MEE 323 Su21 - Homework #4
pdf
keyboard_arrow_up
School
Arizona State University *
*We aren’t endorsed by this school
Course
323
Subject
Mechanical Engineering
Date
Jan 9, 2024
Type
Pages
14
Uploaded by EarlGuineaPigPerson1061
Summer 2021B MEE 323 –
Computer Aided Engineering II Homework #4 Assigned:
July 26, 2021 Due Date:
August 02, 2021 by 11:59 PM
Instructions: C
reate a folder named “Homework
_4
” in your U:
\ drive. Save all of your model data and a copy of your homework report in this folder.
Use this word file as a template for your homework report. Please turn in the assignment on the course Gradescope before the deadline. Homework Objectives: Learn to create and validate line models (beams and trusses). Learn to carry out stress stiffening and buckling analyses in ANSYS Workbench. Reading Assignment: Look through Chapter 6
in the textbook for examples of surface models and simulation techniques. Question 1: The members of the truss shown in the figure below have a square cross-sectional area of 1.96 in
2
and are made of structural steel. The left end is fixed but allowed to pivot, and the right end is allowed to freely move horizontally as well as pivot (no vertical motion is allowed); use appropriate supports to model the two boundary conditions. Model the truss structure in ANSYS by creating lines on a sketch and then using the "Lines from Sketches" tool to generate the line model. Use a mesh "Edge Sizing" control to ensure that each member of the truss consists of only one element (as was done in class).
Summer 2021B 2 (a)
Show a figure of the sketch appropriately dimensioned and fully constrained. (b)
Show a figure of the mesh with one element for each member of the truss. (c)
Show a plot of the total deformation with the undeformed wireframe. (d)
Insert a beam tool and show the figure of the direct stress (unaveraged) in the members of the truss. Right-click on the direct stress and choose "Export" to save the stress data in a file. Show the stress data in a table below. Will the truss support the given load without failing? What is the safety factor?
Summer 2021B 3 Node Number Element Number Direct Stress (psf) 1 3 42399 2 4 -42405 3 2 -42401 4 1 -42405 5 1 -42405 1 5 21206 1 6 42399 1 7 21206 2 7 21206 3 3 42399 3 4 -42405 4 2 -42401 4 6 42399 5 5 21206 F.S. = 5.22E6/42405 = 123 (e)
Insert a probe and extract the reaction forces at the supports and tabulate them below. Verify these values by carrying out a global verification, i.e. sum of forces in the two directions must be zero, and the sum of the moments taken about any point on the structure must also be zero. Pin Support Moment = 0 Force in +Y direction = 500 Roller Support Moment = 0 Force in +Y direction = 500 (f)
Insert a beam result to extract the axial forces in each member of the truss and tabulate them below. Use static equilibrium hand calculation (at node 1) to verify that this is indeed correct
Your preview ends here
Eager to read complete document? Join bartleby learn and gain access to the full version
- Access to all documents
- Unlimited textbook solutions
- 24/7 expert homework help
Summer 2021B 4 for the members M1 and M2 as labeled on the figure (remember to consider the reaction at the node as well). Beam Axial Force –
Ansys Axial Force –
Hand Calc 12 288.65 14 -577.18 23 288.65 24 -577.12 25 577.12 35 -577.18 45 -577.12 (g)
Mesh the truss with multiple elements for each member and carry out an Eigenvalue Buckling analysis. Fix all vertices such that they do not deflect out of the plane of the truss and fix their rotations so that they just pivot about the Z-axis. Show figures of the buckling modes. Identify the critical member and the buckling load multiplier. Is the truss structure safe from a buckling standpoint? a.
Buckling mode 1 –
Load multiplier =35.462 –
Critical member = L_45 b.
Buckling mode 2 –
Load multiplier = 44.56 –
Critical Member(s) = L_14 + L_35 No, the structure is not safe from a buckling standpoint because the F.S. for yield strength of the material is much higher than the load multiplier required for buckling to occur.
