Unit VII MOS 6625
docx
keyboard_arrow_up
School
East Tennessee State University *
*We aren’t endorsed by this school
Course
MISC
Subject
Mechanical Engineering
Date
Feb 20, 2024
Type
docx
Pages
13
Uploaded by EarlResolveTarsier6706
1
SYSTEMS SAFETY PROGRAM PLAN
System Safety Program Plan
Marvin Heflin
Columbia Southern University
2
SYSTEMS SAFETY PROGRAM PLAN
Abstract
TBS Precisions utilizes a machine in plasma cutting, which cuts metal to engineering specifications. Over the last few years of operation, investigation of understanding quantitative risk value related to plasma cutting to the estimate of the organizations system of nay failures that may have occurred. The program plan observes to recognize if implementing preventions in the workplace to reduce injuries and enhance protection with personal protective equipment will be required. The following provides detailed information that creates a system safety plan by creating a step-by-step process that addresses the system controls, analysis, and safety regulations. In addition to the analysis, diagrams are provided to assist in further understanding and development of the safety system plan. The plan focuses on the engineering evaluation of the
plasma system to find hazardous areas. Improvement of safety by a management system to understand the cause. Modify critical areas within the work system to reduce risks introduced. Lastly, implementing the plan and continuously monitoring the controlled work system by checking each step for the effectiveness in place and for improvements.
3
SYSTEMS SAFETY PROGRAM PLAN
Systems Safety Program Plan
At TBS Precision, it is imperative to develop a Systems Safety Program Plan that adequately addresses the important functions of a Plasma Cutter and its operations within the facility. In doing so, the system will be thoroughly examined and analyzed. The analysis will determine specific risk involved and discuss the potential hazards that are common within plasma cutting operations and within the general industry. The hazard controls will follow the guidelines set forth by the Occupational Safety and Health Administration. Risk identifiers will be utilized using a risk matrix to better assess workplace risk and provide necessary feedback on improvements in the workflow or operational area.
Defined Objectives
The overall objectives in the development of the system safety plan are to provide organizational process to perform proper workplace execution of job tasks relating to plasma cutting. Specific Safety objectives include:
Prevention of lost time injuries
Workplace hazard prevention, reduction, or elimination
Prevention of occupational exposure with the use of PPE and ventilation The system safety plan (SSP) provides knowledge and understanding through acknowledging the safety risk through the workplace daily operations within the facility. Furthermore, objectives are designed to help identify and bring forth acceptable compliance to procedures. In Image 1, depicts a qualitative approach of the flow for organizations input to have
different outcomes resulted. In Table 1, objective is to reduce accident cost through preventative measures given by an example from quantitative approach.
Your preview ends here
Eager to read complete document? Join bartleby learn and gain access to the full version
- Access to all documents
- Unlimited textbook solutions
- 24/7 expert homework help
4
SYSTEMS SAFETY PROGRAM PLAN
Image 1: Qualitative Review
European Commission, (2011, November).
Table 1: Quantitative Review Manuele, F. A. (2011, January).
5
SYSTEMS SAFETY PROGRAM PLAN
System Description
The use of a standardized plasma cutting machine with the use of an overhead crane attachment. For standard operation, the system will be welding a cylinder container of large metal sheet for containers or engineering drawings that will include cut outs. Incorporating the overhead crane provides the plasma cutter to place the cutouts. The newly formed material will then be moved manually or by forklift to assembly workstation. After metal material, has been moved to the assembly, workers will use devices such as a grinder and spot welder to correct or smooth such surfaces. The use of a metal bending device may be used to place the metal into a curved shape. Material will be measured to certify lengths are in accordance with the engineering specifications given out to the specific metal. The table Hazard Identification
Hazard identification are the known hazards and hazards that have been identified through previous workplace experiences and within similar areas throughout the plant and on an overall general industry. Utilizing the Hazard Management Process will provide adherence to safety guidelines and strict adherence the Occupational Safety and Health Administration (OSHA) regulations for General Industry 29 CFR 1910. OSHA addresses welding within 29 CFR 1910.251 Definitions, 29 CFR 1910.52 General Requirements, 29 CFR 1910.253 Oxygen-
fuel Gas Welding and Cutting, 29 CFR 1910.254 ARC welding and cutting, and 1910.255 Resistance welding (Occupational Safety and Health Administration, n.d.). The Preliminary Hazards List includes (
South Australian Department of Education and Children’s Services
, n.d.):
Electric Shock
Noise Damage
6
SYSTEMS SAFETY PROGRAM PLAN
Body burns
Radiation Burns
Fumes
Noxious gas
Flying Sparks Hazard Analysis
The Hazard Analysis process is a systematic, comprehensive method to identify, evaluate. And control hazards within the system (Bahr, 2015). A risk matrix system defines the Hazard Severity
Categories and Descriptions in Image 2. Image 3 depicts the risk matrix table of the color’s references to the ranking of a hazardous even occurring.
