AE 460 Laboratory Note for Experiment 1
docx
keyboard_arrow_up
School
University of Illinois, Urbana Champaign *
*We aren’t endorsed by this school
Course
460
Subject
Mechanical Engineering
Date
Apr 3, 2024
Type
docx
Pages
19
Uploaded by PrivateDugong76
AE 460 Laboratory Note for Experiment 1
Wind Tunnel Calibration Lab
by
Ani Saini, Margarita Kuzmanova, Andrew Beusse, Srinu Rayudu
TA: Derrick Wiberg
Section AB6, Group B, Tuesday, 5:00 - 7:00 pm
Date of submission {placed at the bottom of the title page}
1
1. INTRODUCTION
For this experiment, students were acquainted with the use of the Aerolab low-speed wind tunnel, which was calibrated to gather accurate data for future experiments. Using the static pressure ring, the rake of pressure probes, and the Dwyer inclined manometer, data was collected for a range of RPM from 400 to 1400 in increments of 100 RPM. To determine the differential pressure at the tunnel inlet, pressure measurements were obtained from the wall static pressure taps. The rake of pressure probes was used to calculate the average dynamic pressure and speed. The Dwyer inclined manometer and the input motor RPM for the tunnel fan were used to determine the average test-section dynamic pressure. Each data point (measurement) was then recorded in NI LabView software to be accessed later.
2. APPARATUS
This lab utilized a static pressure ring, rake of pressure probes, Omega PX653 Pressure Transmitter, Pressure Systems Incorporated (PSI) NetScanner pressure system, and Model 4195 Compact Digital Barometer to calibrate the Dwyer inclined manometer attached to the Aerolab low-speed wind tunnel using the tunnel fan frequency controller to control the speed of the tunnel. The static pressure ring was used to measure the static pressure in the system which was then used as the reference for the PSI NetScanner pressure system to calculate the difference in pressure of each tap on the pressure rake in the tunnel. This can be seen in the figure below depicting the laboratory set up with one line entering the pressure system coming from the ring and the other from the test section with
2
the rake inside. The Dwyer manometer was used to determine the difference in static pressure and atmospheric pressure. This was also the function of the pressure transducer located under the control panel. Figure 1. Schematic of the experimental apparatus to measure the static and total pressure
through the wind tunnel test section.
Table. 1. List of Laboratory Equipment and their accuracy as used in the experiment No.
Item
Size/Range/
Capacity
Accuracy Use in experiment 1
The Aerolab Low-Speed 9.5:1 contraction ratio / Test … Used as the wind tunnel that
Flo
w In
Flow Conditi
oning Section
Contr
action Sectio
n
Test Sectio
n
Fa
n
Diffus
er Flow out
Static Press
ure Ring
Pressure Rake
Dwyer Manometer
Test Section Zoomed In
Con
trol Pan
el PSI NetScann
er Pressure System
1.
5”
Your preview ends here
Eager to read complete document? Join bartleby learn and gain access to the full version
- Access to all documents
- Unlimited textbook solutions
- 24/7 expert homework help
3
Wind Tunnel
section dimensions: 24” x 12” x 12”
was being calibrated
2
Static Pressure Ring
… … Used as reference which
rake measurements were compared to
3
Rake of 13 Pressure Probes each arm is 4.5”/ each tap is 1.5” apart
… measure pressures at various locations in the test section
4
Dwyer Inclined Manometer 0”-6” of water
1% of measureme
nt
measure the difference between the atmospheric pressure and static pressure
5
Omega PX653 Pressure Transmitter
0”-10” of water
± 0.25% of the measureme
nt
measure the difference between the atmospheric pressure and static pressure 6
PSI NetScanner Pressure System
Maximum pressure differential of 1 Psid
0.1% of the
measureme
nt
Used to find the
differential pressure of the rake and the static pressure
7
Compact Digital Manometer …. ± 0.148 in Hg and ± 1.8 ̊F
Used to get atmospheric pressure and temperature in the lab
4
3. RESULTS AND DISCUSSION
All the following experiments are derived as part of procedures laid out in the laboratory manual.
3.1. Average Total, Static, and Dynamic Pressures
The dynamic pressure was a key element to collect in this lab. The data included nine total pressure probes (T1-T9), and five static pressure probes (S1-S5) for individual runs conducted with a 100 RPM increment from 400-1400 RPM. The values from the probes were averaged and the average dynamic pressure was calculated using the difference between the Average Total Pressure vs Average Static Pressure at each point. This data is provided for reference in Table. 2.
