Starbucks Final Copy
docx
keyboard_arrow_up
School
St. Augustine's University *
*We aren’t endorsed by this school
Course
485
Subject
Management
Date
Nov 24, 2024
Type
docx
Pages
22
Uploaded by JudgeWallaby3248
Starbucks Supply chain 1
CASE STUDY REPORT ON STARBUCK’S SUPPLY CHAIN CHALLENGES
By[Name]
Course
Professor’s Name
Institution
Location of Institution
Date
Starbucks Supply chain 2
Case Study Report on Starbucks' Supply Chain Challenges
Assignment Task 1: Report
Introduction
Starbucks is a well-known brand because of its presence in more than 16,700 locations throughout the world. However, Starbucks' supply chain management has faced difficulties despite its profitability and ubiquity. This study explores the supply chain problems that Starbucks had in 2007 and 2008, which resulted in increased expenses and a drop in service quality. We will look at the function of the supply chain in a large corporation of Starbucks and its importance to the general operations and success of the company.
Starbucks Global Supply Chain
Starbucks' complex global supply chain is in charge of guaranteeing that each mug of coffee and related goods sold in its tens of thousands of locations across the globe reach customers in a reliable and timely manner (Lambert & Enz, 2017). The supply chain includes all procedures involved in procuring, producing, and distributing the goods to Starbucks retail
locations, ensuring they adhere to the high standards for which the company is renowned.
Key components of Starbucks' global supply chain include:
Sourcing and Procurement: Starbucks obtains coffee beans and other components from a variety of places around the world (Attaran, 2004). To make sure a consistent supply of superior raw materials, they keep in touch with coffee growers and suppliers.
Manufacturing and Distribution: To guarantee uniformity in taste and quality, the coffee beans undergo roasting and processed in centralized facilities after procurement (Chopra & Meindl, 2015). Then, the coffee and other goods are shipped to Starbucks locations throughout the world.
Starbucks Supply chain 3
Inventory Management: Starbucks has a strict inventory control system in place to make sure that there is never any excess wastage or product shortages and that products are always accessible to satisfy client demand (Chopra & Sodhi, 2014).
Logistics and Transportation: To get products to the retailers, efficient transportation is essential (Attaran, 2004). Coordination with numerous logistics service providers and transportation partners is required for this.
Quality Control: To guarantee that the coffee, food, and other associated items live up to Starbucks' high standards, stringent quality control procedures are in place (Chopra & Meindl, 2015).
Role of Supply Chain Function in a Multinational Company
The supply chain function is essential to the smooth operation of the business in a multinational corporation like Starbucks (Christopher, 2016). In a large, international firm like Starbucks, the supply chain plays a number of crucial roles and functions, such as:
Cost Management: The supply chain function is in charge of controlling the costs of sourcing, production, shipping, and distribution (Christopher, 2016). Starbucks strives
to minimize expenses in order to increase profitability, much like any other multinational.
Global Sourcing: Starbucks sources its coffee beans and other goods from many countries all over the world. The supply chain team is tasked with finding and assessing suppliers across the globe while taking into account elements like cost, sustainability, and quality (Delfmann, 2002). Starbucks is able to get the best raw materials while minimizing supply chain risks because to this worldwide sourcing strategy.
Logistics and transportation: Both locally and internationally, effective transportation is essential to getting supplies to the stores. To ensure prompt and affordable delivery,
Your preview ends here
Eager to read complete document? Join bartleby learn and gain access to the full version
- Access to all documents
- Unlimited textbook solutions
- 24/7 expert homework help
Starbucks Supply chain 4
the supply chain team works in concert with a variety of transportation and logistical suppliers (Christopher, 2016). This include managing delivery timetables, choosing the best warehouse sites, and choosing the best shipping routes.
Inventory Control: Starbucks has a strict inventory control system to make sure that there is never a lack of supplies or excess wastage that prevents it from meeting client demand (Chopra & Sodhi, 2014). Demand forecasting, safety stock management, and order replenishment procedures are necessary for efficient inventory management.
