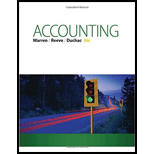
ACCOUNTING-W/CENGAGENOWV2 ACCESS
26th Edition
ISBN: 9781305716780
Author: WARREN
Publisher: CENGAGE L
expand_more
expand_more
format_list_bulleted
Concept explainers
Question
Chapter 20, Problem 20.2APE
To determine
It is a method of cost accounting, which is used where the production is continuous, and the product needs various processes to complete. This method is used to ascertain the cost of the product at each process or stage of production.
To Calculate: started and completed (ounces) during the month July of Company LSC.
Expert Solution & Answer

Want to see the full answer?
Check out a sample textbook solution
Chapter 20 Solutions
ACCOUNTING-W/CENGAGENOWV2 ACCESS
Ch. 20 - Which type of cost system, process or job order,...Ch. 20 - In job order cost accounting, the three elements...Ch. 20 - Prob. 3DQCh. 20 - Why is the cost per equivalent unit often...Ch. 20 - What is the purpose for determining the cost per...Ch. 20 - Rameriz Company is a process manufacturer with two...Ch. 20 - What is the most important purpose of the cost of...Ch. 20 - Prob. 8DQCh. 20 - Prob. 9DQCh. 20 - How does just-in-time processing differ from the...
Ch. 20 - Job order versus process costing Which of the...Ch. 20 - Job order versus process costing Which of the...Ch. 20 - Prob. 20.2APECh. 20 - Units to be assigned costs Keystone Steel Company...Ch. 20 - Equivalent units of materials cost The Filling...Ch. 20 - Equivalent units of materials cost The Rolling...Ch. 20 - Equivalent units of conversion costs The Filling...Ch. 20 - Equivalent units of conversion costs The Rolling...Ch. 20 - Cost per equivalent unit The cost of direct...Ch. 20 - Cost per equivalent unit The cast of direct...Ch. 20 - Cost of units transferred out and ending work in...Ch. 20 - Cost of units transferred out and ending work in...Ch. 20 - Process cost journal entries The cost of materials...Ch. 20 - Process cost journal entries The cost of materials...Ch. 20 - Using process costs for decision making The costs...Ch. 20 - Using process costs for decision making The costs...Ch. 20 - Entries for materials cost flows in a process cost...Ch. 20 - Flowchart of accounts related to service and...Ch. 20 - Entries for flow of factory costs for process cost...Ch. 20 - Factory overhead rate, entry for applying factory...Ch. 20 - Equivalent units of production The Converting...Ch. 20 - Equivalent units of production Units of production...Ch. 20 - Equivalent units of production The following...Ch. 20 - Costs per equivalent unit a. Based upon the data...Ch. 20 - Equivalent units of production Kellogg Company...Ch. 20 - Costs per equivalent unit Georgia Products Inc....Ch. 20 - Equivalent units of production and related costs...Ch. 20 - Cost of units completed and in process a. Based on...Ch. 20 - Errors in equivalent unit computation Napco...Ch. 20 - Cost per equivalent unit The following information...Ch. 20 - Costs per equivalent unit and production costs...Ch. 20 - Cost of production report The debits to Work in...Ch. 20 - Cost of production report The Culling Department...Ch. 20 - Cost of production and journal entries AccuBlade...Ch. 20 - Cost of production and journal entries Lighthouse...Ch. 20 - Process costing for a service company Madison...Ch. 20 - Decision making Mystic Bottling Company bottles...Ch. 20 - Decision making Fix Paper Inc. produces...Ch. 20 - Just-in-time manufacturing The following are some...Ch. 20 - Equivalent units of production: average cost...Ch. 20 - Equivalent units of production: average cost...Ch. 20 - Equivalent units of production: average cost...Ch. 20 - Equivalent units of production and related costs...Ch. 20 - Cost per equivalent unit: average cost method The...Ch. 20 - Cost of production report: average cost method The...Ch. 20 - Cost of production report: average cost method...Ch. 20 - Entries for process cost system FloorMate Carpet...Ch. 20 - Cost of production report Fresh Mountain Coffee...Ch. 20 - Equivalent units and related costs; cost of...Ch. 20 - Work in process account data for two months; cost...Ch. 20 - Cost of production report: average cost method...Ch. 20 - Entries for process cost system Preston Grover...Ch. 20 - Cost of production report Bavarian Chocolate...Ch. 20 - Equivalent units and related costs; cost of...Ch. 20 - Work in process account data for two months; cost...Ch. 20 - Cost of production report: average cost method...Ch. 20 - Ethics in Action Assume that you are the division...Ch. 20 - Accounting for materials costs In papermaking...Ch. 20 - Analyzing unit costs Midstate Containers Inc....Ch. 20 - Communication Jamarcus Bradshaw, plant, manager of...
