Lab2_SachinDasu_A1
pdf
keyboard_arrow_up
School
Georgia Institute Of Technology *
*We aren’t endorsed by this school
Course
4200
Subject
Mechanical Engineering
Date
Apr 3, 2024
Type
Pages
9
Uploaded by S-Dasu
Laboratory 2: Oil Flow in a Pipe CEE 4200: Hydraulic Engineering Section A1 Written By: Sachin Dasu Experiment Date: February 6, 2024 Submitted On: February 20, 2024
2 Table of Contents Extended Abstract……………………………………………………….3 Experiment………………………………………………………...3 Results………………………………………………….………….4 Discussion…………………………………………………………4 Conclusion………………………………………………………...8 Appendix………………………………………………………………...9
3 Extended Abstract Experiment In the Oil Flow in a Pipe laboratory, the experiment performed observes and quantifies the frictional loss for oil moving through a brass pipe. Fluid flow in a pipe is important in many engineering applications including domestic water supply, sewage removal, blood flow in arteries, and industrial oil pipelines. Fluid flow through a straight pipe in these applications loses energy because of friction. The frictional loss depends on several parameters including the fluid viscosity and flow rate. Dimensional analysis reveals that for a smooth pipe wall, the Reynolds number and pipe geometry characterize the frictional losses. The objectives of this laboratory experiment are to measure the streamwise pressure distribution for several Reynolds numbers, use the pressure drop in the fully developed region to calculate the resistance coefficient, and to compare the resistance coefficient with known theoretical and empirical relationships. Fluid flow through a pipe loses energy due to shear in both the laminar and turbulent regimes. The conservation of energy equation can be used, and the shaft work is0 and the velocity are elevation are the same at the inlet and outlet. Thus, the head loss in the pipe flow can be observed as a pressure drop in the flow direction. In the laminar case, the shear stress is equal to the velocity gradient times the molecular viscosity, thus, relating the velocity and the pressure drop. For turbulent flow, the shear stress is due to both molecular viscosity and the fluctuating fluid motion. For both the laminar and turbulent regimes, the resistance coefficient (or Darcy friction factor), is used to relate the pressure drop and velocity. Thus, If the resistance coefficient is known for a flow, the pressure drop and velocity are related. In the laboratory experiment, oil is pumped from the reservoir to the test pipe. After passing through a smooth contraction, the flow enters the 264 ¾ - in long brass pipe. The flow rate is controlled with a gate-valve, the flow rate in the test section increases. At the end of the pipe, oil flows into a weigh tank. The weigh tank will be used to measure the length of time required for a known weight to pass through the system. The specific weight of the fluid is then used to calculate the volumetric flow rate. The weigh tank drains into the reservoir. Nine static pressure taps are located at the following locations measured from the start of the pipe. Rubber tubing connects each tap to an individual manometer attached to the wall. A surveying stick mounted on the manometer board allows for elevation measurements for each meniscus. The static pressure is the distance from the datum location multiplied by the specific weight of oil. Pressure tap #9 is very close to the end of the pipe, and it is assumed that the pressure is 0 gage at that location, thus h
datum
is the elevation of the oil in manometer tube #9. The specific gravity of the red oil is 0.87 and the viscosity is a function of temperature. The oil temperature is measured with the thermometer mounted on the reservoir. The pump motor is started, and a flow rate is set by adjusting the gate valve. The weighing tank is used to measure the volumetric flow rate. With the tank drain valve open, the scale is balanced to set a datum. The drain valve is closed on the weighing tank and a known weight is added to the scale. A stopwatch is used to measure the time required to balance the additional weight. From the weight difference and measured time, the weight flow rate can be calculated as well as the volumetric flow rate. Once the manometer board has reached equilibrium,
Your preview ends here
Eager to read complete document? Join bartleby learn and gain access to the full version
- Access to all documents
- Unlimited textbook solutions
- 24/7 expert homework help
4 the elevation of the oil in each tube is noted by aligning the sliding reference plate with the meniscus. The flow rate is changes and the experiment is repeated for 8 flow rates. Results The table below, Table 1, contains the data collected in the laboratory. Case Weight (lb) Time (s) P1 P2 P3 P4 P5 P6 P7 P8 P9 1 50 61.16 6.35 6 5.18 4.33 3.45 2.61 1.79 0.94 0.12 2 50 67.49 5.45 5.3 4.56 3.83 3.03 2.3 1.51 0.82 0.11 3 50 72.62 5.05 4.79 4.19 3.5 2.8 2.11 1.4 0.79 0.11 4 45 71.72 4.53 4.29 4.29 3.12 2.5 1.9 1.26 0.7 0.1 5 45 82.47 4 3.77 3.77 2.75 2.2 1.67 1.12 0.64 0.1 6 45 96.78 3.48 3.29 3.29 2.4 1.93 1.47 0.98 0.56 0.1 7 40 100.01 3 2.85 2.85 2.09 1.68 1.29 0.87 0.5 0.11 8 40 122.25 2.5 2.37 2.07 1.74 1.4 1.08 0.74 0.44 0.11 Table 1. Oil Flow in a Pipe Laboratory Data.