Quality Control: To guarantee that the coffee, food, and other associated items live up to Starbucks' high standards, strict quality control procedures are in place (Fawcett et al., 2014). To guarantee product quality and safety, the supply chain team works with suppliers, performing inspections and audits to make sure compliance.
Technology Integration: To improve the effectiveness of the supply chain, traceability,
and risk management, Starbucks makes use of digital technologies including IoT, blockchain, and AI (Christopher, 2016). Real-time data is provided by these technologies for tracking shipments, keeping an eye on inventory levels, and forecasting demand patterns. They also assist Starbucks in making data-driven decisions and reacting promptly to disturbances.
Collaboration with Key Suppliers:
Risk management: Operating beyond borders entails a number of hazards, including those related to geopolitics, the economy, and natural calamities (Chopra & Meindl, 2015). To maintain company continuity, the supply chain function evaluates and controls these risks.
Starbucks' global supply chain is a complex web of partners, partners' processes, and technologies that are necessary for providing customers with a consistent, high-quality coffee experience worldwide. 10-Point Plan for Starbucks' Future-Ready Supply Chain
Starbucks Supply chain 5
The case study's issues must be addressed in order to create a 10-point strategy that will guarantee Starbucks' supply chain function and its strategies continue to be pertinent to the company's organizational goals in the future. Here is a thorough strategy:
Improve the visibility and transparency of the supply chain by putting powerful tracking and analytics systems in place to keep an eye on the movement of goods and data in real-time (Gereffi et al., 2005). This will facilitate the quick identification of bottlenecks and inefficiencies. For a multinational corporation like Starbucks to maximize supply chain visibility and transparency, complex tracking and analytics systems must be implemented (Keong Leong et al., 1990). Real-time monitoring of product flow and information is possible
with these solutions, giving users insightful knowledge of the complete supply chain network (Lambert & Enz, 2017). Starbucks can quickly identify bottlenecks, inefficiencies, and potential disruptions by utilizing data analytics and IoT technologies.
Better demand forecasting can be achieved by investing in data analytics and artificial
intelligence. Starbucks can cut down on waste and improve product availability by properly forecasting consumer preferences (Lambert & Enz, 2017). For Starbucks' supply chain to be successful, investing in data analytics and AI for demand forecasting can improve inventory management, cut costs, and boost customer happiness.
Implement lean inventory management techniques to reduce holding costs and guarantee that products are accessible at the appropriate time and location (Mangan, Lalwani & Butcher, 2016). Better supplier cooperation and demand-driven replenishment are required for this.
Encourage solid relationships with important suppliers. Establish long-term contracts and engage in continual improvement projects for stability and cost-effectiveness (Monczka et al., 2015). Starbucks should promote strong, cooperative relationships with important suppliers in order to create a robust supply chain. This may entail participating in projects for
Starbucks Supply chain 6
ongoing improvement, exchanging knowledge, and working together to resolve problems. Long-term agreements can bring stability, encourage productivity, and produce a win-win situation where suppliers and Starbucks both gain from cost-efficiency, dependability, and mutual progress (Monczka et al., 2015). Such alliances increase the resilience of the supply chain and enable speedier reactions to shifting market conditions.
Streamline Distribution to cut expenses and accelerate delivery times, rationalize the distribution network (Monczka et al., 2015). For effective product flow, take into account regional hubs. Starbucks needs to improve the effectiveness of its distribution system. By evaluating the number and location of distribution centers, the network can be rationalized, which can result in lower costs and quicker deliveries (Chopra & Meindl, 2015). Strategically
implementing regional hubs can improve product flow, improve response to local demand changes, shorten lead times, and improve overall supply chain agility. In order to exceed consumer expectations and cut operating costs, this strategy is essential.
Initiatives related to sustainability, that is to include sustainability in your supply chain strategy (Lambert & Enz, 2017). To support Starbucks' dedication to environmental responsibility, take into account eco-friendly shipping methods, sourcing procedures, and packaging.
IoT, blockchain, and AI are examples of digital technologies that should be included into supply chains to improve traceability, efficiency, and risk management (Lambert & Enz, 2017). This will make it possible for Starbucks to react to disturbances rapidly.