Table. 2. Data and Specifications for Dynamic Pressure
Data Point
Motor Speed
[RPM]
Average Total
Pressure [psi]
Average Static
Pressure [psi]
Average Dynamic
Pressure [psi]
1
400
4.62E-03
4.77E-05
4.58E-03
2
500
7.60E-03
8.50E-05
7.52E-03
3
600
1.15E-02
1.22E-04
1.13E-02
4
700
1.63E-02
2.46E-04
1.60E-02
5
800
2.16E-02
2.39E-04
2.14E-02
6
900
2.81E-02
2.75E-04
2.78E-02
7
1000
3.51E-02
4.30E-04
3.47E-02
8
1100
4.28E-02
4.96E-04
4.23E-02
9
1200
5.17E-02
3.81E-04
5.13E-02
10
1300
5.95E-02
9.74E-04
5.85E-02
11
1400
6.94E-02
4.20E-04
6.90E-02
5
The table above presents the average dynamic pressure as derived from the other given quantities. One thing to notice is that the data for all the quantities are not linear, in fact they increase as a quadratic as the motor speed increases linearly. 3.2 Actual Velocity, Reynolds Number per unit Length, and Mach Number
Since the dynamic pressure is calculated, other quantities such as the true velocity, Mach number, and Reynolds number can be computed. Modifying Bernoulli's equation with assumptions such as steady, inviscid, and incompressible allows for the usage of the equation (1): , (1),(2)
where V is the flow velocity, q is the average dynamic pressure, ⍴ is the computed average density of air, P
ambient
is the ambient pressure, R is gas constant, and T
is the ambient temperature. With the flow velocity calculated, equation (3), and (4) will be used to get the Mach number and equation (5) will be used to get the Reynolds number. , (3),(4)
(5)
Your preview ends here
Eager to read complete document? Join bartleby learn and gain access to the full version
- Access to all documents
- Unlimited textbook solutions
- 24/7 expert homework help
6
Table. 3. Data Calculated for Various Attributes from Varying RPM in the Wind Tunnel
Data Point
Motor Speed
[RPM]
Average
Dynamic
Pressure [psi]
Velocity [ft/s]
Reynolds Number
per Unit Length
[1/ft]
Mach Number
1
400
0.00457672
2.01634741
1.19E+04
1.78E-03
2
500
0.00751837
2.58434163
1.52E+04
2.28E-03
3
600
0.01134455
3.17454547
1.87E+04
2.81E-03
4
700
0.01603178
3.77379949
2.22E+04
3.33E-03
5
800
0.0213614
4.3561501
2.57E+04
3.85E-03
6
900
0.02780254
4.9697003
2.93E+04
4.39E-03
7
1000
0.03469222
5.5514194
3.27E+04
4.91E-03
8
1100
0.04229269
6.1294376
3.61E+04
5.42E-03
9
1200
0.05129694
6.75046515
3.98E+04
5.97E-03
10
1300
0.05849267
7.20839688
4.25E+04
6.37E-03
11
1400
0.06901303
7.82985172
4.61E+04
6.92E-03
Based on this data, a comparison was made between the properties and the varying RPM.
The findings are shown in the graphs below.
7
Figure 2. 2-Dimensional Graphs for Computed Quantities against increasing Motor Speed.
Plot 1 (top left), Plot 2 (top right), Plot 3 (Bottom left), Plot 4 (Bottom right) depicting Dynamic Pressure, Flow Velocity, Reynolds number per unit length, and Mach number against increasing Motor Speed.
As a general trend, as the RPM increases the specific attribute also increases. The increase is linear for all attributes except dynamic pressure where the increase is exponential. Also, these graphs can only give an approximation for a given motor speed setting. This is because of many reasons. One such reason is that these values are computed using quantities that
are user (pressure values) and environment (temperature values) dependent that will provide inconsistent results even when the same test is repeated. Another reason that the collected data is an approximation can be seen from the plots as the data measured shows some deviation from the true linear data one can expect to see. This could be due to several factors such as a sudden change in the room pressure, and such as someone walking in front of the intake tunnel.
