DiGiannoCNC lab
docx
keyboard_arrow_up
School
New Jersey Institute Of Technology *
*We aren’t endorsed by this school
Course
215
Subject
Mechanical Engineering
Date
Jan 9, 2024
Type
docx
Pages
18
Uploaded by CorporalSnow2799
Mechanical Engineering Laboratory
New Jersey Institute of Technology
Report Submitted by
Michael F. DiGianno
Experiment No.
2
Date Performed
9/26/23-10/3/23
Date Submitted
10/10/23
Course & Section
ME215-101
Instructor
Naruemon Suwattananont
Computer Numerical Controlled Machining
Experiment Title
Performed by Group
101b
With TA
Md Sojib Kaisar
Group Members
Michael D Bauly S
Yahia Elmanier
Marta D
Stephen M
Jonathan G Braeden G
Table of Contents
Abstract
3
Introduction
3
Objectives
3
Background and importance
3
Procedure
4
Original Data Sheet
5
Results and Calculations
6
Discussion
12
Conclusion
12
Questions and Answers
13
Appendix A
14
2
Abstract
This is the lab report for experiment two, known as computer numerical controlled machining. This two week lab revolves around the computer numerical control machine or “CNC”. The purpose of the lab was to introduce the students to the inner workings, set up, and usage of the CNC machine. The students first developed an understanding of g-code. G-code is the programming language that is used for CNC machines. Once prepared, they had the CNC machine demonstrated and wrote out a second g-code program by hand. Students should have completed this lab with a deeper understanding of how a CNC machine is operated and its uses.
Introduction
This laboratory module is broken down into two weeks. In the first week students will familiarize themselves with the syntax and function of g-code. They will then learn the relevant calculations that are brought out of the g-code such as spindle speed, feed rates, and time required. Then in week two, they will receive a demonstration of the mill. This should resolve many questions that they may have about the function and uses of the CNC mill. They will attempt to analyze the g-code they made at home, and finally test their knowledge with a more difficult piece to calculate.
Objectives
Students participating in this lab should be able to develop an understanding of CNC machines. They should be able to write g-code, as well as perform the required calculations that are derived from the g-code. Aside from this, they should be able to identify the functions of a CNC machine as well as how it works. Background and importance
Computer numerically controlled machining, or CNC machining is a fairly modern method of manufacturing that involves using a computer to control the movements of a machine.
This is commonly associated with machines that have three axes of movement like mills, lathes, and 3d printers. That said, two axis movement machines such as laser cutters and water jets can run on the same programs and principles. The actual process varies based on the machine, but usually follows the flow of a source such as calculations or a model, which gets put through some kind of conversion. This can be a slicer software, CAM (computer aided manufacturing) simulator, or g-code compiler. The output (Commonly g-code) is then loaded into the machine which carries out the instructions provided to it.
3
Your preview ends here
Eager to read complete document? Join bartleby learn and gain access to the full version
- Access to all documents
- Unlimited textbook solutions
- 24/7 expert homework help
Procedure
Lab module two is split into two weeks. During the first week the students were introduced to the concepts of CNC milling and g-code. The students learned and began practicing with the syntax of g-code. They practiced with a part (Figure 1); through this part, they provided the g-code, its description, and relevant calculations (Tables 2.7, 2.8, and 2.9). After week one, they were asked to convert their written g-code into a runnable program.
The second week of the lab started with a demonstration of the CNC mill. A small piece was milled (Figure 2). Students observed how the machine was operated, moved, and ultimately used to create the final product. The students then attempted to analyze their g-code prepared the week before. They attempted to have the analysis machine recreate the toolpath of their program (Figure 3). Once this was done, they were to write out the g-code, description, and relevant calculations for a new piece (Figure 4/5). This information is logged in tables (Tables 2.4, 2.5, and 2.6). Once they had this, and their sheets signed, the lab concluded.