Invest in the supply chain team's education and training (Lambert & Enz, 2017). Give
them the tools they need to adjust to shifting market conditions and technological advancements. This includes instruction on risk management, sustainability, and data analytics. Starbucks needs to place a higher priority on personnel development to ensure a dependable and flexible supply chain. It is essential to make investments in the supply chain
Your preview ends here
Eager to read complete document? Join bartleby learn and gain access to the full version
- Access to all documents
- Unlimited textbook solutions
- 24/7 expert homework help
Starbucks Supply chain 7
team's education and growth (Christopher, 2016). Giving them knowledge in data analytics, sustainability principles, and risk management enables them to successfully traverse rapidly changing market dynamics and technological advancements (Lambert & Enz, 2017). Starbucks can proactively identify areas for improvement, advance sustainability initiatives, and manage risks with the help of an educated and competent workforce, which will boost the
supply chain's overall success and competitiveness.
Establish a culture of continual improvement among the supply chain team members (Christopher, 2016). Encourage creativity and quick thinking when adjusting to market developments. Review the supply chain's efficiency and performance on a regular basis. For Starbucks' supply chain to succeed, a culture of continuous improvement must be implemented. Encourage the supply chain team to embrace innovation and agility so that they
can respond quickly to opportunities and changes in the market (Christopher, 2016). Assess performance and cost-effectiveness frequently to find areas that could be improved. Using this strategy, Starbucks is able to maintain its competitiveness and responsiveness in a fast-
paced market while also steadily increasing operational effectiveness, lowering expenses, and
raising customer satisfaction. Starbucks can strengthen the agility and resilience of its supply chain by promoting a culture of continuous improvement.
Starbucks can make certain that its supply chain function stays pertinent to the organization's goals in the future by putting this 10-point plan into practice. It will not only deal with the problems currently being faced, but it will also get Starbucks ready to adjust to shifting consumer tastes and market realities.
Strategic Supply Chain Management Approaches for Starbucks
Starbucks can accomplish its objectives by utilizing a range of supply chain management techniques that boost productivity, cut expenses, and promote the company's dedication to customer pleasure and sustainability. Here are three crucial tactics:
Starbucks Supply chain 8
Lean Supply Chain Management:
The goals of lean supply chain management are to cut waste, improve workflow, and boost productivity. Starbucks can achieve its objectives by applying lean principles in the following ways:
a. Reducing Inventory Costs: Starbucks may cut back on storage and carrying expenses by keeping minimal stocks. This guarantees that products are available and fresh, which improves customer happiness (Christopher, 2016).
b. Accurate Demand Forecasting: Lean concepts support this practice. This keeps popular items in stock at all times and helps Starbucks avoid overproduction and waste.
c. Streamlined operations: Starbucks can improve the responsiveness and efficiency of its production, distribution, and procurement operations. This shortens lead times and increases delivery dependability.
d. Continuous Improvement: Starbucks is able to effectively adjust to shifting consumer tastes and market situations because to lean management, which promotes a culture of continuous improvement (Christopher, 2016).
Supplier Relationship Management (SRM)
For Starbucks to guarantee a consistent supply of premium coffee and other products, strong supplier connections are essential. Putting SRM strategies into practice can be advantageous in the following ways:
a. Collaboration with Key Suppliers: Starbucks can connect its supply chain with its business objectives by closely collaborating with its key suppliers (Christopher, 2016). Collaboration can result in cost savings, higher-quality output, and environmentally friendly sourcing.
b. Risk Mitigation: A successful SRM entails both risk management and evaluation. This guarantees that Starbucks can react to potential supply-chain disruptions, such as weather-
related occurrences that affect coffee production.
Starbucks Supply chain 9
c. Innovation: Working together can promote innovation. Suppliers may provide fresh goods, eco-friendly sourcing techniques, or packaging options that support Starbucks' goals (Christopher, 2016).
d. Long-Term Commitments: Making long-term agreements with important suppliers can help to stabilize the supply chain, reduce price volatility, and guarantee a steady supply.
