DiGiannoSurface
docx
keyboard_arrow_up
School
New Jersey Institute Of Technology *
*We aren’t endorsed by this school
Course
215
Subject
Mechanical Engineering
Date
Jan 9, 2024
Type
docx
Pages
13
Uploaded by CorporalSnow2799
Mechanical Engineering Laboratory
New Jersey Institute of Technology
Report Submitted by
Michael F. DiGianno
Experiment No.
5
Date Performed
10/10/23
Date Submitted
10/17/23
Course & Section
ME215-101
Instructor
Naruemon Suwattananont
Surface Texture
Experiment Title
Performed by Group
101b
With TA
Md Sojib Kaisar
Group Members
Michael D Bauly S
Yahia Elmanier
Marta D
Stephen M
Jonathan G Braeden G
Table of Contents
Abstract
3
Introduction
3
Objectives
3
Background and importance
3
Procedure
4
Original Data Sheet
5
Results and Calculations
6
Discussion
12
Conclusion
12
Questions and Answers
13
Appendix A
14
2
Abstract
This is the lab report for experiment five, known as the surface texture lab. This lab is designed to introduce students to surface topography which is a term that refers to the profile and
overall roughness of a surface. Students will also become familiar with some machines used to measure surfaces such as a surfometer and perthometer. They will measure samples provided and
record the roughness of the surfaces. This helps build an understanding of both surface topography and which are more accurate and reliable for measurement. Introduction
Surface measurement is an important area to understand when we discuss various machining and measurement techniques. It will allow us to analyze how different machines, machining methods, and tool selections impact the final product. This lab will allow students to interpret which methods help them accomplish this best.
Objectives
Students participating in this lab should be able to develop an understanding of surface finishes. They will be introduced to several machines that will help them understand and measure the roughness of the surface. These machines will help students understand what types of operations such as milling and lathe turning create what finishes.
Background
Surface topography is a very wide field. Its importance spreads beyond our area of discussion. “Surfaces represent an important tool for the description and analysis of a multitude of phenomena related to the social, economic, natural and technical sciences.” (Wolf 2020).
Procedure
In this lab students were asked to take the surface roughness measurements of various samples with different machines and techniques. The samples consisted of samples produced in the previous labs, as well as non metallic samples provided. The machines were demonstrated to the group. The machines consisted of a perthometer, surfometer, and a microfinish comparator. The students then replicated the measurements made by the ta. One of the samples was to
be placed in the vibratory finisher, and ran for forty-five minutes. In the meantime, students drew
pictures of the samples, and converted units. Once finished, they took measurements of the refinished sample.
3
Your preview ends here
Eager to read complete document? Join bartleby learn and gain access to the full version
- Access to all documents
- Unlimited textbook solutions
- 24/7 expert homework help
Original Data Sheet
4
5
Results and Calculations
Perthometer: Lathe sample cut #1
Perthometer: Lathe sample cut #2
6
Your preview ends here
Eager to read complete document? Join bartleby learn and gain access to the full version
- Access to all documents
- Unlimited textbook solutions
- 24/7 expert homework help
Perthometer: Lathe sample cut #3 Perthometer: Lathe sample cut #4 7
Perthometer: Clear block (rougher side)
Perthometer: Pre-vibratory finishing 50ipm
8
Perthometer: Pre-vibratory finishing 25ipm
Perthometer: Pre-vibratory finishing 10ipm
9
Your preview ends here
Eager to read complete document? Join bartleby learn and gain access to the full version
- Access to all documents
- Unlimited textbook solutions
- 24/7 expert homework help
Perthometer: Vibratory finished piece 50ipm
Perthometer: Vibratory finished piece 25ipm
10
Perthometer: Vibratory finished piece 10ipm
Discussion
To restate, the main objectives of this lab module are to familiarize students with surface measurement and its uses. This includes the machines involved with taking the relevant measurements and how they are interpreted. Students also learn about the vibration finishing machine albeit briefly.
From the initial reading, we can draw the conclusion that the faster a machine is running in either RPM or feedrate, the higher the roughness. Although the data is arranged slightly counterintuitively on the data sheet, if you rearrange the numbers to be in order of feed rate or rpms, the trend makes itself clear. The data is currently arranged in order that the cuts appear on the samples, which was easier to keep track of during data collection. The problem starts when we discuss the vibration finishing of the cnc sample. After the vibratory finish, the sample appeared to become rougher which goes against the purpose of the machine used.