4
Original Data Sheet
5
Results and Calculations
Table 2.7 (P-34 toolpath description)
6
Your preview ends here
Eager to read complete document? Join bartleby learn and gain access to the full version
- Access to all documents
- Unlimited textbook solutions
- 24/7 expert homework help
Table 2.8 (P-34 g-code)
7
Table 2.9 (P-34 Calculations)
8
Table 2.4 (Tension specimen toolpath description)
9
Your preview ends here
Eager to read complete document? Join bartleby learn and gain access to the full version
- Access to all documents
- Unlimited textbook solutions
- 24/7 expert homework help
Table 2.5 (Tension specimen g-code)
10
Table 2.6 (Tension specimen calculations)
11
Discussion
To restate, the main objectives of this lab module are to familiarize students with g-code and its syntax. As well as the function and uses of the cnc mill. During week one we were asked to write g-code and calculate values like machining time, spindle speed, and feed rate. The writing of code went well. Some group members struggled at first, which is understandable as they did not have any previous coding experience. That said, it smoothed out quickly as we finished the g-code and descriptions.
The second week was slightly turbulent. It seems there was a series of miscommunications. During week one we were instructed to turn in one g-code, description, and calculation sheet. This left several group members without g-code to digitize. Several other members didn’t own a usb flash drive. In total the group was able to produce two unique flash drives with code. The week started with a demonstration of the CNC milling machine. The operator went slow and showed each function and movement to the class. The finished product is
shown here (Figure 2). Once the demonstration concluded, the operator took questions and moved the students to the next section. The analysis machines were not very user friendly, but it was manageable. We were able to navigate through the buttons and menus, and eventually simulated our code (Figure 3). Neither
of our codes produced a visible toolpath, although it was evident that the machine was attempting. This leads us to believe that there is something wrong with the z or vertical position of our code. The leading theory is that the bit is simply simulating the motions above the workpiece.
The main trouble started when the tension specimen was to be written up. We started working with the instructions given, but later on Prof. disagreed with our current course of action
and requested that we start over with a different approach. Overall, there was much confusion over instructions, but we eventually worked out all relevant papers and concluded the lab. Conclusion
In conclusion, we now have a better understanding of CNC machining and the code that runs it. It's unfortunate that our code did not simulate correctly. That said, with the limited amount of time that we have, it's hard to tell exactly what the problem was. We understand the syntax of g-code and the reasons that one might use a CNC mill during machining or prototyping.
12
Your preview ends here
Eager to read complete document? Join bartleby learn and gain access to the full version
- Access to all documents
- Unlimited textbook solutions
- 24/7 expert homework help
Questions and Answers
1. Position the tool to cut the hole shown in Figure 2.12, use 3 axis x, y, z motion. The starting point is labeled “S” in the Figure. Write the instruction for positioning, in absolute mode, for spot drilling using the spot face cycle. The depth is 0.195 inches and the feed is 10 inches per minute.
n5
g00/g90
x-1
y-1
s1500
t1
m3
n10
z0.5
n15
g00
x2.125
y0.625
n20
g01
z-0.195
f10
n25
g00
z0.5
n30
g00
x-1
y-1
m30
2. What do the following expressions mean? a) N100 G01 G81 Z-1.5 F2100 b)N55 G00 G91 X0
Y0 M3
A.) Line 100, Linear motion, drilling canned cycle tool moves to z -1.5, feed rate =2100in/min
B.) Line 55, Rapid motion, incremental positioning, table homes to (0,0), Spindle rotates 3. Explain the difference between numerical control and computer numerical control.
The difference is that computer numerical control machines are operated with a computer and g-code. NC machines used punch cards that let the machine do simple calculations as the holes
on the punch cards represented numbers that could be used for various calculations.