Sustainable Supply Chain Practices
As a company with a strong commitment to sustainability, Starbucks may better meet customer expectations by incorporating sustainable practices into its supply chain. This tactic entails:
a. Sustainable procuring: Starbucks' environmental and social responsibility objectives can be
met by procuring ingredients ethically and sustainably, including coffee beans. Customers who are becoming more interested about the product's origins are attracted to this method (Christopher, 2016).
b. Eco-Friendly Transportation: By utilizing eco-friendly transportation strategies, such as electric or hybrid delivery cars, Starbucks may lessen its carbon impact. This helps it achieve its environmental goals and could ultimately save money.
c. Waste Reduction: Implementing waste reduction strategies like recycling and responsible packaging not only supports Starbucks' environmental objectives, but it can also cut costs by lowering the cost of garbage disposal (Christopher, 2016).
d. Consumer Engagement: Starbucks can encourage responsible consumption and waste minimization among its customers through marketing and educational initiatives.
Starbucks will be able to efficiently connect its supply chain with its company goals thanks to these supply chain management techniques. Starbucks can improve its supply chain to deliver a consistent and outstanding customer experience while simultaneously fulfilling
Your preview ends here
Eager to read complete document? Join bartleby learn and gain access to the full version
- Access to all documents
- Unlimited textbook solutions
- 24/7 expert homework help
Starbucks Supply chain 10
its sustainability and cost-efficiency goals by embracing lean principles, developing strong supplier relationships, and implementing sustainable practices.
D) Instituted Strategies
During 2007 and 2008, Starbucks experienced substantial supply chain difficulties, such as increased costs, declining revenues, and subpar service (Christopher, 2016). The business adopted a number of approaches to maintain supplier connections and made use of information technology to forge closer ties with its suppliers in order to address these difficulties. The efficacy of these tactics is assessed in this paper.
1. Supplier Relationship Management (SRM):
Starbucks understood the value of preserving solid connections with its suppliers to successfully solve supply chain difficulties (Christopher, 2016). The business implemented many tactics to strengthen these connections:
a. Collaboration and communication were key focuses for Starbucks, who prioritized open and honest contact with its suppliers. Regular meetings, feedback sessions, and group problem-solving were all part of this (Christopher, 2016). Understanding the strengths and problems of the supplier was made easier by effective communication.
b. Long-term Contracts: With important suppliers, Starbucks went into long-term agreements.
These agreements offered both sides stability and promoted spending on raising efficiency and quality (Christopher, 2016).
c. Supplier Performance Metrics: To analyze supplier performance in an unbiased manner, the
organization created key performance indicators (KPIs). These measurements assisted in identifying areas in need of improvement and inspired suppliers to achieve Starbucks' requirements for quality and on-time delivery (Christopher, 2016).
Starbucks Supply chain 11
d. Programs for Supplier Development: Starbucks funded efforts for Supplier Development. These initiatives sought to improve the capacities of suppliers in order to guarantee a steady supply of high-quality goods.
2. Information Technology (IT) Utilization:
Starbucks understood how information technology might be used to develop and maintain supplier relationships. The business used IT strategies to improve supplier relationships and streamline business processes:
a. Starbucks introduced integrated supply chain management systems, allowing for the tracking and monitoring of inventory, orders, and deliveries in real-time. This increased transparency and visibility made it simpler for both Starbucks and its suppliers to successfully manage the supply chain (Christopher, 2016).
b. Vendor Portals: In order to give suppliers easy access to order details, predictions, and performance indicators, Starbucks established vendor portals and online platforms (Christopher, 2016). This improved teamwork, cut back on manual tasks, and improved order
fulfillment accuracy.
c. Data Analytics: To find trends, demand patterns, and supplier performance, Starbucks used data analytics technologies. The business made wise choices to improve inventory levels, shorten lead times, and save money by utilizing data-driven insights.
d. Forecasting and Demand Planning: Starbucks was able to predict customer preferences more accurately and optimize inventory levels thanks to sophisticated forecasting and demand planning technologies (Christopher, 2016). This reduced waste and helped suppliers get ready for changes in demand.
