present value, activity-based costing, and cost-volume-profit scenarios
The choice of analytical method should depend on other aspects of the framework,
such as the strategic or operational importance of the decision it will inform, as well as
the complexity of the particular business scenario being assessed
For example, a single food truck likely would require only a simple method (e.g.,
high-low method) for understanding its cost drivers and constructing the
associated cost functions, whereas a large restaurant chain likely would benefit
from a more complex method (e.g., multiple regression) given its greater
product- and service-line diversity with respect to resource consumption
Additionally, sentiment analysis might use qualitative data from social
media sites to interpret and classify customer reactions to the company’s
product or service performance or employee perception of the company’s
work culture
□
○
-
Another challenging aspect within data analytics involves deciding
when
the analysis is complete
For example, few cost management analyses contain a set of clearly enumerated steps for
their performance, obvious starting and ending points, or check figures for confirming the
○
-
Week 1 Page 11
their performance, obvious starting and ending points, or check figures for confirming the
final result
In other words, many cost management tasks involve data analyses where it is
not clear “what to do first,” “when it is finished,” or “whether the answer is correct"
Instead, many cost management analyses that involve data analytic measures
require the use of considerable judgment to determine when the analysis has
reached the point at which its results will sufficiently improve the decision for
which it was conducted
□
The final step in the framework focuses on
who
within the business will be using the results of cost
management analysis
As such, this step revolves around the need for clear and concise communication to the
eventual decision maker
Oftentimes this step involves data visualization tools, such as Tableau or Microsoft
Power BI
Depending on the cost management task for which data analytics was
employed, the end user could vary widely from a fellow accountant to an
executive with no accounting experience and very little familiarity with the
steps by which the results were created
Therefore, the perspective of the end user should be considered, and care
should be taken to use communication tools (e.g., visual charts versus
numeric tables versus qualitative descriptions) and approaches (e.g., face-
to-face versus email versus virtual conference) that most effectively and
efficiently lead to user understanding
Decision makers who do not understand analyses frequently
disregard them as ineffective or incorrect
Therefore, accountants must be sure that the results of their
analyses are clearly understood so that they inform decision
making as intended
◊
□
○
-
2-2b Data Analytic Types and Cost Management Analyses
As discussed in the previous section, accountants increasingly are expected to be familiar with
each step within the framework of Exhibit 2.5, that is, “The Role of Data Analytics in Management
Accounting”
However, many accountants are unlikely to be experts within each step
For instance, Step 5 (Which Analytical Method Should Be Employed in My Analysis?)
represents one example where accountants are likely to seek assistance and expertise
from subject matter experts, including statisticians, business analysts, and computer
scientists, inside and outside of their organization to help run and interpret analytical
methods
Therefore, Exhibit 2.6 presents a deeper dive into Steps 1, 2, and 3 and Step
5 of Exhibit 2.5
Specifically, Exhibit 2.6 illustrates that the business question to be
answered should drive the specific data analytic tool type to employ in
conducting the relevant cost management analysis
□
○
-
Exhibit 2.6 Matching Data Analytic Types to Cost Management Analyses
Data
Analytic
Type
Question
Answered
Cost Management Analysis Example
Descriptive
What is
happening?
A profit and loss analysis assesses historic trends in the
company’s profitability.
Diagnostic
Why is it
happening?
What-if (i.e., sensitivity), root cause, and activity driver
analyses decipher the significant drivers that cause changes in
key revenues and costs.
Predictive
What is likely
Forecasting and budgeting analyses predict customer demand
-
Week 1 Page 12
Your preview ends here
Eager to read complete document? Join bartleby learn and gain access to the full version
- Access to all documents
- Unlimited textbook solutions
- 24/7 expert homework help
Predictive
What is likely
to happen?
Forecasting and budgeting analyses predict customer demand
patterns to help the company more effectively synchronize its
service provision and product manufacturing capabilities.
Prescriptiv
e
What do I
need to do?
Strategic cost management analysis identifies specific process
reengineering actions to reduce the cost of service provision
and product manufacturing activities.
2-3 Cost Assignment: Direct Tracing, Driver Tracing, and Allocation
To study cost accounting and operational control systems, we need to understand the meaning of
cost and to become familiar with the cost terminology associated with the two systems
We must also understand the process used to assign costs
Cost assignment is one of the key processes of the cost accounting system
Improving the cost assignment process has been one of the major
developments in the cost management field in the past 30 or so years
First, let’s define cost
□
○
-
Cost is the cash or cash equivalent value sacrificed for goods and services that are expected to
bring a current or future benefit to the organization
We say
cash equivalent
because noncash assets can be exchanged for the desired goods or
services
For example, it may be possible to trade equipment for materials used in production
○
-
Costs are incurred to produce future benefits
In a profit-making firm, future benefits usually mean revenues
As costs are used up in the production of revenues, they are said to expire
Expired costs are called expenses
In each period, expenses are deducted from revenues on the income
statement to determine the period’s profit
A loss is a cost that expires without producing any revenue benefit
For example, the cost of uninsured inventory destroyed by a
flood would be classified as a loss on the income statement
◊
□
○
-
Many costs do not expire in a given period
These unexpired costs are classified as assets and appear on the balance sheet
Computers and factory buildings are examples of assets lasting more than one period
Note that the main difference between a cost being classified as an expense or
as an asset is timing
This distinction is important and will be referred to in the development of
other cost concepts later in the text
□
○
-
2-3a Cost Objects
Cost accounting information systems are structured to measure and assign costs to cost objects.