8
3.3. Static and Total Pressure Variation
To compare the variation in the static pressure from the different probe locations, the percent difference of each static pressure from the average static pressure with the difference normalized by the average dynamic pressure was calculated. This static pressure variation (
SPV
i
)
for each static pressure probe is given by SPV
i
[
%
]
=
100%
∗(
PS
i
−
PS
avg
)/
q
actual
where PS
i
is the static pressure of the i
th
static probe on the rake (i.e., S1 to S5) and SPV
i
is the static pressure variation for the i
th
static pressure tap. The graph below shows the static pressure variation on the static pressure probes. Figure 2. Scatterplot Depicting the Trends from the Static Pressure Probes.
(description)
Your preview ends here
Eager to read complete document? Join bartleby learn and gain access to the full version
- Access to all documents
- Unlimited textbook solutions
- 24/7 expert homework help
9
Figure 3. Scatterplot Depicting the Trends from the Total Pressure Probes
As dynamic pressure increased the SPV values had a normal distribution on the scatterplot, whereas as on the TPV scatterplot, the points stayed towards the lower limit but did not increase with dynamic pressure. 3.4. Variation of the Total and Dynamic Pressures
Aside from the slight pressure losses through the converging section, the pressure measured using the manometer and the pressure measured using the Omega transducer should be
approximately equal to the actual dynamic pressure in the test section of the tunnel. The table below shows the values of the percent differences between different pressure data attributes. Table. 4. Percent Differences between Different types of Pressures
10
Data
Point Motor
Speed
[RPM]
Actual
Dynamic
Pressure
[psi] Omega
Transmitter
delta P
[dpsi]
% Difference
(Dynamic and
Omega
Pressure)
Manome
ter delta
P [dpsi]
% Difference
(Dynamic,
Manometer
Pressure)
1
400
4.58E-03
5.49E-03
1.81E+01
5.78E-03
2.32E+01
2
500
7.52E-03
9.02E-03
1.82E+01
9.39E-03
2.21E+01
3
600
1.13E-02
1.33E-02
1.59E+01
1.30E-02
1.36E+01
4
700
1.60E-02
1.84E-02
1.38E+01
1.88E-02
1.59E+01
5
800
2.14E-02
2.45E-02
1.37E+01
2.46E-02
1.41E+01
6
900
2.78E-02
3.14E-02
1.22E+01
3.18E-02
1.34E+01
7
1000
3.47E-02
3.90E-02
1.17E+01
3.97E-02
1.35E+01
8
1100
4.23E-02
4.74E-02
1.14E+01
4.77E-02
1.20E+01
9
1200
5.13E-02
5.69E-02
1.04E+01
5.71E-02
1.07E+01
10
1300
5.85E-02
6.57E-02
1.16E+01
6.65E-02
1.28E+01
11
1400
6.90E-02
7.66E-02
1.04E+01
7.80E-02
1.22E+01
11
0.00E+00
2.00E-02
4.00E-02
6.00E-02
8.00E-02
1.00E-01
0.00E+00
1.00E-02
2.00E-02
3.00E-02
4.00E-02
5.00E-02
6.00E-02
7.00E-02
8.00E-02
f(x) = 0.91 x − 0
Linear fit for dynamic pressure and Omega Transducer Omega Pressure Transmitter P [dpsi] Dynamic Pressure (lbf/ft2)
Figure 3. This graph depicts how dynamic pressure changes as omega pressure transmitter is increased. The equation for the linear fit is also given above. When the actual dynamic pressure to the omega transmitter delta pressure was compared,
it was found that the omega transmitter delta pressure was greater than the actual dynamic pressure for each data point. This might be due to various elements in the wind tunnel room disturbing the flow slightly, therefore altering the readings slightly. Also, the % Difference (Dynamic and Omega Pressure) generally tended to decrease as RPM increased which highlights
that error decreases as RPM increases. When the manometer delta pressure and the actual dynamic pressure were compared, it was found that % difference also decreased as RPM increased but as seen with the omega transmitter delta pressure, the manometer delta pressure was greater than the actual dynamic pressure for each data point.