Knowledge Booster
Learn more about
Need a deep-dive on the concept behind this application? Look no further. Learn more about this topic, accounting and related others by exploring similar questions and additional content below.Similar questions
- Chavez Concrete Inc. has two production departments. Blending had 1,000 units in process at the beginning of the period, two-fifths complete. During the period 7,800 units were received from Mixing, 8,200 units were transferred to the finished goods storeroom, and 600 units were in process at the end of the period, 1/3 complete. The cost of the beginning work in process was: The costs during the month were: 1. Using the data in E5-15, prepare a cost of production summary for the month ended January 31, 2016. 2. Prepare a journal entry to transfer the cost of the completed units from Blending to the finished goods storeroom.arrow_forwardArdt-Barger has a beginning work in process inventory of 5.500 units and transferred in 25,000 units before ending the month with 3.000 u flits that were 100% complete with regard to materials and 80% complete with regard to conversion costs. The cost per unit of material is $5.45, and the cost per unit for conversion is $6.20 per unit, Using the weighted-average method, prepare the companys process cost summary for the month.arrow_forwardThe Converting Department of Worley Company had 2,400 units in work in process at the beginning of the period, which were 35% complete. During the period, 10,800 units were completed and transferred to the Packing Department. There were 1,900 units in process at the end of the period, which were 60% complete. Direct materials are placed into the process at the beginning of production. Determine the number of equivalent units of production with respect to direct materials and conversion costs.arrow_forward
- The Converting Department of Tender Soft Tissue Company uses the weighted average method and had 1,900 units in work in process that were 60% complete at the beginning of the period. During the period, 15,800 units were completed and transferred to the Packing Department. There were 1,200 units in process that were 30% complete at the end of the period. a. Determine the number of whole units to be accounted for and to be assigned costs for the period. b. Determine the number of equivalent units of production for the period. Assume that direct materials are placed in process during production.arrow_forwardA company is using process costing with the first-in, first-out (FIFO) method, and all costs are added evenly throughout the manufacturing process. If there are 5,000 units in beginning work in process inventory (30% complete), 10,000 units in ending work in process inventory (60% complete), and 25,000 units started in process this period, how many equivalent units are there for this period? a. 22,500 units. b. 26,000 units. c. 24,500 units. d. 25,000 units.arrow_forwardFordman Company has a product that passes through two processes: Grinding and Polishing. During December, the Grinding Department transferred 20,000 units to the Polishing Department. The cost of the units transferred into the second department was 40,000. Direct materials are added uniformly in the second process. Units are measured the same way in both departments. The second department (Polishing) had the following physical flow schedule for December: Costs in beginning work in process for the Polishing Department were direct materials, 5,000; conversion costs, 6,000; and transferred in, 8,000. Costs added during the month: direct materials, 32,000; conversion costs, 50,000; and transferred in, 40,000. Required: 1. Assuming the use of the weighted average method, prepare a schedule of equivalent units. 2. Compute the unit cost for the month.arrow_forward
