3
docx
keyboard_arrow_up
School
Conestoga College *
*We aren’t endorsed by this school
Course
8000-4
Subject
Mechanical Engineering
Date
Dec 6, 2023
Type
docx
Pages
2
Uploaded by ashwinbahulayan
3
Instructions
review the Scenario – Cisco Metals
On January 3, 2018, following the Christmas production shutdown, there was a 2 day delay in
the start-up of a production line at Cisco Metals. Over the Christmas shutdown, there was
repair work happening on the furnaces in the facility. Thirty coils were being replaced in one of
the furnaces.
The delay cost 2 days of production at about $7000 per day. There were also 14 additional
people on each crew working around the clock because of the maintenance delay. This delay
was due to the maintenance staff not having the grinding wheels needed to cut this particular
coil from the furnace. The grinding wheels they had were #62 and they needed #62-2.
Maintenance had put in a request 4 weeks ago and received the wheels a week later, but did
not realize they had the incorrect grinding wheels until the job was started.
The purchasing department substituted #62 wheels for the #62-2 wheels that were originally
requested. They appeared to be the same wheel and the #62 wheels were $40 less than the
#62-2 grinding wheels. Purchasing regularly substitutes a less expensive part if it provides the
same function. In this case, the material was different between the two grinding wheels and
had been selected specifically for cutting the alloy that had been used in the furnace coils.
The #62 wheels cut much slower and kept breaking which was dangerous though no one had
been injured. The delay came from the slow cutting time, work stoppage, and waiting for the
original #62-2 wheels that were now being sent on an emergency basis.
2) Create a Cause-and-Effect Relationship Chart Start small using a basic linear flow. Then use questions
to fill in the details by adding causes horizontally and vertically to reflect additional information and/or
"necessary and sufficient logic".
Should contain, must have/follow these
The causes identified are sufficient to produce the associated effect
The causes identified in the map are necessary to produce the linked effects
Impacted goal is properly identified
Enough detail is provided in the map that the final causes are solved, they will prevent the issue.
Evidence of causes is provided where possible.
Leadership, ideas, and collaboration shown in MSTeams and/or participation in at least one meeting with
group
a few seconds ago
Good response
What do you like about this response? How was it good?
Cancel
Submit
Bad response
What was the issue with this response? How could it be improved?
Cancel
Submit
Helpful Assistant
Here is a cause-and-effect relationship chart for the scenario you provided:
The main impacted goal was to restart production at Cisco Metals after the Christmas shutdown.
Cause: Maintenance staff requested incorrect grinding wheels (#62 instead of #62-2) for replacing
furnace coils
Effect: Incorrect grinding wheels (#62) were received by maintenance
Cause: Purchasing department substituted cheaper #62 wheels without verifying they were suitable
Effect: Maintenance started job with #62 wheels, not realizing they were incorrect
Cause: #62 wheels cut much slower than required #62-2 wheels
Effect: Work took longer than expected due to slow cutting
Cause: #62 wheels kept breaking during cutting
Effect: Work had to stop frequently to replace broken wheels, further delaying progress
Cause: Emergency request was made for correct #62-2 wheels
Effect: Delay in receiving #62-2 wheels from emergency order
Effect: 2 day production delay at Cisco Metals
Effect: Increased labor costs of $14,000 due to extra crew members working overtime
The identified causes are sufficient to explain why the production delay occurred. Ensuring the correct
grinding wheels (#62-2) are requested and received is necessary to prevent similar delays in the future.
The purchasing department substituting an incorrect part without verification was a root cause.
Providing more details on part specifications or getting approval for substitutions could help solve this
issue. Let me know if any part of the cause-and-effect relationship chart needs more explanation or
expansion.
