3M03 Lab 3 Measuring the Toughness of Medium Carbon Steel
pdf
keyboard_arrow_up
School
McMaster University *
*We aren’t endorsed by this school
Course
3M03
Subject
Mechanical Engineering
Date
Apr 3, 2024
Type
Pages
7
Uploaded by SargentWater29347
Materials 3M03 Lab 3: Measuring the Toughness of Medium Carbon Steel Name: Hima Patel Student Number: 400373091 Date Performed: March 6
th
, 2023 Submission Date: March 11
th
, 2023
Executive Summary Toughness is a measure of material’s ability to withstand plastic deformation, cracking and fraction when a load is applied to it, which can also be translated to amount of energy said material can absorb before failure [1]. In this demonstration, we aim to understand how fracture toughness can change as the microstructure of a material changes after undergoing differing heat treatments. This was done so by performing a 3-Point-Bend-Test on 3 samples of steel of differing heat treatments (tempered, quenched, as received) [2]. From the data collected from these samples, Applied Force vs Crack Displacement plots were created, and the 95% Secant Method was used to determine data needed to calculate critical crack size and Stress Intensity Factor, K
. For the tempered, quenched, and as received samples, the critical crack sizes were determined to be, respectively, 1.48E-06, 8.93E-07, and 1.31E-06 (mm). Additionally, the stress intensity factors were determined to be 2.94, 2.29, and 1.54 MPa
√࠵?
, respectively. From these results, it can be concluded that a quenched steel is harder and more brittle than a tempered steel. This is because fracture toughness is defined as a materials ability to resist crack propagation, and since the quenched sample had a smaller crack size before failure and therefore produced a smaller fracture toughness, it is more likely to fail when a crack is propagated through it [3]. Background The purpose of this lab was to determine the fracture toughness, also known as the stress intensity fracture, K
IC
, of 3 different heat-treated samples of steel to determine the effect microstructure has on fracture toughness. Fracture toughness is a materials ability to withstand growth of a pre-existing crack without failing, meaning that if a material cannot handle this crack growing without failing, it is likely a very brittle material [3]. In this lab, the 3 different samples consist of a quenched steel, a tempered steel and a steel sample as received. Tempered steel is a heat treatment done to reduce brittleness and increase toughness of the material [4]. This is done so by heating the sample below its melting point and holding it at a specific temperature allowing it to undergo changes in its microstructure [4]. Tempering steel precipitated carbides into the steel which block dislocations from occurring, therefore helping relieve internal stress and making the material more workable [4]. Therefore, it is likely that the tempered steel will have a higher fracture value because of its ductile properties. Conversely, quenched steel is a heat treatment done to strengthen and harden the material [5]. It is done so by heating the steel to an immensely high temperature then rapidly cooling it, therefore ‘quenching it’ [5]. Quenching also changes the microstructure because the rapid cooling of steel creates the saturated solid solution of martensite, which is very hard and brittle [5]. Therefore, as per the definition of fracture toughness, it is likely that a quenched steel will have a low fracture toughness value because it is more likely to fail as a crack propagates through it. To determine the fracture toughness of these materials, a fracture toughness test called the 3-Point-
Bend test will be performed. This test bends pre-cracked samples to failure to determine the maximum crack it can withstand before failure [2]. A force is applied to each specimen increasing in magnitude until failure, collecting data on the applied load and the strain experienced by the sample. Afterwards, using the original gauge length of the sample, the crack displacement for each applied load value can be calculated. In the figure below, the 3-point-bend test is displayed, showing how the force is applied to the pre-cracked sample, and to measure the strain an extensometer was attached to each sample.
Figure 1: Diagram of 3-point-bend test. From this test, using the below equations, it allows us to determine fracture toughness, K
IC
, and the crack shape coefficient Y(b) [2].
(1) ࠵?(࠵?) =
1.99 − ࠵?(1 − ࠵?)[2.15 − 3.39࠵? + 2.7࠵?
!
]
(1 + 2࠵?)(1 − ࠵?)
"/!
(2)
࠵?
$%
=
3࠵?
&
࠵?
2࠵?࠵?
!
√࠵?
∙ ࠵?(࠵?)
From having determined these values, it is then possible to use the following equation to determine the maximum crack length in a specimen before failure [2].
(3)
࠵?
$%
= ࠵?
’
√࠵?࠵?
→ ࠵? =
>
࠵?