Cost objects can be anything for which costs are measured and assigned; they may
include products, customers, departments, projects, activities, and so on
For example, if we want to determine what it costs to produce a bicycle, then the cost
object is the bicycle
If we want to determine the cost of operating a maintenance department within a
factory, then the cost object is the maintenance department
If we want to determine the cost of developing a new toy, then the cost object is the
new toy development project
Activities are a special kind of cost object
An activity is a basic unit of work performed within an organization
An activity can also be defined as an aggregation of actions within an
organization useful to managers for purposes of planning, controlling, and
decision making
In recent years, activities have emerged as important cost objects
◊
□
Activities play a prominent role in assigning costs to other cost objects and are
essential elements of an activity-based cost accounting system
□
○
-
Week 1 Page 13
essential elements of an activity-based cost accounting system
Examples of activities include setting up equipment for production, moving
materials and goods, purchasing parts, billing customers, paying bills,
maintaining equipment, expediting orders, designing products, and inspecting
products
□
Notice that an activity is described by an action verb (e.g., paying or designing)
and an object that receives the action (e.g., bills or products)
□
2-3b Accuracy of Cost Assignments
Assigning costs
accurately
to cost objects is crucial
Accuracy is not evaluated based on knowledge of some underlying “true” cost
Rather, it is a relative concept and has to do with the reasonableness and logic of the
cost assignment methods that are being used
The objective is to measure and assign as accurately as possible the cost of the
resources used by a cost object
Some cost assignment methods are clearly more accurate than others
For example, suppose you want to determine the cost of lunch for
Elaine Day, a student who frequents Hideaway, an off-campus pizza
parlor
One cost assignment approach is to count the number of
customers at the Hideaway between 12:00 P.M. and 1:00
P.M. and then divide that into the total sales receipts earned
by Hideaway during this period
Suppose that this comes to $6.25 per lunchtime
customer
Based on this approach we would conclude that
Elaine spends $6.25 per day for lunch
–
Another approach is to go with Elaine and observe how much
she spends
Suppose that she has a chef’s salad and a medium drink
each day, costing $4.50
–
It is easy to see which cost assignment is more accurate
The $6.25 cost assignment is distorted by the
consumption patterns of other customers (cost objects)
As it turns out, most lunchtime clients order the
luncheon special for $5.95 (a mini-pizza, small
salad, and medium drink)
–
◊
□
○
-
Distorted cost assignments can produce poor decisions
For example, if a plant manager is trying to decide whether to continue producing power
internally or to buy it from a local utility company, then an accurate assessment of how
much it is costing to produce the power internally is fundamental to the analysis
If the cost of internal power production is overstated, the manager might decide to
shut down the internal power department in favor of buying power from an outside
company, whereas a more accurate cost assignment might suggest the opposite
It is easy to see that poor cost assignments can prove to be costly
□
○
-
Traceability
Understanding the relationship of costs to cost objects can increase the accuracy of cost
assignments
Costs are directly or indirectly associated with cost objects
Indirect costs are costs that cannot be traced easily and accurately to a cost
object
□
Direct costs are those costs that can be traced easily and accurately to a cost
object
For costs to be traced easily means that the costs can be assigned in an
economically feasible way
□
○
-
Week 1 Page 14
economically feasible way
For costs to be traced accurately means that the costs are assigned using
a
causal relationship
Thus, traceability is the ability to assign a cost directly to a cost object in an economically
feasible way by means of a causal relationship
The more costs that can be traced to the object, the greater the accuracy of the cost
assignments
○
One additional point needs to be emphasized
Cost management systems typically deal with many cost objects
Thus, it is possible for a particular cost item to be classified as both a direct cost
and an indirect cost
It all depends on
which
cost object is the point of reference
For example, if the plant is the cost object, then the cost of heating
and cooling the plant is a direct cost; however, if the cost objects
are products produced in the plant, then this utility cost is an
indirect cost
◊
□
○
Methods of Tracing
Traceability means that costs can be assigned easily and accurately, using a causal
relationship
Tracing costs to cost objects can occur in one of two ways: (1)
direct tracing
and
(2)
driver tracing
Direct tracing is the process of identifying and assigning costs to a cost object
that are specifically or physically associated with the cost object
Direct tracing is most often accomplished by
physical observation
For example, assume that the power department is the cost object
The salary of the power department’s supervisor and the fuel
used to produce power are examples of costs that can be
specifically identified (by physical observation) with the cost
object (the power department)
◊
As a second example, consider a pair of blue jeans
The materials (denim, zipper, buttons, and thread) and labor
(to cut the denim according to the pattern and sew the pieces
together) are physically observable; therefore, the costs of
materials and labor can be directly charged to a pair of jeans
◊
Ideally, all costs should be charged to cost objects using direct
tracing
◊
□
○
Unfortunately, it is often impossible to physically observe the exact amount of resources
being used by a cost object
The next best approach is to use cause-and-effect reasoning to identify factors—
called
drivers
—that can be observed and which measure a cost object’s resource
consumption
Drivers are factors that
cause
changes in resource usage, activity usage, costs,
and revenues
Driver tracing is the use of
drivers