For the initial readings, these were largely expected. When running machines at higher speed, you run into a few issues. The first is that there is a large amount of vibration being added into the system. This can be compounded with other factors such as heat warping as well as a large volume of shavings that need to be moved away from the workpiece. The vibratory machine on the other hand produced some unexpected effects. We were expecting the roughness to be brought down, but it instead went up. We believe this is an outlier and not the normal for this type of procedure.
11
All of the readings derived from the microcomparitor are very flawed. I’ll be the first to admit that it’s very hard to use. We did our best, but the readings were definitely off due to human error. Professor gave some specific instructions when it came to cleaning the cnc sample after its vibratory finishing. When it was finished, it was taken out of the room and we were not privy to the cleaning process. I believe this is what caused the strange spike in roughness. Many machines use a liquid with small particles of solid dispersed in them to remove material. This is how for instance water jets cut. If the vibratory finisher uses this same technique to smooth out parts of the piece, an improper cleaning would indeed create a rougher surface with leftover particulate on the piece.
Conclusion
In conclusion, we now have a better understanding of the roughness readings that come from a surfometer and a perthometer, and why they are superior to a hand microcomparitor. The results paint us a clear picture of how running machines at higher speeds create rougher surfaces.
The vibration data doesn't seem reliable and it wouldn’t be a good idea to draw conclusions from
it. Through analysis of our data, and error evaluation we can take away important lessons about surface measurement.
Questions and Answers
1. Turning and grinding operations change the microstructure of the metals, by creating heat within the surface of the workpiece. This makes smoother finished have a higher fatigue strength.
2. A) depending on the operation roughes varies from 6-125μin B) Depending on the purpose of
the seal it can range from 0.2-3.2 μm
3. Yes, this is possible through the use of an electron microscope.
4. It means to lay angular in both directions.
5. Yes, the desired finish is possible with both operations.
6. If two light beams are used for measurement, a reading can be made with their displacement.
7. As previously stated electron microscopes as well as the machines used in this lab. Surface micro comparator, surfometer, and perthometer accomplish the job.
8. Vibrational finishing should decrease surface roughness, using particles to smooth small ridges, our data unfortunately does not support this.
12
Your preview ends here
Eager to read complete document? Join bartleby learn and gain access to the full version
- Access to all documents
- Unlimited textbook solutions
- 24/7 expert homework help
9. It seems that the higher the feed rate and/or RPM, the rougher the surface.
10. A) No, its not consistent B) One could snap, saw, or heat roll to name a few C) 0.25μm D) Sources may include heat warping and vibration
11. Boring, chemical milling, drilling, electron beam, forging, laser, milling, sawing, shaping, turning.
Appendix A.
Wolf, G. W. (2020). Surfaces—topography and topology. Surface Topography: Metrology and Properties
, 8
(1), 014003. https://doi.org/10.1088/2051-672x/ab70e8
13
Related Documents
Related Questions
K
mylabmastering.pearson.com
Chapter 12 - Lecture Notes.pptx: (MAE 272-01) (SP25) DY...
P Pearson MyLab and Mastering
Mastering Engineering
Back to my courses
Course Home
Scores
Course Home
arrow_forward
For my assigment, I was asked to design a electric motorbike that has a peformance equal to Honda CBR1000 Fireblade which has a petrol engine. A part of the the assignment is to calculate " An estimate of maximum Power your new motor will need to generate to match the Honda’s performance." I can make the assumption, apart from changing the motor, everything else is going to stay the same so the fairing,the rider and etc they're gonna be the same for the two bikes. So can you please tell me how I can calculate that which information would I need ?
arrow_forward
Chapter 12 - Lecture Notes.pptx: (MAE 272-01) (SP25) DY...
Scores
arrow_forward
3. Microfluidic channels will need to be fabricated on a key micro-scale sensor used by aerospace
industries. Before running machining tests and analyzing machined quality, preliminary efforts are needed
to evaluate selected materials and factors affecting machining process¹. Three material candidates have
been selected, including 422SS (stainless steel), IN718 (nickel alloy), and Ti64 (titanium alloy) with their
measured tensile properties and equation of true stress-true strain relationship used listed below. Tref25°C.
Specifically, three factors will need to be evaluated, including different materials, temperature, and size
effect. Please calculate true stress values for true strain ranging between 0-3 for each case listed below.