- Vexar manufactures nails. Manufacturing is a one-step process where the nails are forged. This is the information related to this years production: Â Ending inventory was 100% complete as to materials and 70% complete as to conversion, and the total materials cost is $115,080 and the total conversion cost is $72,072. Using the weighted-average method, what are the unit costs if the company transferred out 34,000 units? Using the weighted-average method, prepare the companys process cost summary for the month.arrow_forwardPetrini Products Co. has two departments: Mixing and Cooking. At the beginning of the month, Cooking had 4,000 units in process with costs of 8,600 from Mixing, and its own departmental costs of 500 for materials, 1,000 for labor, and 2,500 for factory overhead. During the month, 10,000 units were received from Mixing with a cost of 25,000. Cooking incurred costs of 4,250 for materials, 8,500 for labor, and 21,250 for factory overhead, and finished 12,000 units. At the end of the month, there were 2,000 units in process, one-half completed. Required: 1. Determine the unit cost for the month in Cooking. 2. Determine the adjusted weighted average unit cost for all units received from Mixing. 3. Determine the unit cost of goods finished. 4. Determine the accumulated cost of the goods finished and of the ending work in process. (Round unit costs to three decimal places.)arrow_forwardJacson Company produces two brands of a popular pain medication: regular strength and extra strength. Regular strength is produced in tablet form, and extra strength is produced in capsule form. All direct materials needed for each batch are requisitioned at the start. The work orders for two batches of the products are shown below, along with some associated cost information: In the Mixing Department, conversion costs are applied on the basis of direct labor hours. Budgeted conversion costs for the department for the year were 60,000 for direct labor and 190,000 for overhead. Budgeted direct labor hours were 5,000. It takes one minute of labor time to mix the ingredients needed for a 100-unit bottle (for either product). In the Bottling Department, conversion costs are applied on the basis of machine hours. Budgeted conversion costs for the department for the year were 400,000. Budgeted machine hours were 20,000. It takes one-half minute of machine time to fill a bottle of 100 units. Required: 1. What are the conversion costs applied in the Mixing Department for each batch? The Bottling Department? 2. Calculate the cost per bottle for the regular and extra strength pain medications. 3. Prepare the journal entries that record the costs of the 12,000 regular strength batch as it moves through the various operations. 4. Suppose that the direct materials are requisitioned by each department as needed for a batch. For the 12,000 regular strength batch, direct materials are requisitioned for the Mixing and Bottling departments. Assume that the amount of cost is split evenly between the two departments. How will this change the journal entries made in Requirement 3?arrow_forward
- Larkin Company produces leather strips for western belts using three processes: cutting, design and coloring, and punching. The weighted average method is used for all three departments. The following information pertains to the Design and Coloring Department for the month of June: a. There was no beginning work in process. b. There were 400,000 units transferred in from the Cutting Department. c. Ending work in process, June 30: 50,000 strips, 80 percent complete with respect to conversion costs. d. Units completed and transferred out: 330,000 strips. The following costs were added during the month: a. Direct materials are added at the beginning of the process. b. Inspection takes place at the end of the process. All spoilage is considered normal. Required: 1. Calculate equivalent units of production for transferred-in materials, direct materials added, and conversion costs. 