to assign costs to cost objects
Although less precise than direct tracing, driver tracing can be
accurate if the cause-and-effect relationship is sound
Consider the cost of electricity for the jeans manufacturing
plant
The factory manager might want to know how much
electricity is used to run the sewing machines
Physically observing how much electricity is used
would require a meter to measure the power
consumption of the sewing machines, which may
not be practical
–
◊
□
○
-
Week 1 Page 15
Your preview ends here
Eager to read complete document? Join bartleby learn and gain access to the full version
- Access to all documents
- Unlimited textbook solutions
- 24/7 expert homework help
not be practical
Thus, a driver such as “machine hours”
could be used to assign the cost of
electricity
If the electrical cost per machine hour
is $0.10 and the sewing machines use
200,000 machine hours in a year,
then $20,000 of the electricity cost
($0.10 × 200,000) would be assigned
to the sewing activity
Assigning Indirect Costs
Indirect costs cannot be traced to cost objects
Either there is no causal relationship between the cost and the cost object, or tracing
is not economically feasible
○
Assignment of indirect costs to cost objects is called allocation
Since no causal relationship exists, allocating indirect costs is based on
convenience
or
some
assumed
linkage
For example, consider the cost of heating and lighting a plant that manufactures
five products
Suppose that this utility cost is to be assigned to the five products
Clearly, it is difficult to see any causal relationship
A convenient way to allocate this cost is simply to assign it in
proportion to the direct labor hours used by each product
◊
□
Arbitrarily allocating indirect costs to cost objects reduces the overall accuracy of the
cost assignments
Accordingly, the best costing policy may be that of assigning only traceable
direct costs to cost objects
However, it must be admitted that allocations of indirect costs may serve
other purposes besides accuracy
For example, allocating indirect costs to products may be required
for external reporting
Nonetheless, most managerial uses of cost assignments are
better served by accuracy
At the very least, direct and indirect cost assignments
should be reported separately
–
◊
□
○
-
Cost Assignment Summarized
There are three methods of assigning costs to cost objects: direct tracing, driver tracing, and
allocation
Of the three methods, direct tracing is the most precise since it relies on physically
observable causal relationships
Driver tracing relies on causal factors called drivers to assign costs to cost objects
The precision of driver tracing depends on the strength of the causal
relationship described by the driver
Identifying drivers and assessing the quality of the causal relationship are
more costly than either direct tracing or allocation
□
Allocation, while the simplest and least expensive method, is the least accurate cost
assignment method; its use should be avoided where possible
In many cases, the benefits of increased accuracy by driver tracing outweigh its
additional measurement cost
This cost-benefit issue is discussed more fully later in the chapter
The process really entails choosing among competing cost
management systems
◊
□
○
-
2-4 Product and Service Costs
One of the most important cost objects is the output of organizations
-
Week 1 Page 16
One of the most important cost objects is the output of organizations
The two types of output are tangible products and services
Tangible products are goods produced by converting raw materials into finished
products through the use of labor and capital inputs such as plant, land, and
machinery
Televisions, hamburgers, automobiles, computers, clothes, and furniture are
examples of tangible products
□
Services are tasks or activities performed for a customer or an activity performed by a
customer using an organization’s products or facilities
Services are also produced using materials, labor, and capital inputs
□
Insurance coverage, medical care, dental care, funeral care, and accounting are
examples of service activities performed for customers
□
Car rental, video rental, and skiing are examples of services where the customer
uses an organization’s products or facilities
□
○
-
Services differ from tangible products on three important dimensions: intangibility, perishability,
and inseparability
Intangibility means that buyers of services cannot see, feel, hear, or taste a service before it
is bought
Thus, services are
intangible products
○
Perishability means that services cannot be stored (there are a few unusual cases where
tangible goods cannot be stored)
○
Finally, inseparability means that producers of services and buyers of services must usually
be in direct contact for an exchange to take place
In effect, services are often inseparable from their producers
For example, an eye examination requires both the patient and the optometrist
to be present
□
However, producers of tangible products need not have direct contact with the
buyers of their goods
Buyers of automobiles, for instance, never need to have contact with the
engineers and assembly line workers who produce automobiles
□
○
-
Organizations that produce tangible products are called
manufacturing
organizations
Those that produce intangible products are called
service
organizations
Managers of organizations that produce goods or services need to know how much
individual products cost for a number of reasons, including profitability analysis and
strategic decisions concerning product design, pricing, and product mix
○
-
Service companies also relate cost to profit
-
Given the importance of cost to both manufacturing and service firms, when we discuss product
costs, we are referring to both intangible and tangible products
-
2-4a Different Costs for Different Purposes
A fundamental cost management principle is “different costs for different purposes"
Product cost definitions can differ according to the objective being served
Exhibit 2.7 illustrates this principle by displaying the costs that should be considered
for several important yet different decisions that involve particular managerial
objectives
Exhibit 2.7 also provides numerous examples of costs across the value chain
(The value chain was introduced in Chapter 1 and also is discussed in
detail in Chapter 11.)
