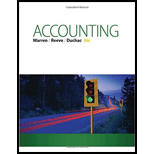
Madison Electric Company uses a fossil fuel (coal) plant for generating electricity. the facility can generate 900 megawatts (million watts) per hour. The plant operates 600 hours during March. Electricity is used as it is generated; thus, there are no inventories at the beginning or end of the period. The March conversion and fuel costs are as follows:
Conversion costs | $40,500,000 |
Fuel | 10,800,000 |
Total | $51,300,000 |
Madison also has a wind farm that can generate 100 megawatts per hour. the wind farm receives sufficient wind to run 300 hours for March. The March conversion costs for the wind farm (mostly
Conversion costs | $2,700,000 |
a. Determine the cost per megawatt hour (MWh) for the fossil fuel plant and the wind farm to identify the lowest cost facility in March,
b. Why are equivalent units of production not needed in determining the cost per megawatt hour (MWh) for generating electricity?
c. What advantage does the fossil fuel plant have over the wind farm?

Trending nowThis is a popular solution!

Chapter 20 Solutions
ACCOUNTING-W/CENGAGENOWV2 ACCESS
- Zippy Inc. manufactures a fuel additive, Surge, which has a stable selling price of 44 per drum. The company has been producing and selling 80,000 drums per month. In connection with your examination of Zippys financial statements for the year ended September 30, management has asked you to review some computations made by Zippys cost accountant. Your working papers disclose the following about the companys operations: Standard costs per drum of product manufactured: Materials: Costs and expenses during September: Chemicals: 645,000 gallons purchased at a cost of 1,140,000; 600,000 gallons used. Empty drums: 94,000 purchased at a cost of 94,000; 80,000 drums used. Direct labor: 81,000 hours worked at a cost of 816,480. Factory overhead: 768,000. Required: Calculate the following for September, using the formulas on pages 421422 and 424 (Round unit costs to the nearest whole cent and compute the materials variances for both Surge and for the drums.): 1. Materials quantity variance. 2. Materials purchase price variance. 3. Labor efficiency variance. 4. Labor rate variance.arrow_forwardAlgers Company produces dry fertilizer. At the beginning of the year, Algers had the following standard cost sheet: Algers computes its overhead rates using practical volume, which is 54,000 units. The actual results for the year are as follows: a. Units produced: 53,000 b. Direct materials purchased: 274,000 pounds at 2.50 per pound c. Direct materials used: 270,300 pounds d. Direct labor: 40,100 hours at 17.95 per hour e. Fixed overhead: 161,700 f. Variable overhead: 122,000 Required: 1. Compute price and usage variances for direct materials. 2. Compute the direct labor rate and labor efficiency variances. 3. Compute the fixed overhead spending and volume variances. Interpret the volume variance. 4. Compute the variable overhead spending and efficiency variances. 5. Prepare journal entries for the following: a. The purchase of direct materials b. The issuance of direct materials to production (Work in Process) c. The addition of direct labor to Work in Process d. The addition of overhead to Work in Process e. The incurrence of actual overhead costs f. Closing out of variances to Cost of Goods Soldarrow_forwardSubject: acountingarrow_forward
- Han Products manufactures 47,500 units of part S-6 each year for use on its production line. At this level of activity, the cost per unit for part S-6 is as follows: Direct materials Direct labour Variable overhead Fixed overhead $ 5.25 11.25 4.25 10.05 Total cost per part $30.80 An outside supplier has offered to sell 41,500 units of part S-6 each year to Han Products for $27.25 per part. If Han Products accepts this offer, the facilities now being used to manufacture part S-6 could be rented to another company at an annual rental of $98,000. However, Han Products has determined that one-third(1/3) of the fixed overhead being applied to part S-6 will be avoided if part S-6 is purchased from the outside supplier. Requlred: 1. What is the net dollar advantage or disadvantage of accepting the outside supplier's offer? (Do not round the Intermedlate calculations. Round your Intermedlete calculetions to two decimal places.) 2. What is the annual rental value at which the company will be…arrow_forwardShine Engine Company manufacturers Part A which is used in several of its engine models. Monthly production costs for 1,000 units are as follows: Direct materials sh. 40,000 Direct labour 10,000 Variable overhead costs 30,000 Fixed overhead costs 20,000 Total costs 100,000 It is estimated that 10% of the fixed overhead costs assigned to Part A will no longer be incurred if the company purchases Part A from the outside supplier. The company has the option of purchasing the part from an outside supplier at sh. 85 per…arrow_forwardShine Engine Company manufacturers Part A which is used in several of its engine models. Monthly production costs for 1,000 units are as follows: Direct materials sh. 40,000 Direct labour 10,000 Variable overhead costs 30,000 Fixed overhead costs 20,000 Total costs 100,000 It is estimated that 10% of the fixed overhead costs assigned to Part A will no longer be incurred if the company purchases Part A from the outside supplier. The company has the option of purchasing the part from an outside supplier at sh. 85 per…arrow_forward
