DiGiannoHeatTreatment
docx
keyboard_arrow_up
School
New Jersey Institute Of Technology *
*We aren’t endorsed by this school
Course
215
Subject
Mechanical Engineering
Date
Jan 9, 2024
Type
docx
Pages
10
Uploaded by CorporalSnow2799
Mechanical Engineering Laboratory
New Jersey Institute of Technology
Report Submitted by
Michael F. DiGianno
Experiment No.
6
Date Performed
10/31-11/07/23
Date Submitted
11/14/23
Course & Section
ME215-101
Instructor
Naruemon Suwattananont
Heat treatment
Experiment Title
Performed by Group
101b
With TA
Md Sojib Kaisar
Group Members
Michael D Bauly S
Yahia Elmanier
Marta D
Stephen M
Jonathan G Braeden G
Table of Contents
Abstract
3
Introduction
3
Objectives
3
Background and importance
3
Procedure
3
Original Data Sheet
4
Results and Calculations
6
Discussion
8
Conclusion
8
Questions and Answers
9
Appendix A
9
2
Abstract
This is the lab report for experiment six, known as the heat treatment lab. This lab is designed to demonstrate to students the process and results of heat treatment. This lab was split into two weeks. The lab mainly consisted of testing the hardness of samples before and after heat
treatment, as well as tempering and annealing. Although our results are dubious, we seem to have validated which heat treatments increase or decrease hardness.
Introduction
Heat treatment is a very common procedure. Its variations and effects are present in many
fields and products. Being familiar with how techniques like tempering and annealing affect the the mechanical properties of the metal is very important as certain processes must be used to achieve desired results
Objectives
Students participating in this lab should be able to understand and predict the mechanical properties of samples that have undergone various different types of heat treatment. Students should be able to operate a rockwell hardness tester and be able to interpret the reading of the tester. Students should also be able to safely operate a furnace.
Background
When heat treating these samples we are primarily moving the sample on the iron carbon phase diagram. “The most important alloying element in steel is carbon. Its presence is largely responsible for the wide range of properties that can be obtained and make this metal such a highly useful commodity in everyday life” (Karl-Erik Thelning, 2000) So it's important to know how to move a material to various spots on the graph.
Procedure
This lab is split into two weeks, although both weeks follow a similar procedure. Students
are to obtain low and high carbon steel samples, then test their hardness. These data values are to
be stored for future reference. The samples will then undergo heat treatment at various temperatures with different quenching techniques. The samples are then retested for their hardness. This should give students an idea of how various techniques affect mechanical properties.
3
Your preview ends here
Eager to read complete document? Join bartleby learn and gain access to the full version
- Access to all documents
- Unlimited textbook solutions
- 24/7 expert homework help
Original Data Sheet
4
5
Results and Calculations
6
Your preview ends here
Eager to read complete document? Join bartleby learn and gain access to the full version
- Access to all documents
- Unlimited textbook solutions
- 24/7 expert homework help
7
8
Discussion
When we zoom out and look at all of our results as a whole, they seem quite accurate, but as we look closer things begin to get fishy. I would not go out right to say that I reject any of the results, but some of the data gathered goes against what we generally know to be true with the sample and heat treatment at large. The most egregious is the low carbon samples becoming softer after heat treatment.
There are a few reasons that this could be occurring. The first is unlikely, but perhaps the samples were improperly heated. We have no specific reason to doubt the furnaces, but it's worth mentioning that. Some of the samples were sanded down, and we are unaware of what improper sanding would do to the results. The air cooled sample was not let cool all of the way. Prof. used water to finish the cooling process, this may have impacted the results slightly.
There are some more reasons that our results may deviate from the expectations.We had various different people taking the measurements. There is a strong possibility that some of them may have used an amount of force that did not correlate with an accurate measurement. There is also a possibility that some of the samples were mixed up. They swapped hands several times and in the lab things can happen. Conclusion
Using our results we can draw some conclusions. Judging by the first round of quenches, it seems that a significant increase in hardness requires a high heat as we only see this result in the samples that have been heated to 960C. Although it may be hard to see there is a trend in the harness with quenching mediums. Air provides the lowest hardness of all the mediums. This trend is formed from the medium's speed at pulling thermal energy out of the sample. We also see an evident trend when observing the hardness values after tempering. The higher temperature that we temper at, the more ductile properties get returned to the material. After reviewing our results, we can conclude that the general trends follow the iron carbon phase diagram, and when prompted group members would be able to suggest processes for attaining certain mechanical properties. Furnaces were operated with no mishaps, but due to the multitude of people operating the Rockwell hardness tester there may have been variation introduced into the data.