Your preview ends here
Eager to read complete document? Join bartleby learn and gain access to the full version
- Access to all documents
- Unlimited textbook solutions
- 24/7 expert homework help
12
4. CONCLUSIONS The average total and static pressure were successfully discovered through experimentation methods, using a pressure rake in a subsonic wind tunnel. Average dynamic pressure was then calculated, using the collected data. A modified Bernoulli’s equation was used to calculate actual velocity, Mach, and inverse Reynolds numbers with ease. These quantities appeared to be linear. The variations of static and total pressure were calculated with a significant difference of 10 to 23%. Future tests should include more stable conditions with minimized flow disruption and a predetermined wait-time to record measurements. Standard conditions would ensure that the error is minimized from the outside factors. Additionally, it will be of benefit to record more points, either in smaller increments or in a wider range. The former would provide more precise data for the current range, while an expanded range would provide insight into the behavior of the pressure measurements at lower or higher RPM. Regardless, more data would result in a more accurate analysis, but would consume more time to implement. Alternatively, different devices for pressure data collection can be used to check which one yields less error. In the future, that can be a significant source of error, if a pressure rake is used, instead of a more sophisticated and error-resistant device.
13
5. REFERENCES
[1] “Experiment #1: Wind Tunnel Calibration,” Laboratory Writeup for AE 460, University of
Illinois at Urbana-Champaign, 2022.
6. APPENDIX
APPENDIX A: SAMPLE CALCULATIONS
ALL THE EQUATIONS USED 1. Actual Velocity Calculation
V = Actual velocity [ft/s]
q = Dynamic pressure [psi]
ρ = Density [lbf/ft
3
]
V = (2*3.47E-02 psi)/()
2. Density Calculation
ρ = Density [lbf/ft
3
]
P
ambient
= Ambient pressure [psi]
R = Gas constant [ft*lbf / (slug*(°R))]
T = Temperature [°R]
3. Reynolds Number Calculation
Re = Reynolds number
14
ρ = Density [lbf/ft
3
]
V = Actual velocity [ft/s]
μ = Atmospheric viscosity [lbf*s/ft
2
]
Re = (? lbf/ft
3
)*(5.5514194 ft/s)/(3.737E-07 lbf*s/ft
2
) = 4. Mach Number Calculation
M = Mach number V = Actual velocity [ft/s]
a = Atmosphere speed of sound [ft/s]
M = (5.5514194 ft/s) / (1125.33 ft/s) = 4.91E-03
5. Atmosphere Speed of Sound Calculation
a = Atmosphere speed of sound [ft/s]
γ = Heat capacity ratio
R = Gas constant [ft*lbf / (slug*(°R))]
T = Temperature [°R]
6. Total Pressure Variation for the i
th
Static Pressure Probe
TPV
i
= Total pressure variation for the i
th
static pressure probe
P
0, i = Total pressure of the i
th total probe on the rake [psi]
P
0, avg = Average total pressure of a total probe on the rake [psi]
q
avg
= Actual dynamic pressure from the rake [psi]
Your preview ends here
Eager to read complete document? Join bartleby learn and gain access to the full version
- Access to all documents
- Unlimited textbook solutions
- 24/7 expert homework help
15
7. Static Pressure Variation for the i
th
Static Pressure Tap
SPV
i
= Static pressure variation for the i
th
static pressure tap
P
S, i = Static pressure of the i
th
static probe on the rake [psi]
P
S, avg = Average static pressure of a static probe on the rake [psi]
q
avg
= Actual dynamic pressure from the rake [psi]
8. The Uncertainty in the Actual Velocity
U
V
= Uncertainty of actual velocity
∂V
∂ p
0
= Partial derivative of actual velocity with respect to total pressure
U
p0
= Uncertainty of total pressure
∂V
∂ p s
= Partial derivative of actual velocity with respect to static pressure
U
ps
= Uncertainty of static pressure
∂V
∂ ρ
= Partial derivative of actual velocity with respect to density
U
ρ
= Uncertainty of density
9. The Uncertainty in the Density
U
ρ
= Uncertainty of density
16
∂ ρ
∂ pamb
= Partial derivative of density with respect to ambient pressure
U
p amb
= Uncertainty of ambient pressure
∂ ρ
∂R
= Partial derivative of density with respect to gas constant
U
R
= Uncertainty of gas constant
∂ ρ
∂T amb
= Partial derivative of density with respect to ambient temperature
U
T amb
= Uncertainty of ambient temperature
10. The Uncertainty in the Pressure
U
p
= Uncertainty of pressure
U
p single
= Uncertainty of pressure from a single source
n = Number of pressures
APPENDIX B: RAW DATA
Motor Speed [RPM]
Actual Velocity [ft/s]
Actual Velocity
Uncertainty [ft/s]
Percent Uncertainty
(%)
400
2.01634741
±1.4762796936638
73.2155424
500
2.58434163
±1.15426206841032
44.6636798
600
3.17454547
±0.94368662259631
29.7266689
700
3.77379949
±0.79981581780645
21.193914
800
4.3561501
±0.70086305174509
16.0890474
900
4.9697003
±0.62527646501277
12.5817741
1000
5.5514194
±0.57280369805835
10.3181485
1100
6.1294376
±0.53442834072577
8.71904366
1200
6.75046515
±0.50501513644787
7.48119019
1300
7.20839688
±0.48964009481017
6.79263508
17
1400
7.82985172
±0.47575633960346
6.07618582
APPENDIX C: GROUP MEMBER CONTRIBUTIONS Laboratory Note #1
Group Member
Contribution to Technical Note
Ani Saini
Completed all the analysis to prepare plots and tables and implemented them in the report. Also completed the handwritten uncertainty analysis and created a formula in excel to get each uncertainty (1-6). Srinu Rayudu
Authored introduction as well as authored results section; Authored data analysis and discussion. Margarita Kuzmanova
Prepared conclusions and all appendices
Your preview ends here
Eager to read complete document? Join bartleby learn and gain access to the full version
- Access to all documents
- Unlimited textbook solutions
- 24/7 expert homework help
18
Related Documents
Related Questions
Can you help with both please.