Material
A (MPa)
& (S-¹)
Tm (°C)
870
0.01
1520
422SS (Peyre et al., 2007)
IN718 (Kobayashi et al., 2008)
Ti64 (Umbrello, 2008)
980
1
1300
782.7
1E-5
1660
Material
422SS (CINDAS, 2011)
IN718 (Davis, 1997)
Ti64 (Fukuhara and Sanpei, 1993)
0 =
X
G (GPa)
1+
B…
arrow_forward
Show work
Part 1 website: https://ophysics.com/r5.html
PArt 2 website: https://ophysics.com/r3.html
arrow_forward
answer pls
arrow_forward
3. Please help me solve all parts to this mech. engineering question
arrow_forward
Instrumentation & Measurements
This homework measures your capability to design/analyze various components/variables of ameasurement system based on what you have studied.
Question is Attached in image. Thank you.
arrow_forward
I need help solving this problem.
arrow_forward
Please answer allquestions
arrow_forward
O Week 2- 20527 22110L
x a MasteringEngineering Mastering x
M Inbox (10,309) - usmikail@gmail x
a Product Detail Page
a Central Service Technical Manual x
O 21) YouTube
i session.masteringengineering.com/myct/itemView?assignmentProblemiD=12443395&offset=next
KHW 1
Problem 12.3
6 of 16
I Review
A particle travels along a straight line with a velocity
v = (12 – 3t2) m/s, where t is in seconds. When
t = 1 s, the particle is located 10 m to the left of the
origin.
Express your answer to three significant figures and include the appropriate units.
As =
437
Submit
Previous Answers Request Answer
X Incorrect; Try Again; 4 attempts remaining
Part C
Determine the distance the particle travels during the time period given in previous part.
Express your answer to three significant figures and include the appropriate units.
?
ST =
Value
Units
arrow_forward
this is a practice problem, not a graded assignment
arrow_forward
est 2 (copy) (page 4 of 9)
A wiseup.wsu.acza/mod/quiz/attempt.php7attempt=610918cmid 148960&page=3
ops
O YouTube
M Gmail
Maps
O GENERAL MATHEM.
O New Tab
:WSU WiSeUp
1 MONLO GOA
ashboard / My courses / FLM15B2_KF_WS6222 2021 / Tests / Test 2 (copy)
uestion 4
Quz navigation
Gate AB in Figure below is 1.0 m long and 0.9 wide. Calculate force F on the gate and position X of its centre of
Not yet
answered
pressure.
Marked out of
Finish attempt
10,000
Rag question
3m
Oil,
s.g.=Q81
7m
1.0m
B
50
Answer
arrow_forward
I need solutions to this question
arrow_forward
00
T
R
%24
Bb R
V qa
du/webapps/assessment/take/launch.jsp?course_assessment_id%=_254968_1&course_id%3D 3565256_1&content id= 52826
* Question Completion Status:
Attach File
Browse Local Files
Browse Content Collection
QUESTION 2
A company needs to choose one supplier for a particular type of silicon wafer used'in the production of
semiconductors. The company has three options. Supplier A sells the silicon wafers for $2.50 per wafer,
independently of the number of wafers ordered. Supplier B sells the wafers for $2.40 each but does not
consider an order for less than 2,000 wafers. Supplier C sells the wafers for $2.30 each but does not accept
an order for less than 3,000 wafers. Assume an order setup cost of $100 and an annual requirement of 20,000
wafers. Assume a 20% annual interest rate for holding cost calculations.
a. Which supplier should be chosen to minimize the total annual cost for the wafers, and what is the
optimal order quantity?
b. If the replenishment lead time for wafers…
arrow_forward
vio-Ou X
28523020?X-Blackboard-Expi
2/3
Ö
150% + A
=651gq|4cRVazVmd0Uq2ZHfoUuaYHSBHXymA39vD1F0g%3D&X-Blackboard-
2) The ballistic pendulum is a simple device to measure projectile speed v by
observing the maximum angle to which the box of sand with the
embedded projectile swings. Calculate the pre-impact speed of the 40-
gram projectile if the 16-kg box of sand swings up to a maximum angle of
0=23° after impact.
2 m
120
arrow_forward
+
P
4.
5.
1/4
R
%24
2.