9
Your preview ends here
Eager to read complete document? Join bartleby learn and gain access to the full version
- Access to all documents
- Unlimited textbook solutions
- 24/7 expert homework help
Questions and Answers
1.
A very hard and brittle version of iron and carbon, it is archived with a specific austenite quenching.
2.
All low carbon steels around 85000psi, Water quenched around 280000 psi, Oil quench around 270000psi, and air quench also 270000psi
3.
This is because the more carbon in the structures results in a higher hardness.
4.
This is due to the specimens heated at 960C being austenite and the specimens at 500 C being cementite. 5.
Normalizing forms a uniform layer of austenite by heating at 60C then removes it. This improves ductility. Full annealing converts to homogeneous austenite, this provides the weakest mechanical properties. Process annealing induces ferrite to form, this reduces hardness and internal stress. 6.
Yes, this statement is true, the composition and heat treatment are main factors.
7.
This appears to be pearlite, and because of the cooling process required to chaiv perlite,
i don't believe this is possible. 8.
Yes the comparison would be valid as they are measuring the same value, similar if one is to convert F to C. 9.
Pearlite has a DPH of 200 kg/mm^2 (Britannica) 10. Yes, cementite is harder than pearlite. The extra carbon in the cementite structure makes it harder 11. Annealing, quenching, tempering
12. A case hardening processes only hardens the outside of the metal, this is done so the interactable surface retains its nee properties, but the inside can absorb shock
13. Tempering returns ductility and fracture resistance to the sample in question
Appendix A.
Karl-Erik Thelning. (2000). Steel and its heat treatment
(2nd ed.). Butterworths.
10
Related Documents
Related Questions
Need
arrow_forward
https://www.sciencedirect.com/science/article/abs/pii/S0965997822001569
In the literature review, they should present the system installed and the main results obtained. In other words, the enhancement due to the installed system. They have to define the system used in this study. (the report talking about ventilation) pls in briefly
Don’t using chatgpt please urgent
i will give u good feedback
arrow_forward
answer pls
arrow_forward
Needs Complete typed solution with complete explanation and 100 % accuracy. Don't use chat gpt or any ai
arrow_forward
University of Basrah - College of Engineering
Department of Mechanical Engineering
Subject: Power Plant I
Class: Fourth
Examiner: Dr. Ahmad A. M Alsahlani
Notes: Giving Sketches is compulsory wherever needed (Total Ma
Q1] Answer the following que
Exam: Final-Exam
Date: 11/09/2023
Time: 2 Hours
1- Explain how the Geothermal Energy can be utilized to generate electricity.
2- State the two classifications of energy sources and give three examples for each.
3- State three advantages and three disadvantages of using Gas Turbine Power Plant.
4- What are the reasons that lead to a deviation in the ideal gas turbine cycle?
5- Draw a block diagram for a regenerative Rankin Cycle using one open feed water
heater.
Q2]
A closed cycle gas-turbine power plant has a pressure ratio of 10. The air temperature is
35 C at the compressor inlet and 1127 C at the turbine inlet. The received energy at the Qi
combustion chamber is 794 kJ/kg. Assume the isentropic efficiency of the turbine is
95%. Determine…
arrow_forward
Algenib
Sherately
Alpher
Sche
M
فرع واحد
/ تدلا سؤال/
Q1/Write a notes on heat balance sheet, draw that on the energy flow and enhance your answers
with equations.
2:2
Q2/An indicator diagram taken from a single cylinder four stroke, compression ignition engine has
a length of 100/mm and an area of 2045 mm². The indicator pointer deflects a distance of 10 mm for
a pressure increment of 2 bar in the cylinder. If the bore and stroke of the engine cylinder are both
100 mm and the engine speed is 900 rev/min, calculate the mean effective pressure and the indicated
power. If the mechanical efficiency is 0.75, what is the brake power developed. Draw the indicator
diagram.)
ip or bif
03 A diesel engine develops 5kW. Its indicated thermal efficiency is 0.3 and mechanical efficiency
0.75. Estimate the fuel consumption of engine in (a) Kg/hr (b) liters/hr (c) indicated specific fuel
consumption and (d) brake specific fuel consumption. Take heat value of fuel 42000 kJ/Kg and
density of fuel 0.87…
arrow_forward
Based on the table and the correct answers provided in Parts A-D, Are any of the claimed efficiencies impossible?