$%
࠵?
’
?
!
࠵?
Data Analysis and Results Below are the plots of Applied Force vs Crack Displacement for each sample (blue), along with the linear region in orange, its trendline in red, and the secondary line plotted using the 95% Secant method in purple. Figure 2: Applied Force vs Crack Displacement Plot for Tempered Sample y = 75.412x - 0.8431
0
5
10
15
20
25
0
0.05
0.1
0.15
0.2
0.25
0.3
0.35
Applied Load (kN)
Crack Displacement (mm)
Force vs Crack Displacement for Tempered Sample
Initial Data
Linear Region
95% Secant Line
Linear (Linear Region)
Your preview ends here
Eager to read complete document? Join bartleby learn and gain access to the full version
- Access to all documents
- Unlimited textbook solutions
- 24/7 expert homework help
Figure 3: Applied Force vs Crack Displacement Plot for Quenched Sample Figure 4: Applied Force vs Crack Displacement Plot for As Received Sample To determine the fracture toughness for each sample, it was necessary to obtain P
Q, seen in equation 2, where P
Q is defined as the critical force; to do so, the 95% secant method was used. This method involves using the applied force vs displacement curve, and highlighting the linear region, as seen in orange. Then, a trendline of this region specifically is created and the equation of that line is also generated, both shown on the graph, with the trendline of the linear region in red. To create the 95% secant line, a new equation is generated from the linear region equation, where both the slope and y-intercept values are 95% of the linear region values. Then, this new equation is plotted on the same graph, and the point of intersection of the secant line and the initial data in blue is marked. The corresponding y coordinate of the point of intersection is named the critical force of the sample. y = 69.383x - 2.431
-5
0
5
10
15
20
25
30
0
0.05
0.1
0.15
0.2
0.25
0.3
0.35
0.4
0.45
Applied Force (kN)
Crack Displacement (mm)
Force vs Crack Displacement for Quenched Sample
Initial Data
Linear Region
95% Secant Line
Linear (Linear Region)
y = 75.872x - 9.9876
-5
0
5
10
15
20
25
0
0.1
0.2
0.3
0.4
0.5
0.6
Applied Force (kN)
Crack Displacement (mm)
Force vs Crack Displacement for As Recieved
Initial Data
Linear Region
95% Secant Line
Linear (Linear Region)
An important note that to use this method, for the trial to be regarded as valid, you must divide the critical force by the max force and obtain a ratio of 1.1 or below. For the data given, only the tempered sample obtained a valid ratio of 1.09. This occurs due to error in the data collection. After identifying this term for each sample, the crack shape factor Y(b), can be calculated by using equation 1, where b crack size divided by specimen width, and then all terms required to calculate the fracture toughness have been calculated. A sample calculation of the fracture toughness value can be seen below. Sample Calculation 1: Fracture Toughness of Tempered Steel Afterwards, the hardness of each sample was also measured using the Rockwell C-scale. Several trials of this test were conducted to calculate a mean value so that the determined tensile strength s
f
, was as accurate as possible. This tensile strength is determined by converting the mean average of the hardness test values to the strength using the chart provided in lab [6]. The data and results of the hardness test are summarized in the table below. Trial 1 Trial 2 Trial 3 Trial 4 Trial 5 Trial 6 Mean Tensile Strength (
s
f
) (MPa) As Received 18
10.9
13.8
11.9
11.2
11.2
13
675.86
Quenched 36.5
38.5
42
41
41.9
35
39
1220.69
Tempered 39.5
40
37
36
40.5
40.9
39
1220.69
Table 1: Summary of Hardness Tests and Results. Now having found the tensile strength of each sample, the crack length before failure of each sample can be calculated using equation 3 as shown below. Sample Calculation 2: Critical Crack Distance Before Failure of Tempered Steel Now having acquired the critical shape factor, fracture toughness and tensile strength of each sample, conclusions of how the microstructure of each treated sample affect the fracture toughness can be made. See below for a summary table of all aforementioned values for each sample of steel. Tempered Steel Quenched Steel As Received Steel Fracture Toughness (MPa
√࠵?
) 2.94 2.29 1.54 Tensile Strength (MPa) 1220.69 1220.69 675.86 Critical Crack Size (mm) 1.48E-06 8.93E-07 1.31E-06 Table 2: Summary of Results for Steel Samples.