Bb Basic BIM/REVIT Drafting (CAD) X
Bb Unit 03 - Reading Measuring loo X
uaptc.edu/bbcswebdav/pid-4073050-dt-content-rid-22008907_1/courses/DFT.1005.A10.2021.S0/pdf_activities_03-03.pdf
pdf
1 / 2 -
Activity 3-3
A | + %00L
E区
Reading a Scale
Name
Tanner Francis
Identify the portion of a foot (12") as indicated by the reading from the zero mark (0) on the scales below. Place your answers
in the spaces provided.
1.
78
88
92
4.
2.
6.
3.
9 6
1
3.
8.
O.
14
13
ju 3
here to search
直 0
85°F
F2
F4
F5
F7
%23
F8
prt sc
2
home
F10
pua
F12
F11
insert
3.
4.
0.
6.
6.
K
H.
arrow_forward
Could you please explain where and what is tight side and also how to find 5-9
arrow_forward
K
mylabmastering.pearson.com
Chapter 12 - Lecture Notes.pptx: (MAE 272-01) (SP25) DY...
P Pearson MyLab and Mastering
Mastering Engineering
Back to my courses
Course Home
Scores
Course Home
arrow_forward
Access Pearson
P Pearson MyLab and Mastering
Study Area
Document Sharing
User Settings
The man having a weight of 180 lb is able to run up a
18-ft-high flight of stairs shiwn in (Figure 1) in 4 s.
Figure
1 of 1
R
mylabmastering.pearson.com
Part A
P Course Home
b My Questions | bartleby
Determine the power generated.
Express your answer in horsepower to three significant figures.
ΜΕ ΑΣΦ. Η
vec
P =
Submit
Request Answer
Part B
?
hp
How long would a 100-W light bulb have to burn to expend the same amount of energy?
Express your answer to three significant figures and include the appropriate units.
HÅ
?
t =
Value
Units
Submit
Request Answer
Provide Feedback
Review
Next >
arrow_forward
Which of these statements are correct?
arrow_forward
SEE MORE QUESTIONS
Recommended textbooks for you
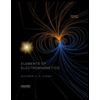
Elements Of Electromagnetics
Mechanical Engineering
ISBN:9780190698614
Author:Sadiku, Matthew N. O.
Publisher:Oxford University Press
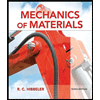
Mechanics of Materials (10th Edition)
Mechanical Engineering
ISBN:9780134319650
Author:Russell C. Hibbeler
Publisher:PEARSON
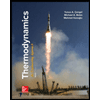
Thermodynamics: An Engineering Approach
Mechanical Engineering
ISBN:9781259822674
Author:Yunus A. Cengel Dr., Michael A. Boles
Publisher:McGraw-Hill Education
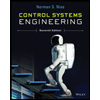
Control Systems Engineering
Mechanical Engineering
ISBN:9781118170519
Author:Norman S. Nise
Publisher:WILEY
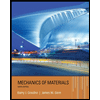
Mechanics of Materials (MindTap Course List)
Mechanical Engineering
ISBN:9781337093347
Author:Barry J. Goodno, James M. Gere
Publisher:Cengage Learning
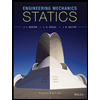
Engineering Mechanics: Statics
Mechanical Engineering
ISBN:9781118807330
Author:James L. Meriam, L. G. Kraige, J. N. Bolton
Publisher:WILEY
Related Questions
- K mylabmastering.pearson.com Chapter 12 - Lecture Notes.pptx: (MAE 272-01) (SP25) DY... P Pearson MyLab and Mastering Mastering Engineering Back to my courses Course Home Scores Course Homearrow_forwardFor my assigment, I was asked to design a electric motorbike that has a peformance equal to Honda CBR1000 Fireblade which has a petrol engine. A part of the the assignment is to calculate " An estimate of maximum Power your new motor will need to generate to match the Honda’s performance." I can make the assumption, apart from changing the motor, everything else is going to stay the same so the fairing,the rider and etc they're gonna be the same for the two bikes. So can you please tell me how I can calculate that which information would I need ?arrow_forwardChapter 12 - Lecture Notes.pptx: (MAE 272-01) (SP25) DY... Scoresarrow_forward
