MEE 323 Su21 - Homework #5
pdf
keyboard_arrow_up
School
Arizona State University *
*We aren’t endorsed by this school
Course
323
Subject
Mechanical Engineering
Date
Jan 9, 2024
Type
Pages
10
Uploaded by EarlGuineaPigPerson1061
Summer 2021B 1 MEE 323 –
Computer Aided Engineering II Homework #5 Assigned: August 02, 2021 Due Date:
August 09, 2021 by 11:59PM
Instructions: Cr
eate a folder named “Homework_
5
” in your U:
\ drive. Save all of your model data and a copy of your homework report in this folder. Use this document as a template for your homework report. Turn in the assignment on the course GradeScope before the deadline. Homework Objectives: Learn heat transfer, thermal analysis, and thermal-mechanical coupling using FEA. Learn modal analysis and the calculation of natural frequencies and mode shapes using ANSYS. Question 1: Temperature Condition
using Static Structural
An assembly of two identical bars 2.5 mm in width is shown below. One is made of structural steel and the other is made of copper alloy; they are bonded to form a bimetallic strip. The left end is completely fixed. The bar is initially at room temperature (22 deg C) then experiences a uniform 25 deg C decrease in temperature. (a)
Show the figure of the mesh. Use a “Relevance Center” setting of “Fine”.
Summer 2021B 2 (b)
Plot the maximum displacement contour plot with undeformed edge. Find the maximum vertical displacement of the tip of the bimetallic strip. (c)
Plot the von Mises stress contour plot. Find the magnitude and location of the maximum von Mises stress. Question 2: Steady State Thermal
Analysis A furnace wall consists of two layers: fire brick and insulating brick. The temperature inside the furnace is 3000 deg F and the inner surface convection coefficient is 3.333e-3 BTU/s-ft
2
-degF. The ambient temperature is 80 deg F and the outer surface convection coefficient is 5.556e-4 BTU/s-ft
2
-degF. Model a section of the wall as shown below. Use perfectly insulated boundary conditions on all faces except the 1 inch x 1 inch faces that represent the inside and outside surfaces of the walls.
Summer 2021B 3 Material Properties: Fire Brick Wall: K = 2.222e-4 BTU/s-ft-degF Insulating Wall: K = 2.778e-5 BTU/s-ft-degF Geometric properties: Cross section: 1 inch x 1 inch Fire Brick Wall thickness: 9 inches Insulating Wall thickness: 5 inches (a)
Show the figure of the mesh. Use a “Relevance Center” setting of “Medium”.
(b)
Show the final steady state temperature distribution in the wall. What are the maximum and minimum temperatures of the wall material?
Your preview ends here
Eager to read complete document? Join bartleby learn and gain access to the full version
- Access to all documents
- Unlimited textbook solutions
- 24/7 expert homework help
Summer 2021B 4 Max temperatures for the wall material are 2957.2F and the minimum temperature is 336.69F. (c)
Show a plot of the thermal error and comment. Given that the largest magnitude of error is in the range of 10^-5 I would personally take this analysis as being accurate should this not be accurate enough for some precision engineering, the mesh could be refined further still as I only performed minor refinement on the area where the two materials join together.
Summer 2021B 5 Question 3: Transient Heat Transfer in an Infinite Slab A semi-infinite slab is initially at a temperature of 0 deg C. The solid is then suddenly exposed to an environment having a temperature of 1000 deg C and a surface convection coefficient h = 50 W/m
2
-degC. Run a transient analysis and determine the temperature distribution through the solid after 2000 seconds. You can approximate the slab by modeling it as a 2-D rectangle of dimensions 1 meter by 0.1 meter. Use appropriate time step settings for the transient thermal analysis (hint: use smallest time step of 0.1s and largest time step of 10 seconds). Material Properties: Thermal Conductivity, K = 54 W/m-degC Density, ρ = 7833 kg/m
3
Specific Heat, c = 465 J/kg-decC (a)
Show the final temperature distribution in the slab at 2000 seconds. What are the maximum and minimum temperatures of the slab material? Comment on the results. The maximum temperature of the slab material was 157.13C and the minimum temperature was 0.004588C. It does make sense that the slab would not be entirely heated at this point given the small contact patch with the environment that is at 1000C as well as the small-time frame that it is exposed to the area of only 30 min. With convection it would take more time for this small contact area to come up closer to the environment temperature.