Discussion 1.
Dimensional analysis can be used to show that the Reynolds number and non-dimensional pipe length characterize the non-dimensional pressure drop. The functional form can be rearranged to show this. Calculations are shown below. If the resistance coefficient is a function of Re, this agrees with the dimensional analysis. 𝛥𝛥𝛥𝛥
=
𝑓𝑓
(
𝐷𝐷
,
𝐿𝐿
,
𝜌𝜌
,
𝜇𝜇
,
𝑉𝑉
)
𝛥𝛥𝛥𝛥
=
𝑘𝑘𝐿𝐿
𝑎𝑎
𝐷𝐷
𝑏𝑏
𝜌𝜌
𝑐𝑐
𝜇𝜇
𝑑𝑑
𝑉𝑉
𝑒𝑒
𝑀𝑀𝐿𝐿
−1
𝑇𝑇
−2
=
𝐿𝐿
𝑎𝑎
𝐷𝐷
𝑏𝑏
(
𝑀𝑀𝐿𝐿
−3
)
𝑐𝑐
(
𝑀𝑀𝐿𝐿
−1
𝑇𝑇
−1
)
𝑑𝑑
(
𝐿𝐿𝑇𝑇
−1
)
𝑒𝑒
𝑀𝑀
: 1 =
𝑐𝑐
+
𝑑𝑑
𝐿𝐿
: −
1 =
𝑎𝑎
+
𝑏𝑏 −
3
𝑐𝑐 − 𝑑𝑑
+
𝑒𝑒
𝑇𝑇
: −
2 = −𝑑𝑑 − 𝑒𝑒
𝑏𝑏
= −
1
− 𝑎𝑎
+ 3
𝑐𝑐
+
𝑑𝑑 − 𝑒𝑒
=
𝑎𝑎 − 𝑑𝑑
𝛥𝛥𝛥𝛥
=
𝑘𝑘𝐿𝐿
𝑎𝑎
𝐷𝐷
−𝑎𝑎−𝑑𝑑
𝜌𝜌
1−𝑑𝑑
𝜇𝜇
𝑑𝑑
𝑉𝑉
2−𝑑𝑑
𝛥𝛥𝛥𝛥
=
𝑘𝑘 �
𝐿𝐿
𝐷𝐷
�
𝑎𝑎
�
𝜇𝜇
𝜌𝜌𝐷𝐷𝑉𝑉
�
𝑑𝑑
𝜌𝜌𝑉𝑉
2
5 2.
The specific gravity can be used to calculate the density and the specific weight of the oil. The table given in the laboratory handout, Table: Viscosity of the Red Oil, is used to determine the viscosity, μ, at the measured temperature. Calculations are shown below. Density = ρ
(oil) = SG * ρ(
H20) = 0.87 * (1.94 slugs/ft3) = 1.688 slugs/ft3 Specific Weight = γ(
oil) = ρ(
oil) * g = 1.689 * (32.2 ft/s2) = 54.347 lbs/ft3 Viscosity (Oil at 19⁰C) = 26.07 cP / 47880 cP = 5.44*10
-4
lbs/ft2 3.
