Lab Report 1
pdf
keyboard_arrow_up
School
Georgia Institute Of Technology *
*We aren’t endorsed by this school
Course
3020
Subject
Mechanical Engineering
Date
Apr 3, 2024
Type
Pages
18
Uploaded by S-Dasu
Laboratory 1: Metals
CEE 3020 Civil Engineering Materials Submitted to: Alexandra Wu by: Sachin Dasu Section B6 Group 1 Thomas Reid Cabe III Katerina Efthymiou Maggie Jiang Shruti Sarkar Sarah Elizabeth Scioli Abstract 10% Introduction 10% Experiment 5% Results 25% Discussion 25% Conclusion 10% Technical Writing 10% Graphics: Design 5% TOTAL Due Date: September 15, 2023
Abstract The main objectives of the first experiment, the Tension Test of Steel and Aluminum, is to develop an understanding of elastic and inelastic behavior of steel and aluminum and the relative influence of composition and processing on these behaviors, measure the strength and certain elastic and inelastic properties of steel and aluminum alloys, observe the behavior of metals under axial tensile load, and to study the failure characteristics of metals under uniaxial tensile load. The main objectives of the second experiment, the Impact Test of Steel and Aluminum, is to develop and understanding of impact toughness testing, measure impact toughness for both brittle and ductile metal alloys, characterize the fracture surface in both brittle and ductile failures, distinguish between ductile and brittle fracture, comparing both the impact toughness and fracture surfaces of different alloys and the behavior of a single alloy but at different temperature, and to assess the influence of col-working on fracture behavior during impact loading. This laboratory is broken up into four parts: Tension Test of Steel and Aluminum, Microscopy, Hardness Testing, and Impact Test of Steel and Aluminum. These are achieved through a tension test, microscopic examination, hardness test, and impact test. The samples are tested through an extensometer, analyzed under a microscope, a hardness testing machine, and a Charpy impact test. The samples analyzed in this experiment are two aluminum allows, Al-6061 and Al-2024, and a steel sample. The results obtained in this laboratory are analyzed and detailed below in this report.
Table of Contents Introduction ......................................................................................................................................
1 Experiment .......................................................................................................................................
1 Materials ...................................................................................................................................
1 Equipment ................................................................................................................................
1 Procedure ..................................................................................................................................
1 Results ..............................................................................................................................................
2 Discussion ........................................................................................................................................
8 Conclusion ......................................................................................................................................
10 References ......................................................................................................................................
11 Appendices .....................................................................................................................................
12
Your preview ends here
Eager to read complete document? Join bartleby learn and gain access to the full version
- Access to all documents
- Unlimited textbook solutions
- 24/7 expert homework help
1 Introduction The Metals Laboratory is comprised of four different sections- the Tension Test of Steel and Aluminum, Microscopy, Hardness Testing, and the Impact Test of Steel and Aluminum. The purpose of this laboratory is to develop an understanding of different material samples under different loads to determine their compositions and characteristics. The objective of this laboratory is to determine the behavior of the metal samples under load and understand their failure characteristics. Experiment Materials The materials and specimens used in the Tension Test of Steel and Aluminum are described as the following from the laboratory handout. “ASTM E8 standard flat tensile specimens of steel and aluminum alloy will be used. ‘Typical’ values for these specimens c
an be found on matweb.com. If typical values cannot be found for these exact samples, use a specimen that is comparable to the one tested, listing the name of this alternate specimen. The materials used in the lab are as follows: Steel Specimen Hot Rolled (HR) Steel –
(AISI 1008) Aluminum Specimens Aluminum –
(Al 2024 –
T4) Aluminum –
(Al 6061 –
T6)
”.
The materials and specimens used in the Impact Test of Steel and Aluminum are described as the following from the laboratory handout. “Standard notched impact samples (2 metals will be tested; specifications to be provided in lab). Each lab section should have 6 samples, 3 from each of 2 alloys, to be tested at 3 temperatures. The alloys are as follows: Specimens Hot Rolled Steel A36, notched impact sample Aluminum 6061 –
76, notched impact sample
”.
Equipment The equipment utilized in the tension test of steel and aluminum are listed below. •
A universal testing machine with grips (Precision +/- 1 lb) •
Extensometer (Precision +/- 5 µσ)
•
Digital Caliper (Precision +/- 0.0005 inch) •
Metal Scale •
Tape •
Safety Glasses •
Pencil. For Part 2 of this laboratory, Microscopy, a microscope was utilized to review the samples. For Part 3, the Hardness Test, a hardness testing machine was used. Part 4, the Impact Test of Steel and Aluminum, the materials used are listed below. •
Charpy impact tester •
Oven •
Dry ice •
Tongs, for handling samples •
Infrared thermometer Procedure
2 The procedures that were followed in this laboratory are detailed in the laboratory handout, which is attached in the References section of this laboratory report. There were no deviations from the procedures that were followed. Results Part 1. Tension Test 1.