arrow_forward
O NWP Assessment Builder UI Appl X
O NWP Assessment Player UI Appli X
+
->
A education.wiley.com/was/ui/v2/assessment-player/index.html?launchld=4599c668-aabf-4aa6-a299-d14a1c37f643#/question/13
E
E Apps
Q Hydrogeology Flas...
3 That Time I Got Rei...
MATLAB Online R2...
Chem Exam 2 Flash...
COP2030 Module 3..
6 SSMagon - ME137L...
S Easy to use Online...
E Reading list
>>
E Chapter 4 Homework
Question 14 of 14
-/1
View Policies
Current Attempt in Progress
As shown in the figure, a 300-ft tank contains 25 lb of H2O initially at 30 lbf/in?. The tank is connected to a large steam line carrying
steam at 200 Ibf/in?, 450°F. Steam flows into the tank through a valve until the tank pressure reaches p2 = 120 lbf/in? and the
temperature is 400°F, at which time the valve is closed.
Steam at
200 lbf/in.².
450°F
Tank
Valve
(1)
Initially:
30 lbfin.?, mı = 25 lb
|(2)
Finally:
Ibfin.?, 400°F.
P2
Determine the amount of mass that enters the tank, in Ib, and the heat transfer to the tank from its…
arrow_forward
Question 7
The following formulas are commonly used by engineers to predict the lift and drag of an airfoil:
where L and Dare the lift and drag forces, V is the airspeed, S is the wing span, is the air density, and CL and CD are the lift and drag coefficients. Both CL and CD depend on α , the angle of attack, the angle between the relative air velocity and the airfoil’s chord line.
Wind tunnel experiments for a particular airfoil have resulted in the following formulas.
where α is in degrees.
arrow_forward
i need clear ans by hand and solve very very fast in 20 min and thank you | ᴅʏʙᴀʟᴀ ?✨؛
arrow_forward
QUESTION 7
A model tow-tank test is conducted on a bare hull model at the model design
speed in calm water. Determine the effective horsepower (hp) for the ship,
including appendage and air resistances. The following parameters apply to the
ship and model:
Ship
1,100
Model
Length (ft)
Hull Wetted Surface Area (ft2)
Speed (knots)
30
250,000
15
Freshwater
Water
Seawater 50°F
70°F
Projected Transverse Area (ft²)
Cair
7,500
0.875
Appendage Resistance (% of bare hull)
10%
Hull Resistance (Ibf)
20
arrow_forward
this is a practice problem, not a graded assignment
arrow_forward
Class X
Class
k Ingrid x k Ingrid x C Auto: X © Shop X
docs.google.com/document/d/1DUa0kRhTJwq|pEZJc3GcnvVhgTU09aBcA54WqeY7hMI/edit
Supreme Court Cas... e New Tab
← → C D
sd206.org bookmarks
E
A T
Ingrid Lyons - Chapter fi...
File Edit View Insert Format Tools Extens
100
I I
I
100%
I
I
Normal text ▼
I 100 I |
Ingrid x
Auto Orientation
Radeke
I
I
~ Messe X
Arial
2
2TO
k
Y
Domi X
I I 3 I
I
с 1 х
14 +
I I I 4
G hown x
I
O
I |
Chapter review questions.