arrow_forward
Help!!! Please answer all Correctly!!! Please
arrow_forward
I asked bartleby to solve this question earlier, it gave me AI answer which is completely different to what's shown in this answer. I don't know which one is correct now. I have attached screenshots of the AI answer. Can you clarify which is correct. Also I previously asked about pv diagram and you said ' the curve in the explanation is correct', did you mean in your explanation or the one I showed as an example? Please advice
arrow_forward
Alert for not submit AI generated answer. I need unique and correct answer. Don't try to copy from anywhere. Do not give answer in image formet and hand writing
arrow_forward
Subject - Determine the effects of sound and vibration related to building services and human comfort
Question - Assess the potential reduction of sound transmission through insulation and attenuation strategies.
arrow_forward
https://www.sciencedirect.com/science/article/ abs/pii/S036013230700025X
In this literature review, they should present the system installed and the main results obtained. In other words, the enhancement due to the installed system. They have to define the system used in this study. (talking about ventilation system) please i briefly about 6 lines
quicklyy
arrow_forward
What are valid reasons for adding Yttrium to the zirconia in the Thermal Barrier Coating (TBC) in a turbine blade?
Select one or more:
O a. To match the thermal conductivity of the TBC to the metal substrate
b. To avoid breakage during change in thermal conditions
O c. To match the thermal conductivity of the TBC to the underlying oxide layer
Od. To increase the weight of the TBC
O e.
To prevent a change of the crystallographic structure as the temperature changes
arrow_forward
I want a literature review on the topic (Enhancing indoor air quality and safe entertainment in sports halls) consisting of several paragraphs... Introduction 5 to 7 line with reference and conclusion
arrow_forward
Alert for not submit AI generated answer. I need unique and correct answer. Don't try to copy from anywhere. Do not give answer in image formet and hand writing
arrow_forward
Quastions about renewable
arrow_forward
University of Babylon
Collage of Engineering\Al-Musayab
Department of Automobile
Engineering
Under Grad/Third stage
Notes:
1-Attempt Four Questions.
2- Q4 Must be Answered
3-Assume any missing data.
4 تسلم الأسئلة بعد الامتحان مع الدفتر
Subject: Mechanical
Element Design I
Date: 2022\01\25
2022-2023
Time: Three Hours
Course 1
Attempt 1
Q1/ Design a thin cylindrical pressure tank (pressure vessel) with hemispherical ends to the
automotive industry, shown in figure I below. Design for an infinite life by finding the
appropriate thickness of the vessel to carry a sinusoidal pressure varied from {(-0.1) to (6) Mpa}.
The vessel is made from Stainless Steel Alloy-Type 316 sheet annealed. The operating
temperature is 80 C° and the dimeter of the cylinder is 36 cm. use a safety factor of 1.8.
Fig. 1
(15 Marks)
Q2/ Answer the following:
1- Derive the design equation for the direct evaluation of the diameter of a shaft to a desired
fatigue safety factor, if the shaft subjected to both fluctuated…
arrow_forward
Review | Constants
arrow_forward
I need parts 8 and 9 answered please and thank you.
arrow_forward
Vo) 1 0.00
LTE2 KB/s
4G
4G
3:43
64
+ IIl yr RAC - Tes... /
Government College of Engineering, Salem-11
Department of Mechanical Engineering
Sub Code:16PTME303 Sub Name: Refrigeration and Air Conditioning
UNIT TEST –I
Date: 23/092020
Class: B.E PT Mechanical Engineering
Marks:50
Semester: III
Duration:90 min
PART – A
Q. No
Question
M
BT
CO
L
1
Draw T-S and P-h diagram for Vapour compression cycle with vapour wet
after compression.
1
1-F
Define ton of refrigeration.
2
1-F
1
Determine the COP of a refrigerating machine working on a reversed Carnot
cycle operates between 310K and 250K.
3
2
1-
1
A
4
2
1-
2
Classify the refrigerant evaporators
A
2
1-
2
State the merits and demerits of air-refrigeration system.
U
PART- B
M
BT
CO
A vapour compression refrigerator circulates 4.5 kg of NH3 per hour, | 15
condensation take place at 30°C and evaporation at -15°C. There is no
under-cooling of the refrigerant. The temperature after isentropic
compression is 75°C and specific heat of superheated…
arrow_forward
SEE MORE QUESTIONS
Recommended textbooks for you
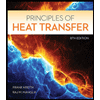
Principles of Heat Transfer (Activate Learning wi...