The definitions for the following terms are found from Professor Dai Sheng’s lecture slides, which will be attached in the References section. i.
Engineering stress Load per cross-sectional area. ii.
Engineering Strain Change in deformation length over original length. iii.
True Stress Load per instantaneous area. iv.
True Strain Natural log of the addition of 1 and the true stress. v.
Proportional Limit Maximum load that a material can sustain without any deformation taking place. vi.
Yield Strength Amount of stress where a specific amount of deformation takes place. vii.
Upper Yield Point Maximum load necessary for deformation to take place. viii.
Lower Yield Point Minimum load necessary for deformation to take place. ix.
Modulus of Elasticity Ratio of stress to strain x.
0.2% Offset Yield Strength Amount of stress required to result in a strain of 0.2%. xi.
Ultimate Tensile Strength Maximum load that can be applied before failure. xii.
Rupture Strength Maximum stress that can be sustained without fracturing. xiii.
Ductility Measure of a material’s ability to undergo significant plastic deformation before rupture or breaking. xiv.
Toughness Ability of a material to absorb energy and plastically deform until fracturing (or ability to withstand impact loading). 2.
The two engineering stress-strain diagrams for each material show the entire stress-strain curve and a ‘close
-
up’ of the early stress
-strain behavior which captures the elastic behavior, yield points, and 0.2% offset yield stress. Figure 1 shows the entire stress-strain curve for hot rolled steel (AISI 1008).
Figure 1. Stress-Strain Diagram for AISI 1008.
3 Figure 2 shows the close-up of the early stress-strain behavior of AISI 1008. Figure 2. Close-up of early stress-strain behavior of AISI 1008. Figure 3 shows the entire stress-strain curve for Al-2024. Figure 3. Stress-Strain Diagram of Al-2024. 0
10000
20000
30000
40000
50000
60000
70000
0
0.05
0.1
0.15
0.2
0.25
0.3
0.35
Strain (Psi)
Strain (in/in)
Stress-Strain of AISI 1008
-10000
0
10000
20000
30000
40000
50000
60000
-0.02
0
0.02
0.04
0.06
0.08
0.1
0.12
0.14
Stress (Psi)
Strain (in/in)
Stress-Strain Diagram of AL-6061
Your preview ends here
Eager to read complete document? Join bartleby learn and gain access to the full version
- Access to all documents
- Unlimited textbook solutions
- 24/7 expert homework help
4 Figure 4 shows the close-up of the early stress-strain behavior of Al-2024. Figure 4. Close-up of early stress-strain behavior of Al-2024. Figure 5 shows the entire stress-strain curve for Al-6061. Figure 5. Stress-Strain Diagram of Al-6061. Figure 6 shows the close-up of the early stress-strain behavior of Al-6061. Figure 6. Close-up of early stress-strain behavior of Al-6061. -20000
0
20000
40000
60000
80000
100000
120000
0
0.05
0.1
0.15
0.2
0.25
0.3
0.35
Stress (Psi)
Strain (in/in)
Stress-Strain Diagram of Al-6061
5 0
10000
20000
30000
40000
50000
60000
70000
0
0.05
0.1
0.15
0.2
0.25
0.3
0.35
Stress (PSI)
Strain
Stress-Strain Diagram 0.2% Offset Yield Strength
Upper Yield Point
0.2% Offset Yield Strength
-10000
0
10000
20000
30000
40000
50000
60000
-0.02
0
0.02
0.04
0.06
0.08
0.1
0.12
0.14
Stress (Psi)
Strain (in/in)
Stress-Strain Diagram of AL-6061
0.2% Offset Yield Strength
3.
Figure 7 shows the stress-strain diagram for AISI 1008 labeled with yield strength, upper and lower yield strength, 0.2% offset yield strength, ultimate tensile strength, and rupture strength. Figure 7. Stress-Strain Diagram for AISI 1008 with labels. Figure 8 shows the stress-strain diagram for Al-2024 labeled with yield strength, upper and lower yield strength, 0.2% offset yield strength, ultimate tensile strength, and rupture strength. Figure 8. Stress-Strain Diagram of Al-2024. Figure 9 shows the stress-strain diagram with Al-6061 labeled with yield strength, upper and lower yield strength, 0.2% offset yield strength, ultimate tensile strength, and rupture strength. Figure 9. Stress-Strain Diagram of Al-6061. Yield Strength Lower yield point Ultimate Tensile Strength Rupture Strength Yield Strength Ultimate Tensile Strength Rupture Strength
6 -20000
0
20000
40000
60000
80000
100000
120000
0
0.05
0.1
0.15
0.2
0.25
0.3
0.35
Stress (Psi)
Strain (in/in)
Stress-Strain Diagram of Al-6061
4.