Your preview ends here
Eager to read complete document? Join bartleby learn and gain access to the full version
- Access to all documents
- Unlimited textbook solutions
- 24/7 expert homework help
Related Questions
Answer all the calculations questions, if you are not not expert please don't attempt, don't use artificial intelligence
arrow_forward
The MPS start quantities for product A calls for the assembly department to begin final assembly accordingto the following schedule: 100 units in week 2; 200 units in week 4; 120 units in week 6; 180 units in week 7;and 60 units in week 8. Develop a material requirements plan for the next 8 weeks for items B, C, and D.The BOM for A is shown in Figure 11.26, and data from the inventory records are shown in Table 11.4.
arrow_forward
The BOM for product A is shown in Figure 11.40, and datafrom the inventory records are shown in Table 11.9. In theMPS for product A, the MPS start row has 100 units in week 3and 200 in week 6. Develop the material requirements planfor the next 6 weeks for items C, D, and E.a. Develop the material requirements plan for the next6 weeks for items C, D, and E.b. What specific managerial actions are required inweek 1?
arrow_forward
I need help with part a b and c in question 2. Question one is listed because it is referenced in question 2. Any help with question 2 would be appreciated even if it is not all 3 parts.
thank you
1. A certain batch of parts is routed through six machines in a batch production plant. The setup and operation times for each machine are given in the table below. Batch size is 200 and the average nonoperation time per machine is15 hr. Determine (a) manufacturing lead time and (b) hourly production rate for operation 4.Machine 1 2 3 4 5 6Setup time (hr) 5 3 6 4 5 3Operation time (min) 3.0 3.3 8.2 3.9 4.5 2.3
a. 6(4.3+200(3.9/60)+15) = 193.8 hours 24.2 days if 8 hour shiftb. 4(60)+200(3.9)/200 =5.1 hourly production for operation 4
2. Suppose the part in the previous problem is made in very large quantities on a production line in which an automated work handling system is used to transfer parts between machines. Transfer time between stations is 30 sec. total time required to…
arrow_forward
1. A certain batch of parts is routed through six machines in a batch production plant. The setup and operation times for each machine are given in the table below. Batch size is 200 and the average nonoperation time per machine is15 hr. Determine (a) manufacturing lead time and (b) hourly production rate for operation 4.Machine 1 2 3 4 5 6Setup time (hr) 5 3 6 4 5 3Operation time (min) 3.0 3.3 8.2 3.9 4.5 2.3
a. 6(4.3+200(3.9/60)+15) = 193.8 hours 24.2 days if 8 hour shiftb. 4(60)+200(3.9)/200 =5.1 hourly production for operation 4
2. Suppose the part in the previous problem is made in very large quantities on a production line in which an automated work handling system is used to transfer parts between machines. Transfer time between stations is 30 sec. total time required to setup the entire line is 102 hr. Assume that the operation times at the individual machines remain the same as in the previous problem, Determine (a) manufacturing lead time for a part coming off the line,…
arrow_forward
Procedure:
1. Copy the following table on a separate sheet of paper.
2. List all knowns
3. List all unknowns
4. List all equations that you need to use
5. Draw a diagram of the problem
6. Substitute and solve the problem. Be sure to show your work (1pt).
7. Final Answer
8. Take a picture and upload your answer!
Problem:
A 25 ft long solid steel rod is subjected to a load of 10,000 lb. This load causes the rod to stretch
0.477 in. The modulus of elasticity of the steel is 30,000,000 psi. Determine the diameter of the rod.