Summer 2021B 6 Question 4: Two structural steel rods of diameter 25 mm are joined to form a “T” part as shown. A 10 mm diameter through hole and a 10 x 10 mm square through hole are placed as shown in the figure. (The 65 mm dimension locates the left edge of the 10 x 10 square through hole). The left end is completely fixed. (a)
Find the three lowest natural frequencies of vibration of the structure. Show plots of the mode shapes and describe in your own words the type of motion that occurs in each. Present the frequencies in Rad/sec, Hz, and RPM. Use the medium mesh size setting in the “relevance center”.
a.
Mode 1 –
75.746Hz = 475.92Rad/sec = 4,544.76 RPM Mode 1 is the top half of the t-bar structure rotating around the y axis; oscillating at 75.746Hz. b.
Mode 2 –
85.271Hz = 535.77 Rad/sec = 5116.26 RPM
Your preview ends here
Eager to read complete document? Join bartleby learn and gain access to the full version
- Access to all documents
- Unlimited textbook solutions
- 24/7 expert homework help
Summer 2021B 7 Mode 2 is the top half of the t-bar structure rotating about the x-axis at a frequency of 85.271Hz c.
Mode 3 –
159.85Hz = 1004.36 Rad/sec = 9591 RPM Mode 3 is the very top of the T-Bar structure rotating about the center bar (x-axis) (b)
Use three different mesh densities by choosing 3 different element sizes with a factor of 2 between each (for example, you may choose mesh sizes of 8 mm, 4 mm, and 2 mm). Plot the three calculated frequencies as a function of the number of elements in the mesh. What do you observe? Element Size First Frequency Second Frequency Third Frequency 3 75.414 85.218 159.46 6 75.682 85.429 160.03 12 76.029 85.405 160.33 The mesh density / element size does not impact the found frequencies enough to warrant very fine meshing. As was mentioned in lecture, a fine mesh would benefit a modal analysis if there were also pre-stresses present. 0
50
100
150
200
0
5
10
15
Chart Title
1st Frequency
2nd Frequency
3rd Frequency
Summer 2021B 8 (c)
How do your results change if you remove the two through holes in the structure? Show plots of the mode shapes. Compare numerically (percentage difference) the change in the natural frequencies of the structure. Use the smallest mesh size setting from part (b) above for this. Element Size First Frequency Second Frequency Third Frequency 3 81.835 87.8 167.17 Mode 1 Mode 2 Mode 3 Element Size First Frequency % Difference Second Frequency % Difference Third Frequency % Difference 3 7.85 2.94 4.61
Summer 2021B 9 Question 5: Compute the lowest two non-zero natural frequencies of the free-free vibration of the aluminum alloy U-bar shown below. Present your results in Hz. (a)
Use a full 3-D model. Show plots of the two mode shapes and carry out a convergence analysis until your frequencies converge to within 1% between iterations. Why do you see zero frequency modes? What kind of motion of the structure do these modes represent? We see zero frequency modes because there are no supports on the body, they are motions of the system that occur when there are no supports on the system. a.
Mode 1 –
Converges at 286.96 Hz –
Mode 1 represents a bending motion b.
Mode 2 –
Converges at 707.14Hz –
Mode 2 represents a twisting motion
Your preview ends here
Eager to read complete document? Join bartleby learn and gain access to the full version
- Access to all documents
- Unlimited textbook solutions
- 24/7 expert homework help
Summer 2021B 10 (b)
Use the “mid
-
surface” tool to create a 2
-D shell model of the structure (2-D surface body but 3-D analysis). Show plots of the two mode shapes and carry out a convergence analysis until your frequencies converge to within 1% between iterations. a.
Mode 1 –
Converges at 280.47 Hz –
Mode 1 represents a bending motion b.