13
4. Assume a 0.750 in wide and 1.650 in deep slot is to be milled into a 6 in cubic block of plain carbon steel with a Brinell Hardness (BHN) of 125 and carbon content of 0.15%. You may assume a HSS (high speed steel) end mill will be used that has 4 cutting teeth, and has a0.750 in diameter. a) Based on the data provided in Figure 2.10 find the recommended speed and feed for this particular material. b) What is the corresponding rpm of the spindle? c)What is the corresponding feed rate for the table? d) Assuming that the mill to be used only has 5 horsepower available, how many passes are needed?
A.) The table (figure 6) suggests using 80-140 rpm B.) N1=12(80)/pi(0.75)=407.5 Rpm N2=12(140)/pi(0.75)= 713rpm
C.)F1= 4*407.5*0.003=4.89 F2=4*713*0.01= 28.52
5. Why is compressed air required for the CNC mill in the lab?
Air is used to clear chips and shavings away from the workpiece. This is especially important during a tool change when the bit will leave the relevant chucking device making its cleanliness vital
6. What is the first step in preparing the program on a NC machine?
To prepare the program for the NC machine (Punch card), you must have an accurately dimensioned drawing of your desired model. This will let you assign number holes correctly to the card.
Appendix A.
Figure 1: Part P-34
14
Figure 2: Milled example
15
Your preview ends here
Eager to read complete document? Join bartleby learn and gain access to the full version
- Access to all documents
- Unlimited textbook solutions
- 24/7 expert homework help
Figure 3 : Analysis machine
Figure 4: Tension specimen
16
Figure 5: Tension specimen drawing
17
Figure 6: Speeds for Materials
18
Your preview ends here
Eager to read complete document? Join bartleby learn and gain access to the full version
- Access to all documents
- Unlimited textbook solutions
- 24/7 expert homework help
Related Documents
Related Questions
answer a & b. Please show all your work!!
arrow_forward
CORRECT AND DETAILED SOLUTION WITH FBD ONLY. I WILL UPVOTE
3 (15 points): A 12-meter-long precast pile segment is to be lifted from a trailer down to the ground and then set in place prior to driving by a crane.1. If two slings are to be used in lifting the pile to the ground, at what distance from the ends must the slings be placed for minimum bending due to its own weight?2. At what distance from the ends must the slings be placed for minimum shear due to its own weight?3. Using one sling to set the pile in a vertical position before driving at what distance from one end must the sling be placed for minimum bending due to its own weight?ANSWERS: (1) 2.48 m, (2) 3.00 m, (3) 3.51 m
arrow_forward
Solve show all steps and solution. Energy systems engineering
arrow_forward
plz solve it within 30-40 mins I'll give you multiple upvote
arrow_forward
reply fast
arrow_forward
For my assigment, I was asked to design a electric motorbike that has a peformance equal to Honda CBR1000 Fireblade which has a petrol engine. A part of the the assignment is to calculate " An estimate of maximum Power your new motor will need to generate to match the Honda’s performance." I can make the assumption, apart from changing the motor, everything else is going to stay the same so the fairing,the rider and etc they're gonna be the same for the two bikes. So can you please tell me how I can calculate that which information would I need ?
arrow_forward
Please give me the answers for this i been looking at this for a hour and my head hurts
arrow_forward
Assignment Booklet 4B
ce 24: Module 4
6 Identify the safety features shown in this automobile from the following list. Place
your answers in the blank spaces given.
• bumper
• hood
• crumple zones
• roll cage
• side-impact beams
Return to page 75 of the Student Module Booklet and begin Lesson 2.
For questions 7 to 10, read each question carefully. Decide which of the choices BEST
completes the statement or answers the question. Place your answer in the blank
space given.
7. According to Transport Canada, how many Canadians owe their lives to
seat belts between 1990 and 2000?
A. 690
В. 1690
С. 1960
D. 11 690
8. By what percent is the webbing of a seat belt designed to stretch to help
absorb energy in a collision?
