hw2
docx
keyboard_arrow_up
School
Pennsylvania State University *
*We aren’t endorsed by this school
Course
243
Subject
Mechanical Engineering
Date
Dec 6, 2023
Type
docx
Pages
11
Uploaded by JusticeAlbatrossMaster898
Chinmayee Gosain ME 410 Home work 2 QUESTION 1 A cold fluid is flowing over a hot flat plate with a length of 1.2 meters. For this system, an expression for convective heat transfer coefficient (with units of W m2 -K) has been predetermined (hx = -7x 2 + 0.1x + 5).
Part A: Plot the average and local heat transfer coefficients for the plate as a function of x. Use 5 points to display your results.
Part B: If the temperature of the fluid and the plate are constant values of T∞ = 20 °C and Ts = 80 °C, respectively. What are the average and local heat fluxes from the plate to the fluid across the flat plate? Again, use 5 different points along the plate.
ANSWER
Part A: To plot the average and local heat transfer coefficients as a function of x, you can use the given expression for the convective heat transfer coefficient ℎ
x = −7x
2 + 0.1x +5. We will calculate the average and local values at five different points along the plate.
Let's calculate and plot the values at x
=0.0,0.3,0.6,0.9,1.2 meters.
1.
x=0.0 :
ℎ
0 = −7 (0.0)
2 + 0.1 (0.0) + 5 = 5.0 W/m
2
K 2.
x=0.3 :
h
0.3
= −7(0.3)
2
+0.1 (0.3) + 5 = 4.46 W
/
m
2
K
3.
x=0.6
ℎ
0.6
=−7(0.6)
2
+0.1 (0.6) + 5 = 3.62 W
/m
2
K
4.
x
=0.9 m
:
ℎ
0.9
=−7(0.9)
2
+0.1 (0.9) + 5 = 2.48 W
/
m
2
K
5.
x
=1.2 m
:
ℎ
1.2
=−7(1.2)
2
+0.1(1.2) + 5 = 1.04 W
/
m
2
K
In the plot below x axis is x with m as units and y is h
x
with W/m
2
K as unit
Now, let's calculate the average heat transfer coefficient h
avgs
by taking the integral of h
x
over the length of the plate (0 to 1.2 meters) and dividing by the plate length (1.2 meters):
h
avg
= 1/1.2 m ∫
0
1.2
( −7 x
2
+ 0.1
x + 5 ) dx
This can be calculated numerically. The integral evaluates to approximately 2.89 W/m²-K
Part B:
Calculate Heat Flux and Plot the Graph
In Part B, we want to calculate the local and average heat flux from the plate to the fluid. The formula for the heat flux (
q
) at each point x
is given by:
Q
x
= h
x ⋅ A ⋅ Δ
T
Where:
h
x
is the local heat transfer coefficient at the specific x
position.
A
is the surface area (considering only one side of the plate).
Δ
T
is the temperature difference between the plate and the fluid.
For the purpose of these calculations, we'll assume a unit width for the plate (
=1
�
2
�
A
=1 m
2) as mentioned in Part A.
Given:
Plate temperature ( T
s ) = 80 °C = 353.15 K
Fluid temperature (
T
∞
) = 20 °C = 293.15 K
Now, we can calculate the local heat flux (
q
x
) at each point �
x
along the plate:
1.
At x
=0.0 m
:
Q
0
= 5.0 W
/
m
2−
K
⋅
1 m
2 ⋅ ( 353.15 K − 293.15 K ) = 5.0 × 60 = 300 W
2.
At x
=0.3 m
: Q 0.3 = 4.46 W
/
m
2−
K
⋅
1 m
2
⋅ ( 353.15 K − 293.15 K ) = 4.46×60 = 267.6 W
3.
At x
=0.6 m
:
Q
0.6
=3.62 W
/
m
2−
K
⋅
1 m
2
⋅ ( 353.15
K − 293.15
K ) = 3.62×60 = 217.2 W
4.