Image 2: Hazard Severity Category & Definition
Bahr, N. J. (2015).
Your preview ends here
Eager to read complete document? Join bartleby learn and gain access to the full version
- Access to all documents
- Unlimited textbook solutions
- 24/7 expert homework help
7
SYSTEMS SAFETY PROGRAM PLAN
Image 3: Risk Matrix Site Safe. (n.d.).
Risk Evaluations
To further determine the risk, a What-Analysis is conducted using the following questions:
a.
What if the overhead crane fails?
b.
What if the overhead crane rigging fails? c.
What if the plasma cutter gas leaks?
d.
What is the plasma cutter runs out of gas?
e.
What if the plasma cutter runs out of coolant?
f.
What if the plasma cutter needs to be reset to a different height?
g.
What if the ventilation is improper?
h.
What if the temperature is too hot?
i.
What if workers are wearing incorrect PPE?
j.
What if welding fumes exceed safe limits?
8
SYSTEMS SAFETY PROGRAM PLAN
k.
What if combustible materials are within the work area?
Hazard Controls
After the creation and design of the of the plasma cutting system, the analysis conducted through the previous steps. Of corrective actions need to be taken hazard controls will be incorporated to either prevent or reduce identified hazards. Overhead Crane Loads
: Cranes connected to plasma cutters must be ensured that all devices and tools are inspected before and after operations are conducted. Anyone involved in the operations of these devices must be trained and certified for operations. Plasma Cutter
: Before and after operations of the plasma cutter, all plasma mechanism must be inspected such as tube line, coolant levels, gauges, etc. Inspection should check for properly functioning hardware and leaks of any coolant and gas. Additionally, coolant levels should be properly maintained. Lastly, anyone involved in the operations of these devices must be trained and certified for operations. Flying Debris
: All employees performing grinding, cutting, or manual labor that contains the possibility of flying debris will use approved eye and face shields in accordance with the American National Standards Institute (ANSI)/ International Society of Exposure Analysis (ISEA) Z87.1-2020: American National Standard for Occupational and Educational Personal Eye and Face Protection Device (Kelechava, 2020).
UV Light
: All welders and those in direct area of the welding shall use welding goggles or helmets and any additional appropriate Personal Protective Equipment (PPE). Welding curtains will be utilized where applicable.
Hot Surfaces: Workers shall use heat and flame retardant clothing to prevent burns.
9
SYSTEMS SAFETY PROGRAM PLAN
Gases
: As standard gases used in the plasma cutter include a mixture of argon and Hydrogen gas. In some cases, a mixture of hydrogen and nitrogen or methane and nitrogen may be used to cut varying material. Large quantities are kept outside of the facility and stored securely. The mixed cylinders will be brought in when needed to connect to the plasma cutter. No additional cylinders may be kept inside as an immediate back up. Fumes
: Due to the use of multiple gases and vapors that occur during the welding process, ventilation will be required. Monitors will be installed to monitor for hazardous levels and forced
air ventilation shall be installed to eliminate hazardous levels. During a forced air ventilation being conducted, a stop work will be called, and workers must leave the area until the area is within the safe level. If applicable, ventilation hood should be installed to reduce fumes during welding operations. Lastly, fans shall be installed along with air scrubbers to maintain safe working conditions. Work Area: The work area shall be maintained with proper housekeeping protocols. The walkways must be properly marked and clear of all debris.