Conclusions This experiment demonstrates the effectiveness of the 3-point bending test for measuring fracture toughness of a material, particularly in the presence of pre-existing values such as cracks in a material. Using the 95% secant method, the critical crack distance and fracture toughness for 3 samples of steel were determined. For the tempered, quenched and as received samples, the fracture toughness values are 2.94, 2.29, and 1.54 MPa
√࠵?
, respectively and the critical crack distance values are 1.48E-06, 8.93E-07, and 1.31E-
06 (mm). Based on these results, it is shown that quenched steel exhibits higher hardness and brittleness than tempered steel, which coincides with the way each individual treatment affects steels microstructure. Where the as received sample acts as a solid foundation as to why heat treatment exists, as it had the lowest fracture toughness and is therefore the most likely to fail during crack propagation. This experiment highlights the importance of differing heat treatments and shows how their effect on a materials microstructure has extensive effects.
Your preview ends here
Eager to read complete document? Join bartleby learn and gain access to the full version
- Access to all documents
- Unlimited textbook solutions
- 24/7 expert homework help
References [1] Iowa State University, “Nondestructive Evaluation Physics: Materials: Toughness,” www.nde-ed.org
, 2019. https://www.nde-ed.org/Physics/Materials/Mechanical/Toughness.xhtml (accessed Mar. 11, 2023). [2] McMaster University. (2023). Materials 3M03, Demonstration 3:Measuring the Toughness of a Medium Carbon Steel. [PDF] Available: https://avenue.cllmcmaster.ca/d2l/le/content/516919/viewContent/3998138/View [3] Iowa State University, “Nondestructive Evaluation Physics: Materials: Fracture Toughness,” www.nde- ed.org
, 2019. https://www.nde-ed.org/Physics/Materials/Mechanical/Toughness.xhtml (accessed Mar. 11, 2023). [4] Monroe Engineering, “What Is Tempered Steel? - Monroe Engineering,” Monroe Engineering
, Oct. 28, 2019. Accessed: Mar. 11, 2023. [Online]. Available: https://monroeengineering.com/blog/what-is- tempered-steel/ [5] C. FitzGibbon, “What Is Quenching?,” Metal Supermarkets - Steel, Aluminum, Stainless, Hot-Rolled, Cold- Rolled, Alloy, Carbon, Galvanized, Brass, Bronze, Copper
, May 09, 2019. https://www.metalsupermarkets.com/what-is-quenching/ (accessed Mar. 11, 2023). [6] McMaster University. (2023). Materials 3M03, Hardness Conversion Chart - provides values for Rockwell C and other scales . [PDF] Available: https://avenue.cllmcmaster.ca/d2l/le/content/516919/viewContent/3998150/View
Related Documents
Related Questions
University of Babylon
Collage of Engineering\Al-Musayab
Department of Automobile
Engineering
Under Grad/Third stage
Notes:
1-Attempt Four Questions.
2- Q4 Must be Answered
3-Assume any missing data.
4 تسلم الأسئلة بعد الامتحان مع الدفتر
Subject: Mechanical
Element Design I
Date: 2022\01\25
2022-2023
Time: Three Hours
Course 1
Attempt 1
Q1/ Design a thin cylindrical pressure tank (pressure vessel) with hemispherical ends to the
automotive industry, shown in figure I below. Design for an infinite life by finding the
appropriate thickness of the vessel to carry a sinusoidal pressure varied from {(-0.1) to (6) Mpa}.
The vessel is made from Stainless Steel Alloy-Type 316 sheet annealed. The operating
temperature is 80 C° and the dimeter of the cylinder is 36 cm. use a safety factor of 1.8.
Fig. 1
(15 Marks)
Q2/ Answer the following:
1- Derive the design equation for the direct evaluation of the diameter of a shaft to a desired
fatigue safety factor, if the shaft subjected to both fluctuated…
arrow_forward
Question 2
You are a biomedical engineer working for a small orthopaedic firm that fabricates rectangular shaped fracture
fixation plates from titanium alloy (model = "Ti Fix-It") materials. A recent clinical report documents some problems with the plates
implanted into fractured limbs. Specifically, some plates have become permanently bent while patients are in rehab and doing partial
weight bearing activities.