For example, in making decisions regarding external financial
reporting (i.e., which must adhere to FASB rules and conventions),
such as inventory and cost of goods sold, manufacturing
organizations should consider only product costs (i.e., the
production costs as shown in green)
However, in making pricing decisions, all traceable costs
◊
□
○
-
Week 1 Page 17
However, in making pricing decisions, all traceable costs
across the entire value chain should be considered (i.e., from
research and design costs shown in purple through customer
service costs shown in orange) as companies need to generate
enough sales revenues to exceed their full costs if they are to
make a positive net income
Furthermore, in special-order tactical decisions that do
not require the company to incur any additional
research and design or development costs (shown in
yellow), only costs to manufacture, ship (e.g., marketing
and distribution costs as shown in blue), and service the
special-order product should be considered when
deciding whether to accept or reject the order
Decisions involving other managerial objectives,
some of which are displayed in Exhibit 2.7, use
other product cost definitions
For example, often costs incurred prior to
production are referred to as upstream
costs, while costs incurred after production
are referred to as downstream costs
–
Exhibit 2.7 Understanding Different Cost Definitions
Exhibit 2.7 also pertains to merchandising and service organizations
For merchandising organizations, such as American Eagle, product cost consists
solely of the cost to purchase inventory and prepare it for sale
□
For service organizations, such as Berkshire Hathaway, Inc., there is no product
cost because they do not manufacture physical products but instead provide
services
However, just as for manufacturing organizations, merchandising and
service organizations consider costs up and down the value chain, as
appropriate, to understand the particular costs associated with the
decision under consideration
□
○
-
2-4b Product Costs and External Financial Reporting
An important objective of a cost management system is the calculation of product costs for
external financial reporting
Externally imposed conventions require costs to be classified in terms of the special
purposes, or functions, they serve
○
-
Week 1 Page 18
Your preview ends here
Eager to read complete document? Join bartleby learn and gain access to the full version
- Access to all documents
- Unlimited textbook solutions
- 24/7 expert homework help
purposes, or functions, they serve
Costs are subdivided into two major functional categories: production and
nonproduction
Production (or product) costs are those costs associated with manufacturing goods or
providing services
Nonproduction costs are those costs associated with the functions of selling and
administration
For tangible goods, production and nonproduction costs are often referred to
as
manufacturing costs
and
nonmanufacturing costs,
respectively
Production costs can be further classified as
direct materials, direct
labor,
and
overhead
Only these three cost elements can be assigned to products for external
financial reporting
□
Direct Materials
Direct materials are those materials traceable to the good or service being produced
The cost of these materials can be directly charged to products because physical
observation can be used to measure the quantity used by each product
Materials that become part of a tangible product or those materials that are
used in providing a service are usually classified as direct materials
For example, steel in an automobile, wood in furniture, alcohol in cologne,
denim in jeans, braces for correcting teeth, surgical gauze and anesthesia
for an operation, ribbon in a corsage, and soft drinks on an airline are all
direct materials
□
○
-
Direct Labor
Direct labor is labor that is traceable to the goods or services being produced
As with direct materials, physical observation is used to measure the quantity of labor
used to produce a product or service
Employees who convert raw materials into a product or who provide a service
to customers are classified as direct labor
Workers on an assembly line at Dell, a chef in a restaurant, a surgical
nurse for an open-heart operation, and a pilot for Southwest Airlines are
examples of direct labor
□
○
-
Overhead
All production costs other than direct materials and direct labor are lumped into one
category called overhead
In a manufacturing firm, overhead is also known as
factory burden
or
manufacturing
overhead
The overhead cost category contains a wide variety of items
Many inputs other than direct labor and direct materials are needed to
produce products
Examples include depreciation on buildings and equipment,
maintenance, supplies, supervision, materials handling, power,
property taxes, landscaping of factory grounds, and plant security
Supplies are generally those materials necessary for
production that do not become part of the finished product or
are not used in providing a service
Dishwasher detergent in a fast-food restaurant and oil
for production equipment are examples of supplies
–
◊
□
○
Direct materials that form an insignificant part of the final product are usually lumped into
the overhead category called indirect materials
This treatment is justified on the basis of cost and convenience
The cost of the tracing is greater than the benefit of increased accuracy
The glue used in making furniture or toys is an example
□
○
-
Week 1 Page 19
The cost of overtime for direct labor is usually assigned to overhead as well
The rationale is that typically no particular production run caused the overtime
Accordingly, overtime cost is common to all production runs and is therefore an
indirect manufacturing cost
Note that
only
the overtime cost itself is treated this way
If workers are paid $16 per hour regular rate and a premium of $8
per overtime hour, then only the $8 overtime premium is assigned
to overhead
The $16 regular rate is still regarded as a direct labor cost
In certain cases, however, overtime is associated with a
particular production run, such as a special order taken
when production is at 100 percent capacity
In these special cases, it is appropriate to treat
overtime premiums as a direct labor cost
–
◊
□
○
Prime and Conversion Costs
The manufacturing and nonmanufacturing classifications give rise to some related cost
concepts
The functional distinction between manufacturing and nonmanufacturing costs is the
basis for the concepts of noninventoriable costs and inventoriable costs—at least for
purposes of external reporting
Combinations of different production costs also produce the concepts of prime
costs and conversion costs
□
○
Prime cost is the sum of direct materials cost and direct labor cost
○
Conversion cost is the sum of direct labor cost and overhead cost
For a manufacturing firm, conversion cost can be interpreted as the cost of converting
raw materials into a final product
○
-
Nonproduction Costs
Nonproduction costs are divided into two categories: marketing (selling) costs and
administrative costs
Marketing and administrative costs are not inventoried and are called
period
costs
Period costs are expensed in the period in which they are incurred
Thus, period costs are not inventoried and are not assigned to products
Period costs appear on the income statement—not the balance
sheet
In a manufacturing organization, the level of these costs can
be significant (often greater than 25 percent of sales
revenue), and controlling them may bring greater cost savings
than the same control exercised in the area of production
costs
◊
□
○
-
For service organizations, the relative importance of selling and administrative costs depends on
the nature of the service being produced
Physicians and dentists, for example, generally do very little marketing and thus have very
low selling costs
○
An airline, on the other hand, may incur substantial marketing costs
○
-
Those costs necessary to market and distribute a product or service are marketing (selling) costs
They are often referred to as
order-getting
and
order-filling
costs
Examples of marketing costs include the following: salaries and commissions of sales
personnel, advertising, warehousing, shipping, and customer service
The first two items are examples of order-getting costs; the last three are order-
filling costs
□
○
-
All costs that cannot be reasonably assigned to either marketing or production are administrative