At x
=0.9 m
: Q
0.9
=2.48 W
/
m
2−
K
⋅
1 m
2
⋅ ( 353.15
K − 293.15
K ) = 2.48×60 = 148.8 W
5.
At x
=1.2 m
: Q
1.2
=1.04 W
/
m
2−
K
⋅
1 m
2
⋅
(353.15
K
−293.15
K
) = 1.04×60 = 62.4 W
Calculated the local heat flux (
qx
) at each point along the plate. These values represent the local heat flux from the plate to the fluid at various positions along the plate.
To find the average heat flux (
avg
�
q
avg), you can calculate the mean of these local heat flux values:
q
avg
= q
x
0
+ q
x
0.3 + qx
0.6
+ q
x
0.9
+ q
x
1.2
/5
Plugging in the values:
Q
avg = 5.0W/m
2 +4.46 W/m
2 + 3.62 W/m
2 + 2.48 W/m
2 + 1.04 W/m
2 / 5 = 3.52 W/m
2
So, the average heat flux (
q
avg
) from the plate to the fluid across the flat plate is approximately 3.52 W/m
2
QUESTION 2
Part A:
Your preview ends here
Eager to read complete document? Join bartleby learn and gain access to the full version
- Access to all documents
- Unlimited textbook solutions
- 24/7 expert homework help
To determine the average convection coefficient (
ℎ
avg
), we need to integrate the local convection coefficients (
h
lam and h
turb
) over the length of the plate and divide by the plate length. The formulas for the local convection coefficients are provided as h
lam
(x) = C
lam
x
−0.6 and h
turb
(
x
) =
C
turb
x
−0.3
The average convection coefficient is given by:
h
avg=
1/L ∫
L
0
h
(
x
) dx
Now, for this problem, we have two different local convection coefficients, h
lam and h
turb
. So we'll
need to calculate two separate average convection coefficients, ℎ
avg_
and h
avg_turb, using the corresponding local convection coefficients:
1.
Average convection coefficient for the laminar region:
h
avg_lam = 1/L ∫
L
0
h
lam
( x ) dx = 1/L ∫
L
0
C
lam
x
−0.6 dx
2.
Average convection coefficient for the turbulent region:
ℎ
avg_turb= 1/L ∫
L
0
h
turb
( x ) dx = 1/L ∫
L
0
C
lam
x
−0.3 dx
Laminar Region:
Given the formula for the local convection coefficient in the laminar region is ℎ
lam
(x) = C
lam
x
-0.6 , and you have a one-meter-long plate (
L =1m),
we can calculate h
avg_lam
for the laminar region as follows:
h
avg_lam = 1/L
∫
L
0
h
lam
(
x
) dx
Substituting the formula for h
lam (x
):
h
avg_lam = 1/1m ∫
1m
0
C
lam
x
-0.6
dx
Now, we can integrate C
lam
x
-0.6
with respect to x
:
h
avg_lam
=
C
lam/1m [ x
−0.6+1
/ 0.6+1 ]
1m
0 m
Simplifying:
ℎ
avg _lam=
C
lam/1m [
x
0.4
/0.4]
0
1m
Now, calculate h
avg_lam
:
ℎ
avg_lam = C
lam /0.4 [1
0.4
−0
0.4
]
h
avg_lam = C
lam/0.4 [1−0]
ℎ
avg_lam=
C
lam/0.4
Turbulent Region:
Given the formula for the local convection coefficient in the turbulent region is h
turb(
x
) = C
turb
x
−0.3
, we can calculate h
avg_turb for the turbulent region:
h
avg_lam = 1/L
∫
L
0
h
turb
(
x
) dx
Substituting the formula for h
turb (x
):
h
avg_lam = 1/1m ∫
1m
0
C
turb
x
-0.3
dx
Now, we can integrate C
turb
x
-0.3
with respect to x
:
h
avg_lam
=
C
turb/1m [ x
−0.3+1
/ -0.3+1 ]
1m
0 m
Simplifying:
ℎ
avg _turb = C
turb / 1m [ x
0.7
/0.7 ]
0
1m
Now, calculate h avg_turb
h
avg_turb = C
turb/0.7 [1
0.7
−0
0.7
]
avg_turb= C
ℎ
turb /0.7 [ 1
0.7
−0
0.7
] h
avg_turb=
C
turb
/0.7 [1−0]
h
avg_turb=
C
turb
/ 0.7 Part B: We will calculate the local convection coefficients (h_lam and h_turb) and the average convection coefficient (h_avg) as a function of x using the given equations for h_lam(x) and h_turb(x) and the provided values of C_lam and C_turb:
C_lam = 5.6 W/m^2∙K
C_turb = 65 W/m^1.7∙K
We'll calculate h_lam and h_turb separately for their respective regions and then calculate h_avg for each value of x.
