Lab 2 Handout - Winter 2024 (1)
pdf
keyboard_arrow_up
School
Oregon State University, Corvallis *
*We aren’t endorsed by this school
Course
437
Subject
Mechanical Engineering
Date
Apr 3, 2024
Type
Pages
6
Uploaded by EarlField7390
- 1 - MFGE437 Lab 2 – Machine Tool Feed Drive Axis Identification & Control (Actual Lab takes place on 2/12 at ATAMI on HP Campus)
Lab TA: Kaan Bahtiyar bahtiyak@oregonstate.edu This laboratory project has a PRELAB. The highlighted text below indicates the PRELAB (30% weight) that you need to complete. The prelab must be done coming to the lab. The aim of this lab project is to identify
dynamics of a ball-screw driven machine tool axis dynamics and design
motion controllers to achieve a desired dynamic characteristic. The system used in the lab is depicted in Figure 1. Figure 1: Experimental laboratory servo motor setup used Figure 1 shows the detailed schematic of the experimental setup featuring a single-axis ball-screw drive. As shown, machine table can move in only one direction, driven by a ball-screw mechanism similar to what has been demonstrated in the class. Rotary encoder is attached to measure the position of the motor shaft. The electrical motor is driven by a servo amplifier. This means, once voltage is sent to the amplifier, the amplifier generates current to the motor windings. Once the motor receives the current, it generates torque based on the motor torque constant and rotates the ball-screw. The feedback control of the motor is achieved by a PC. The PC is equipped with a data acquisition system. 1. Identification of Motor Velocity Dynamics In order to design a motion controller and achieve desired performance, dynamics of the motor system/axis of the machine needs to be identified. As studied in the class, velocity dynamics of the motor system is considered as a 1
st
order system. Simplified block diagram of the system is presented in Figure 2. Figure 2: Velocity dynamics of the motor G
v
(
s
)
=
K
v
τ
v
s
+
1
First Order System
u[v]
(Voltage to Amplifier)
!̇
[mm/sec]
(Moto/Axis Speed)
- 2 - An experimental method to identify dynamics of the system is to simply send a step (constant) voltage and measure the time constant and velocity gain K
V
from velocity response. As shown in Figure 3, when a voltage is sent to the amplifier, the motor of the ball-screw axis starts to speed up with an exponential function showing the first order system dynamics characteristics.
a) Theoretical Response b) Measured Speed Response on the Lab Setup Figure 3: Characteristics of the 1
st
order velocity dynamics of the motor/axis system Pre-lab Tasks (These has to be done and presented to the TA during the lab as a group) 1.
Data associated with Fig. 3.b (axis velocity) is uploaded on Canvas in an excel file. Please use this data (excel file) and identify the time constant and the velocity gain K
V
of the lab setup by “eye-balling”. Lab groups are given at the last page of the handouts. 2.
Use identified parameters and simulate speed response of the model to a 0.15[V] step voltage command. Once you simulate the response, compare measured (see Fig. 3.b) and simulated responses by plotting them on top of each other. The objective is to see how well they match each other. If they do not match at all this means you were not able to identify the parameters correctly. Please note that, you need to have those values with you during the lab. Present your results, including the figure displaying both the experimental and simulation of identified system responses overlaid on top of each other, to the TA. Therefore, you must complete this identification procedure before the actual lab. τ
v
τ
v
- 3 - 2. Velocity controller design:
The velocity dynamics of the axis system is identified in the previous section based on experimental data
. This part of the laboratory assignment is for you to implement a proportional velocity controller based on the identified velocity dynamics. The block diagram of the feedback control system is given in Figure 4. Figure 4: Closed loop Proportional Velocity control Pre-lab Tasks (This has to be done and presented to the TA During the lab as well)
As shown, the Kp
proportional gain multiplies the position error (
e
) and generates voltage to drive actual motor velocity close to the reference. Derive the transfer function of the closed loop system and calculate
feedback control gain Kp
to achieve the desired time constant of t
des
= 0.2[sec]
before
you come the lab. During the lab, TA will implement your controller. After you implement the proportional controller during the lab, you need to comment on the results in your lab report
. How does the resultant system behave? Perform a simulation and compare them together with the measured speed and comment on the differences. What can cause those differences? Using final value theorem calculate the final motor velocity in rpm. Compare it to the measured motor velocity when you implemented your controller. 3. Effect of Load Change on Motor Dynamics
Once you designed your feedback gain for the single axis setup, you will then be asked to implement the controller by removing mass from the setup. You will run your velocity controller again without changing the Kp
gain. As a result, the response would be different, and you will measure the step response again. Determine the new
time constant
of the new closed loop system
. Your task is to mathematically show whether the new time constant should be less than the desired time constant (
t
des
), or more.