(precision of 0.00)
Table:
#1
Substitute and Solve:
Knowns:
Draw:
Unknowns:
Equation:
Final Solution
arrow_forward
A batch of 35 parts is ordered by a customer about every six months. The parts are currently processed sequentially through five conventional machines, listed in the following table with setup times and work cycle times per piece. These machines all require an operator to be in attendance during the work cycle. There is a delay of 10 hr/machine dueto transport between machines and waiting in queues of other parts processed by thesemachines. A recommendation has been made to process the parts on a new multitaskingmachine that would complete the batch in one setup, which would involve a simple fixtureand a setup time of 2.0 hr. The work cycle on the multitasking machine consists of thesame operations that are accomplished by the five machines, but the cycle time would beless than the sum of the five cycle times by one-half because of tool path improvementsand reduced part handling. Determine the manufacturing lead time (how long it takes tocomplete the batch of 35 parts, including…
arrow_forward
A certain job shop specializes in one-of-a-kind orders dealing with parts of medium-to-high complexity. A typical part is processed sequentially through ten machines in batch sizes of one. The shop contains a total of eight conventional machine tools and operates 40 hours per week of production time. Average time values on each part per machine are: Machining time = 0.5 hour; Work handling time = 0.3 hour; Tool change time = 0.2 hour; Setup time = 3 hours; Nonoperation time = 12 hours. A new programmable machine is being considered that can perform all ten operations in a single setup. The programming of the machine for this part will require 20 hours; however, the programming can be done off-line, without tying up the machine. Setup time will be just 2 hours because simpler fixtures will be used. Total machining time will be reduced to 80% of its previous value due to advanced tool control algorithms; work handling time will be the same as for one machine; and total tool change time…
arrow_forward
Complete solution. Thanks
arrow_forward
|Read the problem statement and the solution provided. There may or may not be one or more
mistakes in the solution. Go through the solution carefully and then do the following.
1. State if the solution is correct or incorrect
2. If the solution is incorrect, identify what is the mistake in the solution. Be specific and succinct.
3. If the solution is incorrect, provide the final solution with appropriate steps. You can make the
corrections directly on a copy of this provided solution, but make sure you clearly explain the
corrections.
Problem: Consider fully-developed flow of water through a 24-cm diameter tube. The water comes in at
20°C and exits at 40°C. The surface temperature of the tube is uniform at 60°C. The water flow has a
mass flow rate of 0.24 kg/s. What is the average convection coefficient of the water flow?
Solution: We have T, = 60°C, Tmi = 20°C, Tmo = 40°C, So, the bulk-mean temperature is Tm = 30°C.
The appropriate properties are: u = 7.98 × 10-4 kg/ms;
k = 0.615…
arrow_forward
Kilmer Company's customer demand for its only product exceeds its manufacturing capacity. The company provided the following
information for the machine whose limited capacity is prohibiting the company from producing and selling additional units:
Actual run time this week
Machine time available per week
Actual run rate this week
Ideal run rate
Defect-free output this week
Total output this week (including defects)
1-a. Utilization rate
1-b. Efficiency rate.
1-c. Quality rate
1-d. Overall equipment effectiveness
7,500 minutes
12,500 minutes
2-a. Utilization loss in units
2-b. Efficiency loss in units
2-c. Quality loss in units
6.30 units per minute
7 units per minute
Required:
1. and 2. With respect to the company's overall equipment effectiveness, calculate the following:
Note: Do not round intermediate calculations. Round final answers to 2 decimal places and "Units" answers to the nearest whole
number.
37,800 units
47,250 units
arrow_forward
Monthly delivery rate for a part supplied to an automotive assembly plant is 12,500 pc. There are 20 working days in February and 22 working days in March. The effective operating time of the plant is 840 min per day (two shifts). The fraction defect rate for the component is 0.017, and the automated machine that produces the part has an availability of 96%. Determine the takt time for this part during (a) February and (b) March.
arrow_forward
You are given a line balancing problem with
the following diagram. The processing time is
above each process. Using the ranked
positional weight (RPW) heuristic calculate the
number of workstations for a desired cycle time
CTd
= 11 and the line efficiency based on this
heuristic.