Verification of Controls
Employees shall have a daily safety brief of protocols along with their worksite inspections before starting plant operations with the team lead. Supervisors will conduct a weekly formal inspection. Monthly maintenance inspections shall be conducted on the plasma cutter. Semi-Annual safety audit will be conducted to properly verify worksite is properly created and safety regulations are properly adhered too. Risk Assessment
The overall risk assessment has been determined by using the risk matrix discussed in section 4. If risk is determined to be high, it will be noted under risk level “High” with
Your preview ends here
Eager to read complete document? Join bartleby learn and gain access to the full version
- Access to all documents
- Unlimited textbook solutions
- 24/7 expert homework help
10
SYSTEMS SAFETY PROGRAM PLAN
highlighted in red, which determines that the overall level of risk is unacceptable and worksite review must be conducted to determine what hazard controls will need to be installed before work may be conducted. If risk is determined as moderate, it will be noted as “Moderate” and highlighted in yellow. The moderate risk will be viewed as undesirable and work may be required to reduce hazards before being given the approval to begin work. If risk is determined to
be low, it will be noted as “Low” and highlighted in green. In the low-risk determination, hazard controls are acceptable, and the hazard risk has been reduced to safe working levels and operation may be conducted without additional steps taken. Safety Control Structure Diagram
Image 4: Process of plasma system Bhattacharyya, B., & Doloi, B. (2020).
Planned Periodic System Review
11
SYSTEMS SAFETY PROGRAM PLAN
During the formal weekly review by the supervisor and through the semi-annual safety audit of the worksite will provide a thorough inspection and determination of proper procedure and recommended changes. If any gaps or noted hazards during the inspections or audits, corrective actions will take place. Using a monthly maintenance inspection, the plasma cutter will be reviewed to properly function furthering the overall risk reduction of the worksite. In the three formal system reviews, the process will be maintained, accessed, and reconstructed as needed.
12
SYSTEMS SAFETY PROGRAM PLAN
References
Bahr, N. J. (2015). System safety engineering and risk assessment: A practical approach (2nd ed.). CRC Press. Bhattacharyya, B., & Doloi, B. (2020). Chapter Four - Machining processes utilizing thermal energy
. ScienceDirect. Retrieved January 10, 2022, from https://www.sciencedirect.com/science/article/pii/B9780128128947000049 European Commission. (2011, November). Socio-economic costs of accidents at work and work-
related ill health
. Retrieved January 10, 2022, from file:///C:/Users/User/Downloads/BenOsh_Report_DEF.pdf Kelechava, B. (2020, April 20). ANSI/ISEA Z87.1-2020: Current Standard for Safety Glasses
. ANSI. Retrieved January 10, 2022, from https://blog.ansi.org/2020/04/ansi-isea-z87-1-
2020-safety-glasses-eye-face/#gref Manuele, F. A. (2011, January). Accident Costs Rethinking ratios of indirect to direct costs
. Retrieved January 10, 2022, from https://aeasseincludes.assp.org/professionalsafety/pastissues/056/01/039_047_F2Manuele_
0111Z.pdf Occupational Safety and Health Administration. (n.d.). Hazards and Solutions
. Welding, Cutting, and Brazing. Retrieved January 10, 2022, from https://www.osha.gov/welding-
cutting-brazing/hazards-solutions
Your preview ends here
Eager to read complete document? Join bartleby learn and gain access to the full version
- Access to all documents
- Unlimited textbook solutions
- 24/7 expert homework help
13
SYSTEMS SAFETY PROGRAM PLAN
Occupational Safety and Health Administration. (n.d.). Standards
. Welding, Cutting, and Brazing. Retrieved January 10, 2022, from https://www.osha.gov/welding-cutting-
brazing/standards Site Safe. (n.d.). Risk Control
. Retrieved January 10, 2022, from https://www.sitesafe.org.nz/guides--resources/practical-safety-advice/risk-control/ South Australian Department of Education and Children’s Services. (n.d.). Plasma Cutter
. Safety
Operating Procedures. Retrieved January 10, 2022, from https://worksafe.tas.gov.au/__data/assets/word_doc/0017/540521/SWP_Plasma_Cutter_AS
532.doc
Related Documents
Related Questions
How are plasma cutting equipment classified? Enumerate, define each one.