Clearly show your calculations. How much did the time constant and the final value of the system for a step response has changed? Comment on the response of the system. Hint:
Compare closed loop transfer functions for both setups for the same K
P
. 4. Position Controller Design
In this experiment, you will inspect response of a position controller to the servo system. The block diagram of the system is given in Figure. Figure 5: Closed loop Proportional Position control of servo motor During the lab, the TA will tune a position controller. He will record the response of the system to a step position command. TA will provide you the measured response of the system in .csv file. K
v
τ
v
s
+
1
Kp
u
e
−
Motor/ Axis Velocity
Reference Velocity
K
v
τ
v
s
+
1
Kp
1
s
u
e
−
Motor/ Axis Position
Reference Position
!̇
!
x
r
Your preview ends here
Eager to read complete document? Join bartleby learn and gain access to the full version
- Access to all documents
- Unlimited textbook solutions
- 24/7 expert homework help
- 4 - In your lab reports, please calculate the rise time and overshoot of the system for this Kp
gain. Compare the calculated response to the measured response. How big is the error? What would cause the difference between calculated response and the measured? Please provide engineering comments. Lab Procedure and Report Preparation This lab requires a prelab to be performed. Please prepare your prelab and consult with the TA. During the lab, please follow TA’s instructions. Your lab report should be presented as an engineering report. It should have 3 sections. Namely, Introduction, Main Body and Conclusion
. In the introduction, please summarize the objectives of this lab. In the main body section, explain about the lab tasks, how you performed them. Show your calculations clearly. Be concise. Point out any difference between calculations and the actual measured quantities. Why are they different? Elaborate on them. In the conclusions section, present your final thoughts. Labs will take place on HP Campus B11, also known as the ATAMI building. Details will be given in the announcement. Lab Groups Section 010 2pm-3:50pm in ROG 126 - Rogers Hall 126 Section 011 4pm-5:50pm in ROG 126 - Rogers Hall 126
- 5 - Section 012 10am-11:50am in ROG 126 - Rogers Hall 126 Section 013 12pm-1:50pm in ROG 126 - Rogers Hall 126
- 6 - Section 010 R 8am-9:50am in ROG 126 - Rogers Hall 126
Your preview ends here
Eager to read complete document? Join bartleby learn and gain access to the full version
- Access to all documents
- Unlimited textbook solutions
- 24/7 expert homework help
Related Documents
Related Questions
You are a biomedical engineer working for a small orthopaedic firm that fabricates rectangular shaped fracture
fixation plates from titanium alloy (model = "Ti Fix-It") materials. A recent clinical report documents some problems with the plates
implanted into fractured limbs. Specifically, some plates have become permanently bent while patients are in rehab and doing partial
weight bearing activities.
Your boss asks you to review the technical report that was generated by the previous test engineer (whose job you now have!) and used to
verify the design. The brief report states the following... "Ti Fix-It plates were manufactured from Ti-6Al-4V (grade 5) and machined into
solid 150 mm long beams with a 4 mm thick and 15 mm wide cross section. Each Ti Fix-It plate was loaded in equilibrium in a 4-point bending
test (set-up configuration is provided in drawing below), with an applied load of 1000N. The maximum stress in this set-up was less than the
yield stress for the Ti-6Al-4V…
arrow_forward
Please give me the answers for this i been looking at this for a hour and my head hurts
arrow_forward
You are assigned as the head of the engineering team to work on selecting the right-sized blower that will go on your new line of hybrid vehicles.The fan circulates the warm air on the inside of the windshield to stop condensation of water vapor and allow for maximum visibility during wintertime (see images). You have been provided with some info. and are asked to pick from the bottom table, the right model number(s) that will satisfy the requirement. Your car is equipped with a fan blower setting that allow you to choose between speeds 0, 1,2 and 3. Variation of the convection heat transfer coefficient is dependent upon multiple factors, including the size and the blower configuration.You can only use the following parameters:
arrow_forward
Chrome
File
Edit
View
History
Bookmarks
People
Tab
Window
Help
McGraw-Hill Campus - ALEKS Science - CHM1045 GEN CHEM 1 BLENDED 669113
A bconline.broward.edu/d21/le/content/466883/fullscreen/12868783/View
McGraw-Hill Campus - ALEKS Science
O GASES
Interconverting pressure and force
A chemistry graduate student is designing a pressure vessel for an experiment. The vessel will contain gases at pressures up to 470.0 MPa. The student's
design calls for an observation port on the side of the vessel (see diagram below). The bolts that hold the cover of this port onto the vessel can safely withstand
a force of 2.80 MN.
pressure vessel
bolts
side
View
port
Calculate the maximum safe diameter w of the port. Round your answer to the nearest 0.1 cm.
O cm
Explanation
Check
O2021 McGraw-Hill Education. All Rights Reserved. Terms of Use
FEB
arrow_forward
Don't Use Chat GPT Will Upvote And Give Handwritten Solution Please
arrow_forward
Please show work in a handwritten format.