Summer 2021B 5 Question 2: The members of the 3-D space truss shown in the figure below are made of aluminum alloy and have a circular cross-sectional area of 2.250e-3 m
2
. The 4 left endpoints are fixed but allowed to pivot (use appropriate supports), and the two endpoints on the right end are subjected to a load of 5200 N oriented at 30 deg. from the vertical as shown in the figure. The node numbers and coordinates are given in the following table. Node Number X Coord. (m) Y Coord. (m) Z Coord. (m) 1 0 0 0 2 0 4 0 3 4 4 0 4 4 0 0 5 0 0 4 6 0 4 4 7 4 4 4 8 4 0 4 9 8 0 0 10 8 0 4 5200
N
5200
N
Pinned
Summer 2021B 6 (a)
Create the geometry of the truss by creating a "Point" feature in Design Modeler and using the "Lines From Points" to create the truss elements. Specify a rectangular cross section for the truss members. Create a coordinates text file and read that in when you create the "Point" feature. Show your coordinates text file below (copy and paste what you have in your coordinates text file below). Also show a figure of the final geometry. 1 1 0 0 0 1 2 0 4 0 1 3 4 4 0 1 4 4 0 0 1 5 0 0 4 1 6 0 4 4 1 7 4 4 4 1 8 4 0 4 1 9 8 0 0 1 10 8 0 4 (b)
Use a mesh "Edge Sizing" control to ensure that each member of the truss consists of only one element. Show a figure of the mesh.
Your preview ends here
Eager to read complete document? Join bartleby learn and gain access to the full version
- Access to all documents
- Unlimited textbook solutions
- 24/7 expert homework help
Summer 2021B 7 (c)
Insert a beam tool and show the figure of the direct stress (unaveraged) in the members of the truss. Use the "Max" and "Min" probes to show the location of the maximum and minimum stresses. Explain why we use the unaveraged stresses and not the averaged stresses. Use unaveraged stresses because averaged stresses consider the stress of nearby elements which would be incorrect for trusses since we know from mechanics of materials that the stress in each truss is constant. i)
Minimum combined stress ii)
Maximum combined stress
Summer 2021B 8 (d)
Determine the factor of safety considering yielding failure. Comment on the magnitude of the factor of safety –
i.e., why do you think this structure warrants such a high factor of safety? Which truss member is the critical one from the standpoint of yielding failure? F.S. = 2.8E8Pa/3.3383E6Pa = 83.87 L_68 is the critical member from a standpoint of yielding failure since it experiences the largest magnitude of stress in the analysis. This structure warrants a high factor of safety because of the un equal loading throughout the members and to minimize movement in the structure by ensuring that the structure is ridged enough to withstand the applied load. (e)
Insert probes and extract the reaction forces and moments at the supports and tabulate them below. Do they satisfy static equilibrium conditions? Support Force X Force Y Force Z Moment 6 -9698.6 5239.7 737.77 0 2 -8314 3765.2 -0.35 0 5 7098.6 1.14 -737.7 0 1 5714.8 0.576 0.286 0 All the forces do satisfy static equilibrium conditions. (f)
Duplicate the analysis of (a) above and change the mesh so that you now have 25 elements per truss member. Repeat the analysis and check the safety factor of the design. Comment on any differences seen or not seen. F.S. = 2.8E8Pa/3.34E6 = 83.83, is the factor of safety found from running the analysis again with 25 elements per truss. Support Force X Force Y Force Z Moment 6 -9698.6 5239.7 737.77 0 2 -8314 3765.2 -0.35 0 5 7098.6 1.14 -737.7 0 1 5714.8 0.576 0.286 0 Did not notice any differences in the results for the 25 elements per truss analysis as compared to the analysis with one element per truss. All analyses yielded almost identical results with very small changes. (g)
Pass the solution of (f) to an eigenvalue buckling block and extract the first 4 positive
buckling modes and load multipliers. Show figures of the buckling modes. Considering the first buckling mode, what is the factor of safety of the design from the standpoint of buckling and which is the critical member in the system?
