ACT 5140 chpt 21 hw
docx
keyboard_arrow_up
School
Nova Southeastern University *
*We aren’t endorsed by this school
Course
5140
Subject
Accounting
Date
Jun 14, 2024
Type
docx
Pages
15
Uploaded by CaptainRaz3331
ACT 5140 chpt 21 hw
Brief Exercise 21.4 (Static) Outsourcing a Product (LO21-2, LO21-4, LO21-5)
~ outsourcing cost =$40 per; current cost = $32 per; potential additional income = $9600/year
~@64 installations, outsourcing cost-> (40-32)*64 = $512/month or $6144 a year
I think
Correct answer
Exercise 21.1 (Static) Accounting Terminology (LO21-1, LO21-2, LO21-3, LO21-4, LO21-
5)
Exercise 21.4 (Static) Scarce Resources (LO21-1, LO21-2, LO21-3, LO21-4)
Combination of products shall be:
Denim = 6,000 bolts
Chenille = 240 bolts
Gauze = 1,200 bolts
Explanation:
As provided the machine hours are limited thus, the constraint is machine hours.
Accordingly contribution per machine hour shall be computed.
Denim has contribution of $14 for each 0.5 machine hour, thus, contribution per hour =
Chenille has contribution of $22 per machine hour
Gauze has contribution of $9 per 0.3 hours, thus contribution per machine hour =
= $30
According to contribution per hour, ranking of products shall be
Gauze I
Denim II
Chenille III
Therefore, bolts of gauze to be produced = 1,200 that is maximum
Hours required = 1,200
0.3 = 360
Hours remaining = 3,600 - 360 = 3,240
Bolts of Denim to be produced = 6,000 that is maximum
Hours required = 6,000
0.5 = 3,000
Hours remaining = 3,240 - 3,000 = 240
Your preview ends here
Eager to read complete document? Join bartleby learn and gain access to the full version
- Access to all documents
- Unlimited textbook solutions
- 24/7 expert homework help
Bolts of Chenille that can be produced =
= 240 bolts
Total contribution in this case
= (1,200
$9) + (6,000
$14) + (240
$22)
= ($10,800 + $84,000 + $5,280)
= $100,080
Exercise 21.6 (Static) Incremental Analysis: Make or Buy Decision (LO21-1, LO21-2, LO21-3, LO21-4)
a) The
incremental analysis
for variable overhead is nil, for fixed overhead is 0, purchase
price is $90,000 and for total cost $15000. b) No, the company should continue manufacturing not buying.
a) To determine whether Swank Company should buy the part or continue to manufacture it, we need to compare the total cost of manufacturing with the total cost of buying the part from an outside
supplier
.
Let's complete the comparative schedule using the information:
Make the Part Buy the Part Incremental Analysis
Variable Overhead
$75,000 - -
Fixed
Overhead $60,000 $60,000 0
Purchase Price of part $6 per unit $90,000 ($90,000)
Total cost to acquire part $135,000 $150,000 ($15,000)
In the comparative schedule, we have filled in the costs for the manufacturing option (Make the Part) and the buying option (Buy the Part). Now, we can calculate the incremental analysis by subtracting the costs of the buying option from the costs of the manufacturing option.
Incremental Analysis = Total cost to acquire part (Make the Part) - Total cost to acquire part (Buy the Part)
Incremental Analysis = $135,000 - $150,000
Incremental Analysis = -$15,000
The incremental analysis represents the difference in costs between the two options. In this case, the negative value indicates that it would be $15,000 cheaper to continue manufacturing the part rather than buying it from the outside supplier.
b) Therefore, based on the incremental analysis, Swank Company should continue to manufacture the part rather than buying it.
Learn more about
fixed cost
here:
brainly.com/question/30764172
#SPJ11
Complete question is:
"The cost to Swank Company of manufacturing 15,000 units of a particular part is $135,000, of which $60,000 is fixed and $75,000 is variable. The company can buy the part from an outside supplier for $6 per unit. Fixed costs will remain the same regardless of Swank’s
Your preview ends here
Eager to read complete document? Join bartleby learn and gain access to the full version
- Access to all documents
- Unlimited textbook solutions
- 24/7 expert homework help
decision. Should the company buy the part or continue to manufacture it? Prepare a comparative schedule in the format illustrated in Exhibit 21–6 .