B
5
7
A
D
E
F
4
6.
arrow_forward
The monthly usage for a component supplied to an assembly plant is 3,400 parts. There are 21 working days in the month and the effective operating time of the plant is 450 min per day. Currently, the defect rate for the component is 1.2%, and the equipment used to produce the part is down for repairs an average of 18 min per day. Determine the takt time for this part.
arrow_forward
Create me a simplified cash flow diagram for the project starting from initial development until the first month of profit. (The second photo is the template for cash flow diagram, please follow closely.)
arrow_forward
14.15 ANSWER A AND B
arrow_forward
Q1
arrow_forward
I asked for problems 6 and 7 to be answered, but I did not get a properly structured answered as the example shows on problem number 1. Here is the link to the questions I already had answered, could you please rewrite the answer so its properly answered as the example shows (Problem 1)?
https://www.bartleby.com/questions-and-answers/it-vivch-print-reading-for-industry-228-class-date-name-review-activity-112-for-each-local-note-or-c/cadc3f7b-2c2f-4471-842b-5a84bf505857
arrow_forward
SEE MORE QUESTIONS
Recommended textbooks for you
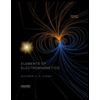
Elements Of Electromagnetics
Mechanical Engineering
ISBN:9780190698614
Author:Sadiku, Matthew N. O.
Publisher:Oxford University Press
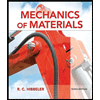
Mechanics of Materials (10th Edition)
Mechanical Engineering
ISBN:9780134319650
Author:Russell C. Hibbeler
Publisher:PEARSON
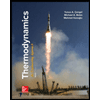
Thermodynamics: An Engineering Approach
Mechanical Engineering
ISBN:9781259822674
Author:Yunus A. Cengel Dr., Michael A. Boles
Publisher:McGraw-Hill Education
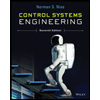
Control Systems Engineering
Mechanical Engineering
ISBN:9781118170519
Author:Norman S. Nise
Publisher:WILEY
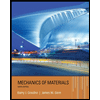
Mechanics of Materials (MindTap Course List)
Mechanical Engineering
ISBN:9781337093347
Author:Barry J. Goodno, James M. Gere
Publisher:Cengage Learning
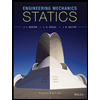
Engineering Mechanics: Statics
Mechanical Engineering
ISBN:9781118807330
Author:James L. Meriam, L. G. Kraige, J. N. Bolton
Publisher:WILEY
Related Questions
- Answer all the calculations questions, if you are not not expert please don't attempt, don't use artificial intelligencearrow_forwardThe MPS start quantities for product A calls for the assembly department to begin final assembly accordingto the following schedule: 100 units in week 2; 200 units in week 4; 120 units in week 6; 180 units in week 7;and 60 units in week 8. Develop a material requirements plan for the next 8 weeks for items B, C, and D.The BOM for A is shown in Figure 11.26, and data from the inventory records are shown in Table 11.4.arrow_forwardThe BOM for product A is shown in Figure 11.40, and datafrom the inventory records are shown in Table 11.9. In theMPS for product A, the MPS start row has 100 units in week 3and 200 in week 6. Develop the material requirements planfor the next 6 weeks for items C, D, and E.a. Develop the material requirements plan for the next6 weeks for items C, D, and E.b. What specific managerial actions are required inweek 1?arrow_forward
- I need help with part a b and c in question 2. Question one is listed because it is referenced in question 2. Any help with question 2 would be appreciated even if it is not all 3 parts. thank you 1. A certain batch of parts is routed through six machines in a batch production plant. The setup and operation times for each machine are given in the table below. Batch size is 200 and the average nonoperation time per machine is15 hr. Determine (a) manufacturing lead time and (b) hourly production rate for operation 4.Machine 1 2 3 4 5 6Setup time (hr) 5 3 6 4 5 3Operation time (min) 3.0 3.3 8.2 3.9 4.5 2.3 a. 6(4.3+200(3.9/60)+15) = 193.8 hours 24.2 days if 8 hour shiftb. 