Table 1 displays the yield strength, 0.2% offset yield strength, ultimate tensile strength, rupture strength, true stress at failure, modulus of elasticity, ductility, and toughness of the three material samples used in this laboratory. Table 1: Stress-Strain Diagram values of each material sample. Material Sample Yield Strength (Psi) 0.2% Offset Yield Strength (Psi) Ultimate Tensile Strength (Psi) Rupture Strength (Psi) True Stress at Failure (Psi) Modulus of Elasticity (Psi) Ductility (%) Toughness (Psi) AISI 1008 4.88E+4 48900 61400 48100 17000 2.00E+6 29.7% 15100 Al-2024 1.89E+3 1890 48500 42100 27400 3.00E+6 14.1% 4900 Al-6061 1.94E+4 19600 98900 84600 53600 4.00E+6 20.5% 28700 Part 2. Microscopy 1.
The table below describes the results from the microscopic examination. The first three are from the tension test, and the last four are from the impact test (Charpy impact test). Samples were analyzed at a magnification of 8x. Table 2. Microscopic Examination Table. Specimen ID Analysis of Failure Mode Description of the Failure Plane Grain Orientation near the Fracture Surface Tension Test Samples AISI 1008 90% Ductile, wide grain Parallel to failure Al-2024 90% Narrow grain Parallel to failure Al-6061 90% Narrow grain Perpendicular to failure due to manufacturing Charpy Impact Test Samples Yield Strength 0.2% Offset Yield Strength Upper Yield Point Lower yield point Ultimate Tensile Strength Rupture Strength
Your preview ends here
Eager to read complete document? Join bartleby learn and gain access to the full version
- Access to all documents
- Unlimited textbook solutions
- 24/7 expert homework help
7 Hot Rolled Steel (A38) at 21⁰C
70% Many points of breakage Parallel to failure Hot Rolled Steel (A36) at 120⁰C
50% Many points of breakage Parallel to failure Al-6061-76 at 21⁰C
20% Many points of breakage Parallel to failure Al-6061-76 at 120⁰C
20% Many points of breakage Parallel to failure Part 3. Hardness 1.
The table below describes the average Rockwell hardness, both away from the necked region, and in the necked region. The standard deviation for each set of measurements is noted below. Table 3: Hardness Test Results, Averages, and Standard Deviations. Material Sample ID Hardness Test 1 (HRB) Hardness Test 2 (HRB) Hardness Test 3 (HRB) Hardness Test 4
(HRB)
Hardness Test 5 (HRB) Average Hardness (HRB) Standard Deviation AISI 1008 Away from Necked Region 82.8 79.3 70.4 67.2 65.5 73.0 7.62 AISI 1008 In Necked Region 86.2 86.1 87.5 86.7 84.7 86.2 1.02 Al-2024 Away from Necked Region 82.2 84.8 78.4 68.5 67.6 76.3 7.87 Al-2024 in Necked Region 84.3 83.5 77.5 82.2 83.0 82.1 2.68 Al-6061 Away from Necked Region 56.8 55.7 50.2 46.8 41.4 50.2 6.40 Al-6061 in Necked Region 51.9 55.6 55.7 52.9 51.7 53.6 1.96 Part 4. Impact 1.
The table below provides the measured impact toughness and temperatures at which those were obtained for the two alloys. The fracture surface characteristics are also noted, which are also found in Table 2. Table 4: Impact Toughness, Temperature, and Fraction Surface Characteristics. Material Sample Alloy Impact Toughness (ft/lb) Temperature Fracture Surface Characteristics Al-6061-76 24 21⁰C
Brittle, many points of breakage Al-6061-76 21 120⁰C
Brittle, many points of breakage Hot Rolled Steel A36 60 21⁰C
Ductile, many points of breakage Hot Rolled Steel A36 50 120⁰C
Ductile, many points of breakage 2.