Summer 2021B 9 a.
Mode 1 –
Multiplier = 7.2332 For the first buckling mode, the factor of safety from the design standpoint of buckling is 20.385, the critical member in the system is the member from point 5 to point 8. b.
Mode 2 –
Multiplier = 8.0242 c.
Mode 3 –
Multiplier = 9.5474 d.
Mode 4 –
Multiplier = 10.351
Your preview ends here
Eager to read complete document? Join bartleby learn and gain access to the full version
- Access to all documents
- Unlimited textbook solutions
- 24/7 expert homework help
Summer 2021B 10 Question 3: Consider the structural steel space load frame shown in the figure below. A frame is different from a truss in that the members are modeled as beams, and the mesh needs to have multiple elements per member. (a)
Create a set of points for the frame in Design Modeler (either from a coordinates file or one by one). Use the Lines from Points tool to create a line body of the geometry shown. Use a rectangular cross section of 0.4 x 0.1 m
2
for all the beams. Show a figure of the final line body with the cross section assigned such that the bending stiffness is maximized in the appropriate direction (i.e. in the X-Y plane for the horizontal beam, and in the Y-Z plane for the vertical beam as well as the angled middle beam). Set the View options in the menu bar as shown on the right. (b)
Mesh the model with the relevance center set to medium. Apply the loads and boundary conditions shown in the figure. Show plots of the mesh, total deformation, minimum combined stress, and maximum combined stress. Set the display options to also show the undeformed model. What is the factor of safety for this design? You can calculate this by dividing the yield strength of structural steel by the maximum absolute value of the stress results. x
y
z
Summer 2021B 11 i)
Mesh ii)
Total deformation iii)
Minimum combined stress iv)
Maximum combined stress
Summer 2021B 12 v)
Factor of safety The factor of safety for the space truss is 2.5E8 Pa / 1.48E8 Pa = 1.68 (c)
Extract the force reactions at the supports and verify that global equilibrium of forces is satisfied. i)
X Y Z Top Support 4527.1 40541 -26300 Bottom Support -4527.1 -25541 -123700 Applied Forces 0 -15000 150000 Sum 0 0 0 (d)
Pass the solution of (b) to an eigenvalue buckling analysis block and extract the first 2 positive buckling modes and load multipliers. Show figures of the buckling modes. Considering the first buckling mode, what is the factor of safety of the design from the standpoint of buckling and which is the critical member in the system? Factor of safety of the design is 16.5 from the standpoint of buckling, the critical member is the middle member between the two supported members. i)
Buckling mode 1 –
Load multiplier = 16.503 ii)
Buckling mode 2 –
Load multiplier = 40.577
Your preview ends here
Eager to read complete document? Join bartleby learn and gain access to the full version
- Access to all documents
- Unlimited textbook solutions
- 24/7 expert homework help
Summer 2021B 13 Question 4: Apply a moment on the thin aluminum alloy
can shown below. Model the can as a surface body
with the appropriate thickness. The can is of length 122 mm with a diameter of 64 mm and a thickness of 0.1 mm. The moment will cause a tensile stress on a principal direction in the can and a compressive stress in another principle direction causing the skin to buckle. Predict the moment that will cause the skin to buckle. (a)
Use the model geometry provided. Mesh the model using a face meshing
control to get a uniform regular mesh. Make sure your mesh is relatively fine. Show a figure of the mesh. (b)
Apply a fixed support on one end. On the other end, create a cylindrical coordinate system. Then apply a displacement support with just the tangential (theta) direction free. Finally apply a moment of 1N-mm to this end. Show a figure of the total deformation.