costs
-
Week 1 Page 20
costs
Administration is responsible for ensuring that the various activities of the organization are
properly integrated in accordance with the overall mission of the firm
The president of the firm, for example, is concerned with the efficiency
of
both
marketing and production as they carry out their respective roles
Proper integration of these two functions is essential for maximizing the overall
profits of a firm
Examples of administrative costs are top-executive salaries, legal fees,
printing and distributing the annual report, and general accounting
Research and development also is part of administrative costs and is
expensed in the period incurred
Exhibit 2.7 provides numerous cost examples within each
value chain component
◊
□
○
2-5 External Financial Statements
The functional classification is the cost classification required for external reporting
In preparing an income statement, production and nonproduction costs are separated
The reason for the separation is that production costs are product costs—costs that
are inventoried until the units are sold—and the nonproduction costs of marketing
and administration are viewed as period costs
Thus, production costs attached to the units sold are recognized as an expense
(cost of goods sold) on the income statement
Production costs attached to units that are not sold are reported as
inventory on the balance sheet
Marketing and administrative expenses are viewed as costs of the
period and must be deducted each and every period as expenses on
the income statement
Nonproduction costs never appear on the balance sheet
◊
□
○
-
2-5a Income Statement: Manufacturing Firm
The income statement prepared for external parties follows the standard format taught in an
introductory financial accounting course
This income statement is frequently referred to as absorption-costing income or full-costing
income because
all
manufacturing costs (direct materials, direct labor, and overhead) are
fully assigned to the product
○
-
Under the absorption-costing approach, expenses are separated according to function and then
deducted from revenues to arrive at operating income
The two major functional categories of expense are cost of goods sold and operating
expenses
These categories correspond to a firm’s manufacturing and nonmanufacturing
(marketing and administrative) expenses
Cost of goods sold is the cost of direct materials, direct labor, and overhead attached
to the units sold
To compute the cost of goods sold, it is first necessary to determine the cost of
goods manufactured
□
○
-
Cost of Goods Manufactured
The cost of goods manufactured represents the total manufacturing cost of goods
completed during the current period
The only costs assigned to goods completed are the manufacturing costs of direct
materials, direct labor, and overhead
The details of this cost assignment are given in a supporting schedule, called
the
statement of cost of goods manufactured
□
○
Work in process consists of all partially completed units found in production at a given point
in time
○
-
Week 1 Page 21
Your preview ends here
Eager to read complete document? Join bartleby learn and gain access to the full version
- Access to all documents
- Unlimited textbook solutions
- 24/7 expert homework help
in time
Beginning work in process consists of the partially completed units on hand at the
beginning of a period
Ending work in process consists of the incomplete units on hand at the period’s end
In the statement of cost of goods manufactured, the cost of these partially completed
units is reported as the cost of beginning work in process and the cost of ending work
in process
The cost of beginning work in process represents the manufacturing costs carried over
from the prior period; the cost of ending work in process represents the
manufacturing costs that will be carried over to the next period
In both cases, additional manufacturing costs must be incurred to complete the units
in work in process
Cost of Goods Sold
Once the cost of goods manufactured statement is prepared, the cost of goods sold can be
computed
The cost of goods sold is the manufacturing cost of the units that were sold during the
period
It is important to remember that the cost of goods sold may or may not equal
the cost of goods manufactured
In addition, we must remember that the cost of goods sold is an expense,
and it belongs on the income statement
□
○
-
Often, the income statement includes a column showing each line item as a percent of sales
Clearly, sales is 100 percent of sales
Management can review these percentages and compare them with past history of
the firm and with industry averages to see whether expenses are in line with
expectations
If the industry generally spends 15 percent of sales on selling expense, then a
company that spends significantly more or less than that amount may want to
carefully consider whether its marketing strategy is appropriate
□
○
-
2-5b Income Statement: Service Organization
The income statement for a service organization looks very similar to the one shown in Example
2.4 for a manufacturing organization
The cost of goods sold does, however, differ in some key ways
For one thing, the service firm has no finished goods inventories since services cannot
be stored, although it is possible to have work in process for services
For example, an architect may have drawings in process and an orthodontist
may have numerous patients in various stages of processing for braces
□
Additionally, some service firms add order fulfillment costs to the cost of goods
sold
□
○
-
2-6 Traditional and Activity-Based Cost Management Systems
Cost management systems can be broadly classified as
traditional
or
activity-based
While both of these systems are found in practice, the traditional cost management systems
are more widely used than the activity-based systems
As the need for highly accurate cost information increases, however, savvy cost
accountants have learned to apply activity-based costing concepts to the
determination of costs for management decision making
This is particularly true in organizations faced with increased product diversity,
more product complexity, shorter product life cycles, increased quality
requirements, and intense competitive pressures
These organizations often adopt a just-in-time manufacturing approach
and implement advanced manufacturing technology (discussed in detail
in Chapter 11)
□
○
-
Week 1 Page 22
Your preview ends here
Eager to read complete document? Join bartleby learn and gain access to the full version
- Access to all documents
- Unlimited textbook solutions
- 24/7 expert homework help
in Chapter 11)
For firms operating in this advanced manufacturing environment,
the traditional cost management system may not work well
More relevant and timely cost information is needed for these
organizations to build a sustainable long-term competitive
advantage
Organizations must improve the value received by their
customers while increasing their own profits at the
same time
Better assessment of cost behavior, increased
accuracy in product costing, and an attempt to
achieve continuous cost improvement are all
critical for the advanced manufacturing
environment
–
◊
2-6a Traditional Cost Management Systems: A Brief Overview
Cost management systems are made up of two subsystems: the cost accounting system and the
operational control system
It is logical and convenient to discuss each subsystem separately
Of course, what is true for a subsystem is true for the overall cost management
system
○
-
Traditional Cost Accounting
A traditional cost accounting system assumes that all costs can be classified as fixed or
variable with respect to changes in the
units
or
volume
of product produced
Thus, units of product or other drivers highly correlated with units produced, such as
direct labor hours and machine hours, are the only drivers
assumed
to be of
importance
These unit- or volume-based drivers are used to assign production costs to
products
A cost accounting system that uses only unit-based activity drivers to
assign costs to cost objects is called a traditional cost system
Since unit-based activity drivers usually are not the only drivers that
explain causal relationships, much of the product cost assignment
activity must be classified as allocation (recall that allocation is cost
assignment based on
assumed
linkages or convenience)
Therefore, traditional cost accounting systems tend to be
allocation intensive.
