KholiaHW1
pdf
keyboard_arrow_up
School
University of Texas, Dallas *
*We aren’t endorsed by this school
Course
6303
Subject
Mechanical Engineering
Date
Dec 6, 2023
Type
Pages
6
Uploaded by axk168131
Abdul Samad kholia
–
axk168131
Problem 2:
1.
AECOM
is an infrastructure consulting company headquartered in Dallas, TX. Their services
include architectural engineering and building design. The CAD software used by the company
include Autodesk’s
AutoCAD and Revit.
Sources:
https://aecom.com/about-us/
https://en.wikipedia.org/wiki/AECOM
2.
Raytheon Technologies
in McKinney, Tx hires mechanical engineers to work on CAD software
that includes PTC Creo. Their products and services include space technologies and defense
systems.
Sources:
https://careers.rtx.com/global/en/job/01644282/Principal-Optomechanical-Design-Engineer
3.
Lockheed Martin
is an aerospace and defense company that has offices in Forth Worth, TX.
Their Aeronautics unit uses CATIA V5 for CAD modelling in design Engineer roles. Some of their
products include Missile and Fire Control, and Space Systems.
Sources:
https://www.lockheedmartinjobs.com/job/fort-worth/design-engineer-level-
2/694/54027322688
4.
GoEngineer
is located in Carrollton, TX and their main service includes 3D Printing. The company
uses SolidWorks for Additive Manufacturing and providing design solutions for their customers.
Sources:
https://www.goengineer.com/3d-printing-services
5.
Qorvo Inc.
in Richardson, TX develops semiconductor devices (CMOS) for satellites among many
other space applications. Mechanical Engineers at Qorvo use CAD packages like SolidWorks and
AutoCAD.
Sources:
https://careers.qorvo.com/job/Mechanical-Engineering-Intern-TX/1071802200/
https://www.qorvo.com/products
Summary Table on next page.
Abdul Samad kholia
–
axk168131
Summary Table:
#
Name of Company
Product
Software used
References
1
AECOM
Building Design
AutoCad, Revit
https://aecom.com/about-us/
2
Raytheon
Technologies
Space Technologies
PTC Creo
https://careers.rtx.com/global/en/job/01644282/Principal
Design-Engineer
3
Lockheed Martin
Missile and Fire Control
Catia V5
https://www.lockheedmartinjobs.com/job/fort-worth/des
2/694/54027322688
4
GoEngineer
3D Printing
SolidWorks
https://www.goengineer.com/3d-printing-services
5
Qorvo Inc.
CMOS Devices
SolidWorks,
AutoCad
https://www.qorvo.com/products
Abdul Samad kholia
–
axk168131
Problem 3:
a)
This sketch is not fully defined. It has 37 DOF and some constraints already applied. To fully
constraint the sketch, we have to provide
13 dimensions
. This was verified using CAD software
as well.
Explanation:
37 total DOF
coincident: 8 * 2 DOF = 16
horizontal: 4 * 1 DOF = 4
tangent: 4 * 1 DOF = 4
37 - (16+4+4) =
13 dimensions needed.
b)
The total number of Degrees of freedom of the sketch without any dimensions or constraints
imposed are 37.
Explanation:
2 arcs: 2 * 5 DOF = 10
1 circle: 1 * 3 DOF = 3
6 straight lines: 6 *4 DOF = 24
Total DOF = 10 + 3 + 24 =
37 DOF
.
Your preview ends here
Eager to read complete document? Join bartleby learn and gain access to the full version
- Access to all documents
- Unlimited textbook solutions
- 24/7 expert homework help
Abdul Samad kholia
–
axk168131
Problem 4:
a)
Design for Assembly (DFA):
Better designed products tend to have lesser number of parts and are easier to assemble. This is the
design principle behind Design for Assembly. It involves optimizing the problem by designing to
minimize the amount of parts or components in the design. As we can see in the figures below, we have
much less fasteners, hence better DFA. This helps the whole design be more durable as well. Minimizing
number of parts, also helps standardize handling and assembly operations as there are lesser number of
assembly operations. This impacts the overall cost of the product as well, which goes down as a result of
the number of parts and assembly operations going down.
