EEE 360 lab 13
docx
keyboard_arrow_up
School
Johns Hopkins University *
*We aren’t endorsed by this school
Course
360
Subject
Electrical Engineering
Date
Apr 3, 2024
Type
docx
Pages
9
Uploaded by AgentCrown4453
EEE 360
Lab 13
The Synchronous Motor - Part I
October 23, 2023
7933adfb48e80c98034e562f8d4929d7dba026a4.docx
13-1
Experiment 13. The Synchronous Motor – Part I
OBJECTIVE
To examine the construction of the three-phase (3Φ) synchronous motor.
To obtain the starting characteristics of the 3Φ synchronous motor.
DISCUSSION
The synchronous motor gets its name from the term synchronous speed, which is the natural speed
of the rotating magnetic field of the stator. As you have learned, this natural speed of rotation is
controlled strictly by the number of pole pairs and the frequency of the applied power.
Like the induction motor, the synchronous motor makes use of the rotating magnetic field. Unlike
the induction motor, however, the torque developed does not depend on the induction currents in
the rotor. Briefly, the principle of operation of the synchronous motor is as follows. A multiphase
source of AC is applied to the stator windings, and a rotating magnetic field is produced. A direct
current is applied to the rotor windings, and a fixed magnetic field is produced. The motor is so
constructed that these two magnetic fields react upon each other causing the rotor to rotate at the
same speed as the rotating magnetic field. If a load is applied to the rotor shaft, the rotor will
momentarily fall behind the rotating field but will continue to rotate at the same synchronous speed.
The falling behind is analogous to the rotor being tied to the rotating field with a rubber band.
Heavier loads will cause stretching of the band, so the rotor position lags the stator field, but the
rotor continues at the same speed. If the load is made too large, the rotor will pull out of
synchronism with the rotating field and, thus, will no longer rotate at the same speed. The motor is
then said to be overloaded.
The synchronous motor is not a self-starting motor. The rotor is heavy, and from a dead stop, it is
not possible to bring the rotor into the magnetic lock with the rotating magnetic field. For this
reason, all synchronous motors have a starting device. A simple starter is another motor which
brings the rotor up to approximately 90% of its synchronous speed. The starting motor is then
7933adfb48e80c98034e562f8d4929d7dba026a4.docx
13-2
disconnected, and the rotor locks in step with the rotating field. The more commonly used starting
method is to have the rotor include a squirrel cage induction winding. This induction winding
brings the rotor almost to synchronous speed as an induction motor. The squirrel cage is also useful
even after the motor has attained synchronous speed because it tends to dampen rotor oscillations
caused by sudden changes in loading. Your Three-Phase Synchronous Motor/Generator contains a
squirrel-cage-type rotor.
PROCEDURE
The grading in this section is 1 point for each correct answer.
1.
Procedure 1
Open the Virtual Laboratory, and from the Virtual Lab, Welcome Window click on the
Experiment 13 Procedure 1 button. Your screen should look like Figure 13-1. Examine the
construction of the Three-phase Synchronous Motor/Generator, paying attention to the motor,
slip rings, connection terminals and the wiring. The rheostat is a variable resistor to adjust the
current and voltage in the circuit.
Figure 13-1. Screen capture of Procedure 1.
View the motor from the rear of the module:
a.
Identify the two slip rings and brushes.
7933adfb48e80c98034e562f8d4929d7dba026a4.docx
13-3
Your preview ends here
Eager to read complete document? Join bartleby learn and gain access to the full version
- Access to all documents
- Unlimited textbook solutions
- 24/7 expert homework help
b.
Note that the two rotor windings are brought out to the two slip rings via a slot in the rotor
shaft.
c.
Identify the DC damper windings on the rotor. Although there are only two windings, they
are connected so that their magnetomotive forces act in opposition, thus, creating four
poles. d.
Identify the four salient poles just beneath the damper windings.
e.
Identify the stator winding and note that it is identical to that of the three-phase squirrel
cage and wound rotor motors.
f.
Close the Experiment 13 Procedure 1 window.
2.
Procedure 2
Circuit
:
Click on the Experiment 13 Procedure 2 button. Your screen should look similar to Figure 13-
2. Using your Three-Phase Synchronous Motor/Generator, Power Supply, and Ammeter,
connect the circuit shown in Figure 13-3. Note that the three stator windings are wye-
connected to the fixed 208 V 3Φ output of the power supply. Also, note that the rotor is left
unconnected. If you are unsure how to make/remove connections, please refer to the
Experiment 1 manual.
Figure 13-2. Screen capture for Procedure 2.
7933adfb48e80c98034e562f8d4929d7dba026a4.docx
13-4
Figure 13-3. Connection circuit of Procedure 2. Motor terminals are 1 = A, 2 = B, 3 = C,
Neutral point is terminals 4,5,6. The rotor DC excitation terminals are 7 and 8.
S is a switch and potentiometer to provide fine regulation of DC excitation current.
Measurements:
a.
Click on the Run
button. If you receive an error message, check your wiring and the
voltage magnitude. Once you have fixed your circuit, click the Run
button again. Note
that the motor starts smoothly and continues to run as an ordinary induction motor.
b.
