Strain Raisers
docx
keyboard_arrow_up
School
University of Calgary *
*We aren’t endorsed by this school
Course
479
Subject
Mechanical Engineering
Date
Dec 6, 2023
Type
docx
Pages
6
Uploaded by ChefPorcupine3740
SKYLER COOK, 30163872
10/16/23
ASSESSMENT OF STRAIN RAISERS USING PHOTOELASTICITY
Introduction:
Geometric discontinuities, or stress raisers, disturb stress fields in ways that
create a higher stress near the stress raiser. It is important to understand the effects of
stress raisers in a material, because if a material is brittle or subject to numerous
loading cycles these stress raisers can cause premature component failure due to
cracks forming at the stress raiser sites. Photoelastic materials are often attached to the
material or workpiece to show what the stress field of the material will look like under a
load. This is a result of taking in polarized light and doubly refracting it creating two rays
when it is stressed. The two rays that emerge create an interference pattern due to their
difference in phase, thus creating a pattern of color bands which corresponds to the
stress within the part. The objective of this lab is to use photoelacticity to determine
stress concentrations around stress raisers.
Equipment and Procedure:
The equipment used in this lab is the Vishay Micro-Measurements system LF/Z-2
reflection photoelasticity system. The equipment emits a polarized light onto the
photoelastic material which is then refracted back to the equipment which reads the
interference pattern of the refracted light and produces the color bands corresponding to
stress on the material’s face.
1.
Calibrate the photoelastic coating on the aluminum by setting up a cantilever
beam of aluminum with the coating over top. Start by finding the coating
thickness, then using the photoelasticity system find the deflection and
compensator reading, which is fringe order, for stress of the color black (both
should be 0). Now add deflection to the beam until the next fringe color indicated
in table 1 in results and record the deflection and compensator reading. To find
the compensator reading turn the dial CCW until the color of the photoelastic
material is back to the same black color as the start. Repeat for every fringe
color.
2.
Plot fringe order versus displacement for the theoretical fringe order found in
table 1 in results and experimental fringe order found in step above. Then find
the slopes of both lines.
3.
Use the calibration coating chart to find the strain optical coefficient K using the
slopes found above and the thickness of the coating.
4.
Use equation 1 in results to find the fringe value.
5.
Take the dimensions of the two tensile samples.
6.
Record the fringe orders for the unloaded state at all points indicated on the
samples.
7.
Record the fringe orders for the loaded state at all points indicated on the
samples.
SKYLER COOK, 30163872
10/16/23
ASSESSMENT OF STRAIN RAISERS USING PHOTOELASTICITY
Results:
Table 1: Isochromatic Fringe Characteristics
Fringe Color
Fringe Order,
N
Displacement, D
(in)
Compensator
Reading
Black
0.0
0
0
Pale Yellow
0.60
0.1600
0.70
Dull Red
0.90
0.2350
1.14
Red/Blue Transition
1.00
0.2900
1.19
Blue-Green
1.22
0.3160
1.50
Yellow
1.39
0.4200
1.86
Rose Red
1.82
0.4760
2.21
Red/Green Transition
2.00
0.5290
2.42
Green
2.35
0.5950
2.55
Yellow
2.50
0.6000
2.88
Red
2.65
0.7050
3.27
Red/Green Transition
3.00
0.7700
3.52
Green
3.10
0.8040
3.81
Digital Compensator slope = 4.665 inches per fringe order
Tabel 1 slope = 3.393 inches per fringe order
K (Digital Compensator) = 0.11
K (Table 1) = 0.085
t = 0.112 in or 0.002845 m
Equation 1
ɛ
1
−
ɛ
2
=
(
λ
2
∗
t
∗
K
)
∗
N
=
f
∗
N
Sample calculation for digital compensator:
f
=
(
575
∗
10
−
9
2
∗
0.002845
∗
0.11
)
=
0.000918677
f (Digital Compensator) = 0.000918677 m/m per fringe or 918.677 um/m per fringe