Don't use chatgpt.
Mechanics of materials/design.
arrow_forward
Please answer the 4th question
arrow_forward
Help me solve this ENGINEERING GRAPHICS question
Use 0.25 cartesian paper or 0.25 Isometric paper please.
arrow_forward
Help can only be sought via private Ed Discussion posts or instructor office hours.
- In all coding, use only functions covered in class. It will be considered a violation of the Academic Integrity Policy if you use
any build-in functions or operators of Matlab that calculate the inverse of a matrix, interpolations, spline, diff, integration, ode,
fft, pdes, etc.;
- You may reuse functions you yourself developed throughout this semester in this class or from solutions posted on Canvas for
this class.
Problem Description (CCOs #1, 2, 3, 4, 5, 6, 7, 8, 11, 12)
A water tank of radius R = 1.8m with two outlet pipes of radius r₁ = 0.05m and r2 installed at heights h₁ = 0.13m
and h₂ = 1m, is mounted in an elevator moving up and down causing a time dependent acceleration g(t) that must be
modeled as
g(t) = go+a1 cos(2π f₁t) + b₁ sin(2π f₁t) + a2 cos(2π f₂t) + b₂ sin(2π f₂t),
(1)
Figure 1: Water tank inside an elevator
The height of water h(t) in the tank can be modeled by the following ODE,…
arrow_forward
Identify the lines
arrow_forward
The first photo is the question, where the 2nd shows some problem solving strategies
arrow_forward
Please make the charts for the questions. Please refer to Successful Project Management (7th Edition). Attached is the example
Thank you.
arrow_forward
please help solve A-F. thank you
You are an engineer working on a project and your prototype has failed prematurely. You question whether or not a key component of the prototype was manufactured with the correct material. There are two way to check for the material properties. The first way is to have a material certification done to confirm the exact material composition. This will take some time. The second method to confirm the material properties is to make an ASTM test sample and test for the material properties. This tensile test was completed on a test sample with an initial diameter of .501” and an initial length of 2”. The Load-Deflection data for this tensile test is below. Use this data to answer the first set of questions on the Final Exam in eLearning. A. Determine the Ultimate Tensile Strength B. Determine the 0.2% Offset Yield Strength C. Determine the value of the Proportional Limit D. Determine the Modulus of Elasticity E. Determine the Strain at Yield F. Calculate %…
arrow_forward
Need correctly all parts
arrow_forward
4. Documents business requirements use-case narratives.for only one process
note: please i want Documents like this in pic
arrow_forward
Access Pearson
Mastering Engineering
Back to my courses
Course Home
Course Home
Scores
■Review
Next >
arrow_forward
est 2 (copy) (page 4 of 9)
A wiseup.wsu.acza/mod/quiz/attempt.php7attempt=610918cmid 148960&page=3
ops
O YouTube
M Gmail
Maps
O GENERAL MATHEM.
O New Tab
:WSU WiSeUp
1 MONLO GOA
ashboard / My courses / FLM15B2_KF_WS6222 2021 / Tests / Test 2 (copy)
uestion 4
Quz navigation
Gate AB in Figure below is 1.0 m long and 0.9 wide. Calculate force F on the gate and position X of its centre of
Not yet
answered
pressure.
Marked out of
Finish attempt
10,000
Rag question
3m
Oil,
s.g.=Q81
7m
1.0m
B
50
Answer
arrow_forward
Pl:1: this was all information that was given to me. If need j would need to look it up online.
arrow_forward
Access Pearson
Mastering Engineering
Back to my courses
Course Home
Course Home
Scores
Review
Next >
arrow_forward
Suppose a flu epidemic has broken out in all math 1215
courses at your school. Assume a total of 24 people have the
flu as of today and that each day the total number people
who have the flu double. Let f(t) represent the number of
people who have the flu at t days since today.
Estimate numerically when the number of people will reach
768. {your final answer just number}
arrow_forward
1) A low-friction cart is placed between two identical springs attached to rigid walls.
If you push the cart against one of the springs and release it, it will continue to
move back and forth between the springs.
www
Draw a force-time graph showing the sum of the horizontal forces exerted on the
cart as it moves back and force between the springs.
Scientific Abilities
Is able to construct a
force diagram
Missing
No representation is
constructed.
Inadequate
FD is constructed but
contains major errors such
as incorrect mislabeled or
not labeled force vectors,
length of vectors, wrong
direction, extra incorrect
vectors are added, or
vectors are missing.
Needs Improvement
FD contains no errors in
vectors but lacks a key
feature such as labels of
forces with two subscripts or
vectors are not drawn from
single point, or axes are
missing.
Adequate
The diagram contains no
errors and each force is
labeled so that it is clearly
understood what each force
represents.