1.
For the laminar portion (0 ≤ x ≤ 0.4 m):
lam(x)=C
ℎ
lam
* x
-0.6
lam(x)= 5.6 * x
ℎ
-0.6
2.
For the turbulent portion (0.4 m ≤ x ≤ 1 m):
turb (x) = C
ℎ
turb
* x
-0.3
turb (x) = 65 * x
ℎ
-0.3
To calculate the average convection coefficient (h_avg) as a function of x, we need to consider the lengths of each region:
L_lam (length of the laminar portion) = x_c = 0.4 m
L_turb (length of the turbulent portion) = L - x_c = 1 m - 0.4 m = 0.6 m
Now, we can calculate h_avg for each value of x:
For 0 ≤ x ≤ 0.4 m (Laminar region): avg(x) = 1/0.4 ∫
ℎ
0.4
0
.5.6
* x^-0.6 dx
For 0.4 m ≤ x ≤ 1 m (Turbulent region): h
avg(
x
)=1/0.6 ∫ 1
0.4
65.x
-0.3
dx
c. 1.
Laminar Flow Region (0 < x < x_c = 0.4 m):
Local convection coefficient, h_lam, decreases with x.
Heat transfer is less effective as you move further along the plate.
2.
Turbulent Flow Region (x_c = 0.4 m < x < 1 m):
Local convection coefficient, h_turb, increases with x.
Heat transfer becomes more effective downstream on the plate.
3.
Transition Point (x_c = 0.4 m):
Marking the transition from laminar to turbulent flow.
Signifies a notable change in heat transfer characteristics.
4.
Average Convection Coefficient (h_avg):
A weighted average of h_lam and h_turb.
H_avg curve shows a significant increase around x_c due to the transition to turbulent flow.
The exact values of coefficients depend on C_lam, C_turb, plate length, and fluid properties. For precise observations, numerical values need to be substituted into the expressions and plotted to visualize the changes along the plate. The transition from laminar to turbulent flow significantly impacts heat transfer.
Your preview ends here
Eager to read complete document? Join bartleby learn and gain access to the full version
- Access to all documents
- Unlimited textbook solutions
- 24/7 expert homework help
QUESTION 3 Question 3.
Average convection coefficients were experimentally measured for a flat plate where the average
Nusselt
number obeys the following form (
𝑁U
= 𝐶Re
m
Pr
?
). When length of the flat plate is 0.5 m, these were the results that were obtained. (for a fluid velocity of 5 m/s, ℎ
?
= 20 W / m 2-K and for a fluid velocity of 10 m/s, ℎ
?
= 34 W /m 2-K.)
Part (A) What is the average convection coefficient if the plate is changed to 1 m in length and the fluid velocity is 15 m/s?
Part (B) What is the average convection coefficient if the plate is changed to 2 m in length and the fluid velocity is 10 m/s?
For this question, we can use the experimental data to determine the value of the constant C
and the exponent n
in the Nusselt number correlation. The Nusselt number is given in the form Nu
=
Cre
n
x
where Nu
is the Nusselt number, Re
is the Reynolds number, and x
is the characteristic
length.