The table below is a scatter plot comparing temperature with impact toughness, and has a curve fit equation for each alloy, as well. Figure 10: Temperature Vs. Impact Toughness
8 Discussion Part 1. Tension 1.
The measured yield strength of the AISI 1008 sample is 48800 psi, and the typical sample value is 24700 psi. The measured value is significantly higher than the expected value; this is due to a manufacturing defect, as was mentioned when conducting the laboratory. The measured ultimate strength is 61400 psi, and the typical value is 44200 psi. The measured value is significantly higher than the expected value; this is due to a manufacturing defect. The measured elastic modulus is 2.00E+6 psi, and the typical value is 29000 ksi. The measured value is significantly lower than the typical value, which is most likely due to a calculation error. The measured ductility is 29.7% and the typical value is 30%. These values are relatively close to each other, and the measured value is accurate. The measured yield strength of the Al-2024 sample is 1890 psi, and the typical sample value is 37700 psi. The measured value is significantly higher than the expected value; this is due to an experimental error. The measured ultimate strength is 48500 psi, and the typical value is 57300 psi. The measured value is significantly higher than the expected value; this is due to an experimental error. The measured elastic modulus is 3.00E+6 psi, and the typical value is 10600 ksi. The measured value is significantly lower than the typical value, which is most likely due to a calculation error. The measured ductility is 14.1% and the typical value is 19%. These values are relatively close to each other, but there could be a calculation error that may have been present. The measured toughness is 4900 psi, and the typical value is 23.7 ksi. This value is significantly lower than the typical value; this is most likely caused by an experimental error. These experimental errors are mostly due to manufacturing errors that caused the tension test to start with slippage. The measured yield strength of the Al-6061 sample is 19400 psi, and the typical sample value is 40000 psi. The measured value is significantly higher than the expected value; this is due to an experimental error. The measured ultimate strength is 98900 psi, and the typical value is 45000 psi. The measured value is significantly higher than the expected value; this is due to an experimental error. The measured elastic modulus is 4.00E+6 psi, and the typical value is 10000 ksi. The measured value is significantly lower than the typical value, which is most likely due to a calculation error. The measured ductility is 20.5% and the typical value is 20%. These values are relatively close to each other, and the measured value is accurate. The measured toughness is 28700si psi, and the typical value is 26.4 ksi. y = -0.0303x + 24.636
y = -0.101x + 62.121
0
10
20
30
40
50
60
70
0
20
40
60
80
100
120
140
Impact Reading
Temperature
Temperature Vs. Impact Toughness Aluminum
Steel
9 These values are close, but potential error could have been likely caused by an experimental error. These experimental errors are mostly due to manufacturing errors that caused the tension test to start with slippage. 2.
Experimental errors are mostly due to manufacturing errors that caused the tension test to start with slippage. Calculations could also be attributed to this as well. The slippage causes the data to be skewed and the offset yield line to also be skewed. 3.
Pure aluminum has a yield strength of 4000 psi, ultimate strength of 13100 psi, modulus of elasticity of 8.99E+6, and ductility of roughly 24%. The yield strength of pure aluminum seems lower than Al-6061 and higher than Al-2024. The ultimate strength is also significantly lower than those of the alloys. The elastic modulus of pure aluminum is also significantly higher than the alloys, and the ductility is similar to both alloys. The alloying and processing of the alloys allows for the metals to be stronger and more ductile, but these calculations may not be an accurate representation of these alloys. 4.
The steel alloy, AISI Type H11 Hot Worked (H11), has a yield strength of 239000 psi, ultimate strength of 289000 psi, elastic modulus of 30500 ksi, and ductility of 14%. These values all are significantly higher than the AISI 1008 alloy values, except for the ductility, which is lower than the AISI 1008 alloy ductility. Relative proportions of materials like carbon play a massive role in the mechanical properties of steel. Higher carbon percentages (to an extent) can increase the alloy’s ability to be less ductile, harder, and stronger. 5.
The measured rupture strength of AISI 1008 is significantly higher than the true stress at failure. The same conclusion can be drawn for the other two alloys as well. This could be due to an error in measuring the cross sectional area, as rupture strength utilizes the initial cross sectional area, while the true stress at failure would consider the instantaneous area. 6.
The necking process is one where a material under load deforms and the cross sectional area is reduced in the material. Necking can be identified in a stress-strain diagram where there is high stress and strain prior to reaching the rupture strength. The necking of the specimen relates to the shape of the stress-strain curve as the true stress would end up being higher, which would increasingly reduce the cross sectional area. Part 3. Hardness 7.
The average typical Rockwell B hardness value is 49.0 for the AISI 1008 alloy sample, 75.0 for the Al-2024 alloy sample, and 60.0 for the Al-6061 alloy sample. The average measured Rockwell B hardness value is 86.2 for the AISI 1008 alloy sample, 82.1 for the Al-2024 alloy sample, and 53.6 for the Al-6061 alloy sample. The AISI 1008 sample has a significantly higher measured value, which could be attributed to a manufacturing error. The two aluminum alloys have similar measured and expected values. 8.