Exhibit 21-6
Make the Part Buy the Part Incremental Analysis
Direct materials . . . . . . . . . . . . . . . . . . . . . . . . . . . . . $ 8,000 $ 8,000
Direct labor . . . . . . . . . . . . . . . . . . . . . . . . . . . . . . . . . 12,500 12,500
Variable overhead . . . . . . . . . . . . . . . . . . . . . . . . . . . 10,000 $ 1,000 9,000
Fixed overhead . . . . . . . . . . . . . . . . . . . . . .. . . . . . . . 29,500 27,000 2,500
Purchase price of part, $5 per unit . . . .. . . . . . . . . . ______ 50,000 (50,000 )
Total cost to acquire part . . . . . . . . . . . . . . . . . . . . . $60,000 $78,000 $ (18,000)
Here is a start to the answer, but I am unsure because there is no reference to a decrease in variable costs.
beginning to answer:
Make the Buy the Incremental
part part Analysis
Variable Overhead $75,000
Fixed Overhead 60,000 60,000
Purchase Price of part, $6 per unit 9,000 (9,000)
Total cost to acquire part $135,000"
(from https://brainly.com/question/33043922
) gives an ok explanation Exercise 21.7 (Static) Make or Buy Decision (LO21-1, LO21-2, LO21-3, LO21-4)
To determine whether Bacrometer should continue producing the fans or accept the bid from the other manufacturer, we need to analyze the costs associated with each option.
1.
Cost of Producing Fans In-House:
o
Variable cost per unit = $9
o
Monthly production = 5,000 units
o
Total variable cost per month = 5,000 units x $9/unit = $45,000
2.
Cost of Purchasing Fans from Another Manufacturer:
o
Cost per unit = $10
o
Monthly requirement = 5,000 units
o
Total cost per month = 5,000 units x $10/unit = $50,000
3.
Opportunity Cost of Renting Out Production Line:
o
Rental income = $7,500 per month
Analysis:
If Bacrometer continues to produce the fans in-house, the total monthly cost is $45,000.
If Bacrometer accepts the bid and rents out the production line, the total monthly cost would be $50,000 for buying the fans, but they would gain $7,500 from renting out the production line. Thus, the net cost would be $50,000 - $7,500 = $42,500.
Conclusion:
Bacrometer would save money by accepting the bid to buy the fans for $10 each and renting out their production line. The savings would be $45,000 (cost of producing in-
house) - $42,500 (net cost after renting out the line) = $2,500 per month. Therefore, it would be financially beneficial for Bacrometer to accept the bid and rent out the production line.
Incremental cost to make = 45000
Incremental cost to make = 42500 (explanation in analysis)
Exercise 21.8 (Static) Sunk Costs: Scrap or Rework Decision (LO21-1, LO21-2, LO21-3, LO21-4)
Your preview ends here
Eager to read complete document? Join bartleby learn and gain access to the full version
- Access to all documents
- Unlimited textbook solutions
- 24/7 expert homework help
The
net proceeds from selling
the reworked units is $66,000 and the scrap value of the units is $60,000.
Explanation:
To prepare a
schedule
showing the
effect
of selling the defective units as scrap or
rework
, we need to compare the
net proceeds
from selling the reworked units and the
scrap value
of the units.
Scrap Value:
The scrap value of the units can be calculated by multiplying the number of defective units (12,000) by the scrap price per unit ($5). This gives us a total scrap value of $60,000.
Net Proceeds from Reworked Units:
To calculate the net proceeds from selling the reworked units, we need to subtract the cost of reworking the units ($30,000) from the total revenue generated by selling the reworked units. The revenue can be calculated by multiplying the number of reworked units (12,000) by the selling price per unit ($8). This gives us a total revenue of $96,000. Subtracting the reworking cost, we get a net proceeds of $66,000.
Therefore, the net proceeds from selling the reworked units is $66,000 and the scrap value of the units is $60,000.
Exercise 21.9 (Static) Scarce Resources (LO21-1, LO21-2, LO21-3, LO21-4)
Solving for my problem
Exercise 21.10 (Static) Joint Products (LO21-1, LO21-2, LO21-3, LO21-4)
This is the answer since we’re comparing the price each can be sold for vs the profit if you split off. Both split off profits are lower than what you could sell. a) Profit beyond split off:
Amoxiphore = 4,200 - 1,600 = 2,600
Benidrate = 6,000 - 3,700 = 2,300
[Take note that 4,000 is not considered since it is sunk costs, which is irrelevant to the decision
making. It is incurred whether the company process further or not.]
