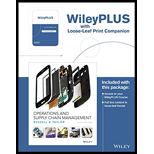
Concept explainers
The Instant Paper Clip Office Supply Company
Christie Levine is the manager of the Instant Paper Clip Office Supply Company in Louisville. The company attempts to gain an advantage over Christie maintains these inventory levels by borrowing cash on a daily basis front the First American Bank. She estimates that for the coming fiscal year the company’s demand for cash to pay for inventory will be $17,000 per day for 305 working days. Any money she borrows during the year must be repaid with interest by the end of the year. The annual interest rate currently charged by the bank is 9%. Any time Christie takes out a loan to purchase inventory, the bank charges the company a loan origination fee of $1200 plus 2¼ points (2.25% of the amount borrowed).
Christie often uses EOQ analysis to determine optimal amounts of inventory to order for different office supplies. Now she is wondering if she can use the same type of analysis to determine an optimal borrowing policy. Determine the amount of the loan Christie should borrow from the bank, the total annual cost of the company’s borrowing policy, and the number of loans the company should obtain during the year. Also determine the level of cash on hand at which the company should apply for a new loan given that it takes 15 days for a loan to be processed by the bank.
Suppose the bank offers Christie a discount as follows. On any loan amount equal to or greater than $500,000, the bank will lower the number of points charged on the loan origination fee from 2.25% to 2.00%. What would be the company’s optimal amount borrowed?

Want to see the full answer?
Check out a sample textbook solution
Chapter 13 Solutions
Operations and Supply Chain Management, 9th Edition WileyPLUS Registration Card + Loose-leaf Print Companion
Additional Business Textbook Solutions
Financial Accounting: Tools for Business Decision Making, 8th Edition
Marketing: An Introduction (13th Edition)
Financial Accounting (12th Edition) (What's New in Accounting)
Operations Management
Essentials of Corporate Finance (Mcgraw-hill/Irwin Series in Finance, Insurance, and Real Estate)
Fundamentals of Management (10th Edition)
- I am not sure if this is correct, because 8 cannot go directly to 10.arrow_forwardA practical application in real life to the Critical Path Method is the construction of a bridge with references, give a detailed essay on the stages involved in constructing a bridgearrow_forwardPlease assist in writing a complete reasearch project of the following title: Title of research: Study on the impact of Technology in the Work Place.arrow_forward
- Intuition is both an emotional experience and a nonconscious analytic process. One problem, however, is that not all emotions signaling that there is a problem or opportunity represent intuition. Please in your Personal opinion how we would know if our “gut feelings” are intuition or not, and if not intuition, suggest what might be causing them.arrow_forwardA coworker suggests that the company where you both work would be much more effective if there were no organizational politics. Please in your personal and detailed opinion, What would you say to this person in reply?arrow_forwardWhat is a bottleneck? Would you try to reduce a bottleneck? Why or why not? Please provide a referencearrow_forward
- Your firm has been the auditor of Caribild Products, a listed company, for a number of years. The engagement partner has asked you to describe the matters you would consider when planning the audit for the year ended 31January 2022. During recent visit to the company you obtained the following information: (a) The management accounts for the 10 months to 30 November 2021 show a revenue of $260 million and profit before tax of $8 million. Assume sales and profits accrue evenly throughout the year. In the year ended 31 January 2021 Caribild Products had sales of $220 million and profit before tax of $16 million. (b) The company installed a new computerised inventory control system which has operated from 1 June 2021. As the inventory control system records inventory movements and current inventory quantities, the company is proposing: (i) To use the inventory quantities on the computer to value the inventory at the year-end (ii) Not to carry out an inventory count at the year-end (c)…arrow_forwardDevelop and implement a complex and scientific project for an organisation of your choice. please include report include the following: Introduction Background research to the project The 5 basic phases in the project management process Project Initiation Project Planning Project Execution Project Monitoring and Controlling Project Closing Conclusionarrow_forwardNot use ai pleasearrow_forward
- Sam's Pet Hotel operates 51 weeks per year, 6 days per week, and uses a continuous review inventory system. It purchases kitty litter for $11.00 per bag. The following information is available about these bags: > Demand 95 bags/week > Order cost $52.00/order > Annual holding cost = 25 percent of cost > Desired cycle-service level = 80 percent >Lead time 4 weeks (24 working days) > Standard deviation of weekly demand = 15 bags > Current on-hand inventory is 320 bags, with no open orders or backorders. a. Suppose that the weekly demand forecast of 95 bags is incorrect and actual demand averages only 75 bags per week. How much higher will total costs be, owing to the distorted EOQ caused by this forecast error? The costs will be $ higher owing to the error in EOQ. (Enter your response rounded to two decimal places.)arrow_forwardSam's Pet Hotel operates 50 weeks per year, 6 days per week, and uses a continuous review inventory system. It purchases kitty litter for $10.50 per bag. The following information is available about these bags: > Demand = 95 bags/week > Order cost = $55.00/order > Annual holding cost = 35 percent of cost > Desired cycle-service level = 80 percent > Lead time = 4 weeks (24 working days) > Standard deviation of weekly demand = 15 bags > Current on-hand inventory is 320 bags, with no open orders or backorders. a. Suppose that the weekly demand forecast of 95 bags is incorrect and actual demand averages only 75 bags per week. How much higher will total costs be, owing to the distorted EOQ caused by this forecast error? The costs will be $ 10.64 higher owing to the error in EOQ. (Enter your response rounded to two decimal places.) b. Suppose that actual demand is 75 bags but that ordering costs are cut to only $13.00 by using the internet to automate order placing. However, the buyer does…arrow_forwardBUS-660 Topic 4: Intege... W Midterm Exam - BUS-66... webassign.net b Answered: The binding c... × W Topic 4 Assignment - BU... how to get more chegg... b My Questions | bartleby + macbook screenshot - G... C Consider the following m... As discussed in Section 8.3, the Markowitz model uses the variance of the portfolio as the measure of risk. However, variance includes deviations both below and above the mean return. Semivariance includes only deviations below the mean and is considered by many to be a better measure of risk. (a) Develop a model that minimizes semivariance for the Hauck Financial data given in the file HauckData with a required return of 10%. Assume that the five planning scenarios in the Hauck Financial Services model are equally likely to occur. Hint: Modify model (8.10)-(8.19). Define a variable d for each 5 - scenario and let d≥ Ŕ – R¸ with d¸ ≥ 0. Then make the objective function: Min 1 5 Σας Let Min s.t. 15 FS = proportion of portfolio invested in the foreign…arrow_forward
- Purchasing and Supply Chain ManagementOperations ManagementISBN:9781285869681Author:Robert M. Monczka, Robert B. Handfield, Larry C. Giunipero, James L. PattersonPublisher:Cengage LearningPractical Management ScienceOperations ManagementISBN:9781337406659Author:WINSTON, Wayne L.Publisher:Cengage,
- MarketingMarketingISBN:9780357033791Author:Pride, William MPublisher:South Western Educational PublishingContemporary MarketingMarketingISBN:9780357033777Author:Louis E. Boone, David L. KurtzPublisher:Cengage LearningFoundations of Business (MindTap Course List)MarketingISBN:9781337386920Author:William M. Pride, Robert J. Hughes, Jack R. KapoorPublisher:Cengage Learning
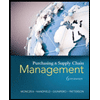
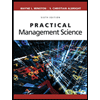
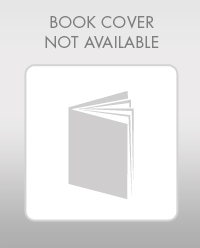
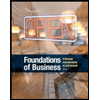