Your boss asks you to review the technical report that was generated by the previous test engineer (whose job you now have!) and used to
verify the design. The brief report states the following... "Ti Fix-It plates were manufactured from Ti-6Al-4V (grade 5) and machined into
solid 150 mm long beams with a 4 mm thick and 15 mm wide cross section. Each Ti Fix-It plate was loaded in equilibrium in a 4-point bending
test (set-up configuration is provided in drawing below), with an applied load of 1000N. The maximum stress in this set-up was less than the
yield stress for the…
arrow_forward
dear tutor please provide neat and clean and detailed answer.
dont copy from google
adress both questions well
arrow_forward
Statics of Rigid Bodies (S5)
Note: I will report you if you answer this post multiple times so please follow it.Thank you for understanding, Tutor!
Content Covered:
- Friction
Direction: Solve the problem below by giving the complete solution. In return, I will give you a good and high rating. Thank you so much!
Note: Be careful with the calculations in the problem. Kindly double check the solution and answer if there is a deficiency. And also, box the final answer. Thank you so much!
arrow_forward
You are a biomedical engineer working for a small orthopaedic firm that fabricates rectangular shaped fracture
fixation plates from titanium alloy (model = "Ti Fix-It") materials. A recent clinical report documents some problems with the plates
implanted into fractured limbs. Specifically, some plates have become permanently bent while patients are in rehab and doing partial
weight bearing activities.
Your boss asks you to review the technical report that was generated by the previous test engineer (whose job you now have!) and used to
verify the design. The brief report states the following... "Ti Fix-It plates were manufactured from Ti-6Al-4V (grade 5) and machined into
solid 150 mm long beams with a 4 mm thick and 15 mm wide cross section. Each Ti Fix-It plate was loaded in equilibrium in a 4-point bending
test (set-up configuration is provided in drawing below), with an applied load of 1000N. The maximum stress in this set-up was less than the
yield stress for the Ti-6Al-4V…
arrow_forward
Statics of Rigid Bodies (S1)
Note: I will report you if you answer this post multiple times so please follow it.Thank you for understanding, Tutor!
Content Covered:
- Analysis of Structures
Direction: Solve the problem below by giving the complete solution. In return, I will give you a good and high rating. Thank you so much!
Note: Be careful with the calculations in the problem. Kindly double check the solution and answer if there is a deficiency. And also, box the final answer. Thank you so much!
arrow_forward
Show work
Part 1 website: https://ophysics.com/r5.html
PArt 2 website: https://ophysics.com/r3.html
arrow_forward
Statics of Rigid Bodies (S6)
Note: I will report you if you answer this post multiple times so please follow it.Thank you for understanding, Tutor!
Content Covered:
- Friction
Direction: Solve the problem below by giving the complete solution. In return, I will give you a good and high rating. Thank you so much!
Note: Be careful with the calculations in the problem. Kindly double check the solution and answer if there is a deficiency. And also, box the final answer. Thank you so much!
arrow_forward
Help!!! Please answer part b correctly like part A. Please!!!!
arrow_forward
Study Area
Document Sharing
User Settings
Access Pearson
mylabmastering.pearson.com
P Pearson MyLab and Mastering
The crash cushion for a highway barrier consists of a
nest of barrels filled with an impact-absorbing material.
The barrier stopping force is measured versus the vehicle
penetration into the barrier. (Figure 1)
Part A
P Course Home
b My Questions | bartleby
Review
Determine the distance a car having a weight of 4000 lb will penetrate the barrier if it is originally traveling at 55 ft/s when it
strikes the first barrel.
Express your answer to three significant figures and include the appropriate units.
Figure
1 of 1
36
μΑ
S =
Value
Units
Submit
Request Answer
Provide Feedback
?
Next >
arrow_forward
Help!!! Please answer all Correctly!!! Please
arrow_forward
Simple Machines-Levers, Inclined Planes, and Pulleys
Directions: Use the appropriate equation to answer the following questions. All answers should be
recorded below or in your Engineering Design journal. Remember to show all work.
A lever has an effort arm that is 5 meters long and a resistance (load) arm that is 3.5 meters
long. How much effort is needed to lift a 100 Newton weight? 5K
i). Draw the figure representing the problem
ii). How much effort is needed to lift a 100 Newton weight?
iii). What is the Actual Mechanical Advantage
1.
