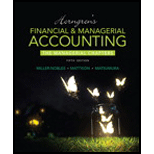
Darrel & Co. makes electronic components. Chris Darrel, the president, recently instructed Vice President Jim Bruegger to develop a total quality control program. “If we don’t at least match the quality improvements our competitors are making,” he told Bruegger, “we’ll soon be out of business.” Bruegger began by listing various “costs of quality” that Darrel incurs. The first six items that came to mind were:
- a. Costs incurred by Darrel customer representatives traveling to customer sites to repair defective products, $13,000.
- b. Lost profits from lost sales due to reputation for less-than-perfect products, $35,000.
- c. Costs of inspecting components in one of Darrel’s production processes, $40,000.
- d. Salaries of engineers who are redesigning components to withstand electrical overloads, $65,000.
- e. Costs of reworking defective components after discovery by company inspectors, $50,000.
- f. Costs of electronic components returned by customers, $70,000.
Classify each item as a prevention cost, an appraisal cost, an internal failure cost, or an external failure cost. Then determine the total cost of quality by category.

Want to see the full answer?
Check out a sample textbook solution
Chapter 19 Solutions
Horngren's Financial & Managerial Accounting, The Managerial Chapters (6th Edition)
Additional Business Textbook Solutions
Intermediate Accounting (2nd Edition)
Essentials of MIS (13th Edition)
Horngren's Accounting (12th Edition)
Gitman: Principl Manageri Finance_15 (15th Edition) (What's New in Finance)
Principles of Operations Management: Sustainability and Supply Chain Management (10th Edition)
Financial Accounting, Student Value Edition (5th Edition)
- Oriole Company sells product 2005WSC for $55 per unit and uses the LIFO method. The cost of one unit of 2005WSC is $52, and the replacement cost is $51. The estimated cost to dispose of a unit is $6, and the normal profit is 40% of selling price. At what amount per unit should product 2005WSC be reported, applying lower-of-cost-or-market?arrow_forwardNonearrow_forwardGeneral accountingarrow_forward
- Please correct answer with accounting questionarrow_forwardA company has decided to purchase equipment, needing to borrow $100,000 from its local bank to make the purchase. The bank gives the company two options: (a) 60-month installment note with 4% interest or (b) 120-month installment note with 8% interest. Lenders often charge a higher interest rate for longer-term loans to compensate for additional risk of lending for a longer time period. Record $100,000 cash received from the issuance of the 120-month installment note with 8% interest.Record $100,000 cash received from the issuance of the 120-month installment note with 8% interest. Select the options to display a 120-month installment note with 12% interest. How much of the principal amount is due after the 60th payment?arrow_forward!??arrow_forward
- Managerial Accounting: The Cornerstone of Busines...AccountingISBN:9781337115773Author:Maryanne M. Mowen, Don R. Hansen, Dan L. HeitgerPublisher:Cengage LearningCornerstones of Cost Management (Cornerstones Ser...AccountingISBN:9781305970663Author:Don R. Hansen, Maryanne M. MowenPublisher:Cengage Learning
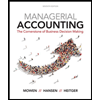
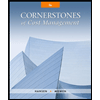