The volumetric flow rate, mean velocity and Reynolds number for each test are calculated below. All Reynolds numbers are in the laminar regime. The table, Table 2, below provides the values for the flow rate, mean velocity, and Reynolds number. Sample calculations are shown below. Case Time (s) Q (ft3/s) V (ft/s) Re 1 61.16 0.0150419 4.0519837 863.88628 2 67.49 0.0136311 3.6719414 782.86094 3 72.62 0.0126682 3.4125492 727.55832 4 71.72 0.0115444 3.1098354 663.01947 5 82.47 0.0100396 2.704467 576.5946 6 96.78 0.0085551 2.3045815 491.33867 7 100.01 0.007359 1.9823564 422.64002 8 122.25 0.0060202 1.6217216 345.75238 Table 2. Volumetric Flow Rate, Mean Velocity, and Reynolds Number Flow Rate = Q = 𝑤𝑤
𝛾𝛾
(
𝑜𝑜𝑜𝑜𝑜𝑜
)
∗𝑡𝑡
= (50
𝑙𝑙𝑏𝑏𝑙𝑙
)/(
�
54.32
𝑜𝑜𝑏𝑏𝑙𝑙
𝑓𝑓𝑡𝑡
3
� ∗
(
61.16s) = 0.015 ft3/2 Mean Velocity = 𝑄𝑄
𝐴𝐴
= (
0
.
015�
𝑓𝑓𝑓𝑓
3
𝑠𝑠
�
�
𝜋𝜋
4
�∗�
0
.
825𝑖𝑖𝑖𝑖
12𝑖𝑖𝑖𝑖
𝑓𝑓𝑓𝑓
�
^
2
)
= 4.052 ft/s Reynolds Number = 𝜌𝜌𝜌𝜌𝜌𝜌
𝜇𝜇
= (1.688 slugs/ft3 * 4.052 ft/s * 0.06875 ft)/( 5.44*10
-4
lbs/ft2) = 863.89 4.
The plot below, Figure 1, shows the pressure (in psf) versus tap location data for each Reynolds number. Each data set is labeled with the appropriate Reynolds number. The pressure gradient is decreasing with Reynolds Numbers.
6 Figure 1. Pressure Vs. Tap location for Each Reynolds Number. 5.
The method of least squares is used to calculate the slope in the fully developed regime for each curve. The table below, Table 3, provides the slopes for each corresponding curve. Reynolds Number Slope dp/dx 863.88628 -15.63664 782.86094 -13.67655 727.55832 -12.47188 663.01947 -11.55847 576.5946 -10.13309 491.33867 -8.807439 422.64002 -7.553231 345.75238 -6.009862 Table 3. Slope of Each Curve in the Fully Developed Regime. 6.
The slope is used to calculate the wall shear stress. The pressure gradient is constant in the fully developed regime. The shear stress decreases with the Reyolds number. The shear stress is calculated below: τ = -(dp/dx)*D/4 = -(-15.637)*0.06875/4 = 0.269 lb/ft2 Reynolds Number
Shear Stress lb/ft2
863.88628 0.2687547 782.86094 0.2350657 727.55832 0.2143605 663.01947 0.1986612 576.5946 0.1741625 491.33867 0.1513779 0
50
100
150
200
250
300
350
400
0
5
10
15
20
25
Pressure (psf)
Tap Location (ft)
864
784
728
663
576
491
423
346
Your preview ends here
Eager to read complete document? Join bartleby learn and gain access to the full version
- Access to all documents
- Unlimited textbook solutions
- 24/7 expert homework help
7 422.64002 0.1298212 345.75238 0.1032945 Table 4. Wall Shear Stress of Each Curve in the Fully Developed Regime. 7.
The slope is used to calculate the resistance coefficient. The figure below, Figure 2, is a log-log plot of the resistance coefficient versus Reynolds number. The plot also shows the theoretical relationship for the laminar regime. The observed and theoretical relationship is calculated below. A table of values is also provided in Table 5. Sample calculations are also shown below. Figure 2. Resistance Coefficient Vs. Reynolds Number Re F (observed) F (Theoretical) 863.88628 0.0775871 0.0740838 782.86094 0.0826355 0.0817514 727.55832 0.0872481 0.0879655 663.01947 0.097366 0.0965281 576.5946 0.1128653 0.1109965 491.33867 0.1350975 0.1302564 422.64002 0.1565853 0.1514291 345.75238 0.1861631 0.1851036 Table 5. Reynolds Number and Resistance Coefficients Values 𝑓𝑓
𝑜𝑜𝑏𝑏𝑙𝑙𝑒𝑒𝑜𝑜𝑜𝑜𝑒𝑒𝑑𝑑
=
2�−
𝑑𝑑𝑑𝑑
𝑑𝑑𝑑𝑑
�
(
𝜌𝜌
)
𝜌𝜌
2
𝜌𝜌
=
2
(
−−15
.