**Amoxiphore is more profitable because it has a higher incremental profit than Benidrate.
b) Some nonfinancial issues to consider are the quality of the medicines and production capacity of the company.
Exercise 21.13 (Static) Evaluating a Special Order (LO21-1, LO21-2, LO21-3)
~ professor’s spreadsheet
Your preview ends here
Eager to read complete document? Join bartleby learn and gain access to the full version
- Access to all documents
- Unlimited textbook solutions
- 24/7 expert homework help
Problem 21.3A (Static) Make or Buy Decision (LO21-1, LO21-2, LO21-3, LO21-4)
~ professor’s spreadsheet has detailed explanation
Problem 21.6A (Static) Sell or Rebuild Decision (LO21-1, LO21-2, LO21-3, LO21-4, LO21-
5)
~ professor’s spreadsheet has detailed explanation
Your preview ends here
Eager to read complete document? Join bartleby learn and gain access to the full version
- Access to all documents
- Unlimited textbook solutions
- 24/7 expert homework help
Related Documents
Related Questions
sions
Question 1
rences
View Policies
porations
Current Attempt in Progress
PLUS Support
Bonita's Manufacturing Company can make 100 units of a
Central
necessary component part with the following costs:
e 365
$119000
Direct Materials
24000
Direct Labor
ges
53000
Variable Overhead
za
30000
Fixed Overhead
If Bonita's Manufacturing Company can purchase the component
externally for $195000 and only $6000 of the fixed costs can be
avoided, what is the correct make-or-buy decision?
O Make and save $7000
O Make and save $22000
Buy and save $7000
OBuy and save $22000
ip
arrow_forward
Chapter 6 Uniform Señes Analysisy Acertain 'ndustrial firm desires an economic
analysis to detemine which of twodifferent machine should be purechased.
Each machine s capable of performing the same task given amount of Hime . Assume
the minimum attactiverate od returnMARR) is 8%. The following data are to beüsedin
your anaylsis
Machine X
Machine Y
First cost
$ 5000.00
$8000,00
$150.00
$2000.00
Annual Manitenance Cost
$00.00
Salvage value
Es timated life inyear
which machine would youchoo se? Base your answer on annual.cost Pravide cash flow
diagrams and Showyour work?
$00.00
12
i50 150 ISo 15. 150
IS. 15a 15. İso 1 2000.
150
ISo
A A
5
6 7
la
12
arrow_forward
Only Q3
arrow_forward
Business
arrow_forward
Multiple Choice Question 74
In applying the high-low method, what is the fixed cost?
Month
Miles
Total Cost
January
70000
$92000
February
42000
70000
March
60000
88000
April
82000
120000
O $50000
O $17500
O $32000
$18000
Click if you would like to Show Work for this question: Qpen Sho
arrow_forward
21.1A
arrow_forward
Multiple Choice Question 73
In applying the high-low method, what is the unit variable cost?
Month
Miles
Total Cost
January
70000
$92000
February
42000
70000
March
60000
88000
April
82000
120000
O $1.46.
O $1.25.
O $1.67.
Cannot be determined from the information given.
Click if you would like to Show Work for this question: Open Show V
arrow_forward
Question #1
arrow_forward
ions
--/1
Question 12
ences
View Policies
orations
Current Attempt in Progress
PLUS Support
Morales Corporation produces microwave ovens. The following per
unit cost information is available: direct materials $39, direct labor
$28, variable manufacturing overhead $12, fixed manufacturing
overhead $40, variable selling and administrative expenses $13,
and fixed selling and administrative expenses $28. Its desired ROI
per unit is $28.80. Compute its markup percentage using a total-
cost approach. (Round answer to 2 decimal places, e-g. 10.50 %.)
Central
ce 365
ges
Zza
Markup percentage
8:46 PM
शी
11/18/2019
hp
ins
prt sc
ho ll
12
home
end
m
to
44
delete
backspace
lock
7
home
arrow_forward
pre.9
arrow_forward
Ch. 7 Incremental Analysis pg 467 Segment Income Statement
Please provide the answer and explain the answer to the following question with the information given below.
