QUIZ 1
pdf
keyboard_arrow_up
School
Concordia University *
*We aren’t endorsed by this school
Course
NDT
Subject
Mechanical Engineering
Date
Apr 3, 2024
Type
Pages
15
Uploaded by DukeKnowledgeLapwing42
1
MECH 6541 : QUIZ 1 Concordia University : Mech 6541-M and Mech 6541-XX Name : Saykhat Chakraborty Student ID: 40236604 This is an open book quiz : Please mark this copy with your answers, electronically in red colour convert it to pdf and upload to the moodle on the 27
th
February 2024 midnight. TOTAL MARKS = 60 1.
The first module of the Hibernia platform in New Foundland, was welded with SMAW process. The platform was make out of 5 different modules. It look approximately 20,000 man hours to weld the first module, with welds made in all positions. You have been asked to improve productivity in the manufacture of the same module for a Spanish off shore Oil rig. What process will you recommend and what will be your estimated man hours for welding using this recommended process? (7) https://www.youtube.com/watch?v=x66K-734CsQ&t=9s check out the video, at Air Liquide we invented the vacuum pack electrode packaging which provided about a million-dollar business in selling E 8018-C3 electrodes for the Hiberina project! E 8018-
C3 electrode productivity is equal to E7018 electrode productivity. a.
Choice of welding process more efficient than SMAW FCAW b.
Choose welding parameter, electrode size and amperage for all position welding for SMAW 2.5 mm and 120 amperage c.
Choose welding parameter for all position welding for the new process 1.2 mm and wire speed 240 ipm d.
From welding productivity ppt, determine the deposition rates for both processes. 1. SMAW 2.5 lbs/hour 2. More efficient process 4.3 lbs/hour e.
Productivity comparison between the two welding electrode f.
Estimated Man hours for welding for the new process 6666.67 man hours
2
2.
For the following questions draw the welding symbol: (5 points as shown below) a.
(1) b.
(1) c.
(1) d.
(1) ¼’’ 3/8’ 45
3
e.
(1) 360
⸰
GSTM
Your preview ends here
Eager to read complete document? Join bartleby learn and gain access to the full version
- Access to all documents
- Unlimited textbook solutions
- 24/7 expert homework help
4
3.
For Questions 3 & 4, please search the (Lincoln) Procedure Handbook of arc welding , 12
th
edition Sections 1.1-1 to 2.1-43 to complete the following statements or paragraphs: ( 15) a.
In 1919, a patent was granted for a paper-covered electrode that did not leave a slag coating on the joint, yet produced a tough, ductile weld. This welding electrode, was used in 1925 to build massive pressure vessel for refineries that process oil. A 500 foot, three-span, all-welded bridge was build in 1923 in
Toronto, Canada b.
In 1927, the development of an extrusion process for applying a covering to the metal core substantially lowered the cost of covered electrodes
. The shielded-arc electrode with its deoxidizers and protective gases and slag became feasible. c.
Use of granular flux with a continuously fed bare steel electrode led to development of Submerged Arc Welding
. A 521 -ft tanker was fabricated by this process in 1936. d.
Impact strength is the ability of metal to absorb the energy of a force applied quickly to the member. e.
Iron melts at 1539
°C f.
Natural gas burner temperature is 1870
°C g.
Oxyacetylene flame temperature is 3500
°C h.
Welding arc temperature is 6020
°C i.
Welded Joint design
.....
The type of joint should be selected primarily on the basis of load requirements. Once the type is selected, however, variables in design and layout can substantially affect costs.( see section 2.2). Generally the following rules apply: 1. Select the joint requiring
the least amount of weld filler metal. 2. Use minimum root opening and included angle in order minimize the filler metal amount required. 3. On thick plate, use double grooves weld metal. 4. Avoid joints that create extremely deep grooves
. 5.Design the joint for easy accessibility for welding
. j.
Anticipating trouble - ....
For example, tanks frequently leak after welding is completed. Suppose a is to be welded with a continuous fillet weld on one side to make it liquid tight, and with intermittent fillets on the other side. On which side should the continuous fillet weld be located? A metal ability to absorb the energy of a load is applied quickly to the external joint if any leak occurs. Conversely, the repair may be completed with minimal rewelding of the continuous external leak location. Instead of load or service needs simplicity repair is the best.…
should leakage occur k.
