Wang_h_Lab4
pdf
keyboard_arrow_up
School
Bellevue College *
*We aren’t endorsed by this school
Course
1500
Subject
Mechanical Engineering
Date
Jan 9, 2024
Type
Pages
7
Uploaded by ElderRoseKudu11
Spring 2023
Lab 4 Report
MSE 1500L
1
1.
Pb-Sn phase diagram
a.
Create a landscape-oriented section and create a single figure containing all 7 Pb-Sn cooling
curves collected by your section.
Each plot should be
3”
tall and
2.25”
wide.
Use arrows on
each plot to identify the phase transition temperatures present.
Spring 2023
Lab 4 Report
MSE 1500L
2
Figure 1. Cooling curves for mixtures of Pb and Sn. A) 0% Sn, B) 20% Sn, C) 40% Sn, D) 62% Sn, E) 75% Sn, F) 85% Sn, G) 100% Sn
A)
B)
C)
D)
E)
F)
G)
Spring 2023
Lab 4 Report
MSE 1500L
3
b.
Summarize the results of your cooling curve analyses by tabulating the temperatures and the
phase transition occurring at each temperature for each composition of the alloy.
Include the
phase transition temperatures shown in
Wiley’s
Animated Figure 9.8 for these 7
compositions.
Table 1. Temperatures and phase transitions occurring for 7 compositions of the alloy compiled from
section 4 data and
Wiley’s
Animated Figure 9.8
Temperature of phase
transition for section 4 (
℃
)
Temperature of phase
transition for Wiley (
℃
)
Transition occurring
Composition
(wt% Sn)
Phase
change 1
Phase
change 2
Phase
change 1
Phase
change 2
Phase
change 1
Phase
change 2
0
326
N/A
327
N/A
Melting
point
α
N/A
20
280
180
277
180
Liquid to
α
+ L
α
+ L to
α
+
β
40
246
180
237
180
Liquid to
α
+ L
α
+ L to
α
+
β
62
180
N/A
180
N/A
Liquid to
α
+
β
N/A
75
192
183
201
180
Liquid to
β
+ L
β
+ L to
α
+
β
85
203
183
215
180
Liquid to
β
+ L
β
+ L to
α
+
β
100
228
N/A
232
N/A
Melting
point
β
N/A
Compositions with only 1 phase transition occurring have the second phase change marked as not
applicable (N/A). Pb is denoted by
α,
and Sn is denoted by
β.
L denotes liquid phase.
c.
Create a phase diagram,
3”
tall by
4”
wide, by plotting your transition temperatures as data
points (y-axis) at each composition (x-axis).
Do not connect the data points. Label the
phases present in each area of your phase diagram.
Your preview ends here
Eager to read complete document? Join bartleby learn and gain access to the full version
- Access to all documents
- Unlimited textbook solutions
- 24/7 expert homework help
Spring 2023
Lab 4 Report
MSE 1500L
4
d.
Create another phase diagram,
3”
tall by
4”
wide, by plotting the transition temperatures read
from
Wiley’s
Animated Figure 9.8 vs composition and label the phases present in each
region.
Comment on i) differences between these phase diagrams, ii) the areas of the
diagram your data could not construct, and iii) any anomalous experimental findings.
i)
In comparing the phase diagram using experimental data and the phase diagram using
Wiley’s
Animated Figure data, they are visually similar. Comparing the numerical values
of the transition temperatures at each composition, all values between the experimental
Figure 2. Transition temperatures at each composition. The phases
present are labeled on the diagram.
α
represents Pb and
β
represents
Sn.
Figure 3. Transition temperatures at each composition. Data
compiled from
Wiley’s
Animated Figure 9.8. The phases present
are labeled on the diagram.
α
represents Pb and
β
represents Sn.
Spring 2023
Lab 4 Report
MSE 1500L
5
and
Wiley’s
Animated Figure differ by an absolute value of less than 10 degrees Celsius.
Only for 85 wt% Sn do the values differ by more than 10 degrees at 12 degrees Celsius.
ii)
The data collected was not able to construct the solidus or the solvus lines for both
α
(Pb
rich solution) and
β
(Sn rich solution) to indicate the limits of solid solubility. The limits
of maximum solid solubility happen at 18.3 and 97.8 wt% Sn, compositions of which
were not recorded.
iii)
In the diagram using
Wiley’s
Animated Figure data, the eutectic temperature stays
constant at 180 degrees Celsius. In the experimental data phase diagram, most of the
eutectic temperatures are at 180 degrees Celsius, but for 75 and 85 wt% Sn, the eutectic
temperature was found to be 183 degrees Celsius. This is minor as the absolute percent
error of 183 degrees Celsius as a result is only 1.67%, but it should be noted that the
eutectic temperature should stay constant.
2.
Microstructure Analysis
a.