The aluminum alloy Al-6061 has similar measured values both away form and in the necked region. The other two alloys do not present data similar away form and in the necked region. This is mainly due to a manufacturing error that the laboratory TA discussed heavily during the experiment. Part 4. Impact 9.
The main possible sources of error are manufacturing error, computational error, and human error. The manufacturing and computational error in the data could be attributed together, as the TA in the laboratory stated that the data that was generated did not seem on par with previous experiments run for this laboratory both this year and in the past few years. The human error would mostly be from not setting up equipment properly, which would cause the data to be skewed. 10.
The fracture surfaces resulting from the testing of the different alloys at different temperatures indicate that higher temperatures generally cause greater failure modes for both alloys (Al-6061-76 and Hot Rolled Steel A36). The lighter area in the aluminum alloy indicates brittle failure. The same is true for the steel alloy. The assessments for the fracture surface generally agree with the measured impact toughness for each alloy.
Your preview ends here
Eager to read complete document? Join bartleby learn and gain access to the full version
- Access to all documents
- Unlimited textbook solutions
- 24/7 expert homework help
10 11.
The temperature vs. toughness plots for the steel and aluminum alloys indicates a ductile-
to-brittle transition relatively well. The steel alloy absorbs more energy than the aluminum alloy, which is indicated in the chart, indicating that the steel alloy is more ductile than the aluminum alloy. Despite this, the increase in heat should make both alloys stronger, but, again, this is mostly due to a manufacturing error. Conclusions This laboratory indicates that heat can affect the ductility and strength of a material. This is shown in the tension and impact tests. It can make alloys more ductile or stronger depending on the temperature. This is shown with the microscopy results. The higher temperature sample generally has a more uniform grain pattern under impact. It can also be concluded that the process of creating an alloy can make the material stronger, which is indicated with the AISI H11 steel alloy and the AISI 1008 steel alloy. The H11 sample is significantly stronger, which is indicated through a higher carbon content. The addition of carbon allows for materials to be stronger than their pure material counterparts. In addition, the aluminum alloys tend to be less ductile than the steel alloy. This is indicated the tension test and microscopy results. The aluminum alloys tend to have a more uniform failure structure compared to the steel alloys, which can be an indicator of ductility.
11 References Dai, S. (n.d.). “Lecture 2 - Stress Strain.” lecture. Dai, S. (n.d.). “Lecture 4 –
Macro Behavior of Metals.” lecture. “Online materials information resource.” (n.d.). MatWeb
, <https://matweb.com/> (Sep. 15, 2023).
12 Appendix
Your preview ends here
Eager to read complete document? Join bartleby learn and gain access to the full version
- Access to all documents
- Unlimited textbook solutions
- 24/7 expert homework help
13
14
15
Your preview ends here
Eager to read complete document? Join bartleby learn and gain access to the full version
- Access to all documents
- Unlimited textbook solutions
- 24/7 expert homework help
Related Documents
Related Questions
Question 2
You are a biomedical engineer working for a small orthopaedic firm that fabricates rectangular shaped fracture
fixation plates from titanium alloy (model = "Ti Fix-It") materials. A recent clinical report documents some problems with the plates
implanted into fractured limbs. Specifically, some plates have become permanently bent while patients are in rehab and doing partial
weight bearing activities.
Your boss asks you to review the technical report that was generated by the previous test engineer (whose job you now have!) and used to
verify the design. The brief report states the following... "Ti Fix-It plates were manufactured from Ti-6Al-4V (grade 5) and machined into
solid 150 mm long beams with a 4 mm thick and 15 mm wide cross section. Each Ti Fix-It plate was loaded in equilibrium in a 4-point bending
test (set-up configuration is provided in drawing below), with an applied load of 1000N. The maximum stress in this set-up was less than the
yield stress for the…
arrow_forward
I want to briefly summarize what he is talking about and what you conclude.
pls very urgent
arrow_forward
A Team of Engineers asked for an internal combustion engine to use it in a designed car. Your role is to describe the operation sequence of different types of available engines, explain their mechanical efficiency, and deliver a detailed technical report to show your approach in solving and discussing the following tasks and issues.
You must follow the following steps to help the team:
STEP 1
Describe the operational sequence of four-stroke spark ignition and four-stroke compression ignition engines with the aid of sketches by constructing simple sketch representing the operation and plotting the P-V diagrams for each process during the cycle to show the following:
The input and output heat and net output work
The expansion and compression strokes
The air-fuel mixture intake and exhaust gasses
The spark plug when it is in the active mode
The complete cycle of ideal Otto and Diesel cycles that shows the input and output heat and net output work.