Mode 2 –
Converges at 697.55Hz –
Mode 2 represents a twisting motion (c)
Tabulate the mesh statistics of the 3-D and 2-D final models (after convergence). Compute the percentage difference in the natural frequencies predicted by these two models and also the percentage reduction in mesh statistics achieved using the 2-D model. Comment. The mesh statistics show an almost 98% reduction in elements by using a 2-D model over a 3-
D model, while still achieving a very accurate estimate for the natural frequency of the object in question, with a percent difference of 0.17 for the first mode and 1.36 for the second mode. Showing that the 2-D analysis is the better choice when seeking to utilize computational resources efficiently. Mode/Model Type # of elements for convergence Converged Frequency % Difference in Frequency % Reduction in elements Mode 1 - 3D Model 62584 280.96 0.17 97.8 Mode 1 - 2D Model 1400 280.47 Mode 2 - 3D Model 62584 707.14 1.36 97.8 Mode 2 - 2D Model 1400 697.55
Related Documents
Related Questions
LESSON: AUTODESK AUTOCAD
Choose from the choices:
arrow_forward
I want to answer all the questions by handwriting.
arrow_forward
Put together a short presentation (pitch) for a mechanical engineering student, emphasizing his period of the course (10th) and his most significant achievements such as his change from the naval to mechanical course, the learning of programming languages focused on data analysis (Python and SQL), since the engineering course does not explore these skills, and the improvement of Excel with the VBA language.
arrow_forward
Astronomy Question:
Read the questions slowly and answer with precise and long details about each of the questions. Answer correctly and follow my guidelines for a long and wonderful review after results. Your target/main observable galaxy is the whirlpool galaxy. Target: Whirlpool Galaxy Object Type: Galaxy Distance: 37 million light-years Constellation: Canes Venatici. DO NOT COPY AND PASTE OTHER WORK OR THINGS FROM THE INTERNET, use your own words.Provide refernces if used
In 500 words, please explain the relevance of this object to the physics course material in university andits importance to astronomy. (Some question you may seek to answer are: What beyond the objectitself is learned by studying this class of objects? What sorts of telescopes and observations would beneeded for more detailed, broader reaching studies of this source and objects of its nature?)
arrow_forward
Please make the charts for the questions. Please refer to Successful Project Management (7th Edition). Attached is the example
Thank you.
arrow_forward
2. In studying for your CBEMS 125B exam, you get hungry and decide to boil some
water in a pot to make instant noodles. You put your aluminum spoon, with a long handle
(i.e. good to use "long fin approximation"), in the pot in anticipation of stirring the
noodles into the boiling water. However, your phone rings, and you leave the spoon in
the boiling water on the stove for quite a while (i.e. the system reaches steady-state
conditions) before you come back to it. The boiling water is at 100°C and room
temperature is 25°C. The spoon has a square handle that is 0.6 cm per side. At a handle
height of 8 cm, the temperature of the long aluminum spoon is 62°C. The Royal Society
for the Prevention of Accidents lists a maximum surface temperature of 58°C as a "safe"
touchable temperature for metals. Is the spoon safe to pick up at a handle height of 12 cm?
Justify your answer with calculations.
Assume (1) No radiation effect, (2) convection heat transfer coefficient is uniform in the
pot…
arrow_forward
You are spending the summer as an assistant learning how to navigate on a large ship carrying freight across Lake Erie. One day, you and your ship are to travel across the lake a distance of 200 km traveling due north from yourorigin port to your destination port. Just as you leave your origin port, the navigation electronics go down. The captain continues sailing, claiming he can depend on his years of experience on the water as a guide. The engineers work on the navigation system while the ship continues to sail,and winds and waves push it off course. Eventually, enough of the navigation system comes back up to tell you your location. The system tells you that your current position is 50.0 km north of the origin port and 25.0 km east of the port. The captain is a little embarrassed that his ship is sofar off course and barks an order to you to tell him immediately what heading he should set from your current position to the destination port. Give him an appropriate heading angle.
arrow_forward
1. Use the collision theory to explain why a lump of sugar is better to use in hot cup of tea ,but granulated sugar is better to use in iced tea.
2.suppose you held a lighted match to a solid pieces of wood and another match to a pile of wood shavings .which form of wood catch fire more easily and why?
arrow_forward
FINALS ASSIGNMENT IN ME 3215
COMBUSTION ENGINEERING
PROBLEM 1:
A Diesel engine overcome a friction of 200 HP and delivers 1000 BHP. Air consumption is 90 kg per minute.