"Big Tent Company is trying to decide whether to keep or drop one of its outdoor wedding tents. The company's segmented income statement shows that this product is generating a net loss as follows:"
Sales Revenue: $100,000
Less: Variable Costs $70,000
Contribution Margin $30,000
Less: Direct Fixed Costs $10,000
Segment Margin $20,000
Less: Allocated common fixed costs $30,000
Net Operating Income $(10,000)
The company estimates that eliminating this product line will increase the contribution margin on a related product line by $25,000. Based on this information, what impact would dropping the line have on the company's overall profitability?
arrow_forward
Check m
A division can sell externally for $73 per unit. Its variable manufacturing costs are $42 per unit, and its variable marketing costs are $20 per unit. What is the optimal
transfer price for transferring internally, assuming the division is operating at capacity?
to search
Multiple Choice
O
$20
$42
$62
$73
I
Hi
37°F Cloudy
^4
arrow_forward
31
arrow_forward
hi tutor pls given correct answer general accounting
arrow_forward
Please do not give solution in image format thanku
arrow_forward
-/1
Question 1
rences
View Policies
borations
Current Attempt in Progress
PLUS Support
Jackson Manufacturing is introducing a new product with a unit
selling price of $12.50. The product required an investment of
$500,000, and the company requires a 20 % ROI. Projected sales
100,000 units. Compute the target cost per unit.
Central
e 365
es
O $14.50
a
O $15.50
O $11.50
O $10
hp
noll
ins
prt sc
home
delete
4
num
backspace
arrow_forward
Ch. 7 Incremental Analysis Pg 461 Self Practice
Please solve the following questions and provide and explanation. Thank you
"Big Tent Company has received a special order for 10,000 units at a discount price of $100 each. The product sells for $150, has the following manufacturing costs: "
Cost Per Unit
Direct Materials $40
Direct Labor $ 20
Variable Manufacturing Overhead $ 20
Fixed Manufacturing Overhead $30
Totaul Unit Cost $110
1) Assume Big Top has enough extra capacity to fill the order without affecting the production or sale of it's product to regular customers. If Big Top accepts offer, what effect will the roder have on the company's short-term profit?
2) If Big Top is at full capacity, what price would be needed to cover all incremental costs, including opportunity costs?
arrow_forward
How to solve this?
arrow_forward
10:13W WSP
□
s25-7
Annual leasing fee for software
Annual maintenance of trucks
Priscilla Smiley manages a fleet of 250 delivery trucks for Daniels Corporation.
Smiley must decide whether the company should outsource the fleet
management function. If she outsources to Fleet Management Services (FMS),
FMS will be responsible for maintenance and scheduling activities. This
alternative would require Smiley to lay off her five employees. However, her own
job would be secure; she would be Daniels's liaison with FMS. If she continues
to manage the fleet, she will need fleet-management software that costs $9,500
per year to lease. FMS offers to manage this fleet for an annual fee of $300,000.
Smiley performed the following analysis:
Total annual salaries of five laid-
off employees
Fleet Management Service's
annual fee
Total differential cost of
⠀⠀⠀
со
Retain In-
House
$ 9,500
147,000
185,000
$ 341,500
1409/ 1480
C
QAA
Outsource to
FMS
Word
>> Bit
Q5G 71%
Ę
$ 300,000
Difference
$9,500…
arrow_forward
00
Company A is currently manufacturing a component but is considering buying the component from a
reliable supplier. Which of the costs are relevant to this decision?
Select one:
O a. direct material costs
O b. fixed costs
avoidable fixed costs
C.
O d. purchase price from supplier
O e. all of these
f.
a,c and d
Clear my choice
Next page
s page
0 抄 胆 メ 直 0
回 # E
ype here to search
f5
24
4.
#
9.
2
V4
3.
5.
3.
arrow_forward
155
arrow_forward
Typed plz and Asap thanks
arrow_forward
Please do not give solution in image format thanku
arrow_forward
Which of the following is the EVC of new product X?