f (Table 1) = 0.001188876 m/m per fringe or 1188.876 um/m per fringe
Table 2: Dimensions of Samples
SKYLER COOK, 30163872
10/16/23
ASSESSMENT OF STRAIN RAISERS USING PHOTOELASTICITY
Thickness, t (mm)
2.845
H (mm)
99.90
d (mm)
49.75
r
1
(mm)
0.5
r
2
(mm)
20
2a (mm)
7.00
Table 3: Elastic Properties of 6061-T651 Aluminum
Yield Stress (MPa)
276
Elastic Modulus (GPa)
69
Poisson’s Ratio
0.33
Table 4: Data for Sample 1
Measurement Point
Fringe Order, N
Unloading, P
1
= 0, N1
Loaded, P
2
= 222.7 lb, N2
a
0
2.37
b
0
3.61
Table 5: Data for Sample 2
Measurement Point
Horizontal distance
from point e (tip of
the hole), (mm)
Fringe Order, N
Unloaded P
1
= 0
N1
Loaded P
2
= 180.1 lb
N2
c
n/a
0
1.99
d
n/a
0
1.70
e
0
0
2.91
f
5
0
2.36
g
11.5
0
2.31
h
16.5
0
2.24
Analysis:
Sample calculation of experimental stress for point a on sample 1:
σ
=
(
E
1
+
v
)
f
(
N
2
−
N
1
)
σ
=
(
69
∗
10
9
1
+
0.33
)
∗
0.000918677
∗
(
2.37
−
0
)
=
112955826.9
Your preview ends here
Eager to read complete document? Join bartleby learn and gain access to the full version
- Access to all documents
- Unlimited textbook solutions
- 24/7 expert homework help
SKYLER COOK, 30163872
10/16/23
ASSESSMENT OF STRAIN RAISERS USING PHOTOELASTICITY
Sample calculation of analytical stress for point a on sample 1:
σnom
=
P
A
=
990.6
2.845
∗
49.75
∗
10
−
6
=
6998790.08
Sample calculation of analytical stress for point b on sample 1:
K
t
= 4.75
σmax
=
Kt
∗
σnom
=
4.75
∗
6998790.08
=
33244252.9
Sample calculation of percent error for point b on sample 1:
%error
=
|
σ
2
−
σ
1
σ
2
|
∗
100
=
417.6
Sample calculation of analytical stress for point c on sample 2:
K
t
= 3
σnom
=
P
A
=
801.1
2.845
∗
49.75
∗
10
−
6
=
5659934.11
σmax
=
Kt
∗
σnom
=
3
∗
5659934.11
=
16979802.33
Sample calculation of analytical stress for point e on sample 2:
Ktg
=
0.284
+
2
1
+
(
d
H
)
−
0.6
∗
(
1
−
(
d
H
)
)
+
1.32
(
1
−
(
d
H
)
)
2
Ktg
=
0.284
+
2
1
+
(
49.75
99.90
)
−
0.6
∗
(
1
−
(
49.75
99.90
)
)
+
1.32
(
1
−
(
49.75
99.90
)
)
2
=
1.65
σnom
=
P
A
=
801.1
2.845
∗
49.75
∗
10
−
6
=
5659934.11
σmax
=
Kt
∗
σnom
=
1.65
∗
5659934.11
=
9338891.28
SKYLER COOK, 30163872
10/16/23
ASSESSMENT OF STRAIN RAISERS USING PHOTOELASTICITY
Table 6: Sample 1 Results
Point
P
2
= 222.7 lb or 990.6 N
σ
1
Experimental
(MPa)
σ
2
Analytical
(MPa)
% Error
a
112.96
7.00
1513.71
b
172.06
33.24
417.6
Table 7: Sample 2 Results
Point
P
2
= 180.1 lb or 801.1 N
σ
1
Experimental
(MPa)
σ
2
Analytical
(MPa)
% Error
c
94.84
16.98
458.5
d
81.02
5.66
1331.4
e
138.69
9.34
1384.9
f
112.48
n/a
n/a
g
110.10
n/a
n/a
h
106.76
n/a
n/a
Discussion:
After viewing the analysis, the percentage of error resulting from the experiment
is quite large which could be a result of many variables. By looking at these initial
results in table 2 and comparing the fringe order to the digital compensator reading, it is
seen that the compensator reading is larger than the fringe order. This could be a result
of excess light entering into the lab room and refracting off the photoelastic material
causing a larger fringe order when calibrating the coating. This same source of error
could have caused larger fringe order when evaluating the stress in the samples after
loading. This error could have affected the analysis when calculating for σ
1
making the
experimental stress larger than the analytical stress.
While photoelasticity is an exceptional way to visualize stress concentrations induced by
a load on a sample, it allows visualization of stress concentrations in expensive or
unique materials where destructive testing is not an option, it does have its limitations. A
significant limitation is accurately calculating stress based on fringe order, one reason is
because the interpretation of fringe patterns can be different between analysts. Another
limitation is that photoelastic materials are extremely sensitive to environmental
conditions such as temperature, vibrations and excess light.