The Air/fuel ratio is 15 to 1. Find the following:
1. Indicated horsepower
2. The Mechanical efficiency
3. The Brake Specific Fuel Consumption
PROBLEM 2:
The brake thermal efficiency of a diesel engine is 30 percent. If the air to fuel ratio by weight is 20 and the
calorific value of the fuel used is 41800 kJ/kg, what brake mean effective pressure may be expected at
S.P. conditions (Standard Temperature and pressure means 15.6°C and 101.325 kPa, respectively)?
arrow_forward
I need parts 8, 9, and 10 answered. Number 1 is an example of how it should be answered.
NOTE: Read the instructions, no where does it say any drawing is required. It is really frustrating when I wait all this time for an answer to a question and some tutor does even read the instructions and just declines it...its ridicilous.
arrow_forward
The class I'm taking is physics for scientists and engineers!
**** I need help with part D only*****
Can you please write out the solution and not type out the solution? I had to reask this question because the last tutor typed out the solution and it was very hard for me to follow . Please and thank you for the special request.
I have attached the problem. Please view attachment before answering. Thank you!
arrow_forward
Directions: modify the standard SolidWorks ANSI B Landscape layout for your own engineering
consulting company. Include a logo, change the legal notice, and make other changes as you see fit.
Be creative! Save this as a SolidWorks drawing layout template and use in subsequent submissions.
Usual DRAWN BY.
Deliverable: screenshot of your personalized layout/template without any drawings on it.
arrow_forward
The first photo is the question, where the 2nd shows some problem solving strategies
arrow_forward
Don't use chatgpt will upvote
arrow_forward
I need parts 1, 2, and 3 answered pertaining to the print provided.
NOTE: If you refuse to answers all 3 parts and insist on wasting my question, then just leave it for someone else to answer. I've never had an issue until recently one single tutor just refuses to even read the instructions of the question and just denies it for a false reasons or drags on 1 part into multiple parts for no reason.
arrow_forward
Hello. I just want to make sure the answers I chosen on the image attached are correct because I am unsure.
arrow_forward
Please give me the answers for this i been looking at this for a hour and my head hurts
arrow_forward
Enginooring Mochanics: Sutca (1
Fint Scitester, Firt yoat, Academic yer 2020-2021
Deputtane of Civil Engnoeg
Callege of Engincenng
Lasenaty ut Mis
Cm link on Miodle
Instructor: Dr. Murtada Abass
Mid-term Examination of E113 1 year
2020-2021
Date: March 5, 2021
Time: 20 Minutes
Answer one question only which is
assigned for you only
Your Question is assigned via Mloodle
in Ouizzes Section
Your answer to the question will be
submitted via Zoom
Question: Determine the reactions of the
truss shown in the Figure,
5 KN
lom
A
جميلة محمد
15
کشيش
lom
IDM
Page15
arrow_forward
You are an engineer in a company that manufactures and designs several mechanical devices, and your manager asked you to help your customers. In this time, you have two customers, one of them wants to ask about internal combustion engines while the other requires a heat exchanger with particular specifications. Follow the parts in the following tasks to do your job and support your customers.Task 1:Your first customer asked for an internal combustion engine to use it in a designed car. Your role is to describe the operation sequence of different types of available engines, explain their mechanical efficiency, and deliver a detailed technical report which includes the following steps:STEP 1Describe with the aid of diagrams the operational sequence of four stroke spark ignition and four stroke compression ignition engines.STEP 2Explain and compare the mechanical efficiency of two and four-stroke engines.STEP 3Review the efficiency of ideal heat engines operating on the Otto and Diesel…
arrow_forward
conceptual question, no calculations
arrow_forward
Learning Goal:
To learn to apply the method of joints to a truss in a systematic way and thereby find the loading in each member of the truss.
In analyzing or designing trusses, it is necessary to determine the force in each member of the truss. One way to do this is the
method of joints. The method of joints is based on the fact that if the entire truss is in equilibrium, each joint in the truss must also be
in equilibrium (i.e., the free-body diagram of each joint must be balanced).
Consider the truss shown in the diagram. The applied forces are P₁ = 630 lb and P₂ = 410 lb and the distance is d = 8.50 ft.
Figure 1)
1 of 1
A
E
30°
d
B
D
P₁
30°
d
C
arrow_forward
SEE MORE QUESTIONS
Recommended textbooks for you
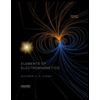
Elements Of Electromagnetics
Mechanical Engineering
ISBN:9780190698614
Author:Sadiku, Matthew N. O.