64
)(.
06875
)
4
.
05
2
∗1
.
687
= 0.078 𝑓𝑓
𝑡𝑡ℎ𝑒𝑒𝑜𝑜𝑜𝑜𝑒𝑒𝑡𝑡𝑜𝑜𝑐𝑐𝑎𝑎𝑜𝑜
=
64
𝑅𝑅𝑒𝑒
=
64
863.89
= 0.074
0.01
0.1
1
100
1000
Resistance Coefficient
Reynolds Number
Observed
Theoretical
8 8.
The uncertainty of the pressure measurements is estimated below. All assumptions and steps are shown below. Standard Deviation of Ruler: 𝜎𝜎𝛥𝛥
=
0
.
01
2
= 0.005
ft Uncertainty of Static Pressure: 𝛥𝛥
= 𝛾𝛾𝛾𝛾
𝜎𝜎𝛥𝛥
= �
�
𝑑𝑑𝛥𝛥
𝑑𝑑𝛾𝛾
�
2
𝜎𝜎
𝑧𝑧
2
𝑑𝑑𝛥𝛥
𝑑𝑑𝛾𝛾
= 𝛾𝛾
𝜎𝜎𝛥𝛥
= �𝛾𝛾
2
(0.005)
2
= �
54.35
2
(0.005)
2
𝜎𝜎𝛥𝛥
= 0.272
𝑙𝑙𝑏𝑏
𝑓𝑓𝑡𝑡
2
Conclusion In the Oil Flow in a Pipe laboratory, the experiment performed observes and quantifies the frictional loss for oil moving through a brass pipe. Fluid flow through a straight pipe in these applications loses energy because of friction. The frictional loss depends on several parameters including the fluid viscosity and flow rate. Dimensional analysis reveals that for a smooth pipe wall, the Reynolds number and pipe geometry characterize the frictional losses. The objectives of this laboratory experiment are to measure the streamwise pressure distribution for several Reynolds numbers, use the pressure drop in the fully developed region to calculate the resistance coefficient, and to compare the resistance coefficient with known theoretical and empirical relationships. The uncertainty of the pressure measurements is also estimated in this laboratory. Calculations are shown above in the Test Results section of this laboratory report. The uncertainty of the static pressure measurement was calculated to be 0.272 lb/ft2.
9 Appendix The raw data collected in this laboratory experiment is provided below. Case Weight (lb) Time (s) P1 P2 P3 P4 P5 P6 P7 P8 P9 1 50 61.16 6.35 6 5.18 4.33 3.45 2.61 1.79 0.94 0.12 2 50 67.49 5.45 5.3 4.56 3.83 3.03 2.3 1.51 0.82 0.11 3 50 72.62 5.05 4.79 4.19 3.5 2.8 2.11 1.4 0.79 0.11 4 45 71.72 4.53 4.29 4.29 3.12 2.5 1.9 1.26 0.7 0.1 5 45 82.47 4 3.77 3.77 2.75 2.2 1.67 1.12 0.64 0.1 6 45 96.78 3.48 3.29 3.29 2.4 1.93 1.47 0.98 0.56 0.1 7 40 100.01 3 2.85 2.85 2.09 1.68 1.29 0.87 0.5 0.11 8 40 122.25 2.5 2.37 2.07 1.74 1.4 1.08 0.74 0.44 0.11
Your preview ends here
Eager to read complete document? Join bartleby learn and gain access to the full version
- Access to all documents
- Unlimited textbook solutions
- 24/7 expert homework help
Related Documents
Related Questions
62. •A 5-kg object is constrained to move along a straight
line. Its initial speed is 12 m/s in one direction, and its final
speed is 8 m/s in the
opposite
Complete the graph of
force versus time with
direction.
F (N)
(s)
appropriate values for
both variables (Figure
7-26). Several answers
are correct, just be sure
that your answer is
internally consistent.
Figure 7-26 Problem 62
arrow_forward
Kindly show the COMPLETE STEP-BY-STEP SOLUTION, DON’T DO SHORTCUTS OF SOLUTION, so I can understand the proccess.