Why do steel scrap yards prefer to use oxyacetylene to cut scrap rather than using the more cheap natural gas? ( answer is not in the reference – it
5
is for your to figure out. They prefer to have oxyacetylene because of the high temperature, portability, adaptability, affordability and structural safety plans.
6
4.
The advantages of Subassemblies...Once the product has been designed, the design laid out for production, and the joints selected and designed, the job is ready for assembly. In visualizing assembly procedure, the designer should break the weldment down into subassemblies several differ ways to determine, which, if any, will offer some of the following cost savings: (5) a.
A large number of subassemblies spreads the work out so that larger amount of people can do job. b.
Subassemblies usually provide better access for welding. c.
If stress relief of a portion of the weldment is necessary, it may be easier to complete before welding in the final assembly. d.
Subassemblies facilities inspection. e.
It is easier to control distortions or locked up stresses in subassemblies than in whole assemblies.
Your preview ends here
Eager to read complete document? Join bartleby learn and gain access to the full version
- Access to all documents
- Unlimited textbook solutions
- 24/7 expert homework help
7
5.
While designing a bridge, the Engineer decided to use API 5L pipe material to make up the structural members. The pipe outside diameter was 20" with a wall thickness of 1.5 inches thick. The architect wanted the welds to be ground flush on the outside surface, where as the field joints were to be made using permanent steel backing rings. The Engineer selected the following welding symbol for showing the field welds using a backing bar (ring) . There are three mistakes in the welding symbol. Please identify them and explain. (3) 1.
Since there is no fillet on the opposite side of the top bar, the aero that represents the fillet weld for the top bar should only have one fillet weld sign, which should be below the aero. 2.
Since the ground is carried out on the aero side, the symbol G should be pointed below the zero. 3.
To clearly display the field, a field weld sign needs to present at the aero junction of the single V-groove weld.
8
6.
Please search the web and find out why “all welded construction” Liberty ships catastrophically failed at sea during the second world war? a.
Why did they fail ?( 1 ) brittle crack b.
How many were built (1) 2708 c.
How many broke catastrophically ?( 1 ) 1200
9
7.
What is the preferred chemistry for steels to be arc welded to avoid brittle fracture at – 20 °C ? In your answer include % ranges for Carbon, Manganese, Silicon , Sulfur, and Phosphorous ( 5) Carbon % range 0.06 to 0.25 Manganese % range 0.35 to 0.80 Silicon % range 0.10 or less Sulphur % range 0.035 or less Phosphorus % range 0.030 or less
Your preview ends here
Eager to read complete document? Join bartleby learn and gain access to the full version
- Access to all documents
- Unlimited textbook solutions
- 24/7 expert homework help
10
8.
What are the four basic prerequisites for hydrogen cracking to occur? Refer to CSA Code W59-03 Appendix P and its commentary. (4) a.
Prerequisite 1 Susceptible Microstructure b.
Prerequisite 2 Sufficient Hydrogen Content c.
Prerequisite 3 Tensile Residual Stress d.
Prerequisite 4 Susceptible Microstructure at critical hydrogen level
11
9.
Using continuous cooling transformation diagrams choose appropriate preheat to avoid hydrogen cracking. Consider the relationship between the preheat temperature and continuous cooling diagram for AISI 4340 steel shown below. What is the recommended preheat temperature for AISI 4340 steel? Refer to your handout Weldability of carbon and low alloy steels, Lincoln Procedure Handbook, 12
th
edition, section 6.1.22. Justify your answer by interpreting the CCT diagram for this steel below (2)
12
Recommended preheat temperature per the Lincoln Procedures Handbook for AISI 4340 steel is (1) 600-700 ℉ Please explain the recommended preheat temperature per the CCT diagram for AISI 4340 steel, (1)… From the diagram the steel has been heated at the mentioned temperature in first question, the cooling rate is generally lower the hardness by allowing the hydrogen to disappear. However, minimizing the cooling rate is 10 hour, shaft cracking is prevented along with the better microstructure properties compared to the brittle marine site.
Your preview ends here
Eager to read complete document? Join bartleby learn and gain access to the full version
- Access to all documents
- Unlimited textbook solutions
- 24/7 expert homework help
13
10.