5m
i)
AOON 5-5m
arrow_forward
The crux of the problem asks you to compute the elastic modulus of a pancake--for this we give you numbers that we got from our own measurements of the pancakes. The last question asks you to hypothesize about which ingredients are playing the role of flour in the gluten free recipes. If you find this topic interesting, you may want to consider exploring something like this for your final project, and design an experiment to understand the difference between the normal and gluten free recipe and try to manipulate the gluten free recipe to better resemble the normal pancakes.If you choose to make the two recipes and compare them in your own kitchen, make sure you use exactly the same protocol for each recipe: In our trials, we made the batter, and then cooked on a skillet, using 1/4 cup of batter per pancake, and flipped when the edges were firm and golden, about 4-5 minutes on each side.Consider a stack of six pancakes. Each pancake is made of 1/4 cup (approximately 60 mL) of batter,…
arrow_forward
Part 2
Set up a spreadsheet solution to this problem. This will require that you derive one
formula to express the relationship between the friction coefficient, the spring constant,
and the spring compression; and a second formula to find the cost of using different slide
and spring types. Set up your spreadsheet as shown below. You can fill in the
"Acceptable?" column manually, rather than using a formula. Turn in a copy of your
spreadsheet/Matlab work
(solve for $)
Friction Spring Constant Spring Compression
M
k
0.1
0.1
0.1
0.2
0.2
0.2
50
100
150
50
100
150
4
Part 3
Your boss has decided to look at a second option. The spring mechanism will be
replaced by a drop box. After leaving the slide, the blocks will travel 5 horizontal feet
through the air and pass through a hole into the drop box. Using the slide you selected
above, determine how far below the slide (h) to place the hole in the drop box.
Yo = 5.2017/5
BLADE
2
RAMPE SLIDE
8⁰
SLIDE
Acceptable?
(Yes or No)
$'
Cost
51
In
DROP…
arrow_forward
Topics:
Statics of Rigid Bodies, Equilibrium of Rigid Bodies, Equilibrium in Two Dimensions, etc.
I will rate you with “LIKE/UPVOTE," if it is COMPLETE STEP-BY-STEP SOLUTION.
If it is INCOMPLETE SOLUTION and there are SHORTCUTS OF SOLUTION, I will rate you with “DISLIKE/DOWNVOTE.”
THANK YOU FOR YOUR HELP.
PS: If you have answered this already, don’t answer it again; give chance to other experts to answer it. I want to verify if all of you will arrive in the same final answer; thats why I ask it multiple times. If you answer it again, i'll dislike all your entries/answers.
arrow_forward
Help!!! Please answer it correctly
arrow_forward
An electric hot water heater consumes 3.1 kilowatts of electricity and converts it to heat. How long will it take the water heater to heat a 67 gallon tank of water from 10 degrees Celsius to 50 degrees Celsius? (1 kilogram of water is 0.37 gallons, 1 Calorie = 4200 J). It may be helpful to refer back to the weekly handout for guidance on this problem.
Your final answer should be in minutes (rounded to the nearest 10 minutes).
arrow_forward
+
X Strength of Materials. (Midterm
x Desmos | Scientific Calculator
x My Questions | bartleby
x Calculus Calculator - Symbolab
https://forms.office.com/Pages/ResponsePage.aspx?id%=Ks62XIUvNEiFeKmoyqxdb5JQ7Qw-I-pOgsEZYNdO7_ZUQIhTTOVNNzAOV1hYUOVOSEpSUFFZS1c1US4u A
. الإشارات الأخری
H التطبيقات
مطلوب
Section
5
3 m
2m
2 m
The rigid beam ABC is supported by pin A and wires BD and CE. If the load P on the beam
causes the end C to be displaced 6 mm downward. What is the normal strain developed in
* ?wire BD
)2 نقطة(
0.0015 C
2.57 O
0.00107
10:02 PM
AR
11/29/2020
arrow_forward
SEE MORE QUESTIONS
Recommended textbooks for you
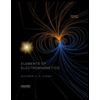
Elements Of Electromagnetics
Mechanical Engineering
ISBN:9780190698614
Author:Sadiku, Matthew N. O.