Summer 2021B 14 (c)
Pass the solution of (b) to an eigenvalue buckling block and predict the moment for the first buckling mode. What is the value of the moment required for this buckling to happen? Also show the first buckling mode shape. The value of moment required for buckling to happen is 24kN*m (d)
The buckling load prediction also shows convergence based on the size of the mesh. Run a convergence analysis by manually
setting the mesh size to 12mm, 10mm, 8mm, 6mm, 4mm, 2mm, and 1mm (you can use parameters to have ANSYS simulate these all at once). Plot the buckling load multiplier vs. mesh size (or number of elements). 0.00E+00
5.00E+09
1.00E+10
1.50E+10
2.00E+10
2.50E+10
3.00E+10
0
2
4
6
8
10
12
14
Load Multiplier
Related Documents
Related Questions
Astronomy Question:
Read the questions slowly and answer with precise and long details about each of the questions. Answer correctly and follow my guidelines for a long and wonderful review after results. Your target/main observable galaxy is the whirlpool galaxy. Target: Whirlpool Galaxy Object Type: Galaxy Distance: 37 million light-years Constellation: Canes Venatici. DO NOT COPY AND PASTE OTHER WORK OR THINGS FROM THE INTERNET, use your own words.Provide refernces if used
In 500 words, please explain the relevance of this object to the physics course material in university andits importance to astronomy. (Some question you may seek to answer are: What beyond the objectitself is learned by studying this class of objects? What sorts of telescopes and observations would beneeded for more detailed, broader reaching studies of this source and objects of its nature?)
arrow_forward
Help me solve this ENGINEERING GRAPHICS question
Use 0.25 cartesian paper or 0.25 Isometric paper please.
arrow_forward
The class I'm taking is physics for scientists and engineers!
**** I need help with part D only*****
Can you please write out the solution and not type out the solution? I had to reask this question because the last tutor typed out the solution and it was very hard for me to follow . Please and thank you for the special request.
I have attached the problem. Please view attachment before answering. Thank you!
arrow_forward
I want to answer all the questions by handwriting.
arrow_forward
Draw it on the graph provided please!
arrow_forward
Don't use chatgpt will upvote
arrow_forward
Put together a short presentation (pitch) for a mechanical engineering student, emphasizing his period of the course (10th) and his most significant achievements such as his change from the naval to mechanical course, the learning of programming languages focused on data analysis (Python and SQL), since the engineering course does not explore these skills, and the improvement of Excel with the VBA language.
arrow_forward
Please make the charts for the questions. Please refer to Successful Project Management (7th Edition). Attached is the example
Thank you.
arrow_forward
I Blackboard @ Texas Tech Uni x
Bb MasteringEngineering - Spri x
E MasteringEngineering Maste X
C Suppose That H = 3.8 M . (Fi x
X Mathway | Calculus Problem x
y! how to take a full page scree
A session.masteringengineering.com/myct/itemView?assignmentProblemID=12360392&offset=next
ABP O
Tp E
G
KAssignment #3
Fundamental Problem 2.29
5 of 6
>
I Review
Part A
Find the magnitude of the projected component of the force along the pipe AO.
(Figure 1)
Express your answer to three significant figures and include the appropriate units.
µA
FAO =
Value
Units
Submit
Request Answer
Figure
4 m
F = 400 N
6 m
5 m
B
4 m
10:31 PM
O Type here to search
2/7/2021
arrow_forward
I need problems 6 and 7 solved.
I got it solved on 2 different occasions and it is not worded correctly.
NOTE: Problem 1 is an example of how it should be answered. Below are 2 seperate links to same question asked and once again it was not answered correctly. 1. https://www.bartleby.com/questions-and-answers/it-vivch-print-reading-for-industry-228-class-date-name-review-activity-112-for-each-local-note-or-c/cadc3f7b-2c2f-4471-842b-5a84bf505857
2. https://www.bartleby.com/questions-and-answers/it-vivch-print-reading-for-industry-228-class-date-name-review-activity-112-for-each-local-note-or-c/bd5390f0-3eb6-41ff-81e2-8675809dfab1
arrow_forward
LESSON: AUTODESK AUTOCAD
Choose from the choices:
arrow_forward
1. Use the collision theory to explain why a lump of sugar is better to use in hot cup of tea ,but granulated sugar is better to use in iced tea.