3. Continuous Improvement:
Starbucks Supply chain 12
Starbucks implemented a philosophy of continuous improvement, assessing and modifying its supplier relationship methods on a regular basis. The organization was able to retain supply chain resilience and adjust to shifting market conditions thanks to this strategy.
E) Recommendations
Here are some suggestions to increase Starbucks' supply chain efficiency based on a review of their supply chain issues:
Streamline Supply Chain Operations:
Starbucks has to concentrate on streamlining its supply chain activities. To accomplish this, it should review its sourcing and distribution plans in order to reduce complexity (Christopher, 2016). Reduce expenses and improve supply chain control by evaluating and optimizing the use of third-party logistics providers (3PLs) and possibly bringing some tasks in-house.
Enhance Supplier Collaboration:
Starbucks needs to improve its relationships with its major suppliers. To guarantee a steady and high-quality supply of coffee beans, the business should make an investment in long-term partnerships with dependable suppliers and collaborate closely with them (Christopher, 2016). Better coordination of the efforts between Starbucks and its suppliers can be achieved by creating a single business plan and exchanging market knowledge.
Invest in IT Solutions:
Starbucks has to keep spending money on IT options that help improve its supply chain. The organization can increase order accuracy and decrease excess inventory by implementing sophisticated inventory management and demand forecasting tools. Data analytics can offer insightful information about consumer preferences and market trends, assisting Starbucks in making wise supply chain decisions.
Improve Outsourcing Decisions:
Your preview ends here
Eager to read complete document? Join bartleby learn and gain access to the full version
- Access to all documents
- Unlimited textbook solutions
- 24/7 expert homework help
Starbucks Supply chain 13
Starbucks needs to reevaluate its outsourcing choices and review the performance of its third-party logistics providers. Starbucks should look into alternate options if some suppliers continuously perform poorly or add to costs (Christopher, 2016). This could entail revising contracts, looking for more dependable partners, or, as was already indicated, bringing some logistics tasks in-house.
Focus on Sustainability:
Starbucks should maintain its dedication to sustainability throughout its supply chain. Along with promoting ecologically sustainable coffee manufacturing, this also entails collaborating with suppliers to ensure ethical sourcing procedures. Sustainability initiatives can help a brand's reputation and draw in an increasing number of eco-aware customers.
Continuous Performance Monitoring:
Starbucks' supply chain needs a reliable performance monitoring solution. Monitoring
key performance indicators (KPIs) such as supplier performance, cost-to-serve metrics, and on-time deliveries on a regular basis can assist spot problems before they become serious problems (Christopher, 2016).
Invest in Employee Training:
To make sure that its team has the capabilities to effectively solve supply chain concerns, Starbucks should make investments in employee training and development. Continuing education on cutting-edge technologies and industry best practices is part of this.
By combining operational upgrades, supplier cooperation, and technological expenditures, Starbucks can overcome its supply chain difficulties. Starbucks can improve the
effectiveness of its supply chain, cut costs, and guarantee a steady and high-quality supply of coffee beans to its thousands of locations throughout the world by putting these suggestions into practice.
Starbucks Supply chain 14
Assignment Task 2: Shipping Scenario
1.Risk Assessment Plan for Importing GT 6 Bladed Rotor
Power Plant International's importation of the GT 6 Bladed Rotor is a crucial operation, and various potential logistical issues must be resolved to guarantee its successful delivery and installation (Wild, 2019). Here is a plan for risk assessment:
1. Delays in Loading at Houston Port:
Risk Level: High
Mitigation: Prioritize timely cargo submission, collaborate with the port administration to hasten loading, and, if necessary, think about employing more labor.
2. Stormy Weather during Hurricane Season:
Risk Level: Moderate
Mitigation: Keep an eye on weather predictions, and if catastrophic storms are predicted, think about delaying loading. Make sure the cargo is securely fastened to the ship to avoid harm.
3. Possibility of Damage at Houston Port:
Risk Level: Moderate
Mitigation: To reduce the chance of damage, check the cargo prior to loading and make sure it is properly packaged and protected.