I will rate you with “LIKE/UPVOTE," if it is COMPLETE STEP-BY-STEP SOLUTION.
If it is INCOMPLETE SOLUTION and there are SHORTCUTS OF SOLUTION, I will rate you with “DISLIKE/DOWNVOTE.”
Topics we discussed:
Statics of Rigid Bodies, Force System of a Force, Moment of a Force, Moment of a Force-Scalar Formulation, Moment of a Force-Vector Formulation, and Principle of Moment.
Thank you for your help.
arrow_forward
While preparing an experiment of a scale model submarine in a wind tunnel, for conditions of dynamic similarity, it is calculated that the wind speed is required to be 120 m/s. Which one of the following options will not help to reduce the air velocity of the wind tunnel?
A) Lowering the design velocity of the prototype (full scale) submarine
B) Increasing the pressure of the air used in the wind tunnel
c) Increasing the size of the scale model
D) Decreasing the density of air used in the wind tunnel
E) Reducing the temperature of the air used in the wind tunnel
arrow_forward
Hello Good Evening Sir,I have a question in my homework related structural statics lesson. The following below is my question. Please advice. Thank you so much
Regards,Yusuf
arrow_forward
Chapter 12 - Lecture Notes.pptx: (MAE 272-01) (SP25) DY...
Scores
arrow_forward
Please help me Matlab
arrow_forward
K
mylabmastering.pearson.com
Chapter 12 - Lecture Notes.pptx: (MAE 272-01) (SP25) DY...
P Pearson MyLab and Mastering
Mastering Engineering
Back to my courses
Course Home
Scores
Course Home
arrow_forward
i just need part 3
arrow_forward
i need the answer quickly
arrow_forward
permanent-magnet (pm) genera x
Bb Blackboard Learn
L STAND-ALONE.mp4 - Google Dri x
O Google Drive: ülwgjuó jc lis u
O ME526-WindEnergy-L25-Shuja.p x
O File | C:/Users/Administrator/Desktop/KFUPM%20Term%232/ME526/ME526-WindEnergy-L25-Shuja.pdf
(D Page view
A Read aloud
T) Add text
V Draw
Y Highlight
O Erase
17
of 26
Wind Farms
Consider the arrangement of three wind turbines in the following schematic in which wind
turbine C is in the wakes of turbines A and B.
Given the following:
- Uo = 12 m/s
A
-XẠC = 500 m
-XBC = 200 m
- z = 60 m
- Zo = 0.3 m
U.
-r, = 20 m
B
- CT = 0.88
Compute the total velocity deficit, udef(C) and the velocity at wind turbine C, namely Vc.
Activate Windows
Go to Settings to activate Windows.
Wind Farms (Example Answer)
5:43 PM
A 4)) ENG
5/3/2022
I!
arrow_forward
Statics of Rigid Bodies (S6)
Note: I will report you if you answer this post multiple times so please follow it.Thank you for understanding, Tutor!
Content Covered:
- Friction
Direction: Solve the problem below by giving the complete solution. In return, I will give you a good and high rating. Thank you so much!
Note: Be careful with the calculations in the problem. Kindly double check the solution and answer if there is a deficiency. And also, box the final answer. Thank you so much!
arrow_forward
Manufacturing process with two variables x1,x2 described by the empirical model:
y=bo +b1 x1 + b2 x2 + b12 x1 x2 + b3 (x1)^2 +b4 (x2)^2
please refere to the image attached
arrow_forward
6. A ball is thrown straight up in the air at time t = 0. Its height y(t) is given by
y(t) = vot -
791²
(1)
Calculate:
(a) The time at which the ball hits the ground. First, make an estimate using a scaling
analysis (the inputs are g and vo and the output is the time of landing. Think about
their units and how you might construct the output using the inputs, just by matching
units). Solve the problem exactly. Verify that the scaling analysis gives you (almost)
the correct answer.
(b) The times at which the ball reaches the height v/(4g). Use the quadratic formula.
(c) The times at which the ball reaches the height v/(2g). You should find that both
solutions are identical. What does this indicate physically?
(d) The times at which the ball reaches the height v/g. What is the physical interpretation
of your solutions?
(e) Does your scaling analysis provide any insight into the answers for questions (a-e)?