Publisher:Oxford University Press
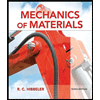
Mechanics of Materials (10th Edition)
Mechanical Engineering
ISBN:9780134319650
Author:Russell C. Hibbeler
Publisher:PEARSON
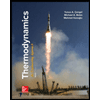
Thermodynamics: An Engineering Approach
Mechanical Engineering
ISBN:9781259822674
Author:Yunus A. Cengel Dr., Michael A. Boles
Publisher:McGraw-Hill Education
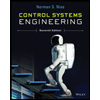
Control Systems Engineering
Mechanical Engineering
ISBN:9781118170519
Author:Norman S. Nise
Publisher:WILEY
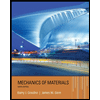
Mechanics of Materials (MindTap Course List)
Mechanical Engineering
ISBN:9781337093347
Author:Barry J. Goodno, James M. Gere
Publisher:Cengage Learning
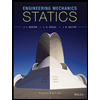
Engineering Mechanics: Statics
Mechanical Engineering
ISBN:9781118807330
Author:James L. Meriam, L. G. Kraige, J. N. Bolton
Publisher:WILEY
Related Questions
- University of Babylon Collage of Engineering\Al-Musayab Department of Automobile Engineering Under Grad/Third stage Notes: 1-Attempt Four Questions. 2- Q4 Must be Answered 3-Assume any missing data. 4 تسلم الأسئلة بعد الامتحان مع الدفتر Subject: Mechanical Element Design I Date: 2022\01\25 2022-2023 Time: Three Hours Course 1 Attempt 1 Q1/ Design a thin cylindrical pressure tank (pressure vessel) with hemispherical ends to the automotive industry, shown in figure I below. Design for an infinite life by finding the appropriate thickness of the vessel to carry a sinusoidal pressure varied from {(-0.1) to (6) Mpa}. The vessel is made from Stainless Steel Alloy-Type 316 sheet annealed. The operating temperature is 80 C° and the dimeter of the cylinder is 36 cm. use a safety factor of 1.8. Fig. 1 (15 Marks) Q2/ Answer the following: 1- Derive the design equation for the direct evaluation of the diameter of a shaft to a desired fatigue safety factor, if the shaft subjected to both fluctuated…arrow_forwardQuestion 2 You are a biomedical engineer working for a small orthopaedic firm that fabricates rectangular shaped fracture fixation plates from titanium alloy (model = "Ti Fix-It") materials. A recent clinical report documents some problems with the plates implanted into fractured limbs. Specifically, some plates have become permanently bent while patients are in rehab and doing partial weight bearing activities. Your boss asks you to review the technical report that was generated by the previous test engineer (whose job you now have!) and used to verify the design. The brief report states the following... "Ti Fix-It plates were manufactured from Ti-6Al-4V (grade 5) and machined into solid 150 mm long beams with a 4 mm thick and 15 mm wide cross section. Each Ti Fix-It plate was loaded in equilibrium in a 4-point bending test (set-up configuration is provided in drawing below), with an applied load of 1000N. The maximum stress in this set-up was less than the yield stress for the…arrow_forwarddear tutor please provide neat and clean and detailed answer. dont copy from google adress both questions wellarrow_forward
- Statics of Rigid Bodies (S5) Note: I will report you if you answer this post multiple times so please follow it.Thank you for understanding, Tutor! Content Covered: - Friction Direction: Solve the problem below by giving the complete solution. In return, I will give you a good and high rating. Thank you so much! Note: Be careful with the calculations in the problem. Kindly double check the solution and answer if there is a deficiency. And also, box the final answer. Thank you so much!arrow_forwardYou are a biomedical engineer working for a small orthopaedic firm that fabricates rectangular shaped fracture fixation plates from titanium alloy (model = "Ti Fix-It") materials. A recent clinical report documents some problems with the plates implanted into fractured limbs. Specifically, some plates have become permanently bent while patients are in rehab and doing partial weight bearing activities. Your boss asks you to review the technical report that was generated by the previous test engineer (whose job you now have!) and used to verify the design. The brief report states the following... "Ti Fix-It plates were manufactured from Ti-6Al-4V (grade 5) and machined into solid 150 mm long beams with a 4 mm thick and 15 mm wide cross section. Each Ti Fix-It plate was loaded in equilibrium in a 4-point bending test (set-up configuration is provided in drawing below), with an applied load of 1000N. The maximum stress in this set-up was less than the yield stress for the Ti-6Al-4V…arrow_forwardStatics of Rigid Bodies (S1) Note: I will report you if you answer this post multiple times so please follow it.Thank you for understanding, Tutor! Content Covered: - Analysis of Structures Direction: Solve the problem below by giving the complete solution. In return, I will give you a good and high rating. Thank you so much! Note: Be careful with the calculations in the problem. Kindly double check the solution and answer if there is a deficiency. And also, box the final answer. Thank you so much!arrow_forward