2.Plan B: Contingency Plan for Power Plant International's GT 6 Bladed Rotor Import
Objective
A clearly defined contingency plan is essential to guarantee on-time installation on November
1st, 2019, in the event that the GT 6 Bladed Rotor shipment meets unanticipated difficulties or delays. Alternative steps to lessen potential disruptions are outlined in the following Plan B:
1. Pre-Shipment Preparations:
Starbucks Supply chain 15
a. Consistently follow Houston's weather forecasts and hurricane updates.
b. Keep the vessel operator and freight forwarder in the loop at all times to stay informed of any potential delays or disturbances at the Houston port.
2. Contingency Shipping Route:
If Houston loading delays or bad weather are expected, take the following action: a. Look into alternate routes or ports that are not impacted by bad weather.
b. In the event that Houston is rendered impractical, figure out alternative shipping routes, such as using the Port of New Orleans or other neighboring ports for unloading.
3. Expedited Shipping and Customs Clearance:
a. If there are prolonged delays at the Houston port, take into account accelerated delivery options like air freight or fast shipping.
a. In the event that there are any unanticipated delays in Venezuela, work with local authorities and customs to hasten the clearance and delivery procedure.
4. Supplier and Agent Oversight
:
a. To guarantee that the supplier and agent follow the correct lifting and loading procedures, establish clear communication with them.
b. To avoid any harm, implement real-time tracking and monitoring of the loading and handling of cargo.
5. Labour and Workforce Management:
a. Stay in touch with the labor movement and the workforce to address any possible industrial
disturbance as soon as it arises.
b. Establish a backup plan to guarantee the accessibility of skilled employees in the event of accidents or staffing concerns.
6. Alternative Incoterms:
Your preview ends here
Eager to read complete document? Join bartleby learn and gain access to the full version
- Access to all documents
- Unlimited textbook solutions
- 24/7 expert homework help
Starbucks Supply chain 16
If the existing incoterms prove to be inadequate as a result of unanticipated difficulties, you should: a. Review and renegotiate the incoterms to assign some duties to suppliers, carriers, or freight
forwarders for the remaining shipping voyage.
b. Take into account using more adaptable incoterms that permit modifications in response to shifting conditions.
C) Shipping Documents Needed for Clearance of Cargo at the Port:
To ensure that commodities are transported lawfully and without incident, clearing cargo at the port requires a substantial amount of paperwork (Wild, 2019). According to Wild 2019, Power Plant International should make sure the following shipping documents are in order in order for the GT 6 Bladed Rotor to be imported at the Port of Point Lisas:
B/L, or bill of lading: This important document, which the carrier (shipping business) issues, acts as proof of the transport contract and acknowledges receipt of the goods. The quantity, description, weight, and destination of the shipment are all specified on the bill of lading.
Commercial Invoice: Commercial Billing a comprehensive invoice given by the shipper or supplier that details the worth of the goods being shipped (Narasimhan & Nair, 2005). This document is necessary for calculating import taxes and levies as well as for customs purposes.
Packing List: A list of each package or container's contents, weight, and measurements is called a packing list. This is used by customs officials to monitor inventories and to confirm the cargo's contents.
Certificate of Origin: A Certificate of Origin should be offered if there are any trade agreements in existence or if origin information is necessary for customs purposes.
Starbucks Supply chain 17
License or permit for imports: Certain goods may need particular licenses or permits for importation depending on their nature.
Invoice of Entry: This is an official declaration issued to the customs officials that includes information on the consignee, the items, and the value. It is necessary for the evaluation and clearance of customs.
Insurance Certificate: If the products are covered by insurance while in transit, the insurance certificate should be given in order to handle the filing of claims in the event that something goes wrong.
International Commercial Terms, or Incoterm The obligations of the buyer and seller are outlined in these conditions, as well as the point at which risk and expenses are transferred. For logistical and customs reasons, it is crucial to utilize the right Incoterm.
Shipping & Transportation Documents: Any further paperwork needed for the cargo's shipping and transportation, such as a certificate of transport, is frequently needed.
