ASCI 309 Group Assignment - Luke Morgan
docx
keyboard_arrow_up
School
Embry-Riddle Aeronautical University *
*We aren’t endorsed by this school
Course
309
Subject
Mechanical Engineering
Date
Dec 6, 2023
Type
docx
Pages
5
Uploaded by SuperJaguar1418
1
Reciprocating engines utilize one or more pistons to convert pressure into rotational
motion. Each piston is sealed in a chamber which has an inlet, outlet, and a sparking mechanism.
The inlet allows the fuel/air mixture in as the piston moves down, the inlet is sealed and the
piston moves upwards and pressurizes the fuel/air mixture until it cannot be pressurized any
further. Once the piston reaches the top of the chamber, the spark plug creates a spark and ignites
the mixture which forces the piston down. When the piston begins moving back up, the outlet
valve is opened to release exhaust. Once the piston reaches the top again, the outlet is closed and
then the process repeats (Reciprocating engine). This entire process is done hundreds or even
thousands of times every minute based on the power settings. The process of the piston moving
up and down is used to turn a crankshaft that is attached to the propeller of the airplane. It
converts up and down motion to horizontal rotation to turn the propeller.
Some limitations of reciprocating engines would include the power to weight ratio, speed,
and RPM. Reciprocating engines utilize the force of controlled explosions in each cylinder,
which get extremely hot. To enable this, the engines are made of high density metal to allow high
temperatures and to increase the lifespan of the engine.As reciprocating engines become more
powerful, they become heavier, thus requiring more power from the engine to gain speeds/lift to
overcome the weight of the engine. Speed is also a limit on reciprocating engines, because with
these engines, there will also be a propeller to create thrust. Propellers are limited to rotations per
minute (RPM), because if the tips of the propeller rotate close to the speed of sound, the
propeller will be extremely loud, and lose thrust (Konz et al.). Therefore, propeller driven
airplanes can only travel so fast.
Propellers operate by using torque from the shaft to turn the blades. The blades are mini
airfoils that generate a pressure difference from the front of the propeller to the back of the
2
propeller, a high pressure behind and low pressure in the front (Konz et al.). This pressure
difference pushes the airplane forward. Propellers are twisted to create equal lift along the entire
blade. This twist can sometimes be up to 40 degrees, but the amount will depend on the purpose
of the blade (Konz et al.).
There are many different ways to improve propeller efficiency. One way would be by
adding more propellers, counter rotating propellers, or variable pitch propellers. This would
allow for more chunks of air to be pulled through the propeller, creating a greater pressure
difference and therefore more thrust.
The counter rotating propellers have an advantage, because the second set of blades are
able to recover part of the slipstream rotational energy that would be lost on conventional single
screw systems (Carlton).
Having the ability to adjust the angle of the propeller has huge effects on efficiency of the
propeller. It allows that propeller to be at the most efficient angle for each phase of flight (Konz
et al.). For example, as the blade angle is decreased, the engine RPM is higher, resulting in more
thrust (Wood, 2022). A low blade angle is most efficient during takeoff. However, during climb
and cruise, the blade angle will be increased because the propellers do not need to produce as
much thrust during these phases (Wood, 2022). The angle of the blades are increased, causing
more resistance on the blades as they spin, thus causing a decrease in RPM. This larger angle
allows the blade to take much larger chunks out of the air, causing the airplane to move much
further with each rotation.
Brake horsepower is the available power from the engine (Mlblevins, 2009). However, as
that power is converted from the engine to the crankshaft, it loses some power. The force that is
delivered to the crankshaft is the shaft horsepower (Hendricks, 2023). This rotational force is
3
what spins the propeller of the airplane. Thrust horsepower is the actual force of the propeller.
This is dependent on the efficiency of the airfoil that is the propeller. If the engine, crankshaft,
and propeller were 100% efficient, then the amount of brake horsepower delivered from the
engine would be the same as the thrust horsepower (
Thrust horsepower definition & meaning
).