1. What noise level is too high and can hurt your ears?
2. What are the Safety Data Sheets?
3. If you get something in your eye what should you do?
I
TextNxb Home X
5
TURN IN
I I | I
I I 6
+
Share
I I I
Ar
7
19
☐
31
>
X
:
arrow_forward
Fluid Mechanics Problem:
Part d) please. Thanks
arrow_forward
3. Problem
Estimate the frictional resistance Rp for a container ship using the ITTC 1957 model-ship correlation line
Equation (2):
0.075
CF
[ log,,(Re) – 21
The ship has the following particulars:
Full scale ship data
length between perpendiculars Lep
length in waterline
length over wetted surface
195.40 m
Lwz
Los
For the wetted surface S you can use the following
formula by Kristensen and Lützen (2012) derived
for container ships.
200.35 m
205.65 m
breadth
B
29.80 m
draft
T
10.10 m
37085.01 m3
S = 5 + Lw. T
0.995
displacement
design speed
Again, use the most up-to-date ITTC water properties sheet for density and kinematic viscosity.
V
21.00 kn
arrow_forward
The red questions please q4 and q5 and q7
arrow_forward
Lab 2-Measurement Asynch - Tagged.pdf
Page 4 of 7
?
Part I: Taking Measurements & Estimating Uncertainties for a single measurement
www.stefanelli.eng.br
The mass of the object is_
0
i
Parts on a tripie peam palance
0
0
10 20 30
1
100
2 3
40
200
4
+/-
50 60 70
5
300
7
400
80
Qv Search
8
90
9
500
100
9
10 g
www.stefanelli.eng.br
arrow_forward
Question 4.4
A core was mounted in a gas permeameter to measure permeability, and the
following laboratory data are obtained from the experiment:
Diameter of the core = 2.59 cm
- Length of the core = 6.03 cm
- Gas viscosity = 0.0148 cP
q [cm/s]
Р, [КРa]
P, [kPa]
13.09
65.4
13.5
7.91
44.6
11.2
4.12
25.3
6.4
3.23
19.4
4.1
Determine the gas permeability and equivalent liquid permeability of the core
using the above data (in Darcy units).
arrow_forward
Select two saturated and two unsaturated samples of air from the dataset of pressure and temperature given below:
Pressure (mb): 10, 20, 30
Temperature (°C): 10, 20, 30
Let A and B be two air samples, where A: (T=30°C, P=25 mb) and B: (T=30°C, P=30 mb). For each sample, determine the following:
a. Saturation vapor pressure
b. Dew point
c. Relative humidity
d. If samples A and B were cooled to 15°C. What would be their relative humidity? What would be their dew point temperature?
arrow_forward
O NWP Assessment Builder UI Appl X
O NWP Assessment Player UI Appli X
+
->
A education.wiley.com/was/ui/v2/assessment-player/index.html?launchld=4599c668-aabf-4aa6-a299-d14a1c37f643#/question/2
E
E Apps
Q Hydrogeology Flas..
3 That Time I Got Rei...
MATLAB Online R2..
Chem Exam 2 Flash..
СОР2030 Мodule 3...
A SSMagon - ME137L...
S Easy to use Online...
E Reading list
>>
E Chapter 4 Homework
Question 3 of 14
>
0/1
Your answer is incorrect.
Refrigerant 134a enters a well-insulated nozzle at 200 Ibf/in.?, 140°F, with a velocity of 120 ft/s and exits at 50 Ibf/in.? with a velocity
of 1500 ft/s.
For steady-state operation, and neglecting potential energy effects, determine the temperature, in °F, and the quality of the refrigerant
at the exit.
T2 =
i
72.78
°F
X2 =
i
75.9019
eTextbook and Media
Hint
7:31 PM
O Type here to search
30°C Partly cloudy
22/09/2021
D
arrow_forward
7) Give two disadvantages of empirical thermometers.
8) Consider two liquids, A and B. with temperatures Te > TA. The two objects are put into thermal contact for a
time period. Without just saying 'heat flows from hot to cold' how would you prove to someone that a quantity of
heat flowed from B to A. (think of James Joule's experiments)
9) If the temperature of the sun were to suddenly double, by what multiplicative factor would the thermal radiation
change ? Show Work
arrow_forward
Thermodynamics question. please help
(2nd Attachment is the table question B is referring to)
arrow_forward
SEE MORE QUESTIONS
Recommended textbooks for you
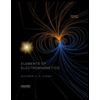
Elements Of Electromagnetics
Mechanical Engineering
ISBN:9780190698614
Author:Sadiku, Matthew N. O.