Source: https://www.semanticscholar.org/paper/DESIGN-FOR-ASSEMBLY-%3A-A-CRITICAL-
METHODOLOGY-FOR-t-Tatikonda
Abdul Samad kholia
–
axk168131
b)
Concurrent Engineering:
This methodology involves simultaneously working on different steps of the design and development
stage to reduce time to bring a new product to market, leading to improved productivity and cost
savings. A famous example of the use of concurrent engineering is in the development of Boeing 777
aircraft that involved customer feedback during development stages. The principles of concurrent
engineering are based on having a multidisciplinary team, effective communication and management
support and involvement on customers. Concurrent engineering significantly reduces errors and
effectively saves time with respect to any conventional project management approach.
Source:
https://whatispiping.com/concurrent-engineering/
Abdul Samad kholia
–
axk168131
c)
Fail-safe Design
Fail-safe design is a common feature of aircrafts as these systems are supposed to have redundancies
and have to work even if some parts have failed. This is why commercial aircrafts are 2 instead of 1
engine. There are factors of safety added to all stages of the design after systems going through
extensive fatigue testing. Typically factors of safety range from 1.5
–
5. Fail safe designs tend to employ
inexpensive components to prevent damage to expensive, difficult to repair components. Fuses in
electrical systems are one example of fail-safe design. Another example is shear pins in a boat propeller
that transmit power from the shaft to propeller. These are design to fail before the shaft or propeller are
damaged, and are easy to replace.
Source: https://www.sciencedirect.com/topics/materials-science/fail-safe-design
Your preview ends here
Eager to read complete document? Join bartleby learn and gain access to the full version
- Access to all documents
- Unlimited textbook solutions
- 24/7 expert homework help
Related Documents
Related Questions
I need help solving this problem.
arrow_forward
"Design and Fabrication of an Agricultural Spraying Attachment foran Autonomous Rover"we need help in the machine design part of our study, specifically Pump selection, batteryselection, and center of gravity computation.
Rover weight capacity 35 kilo grams (payload)Rover measurements:Wheel distance - 14.5 inches and 8.5 inchesRover platform size (width & length) 14.4 inches x 10.4 inchesHeight- 15.8 inches.
....help it
arrow_forward
use LMTD for part a and b
arrow_forward
mylabmastering.pearson.com
Chapter 12 - Lecture Notes.pptx: (MAE 272-01) (SP25) DY...
P Pearson MyLab and Mastering
Scores
arrow_forward
The title of our study is "Design and Fabrication of an Agricultural Spraying Attachment for an Autonomous Rover" we need help in the machine design part of our study, specifically Pump selection, battery selection, and center of gravity computation I already sent you the image of the rover Rover weight capacity 35 kilo grams (payload) Rover measurements: Wheel distance - 14.5 inches and 8.5 inches Rover platform size (width & length) 14.4 inches x 10.4 inches Height- 15.8 inches. Water tank selection More or less 25 liters *For tank selection we need to justify the size with the center of gravity, proving that is the maximum dimension or liters of the tank because the center of gravity will be higher making the rover prone to toppling Pump selection *Our sprayer design has two nozzles which splits using a tee splitter, we need to find the size of the pump to obtain the same discharge rate of a normal sprayer. A normal sprayer has a 12V pump and a pressure from 0.2 to 0.45 mpa…
arrow_forward
Test 1 .DOCX * A
File Edit View
Tools Help
INDUSTRIAL ENGINEERING PROGRAMME
IMB 411-INDUSTRIAL LOGISTICS
TEST 1- SEPTEMBER 12, 2012
Instructions: Answer all questions. Time allowed is 1.5 hours. Identify your script with your
student number ONLY (Do not write your name).
1. Define the following terms
(i) Logistics management
(ii) Supply chain management
(iii) Vertical integration in a supply chain
(3 Marks)
(3 Marks)
(3 Marks)
2. (a) Using examples of your choice, briefly discuss the following levels of customer
service
(1) Pre-transaction elements
(ii) Transaction elements
(4 Marks)
(4 Marks)
(iii) Post-transaction elements
(4 Marks)
(b) "The challenge facing Dumelang Enterprise (Pty) Ltd is to establish the real
profitability of their customers and to develop service strategies that will improve the
profitability of all customers". As a logistics consultant, briefly discuss how you can
advise Dumelang's customer service management.