As altitude increases, air density decreases. This is because there is less atmosphere
weighing down on the air at higher altitudes, and there is less gravity as one increases altitude.
Lower air density relates to how densely air molecules are grouped together in a given area. For
example, on a standard day at sea level the air density is 0.0765 lb/ft^3, and on a standard day at
30,000 feet the air density is 0.02272 lb/ft^3 (Admin, 2020). Because of this decrease in air
density, the propeller will have less performance.
The propeller is a rotating airfoil that generates lift along the longitudinal axis of the
airplane. To do this the airfoil rotates and creates a low pressure on the front of the propeller and
a high pressure behind it, resulting in thrust that pushes the plane forward. When the air density
is low at high altitudes, the propeller cannot generate as much thrust as before because there are
less air molecules readily available.
Your preview ends here
Eager to read complete document? Join bartleby learn and gain access to the full version
- Access to all documents
- Unlimited textbook solutions
- 24/7 expert homework help
4
Resources
Admin. (2020, March 30).
How do you find the density of air at altitude?
. MassInitiative.
https://massinitiative.org/how-do-you-find-the-density-of-air-at-altitude/#:~:text=The
%20tropospheric%20tabulation%20continues%20to%2011%2C000%20meters
%20%2836%2C089,Standard%20Atmosphere%20Air%20Properties%20–%20Imperial
%20%28BG%29%20Units
Carlton. (n.d.).
Contra-rotating propeller
. Contra-Rotating Propeller - an overview |
ScienceDirect Topics.
https://www.sciencedirect.com/topics/engineering/contra-rotating-
propeller
Hendriks, A. (2023, May 12).
Difference between shaft horsepower and horsepower
. Compare
Factory.
https://comparefactory.com/difference-between-shaft-horsepower-and-
horsepower/
Konz, C., Happel, C. C., Turano, D., Daniel, G., Bigger, M., & Leishman, G. J. (n.d.).
Reciprocating engine/propeller
. Introduction to Aerospace Flight Vehicles.
https://oer.pressbooks.pub/introductiontoaerospaceflightvehicles/chapter/reciprocating-
engine-propeller/
Merriam-Webster. (n.d.).
Thrust horsepower definition & meaning
. Merriam-Webster.
https://www.merriam-webster.com/dictionary/thrust%20horsepower
Mlblevins. (2009, June 1).
What is Brake Horsepower (bhp)?
. Science Struck.
https://sciencestruck.com/what-is-bhp-brake-horsepower
5
Reciprocating engine
. Reciprocating engine - Energy Education. (n.d.).
https://energyeducation.ca/encyclopedia/Reciprocating_engine
Wood, A. (2022, September 28).
Aircraft Propeller theory
. AeroToolbox.
https://aerotoolbox.com/propeller/
Related Questions
what is the average speed of the flame-front inside the cylinder, negating turbulence?
arrow_forward
Which does makes the volumetric efficiency of the reciprocating engine
decrease? *
Low cylinder head temperatures
Improper valve timing
Full throttle operation
Sharp bends in the induction system
High carburetor air temperatures
When the piston reaches the bottom center it reverses direction and starts
moving up on the compression stroke. TRUE OR FALSE? *
Your answer
What happens with the volumetric efficiency when the engine's heat increases?
