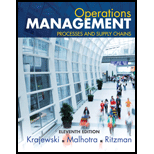
Concept explainers
(a)
Interpretation:The objective here is to demonstrate all three cost
Concept Introduction:
The Company is in the process of buying a new warehouse in three of the cities. Annual fixed costs and variable costs are different between cities.
Fixed costs are defined as the cost that does not change with the change in level of output whereas the variable costs are defined as the costs that change with the change in the level of output. Total cost is the addition of fixed costs and variable costs.
(b)
Interpretation:The city that provides the lowest total costs is to be identified.
Concept Introduction:Fixed costs are defined as the cost that does not change with the change in level of output whereas the variable costs are defined as the costs that change with the change in the level of output. Total cost is the addition of fixed costs and variable costs.

Want to see the full answer?
Check out a sample textbook solution
Chapter 13 Solutions
Operations Management: Processes and Supply Chains (11th Edition)
- At Quick Car Wash, the wash process is advertised to take less than 6 minutes. Consequently, management has set a target average of 330 seconds for the wash process. Suppose the average range for a sample of 7 cars is 10 seconds. Use the accompanying table to establish control limits for sample means and ranges for the car wash process. Click the icon to view the table of factors for calculating three-sigma limits for the x-chart and R-chart. The UCLR equals seconds and the LCLR equals seconds. (Enter your responses rounded to two decimal places.)arrow_forwardIf Jeremy who is the VP for the operations, proceeds with their existing prototype (which is option a), the firm can then expect sales to be 120,000 units at $550 each. And with a probability of 0.52 and a 0.48 probability of 65,000 at $550. we However, he uses his value analysis team (option b), the firm expects sales of 75,000 units at $770, with a probability of 0.78 and a 0.22 probability of 65,000 units at $770. Value engineering, at a cost of $100,000, is only used in option b. Which option for this has the highest expected monetary value (EMV)? The EMV for option a is $? The EMV for option b is $? Which has the highest expected monetary value. A or B?arrow_forwardPart 1 of 2 Jim's Outfitters, Inc., makes custom western shirts. The shirts could be flawed in various ways, including flaws in the weave or color of the fabric, loose buttons or decorations, wrong dimensions, and uneven stitches. Jim randomly examined 10 shirts, with the following results shown to the right. Shirt Defects 1 7 2 1 4 13 3 10 2 8 5 9 10 8 7 a. Assuming that 10 observations are adequate for these purposes, determine the three-sigma control limits for defects per shirt. The UCLC equals and the LCL equals (Enter your responses rounded to two decimal places. If your answer for LCL is negative, enter this value as 0.)arrow_forward
- Management at Webster Chemical Company is concerned as to whether caulking tubes are being properly capped. If a significant proportion of the tubes are not being sealed, Webster is placing its customers in a messy situation. Tubes are packaged in large boxes of 144. Several boxes are inspected, and the following numbers of leaking tubes are found: Sample Tubes Sample Tubes Sample Tubes 1 7 8 7 15 7 2 7 9 8 16 9 3 6 10 7 17 3 4 4 11 1 18 7 5 8 12 8 19 7 6 7 2 9 13 14 1 20 6 7 Total 121 Calculate p-chart three-sigma control limits to assess whether the capping process is in statistical control. The UCLp equals and the LCLp equals (Enter your responses rounded to three decimal places. If your answer for LCLp is negative, enter this value as 0.)arrow_forwardAspen Plastics produces plastic bottles to customer order. The quality inspector randomly selects four bottles from the bottle machine and measures the outside diameter of the bottle neck, a critical quality dimension that determines whether the bottle cap will fit properly. The dimensions (in.) from the last six samples are Bottle Sample 1 2 3 4 1 0.624 0.586 0.602 0.591 2 0.613 0.599 0.578 0.618 3 0.606 0.585 0.587 0.623 4 0.581 0.623 0.571 0.610 5 0.609 0.610 0.623 0.617 6 0.605 0.573 0.570 0.602 Click the icon to view the table of factors for calculating three-sigma limits for the x-chart and R-chart. Suppose that the specification for the bottle neck diameter is 0.600 ± 0.050 in. and the population standard deviation is 0.014 in. a. What is the process capability index? The Cpk is (Enter your response rounded to two decimal places.)arrow_forwardHow would you handle the Apple 'batterygate' scandal as an operations manager? What quality measures would you take to fix the problem and prevent it from happening again? When would you implement these measures and communicate with the stakeholders?arrow_forward
- Perosnal Thoughts about the articlearrow_forwardRevenue retrieval for Brew Mini= $ round response to two decimal places What would be the best design alternative? Brew master or brew miniarrow_forwardThe revenue retrieval for PG Glass design is ?. Enter response as a whole number). The revenue retrieval for Glass Unlimited design is ? (enter your response as a whole number). What is The best design alternative? Glass unlimited or PG Glass?arrow_forward
- Practical Management ScienceOperations ManagementISBN:9781337406659Author:WINSTON, Wayne L.Publisher:Cengage,Purchasing and Supply Chain ManagementOperations ManagementISBN:9781285869681Author:Robert M. Monczka, Robert B. Handfield, Larry C. Giunipero, James L. PattersonPublisher:Cengage Learning
- Management, Loose-Leaf VersionManagementISBN:9781305969308Author:Richard L. DaftPublisher:South-Western College PubContemporary MarketingMarketingISBN:9780357033777Author:Louis E. Boone, David L. KurtzPublisher:Cengage Learning
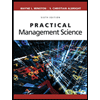
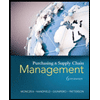
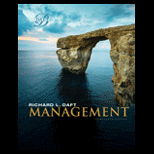
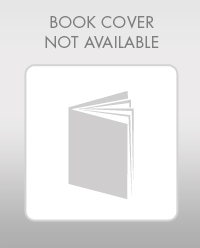