Publisher:Oxford University Press
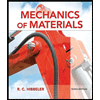
Mechanics of Materials (10th Edition)
Mechanical Engineering
ISBN:9780134319650
Author:Russell C. Hibbeler
Publisher:PEARSON
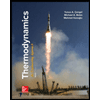
Thermodynamics: An Engineering Approach
Mechanical Engineering
ISBN:9781259822674
Author:Yunus A. Cengel Dr., Michael A. Boles
Publisher:McGraw-Hill Education
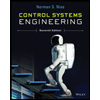
Control Systems Engineering
Mechanical Engineering
ISBN:9781118170519
Author:Norman S. Nise
Publisher:WILEY
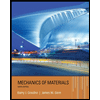
Mechanics of Materials (MindTap Course List)
Mechanical Engineering
ISBN:9781337093347
Author:Barry J. Goodno, James M. Gere
Publisher:Cengage Learning
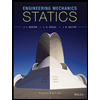
Engineering Mechanics: Statics
Mechanical Engineering
ISBN:9781118807330
Author:James L. Meriam, L. G. Kraige, J. N. Bolton
Publisher:WILEY
Related Questions
- Can you help with both please.arrow_forwardO NWP Assessment Builder UI Appl X O NWP Assessment Player UI Appli X + -> A education.wiley.com/was/ui/v2/assessment-player/index.html?launchld=4599c668-aabf-4aa6-a299-d14a1c37f643#/question/13 E E Apps Q Hydrogeology Flas... 3 That Time I Got Rei... MATLAB Online R2... Chem Exam 2 Flash... COP2030 Module 3.. 6 SSMagon - ME137L... S Easy to use Online... E Reading list >> E Chapter 4 Homework Question 14 of 14 -/1 View Policies Current Attempt in Progress As shown in the figure, a 300-ft tank contains 25 lb of H2O initially at 30 lbf/in?. The tank is connected to a large steam line carrying steam at 200 Ibf/in?, 450°F. Steam flows into the tank through a valve until the tank pressure reaches p2 = 120 lbf/in? and the temperature is 400°F, at which time the valve is closed. Steam at 200 lbf/in.². 450°F Tank Valve (1) Initially: 30 lbfin.?, mı = 25 lb |(2) Finally: Ibfin.?, 400°F. P2 Determine the amount of mass that enters the tank, in Ib, and the heat transfer to the tank from its…arrow_forwardQuestion 7 The following formulas are commonly used by engineers to predict the lift and drag of an airfoil: where L and Dare the lift and drag forces, V is the airspeed, S is the wing span, is the air density, and CL and CD are the lift and drag coefficients. Both CL and CD depend on α , the angle of attack, the angle between the relative air velocity and the airfoil’s chord line. Wind tunnel experiments for a particular airfoil have resulted in the following formulas. where α is in degrees.arrow_forward
- i need clear ans by hand and solve very very fast in 20 min and thank you | ᴅʏʙᴀʟᴀ ?✨؛arrow_forwardQUESTION 7 A model tow-tank test is conducted on a bare hull model at the model design speed in calm water. Determine the effective horsepower (hp) for the ship, including appendage and air resistances. The following parameters apply to the ship and model: Ship 1,100 Model Length (ft) Hull Wetted Surface Area (ft2) Speed (knots) 30 250,000 15 Freshwater Water Seawater 50°F 70°F Projected Transverse Area (ft²) Cair 7,500 0.875 Appendage Resistance (% of bare hull) 10% Hull Resistance (Ibf) 20arrow_forwardthis is a practice problem, not a graded assignmentarrow_forward