2.suppose you held a lighted match to a solid pieces of wood and another match to a pile of wood shavings .which form of wood catch fire more easily and why?
arrow_forward
Home
Insert
Draw
Design
Layout
References
Maili
OLYTECH
Calibri (Bo...
11
v A A
Aa v
m Air. Ma
Paste
в I
U v ab x,
x | A
Name:
ID No.:
rm Air. M
Date:
CRN:
Course Code: JACV 506E
Aircraft Mechanical Mainte
Practice.
ces ( CRI
Page
Originated By
Mark awarded -
Instructor/Assessor:
Assignment: Interpret engineering drawings and diagrams
bus
se Mat
hing Pl
Questions: -
1. Write 2 differences between isometric and oblique projections?
ssment
2. Write 5 details found on the drawing title block?
Feedba
3. Write 4 types of sectional views?
4. Name 3 methods how drawings are stored in?
5. Name 3 types of fits?
arrow_forward
I just need help with part D, thanks
arrow_forward
reful-files from the Internet can contain viruses. Unless you need to edit, it's safer to stay in Protected View.
Your Full Name
Enable Editing
ID:
Sec:
Q1: Which one is stronger; undeformed copper or
copper that has been plastically deformed?
Q2: Which one is stronger; unannealed copper or
copper annealed (heated) at 750° C?
Q3: Why?
101.
O
Focus
arrow_forward
The first photo is the question, where the 2nd shows some problem solving strategies
arrow_forward
I need parts 8, 9, and 10 answered. Number 1 is an example of how it should be answered.
NOTE: Read the instructions, no where does it say any drawing is required. It is really frustrating when I wait all this time for an answer to a question and some tutor does even read the instructions and just declines it...its ridicilous.
arrow_forward
Hello. I just want to make sure the answers I chosen on the image attached are correct because I am unsure.
arrow_forward
Directions: modify the standard SolidWorks ANSI B Landscape layout for your own engineering
consulting company. Include a logo, change the legal notice, and make other changes as you see fit.
Be creative! Save this as a SolidWorks drawing layout template and use in subsequent submissions.
Usual DRAWN BY.
Deliverable: screenshot of your personalized layout/template without any drawings on it.
arrow_forward
please help solve A-F. thank you
You are an engineer working on a project and your prototype has failed prematurely. You question whether or not a key component of the prototype was manufactured with the correct material. There are two way to check for the material properties. The first way is to have a material certification done to confirm the exact material composition. This will take some time. The second method to confirm the material properties is to make an ASTM test sample and test for the material properties. This tensile test was completed on a test sample with an initial diameter of .501” and an initial length of 2”. The Load-Deflection data for this tensile test is below. Use this data to answer the first set of questions on the Final Exam in eLearning. A. Determine the Ultimate Tensile Strength B. Determine the 0.2% Offset Yield Strength C. Determine the value of the Proportional Limit D. Determine the Modulus of Elasticity E. Determine the Strain at Yield F. Calculate %…
arrow_forward
I need parts 1, 2, and 3 answered pertaining to the print provided.