- Show work Part 1 website: https://ophysics.com/r5.html PArt 2 website: https://ophysics.com/r3.htmlarrow_forwardStatics of Rigid Bodies (S6) Note: I will report you if you answer this post multiple times so please follow it.Thank you for understanding, Tutor! Content Covered: - Friction Direction: Solve the problem below by giving the complete solution. In return, I will give you a good and high rating. Thank you so much! Note: Be careful with the calculations in the problem. Kindly double check the solution and answer if there is a deficiency. And also, box the final answer. Thank you so much!arrow_forwardHelp!!! Please answer part b correctly like part A. Please!!!!arrow_forward
- Study Area Document Sharing User Settings Access Pearson mylabmastering.pearson.com P Pearson MyLab and Mastering The crash cushion for a highway barrier consists of a nest of barrels filled with an impact-absorbing material. The barrier stopping force is measured versus the vehicle penetration into the barrier. (Figure 1) Part A P Course Home b My Questions | bartleby Review Determine the distance a car having a weight of 4000 lb will penetrate the barrier if it is originally traveling at 55 ft/s when it strikes the first barrel. Express your answer to three significant figures and include the appropriate units. Figure 1 of 1 36 μΑ S = Value Units Submit Request Answer Provide Feedback ? Next >arrow_forwardHelp!!! Please answer all Correctly!!! Pleasearrow_forwardSimple Machines-Levers, Inclined Planes, and Pulleys Directions: Use the appropriate equation to answer the following questions. All answers should be recorded below or in your Engineering Design journal. Remember to show all work. A lever has an effort arm that is 5 meters long and a resistance (load) arm that is 3.5 meters long. How much effort is needed to lift a 100 Newton weight? 5K i). Draw the figure representing the problem ii). How much effort is needed to lift a 100 Newton weight? iii). What is the Actual Mechanical Advantage 1. 5m i) AOON 5-5marrow_forward
arrow_back_ios
SEE MORE QUESTIONS
arrow_forward_ios
Recommended textbooks for you
- Elements Of ElectromagneticsMechanical EngineeringISBN:9780190698614Author:Sadiku, Matthew N. O.Publisher:Oxford University PressMechanics of Materials (10th Edition)Mechanical EngineeringISBN:9780134319650Author:Russell C. HibbelerPublisher:PEARSONThermodynamics: An Engineering ApproachMechanical EngineeringISBN:9781259822674Author:Yunus A. Cengel Dr., Michael A. BolesPublisher:McGraw-Hill Education
- Control Systems EngineeringMechanical EngineeringISBN:9781118170519Author:Norman S. NisePublisher:WILEYMechanics of Materials (MindTap Course List)Mechanical EngineeringISBN:9781337093347Author:Barry J. Goodno, James M. GerePublisher:Cengage LearningEngineering Mechanics: StaticsMechanical EngineeringISBN:9781118807330Author:James L. Meriam, L. G. Kraige, J. N. BoltonPublisher:WILEY
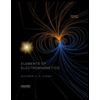
Elements Of Electromagnetics
Mechanical Engineering
ISBN:9780190698614
Author:Sadiku, Matthew N. O.
Publisher:Oxford University Press
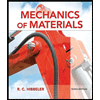
Mechanics of Materials (10th Edition)
Mechanical Engineering
ISBN:9780134319650
Author:Russell C. Hibbeler
Publisher:PEARSON
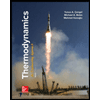
Thermodynamics: An Engineering Approach
Mechanical Engineering
ISBN:9781259822674
Author:Yunus A. Cengel Dr., Michael A. Boles
Publisher:McGraw-Hill Education
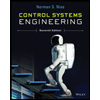
Control Systems Engineering
Mechanical Engineering
ISBN:9781118170519
Author:Norman S. Nise
Publisher:WILEY
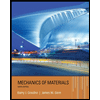
Mechanics of Materials (MindTap Course List)
Mechanical Engineering
ISBN:9781337093347
Author:Barry J. Goodno, James M. Gere
Publisher:Cengage Learning
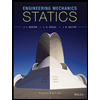
Engineering Mechanics: Statics
Mechanical Engineering
ISBN:9781118807330
Author:James L. Meriam, L. G. Kraige, J. N. Bolton
Publisher:WILEY