The magnitudes of stress at various points on the sample can be seen in table 7. By
looking purely at the analytical stress, the max stress in the sample occurs at the notch
SKYLER COOK, 30163872
10/16/23
ASSESSMENT OF STRAIN RAISERS USING PHOTOELASTICITY
of the sample which is verified by the equation
σmax
=
Kt
∗
σnom
. The second highest
stress occurs at the point closest to the stress raiser and as the points increase in
distance from the stress raiser the stress decreases. So, to mitigate the effects of stress
raisers in a sample introducing notches into the sample to redistribute the stress, as
seen in the experiment, it causes the max stress to occur at a different point.
Conclusion:
Materials that include strain raisers cause a higher stress to occur around that
point due to the discontinuity of the material. The higher stress around the stress raiser
could cause premature component failure if the material being used is subject to many
loading cycles or if the material is brittle. The stress concentrations around the stress
raiser were analysed using photoelasticity which gave us a visual of the stress
concentrations resulting from the loaded sample. The experiment was an overall
success due to the fact that the relationship between stress raisers and stress
concentrations was seen while using photoelasticity and the effects of notches in the
sample causing a max stress.
Your preview ends here
Eager to read complete document? Join bartleby learn and gain access to the full version
- Access to all documents
- Unlimited textbook solutions
- 24/7 expert homework help
Related Documents
Related Questions
1. For the stress-strain curve shown below, please estimate the properties indicated.
(a) Fracture Strain
Please do your work on a separate sheet of paper,
and put your answers in the boxes on the right.
Be sure to include the proper symbol and units.
Stress Strain
70
60
50
Stress (ksi)
240
30
20
10
70
0
0.000
60
50
Stress (ksi)
40
20
10
KULL
0
0.000
0.010
0.050
0.100
Strain (in/in)
Stress Strain
0.020 0.030
Strain (in/in)
0.040
0.150
0.050
(b) Ultimate Tensile Stress
(c) Fracture Stress
(d) Proportional Limit
(e) Elastic Modulus
(1) Yield Stress
(g) Tensile Toughness
(Modulus of Toughness)
(h) Modulus of Resilience
arrow_forward
Need help with this Mechanics of Materials review
arrow_forward
Calculate the young’s modulus from one of these two graphs?
arrow_forward
Detailed steps
arrow_forward
6. State your answers to the following questions.Strain Gauge represents the deformation of a material through a change in resistance. If so, explain how temperature will affect the strain gauge in the experimental environment.①:In this experiment, the Strain Gauge measures the strain in micro units. Explain one possible error factor when applying a load by hanging a weight on the material with the strain gauge attached. (Hint: It is easy to shake by hanging the weight using a thread)①:
arrow_forward
(d) Following experimental data (TableQ1b) has obtained from the
torsion test for the specimen dimension given in Table Q1a.
Determine the material of a circular bar. (Take the material
Poisson's Ratio as 0.32)
Table Q1a Specimen Dimensions
Dimensions
Material
Diameter (mm)
6
Length (mm)
77.15
TableQ1b Experimental Results from Torsion test
Angular Deflection
Degree
Radian
Torque/Nm
0.5
0.008727
0.06
1
0.017453
0.47
1.5
0.02618
0.76
2
0.034907
1.01
2.5
0.043633
1.32
3
0.05236
1.65
3.5
0.061087
1.99
4
0.069813
2.32
4.5
0.07854
2.66
5
0.087267
3.00
5.5
0.095993
3.33
6
0.10472
3.64
10
0.174533
5.92
20
0.349066
7.74
30
0.523599
8.07
40
0.698132
8.17
50
0.872665
7.93
60
1.047198
8.10
70
1.221731
8.2
80
1.396264
8.4
90
1.570797
8.24
100
1.74533
8.7
110
1.919863
8.7
120
2.094396
8.7
180
3.141594
9.02
240
4.188792
9.11
300
5.23599
9.48
360
6.283188
9.51
420
7.330386
9.71
arrow_forward
Consider the graph below for 3 test samples A, B and C of the same metal
composition which have been cold-worked, but to different extents. If you had to
sort the samples by the degree of cold-working they have undergone, how would
you rank them?
