Wilfong Week 8 Save A Lot Reserach Project
docx
keyboard_arrow_up
School
Webster University *
*We aren’t endorsed by this school
Course
614
Subject
Business
Date
Feb 20, 2024
Type
docx
Pages
10
Uploaded by DannyW77
Running head: SAVE A LOT SUPPLY CHAIN 1
Save A Lot Supply Chain
Daniel Wilfong
Maryville University
SAVE A LOT SUPPLY CHAIN
2
Abstract
Save A Lot is a wholesale grocery distributor. Save A Lot currently has ten distribution centers that service approximately nine hundred stores. Save A Lot’s supply chain consists of procurement, warehousing, distribution, logistics, and transportation. Each of these functions is critical to the supply chain and the business. Save A Lot has been successful but will need to evolve and improve in some areas in order to continue to grow and have a successful supply chain that will result in a successful company.
SAVE A LOT SUPPLY CHAIN
3
Supply Chain is the sequence of processes involved in the production and distribution of a product. The supply chain is an important function of a business in order for the business to be successful. Without supply chain, businesses may struggle with obtaining materials needed for production or distribution and then struggle to get the finished product to customers. Save A Lot is a wholesale distributor of groceries. Save A Lot currently operates nine Distribution Centers that services around 1,400 stores. Most of those stores are licensee retail partners with only 18 stores being owned and operated by Save A Lot as corporate stores. Being a wholesale distributor, Save A Lot has supply chain functions for getting products to the distribution centers and then supply chain functions for getting the materials to the stores. In looking at the supply chain of Save A Lot, there are good processes and then processes that need to be reviewed and possibly changed to help the supply chain and business.
Save A Lot Company
Save A Lot was founded in 1977 by Bill Moran as an alternative to the larger supermarkets. The first Save A Lot store was opened in Cahokia, IL. In 1978, the company expanded its presence in the greater St. Louis, MO area by expanding to thirty stores. The growth of the company could be contributed to a licensee relationship where Save A Lot would act as a wholesaler to independently owned stores as opposed to a franchisor. Smaller, independent grocery retailers soon found the limited assortment model to be an effective defensive strategy against the larger chain supermarkets. With the help of the new licensees, in 1980 Save A Lot added an additional fifty stores in the Mid-South region, and a distribution warehouse in Jackson, TN area. In 1984, Save A Lot purchased seventy-five format Jewel T stores and two distribution centers from Jewel in Florida and Pennsylvania. In 1987, Save A Lot was purchased by a St. Louis-based food retailer and wholesaler Wetterau Inc which also owned Shop’n Save stores. In 1994, both Save A Lot and Shop’n Save banners become wholly owned subsidiaries of Supervalu Inc, one of the largest independent grocery wholesalers, and the owners of Cub Foods and Scott’s Food and Pharmacy at the time. The acquisition opened Save A Lot licensee opportunities to
Your preview ends here
Eager to read complete document? Join bartleby learn and gain access to the full version
- Access to all documents
- Unlimited textbook solutions
- 24/7 expert homework help
SAVE A LOT SUPPLY CHAIN
4
conventional Supervalu-supplied operators including Niemann Foods. Save A Lot continued its growth and expanded into Southern California with the purchase of twenty-one discount-grocery Sav U Foods stores and a distribution center from the Fleming Companies in late 1996. In 2002, Save A Lot acquired discount variety store chain Deals with forty-five stores in the Midwest. The typical Deals store had a slightly smaller footprint than a Save A Lot but carried mostly non-food merchandise at dollar-increment price points. The Deals concept was expanded under Save A Lot to 138 stores in 2006. The acquisition of Deals also allowed Save A Lot grocery stores to expanded and stock more general merchandise in the grocery stores. Save A Lot experimented with hypermarkets which combined discount grocery and merchandise concepts under one roof. This experiment led to 480 combination stores that did not carry the Deals banner. In 2006, Save A Lot sold Deals to Dollar Tree and reduced the amount of general merchandise carried in its combination stores and Save A Lot returned to the grocery-focused model
(SAVE A LOT HISTORY, 2023)
.
In 2009, Save A Lot continued its expansion and the CEO at time announced that Save A Lot’s goal was to double the grocery store network to 2,400 locations within five years. Save A Lot would go on to open nearly 100 stores in 2010 with the major focus of the store openings being on the Southeastern
United States. In 2010, Rite Aid became a licensed Save A Lot operator when it converted ten of its existing pharmacies in the Greenville, SC area to a co-branded Save A Lot/Rite Aid units. In September 2012, Supervalu announced it would close twenty-two stores in seven states and then made several executive changes. The changes came in the midst of plans by Supervalu to sell a number of its grocery chains to Cerberus Capital Management. In October 2016, Supervalu sold Save A Lot to Onex Corporation
(SAVE A LOT HISTORY, 2023)
. Starting in 2020, Save A Lot made a complete change of strategy and started a transition to a complete wholesaler by selling off corporate owned stores. In 2020 and 2021, Save A Lot made many agreements with different licensee partners to purchase and operate Save A Lot branded stores. Save A Lot sold nearly three hundred corporate stores in this transition and kept just eighteen stores that are located in the greater St. Louis area. Save A Lot’s network is now
SAVE A LOT SUPPLY CHAIN
5
approximately nine hundred stores in thirty-two states
(Save A Lot Completes Wholesale Model Transition, 2022)
. Save A Lot Supply Chain
With the different strategies and different owners, Save A Lot’s supply chain has had to continue to adapt and change in order to meet the needs of the company and the stores. In order to service the approximately nine hundred stores, Save A Lot currently operates ten warehouses and distribution centers
with two of them currently being shut down in the first quarter of 2023 to help optimize the supply chain network. From the business model of Save A Lot, the supply chain would seem to be simple but it is more complex than it would sound. Save A Lot has a group of buyers and category managers that works to procure the goods to distribute to the stores. Save A Lot has a logistics group that helps get the goods from the vendor to the distribution centers and then to the stores. Save A Lot is a distribution group that receives the goods into inventory and then fulfills the orders to the stores. All of this seems like a simple and straightforward process but there are complexities. With Save A Lot being a grocery wholesale supplier, there is perishable inventory that has short shelf lives and has to be turned quickly in the distribution centers in order to sale before it spoils. This takes coordination between the vendor, purchasing, logistics, and distribution centers and then the stores otherwise the goods will not make to the
store shelves in time to sale. The other complexity is trying to utilize the logistics network so that trucks are not running empty. When a truck drops off at a store, trying to find a backhaul load from a vendor back to the warehouse so that the truck is not running empty to try to utilize the trucks and reduce cost. Save A Lot has many different vendors from Quaker to Tyson to Procter and Gamble to many others vendors. In order to supply the needs of the end customers, Save A Lot has partnered with many vendors.