Given data:
For a fluid velocity of 5 m/s and a plate length of 0.5 m, Nu
=20.
For a fluid velocity of 10 m/s and a plate length of 0.5 m, Nu
=34.
Let's first calculate the values of C
and n
using the data provided:
1.
For Re
=5 and x=0.5: 20 =
C ⋅
5
n
⋅
0.5
2.
For Re
=10 and x=0.5: 34 =
C ⋅
10
n
⋅
0.5
Now, we have two equations with two unknowns, C
and n
. We can solve this system of equations:
Equation 1: 20= C
⋅
5
n
⋅
0.5
Equation 2: 34=
C
⋅
10
n
⋅
0.5
Let's first find the values of C
and (n):
Divide Equation 2 by Equation 1: 34/20=
C
⋅
10
n
⋅
0.5 / C
⋅
5
n
⋅
0.5
C
Simplify: 17/10 = 2
n
Take the logarithm of both sides: log (17/10)=log(2
n
)
Apply the logarithm rule:
log(17/10 )= n log(2)
Now, solve for n
=log(10/17)/log(2)
Calculate n
≈0.78
Now that we have found the value of n
, we can use it to calculate C
using one of the original equations (let's use Equation 1):
20 = C
⋅
5
n
⋅
0.5
Substitute the value of n
:
20= C
⋅
5
0.78
⋅
0.5
Now, solve for C
:
C=20/0.5
⋅
5
0.78
Calculate C
≈10.17
Now that we have the values of C
and n
, we can use them to answer the two parts of the question:
Part (A): If the plate length is changed to 1 m and the fluid velocity is 15 m/s, we can use the correlation to find the average convection coefficient (
h
):
Nu = CRe
n
x
For Part (A):
Re
=15
x
=1
Nu
=10* 17 * 15
0.78
* 1
The plate length is changed to 1 m, and the fluid velocity is 15 m/s.
We already found the values of C
and n
:
C
≈10.17
n
≈0.78
Given:
Plate length (
x
) = 1 m
Fluid velocity (
Re
) = 15
We'll use the Nusselt number correlation: Nu
=
CRe
n
x
Substitute the values: Nu = 10.17 ⋅ 15
0.78
⋅
1
Now, calculate Nu
:
≈10.17 ⋅ 15
0.78 ≈ 75.19
Part (B): If the plate length is changed to 2 m and the fluid velocity is 10 m/s, we can use the correlation to find the average convection coefficient (
):
ℎ
Re
=10
x
=2
Nu = 10.17
⋅
10
0.78
⋅
2 ≈49.29
QUESTION 4 Question 4.
Present a question and solution for simple steady state convection problem based on a real-world
scenario. Clearly describe what is known and unknown about the problem. Support any inputs and assumptions surrounding your inputs like temperature ranges, material properties, or thermal
energy values with reliable sources. Conduct a sensitivity analysis of a key variable, plot the results and comment on its implications. This question requires one system diagram outlining the
problem (like we do in our class examples). Answers will be evaluated based on your ability to provide a convincing argument for practicality of your solution (i.e. why should a skeptical reviewer believe you)
Question:
In a real-world scenario, consider a simple steady-state convection problem related to cooling a computer processor with a heat sink. The processor dissipates a known amount of thermal power,
and it is essential to determine the minimum heat sink temperature required to keep the processor
within a safe temperature range. What is the minimum temperature the heat sink should maintain, and what are the critical factors influencing it?
Solution:
Problem Statement:
We are tasked with determining the minimum heat sink temperature necessary to cool a computer processor within a safe operating temperature range.
Knowns:
1.
Thermal power dissipation by the processor: Let's assume a realistic value of 95 watts, which is typical for a high-performance CPU (source: Intel Core i9-11900K Thermal Design Power
).
2.
Ambient temperature: Suppose the computer operates in a room with an ambient temperature of 25°C.
