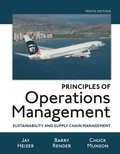
Concept explainers
Managing Inventory at Frito-Lay
Frito-Lay hat flourished since its origin—the 1931 purchase of a small San Antonio firm for $100 that included a recipe, 19 retail accounts, and a hand-operated potato ricer. The multi-billion-dollar company, headquartered in Dallas, now hat 41 products—15 with sales of over $100 million per year and 7 at over $1 billion in sales. Production takes place in 36 product-focused plants in the U.S. and Canada, with 48,000 employees.
Inventory it a mayor investment and an expensive asset in most firms. Holding costs often exceed 25% of product value, but in Frito-Lay’s prepared food industry, holding cost can be much higher because the raw materials are perishable. In the food industry, inventory spoils. So poor inventory management is not only expensive but can also yield an unsatisfactory product that in the extreme can also ruin market acceptance.
Mayor ingredients at Frito-Lay are corn meal, corn, potatoes, oil, and seasoning. Using potato chips to illustrate rapid inventory flow: potatoes are moved via truck from farm, to regional plants for processing, to warehouse, to the retail store. This happens in a matter of hours—not days or weeks. This keeps freshness high and holding costs low.
Frequent deliveries of the main ingredients at the Florida plant, for example, take several forms:
♦ Potatoes are delivered in 10 truckloads per day, with 150,000 lbs consumed in one shift: the entire potato storage area will only hold 7½ hours’ worth of potatoes
♦ Oil inventory arrives by rail car, which lasts only 4½ days.
♦ Corn meal arrives from various farms in the Midwest, and inventory typically averages 4 days’ production.
♦ Seasoning inventory averages 7 days.
♦ Packaging inventory averages 8 to 10 days.
Frito-Lay’s product-focused facility represents a major capital investment. That investment must achieve high utilization to be efficient. The capital cost must be spread over a substantial volume to drive down total cost of the snack foods produced. This demand for high utilization requires reliable equipment and tight
Frito-Lay’s non-MRO inventory moves rapidly. Raw material quickly becomes work-in-process, moving through the system and out the door as a bag of chips in about
1. Hem does the mix of Frito-Lay’s inventory differ from those at a machine or cabinet shop (a process-focused facility)?

Want to see the full answer?
Check out a sample textbook solution
Chapter 12 Solutions
EBK PRINCIPLES OF OPERATIONS MANAGEMENT
- How would you design and implement a modern networking solution for JAMS Manufacturing to connect all their facilities and ensure seamless communication? The company currently has standalone systems in three manufacturing plants and an office building, each using its own modem or router for internet access. The goal is to create private networks for each location, connect them to one another, and provide Internet access to all. You’ll need to consider factors like new computer systems, servers, and telecommunications wiring, and explain how your solution will benefit the company and how it will be implemented effectively.arrow_forwardIdentify specific performance management processes covered in this course and how each aligns with an elements of LaFevor’s HCMS Model.arrow_forwardIdentify specific performance management processes covered in this course and how each aligns with LaFevor’s HCMS Model. LaFevor, K. (2017). What’s in Your Human Capital Management Strategy? The Game Plan, the Path, and Achievingarrow_forward
- assess how Human Capital Management Strategy is aimed at building an effective integrated performance management system: Discuss how human capital management strategy relates to performance management.arrow_forwardCASE STUDY 9-1 Was Robert Eaton a Good Performance Management Leader? R obert Eaton was CEO and chairman of Chrys- ler from 1993 to 1998, replacing Lee Iacocca, who retired after serving in this capacity since 1978. Eaton then served as cochairman of the newly merged DaimlerChrysler organization from 1998 to 2000. In fact, Eaton was responsible for the sale of Chrysler Corporation to Daimler-Benz, thereby creating DaimlerChrysler. With 362,100 employees, DaimlerChrysler had achieved revenues of €136.4 billion in 2003. DaimlerChrysler's passenger car brands included Maybach, Mercedes-Benz, Chrysler, Jeep, Dodge, and Smart. Commercial vehicle brands included Mercedes-Benz, Freightliner, Sterling, Western Star, and Setra. From the beginning of his tenure as CEO, Eaton communicated with the people under him. He immediately shared his plans for the future with his top four executives, and upon the advice of his colleague, Bob Lutz, decided to look around the company before making any hasty…arrow_forwardCritically assess Martin’s coaching style.arrow_forward
- Compare Robert Eaton’s performance management leadership presented in the case against the performance management leadership principles, functions, and behaviors. What recommendations can be made about what he might do more effectively? Explain and defend your answer.arrow_forwardIn the context of the material in Chapter 9, provide a critical analysis of the decisions that Henry has made in assigning Martin to this role.arrow_forwardpanies (pp. 80-118). New York, NY: Times Books, specifically Chap. 4, "Robert Eaton and Robert Lutz; The Copilots." CASE STUDY 9-2 Performance Management Leadership at Henry's Commercial Sales and Leasing H enry is the owner of a small real estate agency that handles the sale and leasing of commercial property. He has two real estate agents working in the office, along with himself. He also has two customer service representatives (CSRs), each of whom has a real estate license, and one receptionist who has worked for the company for about three months. Henry has recently decided that he needs another customer service representative. He hasarrow_forward
- Discuss possible solutions to help Tara become an effective CSR. What should martin be doing to help her?arrow_forwardWhat are the ethical challenges regarding employees (i.e., diversity, discrimination, sexual harassment, privacy, employee theft, bad leadership, etc.) that Apple Inc. has faced over the past five to ten years and that they should prepare to face in the next five to ten years. Once a developed list of challenges is created, consider how having faced those challenges will impact and be impacted by the social cause you've selected. Propose the findings on the ethical challenges faced by Apple Inc. in recent history and the near future. Analyze ways in which each challenge was (and/or could be) appropriately handled and areas for improvement. Evaluate the ethical/moral aspects of Apple Inc. that protected it from ethical challenges in the past and could protect it in the future. Assess how ethical challenges and handling of ethical challenges could positively or negatively impact the charitable cause are selected and how the selection of your social cause could positively or negatively…arrow_forwardBy selecting Cigna Accredo pharmacy that i identify in my resand compare the current feedback system against the “Characteristics of a Good Multiple Source Feedback Systems” described in section 8-3-3. What can be improved? As a consultant, what recommendations would you make?arrow_forward
- Purchasing and Supply Chain ManagementOperations ManagementISBN:9781285869681Author:Robert M. Monczka, Robert B. Handfield, Larry C. Giunipero, James L. PattersonPublisher:Cengage LearningPractical Management ScienceOperations ManagementISBN:9781337406659Author:WINSTON, Wayne L.Publisher:Cengage,
- Contemporary MarketingMarketingISBN:9780357033777Author:Louis E. Boone, David L. KurtzPublisher:Cengage LearningMarketingMarketingISBN:9780357033791Author:Pride, William MPublisher:South Western Educational Publishing
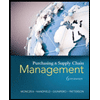
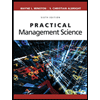
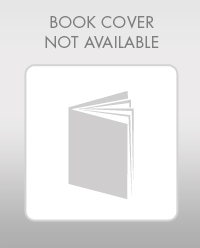