NOTE: If you refuse to answers all 3 parts and insist on wasting my question, then just leave it for someone else to answer. I've never had an issue until recently one single tutor just refuses to even read the instructions of the question and just denies it for a false reasons or drags on 1 part into multiple parts for no reason.
arrow_forward
I think I drew it wrong but can it please be drawn on the isometric paper on my image!
arrow_forward
Enginooring Mochanics: Sutca (1
Fint Scitester, Firt yoat, Academic yer 2020-2021
Deputtane of Civil Engnoeg
Callege of Engincenng
Lasenaty ut Mis
Cm link on Miodle
Instructor: Dr. Murtada Abass
Mid-term Examination of E113 1 year
2020-2021
Date: March 5, 2021
Time: 20 Minutes
Answer one question only which is
assigned for you only
Your Question is assigned via Mloodle
in Ouizzes Section
Your answer to the question will be
submitted via Zoom
Question: Determine the reactions of the
truss shown in the Figure,
5 KN
lom
A
جميلة محمد
15
کشيش
lom
IDM
Page15
arrow_forward
Please give me the answers for this i been looking at this for a hour and my head hurts
arrow_forward
I need help solving this problem.
arrow_forward
SEE MORE QUESTIONS
Recommended textbooks for you
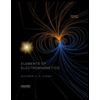
Elements Of Electromagnetics
Mechanical Engineering
ISBN:9780190698614
Author:Sadiku, Matthew N. O.
Publisher:Oxford University Press
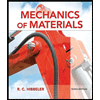
Mechanics of Materials (10th Edition)
Mechanical Engineering
ISBN:9780134319650
Author:Russell C. Hibbeler
Publisher:PEARSON
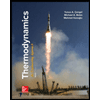
Thermodynamics: An Engineering Approach
Mechanical Engineering
ISBN:9781259822674
Author:Yunus A. Cengel Dr., Michael A. Boles
Publisher:McGraw-Hill Education
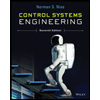
Control Systems Engineering
Mechanical Engineering
ISBN:9781118170519
Author:Norman S. Nise
Publisher:WILEY
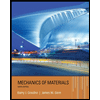
Mechanics of Materials (MindTap Course List)
Mechanical Engineering
ISBN:9781337093347
Author:Barry J. Goodno, James M. Gere
Publisher:Cengage Learning
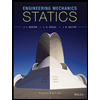
Engineering Mechanics: Statics
Mechanical Engineering
ISBN:9781118807330
Author:James L. Meriam, L. G. Kraige, J. N. Bolton
Publisher:WILEY
Related Questions
- Astronomy Question: Read the questions slowly and answer with precise and long details about each of the questions. Answer correctly and follow my guidelines for a long and wonderful review after results. Your target/main observable galaxy is the whirlpool galaxy. Target: Whirlpool Galaxy Object Type: Galaxy Distance: 37 million light-years Constellation: Canes Venatici. DO NOT COPY AND PASTE OTHER WORK OR THINGS FROM THE INTERNET, use your own words.Provide refernces if used In 500 words, please explain the relevance of this object to the physics course material in university andits importance to astronomy. (Some question you may seek to answer are: What beyond the objectitself is learned by studying this class of objects? What sorts of telescopes and observations would beneeded for more detailed, broader reaching studies of this source and objects of its nature?)arrow_forwardHelp me solve this ENGINEERING GRAPHICS question Use 0.25 cartesian paper or 0.25 Isometric paper please.arrow_forwardThe class I'm taking is physics for scientists and engineers! **** I need help with part D only***** Can you please write out the solution and not type out the solution? I had to reask this question because the last tutor typed out the solution and it was very hard for me to follow . Please and thank you for the special request. I have attached the problem. Please view attachment before answering. Thank you!arrow_forward