Stress (MPa)
600
500
4006
300
200
100
0
A
B
0.05
1
0.1
0.15
Strain
Select the correct answer:
a. A
arrow_forward
Stress Strain Diagram
The Data shown in the table have been obtained from a tensile test conducted on
a high-strength steel. The test specimen had a diameter of 0.505 inch and a gage
length of 2.00 inch. Using software. plot the Stress-Strain Diagram for this steel
and determine its:
A= TTdT(050s
A
%3D
1. Proportional Limit,
2. Modulus of Elasticity,
3. Yield Strength (SY) at 0.2% Offset,
4. Ultimate Strength (Su),
5. Percent Elongation in 2.00 inch,
6. Percent Reduction in Area,
7. Present the results (for Steps 1-6) in a highly organized table.
e Altac ie sheet (as problelle
4
A = 0.2.002
BEOINNING of the effort
Elongation
(in)
Elongation
(In)
Load
Load
#:
#3
(Ib)
(Ib)
1
0.0170
15
12,300
0.0004
1,500
16
12,200
0.0200
0.0010
3.
3,100
17
12,000
0.0275
0.0016
4,700
18
13,000
0.0335
5.
6,300
0.0022
19
15,000
0.0400
0.0026
6.
8,000
20
16,200
0.055
0.0032
9,500
21
17,500
0.0680
0.0035
8.
11,000
22
18,800
0.1080
0.0041
11,800
23
19,600
0.1515
0.0051
24
20,100
0.2010
10
12,300
0.0071
25…
arrow_forward
Hi, I need help with this question.
arrow_forward
By looking at these graphs, answer the following answer:
1/ Is the material is ductile or brittle? explain by using information from the graphs.
2/ What are the differences between these two graphs?
arrow_forward
solve the question given in the image.
arrow_forward
You have been given the following test sample data following mechanical testing of 15
test pieces of a modified Alumina.
What is the Weibull modulus of this material?
Would you advise the use of this material over one with a Weibull Modulus of 19.6 and a
mean failure stress of 270 MPa, if you anticipate that the peak stress on the material
could be 255 MPa?
Sample
1
2
3
4
5
6
7
8
9
10
11
12
13
14
15
Select one or more:
a. 185
b. No
Yes
□d. 49
□e. 28.6
3.7
Failure Stress (MPa)
297
293
270
300
g. 22.8
260
296
265
295
280
288
263
290
298
275
arrow_forward
1. A tensile test was conducted on a metal "505" specimen and the following stress-strain curves
were generated, both curves generated from the same set of data. Use the graphs to fill in the
mechanical properties of the material tested in the box below. Don't forget units!
Stress vs Strain
Stress, psi
Stress, psi
80000
70000
60000
50000
40000
30000
20000
10000
0
0.00
80000
70000
60000
50000
40000
30000
20000
10000
0.02
0
0.000 0.002
0.04
0.004
0.06
0.006
0.08
0.10
Strain
Stress vs Strain
0.008
0.12
Elastic Modulus, E:
0.2% Offset Yield Strength, oo:
Tensile Strength, ou:
Breaking Strength, of:
% Elongation:
0.14
0.010 0.012 0.014
Strain
0.16
0.18
0.016 0.018
0.20
0.020
arrow_forward
True stress (MPa)
8-7 Figure 8-21 is a plot of true stress
versus true strain for a metal. For total
imposed strains of 0.1, 0.2, 0.3 and
0.4, determine the elastic and plastic
components of the strain. The modulus
of elasticity of the metal is 100 GPa.
600
500
400
300
200
100
0.1
0.2
0.3
0.4
0.5
True strain
Figure 8-21 A true stress versus true strain curve
for a metal (for Problem 8-7).
arrow_forward
5. The following data were collected from a standard 0.505-in.-diameter test
specimen of a copper alloy (initial length lo= 2.0 in.). After fracture, the total
length was 3.014 in. and the diameter was 0.374 in.
Load
(Ib)
Al
(in.)
00000
3,000
6,000
0.00167
0.00333
7,500
0.00417
9,000
10,500
0.0090
0.040
12,000
0.26
12,400
11,400
0.50 (maximum load)
1.02 (fracture)
a)
Plot the data as engineering stress versus engineering strain.
b)
Compute the modulus of elasticity.
c)
Determine the yield strength at a strain offset of 0.002.
d)
Determine the tensile strength of this alloy.
e)
What is the approximate ductility, in percent elongation?
f)
Compute the modulus of resilience.
g)
Compute from the data and plot true stress versus true strain diagram.
arrow_forward
SEE MORE QUESTIONS
Recommended textbooks for you
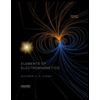
Elements Of Electromagnetics
Mechanical Engineering
ISBN:9780190698614
Author:Sadiku, Matthew N. O.