Create a figure containing the original and the thresholded images used to determine the
composition of your steel sample. Keep the aspect ratio of your image constant, but scale
each so that they fit side-by-side in one figure.
Figure 4. Image of original sample (left) and image of the sample after threshold (right).
b.
Document your composition calculations and identify the type of steel (1018 or 1045) that
your sample was made from.
Research the typical range of carbon content in each of these
steel alloys. Provide a complete citation of the source or sources you consulted. Do your
results fall within these typical ranges?
For plain-carbon steels, the least significant two digits in the number indicate the weight
percent carbon in each alloy divided by 100. Therefore, for 1018 steel, the weight percent of
carbon would be 0.18% and for 1045 steel, it would be 0.45 wt% carbon (Professor
Choudhury Lecture 26). However, the acceptable range of carbon content for 1018 steel is
0.15-0.20 wt% C (McHone Industries). The acceptable range of carbon content for 1045 steel
is 0.43-0.50 wt% C (AZO Materials). After performing analysis on the sample image, it was
found that the mass fraction of pearlite in ferrite was 59.591% or 0.59591. At 0.76 wt% C,
Spring 2023
Lab 4 Report
MSE 1500L
6
100% composition of pearlite occurs. Using the lever rule, the wt% C (C
0
) in the sample can
be calculated by using the following formula:
𝑊
𝑝𝑒𝑎𝑟𝑙𝑖𝑡𝑒
=
𝐶
0
− 𝐶
𝛼
𝐶
𝑒
− 𝐶
𝛼
Where C
0
is the wt% C at the sample
’
s composition, C
α
is the wt % C at maximum solubility
of
α
ferrite,
𝐶
𝑒
is the wt% C at the eutectoid, where the composition of the sample is 100%
pearlite.
0.59591 =
𝐶
0
− 0.022
0.76 − 0.022
𝐶
0
= 0.46 𝑤𝑡% 𝐶
As shown, the wt% C of the sample is found to be 0.46 which falls in the acceptable range
for 1045 steel, so the identity of the sample is 1045 steel.
1018 steel carbon content source:
https://www.mchoneind.com/carbon-steel-grades-
chart/#:~:text=A%20piece%20of%201018%20steel%20contains%200.18%25%20carbon.,all
owable%20carbon%20range%20of%200.15-0.20%25%20for%20this%20grade.
1045 steel carbon content source:
https://www.azom.com/article.aspx?ArticleID=9153
3.
Hardness profile
a.
Create a
3”
by
3”
plot of the Rockwell hardness (y-axis) versus distance from the quenched
end (x-axis) for each Jominy bar sample.
15
25
35
45
55
0
10
20
30
40
Hardness (RF)
Distance (mm)
Figure 5. Rockwell hardness versus distance from the
quenched end for 1045 steel. Hardness measured on
Rockwell C scale.
Your preview ends here
Eager to read complete document? Join bartleby learn and gain access to the full version
- Access to all documents
- Unlimited textbook solutions
- 24/7 expert homework help
Spring 2023
Lab 4 Report
MSE 1500L
7
b.
Quantitatively compare the hardness profiles for the 1045 and 4140 steels.
In general, 4140 steel has higher hardness measurements compared to 1045 steel. Although
the first hardness measurement closest to the quenching surface for 1045 steel (highest 56.10
RF) is higher than any of the hardness measurements for 4140 steel (highest 52.30 RF), 1045
steel experiences a sharp decline in hardness values and ultimately drops to 19.60 RF. On the
other hand, 4140 steel has relatively high hardness near the surface due to the effects of heat
treatment (quenching). The hardness measurements for 4140 steel experience a more gradual
decline than 1045 steel and ultimately drops to 36.90 RF, which is higher than 1045 steel.
The difference in hardness is due to the composition of the alloys. 1045 steel contains no
other alloying elements, so it is softer and more ductile than 4140 steel which does contain
alloying elements, specifically chromium and molybdenum.
c.
Why is knowing the hardenability of a material important?
Provide an example of an
application where this information would be used in the design of a component.
It is important to know the hardenability of a material because it helps predict how the
material will respond to heat treatment processes and how it will affect the resulting
microstructure and mechanical properties of the material. Using the hardenability of a
material, the appropriate heat treatment process can be used to achieve the desired
microstructure and mechanical properties for a given application. For example, in the design
of a component like a gear, the hardenability of the material must be considered to ensure
that the gear will have the necessary strength and wear resistance over time. If the material
has low hardenability, it is not possible to achieve the desired hardness and strength through
heat treatment, which would compromise the performance and reliability of the gear.
Contrary, if the material has high hardenability, it may be possible to achieve the desired
properties with a less severe quenching process, reducing the risk of distortion or cracking
during heat treatment.