- Put together a short presentation (pitch) for a mechanical engineering student, emphasizing his period of the course (10th) and his most significant achievements such as his change from the naval to mechanical course, the learning of programming languages focused on data analysis (Python and SQL), since the engineering course does not explore these skills, and the improvement of Excel with the VBA language.arrow_forwardPlease make the charts for the questions. Please refer to Successful Project Management (7th Edition). Attached is the example Thank you.arrow_forwardI Blackboard @ Texas Tech Uni x Bb MasteringEngineering - Spri x E MasteringEngineering Maste X C Suppose That H = 3.8 M . (Fi x X Mathway | Calculus Problem x y! how to take a full page scree A session.masteringengineering.com/myct/itemView?assignmentProblemID=12360392&offset=next ABP O Tp E G KAssignment #3 Fundamental Problem 2.29 5 of 6 > I Review Part A Find the magnitude of the projected component of the force along the pipe AO. (Figure 1) Express your answer to three significant figures and include the appropriate units. µA FAO = Value Units Submit Request Answer Figure 4 m F = 400 N 6 m 5 m B 4 m 10:31 PM O Type here to search 2/7/2021arrow_forward
- I need problems 6 and 7 solved. I got it solved on 2 different occasions and it is not worded correctly. NOTE: Problem 1 is an example of how it should be answered. Below are 2 seperate links to same question asked and once again it was not answered correctly. 1. https://www.bartleby.com/questions-and-answers/it-vivch-print-reading-for-industry-228-class-date-name-review-activity-112-for-each-local-note-or-c/cadc3f7b-2c2f-4471-842b-5a84bf505857 2. https://www.bartleby.com/questions-and-answers/it-vivch-print-reading-for-industry-228-class-date-name-review-activity-112-for-each-local-note-or-c/bd5390f0-3eb6-41ff-81e2-8675809dfab1arrow_forwardLESSON: AUTODESK AUTOCAD Choose from the choices:arrow_forward1. Use the collision theory to explain why a lump of sugar is better to use in hot cup of tea ,but granulated sugar is better to use in iced tea. 2.suppose you held a lighted match to a solid pieces of wood and another match to a pile of wood shavings .which form of wood catch fire more easily and why?arrow_forward
arrow_back_ios
SEE MORE QUESTIONS
arrow_forward_ios
Recommended textbooks for you
- Elements Of ElectromagneticsMechanical EngineeringISBN:9780190698614Author:Sadiku, Matthew N. O.Publisher:Oxford University PressMechanics of Materials (10th Edition)Mechanical EngineeringISBN:9780134319650Author:Russell C. HibbelerPublisher:PEARSONThermodynamics: An Engineering ApproachMechanical EngineeringISBN:9781259822674Author:Yunus A. Cengel Dr., Michael A. BolesPublisher:McGraw-Hill Education
- Control Systems EngineeringMechanical EngineeringISBN:9781118170519Author:Norman S. NisePublisher:WILEYMechanics of Materials (MindTap Course List)Mechanical EngineeringISBN:9781337093347Author:Barry J. Goodno, James M. GerePublisher:Cengage LearningEngineering Mechanics: StaticsMechanical EngineeringISBN:9781118807330Author:James L. Meriam, L. G. Kraige, J. N. BoltonPublisher:WILEY
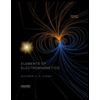
Elements Of Electromagnetics
Mechanical Engineering
ISBN:9780190698614
Author:Sadiku, Matthew N. O.
Publisher:Oxford University Press
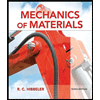
Mechanics of Materials (10th Edition)
Mechanical Engineering
ISBN:9780134319650
Author:Russell C. Hibbeler
Publisher:PEARSON
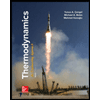
Thermodynamics: An Engineering Approach
Mechanical Engineering
ISBN:9781259822674
Author:Yunus A. Cengel Dr., Michael A. Boles
Publisher:McGraw-Hill Education
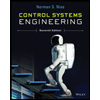
Control Systems Engineering
Mechanical Engineering
ISBN:9781118170519
Author:Norman S. Nise
Publisher:WILEY
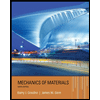
Mechanics of Materials (MindTap Course List)
Mechanical Engineering
ISBN:9781337093347
Author:Barry J. Goodno, James M. Gere
Publisher:Cengage Learning
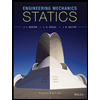
Engineering Mechanics: Statics
Mechanical Engineering
ISBN:9781118807330
Author:James L. Meriam, L. G. Kraige, J. N. Bolton
Publisher:WILEY