What types of metals can be cut by plasma cutting equipment? Enumerate and define each.
arrow_forward
An in-depth analysis of the processes through which the technology connected with safety functions
arrow_forward
20
61. Flashbacks are common in gas welding process if metal surface are not cleaned.
Select one:
True
False
arrow_forward
QUESTION 1
What practical skills were taught and assessed in you Electronic Engineering lab? Choose one or more correct answers in the following list:
A. Soldering electronic components on a PCB
B. Working principles of a semiconductor diode.
C. Electronic PCB design
D. Soldering an IC on a PCB
E. De-soldering surface mount component techniques
F. Cleaning the soldering iron tip
QUESTION 2
Identify which safety equipment was used when you soldered the PCB (choose all which apply)
A. Safety Glasses
B. Fume Extractor
C. Gas Mask
D. Safety Boots
E. Heat-Proof Gloves
F. Solder Flux
50 points
Saved
50 points
Saved
arrow_forward
What is the minimum and the maximum thickness of metal that can be cut using a plasma cutter? Explain each briefly.
arrow_forward
Why might IAV become less harmful with time?
arrow_forward
It says surface Temperature is not 125.49oC (look at picture I attached). What would be the correct value? Thank you.
arrow_forward
Correct the view that is incomplete.
Subject: blueprint for welders
arrow_forward
SEE MORE QUESTIONS
Recommended textbooks for you
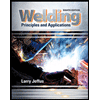
Welding: Principles and Applications (MindTap Cou...
Mechanical Engineering
ISBN:9781305494695
Author:Larry Jeffus
Publisher:Cengage Learning
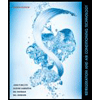
Refrigeration and Air Conditioning Technology (Mi...
Mechanical Engineering
ISBN:9781305578296
Author:John Tomczyk, Eugene Silberstein, Bill Whitman, Bill Johnson
Publisher:Cengage Learning
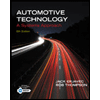
Automotive Technology: A Systems Approach (MindTa...
Mechanical Engineering
ISBN:9781133612315
Author:Jack Erjavec, Rob Thompson
Publisher:Cengage Learning
Related Questions
- How are plasma cutting equipment classified? Enumerate, define each one. What types of metals can be cut by plasma cutting equipment? Enumerate and define each.arrow_forwardAn in-depth analysis of the processes through which the technology connected with safety functionsarrow_forward20 61. Flashbacks are common in gas welding process if metal surface are not cleaned. Select one: True Falsearrow_forward
- QUESTION 1 What practical skills were taught and assessed in you Electronic Engineering lab? Choose one or more correct answers in the following list: A. Soldering electronic components on a PCB B. Working principles of a semiconductor diode. C. Electronic PCB design D. Soldering an IC on a PCB E. De-soldering surface mount component techniques F. Cleaning the soldering iron tip QUESTION 2 Identify which safety equipment was used when you soldered the PCB (choose all which apply) A. Safety Glasses B. Fume Extractor C. Gas Mask D. Safety Boots E. Heat-Proof Gloves F. Solder Flux 50 points Saved 50 points Savedarrow_forwardWhat is the minimum and the maximum thickness of metal that can be cut using a plasma cutter? Explain each briefly.arrow_forwardWhy might IAV become less harmful with time?arrow_forward
arrow_back_ios
arrow_forward_ios
Recommended textbooks for you
- Welding: Principles and Applications (MindTap Cou...Mechanical EngineeringISBN:9781305494695Author:Larry JeffusPublisher:Cengage LearningRefrigeration and Air Conditioning Technology (Mi...Mechanical EngineeringISBN:9781305578296Author:John Tomczyk, Eugene Silberstein, Bill Whitman, Bill JohnsonPublisher:Cengage LearningAutomotive Technology: A Systems Approach (MindTa...Mechanical EngineeringISBN:9781133612315Author:Jack Erjavec, Rob ThompsonPublisher:Cengage Learning
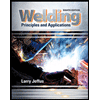
Welding: Principles and Applications (MindTap Cou...
Mechanical Engineering
ISBN:9781305494695
Author:Larry Jeffus
Publisher:Cengage Learning
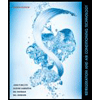
Refrigeration and Air Conditioning Technology (Mi...
Mechanical Engineering
ISBN:9781305578296
Author:John Tomczyk, Eugene Silberstein, Bill Whitman, Bill Johnson
Publisher:Cengage Learning
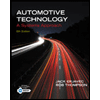
Automotive Technology: A Systems Approach (MindTa...
Mechanical Engineering
ISBN:9781133612315
Author:Jack Erjavec, Rob Thompson
Publisher:Cengage Learning