Customs Declaration: An official statement given by the importer that outlines the contents of the shipment and its intended purpose.
These papers are necessary for the importation of the goods legally and effectively, as well as for customs clearance. It will be easier to prevent delays, fines, and other problems throughout the importing and transportation processes if these paperwork are properly prepared. It's crucial to collaborate closely with a customs broker or logistics specialist who can guide you through the Port of Point Lisas' unique requirements and make sure all required paperwork is in order.
D) Payment Options for Managing Supply Chain Costs
The client (Starbucks) could investigate other payment alternatives for managing their
supply chain costs and boosting overall efficiency in light of the supply chain difficulties that
Starbucks Supply chain 18
the company faced in 2007 and 2008. The following payment methods are listed along with their benefits and drawbacks for both the importer (suppliers) and the shipper (Starbucks):
Letters of Credit (L/C):
Advantages of Starbucks (Shipper): Starbucks can utilize L/Cs to make sure that payments are given to suppliers only when specific requirements are met, such as on-
time delivery or quality standards. This can lessen legal and financial concerns.
Disadvantages for Starbucks (Shipper): L/Cs can be expensive to set up and operate and can be administratively onerous, which is disadvantageous for Starbucks (Shipper). They can also make the payment procedure take longer.
Benefits for Suppliers (Importers): If they adhere to the L/C terms, Suppliers are guaranteed payment, lowering their financial risk. If they have payment assurance, they might also be more inclined to offer competitive pricing.
Supplier (Importers) disadvantages: Suppliers may find L/Cs burdensome and time-
consuming. To receive payment, they might have to meet certain requirements.
Open Account:
Advantages for Starbucks (Shipper): Open account terms make the payment procedure simpler and save down on administrative costs for Starbucks (Shipper). It enables payment flexibility and fosters relationships of trust with dependable suppliers (Poirier & Reiter, 1996).
Starbucks (Shipper)'s disadvantages include: If suppliers don't achieve deadlines or quality standards, there is a bigger risk for Starbucks. Payment can be postponed.
Advantages for Suppliers (Importers): Suppliers (Importers) benefit from prompt payments, which can help with their cash flow (Spekman & Davis, 2004). Compared to other approaches, it lessens administrative burdens.
Your preview ends here
Eager to read complete document? Join bartleby learn and gain access to the full version
- Access to all documents
- Unlimited textbook solutions
- 24/7 expert homework help
Starbucks Supply chain 19
Disadvantages for Suppliers (Importers): Suppliers (Importers) face the risk of non-
payment if the customer fails, which may have an adverse financial impact.
Advance Payment:
Advantages for Starbucks (Shipper): Starbucks (Shipper) benefits from being able to secure items before shipping and guarantee on-time deliveries, lowering the risk of supply chain disruption.
Disadvantages for Starbucks (Shipper): Starbucks (Shipper) may be restricted in cash flow due to upfront payments, and there is a chance of financial loss if the supplier fails to fulfill the order.
Benefits for Suppliers (Importers): Receiving payment in advance lowers their financial risk and enhances cash flow.
Disadvantages for Suppliers (Importers): Suppliers (Importers) may find it difficult to draw in customers who are hesitant to make payments in advance.
When faced with supply chain difficulties in 2007 and 2008, Starbucks had a variety of payment options to consider, each of which had pros and cons for both the coffee giant (the shipper) and its suppliers (the importers) (Seuring & Gold, 2013). When choosing a payment method, it's important to take into account things like your willingness to take on financial risk, your requirement for administrative efficiency, and the caliber of your supplier relationships (Seuring & Gold, 2013). The ultimate objective is to find a balance that guarantees on-time deliveries, upholds a trustworthy supply chain, and protects the financial interests of both Starbucks and its suppliers. For risk mitigation and fostering a seamless and cost-effective supply chain operation, carefully crafted supply contracts with explicit terms and conditions are crucial.