3. (a) List the three main forms of inventory in a…
arrow_forward
A realistic CAD model of the whole jack must be produced from which you will generate an
assembly drawing. Standard bought-in components must be specified. Material specifications of components listed in your 'bill of materials' must be provided. Detail designs calculations, for the main pivots, hydraulic actuation safety system, must be carried out.
arrow_forward
Problem 1: You are working in a consulting company that does a lot of hand calculations for designs in
Aerospace Industry for mechanical, thermal, and fluidic systems. You took the Virtual engineering
course, and you want to convince your boss and the team you work to move to modelling and simulation
in computers using a certain software (Ansys, Abaqus, etc). Discuss the benefits and pitfalls of computer
based models used within an industrial environment to solve problems in engineering.
arrow_forward
Please don't use AI becuase it is not correct.
arrow_forward
DISCUSS THE STEP-BY-STEP PROCESS OF HOW TO COME UP WITH A SOLUTION.
*Preferably if you typed the answer
Thumbs up guaranteed If you discuss the steps. Thankyou!
arrow_forward
Look up the Arduino Mega 2560. Document the steps how to work with the Arduino in Matlab and Simulink. Make a simulink program turning on the LED on the board for 10sec. Explain your program, comment on your findings and explain how to test it on the actual hardware.
arrow_forward
permanent-magnet (pm) genera x
Bb Blackboard Learn
L STAND-ALONE.mp4 - Google Dri x
O Google Drive: ülwgjuó jc lis u
O ME526-WindEnergy-L25-Shuja.p x
O File | C:/Users/Administrator/Desktop/KFUPM%20Term%232/ME526/ME526-WindEnergy-L25-Shuja.pdf
(D Page view
A Read aloud
T) Add text
V Draw
Y Highlight
O Erase
17
of 26
Wind Farms
Consider the arrangement of three wind turbines in the following schematic in which wind
turbine C is in the wakes of turbines A and B.
Given the following:
- Uo = 12 m/s
A
-XẠC = 500 m
-XBC = 200 m
- z = 60 m
- Zo = 0.3 m
U.
-r, = 20 m
B
- CT = 0.88
Compute the total velocity deficit, udef(C) and the velocity at wind turbine C, namely Vc.
Activate Windows
Go to Settings to activate Windows.
Wind Farms (Example Answer)
5:43 PM
A 4)) ENG
5/3/2022
I!
arrow_forward
Please do not copy other's work and do not use ChatGPT or Gpt4,i will be very very very appreciate!!!
Thanks a lot!!!!!
arrow_forward
After watching the following video:ABC Nightline. (2009, December 2). IDEO Shopping Cart.
and read article: Boeing. (n.d.). The Boeing Design Change Process. 787updates
After watching the video and reading the article, discuss the role of different members working together as a team in the design process?
arrow_forward
I want the answer of part c
arrow_forward
Example 1.1 Figure 1.5 shows the block diagram of a closed-loop flow control system. Identify the following elements: (a) the sensor, (b) the transducer, (c) the actuator, (d) the transmitter, (e) the controller, (f) the manipulated variable, and (g) the measured variable.
In the figure above, the (a) sensor is labeled as the pressure cell. The (b) transducer is labeled as the converter. However, there are two converters: one for converting pressure to current, and another converting current to pressure for operating the actuator. The (c) actuator is labeled as the pneumatic valve. The (d) transmitter is labeled as the line driver. The (e) controller is labeled as the PLC. The (f) manipulated variable is labeled as the pressure developed by the fluid flowing through the orifice plate. The (g) measured variable is the flow rate of the liquid.
arrow_forward
SEE MORE QUESTIONS
Recommended textbooks for you
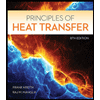
Principles of Heat Transfer (Activate Learning wi...
Mechanical Engineering
ISBN:9781305387102
Author:Kreith, Frank; Manglik, Raj M.