A. 0%
B. 5-10%
C. 10-15%
D. 15-20%
9. What is the level of seat belt use in Alberta?
A. 90%
В. 70%
С. 50%
D. 30%
Teacher
arrow_forward
A Team of Engineers asked for an internal combustion engine to use it in a designed car. Your role is to describe the operation sequence of different types of available engines, explain their mechanical efficiency, and deliver a detailed technical report to show your approach in solving and discussing the following tasks and issues.
You must follow the following steps to help the team:
STEP 1
Describe the operational sequence of four-stroke spark ignition and four-stroke compression ignition engines with the aid of sketches by constructing simple sketch representing the operation and plotting the P-V diagrams for each process during the cycle to show the following:
The input and output heat and net output work
The expansion and compression strokes
The air-fuel mixture intake and exhaust gasses
The spark plug when it is in the active mode
The complete cycle of ideal Otto and Diesel cycles that shows the input and output heat and net output work.
STEP 2
Explain the mechanical…
arrow_forward
O Week 2- 20527 22110L
x a MasteringEngineering Mastering x
M Inbox (10,309) - usmikail@gmail x
a Product Detail Page
a Central Service Technical Manual x
O 21) YouTube
i session.masteringengineering.com/myct/itemView?assignmentProblemiD=12443395&offset=next
KHW 1
Problem 12.3
6 of 16
I Review
A particle travels along a straight line with a velocity
v = (12 – 3t2) m/s, where t is in seconds. When
t = 1 s, the particle is located 10 m to the left of the
origin.
Express your answer to three significant figures and include the appropriate units.
As =
437
Submit
Previous Answers Request Answer
X Incorrect; Try Again; 4 attempts remaining
Part C
Determine the distance the particle travels during the time period given in previous part.
Express your answer to three significant figures and include the appropriate units.
?
ST =
Value
Units
arrow_forward
University of Babylon
Collage of Engineering/
Al-Musayab
Department of Automobiles
Final Examination/ Stage: 3rd
Notes:
Answer 4 questions only
2023-2202
Subject: Theory of vehicles
Date: 2023\06\10-Saturday
Time: Three Hours
Course 2nd Attempt 1st
Q1: A Hooke's coupling connects two shafts whose axes are inclined at 30°. The
of the driven shaft? Find the maximum value of retardation or acceleration and
driving shaft rotates uniformly at 600 rpm. What are the extreme angular velocities
state the angle where both will occur.
(12.5 Marks)
Q2: Four masses, A, B, C, and D), revolve at equal radii and are equally spaced
along a shaft. The mass B is 7 kg, and the radius of C and D make angles of 90°
and 240°, respectively, with the radius of B. Find the magnitude of the masses A,
C, and D and the angular position of A so that the system may be completely
balanced.
(12.5 Marks)
Q3: A cam has straight worked faces that are tangential to a base circle of diameter
90 mm. The follower is a roller…
arrow_forward
PLEASE ANSWER NUMBER 9.MECH 221-KINEMATICS: PLEASE GIVE DETAILED ANSWER AND CORRECT ANSWERS. I WILL REPORT TO BARTLEBY THOSE TUTORS WHO WILL GIVE INCORRECT ANSWERS.
arrow_forward
University of Babylon
Collage of Engineering\Al-Musayab
Department of Automobile
Engineering
Under Grad/Third stage
Notes:
1-Attempt Four Questions.
2- Q4 Must be Answered
3-Assume any missing data.
4 تسلم الأسئلة بعد الامتحان مع الدفتر
Subject: Mechanical
Element Design I
Date: 2022\01\25
2022-2023
Time: Three Hours
Course 1
Attempt 1
Q1/ Design a thin cylindrical pressure tank (pressure vessel) with hemispherical ends to the
automotive industry, shown in figure I below. Design for an infinite life by finding the
appropriate thickness of the vessel to carry a sinusoidal pressure varied from {(-0.1) to (6) Mpa}.