Your answer
As an aircraft climbs, air density decreases, thereby decreasing the amount of air
in the fuel/air mixture. This results in a vibrant air/fuel mixture which causes a
reduction in engine power. TRUE OR FALSE? *
Your answer
arrow_forward
Swirl vanes in the combustion chamber:
increase the velocity of the airflow
reduce the axial velocity of the airflow
O prevent compressor stall
arrow_forward
I need help on answering these from the following question below:
1. you need to calculate the mass flow rate of air inducted to the engine
2. from your answer, in the question above, you need to determine the ratios of heat release in the flue gas and cooling water against input power for the engine
3. you need to discuss how emissions can be minimised with regards to the engine
The question:
A diesel engine is a type of internal combustion engine that uses compression ignitio to turn energy in diesel fuel to rotary mechanical energy. A four-stroke (i = 0.5 for fourstroke engine, stroke = 150 mm and revolution = 2100 min−1) diesel engine with 6 cylinders and an effective specific fuel consumption of 0.23 kg kW−1h−1 has an effective and indicated mean pressure of 9.2 bar and 6.8 bar, respectively, and a compression ratio of 17. The ambient temperature and pressure of the diesel engine is 30 ℃ and 1.017 bar, respectively, and the temperature of the exhaust gas is 650 ℃. The clearance…
arrow_forward
15. The impulse-reaction blade is twisted along its length so that:
The gas flow is decelerated through the nozzle guide vanes.
The gas does equal work along the whole of its length.
There is a greater angle at the base than at the tip.
The
gas
flow is accelerated through the turbine.
arrow_forward
Part A. How much heat goes into this gas per cycle?
Express your answer to two significant figures and include the appropriate units.
Part C. How much heat is ejected by the gas per cycle?
Express your answer to two significant figures and include the appropriate units.
Part E.How much work does this engine do each cycle?
Express your answer to two significant figures and include the appropriate units.
Part F.What is the thermal efficiency of the engine?
Express your answer as a percentage to two significant figures.
arrow_forward
I want answer for these
arrow_forward
Q6. Answer following questions by True or False
1. Injector that sprays into the intake system operate at the same pressure of the carburetor.
2. Swirl in the cylinder enhances the mixing of air and fuel to give a homogeneous mixture
in the very short time.
3. Flame development region is consumed 80% of the air-fuel mixture.
4. Maximum temperature and pressure of flame propagation occurs somewhere between 20"
and 30° aTDC for a four-stroke cycle.
5. Knock caused by self-ignition could occur in S1 engines as well as in CI engines.
6. Detonation is the minimum combustion time possible without actually having an
instantaneous constant-volume reaction.
7. Combustion in a CI engine is a flame front moving through a homogeneous mixture.
8. Fuel injection time in CI engine is usually starting at about 15° bTDC and ending about
5° aTDC.
9. Exhaust blowdown occurs when the exhaust valve starts to open somewhere around 60°
to 40° bTDC.
10. The average temperature in the exhaust system of a…
arrow_forward
Answer the following statements by True or False:
1. Superchargers are used to increase the power of an IC engine by raising the
intake pressure and thus allowing more fuel to be burned per cycle.
2. Scavenging is the process by which the oil rings scrape the lubricating oil
from the cylinder wall and allow the oil to return to the oil pan.
3. The power output of a two-stroke engine equals that of a four-stroke engine
for the same displacement.
4. After coolers are used after the compressor to drop the air temperature and thus
increase its density.
5. The rotary engine has the advantages of better sealing of high pressure gases
and less wear on seals.
arrow_forward
SEE MORE QUESTIONS
Recommended textbooks for you
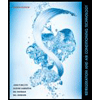
Refrigeration and Air Conditioning Technology (Mi...