- Juan Company considers repairs and maintenance (R&M) to be a mixed cost. Over the past five months they've had the following R&M costs: Month Units Produced Total R&M cost February 400 $5, 680 March 350 $4, 800 April 870 $6, 900 May 300 $4, 890 June 800 $7,350 Using the High-Low method calculate the expected cost of R&M for July assuming they expect 1,000 units to be producedarrow_forwardABC Company manufactures Part AA for use in its production cycle. The costs per unit for 25,000 units for the part are as follows: Direct materials P 7.50 Direct labor 37.50 Variable overhead 15.00 Fixed overhead 20.00 XYZ Company has offered to sell ABC Company the 25,000 units needed by the latter for P75 per unit. If ABC Company accepts the offer, the released facilities could be rented out in the amount of P112,500. In addition, P12.50 per unit of fixed overhead applied to part AA would be eliminated or avoided. What alternative is more desirable and by what amount it is more desirable? 1. Buy - P 50,000 2. Make - P50,000 3. Buy - P262,500 4. Make - P 262,500 O 1 O 2 O 3 O 4arrow_forwardABC Company manufactures Part AA for use in its production cycle. The costs per unit for 25,000 units for the part are as follows: Direct materials P 7.50 Direct labor 37.50 Variable overhead 15.00 Fixed overhead 20.00 XYZ Company has offered to sell ABC Company the 25,000 units needed by the latter for P75 per unit. If ABC Company accepts the offer, the released facilities could be rented out in the amount of P112,500. In addition, P12.50 per unit of fixed overhead applied to part AA would be eliminated or avoided. What alternative is more desirable and by what amount it is more desirable? Buy – P 50,000 Make – P50,000 Buy – P262,500 Make – P 262,500 Group of answer choices 1 2 3 4arrow_forward
- Can you please check my workarrow_forwardAerobill Inc. makes 7,500 units of a part each year. This part is used in one of the company's products. The company's Accounting Department reports the following costs of producing the part at the current production volume: Direct materials $10.25 per unit Direct labor $15.50 per unit Variable overhead $5.90 per unit Supervisor's salary $81,000 per year Depreciation of special $15,500 per year equipment Allocated general $2.10 per unit overhead An outside supplier has offered to make the part for Aerobill and sell it to Aerobill for $41.50 per unit. If this offer is accepted, then the supervisor's salary and all variable costs can be avoided. The special equipment used to make the part was purchased many years ago and has no salvage value or other use. The allocated general overhead represents fixed costs of the entire company and would be reallocated if the part were outsourced. If the part is outsourced, then the space used to produce the part could be used to make more of one of…arrow_forwardGraham Petroleum produces oil. On May 1, it had no work-in-process inventory. It started production of 205 million barrels of oil in May and shipped 175 million barrels in the pipeline. The costs of the resources used by Graham in May consist of the following: Materials $ 1,981 million Conversion costs (labor and overhead) $ 3,230 million Required: The production supervisor estimates that the ending work in process is 60 percent complete on May 31. Compute the cost of oil shipped in the pipeline and the amount in work-in-process ending inventory as of May 31. (Do not round intermediate calculations. Enter your answers in millions. For example, enter "1" instead of "1,000,000".)arrow_forward
- Financial And Managerial AccountingAccountingISBN:9781337902663Author:WARREN, Carl S.Publisher:Cengage Learning,Managerial AccountingAccountingISBN:9781337912020Author:Carl Warren, Ph.d. Cma William B. TaylerPublisher:South-Western College PubPrinciples of Accounting Volume 2AccountingISBN:9781947172609Author:OpenStaxPublisher:OpenStax College
- Cornerstones of Cost Management (Cornerstones Ser...AccountingISBN:9781305970663Author:Don R. Hansen, Maryanne M. MowenPublisher:Cengage LearningManagerial Accounting: The Cornerstone of Busines...AccountingISBN:9781337115773Author:Maryanne M. Mowen, Don R. Hansen, Dan L. HeitgerPublisher:Cengage LearningPrinciples of Cost AccountingAccountingISBN:9781305087408Author:Edward J. Vanderbeck, Maria R. MitchellPublisher:Cengage Learning
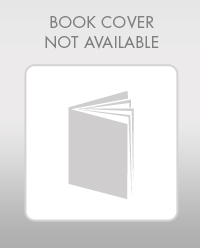
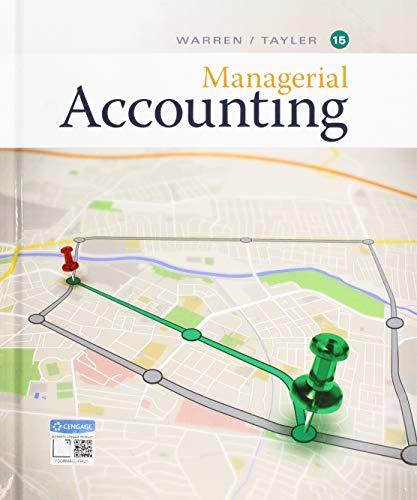
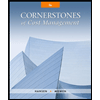
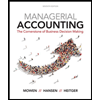
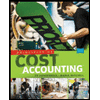