Publisher:Cengage Learning
Related Questions
- I need help solving this problem.arrow_forward"Design and Fabrication of an Agricultural Spraying Attachment foran Autonomous Rover"we need help in the machine design part of our study, specifically Pump selection, batteryselection, and center of gravity computation. Rover weight capacity 35 kilo grams (payload)Rover measurements:Wheel distance - 14.5 inches and 8.5 inchesRover platform size (width & length) 14.4 inches x 10.4 inchesHeight- 15.8 inches. ....help itarrow_forwarduse LMTD for part a and barrow_forward
- mylabmastering.pearson.com Chapter 12 - Lecture Notes.pptx: (MAE 272-01) (SP25) DY... P Pearson MyLab and Mastering Scoresarrow_forwardThe title of our study is "Design and Fabrication of an Agricultural Spraying Attachment for an Autonomous Rover" we need help in the machine design part of our study, specifically Pump selection, battery selection, and center of gravity computation I already sent you the image of the rover Rover weight capacity 35 kilo grams (payload) Rover measurements: Wheel distance - 14.5 inches and 8.5 inches Rover platform size (width & length) 14.4 inches x 10.4 inches Height- 15.8 inches. Water tank selection More or less 25 liters *For tank selection we need to justify the size with the center of gravity, proving that is the maximum dimension or liters of the tank because the center of gravity will be higher making the rover prone to toppling Pump selection *Our sprayer design has two nozzles which splits using a tee splitter, we need to find the size of the pump to obtain the same discharge rate of a normal sprayer. A normal sprayer has a 12V pump and a pressure from 0.2 to 0.45 mpa…arrow_forwardTest 1 .DOCX * A File Edit View Tools Help INDUSTRIAL ENGINEERING PROGRAMME IMB 411-INDUSTRIAL LOGISTICS TEST 1- SEPTEMBER 12, 2012 Instructions: Answer all questions. Time allowed is 1.5 hours. Identify your script with your student number ONLY (Do not write your name). 1. Define the following terms (i) Logistics management (ii) Supply chain management (iii) Vertical integration in a supply chain (3 Marks) (3 Marks) (3 Marks) 2. (a) Using examples of your choice, briefly discuss the following levels of customer service (1) Pre-transaction elements (ii) Transaction elements (4 Marks) (4 Marks) (iii) Post-transaction elements (4 Marks) (b) "The challenge facing Dumelang Enterprise (Pty) Ltd is to establish the real profitability of their customers and to develop service strategies that will improve the profitability of all customers". As a logistics consultant, briefly discuss how you can advise Dumelang's customer service management. 3. (a) List the three main forms of inventory in a…arrow_forward
- A realistic CAD model of the whole jack must be produced from which you will generate an assembly drawing. Standard bought-in components must be specified. Material specifications of components listed in your 'bill of materials' must be provided. Detail designs calculations, for the main pivots, hydraulic actuation safety system, must be carried out.arrow_forwardProblem 1: You are working in a consulting company that does a lot of hand calculations for designs in Aerospace Industry for mechanical, thermal, and fluidic systems. You took the Virtual engineering course, and you want to convince your boss and the team you work to move to modelling and simulation in computers using a certain software (Ansys, Abaqus, etc). Discuss the benefits and pitfalls of computer based models used within an industrial environment to solve problems in engineering.arrow_forwardPlease don't use AI becuase it is not correct.arrow_forward
- DISCUSS THE STEP-BY-STEP PROCESS OF HOW TO COME UP WITH A SOLUTION. *Preferably if you typed the answer Thumbs up guaranteed If you discuss the steps. Thankyou!arrow_forwardLook up the Arduino Mega 2560. Document the steps how to work with the Arduino in Matlab and Simulink. Make a simulink program turning on the LED on the board for 10sec. Explain your program, comment on your findings and explain how to test it on the actual hardware.arrow_forwardpermanent-magnet (pm) genera x Bb Blackboard Learn L STAND-ALONE.mp4 - Google Dri x O Google Drive: ülwgjuó jc lis u O ME526-WindEnergy-L25-Shuja.p x O File | C:/Users/Administrator/Desktop/KFUPM%20Term%232/ME526/ME526-WindEnergy-L25-Shuja.pdf (D Page view A Read aloud T) Add text V Draw Y Highlight O Erase 17 of 26 Wind Farms Consider the arrangement of three wind turbines in the following schematic in which wind turbine C is in the wakes of turbines A and B. Given the following: - Uo = 12 m/s A -XẠC = 500 m -XBC = 200 m - z = 60 m - Zo = 0.3 m U. -r, = 20 m B - CT = 0.88 Compute the total velocity deficit, udef(C) and the velocity at wind turbine C, namely Vc. Activate Windows Go to Settings to activate Windows. Wind Farms (Example Answer) 5:43 PM A 4)) ENG 5/3/2022 I!arrow_forward
arrow_back_ios
SEE MORE QUESTIONS
arrow_forward_ios
Recommended textbooks for you
- Principles of Heat Transfer (Activate Learning wi...Mechanical EngineeringISBN:9781305387102Author:Kreith, Frank; Manglik, Raj M.Publisher:Cengage Learning
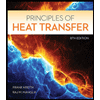
Principles of Heat Transfer (Activate Learning wi...
Mechanical Engineering
ISBN:9781305387102
Author:Kreith, Frank; Manglik, Raj M.
Publisher:Cengage Learning