STEP 2
Explain the mechanical…
arrow_forward
Instrumentation & Measurements
This homework measures your capability to design/analyze various components/variables of ameasurement system based on what you have studied.
Question is Attached in image. Thank you.
arrow_forward
You are a biomedical engineer working for a small orthopaedic firm that fabricates rectangular shaped fracture
fixation plates from titanium alloy (model = "Ti Fix-It") materials. A recent clinical report documents some problems with the plates
implanted into fractured limbs. Specifically, some plates have become permanently bent while patients are in rehab and doing partial
weight bearing activities.
Your boss asks you to review the technical report that was generated by the previous test engineer (whose job you now have!) and used to
verify the design. The brief report states the following... "Ti Fix-It plates were manufactured from Ti-6Al-4V (grade 5) and machined into
solid 150 mm long beams with a 4 mm thick and 15 mm wide cross section. Each Ti Fix-It plate was loaded in equilibrium in a 4-point bending
test (set-up configuration is provided in drawing below), with an applied load of 1000N. The maximum stress in this set-up was less than the
yield stress for the Ti-6Al-4V…
arrow_forward
Please Use excel Shee t
Note:-
• Do not provide handwritten solution. Maintain accuracy and quality in your answer. Take care of plagiarism.
• Answer completely.
• You will get up vote for sure.
arrow_forward
Please give a complete solution in Handwritten format.
Strictly don't use chatgpt,I need correct answer.
Engineering dynamics
arrow_forward
Analysis and Interpretation of vertical Ground Reaction Forces. In this study, a volunteer was asked to walk on two force platforms under two different conditions. Condition 1- Normal Walk (NW), condition 2 - walking over an obstacle (OW). The right limb was the one to step on platform 1 in both conditions. The force platforms were used to measure the vertical ground reaction forces on the right limb. Data was collected on Vicon (Nexus) software and the attached graphs ( mean NW/OW, Mean (+-)1SD NW/OW) were created. Analyse and Interpret the graphs attached.
arrow_forward
How may acoustic designers alter the design of a room, which was previously used for music performances, into a room now to be used for spoken word performances? Use annotated diagrams for your response
arrow_forward
00
T
R
%24
Bb R
V qa
du/webapps/assessment/take/launch.jsp?course_assessment_id%=_254968_1&course_id%3D 3565256_1&content id= 52826
* Question Completion Status:
Attach File
Browse Local Files
Browse Content Collection
QUESTION 2
A company needs to choose one supplier for a particular type of silicon wafer used'in the production of
semiconductors. The company has three options. Supplier A sells the silicon wafers for $2.50 per wafer,
independently of the number of wafers ordered. Supplier B sells the wafers for $2.40 each but does not
consider an order for less than 2,000 wafers. Supplier C sells the wafers for $2.30 each but does not accept
an order for less than 3,000 wafers. Assume an order setup cost of $100 and an annual requirement of 20,000
wafers. Assume a 20% annual interest rate for holding cost calculations.
a. Which supplier should be chosen to minimize the total annual cost for the wafers, and what is the
optimal order quantity?
b. If the replenishment lead time for wafers…
arrow_forward
Access Pearson
Mastering Engineering
Back to my courses
Course Home
Course Home
Scores
■Review
Next >
arrow_forward
Which of these statements are correct?
arrow_forward
Please give me the answers for this i been looking at this for a hour and my head hurts
arrow_forward
PHYS X PHYS X
印 PHYS X
PHYS X
POTPHYS X
PHYS X
E PHYS X E PHYS
top/semester2/physics%20for%20engineers/PHYS220_CH15_Lecture%20Notes_Problems%2015 19,15.29 S
(D Page view
A Read aloud
V Draw
Problem-15-19: page-475
A 0.500-kg object attached to a spring with a force constant of 8.00 N/m vibrates in simple harmonic motion
with an amplitude of 10.0 cm. Calculate the maximum value of its
(a) speed, and acceleration.
(b) the speed and the acceleration when the object is 6.00 em from the equilibrium position, and
(c) the time interval required for the object to move from.r50 to r5 8.O0 cm.
Solution:
arrow_forward
dear tutor please provide neat and clean and detailed answer.
dont copy from google
adress both questions well
arrow_forward
Chapter 14, question 5:Using the information in Problem 14.5, construct a net material requirements plan using the following on-hand inventory.
ITEM
ON-HAND INVENTORY
ITEM
ON-HAND INVENTORY
S
20
W
30
T
20
X
25
U
40
Y
240
V
30
Z
40
Note: Fill out the following table to answer this question:
Group of answer choices
Item Z has an order release of 320 units in week 3.