4(60)+200(3.9)/200 =5.1 hourly production for operation 4 2. Suppose the part in the previous problem is made in very large quantities on a production line in which an automated work handling system is used to transfer parts between machines. Transfer time between stations is 30 sec. total time required to…arrow_forward1. A certain batch of parts is routed through six machines in a batch production plant. The setup and operation times for each machine are given in the table below. Batch size is 200 and the average nonoperation time per machine is15 hr. Determine (a) manufacturing lead time and (b) hourly production rate for operation 4.Machine 1 2 3 4 5 6Setup time (hr) 5 3 6 4 5 3Operation time (min) 3.0 3.3 8.2 3.9 4.5 2.3 a. 6(4.3+200(3.9/60)+15) = 193.8 hours 24.2 days if 8 hour shiftb. 4(60)+200(3.9)/200 =5.1 hourly production for operation 4 2. Suppose the part in the previous problem is made in very large quantities on a production line in which an automated work handling system is used to transfer parts between machines. Transfer time between stations is 30 sec. total time required to setup the entire line is 102 hr. Assume that the operation times at the individual machines remain the same as in the previous problem, Determine (a) manufacturing lead time for a part coming off the line,…arrow_forwardProcedure: 1. Copy the following table on a separate sheet of paper. 2. List all knowns 3. List all unknowns 4. List all equations that you need to use 5. Draw a diagram of the problem 6. Substitute and solve the problem. Be sure to show your work (1pt). 7. Final Answer 8. Take a picture and upload your answer! Problem: A 25 ft long solid steel rod is subjected to a load of 10,000 lb. This load causes the rod to stretch 0.477 in. The modulus of elasticity of the steel is 30,000,000 psi. Determine the diameter of the rod. (precision of 0.00) Table: #1 Substitute and Solve: Knowns: Draw: Unknowns: Equation: Final Solutionarrow_forward
- A batch of 35 parts is ordered by a customer about every six months. The parts are currently processed sequentially through five conventional machines, listed in the following table with setup times and work cycle times per piece. These machines all require an operator to be in attendance during the work cycle. There is a delay of 10 hr/machine dueto transport between machines and waiting in queues of other parts processed by thesemachines. A recommendation has been made to process the parts on a new multitaskingmachine that would complete the batch in one setup, which would involve a simple fixtureand a setup time of 2.0 hr. The work cycle on the multitasking machine consists of thesame operations that are accomplished by the five machines, but the cycle time would beless than the sum of the five cycle times by one-half because of tool path improvementsand reduced part handling. Determine the manufacturing lead time (how long it takes tocomplete the batch of 35 parts, including…arrow_forwardA certain job shop specializes in one-of-a-kind orders dealing with parts of medium-to-high complexity. A typical part is processed sequentially through ten machines in batch sizes of one. The shop contains a total of eight conventional machine tools and operates 40 hours per week of production time. Average time values on each part per machine are: Machining time = 0.5 hour; Work handling time = 0.3 hour; Tool change time = 0.2 hour; Setup time = 3 hours; Nonoperation time = 12 hours. A new programmable machine is being considered that can perform all ten operations in a single setup. The programming of the machine for this part will require 20 hours; however, the programming can be done off-line, without tying up the machine. Setup time will be just 2 hours because simpler fixtures will be used. Total machining time will be reduced to 80% of its previous value due to advanced tool control algorithms; work handling time will be the same as for one machine; and total tool change time…arrow_forwardComplete solution. Thanksarrow_forward
