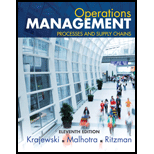
Concept explainers
i)
Interpretation: by using
Concept introduction: Mean(x-bar) charts:
X bar charts is a type of statistical process control chart which measures a central a shift in the central tendency of the process. In other words, X- bar charts monitor the mean or average of a product characteristics. The central line of the X-bar chart is the average of the samples and limits are defined as
Upper control limit
Lower control limit
(
Abbreviations:
R chart:
R-chart or range-chart is also a type of statistical process control chart, but it monitors the range of dispersion or variability of process. The central line of the r- chart is the average range and limits are:
(
The data corresponding to sampling of the given firm is given below
Mean of the diameter
Average range
Control limits are
ii)
Interpretation: by set up
Concept introduction:In probability sampling method,the systematic sampling is a form of it. In which from a larger population sample member are chosen with a fixed, periodic interval but this starts with random sampling.

Want to see the full answer?
Check out a sample textbook solution
Chapter 3 Solutions
Operations Management: Processes and Supply Chains (11th Edition)
- Prepare a graph of the monthly forecasts and average forecast demand for Chicago Paint Corp., a manufacturer of specialized paint for artists. Compute the demand per day for each month (round your responses to one decimal place). Month B Production Days Demand Forecast Demand per Day January 21 950 February 19 1,150 March 21 1,150 April 20 1,250 May 23 1,200 June 22 1,000' July 20 1,350 August 21 1,250 September 21 1,050 October 21 1,050 November 21 December 225 950 19 850arrow_forwardThe president of Hill Enterprises, Terri Hill, projects the firm's aggregate demand requirements over the next 8 months as follows: 2,300 January 1,500 May February 1,700 June 2,100 March April 1,700 1,700 July August 1,900 1,500 Her operations manager is considering a new plan, which begins in January with 200 units of inventory on hand. Stockout cost of lost sales is $125 per unit. Inventory holding cost is $25 per unit per month. Ignore any idle-time costs. The plan is called plan C. Plan C: Keep a stable workforce by maintaining a constant production rate equal to the average gross requirements excluding initial inventory and allow varying inventory levels. Conduct your analysis for January through August. The average monthly demand requirement = units. (Enter your response as a whole number.) In order to arrive at the costs, first compute the ending inventory and stockout units for each month by filling in the table below (enter your responses as whole numbers). Ending E Period…arrow_forwardMention four early warning indicators that a business may be at risk.arrow_forward
- 1. Define risk management and explain its importance in a small business. 2. Describe three types of risks commonly faced by entrepreneurs. 3. Explain the purpose of a risk register. 4. List and briefly describe four risk response strategies. (5 marks) (6 marks) (4 marks) (8 marks) 5. Explain how social media can pose a risk to small businesses. (5 marks) 6. Identify and describe any four hazard-based risks. (8 marks) 7. Mention four early warning indicators that a business may be at risk. (4 marks)arrow_forwardState whether each of the following statements is TRUE or FALSE. 1. Risk management involves identifying, analysing, and mitigating risks. 2. Hazard risks include interest rate fluctuations. 3. Entrepreneurs should avoid all forms of risks. 4. SWOT analysis is a tool for risk identification. 5. Scenario building helps visualise risk responses. 6. Risk appetite defines how much risk an organisation is willing to accept. 7. Diversification is a risk reduction strategy. 8. A risk management framework must align with business goals. 9. Political risk is only relevant in unstable countries. 10. All risks can be eliminated through insurance.arrow_forward9. A hazard-based risk includes A. Political instability B. Ergonomic issues C. Market demand D. Taxation changesarrow_forward
- Practical Management ScienceOperations ManagementISBN:9781337406659Author:WINSTON, Wayne L.Publisher:Cengage,
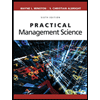