Item Z has an order release of 320 units in week 1.
Item Z has an order release of 320 units in week 2.
Item Z has an order release of 60 units in week 3.
Item Z has an order release of 300 units in week 2.
Chapter 14, question 7:Refer again to Problems 14.5 and 14.7. In addition to 100 units of S, there is also a demand for 20 units of U, which is a component of S. The 20 units of U are needed for maintenance purposes. These units are needed in week 6. Modify the net material requirements plan to reflect this change.
Group of answer choices
Item Z has an order release of 300 units in…
arrow_forward
SEE MORE QUESTIONS
Recommended textbooks for you
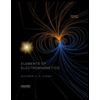
Elements Of Electromagnetics
Mechanical Engineering
ISBN:9780190698614
Author:Sadiku, Matthew N. O.
Publisher:Oxford University Press
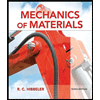
Mechanics of Materials (10th Edition)
Mechanical Engineering
ISBN:9780134319650
Author:Russell C. Hibbeler
Publisher:PEARSON
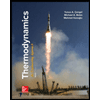
Thermodynamics: An Engineering Approach
Mechanical Engineering
ISBN:9781259822674
Author:Yunus A. Cengel Dr., Michael A. Boles
Publisher:McGraw-Hill Education
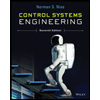
Control Systems Engineering
Mechanical Engineering
ISBN:9781118170519
Author:Norman S. Nise
Publisher:WILEY
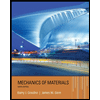
Mechanics of Materials (MindTap Course List)
Mechanical Engineering
ISBN:9781337093347
Author:Barry J. Goodno, James M. Gere
Publisher:Cengage Learning
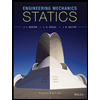
Engineering Mechanics: Statics
Mechanical Engineering
ISBN:9781118807330
Author:James L. Meriam, L. G. Kraige, J. N. Bolton
Publisher:WILEY
Related Questions
- Question 2 You are a biomedical engineer working for a small orthopaedic firm that fabricates rectangular shaped fracture fixation plates from titanium alloy (model = "Ti Fix-It") materials. A recent clinical report documents some problems with the plates implanted into fractured limbs. Specifically, some plates have become permanently bent while patients are in rehab and doing partial weight bearing activities. Your boss asks you to review the technical report that was generated by the previous test engineer (whose job you now have!) and used to verify the design. The brief report states the following... "Ti Fix-It plates were manufactured from Ti-6Al-4V (grade 5) and machined into solid 150 mm long beams with a 4 mm thick and 15 mm wide cross section. Each Ti Fix-It plate was loaded in equilibrium in a 4-point bending test (set-up configuration is provided in drawing below), with an applied load of 1000N. The maximum stress in this set-up was less than the yield stress for the…arrow_forwardI want to briefly summarize what he is talking about and what you conclude. pls very urgentarrow_forwardA Team of Engineers asked for an internal combustion engine to use it in a designed car. Your role is to describe the operation sequence of different types of available engines, explain their mechanical efficiency, and deliver a detailed technical report to show your approach in solving and discussing the following tasks and issues. You must follow the following steps to help the team: STEP 1 Describe the operational sequence of four-stroke spark ignition and four-stroke compression ignition engines with the aid of sketches by constructing simple sketch representing the operation and plotting the P-V diagrams for each process during the cycle to show the following: The input and output heat and net output work The expansion and compression strokes The air-fuel mixture intake and exhaust gasses The spark plug when it is in the active mode The complete cycle of ideal Otto and Diesel cycles that shows the input and output heat and net output work. STEP 2 Explain the mechanical…arrow_forward
- Instrumentation & Measurements This homework measures your capability to design/analyze various components/variables of ameasurement system based on what you have studied. Question is Attached in image. Thank you.arrow_forwardYou are a biomedical engineer working for a small orthopaedic firm that fabricates rectangular shaped fracture fixation plates from titanium alloy (model = "Ti Fix-It") materials. A recent clinical report documents some problems with the plates implanted into fractured limbs. Specifically, some plates have become permanently bent while patients are in rehab and doing partial weight bearing activities. Your boss asks you to review the technical report that was generated by the previous test engineer (whose job you now have!) and used to verify the design. The brief report states the following... "Ti Fix-It plates were manufactured from Ti-6Al-4V (grade 5) and machined into solid 150 mm long beams with a 4 mm thick and 15 mm wide cross section. Each Ti Fix-It plate was loaded in equilibrium in a 4-point bending test (set-up configuration is provided in drawing below), with an applied load of 1000N. The maximum stress in this set-up was less than the yield stress for the Ti-6Al-4V…arrow_forwardPlease Use excel Shee t Note:- • Do not provide handwritten solution. Maintain accuracy and quality in your answer. Take care of plagiarism. • Answer completely. • You will get up vote for sure.arrow_forward