Answer the following questions: (6) points as shown below a.
What is the mandatory preheat temperature for P6 Group 1, 2, or 3 material per ASME rules (1) or what is a P6 material per ASME rules? 400℉ b.
Is stress relieving mandatory for CSA W59-03 construction (1) required if its mentioned on specification of drawing during the contact. c.
What are the two benefits of performing stress relief according to W59-03 code(2) Dimensional Stability, Fatigue Strength d.
e.
When performing deep penetration single pass welds, for processes other than ESW and EGW, what is the requirement for the depth to width ratio according to CSA W59-03 (1) Apart from the mentioned processes, the width of the weld pass face cannot exceed either the minimum width or depth of the cross-section of deposited weld metal. f.
CSA W59-03 standard considers a maximum HAZ hardness of 350 HV acceptable for bridge construction, while using low hydrogen electrodes. (1) Please explain why there is a chance of cracking or fatigue due to the hydrogen. To avoid the risk use HAZ hardness.
14
11.
How are lifting chains manufactured? (10) Note: Grade 80 lifting chain ( 80,000 psi UTS) is manufactured to the ASTM A 391 standard, with the following chemistry: Material Requirements : Heat Analysis—The selection and amounts of the alloying elements in the steel are left to the judgment of the individual chain manufacturer provided the steel meets the following criteria: Carbon: 0.35 % max.; Phosphorous:0.025 % max.; Sulfur: 0.025 % max. Nickel must be present in an alloying amount (0.40 % min); and at least one of the following elements must be present in an alloying amount: Chromium (0.40 % min) or Molybdenum (0.15 % min). 1 mark for each bullet = (5) marks a.
Describe the manufacturing of a chain in your words Material selection to forming, joining, heat treatment, and quality control all focus on reliable and high-quality products perfect for lifting. b.
What is the welding process used to butt weld the chain links and draw the welding symbol c.
Looking at the chemistry of the chain, what would be the heat treatment sequence and approximate heat treatment temperatures used in the manufacture of the chain (look at the video on chain making shown in the class) two heat treatment processes should be applied. First, put the chain into the Copper coil where the chain turns orange hot with a temperature of 940℃. Then the second heat treatment is a cooling bath, where the heated chain is submerged in the cold water to increase the stretch. d.
Why does the steel contain alloying elements like Nickel, Chromium or Molybdenum in making up of the chain. To make it more durable, longevity, stronger. e.
Why does the safety data sheet recommend not to use the chain below -40° F ? to avoid the hazard, increase the reliability and follow the operation procedure. RW
15
Your preview ends here
Eager to read complete document? Join bartleby learn and gain access to the full version
- Access to all documents
- Unlimited textbook solutions
- 24/7 expert homework help
Related Documents
Related Questions
Don't Use Chat GPT Will Upvote And Give Handwritten Solution Please
arrow_forward
kamihq.com/web/viewer.html?state%=D%7B"ids"%3A%5B"1vSrSXbH_6clkKyVVKKAtzZb_GOMRwrCG"%5D%...
lasses
Gmail
Copy of mom it for..
Маps
OGOld Telephone Ima.
Preview attachmen...
Kami Uploads ►
Sylvanus Gator - Mechanical Advantage Practice Sheet.pdf
rec
Times New Roman
14px
1.5pt
BIUSA
A Xa x* 三三
To find the Mechanical Advantage of ANY simple machine when given the force, use MA = R/E.
1.
An Effort force of 30N is appliled to a screwdriver to pry the lid off of a can of paint. The
screwdriver applies 90N of force to the lid. What is the MA of the screwdriver?
MA =
arrow_forward
Identify the lines
arrow_forward
mylabmastering.pearson.com
Chapter 12 - Lecture Notes.pptx: (MAE 272-01) (SP25) DY...
P Pearson MyLab and Mastering
Scores
arrow_forward
K
mylabmastering.pearson.com
Chapter 12 - Lecture Notes.pptx: (MAE 272-01) (SP25) DY...