Conclusion
Starbucks Supply chain 20
Starbucks' supply chain issues in 2007–2008 demonstrated the value of a properly organized and effective supply chain. Starbucks was able to go through a difficult time and maintain its success in the coffee market on a global scale by correcting service flaws, making the best outsourcing decisions, and carefully choosing payment alternatives. The importance of supply chain management in maintaining the longevity and expansion of a worldwide brand is shown by this case study.
Starbucks Supply chain 21
References
Attaran, M. (2004). Exploring the relationship between information technology and business process reengineering. Information & Management, 41(5), 585-596
Chopra, S., & Meindl, P. (2015). Supply Chain Management: Strategy, Planning, and Operation. Pearson.
Chopra, S., & Sodhi, M. S. (2014). Reducing the risk of supply chain disruptions. MIT Sloan Management Review, 55(3), 73-80.
Christopher, M. (2016). Logistics and Supply Chain Management. Pearson.
Delfmann, W., Albers, S., Gehring, M., & Gehring, M. (2002). The impact of electronic commerce on logistics service providers. International Journal of Physical Distribution & Logistics Management, 32(3), 203-222.
Fawcett, S. E., Ellram, L. M., & Ogden, J. A. (2014). Supply chain management: From vision
to implementation. Pearson.
Gereffi, G., Humphrey, J., & Sturgeon, T. (2005). The governance of global value chains. Review of International Political Economy, 12(1), 78-104.
Keong Leong, G., Snyder, D. L., & Ward, Y. (1990). Research in the process and content of manufacturing strategy. Omega, 18(2), 109-122.
Lambert, D. M., & Enz, M. G. (2017). Issues in supply chain management. International Journal of Physical Distribution & Logistics Management, 47(2), 2-2.
Mangan, J., Lalwani, C., & Butcher, T. (2016). Global Logistics and Supply Chain Management. Wiley.
Monczka, R. M., Handfield, R. B., Giunipero, L. C., & Patterson, J. L. (2015). Purchasing and Supply Chain Management. Cengage Learning.
Narasimhan, R., & Nair, A. (2005). Vendor evaluation and performance monitoring system: A
service provider's perspective. Omega, 33(6), 497-507.
Your preview ends here
Eager to read complete document? Join bartleby learn and gain access to the full version
- Access to all documents
- Unlimited textbook solutions
- 24/7 expert homework help
Starbucks Supply chain 22
Poirier, C. C., & Reiter, S. E. (1996). World-Class Supply Management: The Key to Supply Chain Management. Simon and Schuster.
Seuring, S., & Gold, S. (2013). Sustainability in supply chain management: An introduction to the special issue. Journal of Cleaner Production, 56, 1-6.
Spekman, R. E., & Davis, E. W. (2004). Risky business: expanding the discussion on risk and
the extended enterprise. International Journal of Physical Distribution & Logistics Management, 34(5), 414-430.
Wild, R. (2019). International Business: The Challenges of Globalization. Pearson.
Your preview ends here
Eager to read complete document? Join bartleby learn and gain access to the full version
- Access to all documents
- Unlimited textbook solutions
- 24/7 expert homework help
Recommended textbooks for you
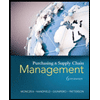
Purchasing and Supply Chain Management
Operations Management
ISBN:9781285869681
Author:Robert M. Monczka, Robert B. Handfield, Larry C. Giunipero, James L. Patterson
Publisher:Cengage Learning
Marketing
Marketing
ISBN:9780357033791
Author:Pride, William M
Publisher:South Western Educational Publishing
Recommended textbooks for you
- Purchasing and Supply Chain ManagementOperations ManagementISBN:9781285869681Author:Robert M. Monczka, Robert B. Handfield, Larry C. Giunipero, James L. PattersonPublisher:Cengage LearningMarketingMarketingISBN:9780357033791Author:Pride, William MPublisher:South Western Educational Publishing
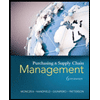
Purchasing and Supply Chain Management
Operations Management
ISBN:9781285869681
Author:Robert M. Monczka, Robert B. Handfield, Larry C. Giunipero, James L. Patterson
Publisher:Cengage Learning
Marketing
Marketing
ISBN:9780357033791
Author:Pride, William M
Publisher:South Western Educational Publishing