- |Read the problem statement and the solution provided. There may or may not be one or more mistakes in the solution. Go through the solution carefully and then do the following. 1. State if the solution is correct or incorrect 2. If the solution is incorrect, identify what is the mistake in the solution. Be specific and succinct. 3. If the solution is incorrect, provide the final solution with appropriate steps. You can make the corrections directly on a copy of this provided solution, but make sure you clearly explain the corrections. Problem: Consider fully-developed flow of water through a 24-cm diameter tube. The water comes in at 20°C and exits at 40°C. The surface temperature of the tube is uniform at 60°C. The water flow has a mass flow rate of 0.24 kg/s. What is the average convection coefficient of the water flow? Solution: We have T, = 60°C, Tmi = 20°C, Tmo = 40°C, So, the bulk-mean temperature is Tm = 30°C. The appropriate properties are: u = 7.98 × 10-4 kg/ms; k = 0.615…arrow_forwardKilmer Company's customer demand for its only product exceeds its manufacturing capacity. The company provided the following information for the machine whose limited capacity is prohibiting the company from producing and selling additional units: Actual run time this week Machine time available per week Actual run rate this week Ideal run rate Defect-free output this week Total output this week (including defects) 1-a. Utilization rate 1-b. Efficiency rate. 1-c. Quality rate 1-d. Overall equipment effectiveness 7,500 minutes 12,500 minutes 2-a. Utilization loss in units 2-b. Efficiency loss in units 2-c. Quality loss in units 6.30 units per minute 7 units per minute Required: 1. and 2. With respect to the company's overall equipment effectiveness, calculate the following: Note: Do not round intermediate calculations. Round final answers to 2 decimal places and "Units" answers to the nearest whole number. 37,800 units 47,250 unitsarrow_forwardMonthly delivery rate for a part supplied to an automotive assembly plant is 12,500 pc. There are 20 working days in February and 22 working days in March. The effective operating time of the plant is 840 min per day (two shifts). The fraction defect rate for the component is 0.017, and the automated machine that produces the part has an availability of 96%. Determine the takt time for this part during (a) February and (b) March.arrow_forward
arrow_back_ios
SEE MORE QUESTIONS
arrow_forward_ios
Recommended textbooks for you
- Elements Of ElectromagneticsMechanical EngineeringISBN:9780190698614Author:Sadiku, Matthew N. O.Publisher:Oxford University PressMechanics of Materials (10th Edition)Mechanical EngineeringISBN:9780134319650Author:Russell C. HibbelerPublisher:PEARSONThermodynamics: An Engineering ApproachMechanical EngineeringISBN:9781259822674Author:Yunus A. Cengel Dr., Michael A. BolesPublisher:McGraw-Hill Education
- Control Systems EngineeringMechanical EngineeringISBN:9781118170519Author:Norman S. NisePublisher:WILEYMechanics of Materials (MindTap Course List)Mechanical EngineeringISBN:9781337093347Author:Barry J. Goodno, James M. GerePublisher:Cengage LearningEngineering Mechanics: StaticsMechanical EngineeringISBN:9781118807330Author:James L. Meriam, L. G. Kraige, J. N. BoltonPublisher:WILEY
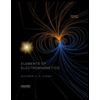
Elements Of Electromagnetics
Mechanical Engineering
ISBN:9780190698614
Author:Sadiku, Matthew N. O.
Publisher:Oxford University Press
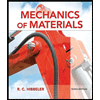
Mechanics of Materials (10th Edition)
Mechanical Engineering
ISBN:9780134319650
Author:Russell C. Hibbeler
Publisher:PEARSON
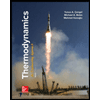
Thermodynamics: An Engineering Approach
Mechanical Engineering
ISBN:9781259822674
Author:Yunus A. Cengel Dr., Michael A. Boles
Publisher:McGraw-Hill Education
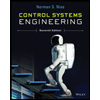
Control Systems Engineering
Mechanical Engineering
ISBN:9781118170519
Author:Norman S. Nise
Publisher:WILEY
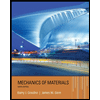
Mechanics of Materials (MindTap Course List)
Mechanical Engineering
ISBN:9781337093347
Author:Barry J. Goodno, James M. Gere
Publisher:Cengage Learning
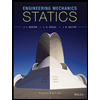
Engineering Mechanics: Statics
Mechanical Engineering
ISBN:9781118807330
Author:James L. Meriam, L. G. Kraige, J. N. Bolton
Publisher:WILEY