The vessel is made from Stainless Steel Alloy-Type 316 sheet annealed. The operating
temperature is 80 C° and the dimeter of the cylinder is 36 cm. use a safety factor of 1.8.
Fig. 1
(15 Marks)
Q2/ Answer the following:
1- Derive the design equation for the direct evaluation of the diameter of a shaft to a desired
fatigue safety factor, if the shaft subjected to both fluctuated…
arrow_forward
Home
Insert
Draw
Design
Layout
References
Maili
OLYTECH
Calibri (Bo...
11
v A A
Aa v
m Air. Ma
Paste
в I
U v ab x,
x | A
Name:
ID No.:
rm Air. M
Date:
CRN:
Course Code: JACV 506E
Aircraft Mechanical Mainte
Practice.
ces ( CRI
Page
Originated By
Mark awarded -
Instructor/Assessor:
Assignment: Interpret engineering drawings and diagrams
bus
se Mat
hing Pl
Questions: -
1. Write 2 differences between isometric and oblique projections?
ssment
2. Write 5 details found on the drawing title block?
Feedba
3. Write 4 types of sectional views?
4. Name 3 methods how drawings are stored in?
5. Name 3 types of fits?
arrow_forward
Help!!! Please answer all Correctly!!! Please
arrow_forward
Please do not copy other's work and do not use ChatGPT or Gpt4,i will be very very very appreciate!!!
Thanks a lot!!!!!
arrow_forward
Draw the top, the front, and the right-side orthographic views of the objects shown. Indicate when an object needs only one or two views to be fully described.
arrow_forward
a. Currently, you serve as a robotic engineer by a company, and your boss want you
to design a robot in spatial space to satisfy the following conditions:
i. Max reachable distance of the robot is 1 meter.
ii.
Only using revolute joints, connecting links and rigid load bearing links
(the length of link is 0.5m).
iii. The degree of freedom (Dof) of the robot is 2.
What is your design, how many joints and links will you use?
b. The payload of your design is 10 kg (each load bearing link can hold 5 kg, 5 kg+5
kg=10kg, the weight and payload of the connecting links will be ignored), but
your boss wants your designed robots to handle 20 kg payload. How will you
update your current design, and how many joints and links will you use in the
new design? What is the Dof of the new designed robot.
arrow_forward
solve the questionI got my answer but im not sure if it is correct(628.75 or 718.7 ?)
arrow_forward
I asked for problems 6 and 7 to be answered, but I did not get a properly structured answered as the example shows on problem number 1. Here is the link to the questions I already had answered, could you please rewrite the answer so its properly answered as the example shows (Problem 1)?
https://www.bartleby.com/questions-and-answers/it-vivch-print-reading-for-industry-228-class-date-name-review-activity-112-for-each-local-note-or-c/cadc3f7b-2c2f-4471-842b-5a84bf505857
arrow_forward
SEE MORE QUESTIONS
Recommended textbooks for you
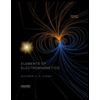
Elements Of Electromagnetics
Mechanical Engineering
ISBN:9780190698614
Author:Sadiku, Matthew N. O.