35
40
45
50
55
0
10
20
30
40
Hardness (RF)
Distance (mm)
Figure 6. Rockwell hardness versus distance from the
quenched end for 4140 steel. Hardness measured on
Rockwell C scale.
Related Questions
please show work and formulas so that i may learn
the process correctly. if you use a table please
mention which table was used. thank you so
much.
2. Fill in the blank cells of this table:
T( C)
P(kPa)
u(kJ/kg)
Phase description
175
2524.5
325
4000
325
Saturated liquid
arrow_forward
Draw the cooling curve for steam cooling from 115C to -5 Label each phase (solid, liquid, gas), and each phase change (ie: vaporization, condensation, melt, freeze, sublimation, deposition, etc) on your graph. Reminder: Temperature is on your Y-axis and heat is on your X-axis.
arrow_forward
A substance exists in two solid modifications alpha and beta and also as liquid and vapour at a pressure of 1 atm alpha melts at a lower temperature to form liquid. Also alpha is denser than the liquid but beta is less dense than the liquid assuming that no meta stable equilibria are observed sketch p-t phase diagram show the significance of each point,line and region also show all triple points.
arrow_forward
D23/ Below are given the solidus and liquidus temperatures for the germanium-silicon system. Construct the phase diagram for this system and label each region.
arrow_forward
Usng the phase chan
For each thezgments below answer the assigned questions. Luestions will center around change
in temperature, kinetic energy, particle speed, bonds breaking or forming.
-Alo, make use of the following vocabulary words as they apply for each of the segments below
GAS, SOLID, LIQUID, MEILTING, VAPORIZATION, FREEZING, CONDENSATION
B-C
1. Wha process is taking place during this segment?
2. L chermal energy being added or removed during this segment?
1. Explain why the temperatture is not chaging during this segment.
s the procE6s during this segment andothermic.or expthermic?
C-D
5. What is thr sate of matterfor this segment?
6. What is happening to the temperature?
7. Explain why the temperatiure ischanging,
8. L this change an endothermic or exothumie process/
9. Dexribe the kinetic energy during this sepment
10. Dexribe the particle speed during this gment.
arrow_forward
4. For the A-B alloy the phase diagram below, use the lever rule to find the amount of liquid and solid states and their compositions
at Temperature T. Let Cx = 25%B, C =40%B, Cy = 60 %B
Complete solubility of two metals
in liquid and solid states (Ni -Cu ,Sb - Bi)
TA
M
EM
T
EMa
T
Cy
A
B
Concentration of B in A
www.substoch com
Temperature
arrow_forward
b) Figure 1 shows a phase diagram for Cu-Ni binary system. Make a phase analysis of this
system at point Q.
T.°C
1450
1250
1050
0
20
40
60
80 100
arrow_forward
I need solve without AI and chatgpt
arrow_forward
Please do not copy/repost previous diagrams from chemistry Q&A. Either place path drawing on or use same EXACT axis labeling as the diagram.
arrow_forward
Please help me. thank u!
arrow_forward
can you help me with 4?
arrow_forward
How many kilograms of nickel must be added to 5.66 kg of copper to yield a liquidus temperature of 1200°C? Use Animated Figure.
kg
i
arrow_forward
For the metals A and B, which are given below, create the hypothetical phase diagram between 500 ° C and 900 ° C temperatures.The melting temperature of metal A is 840 ° C.The solubility of B in A can be ignored at all temperatures.Metal B has a melting temperature of 730 ° C.The maximum resolution of A in B is 10 wt% A, which occurs at 600 ° C.At 500 ° C, the solubility of A in B is 6% A by weight.A eutectic 600 ° C and 74% B by weight - 26% by weight A are formed.The second eutectic occurs at 630 ° C and 59% B - 41% A by weight.A third eutectic occurs at 655 ° C and 39% B - 61% A by weight.A congress melting point is formed at 680 ° C and 52% B - 48% A by weight.A second congress melting point is formed at 655 ° C and 66% B - 34% A by weight.The intermetallic compound AB is present at 52 wt% B - 48 wt% A.The intermetallic compound AB2 is present at 66 wt% B to 34 wt% A.
arrow_forward
X Incorrect.
A 40 wt% Ni-60 wt% Cu alloy (Animated Figure 9.3a) is slowly cooled from 1400°C (2550°F) to 1150°C (2100°F).
(a) At what temperature does the first solid phase form?
i
1320
°C
(b) What is the composition of this solid phase?
i
62
%wt Ni
(c) At what temperature does the last of the liquid solidify?
i
1270
°C
(d) What is the composition of this last remaining liquid phase?
i
38
%wt Ni
arrow_forward
Design of a Melting Procedure for a
Casting
You need to produce a M=1000 kg Cu-Ni alloy having minimum
yield strength of Sy = 20,000 psi, a minimum tensile strength
of Sut = 60, 000 psi, and a minimum % elongation of 20%.