◊
□
○
The product costing objective of a traditional cost accounting system is typically satisfied by
assigning production costs to inventories and cost of goods sold for purposes of financial
reporting
More comprehensive product cost definitions, such as the value-chain and operating
cost definitions illustrated in Exhibit 2.7, are not available for management use
Traditional cost accounting systems, however, often furnish useful variants of
the product cost definitions
For example, prime costs and variable manufacturing costs per unit may
be reported
□
○
-
Traditional Cost Control
A traditional operation control system assigns costs to organizational units and then holds
the organizational unit manager responsible for controlling the assigned costs
Performance is measured by comparing actual outcomes with standard or budgeted
outcomes
The emphasis is on financial measures of performance; nonfinancial measures
may be ignored
□
○
-
Week 1 Page 23
Your preview ends here
Eager to read complete document? Join bartleby learn and gain access to the full version
- Access to all documents
- Unlimited textbook solutions
- 24/7 expert homework help
may be ignored
Managers are rewarded based on their ability to control costs
This approach traces costs to individuals who are responsible for the
incurrence of costs
The reward system is used to motivate these individuals to
manage costs
The approach assumes that maximizing the
performance of the overall organization is achieved by
maximizing the performance of individual
organizational subunits (referred to as
responsibility
centers
)
–
◊
2-6b Activity-Based Cost Management Systems: A Brief Overview
Activity-based cost management systems have evolved in response to significant changes in the
competitive business environment faced by both service and manufacturing firms
The overall objective of an activity-based cost management system is to manage activities to
reduce costs and improve customer value
A well-designed activity-based cost management system helps managers achieve
operational and strategic objectives
Operational activity-based management relates to efficiency or “doing things
right”
Thus, activity-based costing information is used to improve efficiency and
lower cost while maintaining or improving customer value
Strategic activity-based management relates to effectiveness or
“doing the right things”
Thus, activity-based costing information helps managers
choose which services or products to produce and which
activities would be most appropriate to produce them
Generally, more managerial objectives can be met with
an activity-based system than with a traditional system
–
◊
□
○
-
Activity-Based Cost Accounting
An activity-based cost accounting system emphasizes tracing over allocation
The role of driver tracing is significantly expanded by identifying drivers unrelated to
the volume of product produced (called
non-unit-based activity drivers
)
The use of both unit- and non-unit-based activity drivers increases the accuracy
of cost assignments and the overall quality and relevance of cost information
A cost accounting system that uses both unit- and non-unit-based activity
drivers to assign activity costs to cost objects is called an activity-based
cost (ABC) system
For example, consider the activity called “moving materials”
(moving raw materials and partially finished goods from one point
to another within a factory)
The number of moves required for a product may be a much
better measure of the product’s demand for the materials
handling activity than the number of units produced
In fact, the number of units produced may have little to
do with measuring products’ demands for materials
handling
(A batch of 10 units of one product could require
as much materials handling activity as a batch of
100 units of another product.)
Thus, an activity-based cost accounting
system tends to be tracing intensive
–
◊
□
○
-
Week 1 Page 24
Your preview ends here
Eager to read complete document? Join bartleby learn and gain access to the full version
- Access to all documents
- Unlimited textbook solutions
- 24/7 expert homework help
system tends to be tracing intensive
Product costing in an activity-based system tends to be flexible
The activity-based cost management system is capable of producing cost information
for a variety of managerial objectives, including the financial reporting objective
More comprehensive product costing definitions are emphasized for better
planning, control, and decision making
Therefore, the maxim of “different costs for different purposes” takes on
real meaning
□
○
Activity-Based Cost Control
The activity-based operational control subsystem also differs significantly from that of a
traditional system
The emphasis of the traditional cost management accounting system is on managing
costs
However, the management of activities—not costs—is the key to successful
control in the advanced manufacturing environment, and
activity-based
management
is at the heart of a contemporary operational control system
Activity-based management (ABM) focuses on the management of
activities with the objective of improving the value received by the
customer and the profit received by the company in providing this value
It includes driver analysis, activity analysis, and performance
evaluation and draws on ABC as a major source of information
In Exhibit 2.8, the vertical dimension, or
cost view
, traces the
cost of resources to activities and then to the cost objects
The cost view serves as an important input to the
control dimension, which is called the
process view
The process view identifies factors that cause an
activity’s cost (explains why costs are incurred),
assesses what work is done (identifies activities),
and evaluates the work performed and the results
achieved (how well the activity is performed)
Thus, an activity-based control system
requires detailed information on activities
–
◊
□
○
-
Exhibit 2.8 Activity-Based Management Model
-
Week 1 Page 25
Your preview ends here
Eager to read complete document? Join bartleby learn and gain access to the full version
- Access to all documents
- Unlimited textbook solutions
- 24/7 expert homework help
○
This new approach focuses on accountability for activities rather than costs to maximize
systemwide, rather than individual, performance
Activities cut across functional and departmental lines, are systemwide in focus, and require