Publisher:Oxford University Press
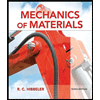
Mechanics of Materials (10th Edition)
Mechanical Engineering
ISBN:9780134319650
Author:Russell C. Hibbeler
Publisher:PEARSON
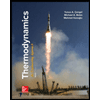
Thermodynamics: An Engineering Approach
Mechanical Engineering
ISBN:9781259822674
Author:Yunus A. Cengel Dr., Michael A. Boles
Publisher:McGraw-Hill Education
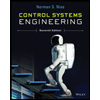
Control Systems Engineering
Mechanical Engineering
ISBN:9781118170519
Author:Norman S. Nise
Publisher:WILEY
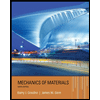
Mechanics of Materials (MindTap Course List)
Mechanical Engineering
ISBN:9781337093347
Author:Barry J. Goodno, James M. Gere
Publisher:Cengage Learning
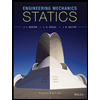
Engineering Mechanics: Statics
Mechanical Engineering
ISBN:9781118807330
Author:James L. Meriam, L. G. Kraige, J. N. Bolton
Publisher:WILEY
Related Questions
- answer a & b. Please show all your work!!arrow_forwardCORRECT AND DETAILED SOLUTION WITH FBD ONLY. I WILL UPVOTE 3 (15 points): A 12-meter-long precast pile segment is to be lifted from a trailer down to the ground and then set in place prior to driving by a crane.1. If two slings are to be used in lifting the pile to the ground, at what distance from the ends must the slings be placed for minimum bending due to its own weight?2. At what distance from the ends must the slings be placed for minimum shear due to its own weight?3. Using one sling to set the pile in a vertical position before driving at what distance from one end must the sling be placed for minimum bending due to its own weight?ANSWERS: (1) 2.48 m, (2) 3.00 m, (3) 3.51 marrow_forwardSolve show all steps and solution. Energy systems engineeringarrow_forward
- plz solve it within 30-40 mins I'll give you multiple upvotearrow_forwardreply fastarrow_forwardFor my assigment, I was asked to design a electric motorbike that has a peformance equal to Honda CBR1000 Fireblade which has a petrol engine. A part of the the assignment is to calculate " An estimate of maximum Power your new motor will need to generate to match the Honda’s performance." I can make the assumption, apart from changing the motor, everything else is going to stay the same so the fairing,the rider and etc they're gonna be the same for the two bikes. So can you please tell me how I can calculate that which information would I need ?arrow_forward
- Please give me the answers for this i been looking at this for a hour and my head hurtsarrow_forwardAssignment Booklet 4B ce 24: Module 4 6 Identify the safety features shown in this automobile from the following list. Place your answers in the blank spaces given. • bumper • hood • crumple zones • roll cage • side-impact beams Return to page 75 of the Student Module Booklet and begin Lesson 2. For questions 7 to 10, read each question carefully. Decide which of the choices BEST completes the statement or answers the question. Place your answer in the blank space given. 7. According to Transport Canada, how many Canadians owe their lives to seat belts between 1990 and 2000? A. 690 В. 1690 С. 1960 D. 11 690 8. By what percent is the webbing of a seat belt designed to stretch to help absorb energy in a collision? A. 0% B. 5-10% C. 10-15% D. 15-20% 9. What is the level of seat belt use in Alberta? A. 90% В. 70% С. 50% D. 30% Teacherarrow_forwardA Team of Engineers asked for an internal combustion engine to use it in a designed car. Your role is to describe the operation sequence of different types of available engines, explain their mechanical efficiency, and deliver a detailed technical report to show your approach in solving and discussing the following tasks and issues. You must follow the following steps to help the team: STEP 1 Describe the operational sequence of four-stroke spark ignition and four-stroke compression ignition engines with the aid of sketches by constructing simple sketch representing the operation and plotting the P-V diagrams for each process during the cycle to show the following: The input and output heat and net output work The expansion and compression strokes The air-fuel mixture intake and exhaust gasses The spark plug when it is in the active mode The complete cycle of ideal Otto and Diesel cycles that shows the input and output heat and net output work. STEP 2 Explain the mechanical…arrow_forward