Publisher:Oxford University Press
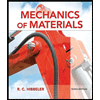
Mechanics of Materials (10th Edition)
Mechanical Engineering
ISBN:9780134319650
Author:Russell C. Hibbeler
Publisher:PEARSON
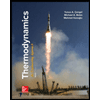
Thermodynamics: An Engineering Approach
Mechanical Engineering
ISBN:9781259822674
Author:Yunus A. Cengel Dr., Michael A. Boles
Publisher:McGraw-Hill Education
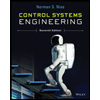
Control Systems Engineering
Mechanical Engineering
ISBN:9781118170519
Author:Norman S. Nise
Publisher:WILEY
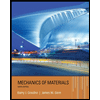
Mechanics of Materials (MindTap Course List)
Mechanical Engineering
ISBN:9781337093347
Author:Barry J. Goodno, James M. Gere
Publisher:Cengage Learning
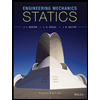
Engineering Mechanics: Statics
Mechanical Engineering
ISBN:9781118807330
Author:James L. Meriam, L. G. Kraige, J. N. Bolton
Publisher:WILEY
Related Questions
- 1. For the stress-strain curve shown below, please estimate the properties indicated. (a) Fracture Strain Please do your work on a separate sheet of paper, and put your answers in the boxes on the right. Be sure to include the proper symbol and units. Stress Strain 70 60 50 Stress (ksi) 240 30 20 10 70 0 0.000 60 50 Stress (ksi) 40 20 10 KULL 0 0.000 0.010 0.050 0.100 Strain (in/in) Stress Strain 0.020 0.030 Strain (in/in) 0.040 0.150 0.050 (b) Ultimate Tensile Stress (c) Fracture Stress (d) Proportional Limit (e) Elastic Modulus (1) Yield Stress (g) Tensile Toughness (Modulus of Toughness) (h) Modulus of Resiliencearrow_forwardNeed help with this Mechanics of Materials reviewarrow_forwardCalculate the young’s modulus from one of these two graphs?arrow_forward
- Detailed stepsarrow_forward6. State your answers to the following questions.Strain Gauge represents the deformation of a material through a change in resistance. If so, explain how temperature will affect the strain gauge in the experimental environment.①:In this experiment, the Strain Gauge measures the strain in micro units. Explain one possible error factor when applying a load by hanging a weight on the material with the strain gauge attached. (Hint: It is easy to shake by hanging the weight using a thread)①:arrow_forward(d) Following experimental data (TableQ1b) has obtained from the torsion test for the specimen dimension given in Table Q1a. Determine the material of a circular bar. (Take the material Poisson's Ratio as 0.32) Table Q1a Specimen Dimensions Dimensions Material Diameter (mm) 6 Length (mm) 77.15 TableQ1b Experimental Results from Torsion test Angular Deflection Degree Radian Torque/Nm 0.5 0.008727 0.06 1 0.017453 0.47 1.5 0.02618 0.76 2 0.034907 1.01 2.5 0.043633 1.32 3 0.05236 1.65 3.5 0.061087 1.99 4 0.069813 2.32 4.5 0.07854 2.66 5 0.087267 3.00 5.5 0.095993 3.33 6 0.10472 3.64 10 0.174533 5.92 20 0.349066 7.74 30 0.523599 8.07 40 0.698132 8.17 50 0.872665 7.93 60 1.047198 8.10 70 1.221731 8.2 80 1.396264 8.4 90 1.570797 8.24 100 1.74533 8.7 110 1.919863 8.7 120 2.094396 8.7 180 3.141594 9.02 240 4.188792 9.11 300 5.23599 9.48 360 6.283188 9.51 420 7.330386 9.71arrow_forward