P Pearson MyLab and Mastering
Mastering Engineering
Back to my courses
Course Home
Scores
Course Home
arrow_forward
Plz solve within 30min I vill give definitely upvote and vill give positive feedback thank you
arrow_forward
Esker on Demand- Customer X Chat Process Jobs In Hyderaba x
(Messages | Mynaukri
M Chegg Expert Hiring | Complet x
O Zoho Creator - Chegg Expert
experthiring.cheggindia.com/%23Form:Subject test?privateLink=bF53Pq3tqOdXDb6qq0PKbXBKnU6s212F4b2fdONuXXgZX2DTmgJz56EF3A79haQq4A..
Q
S Paused
Apps
State Bank of India...
Welcome to Esker o...
I Feet to Inches conv...
en Watch Super Hit Ful...
IRCTC Next Generat...
A TASHRM
A Time Tracker Time
Prime Video: Good...
Chin Expert Hr
saKANOLA
Subect Test
Determine the Sommerfeld number of a bearing whose clearance ratio is 600 and the
bearing load is 750 lbf . The length and radius of the given bearing is 1.75 in. and 0.75 in.
respectively. The viscosity of the oil inside the bearing is u=6 µreyn. The bearing is
rotating at a speed of 1800 rpm.
a) 0.28
b) 0.58
c) 0.23
d) 0.36
Activate Windows
Go to Settings to activate Windows.
453 PM
ヘ)み
OType here to search
THan-21
oms UP
...
arrow_forward
Please do not copy other's work and do not use ChatGPT or Gpt4,i will be very very very appreciate!!!
Thanks a lot!!!!!
arrow_forward
DISCUSS THE STEP-BY-STEP PROCESS OF HOW TO COME UP WITH A SOLUTION.
*Preferably if you typed the answer
Thumbs up guaranteed If you discuss the steps. Thankyou!
arrow_forward
The free body diagram must be drawn , its mandatory.
Don't use chatgpt
arrow_forward
permanent-magnet (pm) genera x
Bb Blackboard Learn
L STAND-ALONE.mp4 - Google Dri x
O Google Drive: ülwgjuó jc lis u
O ME526-WindEnergy-L25-Shuja.p x
O File | C:/Users/Administrator/Desktop/KFUPM%20Term%232/ME526/ME526-WindEnergy-L25-Shuja.pdf
(D Page view
A Read aloud
T) Add text
V Draw
Y Highlight
O Erase
17
of 26
Wind Farms
Consider the arrangement of three wind turbines in the following schematic in which wind
turbine C is in the wakes of turbines A and B.
Given the following:
- Uo = 12 m/s
A
-XẠC = 500 m
-XBC = 200 m
- z = 60 m
- Zo = 0.3 m
U.
-r, = 20 m
B
- CT = 0.88
Compute the total velocity deficit, udef(C) and the velocity at wind turbine C, namely Vc.
Activate Windows
Go to Settings to activate Windows.
Wind Farms (Example Answer)
5:43 PM
A 4)) ENG
5/3/2022
I!
arrow_forward
I need help solving this problem.
arrow_forward
I want to answer all the questions by handwriting.
arrow_forward
SEE MORE QUESTIONS
Recommended textbooks for you
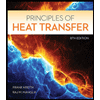
Principles of Heat Transfer (Activate Learning wi...
Mechanical Engineering
ISBN:9781305387102
Author:Kreith, Frank; Manglik, Raj M.
Publisher:Cengage Learning
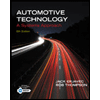
Automotive Technology: A Systems Approach (MindTa...