2. Calculate unit costs for the three categories of Requirement 1. 3. What is the total cost of units transferred out? What is the cost of ending work-in-process inventory? How is the cost of spoilage treated? 4. Assume that all spoilage is considered abnormal. Now, how is spoilage treated? Give the journal entry to account for the cost of the spoiled units. Some companies view all spoilage as abnormal. Explain why. 5. Assume that 80 percent of the units spoiled are abnormal and 20 percent are normal spoilage. Show the spoilage treatment for this scenario.arrow_forwardProteger Company manufactures insect repellant lotion. The Mixing Department, the first process department, mixes the chemicals required for the repellant. The following data are for the current year: Direct materials are added at the beginning of the process. Ending inventory is 95 percent complete with respect to direct labor and overhead. The cost of goods transferred out for the year is: a. 4,471,200 b. 3,571,200 c. 3,780,000 d. 3,024,000arrow_forwardPant Risers manufactures bands for self-dressing assistive devices for mobility-impaired individuals. Manufacturing is a one-step process where the bands are cut and sewn. This is the information related to this years production: Â Ending inventory was 100% complete as to materials and 70% complete as to conversion, and the total materials cost is $57,540 and the total conversion cost is $36,036. Using the weighted-average method, what are the unit costs if the company transferred out 17,000 units? What is the value of the inventory transferred out and the value of the ending WIP inventory?arrow_forward
arrow_back_ios
SEE MORE QUESTIONS
arrow_forward_ios
Recommended textbooks for you
- Managerial AccountingAccountingISBN:9781337912020Author:Carl Warren, Ph.d. Cma William B. TaylerPublisher:South-Western College PubPrinciples of Accounting Volume 2AccountingISBN:9781947172609Author:OpenStaxPublisher:OpenStax CollegeCornerstones of Cost Management (Cornerstones Ser...AccountingISBN:9781305970663Author:Don R. Hansen, Maryanne M. MowenPublisher:Cengage Learning
- Principles of Cost AccountingAccountingISBN:9781305087408Author:Edward J. Vanderbeck, Maria R. MitchellPublisher:Cengage LearningFinancial And Managerial AccountingAccountingISBN:9781337902663Author:WARREN, Carl S.Publisher:Cengage Learning,Managerial Accounting: The Cornerstone of Busines...AccountingISBN:9781337115773Author:Maryanne M. Mowen, Don R. Hansen, Dan L. HeitgerPublisher:Cengage Learning
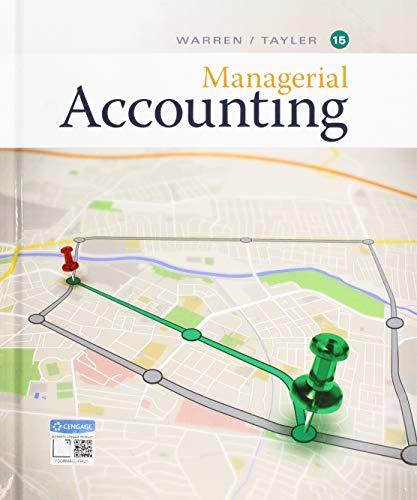
Managerial Accounting
Accounting
ISBN:9781337912020
Author:Carl Warren, Ph.d. Cma William B. Tayler
Publisher:South-Western College Pub
Principles of Accounting Volume 2
Accounting
ISBN:9781947172609
Author:OpenStax
Publisher:OpenStax College
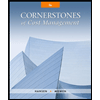
Cornerstones of Cost Management (Cornerstones Ser...
Accounting
ISBN:9781305970663
Author:Don R. Hansen, Maryanne M. Mowen
Publisher:Cengage Learning
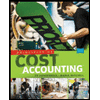
Principles of Cost Accounting
Accounting
ISBN:9781305087408
Author:Edward J. Vanderbeck, Maria R. Mitchell
Publisher:Cengage Learning
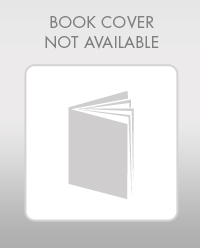
Financial And Managerial Accounting
Accounting
ISBN:9781337902663
Author:WARREN, Carl S.
Publisher:Cengage Learning,
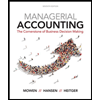
Managerial Accounting: The Cornerstone of Busines...
Accounting
ISBN:9781337115773
Author:Maryanne M. Mowen, Don R. Hansen, Dan L. Heitger
Publisher:Cengage Learning
Cost Accounting - Definition, Purpose, Types, How it Works?; Author: WallStreetMojo;https://www.youtube.com/watch?v=AwrwUf8vYEY;License: Standard YouTube License, CC-BY