Prior to beginning work on this assignment
docx
keyboard_arrow_up
School
Nairobi Institute Of Business Studies *
*We aren’t endorsed by this school
Course
443
Subject
Management
Date
Nov 24, 2024
Type
docx
Pages
4
Uploaded by MasterBoulderKouprey30
Your preview ends here
Eager to read complete document? Join bartleby learn and gain access to the full version
- Access to all documents
- Unlimited textbook solutions
- 24/7 expert homework help
Recommended textbooks for you
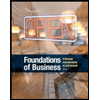
Foundations of Business (MindTap Course List)
Marketing
ISBN:9781337386920
Author:William M. Pride, Robert J. Hughes, Jack R. Kapoor
Publisher:Cengage Learning
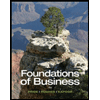
Foundations of Business - Standalone book (MindTa...
Marketing
ISBN:9781285193946
Author:William M. Pride, Robert J. Hughes, Jack R. Kapoor
Publisher:Cengage Learning
Recommended textbooks for you
- Foundations of Business (MindTap Course List)MarketingISBN:9781337386920Author:William M. Pride, Robert J. Hughes, Jack R. KapoorPublisher:Cengage LearningFoundations of Business - Standalone book (MindTa...MarketingISBN:9781285193946Author:William M. Pride, Robert J. Hughes, Jack R. KapoorPublisher:Cengage Learning
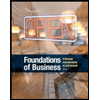
Foundations of Business (MindTap Course List)
Marketing
ISBN:9781337386920
Author:William M. Pride, Robert J. Hughes, Jack R. Kapoor
Publisher:Cengage Learning
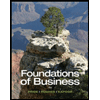
Foundations of Business - Standalone book (MindTa...
Marketing
ISBN:9781285193946
Author:William M. Pride, Robert J. Hughes, Jack R. Kapoor
Publisher:Cengage Learning