3.
Heat sink material and properties: The heat sink is made of aluminum (thermal conductivity, k = 237 W/(m∙K)).
Unknowns:
1.
Minimum heat sink temperature required to maintain the processor within the safe operating temperature.
2.
Theoretical assumptions made for simplicity.
Your preview ends here
Eager to read complete document? Join bartleby learn and gain access to the full version
- Access to all documents
- Unlimited textbook solutions
- 24/7 expert homework help
Assumptions:
1.
Steady-state conditions.
2.
One-dimensional conduction through the heat sink.
3.
Negligible heat transfer from the sides and base of the processor.
4.
Negligible heat transfer from the surroundings other than the heat sink.
5.
The processor has uniform temperature distribution.
Analysis:
To determine the minimum heat sink temperature required, we can use a simplified conduction heat transfer equation for a one-dimensional case:
Q =
kA
Δ
T
/ L
Where:
Q
is the thermal power dissipation by the processor (95 W).
k
is the thermal conductivity of aluminum (237 W/(m∙K)).
A
is the cross-sectional area of heat flow.
Δ
T
is the temperature difference between the processor and the heat sink.
L
is the thickness of the heat sink.
We want to maintain the processor within a safe temperature range, typically around 60-80°C for
most CPUs. We'll use 80°C as the maximum processor temperature:
Δ
T
=80°
C
−25°
C
=55°
C
Now, we can rearrange the equation to find the minimum temperature of the heat sink:
Minimum Heat Sink Temperature=
kAQL
+Ambient Temperature
Let's conduct a sensitivity analysis by varying the thickness of the heat sink (L) to see how it affects the minimum heat sink temperature:
Assume:
Cross-sectional area (A) of heat flow = 1 cm² = 0.0001 m² (typical for a small CPU).
Processor power (Q) = 95 W.
Ambient temperature = 25°C.
Now, let's calculate the minimum heat sink temperature for different values of �
L
(thickness of the heat sink) and plot the results:
Thickness of Heat Sink (L, m)
Minimum Heat Sink Temperature (°C)
0.005 m (5 mm)
50.41
0.01 m (10 mm)
46.72
0.02 m (20 mm)
39.34
Implications:
The minimum heat sink temperature required decreases as the thickness of the heat sink (L) increases. Thicker heat sinks can dissipate heat more effectively.
In practice, it's important to choose a heat sink with an appropriate size and design to ensure the processor operates within a safe temperature range.
This analysis provides a practical basis for designing an effective heat sink to cool a computer processor, taking into consideration thermal properties and safe operating temperatures. It illustrates the real-world application of steady-state convection problems in electronics cooling.
Related Documents
Related Questions
(heat transfer)
arrow_forward
Obtain by dimensional analysis a functional relationship for the wall
heat transfer coefficient h (W/m2-K) for a fluid flowing through a
straight pipe of circular cross section. Assume that the effects of
natural convection may be neglected in comparison with those of
forced convection. Taking the heat transfer coefficient, h, as a
function of the fluid velocity, density, viscosity specific heat and
thermal conductivity, v, p, H, Cp and k, respectively, and of the inside
diameter of the pipe, d. For recurring set, the variables d, u, k, and p. It
found by experiment that, when the flow is turbulent, increasing the
flowrate by a factor of 2 always results in a 60 percent increase in the
coefficient. How would a 50 percent increase in density of the fluid be
expected to affect coefficient, all other variables remaining constant?