- Class X Class k Ingrid x k Ingrid x C Auto: X © Shop X docs.google.com/document/d/1DUa0kRhTJwq|pEZJc3GcnvVhgTU09aBcA54WqeY7hMI/edit Supreme Court Cas... e New Tab ← → C D sd206.org bookmarks E A T Ingrid Lyons - Chapter fi... File Edit View Insert Format Tools Extens 100 I I I 100% I I Normal text ▼ I 100 I | Ingrid x Auto Orientation Radeke I I ~ Messe X Arial 2 2TO k Y Domi X I I 3 I I с 1 х 14 + I I I 4 G hown x I O I | Chapter review questions. 1. What noise level is too high and can hurt your ears? 2. What are the Safety Data Sheets? 3. If you get something in your eye what should you do? I TextNxb Home X 5 TURN IN I I | I I I 6 + Share I I I Ar 7 19 ☐ 31 > X :arrow_forwardFluid Mechanics Problem: Part d) please. Thanksarrow_forward3. Problem Estimate the frictional resistance Rp for a container ship using the ITTC 1957 model-ship correlation line Equation (2): 0.075 CF [ log,,(Re) – 21 The ship has the following particulars: Full scale ship data length between perpendiculars Lep length in waterline length over wetted surface 195.40 m Lwz Los For the wetted surface S you can use the following formula by Kristensen and Lützen (2012) derived for container ships. 200.35 m 205.65 m breadth B 29.80 m draft T 10.10 m 37085.01 m3 S = 5 + Lw. T 0.995 displacement design speed Again, use the most up-to-date ITTC water properties sheet for density and kinematic viscosity. V 21.00 knarrow_forward
- The red questions please q4 and q5 and q7arrow_forwardLab 2-Measurement Asynch - Tagged.pdf Page 4 of 7 ? Part I: Taking Measurements & Estimating Uncertainties for a single measurement www.stefanelli.eng.br The mass of the object is_ 0 i Parts on a tripie peam palance 0 0 10 20 30 1 100 2 3 40 200 4 +/- 50 60 70 5 300 7 400 80 Qv Search 8 90 9 500 100 9 10 g www.stefanelli.eng.brarrow_forwardQuestion 4.4 A core was mounted in a gas permeameter to measure permeability, and the following laboratory data are obtained from the experiment: Diameter of the core = 2.59 cm - Length of the core = 6.03 cm - Gas viscosity = 0.0148 cP q [cm/s] Р, [КРa] P, [kPa] 13.09 65.4 13.5 7.91 44.6 11.2 4.12 25.3 6.4 3.23 19.4 4.1 Determine the gas permeability and equivalent liquid permeability of the core using the above data (in Darcy units).arrow_forward
arrow_back_ios
SEE MORE QUESTIONS
arrow_forward_ios
Recommended textbooks for you
- Elements Of ElectromagneticsMechanical EngineeringISBN:9780190698614Author:Sadiku, Matthew N. O.Publisher:Oxford University PressMechanics of Materials (10th Edition)Mechanical EngineeringISBN:9780134319650Author:Russell C. HibbelerPublisher:PEARSONThermodynamics: An Engineering ApproachMechanical EngineeringISBN:9781259822674Author:Yunus A. Cengel Dr., Michael A. BolesPublisher:McGraw-Hill Education
- Control Systems EngineeringMechanical EngineeringISBN:9781118170519Author:Norman S. NisePublisher:WILEYMechanics of Materials (MindTap Course List)Mechanical EngineeringISBN:9781337093347Author:Barry J. Goodno, James M. GerePublisher:Cengage LearningEngineering Mechanics: StaticsMechanical EngineeringISBN:9781118807330Author:James L. Meriam, L. G. Kraige, J. N. BoltonPublisher:WILEY
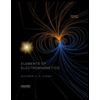
Elements Of Electromagnetics
Mechanical Engineering
ISBN:9780190698614
Author:Sadiku, Matthew N. O.
Publisher:Oxford University Press
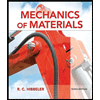
Mechanics of Materials (10th Edition)
Mechanical Engineering
ISBN:9780134319650
Author:Russell C. Hibbeler
Publisher:PEARSON
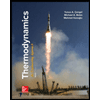
Thermodynamics: An Engineering Approach
Mechanical Engineering
ISBN:9781259822674
Author:Yunus A. Cengel Dr., Michael A. Boles
Publisher:McGraw-Hill Education
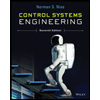
Control Systems Engineering
Mechanical Engineering
ISBN:9781118170519
Author:Norman S. Nise
Publisher:WILEY
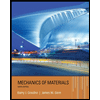
Mechanics of Materials (MindTap Course List)
Mechanical Engineering
ISBN:9781337093347
Author:Barry J. Goodno, James M. Gere
Publisher:Cengage Learning
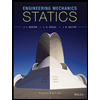
Engineering Mechanics: Statics
Mechanical Engineering
ISBN:9781118807330
Author:James L. Meriam, L. G. Kraige, J. N. Bolton
Publisher:WILEY