Mechanical Engineering
ISBN:9781133612315
Author:Jack Erjavec, Rob Thompson
Publisher:Cengage Learning
Related Questions
- Don't Use Chat GPT Will Upvote And Give Handwritten Solution Pleasearrow_forwardkamihq.com/web/viewer.html?state%=D%7B"ids"%3A%5B"1vSrSXbH_6clkKyVVKKAtzZb_GOMRwrCG"%5D%... lasses Gmail Copy of mom it for.. Маps OGOld Telephone Ima. Preview attachmen... Kami Uploads ► Sylvanus Gator - Mechanical Advantage Practice Sheet.pdf rec Times New Roman 14px 1.5pt BIUSA A Xa x* 三三 To find the Mechanical Advantage of ANY simple machine when given the force, use MA = R/E. 1. An Effort force of 30N is appliled to a screwdriver to pry the lid off of a can of paint. The screwdriver applies 90N of force to the lid. What is the MA of the screwdriver? MA =arrow_forwardIdentify the linesarrow_forward
- mylabmastering.pearson.com Chapter 12 - Lecture Notes.pptx: (MAE 272-01) (SP25) DY... P Pearson MyLab and Mastering Scoresarrow_forwardK mylabmastering.pearson.com Chapter 12 - Lecture Notes.pptx: (MAE 272-01) (SP25) DY... P Pearson MyLab and Mastering Mastering Engineering Back to my courses Course Home Scores Course Homearrow_forwardPlz solve within 30min I vill give definitely upvote and vill give positive feedback thank youarrow_forward
- Esker on Demand- Customer X Chat Process Jobs In Hyderaba x (Messages | Mynaukri M Chegg Expert Hiring | Complet x O Zoho Creator - Chegg Expert experthiring.cheggindia.com/%23Form:Subject test?privateLink=bF53Pq3tqOdXDb6qq0PKbXBKnU6s212F4b2fdONuXXgZX2DTmgJz56EF3A79haQq4A.. Q S Paused Apps State Bank of India... Welcome to Esker o... I Feet to Inches conv... en Watch Super Hit Ful... IRCTC Next Generat... A TASHRM A Time Tracker Time Prime Video: Good... Chin Expert Hr saKANOLA Subect Test Determine the Sommerfeld number of a bearing whose clearance ratio is 600 and the bearing load is 750 lbf . The length and radius of the given bearing is 1.75 in. and 0.75 in. respectively. The viscosity of the oil inside the bearing is u=6 µreyn. The bearing is rotating at a speed of 1800 rpm. a) 0.28 b) 0.58 c) 0.23 d) 0.36 Activate Windows Go to Settings to activate Windows. 453 PM ヘ)み OType here to search THan-21 oms UP ...arrow_forwardPlease do not copy other's work and do not use ChatGPT or Gpt4,i will be very very very appreciate!!! Thanks a lot!!!!!arrow_forwardDISCUSS THE STEP-BY-STEP PROCESS OF HOW TO COME UP WITH A SOLUTION. *Preferably if you typed the answer Thumbs up guaranteed If you discuss the steps. Thankyou!arrow_forward
- The free body diagram must be drawn , its mandatory. Don't use chatgptarrow_forwardpermanent-magnet (pm) genera x Bb Blackboard Learn L STAND-ALONE.mp4 - Google Dri x O Google Drive: ülwgjuó jc lis u O ME526-WindEnergy-L25-Shuja.p x O File | C:/Users/Administrator/Desktop/KFUPM%20Term%232/ME526/ME526-WindEnergy-L25-Shuja.pdf (D Page view A Read aloud T) Add text V Draw Y Highlight O Erase 17 of 26 Wind Farms Consider the arrangement of three wind turbines in the following schematic in which wind turbine C is in the wakes of turbines A and B. Given the following: - Uo = 12 m/s A -XẠC = 500 m -XBC = 200 m - z = 60 m - Zo = 0.3 m U. -r, = 20 m B - CT = 0.88 Compute the total velocity deficit, udef(C) and the velocity at wind turbine C, namely Vc. Activate Windows Go to Settings to activate Windows. Wind Farms (Example Answer) 5:43 PM A 4)) ENG 5/3/2022 I!arrow_forwardI need help solving this problem.arrow_forward
arrow_back_ios
SEE MORE QUESTIONS
arrow_forward_ios
Recommended textbooks for you
- Principles of Heat Transfer (Activate Learning wi...Mechanical EngineeringISBN:9781305387102Author:Kreith, Frank; Manglik, Raj M.Publisher:Cengage LearningAutomotive Technology: A Systems Approach (MindTa...Mechanical EngineeringISBN:9781133612315Author:Jack Erjavec, Rob ThompsonPublisher:Cengage Learning
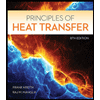
Principles of Heat Transfer (Activate Learning wi...
Mechanical Engineering
ISBN:9781305387102
Author:Kreith, Frank; Manglik, Raj M.
Publisher:Cengage Learning
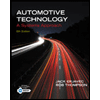
Automotive Technology: A Systems Approach (MindTa...
Mechanical Engineering
ISBN:9781133612315
Author:Jack Erjavec, Rob Thompson
Publisher:Cengage Learning