arrow_forward
answer shown is 100% correct
arrow_forward
Only handwritten otherwise skip and dont copy
arrow_forward
Define:
a. Convection heat transfer coefficient
b. Loss of pressure across the tube arrangement
*)Based on image below:
arrow_forward
To cool hot oil, an engineer has suggested that the oil be pumped through a pipe submerged in a nearby lake. The pipe (external diameter = 15 cm) will be placed in the horizontal direction. The temperature of the outer surface of the pipe averages 125 ° C. The surrounding water temperature is assumed to be constant at 15 ° C. Pipe length 125 m. If it is assumed that there is no water movement. a. Determine the convective heat transfer coefficient of the outer pipe surface to the water. = Answer Watt / (m² ° C) b. Determine the heat transfer rate from the pipe to the water. = Answer kW
arrow_forward
To cool hot oil, an engineer has suggested that the oil be pumped through a pipe submerged in a nearby lake. The pipe (external diameter = 15 cm) will be placed in the horizontal direction. The temperature of the outer surface of the pipe averages 125 ° C. The surrounding water temperature is assumed to be constant at 15 ° C. Pipe length 100 m. If it is assumed that there is no water movement.
a. Determine the convective heat transfer coefficient of the outer pipe surface to the water. = ..... Watt / (m² ° C)
b. Determine the heat transfer rate from the pipe to the water. = ..... kW
arrow_forward
Please quick what is the true answer
arrow_forward
SEE MORE QUESTIONS
Recommended textbooks for you
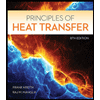
Principles of Heat Transfer (Activate Learning wi...
Mechanical Engineering
ISBN:9781305387102
Author:Kreith, Frank; Manglik, Raj M.
Publisher:Cengage Learning
Related Questions
- (heat transfer)arrow_forwardObtain by dimensional analysis a functional relationship for the wall heat transfer coefficient h (W/m2-K) for a fluid flowing through a straight pipe of circular cross section. Assume that the effects of natural convection may be neglected in comparison with those of forced convection. Taking the heat transfer coefficient, h, as a function of the fluid velocity, density, viscosity specific heat and thermal conductivity, v, p, H, Cp and k, respectively, and of the inside diameter of the pipe, d. For recurring set, the variables d, u, k, and p. It found by experiment that, when the flow is turbulent, increasing the flowrate by a factor of 2 always results in a 60 percent increase in the coefficient. How would a 50 percent increase in density of the fluid be expected to affect coefficient, all other variables remaining constant?arrow_forwardanswer shown is 100% correctarrow_forward
- Only handwritten otherwise skip and dont copyarrow_forwardDefine: a. Convection heat transfer coefficient b. Loss of pressure across the tube arrangement *)Based on image below:arrow_forwardTo cool hot oil, an engineer has suggested that the oil be pumped through a pipe submerged in a nearby lake. The pipe (external diameter = 15 cm) will be placed in the horizontal direction. The temperature of the outer surface of the pipe averages 125 ° C. The surrounding water temperature is assumed to be constant at 15 ° C. Pipe length 125 m. If it is assumed that there is no water movement. a. Determine the convective heat transfer coefficient of the outer pipe surface to the water. = Answer Watt / (m² ° C) b. Determine the heat transfer rate from the pipe to the water. = Answer kWarrow_forward
- To cool hot oil, an engineer has suggested that the oil be pumped through a pipe submerged in a nearby lake. The pipe (external diameter = 15 cm) will be placed in the horizontal direction. The temperature of the outer surface of the pipe averages 125 ° C. The surrounding water temperature is assumed to be constant at 15 ° C. Pipe length 100 m. If it is assumed that there is no water movement. a. Determine the convective heat transfer coefficient of the outer pipe surface to the water. = ..... Watt / (m² ° C) b. Determine the heat transfer rate from the pipe to the water. = ..... kWarrow_forwardPlease quick what is the true answerarrow_forward
arrow_back_ios
arrow_forward_ios
Recommended textbooks for you
- Principles of Heat Transfer (Activate Learning wi...Mechanical EngineeringISBN:9781305387102Author:Kreith, Frank; Manglik, Raj M.Publisher:Cengage Learning
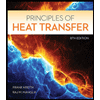
Principles of Heat Transfer (Activate Learning wi...
Mechanical Engineering
ISBN:9781305387102
Author:Kreith, Frank; Manglik, Raj M.
Publisher:Cengage Learning