- Please give a complete solution in Handwritten format. Strictly don't use chatgpt,I need correct answer. Engineering dynamicsarrow_forwardAnalysis and Interpretation of vertical Ground Reaction Forces. In this study, a volunteer was asked to walk on two force platforms under two different conditions. Condition 1- Normal Walk (NW), condition 2 - walking over an obstacle (OW). The right limb was the one to step on platform 1 in both conditions. The force platforms were used to measure the vertical ground reaction forces on the right limb. Data was collected on Vicon (Nexus) software and the attached graphs ( mean NW/OW, Mean (+-)1SD NW/OW) were created. Analyse and Interpret the graphs attached.arrow_forwardHow may acoustic designers alter the design of a room, which was previously used for music performances, into a room now to be used for spoken word performances? Use annotated diagrams for your responsearrow_forward
- 00 T R %24 Bb R V qa du/webapps/assessment/take/launch.jsp?course_assessment_id%=_254968_1&course_id%3D 3565256_1&content id= 52826 * Question Completion Status: Attach File Browse Local Files Browse Content Collection QUESTION 2 A company needs to choose one supplier for a particular type of silicon wafer used'in the production of semiconductors. The company has three options. Supplier A sells the silicon wafers for $2.50 per wafer, independently of the number of wafers ordered. Supplier B sells the wafers for $2.40 each but does not consider an order for less than 2,000 wafers. Supplier C sells the wafers for $2.30 each but does not accept an order for less than 3,000 wafers. Assume an order setup cost of $100 and an annual requirement of 20,000 wafers. Assume a 20% annual interest rate for holding cost calculations. a. Which supplier should be chosen to minimize the total annual cost for the wafers, and what is the optimal order quantity? b. If the replenishment lead time for wafers…arrow_forwardAccess Pearson Mastering Engineering Back to my courses Course Home Course Home Scores ■Review Next >arrow_forwardWhich of these statements are correct?arrow_forward
arrow_back_ios
SEE MORE QUESTIONS
arrow_forward_ios
Recommended textbooks for you
- Elements Of ElectromagneticsMechanical EngineeringISBN:9780190698614Author:Sadiku, Matthew N. O.Publisher:Oxford University PressMechanics of Materials (10th Edition)Mechanical EngineeringISBN:9780134319650Author:Russell C. HibbelerPublisher:PEARSONThermodynamics: An Engineering ApproachMechanical EngineeringISBN:9781259822674Author:Yunus A. Cengel Dr., Michael A. BolesPublisher:McGraw-Hill Education
- Control Systems EngineeringMechanical EngineeringISBN:9781118170519Author:Norman S. NisePublisher:WILEYMechanics of Materials (MindTap Course List)Mechanical EngineeringISBN:9781337093347Author:Barry J. Goodno, James M. GerePublisher:Cengage LearningEngineering Mechanics: StaticsMechanical EngineeringISBN:9781118807330Author:James L. Meriam, L. G. Kraige, J. N. BoltonPublisher:WILEY
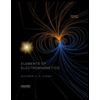
Elements Of Electromagnetics
Mechanical Engineering
ISBN:9780190698614
Author:Sadiku, Matthew N. O.
Publisher:Oxford University Press
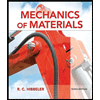
Mechanics of Materials (10th Edition)
Mechanical Engineering
ISBN:9780134319650
Author:Russell C. Hibbeler
Publisher:PEARSON
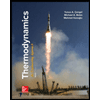
Thermodynamics: An Engineering Approach
Mechanical Engineering
ISBN:9781259822674
Author:Yunus A. Cengel Dr., Michael A. Boles
Publisher:McGraw-Hill Education
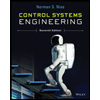
Control Systems Engineering
Mechanical Engineering
ISBN:9781118170519
Author:Norman S. Nise
Publisher:WILEY
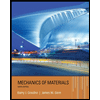
Mechanics of Materials (MindTap Course List)
Mechanical Engineering
ISBN:9781337093347
Author:Barry J. Goodno, James M. Gere
Publisher:Cengage Learning
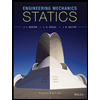
Engineering Mechanics: Statics
Mechanical Engineering
ISBN:9781118807330
Author:James L. Meriam, L. G. Kraige, J. N. Bolton
Publisher:WILEY