Production planning and control is the single decision area in a company's manufacturing strategy that most directly impacts the manufacturing system's ability to achieve operational mix flexibility. With product variety being a fundamental industrial feature in modern manufacturing environments, mix flexibility is a key objective for manufacturing companies to meet customer requirements, with regard to the correct mix of products, at the required volumes and at the required timing. Sequencing is perhaps the single most important production planning routine for mix flexibility achievement on a shared manufacturing resource. However, unlike discrete manufacturing, there are limited prescribed techniques for sequencing routines in process manufacturing. This paper explores sequencing via the product wheel technique through its application in two case studies. Sequencing of n jobs through 2 machines (Johnson's rule) Problem: Consider two machines and six jobs flow shop scheduling in Francisco's Junkshop problem. Job Taken by machines 1 2 1 4 3 3 3 14 16 4 10 1 8 12 12 9 Sum 53 45
Production planning and control is the single decision area in a company's manufacturing strategy that most directly impacts the manufacturing system's ability to achieve operational mix flexibility. With product variety being a fundamental industrial feature in modern manufacturing environments, mix flexibility is a key objective for manufacturing companies to meet customer requirements, with regard to the correct mix of products, at the required volumes and at the required timing. Sequencing is perhaps the single most important production planning routine for mix flexibility achievement on a shared manufacturing resource. However, unlike discrete manufacturing, there are limited prescribed techniques for sequencing routines in process manufacturing. This paper explores sequencing via the product wheel technique through its application in two case studies. Sequencing of n jobs through 2 machines (Johnson's rule) Problem: Consider two machines and six jobs flow shop scheduling in Francisco's Junkshop problem. Job Taken by machines 1 2 1 4 3 3 3 14 16 4 10 1 8 12 12 9 Sum 53 45
Practical Management Science
6th Edition
ISBN:9781337406659
Author:WINSTON, Wayne L.
Publisher:WINSTON, Wayne L.
Chapter2: Introduction To Spreadsheet Modeling
Section: Chapter Questions
Problem 20P: Julie James is opening a lemonade stand. She believes the fixed cost per week of running the stand...
Related questions
Question

Transcribed Image Text:Production planning and control is the single decision area in a company's manufacturing
strategy that most directly impacts the manufacturing system's ability to achieve
operational mix flexibility. With product variety being a fundamental industrial feature in
modern manufacturing environments, mix flexibility is a key objective for manufacturing
companies to meet customer requirements, with regard to the correct mix of products, at
the required volumes and at the required timing.
Sequencing is perhaps the single most important production planning routine for mix
flexibility achievement on a shared manufacturing resource. However, unlike discrete
manufacturing, there are limited prescribed techniques for sequencing routines in process
manufacturing. This paper explores sequencing via the product wheel technique through
its application in two case studies.
Sequencing of n jobs through 2 machines (Johnson's rule)
Problem: Consider two machines and six jobs flow shop scheduling in Francisco's
Junkshop problem.
Job
Taken by machines
1
6
4
2
3
3
3
14
16
4
10
1
8
12
6
12
9
Sum
53
45
2.

Transcribed Image Text:Using Johnson's algorithm obtain the optimal sequence.
Stage
Unscheduled
Min
Assignment
Partial
Job
sequence/ Full
sequence
1
4
Then use the optimal sequence to minimize and identify the markspan, write your answer
on the table below.
Job
M/C-1
M/C-1
Idle time on
m/c-2
Time in
Time out
Time in
Time out
Expert Solution

This question has been solved!
Explore an expertly crafted, step-by-step solution for a thorough understanding of key concepts.
Step by step
Solved in 3 steps with 3 images

Recommended textbooks for you
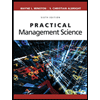
Practical Management Science
Operations Management
ISBN:
9781337406659
Author:
WINSTON, Wayne L.
Publisher:
Cengage,
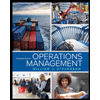
Operations Management
Operations Management
ISBN:
9781259667473
Author:
William J Stevenson
Publisher:
McGraw-Hill Education
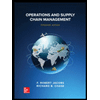
Operations and Supply Chain Management (Mcgraw-hi…
Operations Management
ISBN:
9781259666100
Author:
F. Robert Jacobs, Richard B Chase
Publisher:
McGraw-Hill Education
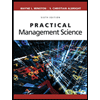
Practical Management Science
Operations Management
ISBN:
9781337406659
Author:
WINSTON, Wayne L.
Publisher:
Cengage,
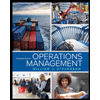
Operations Management
Operations Management
ISBN:
9781259667473
Author:
William J Stevenson
Publisher:
McGraw-Hill Education
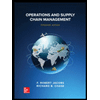
Operations and Supply Chain Management (Mcgraw-hi…
Operations Management
ISBN:
9781259666100
Author:
F. Robert Jacobs, Richard B Chase
Publisher:
McGraw-Hill Education
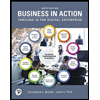
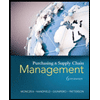
Purchasing and Supply Chain Management
Operations Management
ISBN:
9781285869681
Author:
Robert M. Monczka, Robert B. Handfield, Larry C. Giunipero, James L. Patterson
Publisher:
Cengage Learning
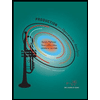
Production and Operations Analysis, Seventh Editi…
Operations Management
ISBN:
9781478623069
Author:
Steven Nahmias, Tava Lennon Olsen
Publisher:
Waveland Press, Inc.