%3D
You have in your inventory
a Cu-20% Ni alloy and pure
1500
1400
1300
1200
nickel.
1100
1000
Design a method for
producing castings having
the required properties.
80,000
80
Tensile strength
Cu strengthens Ni
60,000
60
40,000
40
Ni strengthens Cu
% Elongation
20.000
20
Yield strength
20
40
80
Weight percent nickel
60
Ni
Strength (psi)
Temperature ('C)
&Elongation
arrow_forward
Question 4
The following diagram shows the basic structure of the gamma camera used for medical imaging
to data-logger
and computer
Photomultiplier
tube
Sodium iodide
crystal
Lead grating
Describe how the gamma camera detects gamma rays allowing the production of images.
[Suggested word count 130] [2.1]
arrow_forward
GEOLOGY (Phase Diagram). Given a certain substance (in red dot), answer the following questions and show your solution by drawing the necessary lines in the graph.
a. What is the composition of the melt at T=1650C?
b. What is the composition of the melt at T=1300C (if the temperature is at 1300C)?
c. What conditions are needed in order for Anorthite (An), Diopside (Di) and liquid to exist in the system?
arrow_forward
Help with #3 and coding in MATLAB
arrow_forward
SEE MORE QUESTIONS
Recommended textbooks for you
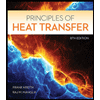
Principles of Heat Transfer (Activate Learning wi...
Mechanical Engineering
ISBN:9781305387102
Author:Kreith, Frank; Manglik, Raj M.
Publisher:Cengage Learning
Related Questions
- please show work and formulas so that i may learn the process correctly. if you use a table please mention which table was used. thank you so much. 2. Fill in the blank cells of this table: T( C) P(kPa) u(kJ/kg) Phase description 175 2524.5 325 4000 325 Saturated liquidarrow_forwardDraw the cooling curve for steam cooling from 115C to -5 Label each phase (solid, liquid, gas), and each phase change (ie: vaporization, condensation, melt, freeze, sublimation, deposition, etc) on your graph. Reminder: Temperature is on your Y-axis and heat is on your X-axis.arrow_forwardA substance exists in two solid modifications alpha and beta and also as liquid and vapour at a pressure of 1 atm alpha melts at a lower temperature to form liquid. Also alpha is denser than the liquid but beta is less dense than the liquid assuming that no meta stable equilibria are observed sketch p-t phase diagram show the significance of each point,line and region also show all triple points.arrow_forward
- D23/ Below are given the solidus and liquidus temperatures for the germanium-silicon system. Construct the phase diagram for this system and label each region.arrow_forwardUsng the phase chan For each thezgments below answer the assigned questions. Luestions will center around change in temperature, kinetic energy, particle speed, bonds breaking or forming. -Alo, make use of the following vocabulary words as they apply for each of the segments below GAS, SOLID, LIQUID, MEILTING, VAPORIZATION, FREEZING, CONDENSATION B-C 1. Wha process is taking place during this segment? 2. L chermal energy being added or removed during this segment? 1. Explain why the temperatture is not chaging during this segment. s the procE6s during this segment andothermic.or expthermic? C-D 5. What is thr sate of matterfor this segment? 6. What is happening to the temperature? 7. Explain why the temperatiure ischanging, 8. L this change an endothermic or exothumie process/ 9. Dexribe the kinetic energy during this sepment 10. Dexribe the particle speed during this gment.arrow_forward4. For the A-B alloy the phase diagram below, use the lever rule to find the amount of liquid and solid states and their compositions at Temperature T. Let Cx = 25%B, C =40%B, Cy = 60 %B Complete solubility of two metals in liquid and solid states (Ni -Cu ,Sb - Bi) TA M EM T EMa T Cy A B Concentration of B in A www.substoch com Temperaturearrow_forward
- b) Figure 1 shows a phase diagram for Cu-Ni binary system. Make a phase analysis of this system at point Q. T.°C 1450 1250 1050 0 20 40 60 80 100arrow_forwardI need solve without AI and chatgptarrow_forwardPlease do not copy/repost previous diagrams from chemistry Q&A. Either place path drawing on or use same EXACT axis labeling as the diagram.arrow_forward
arrow_back_ios
SEE MORE QUESTIONS
arrow_forward_ios
Recommended textbooks for you
- Principles of Heat Transfer (Activate Learning wi...Mechanical EngineeringISBN:9781305387102Author:Kreith, Frank; Manglik, Raj M.Publisher:Cengage Learning
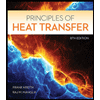
Principles of Heat Transfer (Activate Learning wi...
Mechanical Engineering
ISBN:9781305387102
Author:Kreith, Frank; Manglik, Raj M.
Publisher:Cengage Learning