Publisher:Oxford University Press
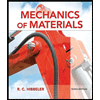
Mechanics of Materials (10th Edition)
Mechanical Engineering
ISBN:9780134319650
Author:Russell C. Hibbeler
Publisher:PEARSON
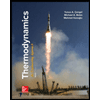
Thermodynamics: An Engineering Approach
Mechanical Engineering
ISBN:9781259822674
Author:Yunus A. Cengel Dr., Michael A. Boles
Publisher:McGraw-Hill Education
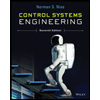
Control Systems Engineering
Mechanical Engineering
ISBN:9781118170519
Author:Norman S. Nise
Publisher:WILEY
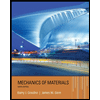
Mechanics of Materials (MindTap Course List)
Mechanical Engineering
ISBN:9781337093347
Author:Barry J. Goodno, James M. Gere
Publisher:Cengage Learning
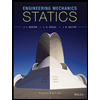
Engineering Mechanics: Statics
Mechanical Engineering
ISBN:9781118807330
Author:James L. Meriam, L. G. Kraige, J. N. Bolton
Publisher:WILEY
Related Questions
- LESSON: AUTODESK AUTOCAD Choose from the choices:arrow_forwardI want to answer all the questions by handwriting.arrow_forwardPut together a short presentation (pitch) for a mechanical engineering student, emphasizing his period of the course (10th) and his most significant achievements such as his change from the naval to mechanical course, the learning of programming languages focused on data analysis (Python and SQL), since the engineering course does not explore these skills, and the improvement of Excel with the VBA language.arrow_forward
- Astronomy Question: Read the questions slowly and answer with precise and long details about each of the questions. Answer correctly and follow my guidelines for a long and wonderful review after results. Your target/main observable galaxy is the whirlpool galaxy. Target: Whirlpool Galaxy Object Type: Galaxy Distance: 37 million light-years Constellation: Canes Venatici. DO NOT COPY AND PASTE OTHER WORK OR THINGS FROM THE INTERNET, use your own words.Provide refernces if used In 500 words, please explain the relevance of this object to the physics course material in university andits importance to astronomy. (Some question you may seek to answer are: What beyond the objectitself is learned by studying this class of objects? What sorts of telescopes and observations would beneeded for more detailed, broader reaching studies of this source and objects of its nature?)arrow_forwardPlease make the charts for the questions. Please refer to Successful Project Management (7th Edition). Attached is the example Thank you.arrow_forward2. In studying for your CBEMS 125B exam, you get hungry and decide to boil some water in a pot to make instant noodles. You put your aluminum spoon, with a long handle (i.e. good to use "long fin approximation"), in the pot in anticipation of stirring the noodles into the boiling water. However, your phone rings, and you leave the spoon in the boiling water on the stove for quite a while (i.e. the system reaches steady-state conditions) before you come back to it. The boiling water is at 100°C and room temperature is 25°C. The spoon has a square handle that is 0.6 cm per side. At a handle height of 8 cm, the temperature of the long aluminum spoon is 62°C. The Royal Society for the Prevention of Accidents lists a maximum surface temperature of 58°C as a "safe" touchable temperature for metals. Is the spoon safe to pick up at a handle height of 12 cm? Justify your answer with calculations. Assume (1) No radiation effect, (2) convection heat transfer coefficient is uniform in the pot…arrow_forward
- You are spending the summer as an assistant learning how to navigate on a large ship carrying freight across Lake Erie. One day, you and your ship are to travel across the lake a distance of 200 km traveling due north from yourorigin port to your destination port. Just as you leave your origin port, the navigation electronics go down. The captain continues sailing, claiming he can depend on his years of experience on the water as a guide. The engineers work on the navigation system while the ship continues to sail,and winds and waves push it off course. Eventually, enough of the navigation system comes back up to tell you your location. The system tells you that your current position is 50.0 km north of the origin port and 25.0 km east of the port. The captain