- 3. Microfluidic channels will need to be fabricated on a key micro-scale sensor used by aerospace industries. Before running machining tests and analyzing machined quality, preliminary efforts are needed to evaluate selected materials and factors affecting machining process¹. Three material candidates have been selected, including 422SS (stainless steel), IN718 (nickel alloy), and Ti64 (titanium alloy) with their measured tensile properties and equation of true stress-true strain relationship used listed below. Tref25°C. Specifically, three factors will need to be evaluated, including different materials, temperature, and size effect. Please calculate true stress values for true strain ranging between 0-3 for each case listed below. Material A (MPa) & (S-¹) Tm (°C) 870 0.01 1520 422SS (Peyre et al., 2007) IN718 (Kobayashi et al., 2008) Ti64 (Umbrello, 2008) 980 1 1300 782.7 1E-5 1660 Material 422SS (CINDAS, 2011) IN718 (Davis, 1997) Ti64 (Fukuhara and Sanpei, 1993) 0 = X G (GPa) 1+ B…arrow_forwardShow work Part 1 website: https://ophysics.com/r5.html PArt 2 website: https://ophysics.com/r3.htmlarrow_forwardanswer plsarrow_forward
- 3. Please help me solve all parts to this mech. engineering questionarrow_forwardInstrumentation & Measurements This homework measures your capability to design/analyze various components/variables of ameasurement system based on what you have studied. Question is Attached in image. Thank you.arrow_forwardI need help solving this problem.arrow_forward
- Please answer allquestionsarrow_forwardO Week 2- 20527 22110L x a MasteringEngineering Mastering x M Inbox (10,309) - usmikail@gmail x a Product Detail Page a Central Service Technical Manual x O 21) YouTube i session.masteringengineering.com/myct/itemView?assignmentProblemiD=12443395&offset=next KHW 1 Problem 12.3 6 of 16 I Review A particle travels along a straight line with a velocity v = (12 – 3t2) m/s, where t is in seconds. When t = 1 s, the particle is located 10 m to the left of the origin. Express your answer to three significant figures and include the appropriate units. As = 437 Submit Previous Answers Request Answer X Incorrect; Try Again; 4 attempts remaining Part C Determine the distance the particle travels during the time period given in previous part. Express your answer to three significant figures and include the appropriate units. ? ST = Value Unitsarrow_forwardthis is a practice problem, not a graded assignmentarrow_forward
arrow_back_ios
SEE MORE QUESTIONS
arrow_forward_ios
Recommended textbooks for you
- Elements Of ElectromagneticsMechanical EngineeringISBN:9780190698614Author:Sadiku, Matthew N. O.Publisher:Oxford University PressMechanics of Materials (10th Edition)Mechanical EngineeringISBN:9780134319650Author:Russell C. HibbelerPublisher:PEARSONThermodynamics: An Engineering ApproachMechanical EngineeringISBN:9781259822674Author:Yunus A. Cengel Dr., Michael A. BolesPublisher:McGraw-Hill Education
- Control Systems EngineeringMechanical EngineeringISBN:9781118170519Author:Norman S. NisePublisher:WILEYMechanics of Materials (MindTap Course List)Mechanical EngineeringISBN:9781337093347Author:Barry J. Goodno, James M. GerePublisher:Cengage LearningEngineering Mechanics: StaticsMechanical EngineeringISBN:9781118807330Author:James L. Meriam, L. G. Kraige, J. N. BoltonPublisher:WILEY
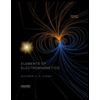
Elements Of Electromagnetics
Mechanical Engineering
ISBN:9780190698614
Author:Sadiku, Matthew N. O.
Publisher:Oxford University Press
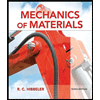
Mechanics of Materials (10th Edition)
Mechanical Engineering
ISBN:9780134319650
Author:Russell C. Hibbeler
Publisher:PEARSON
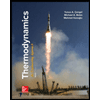
Thermodynamics: An Engineering Approach
Mechanical Engineering
ISBN:9781259822674
Author:Yunus A. Cengel Dr., Michael A. Boles
Publisher:McGraw-Hill Education
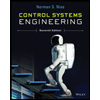
Control Systems Engineering
Mechanical Engineering
ISBN:9781118170519
Author:Norman S. Nise
Publisher:WILEY
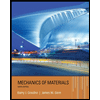
Mechanics of Materials (MindTap Course List)
Mechanical Engineering
ISBN:9781337093347
Author:Barry J. Goodno, James M. Gere
Publisher:Cengage Learning
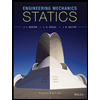
Engineering Mechanics: Statics
Mechanical Engineering
ISBN:9781118807330
Author:James L. Meriam, L. G. Kraige, J. N. Bolton
Publisher:WILEY