Explain whether or not this…
arrow_forward
I need help with the first part and Matlab for this problem
arrow_forward
SEE MORE QUESTIONS
Recommended textbooks for you
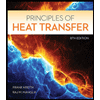
Principles of Heat Transfer (Activate Learning wi...
Mechanical Engineering
ISBN:9781305387102
Author:Kreith, Frank; Manglik, Raj M.
Publisher:Cengage Learning
Related Questions
- You are a biomedical engineer working for a small orthopaedic firm that fabricates rectangular shaped fracture fixation plates from titanium alloy (model = "Ti Fix-It") materials. A recent clinical report documents some problems with the plates implanted into fractured limbs. Specifically, some plates have become permanently bent while patients are in rehab and doing partial weight bearing activities. Your boss asks you to review the technical report that was generated by the previous test engineer (whose job you now have!) and used to verify the design. The brief report states the following... "Ti Fix-It plates were manufactured from Ti-6Al-4V (grade 5) and machined into solid 150 mm long beams with a 4 mm thick and 15 mm wide cross section. Each Ti Fix-It plate was loaded in equilibrium in a 4-point bending test (set-up configuration is provided in drawing below), with an applied load of 1000N. The maximum stress in this set-up was less than the yield stress for the Ti-6Al-4V…arrow_forwardPlease give me the answers for this i been looking at this for a hour and my head hurtsarrow_forwardYou are assigned as the head of the engineering team to work on selecting the right-sized blower that will go on your new line of hybrid vehicles.The fan circulates the warm air on the inside of the windshield to stop condensation of water vapor and allow for maximum visibility during wintertime (see images). You have been provided with some info. and are asked to pick from the bottom table, the right model number(s) that will satisfy the requirement. Your car is equipped with a fan blower setting that allow you to choose between speeds 0, 1,2 and 3. Variation of the convection heat transfer coefficient is dependent upon multiple factors, including the size and the blower configuration.You can only use the following parameters:arrow_forward
- Chrome File Edit View History Bookmarks People Tab Window Help McGraw-Hill Campus - ALEKS Science - CHM1045 GEN CHEM 1 BLENDED 669113 A bconline.broward.edu/d21/le/content/466883/fullscreen/12868783/View McGraw-Hill Campus - ALEKS Science O GASES Interconverting pressure and force A chemistry graduate student is designing a pressure vessel for an experiment. The vessel will contain gases at pressures up to 470.0 MPa. The student's design calls for an observation port on the side of the vessel (see diagram below). The bolts that hold the cover of this port onto the vessel can safely withstand a force of 2.80 MN. pressure vessel bolts side View port Calculate the maximum safe diameter w of the port. Round your answer to the nearest 0.1 cm. O cm Explanation Check O2021 McGraw-Hill Education. All Rights Reserved. Terms of Use FEBarrow_forwardDon't Use Chat GPT Will Upvote And Give Handwritten Solution Pleasearrow_forwardPlease show work in a handwritten format. Don't use chatgpt. Mechanics of materials/design.arrow_forward
- Please answer the 4th questionarrow_forwardHelp me solve this ENGINEERING GRAPHICS question Use 0.25 cartesian paper or 0.25 Isometric paper please.arrow_forwardHelp can only be sought via private Ed Discussion posts or instructor office hours. - In all coding, use only functions covered in class. It will be considered a violation of the Academic Integrity Policy if you use any build-in functions or operators of Matlab that calculate the inverse of a matrix, interpolations, spline, diff, integration, ode, fft, pdes, etc.; - You may reuse functions you yourself developed throughout this semester in this class or from solutions posted on Canvas for this class. Problem Description (CCOs #1, 2, 3, 4, 5, 6, 7, 8, 11, 12) A water tank of radius R = 1.8m with two outlet pipes of radius r₁ = 0.05m and r2 installed at heights h₁ = 0.13m and h₂ = 1m, is mounted in an elevator moving up and down causing a time dependent acceleration g(t) that must be modeled as g(t) = go+a1 cos(2π f₁t) + b₁ sin(2π f₁t) + a2 cos(2π f₂t) + b₂ sin(2π f₂t), (1) Figure 1: Water tank inside an elevator The height of water h(t) in the tank can be modeled by the following ODE,…arrow_forward
arrow_back_ios
SEE MORE QUESTIONS
arrow_forward_ios
Recommended textbooks for you
- Principles of Heat Transfer (Activate Learning wi...Mechanical EngineeringISBN:9781305387102Author:Kreith, Frank; Manglik, Raj M.Publisher:Cengage Learning
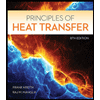
Principles of Heat Transfer (Activate Learning wi...
Mechanical Engineering
ISBN:9781305387102
Author:Kreith, Frank; Manglik, Raj M.
Publisher:Cengage Learning