Note the direction of rotation (clockwise/counterclockwise) and the line current.
Rotation = counterclockwise
I
A
= 1.218
A
c.
Interchange any two of the leads from the power supply. If you are unsure how to
make/remove connections, please refer to the Experiment 1 manual.
d.
Click the Run
button and note the direction of rotation (clockwise/counterclockwise) and
the line current.
Rotation =clockwise
I
A
=1.218
A
e.
Close the Experiment 13 Procedure 2 window.
7933adfb48e80c98034e562f8d4929d7dba026a4.docx
13-5
3.
Procedure 3
Circuit
:
Click on the Experiment 13 Procedure 3 button. Your screen should look like Figure 13-4.
Connect the circuit shown in Figure 13-5. The motor is now coupled to the
electrodynamometer with a belt.
Figure 13-4. Screen capture of Procedure 3.
7933adfb48e80c98034e562f8d4929d7dba026a4.docx
13-6
Your preview ends here
Eager to read complete document? Join bartleby learn and gain access to the full version
- Access to all documents
- Unlimited textbook solutions
- 24/7 expert homework help
Figure 13-5. Circuit diagram for Procedure 3. Generator terminals 1 = A, 2 = B, 3 = C. Neutral
point N is terminals 4,5,6. The rotor DC excitation terminals are 7 and 8. S is a switch and
potentiometer (rheostat) which provides fine regulation of DC excitation current.
a.
The dynamometer is used to load the synchronous motor. Set the dynamometer control
slider to 40% excitation (torque reference). The motor is loaded.
b.
The rotor of the synchronous motor is connected to the fixed 120 V DC output of the
power supply, terminals 7 and 8. Set the field rheostat for zero resistance (and close the
switch {ON position}). Note that if this switch is OFF, no voltage will be applied to the
rotor windings.
Measurements (round one)
:
i.
With the rotor switch in the ON position, click on the Run
button. If you receive an
error message, check your wiring and the voltage magnitude. Once you have fixed
your circuit, click the Run
button again.
7933adfb48e80c98034e562f8d4929d7dba026a4.docx
13-7
ii.
Describe what happened.
The motor shook erratically and created a lot of noise when the current climbed to 4.028 Amperes. The rotor scarcely rotates.
iii.
What was the maximum reading on the ammeter?
4.028 A
iv.
Should a synchronous motor, under load, be started with DC excitation on its field?
Yes
No
Measurements (round two)
:
v.
Connect the rotor of the synchronous motor to the variable 0-120 V DC output of
the power supply. Do not disturb any of the other connections or change any control
settings.
vi.
The generator is unloaded when the Dynamometer voltage is zero. With the variable
output voltage control at zero, turn on the power supply. Apply 3Φ power by
closing the synchronizing switch and observe what happens.
vii.
Describe what happened.
Current stayed at 1.24
viii.
Is your motor operating as an induction motor?
Yes
No
ix.
Is your motor operating as a synchronous motor?
Yes
No
x.
Close the Experiment 13 Procedure 3 window.
REVIEW QUESTIONS
1.
What precautions should be taken during the start-up period of a synchronous motor? (4)
The stator magnetic field's speed should be initially reduced. The synchronous motor should
then be accelerated to synchronous speed using an external prime mover. Use of damper winds
is also required.
7933adfb48e80c98034e562f8d4929d7dba026a4.docx
13-8
2.
If the squirrel-cage winding were removed from a synchronous motor, could it start by itself?
(4)
Yes
No
3.
What function does the damper winding serve? (4)
The main winding is assisted in correcting the field without discontinuity by damper
windings connected in series with the field windings, placing the in synchronous operation.
7933adfb48e80c98034e562f8d4929d7dba026a4.docx
13-9
Your preview ends here
Eager to read complete document? Join bartleby learn and gain access to the full version
- Access to all documents
- Unlimited textbook solutions
- 24/7 expert homework help
Related Documents
Related Questions
3. (a) Can single phase induction motor be self-started? Explain the operation of a capacitor run single phase induction motor?
arrow_forward
Explain the working principle of the synchronous motor and the 3-phase induction motor with the diagrm.
arrow_forward
3.An induction motor has a rotor resistance and reactance at standstill of 0.1 ohm and 3.5 ohm respectively. At standstill the voltage induced to the rotor is 60volts per phase. If the slip is 5%, determine the rotor current
arrow_forward
Induction Motor
arrow_forward
A 50 Hz, 4-pole, 3 phase induction motor has a rotor current of frequency 2 Hz.