- Consider the graph below for 3 test samples A, B and C of the same metal composition which have been cold-worked, but to different extents. If you had to sort the samples by the degree of cold-working they have undergone, how would you rank them? Stress (MPa) 600 500 4006 300 200 100 0 A B 0.05 1 0.1 0.15 Strain Select the correct answer: a. Aarrow_forwardStress Strain Diagram The Data shown in the table have been obtained from a tensile test conducted on a high-strength steel. The test specimen had a diameter of 0.505 inch and a gage length of 2.00 inch. Using software. plot the Stress-Strain Diagram for this steel and determine its: A= TTdT(050s A %3D 1. Proportional Limit, 2. Modulus of Elasticity, 3. Yield Strength (SY) at 0.2% Offset, 4. Ultimate Strength (Su), 5. Percent Elongation in 2.00 inch, 6. Percent Reduction in Area, 7. Present the results (for Steps 1-6) in a highly organized table. e Altac ie sheet (as problelle 4 A = 0.2.002 BEOINNING of the effort Elongation (in) Elongation (In) Load Load #: #3 (Ib) (Ib) 1 0.0170 15 12,300 0.0004 1,500 16 12,200 0.0200 0.0010 3. 3,100 17 12,000 0.0275 0.0016 4,700 18 13,000 0.0335 5. 6,300 0.0022 19 15,000 0.0400 0.0026 6. 8,000 20 16,200 0.055 0.0032 9,500 21 17,500 0.0680 0.0035 8. 11,000 22 18,800 0.1080 0.0041 11,800 23 19,600 0.1515 0.0051 24 20,100 0.2010 10 12,300 0.0071 25…arrow_forwardHi, I need help with this question.arrow_forwardBy looking at these graphs, answer the following answer: 1/ Is the material is ductile or brittle? explain by using information from the graphs. 2/ What are the differences between these two graphs?arrow_forwardsolve the question given in the image.arrow_forwardYou have been given the following test sample data following mechanical testing of 15 test pieces of a modified Alumina. What is the Weibull modulus of this material? Would you advise the use of this material over one with a Weibull Modulus of 19.6 and a mean failure stress of 270 MPa, if you anticipate that the peak stress on the material could be 255 MPa? Sample 1 2 3 4 5 6 7 8 9 10 11 12 13 14 15 Select one or more: a. 185 b. No Yes □d. 49 □e. 28.6 3.7 Failure Stress (MPa) 297 293 270 300 g. 22.8 260 296 265 295 280 288 263 290 298 275arrow_forwardarrow_back_iosSEE MORE QUESTIONSarrow_forward_ios
Recommended textbooks for you
- Elements Of ElectromagneticsMechanical EngineeringISBN:9780190698614Author:Sadiku, Matthew N. O.Publisher:Oxford University PressMechanics of Materials (10th Edition)Mechanical EngineeringISBN:9780134319650Author:Russell C. HibbelerPublisher:PEARSONThermodynamics: An Engineering ApproachMechanical EngineeringISBN:9781259822674Author:Yunus A. Cengel Dr., Michael A. BolesPublisher:McGraw-Hill Education
- Control Systems EngineeringMechanical EngineeringISBN:9781118170519Author:Norman S. NisePublisher:WILEYMechanics of Materials (MindTap Course List)Mechanical EngineeringISBN:9781337093347Author:Barry J. Goodno, James M. GerePublisher:Cengage LearningEngineering Mechanics: StaticsMechanical EngineeringISBN:9781118807330Author:James L. Meriam, L. G. Kraige, J. N. BoltonPublisher:WILEY
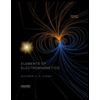
Elements Of Electromagnetics
Mechanical Engineering
ISBN:9780190698614
Author:Sadiku, Matthew N. O.
Publisher:Oxford University Press
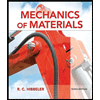
Mechanics of Materials (10th Edition)
Mechanical Engineering
ISBN:9780134319650
Author:Russell C. Hibbeler
Publisher:PEARSON
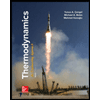
Thermodynamics: An Engineering Approach
Mechanical Engineering
ISBN:9781259822674
Author:Yunus A. Cengel Dr., Michael A. Boles
Publisher:McGraw-Hill Education
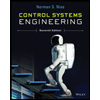
Control Systems Engineering
Mechanical Engineering
ISBN:9781118170519
Author:Norman S. Nise
Publisher:WILEY
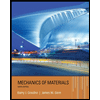
Mechanics of Materials (MindTap Course List)
Mechanical Engineering
ISBN:9781337093347
Author:Barry J. Goodno, James M. Gere
Publisher:Cengage Learning
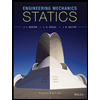
Engineering Mechanics: Statics
Mechanical Engineering
ISBN:9781118807330
Author:James L. Meriam, L. G. Kraige, J. N. Bolton
Publisher:WILEY