a global approach to control
Essentially, this form of control admits that maximizing the efficiency of individual
subunits does not necessarily lead to maximum efficiency for the system as a whole
Another significant difference exists; in the ABM operational control
information system, both financial and nonfinancial measures of performance
are important
Exhibit 2.9 compares the characteristics of the traditional and activity-
based cost management systems
□
○
-
Exhibit 2.9 Comparison of Traditional and Activity-Based Cost Management Systems
Traditional
Activity-Based
Unit-based drivers
Unit- and non-unit-based drivers
Allocation intensive
Tracing intensive
Narrow and rigid product costing
Broad, flexible product costing
Focus on managing costs
Focus on managing activities
Sparse activity information
Detailed activity information
Maximization of individual unit
performance
Systemwide performance maximization
Uses financial measures of
performance
Uses both financial and nonfinancial measures of
performance
-
2-6c Choice of a Cost Management System
An activity-based cost management system offers significant benefits, including greater product
costing accuracy, improved decision making, enhanced strategic planning, and an increased ability
to manage activities
These benefits, however, are expensive
-
Week 1 Page 26
Your preview ends here
Eager to read complete document? Join bartleby learn and gain access to the full version
- Access to all documents
- Unlimited textbook solutions
- 24/7 expert homework help
These benefits, however, are expensive
An activity-based cost management system is more complex and requires
considerably more measurement activity—and measurement can be costly
As Kaplan and Anderson point out, “ABC systems (are) expensive to build,
complex to sustain, and difficult to modify”
□
○
In deciding whether to implement an activity-based cost management system, a manager must
assess the trade-off between the cost of measurement and the cost of errors
Measurement costs are the costs associated with the measurements required by the cost
management system
○
Error costs are the costs associated with making poor decisions based on bad cost
information
○
Optimally, a cost management system would minimize the sum of measurement and error
costs
Note, however, that the two costs conflict
More complex cost management systems produce lower error costs but have
higher measurement costs
(Consider, for example, the number of activities that must be identified
and analyzed, along with the number of drivers that must be used to
assign costs to products.)
The tradeoff between error and measurement costs is illustrated
in Exhibit 2.10
The message is clear
◊
□
○
-
Exhibit 2.10 Trade-Off between Measurement and Error Costs
○
-
New approaches to activity-based costing are being developed
For example, time-driven activity-based costing streamlines the cost drivers and focuses on
the time it takes to perform an activity
Alternatively, for some organizations, the optimal cost system may not be an ABM
system
Depending on the trade-offs, the optimal cost management system may very
□
○
-
Week 1 Page 27
Your preview ends here
Eager to read complete document? Join bartleby learn and gain access to the full version
- Access to all documents
- Unlimited textbook solutions
- 24/7 expert homework help
Depending on the trade-offs, the optimal cost management system may very
well be a simpler, traditional system
This could explain, in part, why most firms still maintain this type of
system
□
Recent changes in the manufacturing environment may increase the attractiveness of more
accurate, yet complex, cost management systems
New information technology decreases measurement costs; computerized production
planning systems and more powerful, less expensive computers make it easier to collect
data and perform calculations
As measurement costs decrease, the measurement cost curve shown in Exhibit
2.10 shifts downward and to the right, causing the total cost curve to shift to the right
The optimal cost management system is now one that allows more accuracy
□
○
-
As the cost of measurement has decreased, the cost of errors has increased
Basically, errors consist of over- or under-costing products
If competition heats up for an overcosted product, the firm may drop what
appears
to
be an unprofitable product under a traditional system
If the nature of the competition changes, error costs can increase as well
□
○
-
For example, if single-product-focused competitors emerge, then their pricing and marketing
strategies will be based on more accurate cost information (since all costs are known to belong to
the single product)
Because of better cost information, the more focused firms may gain market share at the
expense of multiple-product producers (whose cost systems may be allocating rather than
tracing costs to individual products)
Other factors such as deregulation and just-in-time manufacturing (which leads to a
more focused production environment) can also increase the cost of errors
As the cost of errors increases, the error cost curve in Exhibit 2.10 shifts upward
and to the right, causing the total cost curve to shift to the right, making a more
accurate cost system the better choice
□
○
-
Another cost, which is increasing for some firms, is the cost of unethical conduct
-
Exhibit 2.11 Shifting Measurement and Error Costs
-
Week 1 Page 28
Your preview ends here
Eager to read complete document? Join bartleby learn and gain access to the full version
- Access to all documents
- Unlimited textbook solutions
- 24/7 expert homework help
○
2-7a Summary of Learning Objectives
LO1
Describe a cost management information system, its objectives, and its major subsystems,
and indicate how it relates to other operating and information systems
Cost management system, a subsystem of the accounting information system, designed to
satisfy costing, controlling, and decision-making objectives
○
Two major subsystems: cost accounting system and the operational control system
○
-
LO2
Define data analytics, and describe its role in cost management
Data analytics represents the process through which an organization utilizes various
amounts and types of data to help connect strategy and other key goals to improved
decision making
○
Effectively utilizing data analytics requires accountants to answer seven important