Discuss. (Hint: Observe how your answers depend on g and vo).
arrow_forward
F(t)
Force_Crate
Known values:
Mass of Block
68 kg
TT
Hs μk
0
0.63 0.53 26°
Problem Statement:
A crate is initially at rest on a sloped surface, when a force is applied: F(t)
where t is in seconds.
Answers:
When t=44.47 seconds, the crate has not yet started moving.
Find the magnitude of the friction force at that time:
317.771 N
The direction of the friction force at that time is: down the slope
Find the time required for the crate to start moving:
Find the crate's speed when t=174.9 s: 9.485 m/s
Be sure to include units with your answers.
169.756 S
240+0.2 N,
arrow_forward
Needs Complete typed solution with 100 % accuracy
arrow_forward
Lessons Discussed:
Static of Rigid Bodies, Force Vector, Addition of A System of Coplanar Forces, Cartesian Vector, Position and Force Vector Direction, Equilibrium of a Particle,
Reminder:
Kindly show the complete step-by-step solution. Please make sure that your handwriting is understandable and the picture of the solution is clear. I will rate you with “like/upvote” after. I need the answer right away, thank you.
Given Problem:
Please see the attached photo.
arrow_forward
SEE MORE QUESTIONS
Recommended textbooks for you
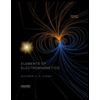
Elements Of Electromagnetics
Mechanical Engineering
ISBN:9780190698614
Author:Sadiku, Matthew N. O.
Publisher:Oxford University Press
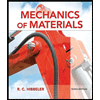
Mechanics of Materials (10th Edition)
Mechanical Engineering
ISBN:9780134319650
Author:Russell C. Hibbeler
Publisher:PEARSON
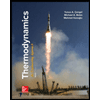
Thermodynamics: An Engineering Approach
Mechanical Engineering
ISBN:9781259822674
Author:Yunus A. Cengel Dr., Michael A. Boles
Publisher:McGraw-Hill Education
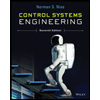
Control Systems Engineering
Mechanical Engineering
ISBN:9781118170519
Author:Norman S. Nise
Publisher:WILEY
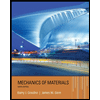
Mechanics of Materials (MindTap Course List)
Mechanical Engineering
ISBN:9781337093347
Author:Barry J. Goodno, James M. Gere
Publisher:Cengage Learning
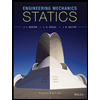
Engineering Mechanics: Statics
Mechanical Engineering
ISBN:9781118807330
Author:James L. Meriam, L. G. Kraige, J. N. Bolton
Publisher:WILEY
Related Questions
- 62. •A 5-kg object is constrained to move along a straight line. Its initial speed is 12 m/s in one direction, and its final speed is 8 m/s in the opposite Complete the graph of force versus time with direction. F (N) (s) appropriate values for both variables (Figure 7-26). Several answers are correct, just be sure that your answer is internally consistent. Figure 7-26 Problem 62arrow_forwardKindly show the COMPLETE STEP-BY-STEP SOLUTION, DON’T DO SHORTCUTS OF SOLUTION, so I can understand the proccess. I will rate you with “LIKE/UPVOTE," if it is COMPLETE STEP-BY-STEP SOLUTION. If it is INCOMPLETE SOLUTION and there are SHORTCUTS OF SOLUTION, I will rate you with “DISLIKE/DOWNVOTE.” Topics we discussed: Statics of Rigid Bodies, Force System of a Force, Moment of a Force, Moment of a Force-Scalar Formulation, Moment of a Force-Vector Formulation, and Principle of Moment. Thank you for your help.arrow_forwardWhile preparing an experiment of a scale model submarine in a wind tunnel, for conditions of dynamic similarity, it is calculated that the wind speed is required to be 120 m/s. Which one of the following options will not help to reduce the air velocity of the wind tunnel? A) Lowering the design velocity of the prototype (full scale) submarine B) Increasing the pressure of the air used in the wind tunnel c) Increasing the size of the scale model D) Decreasing the density of air used in the wind tunnel E) Reducing the temperature of the air used in the wind tunnelarrow_forward