Mechanical Engineering
ISBN:9781305387102
Author:Kreith, Frank; Manglik, Raj M.
Publisher:Cengage Learning
Related Questions
- Needarrow_forwardhttps://www.sciencedirect.com/science/article/abs/pii/S0965997822001569 In the literature review, they should present the system installed and the main results obtained. In other words, the enhancement due to the installed system. They have to define the system used in this study. (the report talking about ventilation) pls in briefly Don’t using chatgpt please urgent i will give u good feedbackarrow_forwardanswer plsarrow_forward
- Needs Complete typed solution with complete explanation and 100 % accuracy. Don't use chat gpt or any aiarrow_forwardUniversity of Basrah - College of Engineering Department of Mechanical Engineering Subject: Power Plant I Class: Fourth Examiner: Dr. Ahmad A. M Alsahlani Notes: Giving Sketches is compulsory wherever needed (Total Ma Q1] Answer the following que Exam: Final-Exam Date: 11/09/2023 Time: 2 Hours 1- Explain how the Geothermal Energy can be utilized to generate electricity. 2- State the two classifications of energy sources and give three examples for each. 3- State three advantages and three disadvantages of using Gas Turbine Power Plant. 4- What are the reasons that lead to a deviation in the ideal gas turbine cycle? 5- Draw a block diagram for a regenerative Rankin Cycle using one open feed water heater. Q2] A closed cycle gas-turbine power plant has a pressure ratio of 10. The air temperature is 35 C at the compressor inlet and 1127 C at the turbine inlet. The received energy at the Qi combustion chamber is 794 kJ/kg. Assume the isentropic efficiency of the turbine is 95%. Determine…arrow_forwardAlgenib Sherately Alpher Sche M فرع واحد / تدلا سؤال/ Q1/Write a notes on heat balance sheet, draw that on the energy flow and enhance your answers with equations. 2:2 Q2/An indicator diagram taken from a single cylinder four stroke, compression ignition engine has a length of 100/mm and an area of 2045 mm². The indicator pointer deflects a distance of 10 mm for a pressure increment of 2 bar in the cylinder. If the bore and stroke of the engine cylinder are both 100 mm and the engine speed is 900 rev/min, calculate the mean effective pressure and the indicated power. If the mechanical efficiency is 0.75, what is the brake power developed. Draw the indicator diagram.) ip or bif 03 A diesel engine develops 5kW. Its indicated thermal efficiency is 0.3 and mechanical efficiency 0.75. Estimate the fuel consumption of engine in (a) Kg/hr (b) liters/hr (c) indicated specific fuel consumption and (d) brake specific fuel consumption. Take heat value of fuel 42000 kJ/Kg and density of fuel 0.87…arrow_forward
- Based on the table and the correct answers provided in Parts A-D, Are any of the claimed efficiencies impossible?arrow_forwardHelp!!! Please answer all Correctly!!! Pleasearrow_forwardI asked bartleby to solve this question earlier, it gave me AI answer which is completely different to what's shown in this answer. I don't know which one is correct now. I have attached screenshots of the AI answer. Can you clarify which is correct. Also I previously asked about pv diagram and you said ' the curve in the explanation is correct', did you mean in your explanation or the one I showed as an example? Please advicearrow_forward
- Alert for not submit AI generated answer. I need unique and correct answer. Don't try to copy from anywhere. Do not give answer in image formet and hand writingarrow_forwardSubject - Determine the effects of sound and vibration related to building services and human comfort Question - Assess the potential reduction of sound transmission through insulation and attenuation strategies.arrow_forwardhttps://www.sciencedirect.com/science/article/ abs/pii/S036013230700025X In this literature review, they should present the system installed and the main results obtained. In other words, the enhancement due to the installed system. They have to define the system used in this study. (talking about ventilation system) please i briefly about 6 lines quicklyyarrow_forward
arrow_back_ios
SEE MORE QUESTIONS
arrow_forward_ios
Recommended textbooks for you
- Principles of Heat Transfer (Activate Learning wi...Mechanical EngineeringISBN:9781305387102Author:Kreith, Frank; Manglik, Raj M.Publisher:Cengage Learning
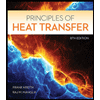
Principles of Heat Transfer (Activate Learning wi...
Mechanical Engineering
ISBN:9781305387102
Author:Kreith, Frank; Manglik, Raj M.
Publisher:Cengage Learning