- O Week 2- 20527 22110L x a MasteringEngineering Mastering x M Inbox (10,309) - usmikail@gmail x a Product Detail Page a Central Service Technical Manual x O 21) YouTube i session.masteringengineering.com/myct/itemView?assignmentProblemiD=12443395&offset=next KHW 1 Problem 12.3 6 of 16 I Review A particle travels along a straight line with a velocity v = (12 – 3t2) m/s, where t is in seconds. When t = 1 s, the particle is located 10 m to the left of the origin. Express your answer to three significant figures and include the appropriate units. As = 437 Submit Previous Answers Request Answer X Incorrect; Try Again; 4 attempts remaining Part C Determine the distance the particle travels during the time period given in previous part. Express your answer to three significant figures and include the appropriate units. ? ST = Value Unitsarrow_forwardUniversity of Babylon Collage of Engineering/ Al-Musayab Department of Automobiles Final Examination/ Stage: 3rd Notes: Answer 4 questions only 2023-2202 Subject: Theory of vehicles Date: 2023\06\10-Saturday Time: Three Hours Course 2nd Attempt 1st Q1: A Hooke's coupling connects two shafts whose axes are inclined at 30°. The of the driven shaft? Find the maximum value of retardation or acceleration and driving shaft rotates uniformly at 600 rpm. What are the extreme angular velocities state the angle where both will occur. (12.5 Marks) Q2: Four masses, A, B, C, and D), revolve at equal radii and are equally spaced along a shaft. The mass B is 7 kg, and the radius of C and D make angles of 90° and 240°, respectively, with the radius of B. Find the magnitude of the masses A, C, and D and the angular position of A so that the system may be completely balanced. (12.5 Marks) Q3: A cam has straight worked faces that are tangential to a base circle of diameter 90 mm. The follower is a roller…arrow_forwardPLEASE ANSWER NUMBER 9.MECH 221-KINEMATICS: PLEASE GIVE DETAILED ANSWER AND CORRECT ANSWERS. I WILL REPORT TO BARTLEBY THOSE TUTORS WHO WILL GIVE INCORRECT ANSWERS.arrow_forward
arrow_back_ios
SEE MORE QUESTIONS
arrow_forward_ios
Recommended textbooks for you
- Elements Of ElectromagneticsMechanical EngineeringISBN:9780190698614Author:Sadiku, Matthew N. O.Publisher:Oxford University PressMechanics of Materials (10th Edition)Mechanical EngineeringISBN:9780134319650Author:Russell C. HibbelerPublisher:PEARSONThermodynamics: An Engineering ApproachMechanical EngineeringISBN:9781259822674Author:Yunus A. Cengel Dr., Michael A. BolesPublisher:McGraw-Hill Education
- Control Systems EngineeringMechanical EngineeringISBN:9781118170519Author:Norman S. NisePublisher:WILEYMechanics of Materials (MindTap Course List)Mechanical EngineeringISBN:9781337093347Author:Barry J. Goodno, James M. GerePublisher:Cengage LearningEngineering Mechanics: StaticsMechanical EngineeringISBN:9781118807330Author:James L. Meriam, L. G. Kraige, J. N. BoltonPublisher:WILEY
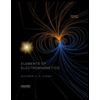
Elements Of Electromagnetics
Mechanical Engineering
ISBN:9780190698614
Author:Sadiku, Matthew N. O.
Publisher:Oxford University Press
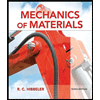
Mechanics of Materials (10th Edition)
Mechanical Engineering
ISBN:9780134319650
Author:Russell C. Hibbeler
Publisher:PEARSON
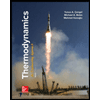
Thermodynamics: An Engineering Approach
Mechanical Engineering
ISBN:9781259822674
Author:Yunus A. Cengel Dr., Michael A. Boles
Publisher:McGraw-Hill Education
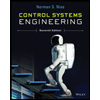
Control Systems Engineering
Mechanical Engineering
ISBN:9781118170519
Author:Norman S. Nise
Publisher:WILEY
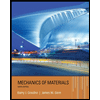
Mechanics of Materials (MindTap Course List)
Mechanical Engineering
ISBN:9781337093347
Author:Barry J. Goodno, James M. Gere
Publisher:Cengage Learning
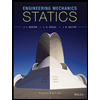
Engineering Mechanics: Statics
Mechanical Engineering
ISBN:9781118807330
Author:James L. Meriam, L. G. Kraige, J. N. Bolton
Publisher:WILEY