- Hello Good Evening Sir,I have a question in my homework related structural statics lesson. The following below is my question. Please advice. Thank you so much Regards,Yusufarrow_forwardChapter 12 - Lecture Notes.pptx: (MAE 272-01) (SP25) DY... Scoresarrow_forwardPlease help me Matlabarrow_forwardK mylabmastering.pearson.com Chapter 12 - Lecture Notes.pptx: (MAE 272-01) (SP25) DY... P Pearson MyLab and Mastering Mastering Engineering Back to my courses Course Home Scores Course Homearrow_forwardi just need part 3arrow_forwardi need the answer quicklyarrow_forwardpermanent-magnet (pm) genera x Bb Blackboard Learn L STAND-ALONE.mp4 - Google Dri x O Google Drive: ülwgjuó jc lis u O ME526-WindEnergy-L25-Shuja.p x O File | C:/Users/Administrator/Desktop/KFUPM%20Term%232/ME526/ME526-WindEnergy-L25-Shuja.pdf (D Page view A Read aloud T) Add text V Draw Y Highlight O Erase 17 of 26 Wind Farms Consider the arrangement of three wind turbines in the following schematic in which wind turbine C is in the wakes of turbines A and B. Given the following: - Uo = 12 m/s A -XẠC = 500 m -XBC = 200 m - z = 60 m - Zo = 0.3 m U. -r, = 20 m B - CT = 0.88 Compute the total velocity deficit, udef(C) and the velocity at wind turbine C, namely Vc. Activate Windows Go to Settings to activate Windows. Wind Farms (Example Answer) 5:43 PM A 4)) ENG 5/3/2022 I!arrow_forwardStatics of Rigid Bodies (S6) Note: I will report you if you answer this post multiple times so please follow it.Thank you for understanding, Tutor! Content Covered: - Friction Direction: Solve the problem below by giving the complete solution. In return, I will give you a good and high rating. Thank you so much! Note: Be careful with the calculations in the problem. Kindly double check the solution and answer if there is a deficiency. And also, box the final answer. Thank you so much!arrow_forwardManufacturing process with two variables x1,x2 described by the empirical model: y=bo +b1 x1 + b2 x2 + b12 x1 x2 + b3 (x1)^2 +b4 (x2)^2 please refere to the image attachedarrow_forwardarrow_back_iosSEE MORE QUESTIONSarrow_forward_ios
Recommended textbooks for you
- Elements Of ElectromagneticsMechanical EngineeringISBN:9780190698614Author:Sadiku, Matthew N. O.Publisher:Oxford University PressMechanics of Materials (10th Edition)Mechanical EngineeringISBN:9780134319650Author:Russell C. HibbelerPublisher:PEARSONThermodynamics: An Engineering ApproachMechanical EngineeringISBN:9781259822674Author:Yunus A. Cengel Dr., Michael A. BolesPublisher:McGraw-Hill Education
- Control Systems EngineeringMechanical EngineeringISBN:9781118170519Author:Norman S. NisePublisher:WILEYMechanics of Materials (MindTap Course List)Mechanical EngineeringISBN:9781337093347Author:Barry J. Goodno, James M. GerePublisher:Cengage LearningEngineering Mechanics: StaticsMechanical EngineeringISBN:9781118807330Author:James L. Meriam, L. G. Kraige, J. N. BoltonPublisher:WILEY
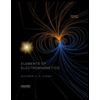
Elements Of Electromagnetics
Mechanical Engineering
ISBN:9780190698614
Author:Sadiku, Matthew N. O.
Publisher:Oxford University Press
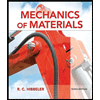
Mechanics of Materials (10th Edition)
Mechanical Engineering
ISBN:9780134319650
Author:Russell C. Hibbeler
Publisher:PEARSON
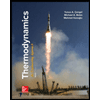
Thermodynamics: An Engineering Approach
Mechanical Engineering
ISBN:9781259822674
Author:Yunus A. Cengel Dr., Michael A. Boles
Publisher:McGraw-Hill Education
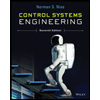
Control Systems Engineering
Mechanical Engineering
ISBN:9781118170519
Author:Norman S. Nise
Publisher:WILEY
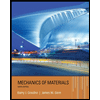
Mechanics of Materials (MindTap Course List)
Mechanical Engineering
ISBN:9781337093347
Author:Barry J. Goodno, James M. Gere
Publisher:Cengage Learning
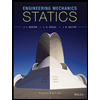
Engineering Mechanics: Statics
Mechanical Engineering
ISBN:9781118807330
Author:James L. Meriam, L. G. Kraige, J. N. Bolton
Publisher:WILEY