Determine (i) slip and (ii) speed of the motor.
arrow_forward
. A) Which of the following is/are a part of a 3-phase induction motor? a) stator b) rotor c) both "a" and "b" d) neither "a" nor "b" B) Which of the following is sometimes referred to as the motor secondary of a 3-phase induction motor? a) stator b) rotor c) both "a" and "b" d) neither "a" nor "b" C) How does the rotor of a 3-phase induction motor get power? a) through brushes and commutator segments b) through brushes and slip rings c) induction from the stator d) none of the above
arrow_forward
L-1). The 3-phase wound-rotor induction motor has .... . a) high starting torque b) low starting current c) both "a" and "b" d) neither "a" nor "b" L-2). The 3-phase wound-rotor induction.........a) motor has a wire wound rotor b) motor's rotor can be connected to an external resistive load by way of slip rings and brushes c) motor requires more maintenance than the 3-phase squirrel-cage induction motor d) all of the above L-3). The 3-phase wound-rotor induction motor's rotor circuit's resistance should be adjusted so it is__________ during starting. a) low b) high c) either "a" or "b" d) neither "a" nor "b" L-4). Will a 3-phase wound-rotor induction motor start with no external circuit connected to its rotor leads? a) yes b) no
arrow_forward
A 3-phase, 50 Hz induction motor has 8 poles.
If the full load slip is 2.5 per cent, determine
(a) the synchronous speed,
(b) the rotor speed, and
(c) the frequency of the rotor e.m.f.'s
arrow_forward
A 2300 V,3 phase,wye-connected synchronous motor has a synchronous reactance of 3 ohms per phase and an armature resistance of 0.25 ohms per phase. The motor operates on load such that the power angle is -15, and the excitation is so adjusted that the internally induced voltage is equal in magnitude to the internal voltage. Determine the armature current
arrow_forward
Characteristics curve of a single phase induction motor (open and closed circuit )
arrow_forward
(Qld)
A three-phase 20-pole induction motor is rated at 800 V, 50 Hz. What is the synchronous speed
of this machine if the voltage at its terminals is reduced to 400 V
(a) 150 rpm,
(b) 300 rpm,
(c) 600 rpm,
(d) 3000 rpm
arrow_forward
SEE MORE QUESTIONS
Recommended textbooks for you
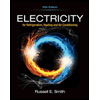
Electricity for Refrigeration, Heating, and Air C...
Mechanical Engineering
ISBN:9781337399128
Author:Russell E. Smith
Publisher:Cengage Learning
Related Questions
- 3. (a) Can single phase induction motor be self-started? Explain the operation of a capacitor run single phase induction motor?arrow_forwardExplain the working principle of the synchronous motor and the 3-phase induction motor with the diagrm.arrow_forward3.An induction motor has a rotor resistance and reactance at standstill of 0.1 ohm and 3.5 ohm respectively. At standstill the voltage induced to the rotor is 60volts per phase. If the slip is 5%, determine the rotor currentarrow_forward
- Induction Motorarrow_forwardA 50 Hz, 4-pole, 3 phase induction motor has a rotor current of frequency 2 Hz. Determine (i) slip and (ii) speed of the motor.arrow_forward. A) Which of the following is/are a part of a 3-phase induction motor? a) stator b) rotor c) both "a" and "b" d) neither "a" nor "b" B) Which of the following is sometimes referred to as the motor secondary of a 3-phase induction motor? a) stator b) rotor c) both "a" and "b" d) neither "a" nor "b" C) How does the rotor of a 3-phase induction motor get power? a) through brushes and commutator segments b) through brushes and slip rings c) induction from the stator d) none of the abovearrow_forward
- L-1). The 3-phase wound-rotor induction motor has .... . a) high starting torque b) low starting current c) both "a" and "b" d) neither "a" nor "b" L-2). The 3-phase wound-rotor induction.........a) motor has a wire wound rotor b) motor's rotor can be connected to an external resistive load by way of slip rings and brushes c) motor requires more maintenance than the 3-phase squirrel-cage induction motor d) all of the above L-3). The 3-phase wound-rotor induction motor's rotor circuit's resistance should be adjusted so it is__________ during starting. a) low b) high c) either "a" or "b" d) neither "a" nor "b" L-4). Will a 3-phase wound-rotor induction motor start with no external circuit connected to its rotor leads? a) yes b) noarrow_forwardA 3-phase, 50 Hz induction motor has 8 poles. If the full load slip is 2.5 per cent, determine (a) the synchronous speed, (b) the rotor speed, and (c) the frequency of the rotor e.m.f.'sarrow_forwardA 2300 V,3 phase,wye-connected synchronous motor has a synchronous reactance of 3 ohms per phase and an armature resistance of 0.25 ohms per phase. The motor operates on load such that the power angle is -15, and the excitation is so adjusted that the internally induced voltage is equal in magnitude to the internal voltage. Determine the armature currentarrow_forward
- Characteristics curve of a single phase induction motor (open and closed circuit )arrow_forward(Qld) A three-phase 20-pole induction motor is rated at 800 V, 50 Hz. What is the synchronous speed of this machine if the voltage at its terminals is reduced to 400 V (a) 150 rpm, (b) 300 rpm, (c) 600 rpm, (d) 3000 rpmarrow_forward
arrow_back_ios
arrow_forward_ios
Recommended textbooks for you
- Electricity for Refrigeration, Heating, and Air C...Mechanical EngineeringISBN:9781337399128Author:Russell E. SmithPublisher:Cengage Learning
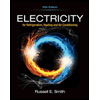
Electricity for Refrigeration, Heating, and Air C...
Mechanical Engineering
ISBN:9781337399128
Author:Russell E. Smith
Publisher:Cengage Learning