Mechanical Engineering
ISBN:9781305578296
Author:John Tomczyk, Eugene Silberstein, Bill Whitman, Bill Johnson
Publisher:Cengage Learning
Related Questions
- what is the average speed of the flame-front inside the cylinder, negating turbulence?arrow_forwardWhich does makes the volumetric efficiency of the reciprocating engine decrease? * Low cylinder head temperatures Improper valve timing Full throttle operation Sharp bends in the induction system High carburetor air temperatures When the piston reaches the bottom center it reverses direction and starts moving up on the compression stroke. TRUE OR FALSE? * Your answer What happens with the volumetric efficiency when the engine's heat increases? Your answer As an aircraft climbs, air density decreases, thereby decreasing the amount of air in the fuel/air mixture. This results in a vibrant air/fuel mixture which causes a reduction in engine power. TRUE OR FALSE? * Your answerarrow_forwardSwirl vanes in the combustion chamber: increase the velocity of the airflow reduce the axial velocity of the airflow O prevent compressor stallarrow_forward
- I need help on answering these from the following question below: 1. you need to calculate the mass flow rate of air inducted to the engine 2. from your answer, in the question above, you need to determine the ratios of heat release in the flue gas and cooling water against input power for the engine 3. you need to discuss how emissions can be minimised with regards to the engine The question: A diesel engine is a type of internal combustion engine that uses compression ignitio to turn energy in diesel fuel to rotary mechanical energy. A four-stroke (i = 0.5 for fourstroke engine, stroke = 150 mm and revolution = 2100 min−1) diesel engine with 6 cylinders and an effective specific fuel consumption of 0.23 kg kW−1h−1 has an effective and indicated mean pressure of 9.2 bar and 6.8 bar, respectively, and a compression ratio of 17. The ambient temperature and pressure of the diesel engine is 30 ℃ and 1.017 bar, respectively, and the temperature of the exhaust gas is 650 ℃. The clearance…arrow_forward15. The impulse-reaction blade is twisted along its length so that: The gas flow is decelerated through the nozzle guide vanes. The gas does equal work along the whole of its length. There is a greater angle at the base than at the tip. The gas flow is accelerated through the turbine.arrow_forwardPart A. How much heat goes into this gas per cycle? Express your answer to two significant figures and include the appropriate units. Part C. How much heat is ejected by the gas per cycle? Express your answer to two significant figures and include the appropriate units. Part E.How much work does this engine do each cycle? Express your answer to two significant figures and include the appropriate units. Part F.What is the thermal efficiency of the engine? Express your answer as a percentage to two significant figures.arrow_forward
- I want answer for thesearrow_forwardQ6. Answer following questions by True or False 1. Injector that sprays into the intake system operate at the same pressure of the carburetor. 2. Swirl in the cylinder enhances the mixing of air and fuel to give a homogeneous mixture in the very short time. 3. Flame development region is consumed 80% of the air-fuel mixture. 4. Maximum temperature and pressure of flame propagation occurs somewhere between 20" and 30° aTDC for a four-stroke cycle. 5. Knock caused by self-ignition could occur in S1 engines as well as in CI engines. 6. Detonation is the minimum combustion time possible without actually having an instantaneous constant-volume reaction. 7. Combustion in a CI engine is a flame front moving through a homogeneous mixture. 8. Fuel injection time in CI engine is usually starting at about 15° bTDC and ending about 5° aTDC. 9. Exhaust blowdown occurs when the exhaust valve starts to open somewhere around 60° to 40° bTDC. 10. The average temperature in the exhaust system of a…arrow_forwardAnswer the following statements by True or False: 1. Superchargers are used to increase the power of an IC engine by raising the intake pressure and thus allowing more fuel to be burned per cycle. 2. Scavenging is the process by which the oil rings scrape the lubricating oil from the cylinder wall and allow the oil to return to the oil pan. 3. The power output of a two-stroke engine equals that of a four-stroke engine for the same displacement. 4. After coolers are used after the compressor to drop the air temperature and thus increase its density. 5. The rotary engine has the advantages of better sealing of high pressure gases and less wear on seals.arrow_forward
arrow_back_ios
arrow_forward_ios
Recommended textbooks for you
- Refrigeration and Air Conditioning Technology (Mi...Mechanical EngineeringISBN:9781305578296Author:John Tomczyk, Eugene Silberstein, Bill Whitman, Bill JohnsonPublisher:Cengage Learning
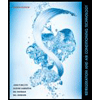
Refrigeration and Air Conditioning Technology (Mi...
Mechanical Engineering
ISBN:9781305578296
Author:John Tomczyk, Eugene Silberstein, Bill Whitman, Bill Johnson
Publisher:Cengage Learning