Product
Product price
Startup cost
Maintenance and
operations cost
Productivity
600
650
750
850
900
Reference
Product Y
$400
$200
$500
New Product X
EVC:
$100
$400
$150
arrow_forward
11q12
arrow_forward
SEE MORE QUESTIONS
Recommended textbooks for you
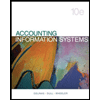
Pkg Acc Infor Systems MS VISIO CD
Finance
ISBN:9781133935940
Author:Ulric J. Gelinas
Publisher:CENGAGE L
Related Questions
- sions Question 1 rences View Policies porations Current Attempt in Progress PLUS Support Bonita's Manufacturing Company can make 100 units of a Central necessary component part with the following costs: e 365 $119000 Direct Materials 24000 Direct Labor ges 53000 Variable Overhead za 30000 Fixed Overhead If Bonita's Manufacturing Company can purchase the component externally for $195000 and only $6000 of the fixed costs can be avoided, what is the correct make-or-buy decision? O Make and save $7000 O Make and save $22000 Buy and save $7000 OBuy and save $22000 iparrow_forwardChapter 6 Uniform Señes Analysisy Acertain 'ndustrial firm desires an economic analysis to detemine which of twodifferent machine should be purechased. Each machine s capable of performing the same task given amount of Hime . Assume the minimum attactiverate od returnMARR) is 8%. The following data are to beüsedin your anaylsis Machine X Machine Y First cost $ 5000.00 $8000,00 $150.00 $2000.00 Annual Manitenance Cost $00.00 Salvage value Es timated life inyear which machine would youchoo se? Base your answer on annual.cost Pravide cash flow diagrams and Showyour work? $00.00 12 i50 150 ISo 15. 150 IS. 15a 15. İso 1 2000. 150 ISo A A 5 6 7 la 12arrow_forwardOnly Q3arrow_forward
- Businessarrow_forwardMultiple Choice Question 74 In applying the high-low method, what is the fixed cost? Month Miles Total Cost January 70000 $92000 February 42000 70000 March 60000 88000 April 82000 120000 O $50000 O $17500 O $32000 $18000 Click if you would like to Show Work for this question: Qpen Shoarrow_forward21.1Aarrow_forward
- Multiple Choice Question 73 In applying the high-low method, what is the unit variable cost? Month Miles Total Cost January 70000 $92000 February 42000 70000 March 60000 88000 April 82000 120000 O $1.46. O $1.25. O $1.67. Cannot be determined from the information given. Click if you would like to Show Work for this question: Open Show Varrow_forwardQuestion #1arrow_forwardions --/1 Question 12 ences View Policies orations Current Attempt in Progress PLUS Support Morales Corporation produces microwave ovens. The following per unit cost information is available: direct materials $39, direct labor $28, variable manufacturing overhead $12, fixed manufacturing overhead $40, variable selling and administrative expenses $13, and fixed selling and administrative expenses $28. Its desired ROI per unit is $28.80. Compute its markup percentage using a total- cost approach. (Round answer to 2 decimal places, e-g. 10.50 %.) Central ce 365 ges Zza Markup percentage 8:46 PM शी 11/18/2019 hp ins prt sc ho ll 12 home end m to 44 delete backspace lock 7 homearrow_forward
- pre.9arrow_forwardCh. 7 Incremental Analysis pg 467 Segment Income Statement Please provide the answer and explain the answer to the following question with the information given below. "Big Tent Company is trying to decide whether to keep or drop one of its outdoor wedding tents. The company's segmented income statement shows that this product is generating a net loss as follows:" Sales Revenue: $100,000 Less: Variable Costs $70,000 Contribution Margin $30,000 Less: Direct Fixed Costs $10,000 Segment Margin $20,000 Less: Allocated common fixed costs $30,000 Net Operating Income $(10,000) The company estimates that eliminating this product line will increase the contribution margin on a related product line by $25,000. Based on this information, what impact would dropping the line have on the company's overall profitability?arrow_forwardCheck m A division can sell externally for $73 per unit. Its variable manufacturing costs are $42 per unit, and its variable marketing costs are $20 per unit. What is the optimal transfer price for transferring internally, assuming the division is operating at capacity? to search Multiple Choice O $20 $42 $62 $73 I Hi 37°F Cloudy ^4arrow_forward
arrow_back_ios
SEE MORE QUESTIONS
arrow_forward_ios
Recommended textbooks for you
- Pkg Acc Infor Systems MS VISIO CDFinanceISBN:9781133935940Author:Ulric J. GelinasPublisher:CENGAGE L
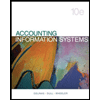
Pkg Acc Infor Systems MS VISIO CD
Finance
ISBN:9781133935940
Author:Ulric J. Gelinas
Publisher:CENGAGE L