questions—What, Why, How, Where, Which, When, and Who—in order to improve cost
management decisions
○
-
LO3
Explain the cost assignment process
Objective of the cost accounting system is assigning costs to cost objects
○
Three methods of cost assignment:
Direct tracing—physical observation, most accurate
Driver tracing—more expensive, more accurate than allocation
Allocation—least accurate, easiest to apply
○
-
LO4
Define tangible and intangible products, and explain why there are different product cost
definitions
Products are tangible
○
Services are:
Intangible
Perishable (cannot be inventoried)
Inseparable (buyer and provider interact)
○
Product cost definitions:
-
Week 1 Page 29
Your preview ends here
Eager to read complete document? Join bartleby learn and gain access to the full version
- Access to all documents
- Unlimited textbook solutions
- 24/7 expert homework help
Product cost definitions:
Value chain includes research and development, production, marketing, and customer
service
Used for pricing decisions, product mix decisions, strategic profitability analysis
□
Operating product costs include production, marketing, and customer service
Used for strategic design decisions, tactical profitability analysis
□
Traditional product costs include only production (direct materials, direct labor,
overhead) and are used for external financial reporting
○
LO5
Prepare income statements for manufacturing and service organizations
Income statements rely on:
Cost of goods manufactured or services provided
Cost of goods sold or services sold (typically the same as services provided)
○
Gross margin is the difference between sales revenue and the cost of goods (or services)
sold
○
Operating income is the difference between gross margin and selling (or marketing) and
administrative expense
○
-
LO6
Explain the differences between traditional and contemporary cost management systems
Traditional systems characterized by:
Use of unit-based drivers
Allocation
Narrow and rigid product costing
Focus on managing costs
Maximization of individual unit performance
Use of financial measures of performance
○
Activity-based systems characterized by:
Use of unit- and non-unit-based drivers
Tracing
Broad, flexible product costing
Focus on managing activities
Systemwide performance maximization
Use of both financial and nonfinancial measures of performance
○
-
Week 1 Page 30
Your preview ends here
Eager to read complete document? Join bartleby learn and gain access to the full version
- Access to all documents
- Unlimited textbook solutions
- 24/7 expert homework help
Related Documents
Related Questions
Define and explain cost accounting system
arrow_forward
Why does a cost accountant need to be familiar with new developments in information technology?
arrow_forward
Discuss the characteristics and costs of useful information. What makes information useful and what types of costs are associated?
arrow_forward
Explain the Problems in Cost Accounting Measurements?
arrow_forward
Under operations analysis, how do you describe cost analysis?
arrow_forward
Systems Concepts, Traditional versus Activity-Based Cost Accounting Systems
The following items are associated with a traditional cost accounting information system, an activity-based cost accounting information system, or both (that is, some elements are common to the two systems):
Required:
1. Select the appropriate categories for each of the following items:
a.
Usage of direct materials
b.
Direct materials cost assigned to products using direct tracing
c.
Direct labor cost incurrence
d.
Direct labor cost assigned to products using direct tracing
e.
Setup cost incurrence
f.
Setup cost assigned using number of setups as the activity driver
g.
Setup cost assigned using direct labor hours as the activity driver
h.
Cost accounting personnel
i.
Submission of a bid, using product cost plus 25 percent
j.
Purchasing cost incurrence
k.
Purchasing cost assigned to products using direct labor hours as the activity driver
l.
Purchasing cost assigned…
arrow_forward
SEE MORE QUESTIONS
Recommended textbooks for you
Principles of Accounting Volume 2
Accounting
ISBN:9781947172609
Author:OpenStax
Publisher:OpenStax College
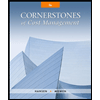
Cornerstones of Cost Management (Cornerstones Ser...
Accounting
ISBN:9781305970663
Author:Don R. Hansen, Maryanne M. Mowen
Publisher:Cengage Learning
Related Questions
- Define and explain cost accounting systemarrow_forwardWhy does a cost accountant need to be familiar with new developments in information technology?arrow_forwardDiscuss the characteristics and costs of useful information. What makes information useful and what types of costs are associated?arrow_forward
- Explain the Problems in Cost Accounting Measurements?arrow_forwardUnder operations analysis, how do you describe cost analysis?arrow_forwardSystems Concepts, Traditional versus Activity-Based Cost Accounting Systems The following items are associated with a traditional cost accounting information system, an activity-based cost accounting information system, or both (that is, some elements are common to the two systems): Required: 1. Select the appropriate categories for each of the following items: a. Usage of direct materials b. Direct materials cost assigned to products using direct tracing c. Direct labor cost incurrence d. Direct labor cost assigned to products using direct tracing e. Setup cost incurrence f. Setup cost assigned using number of setups as the activity driver g. Setup cost assigned using direct labor hours as the activity driver h. Cost accounting personnel i. Submission of a bid, using product cost plus 25 percent j. Purchasing cost incurrence k. Purchasing cost assigned to products using direct labor hours as the activity driver l. Purchasing cost assigned…arrow_forward
arrow_back_ios
arrow_forward_ios
Recommended textbooks for you
- Principles of Accounting Volume 2AccountingISBN:9781947172609Author:OpenStaxPublisher:OpenStax CollegeCornerstones of Cost Management (Cornerstones Ser...AccountingISBN:9781305970663Author:Don R. Hansen, Maryanne M. MowenPublisher:Cengage Learning
Principles of Accounting Volume 2
Accounting
ISBN:9781947172609
Author:OpenStax
Publisher:OpenStax College
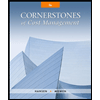
Cornerstones of Cost Management (Cornerstones Ser...
Accounting
ISBN:9781305970663
Author:Don R. Hansen, Maryanne M. Mowen
Publisher:Cengage Learning