is a little embarrassed that his ship is sofar off course and barks an order to you to tell him immediately what heading he should set from your current position to the destination port. Give him an appropriate heading angle.arrow_forward1. Use the collision theory to explain why a lump of sugar is better to use in hot cup of tea ,but granulated sugar is better to use in iced tea. 2.suppose you held a lighted match to a solid pieces of wood and another match to a pile of wood shavings .which form of wood catch fire more easily and why?arrow_forwardFINALS ASSIGNMENT IN ME 3215 COMBUSTION ENGINEERING PROBLEM 1: A Diesel engine overcome a friction of 200 HP and delivers 1000 BHP. Air consumption is 90 kg per minute. The Air/fuel ratio is 15 to 1. Find the following: 1. Indicated horsepower 2. The Mechanical efficiency 3. The Brake Specific Fuel Consumption PROBLEM 2: The brake thermal efficiency of a diesel engine is 30 percent. If the air to fuel ratio by weight is 20 and the calorific value of the fuel used is 41800 kJ/kg, what brake mean effective pressure may be expected at S.P. conditions (Standard Temperature and pressure means 15.6°C and 101.325 kPa, respectively)?arrow_forward
- I need parts 8, 9, and 10 answered. Number 1 is an example of how it should be answered. NOTE: Read the instructions, no where does it say any drawing is required. It is really frustrating when I wait all this time for an answer to a question and some tutor does even read the instructions and just declines it...its ridicilous.arrow_forwardThe class I'm taking is physics for scientists and engineers! **** I need help with part D only***** Can you please write out the solution and not type out the solution? I had to reask this question because the last tutor typed out the solution and it was very hard for me to follow . Please and thank you for the special request. I have attached the problem. Please view attachment before answering. Thank you!arrow_forwardDirections: modify the standard SolidWorks ANSI B Landscape layout for your own engineering consulting company. Include a logo, change the legal notice, and make other changes as you see fit. Be creative! Save this as a SolidWorks drawing layout template and use in subsequent submissions. Usual DRAWN BY. Deliverable: screenshot of your personalized layout/template without any drawings on it.arrow_forward
arrow_back_ios
SEE MORE QUESTIONS
arrow_forward_ios
Recommended textbooks for you
- Elements Of ElectromagneticsMechanical EngineeringISBN:9780190698614Author:Sadiku, Matthew N. O.Publisher:Oxford University PressMechanics of Materials (10th Edition)Mechanical EngineeringISBN:9780134319650Author:Russell C. HibbelerPublisher:PEARSONThermodynamics: An Engineering ApproachMechanical EngineeringISBN:9781259822674Author:Yunus A. Cengel Dr., Michael A. BolesPublisher:McGraw-Hill Education
- Control Systems EngineeringMechanical EngineeringISBN:9781118170519Author:Norman S. NisePublisher:WILEYMechanics of Materials (MindTap Course List)Mechanical EngineeringISBN:9781337093347Author:Barry J. Goodno, James M. GerePublisher:Cengage LearningEngineering Mechanics: StaticsMechanical EngineeringISBN:9781118807330Author:James L. Meriam, L. G. Kraige, J. N. BoltonPublisher:WILEY
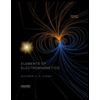
Elements Of Electromagnetics
Mechanical Engineering
ISBN:9780190698614
Author:Sadiku, Matthew N. O.
Publisher:Oxford University Press
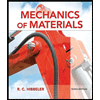
Mechanics of Materials (10th Edition)
Mechanical Engineering
ISBN:9780134319650
Author:Russell C. Hibbeler
Publisher:PEARSON
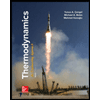
Thermodynamics: An Engineering Approach
Mechanical Engineering
ISBN:9781259822674
Author:Yunus A. Cengel Dr., Michael A. Boles
Publisher:McGraw-Hill Education
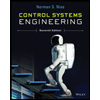
Control Systems Engineering
Mechanical Engineering
ISBN:9781118170519
Author:Norman S. Nise
Publisher:WILEY
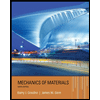
Mechanics of Materials (MindTap Course List)
Mechanical Engineering
ISBN:9781337093347
Author:Barry J. Goodno, James M. Gere
Publisher:Cengage Learning
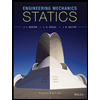
Engineering Mechanics: Statics
Mechanical Engineering
ISBN:9781118807330
Author:James L. Meriam, L. G. Kraige, J. N. Bolton
Publisher:WILEY