Save A Lot also has many of its own private label branded items to help provide cost efficient options. The supply chain partners with the sales team and the buyers and category managers in order to ensure there is demand forecasting and sales forecasting to ensure goods are purchased and arrive in time to get to the shelves when needed. For example, you don’t want your Christmas goods showing up in the
SAVE A LOT SUPPLY CHAIN
6
distribution centers in the middle of December. These goods would not make it to the shelves in time for Christmas and would not be able to be sold and cause a huge loss. Save A Lot Warehousing, Logistics, and Transportation Processes
Save A Lot has a network of distribution centers and a network of trucks and logistics systems in order to meet the needs of the stores and customers. Save A Lot currently has ten distribution centers in the Midwest and East Coast. Save A Lot has distribution centers in Edwardsville, IL, Muncie, IN, Humboldt, TN, St. Johns, MI, Coxsackie, NY, Williamsport, MD, Winchester, KY, Fort Worth, TX, Austinburg, OH, and Plant City, FL. In order to optimize the network and create efficiencies, Save A Lot
has announced the closure of St. Johns, MI and Coxsackie, NY. This will help reduce cost and gain efficiencies by utilizing unused capacity at the remaining distribution centers. The distribution centers also warehouse the inventory needed to fulfill the orders to the stores. In order to get the goods from vendor to distribution center and warehouse and then to the stores, Save A Lot has a logistics and transportation network. Save A Lot has a couple of different programs for the transportation network. Save A Lot does own some trucks that are utilized, brokers some loads with third-party logistics companies, and also utilizes the vendors to deliver goods to the distribution centers. Deliveries to the stores are handled by Save A Lots own fleet and brokers. In order to try take full advantage of their own fleet and brokered loads, Save A Lot has put a backhaul program in place to try to eliminate trucks running with empty loads that would be just sunk cost. Performance Measures
Save A Lot does use different performance measures to see how the supply chain functions and to
find areas for improvement. Save A Lot tracks it’s on time deliveries, truck utilization, stock outs, inventory turns to name a few. Save A Lot uses all of the data it has in order to see how the supply chain functions and which areas need improved to provide better customer service to the stores and ultimately the end customers purchasing from the stores. Save A Lot uses the measure of on time delivery to determine if the goods are making it to the stores at the times that are scheduled and needed to avoid
Your preview ends here
Eager to read complete document? Join bartleby learn and gain access to the full version
- Access to all documents
- Unlimited textbook solutions
- 24/7 expert homework help
SAVE A LOT SUPPLY CHAIN
7
inventory arriving late and being spoiled. Truck utilization is used to ensure trucks are being utilized and not running on the roads empty. Utilizing costs and not running trucks empty can be a cost reduction and benefit to the company. Tracking stock outs helps to determine customer satisfaction. If there is a continually stock out of certain items, stores and customers are going to be upset and could possible start looking for another supplier of that item for the store and could push the customer to a different grocery store to purchase that item. Inventory turns goes with stocks out and is used to ensure the right items are being purchased and moved. Being a grocery wholesale supplier, you want inventory to turn and not sit otherwise you are at a larger risk of spoilage and throwing out inventory. Thes different performance measures are used to assess the effectiveness of the supply chain and how to improve to keep customers happy.
Information Systems
Save A Lot has different information systems that are used by the supply chain. The distribution centers use a system called Triceps to receive inventory and fulfill orders to the stores. The Triceps system then sends all of the info to an AS400 system that houses and is the perpetual inventory system. The AS400 sends all of the transactions it receives from Triceps to Oracle. Oracle is the ERP system where all of the accounting and payables tasks are handled. The AS400 system is also the purchase order system that sends the purchase orders to Triceps and Oracle. For logistics and transportation there is a C3
system that takes appointments and works with dispatching the trucks so that the trucks are where they need to be when they are needed. Having all of the different systems work together is a big problem. Some of the data that would be needed to manage the supply chain more effectively is missing as each system has its own data in different formats so it is hard to consolidate and review. The other issue is some systems do not hold data for long periods of time. The Triceps system only holds its data for 40 days. This makes it difficult to look at inventory receipts and sales orders as the only data available for those transactions is in the AS400 and in a different format now. In order to try to streamline the process on the information systems, Save A Lot recently selected Symphony AI Retail CPG Supply Chain solution to help modernize the and expand its core merchandising system. This change will start moving
SAVE A LOT SUPPLY CHAIN
8
the transactions and data that is in the AS400 to one place and a more modern technology
(Save A Lot Selects SymphonyAI Retail CPG Supply Chain Solutions To Modernize and Expand Its Core Merchandising
Systems, 2023)
. There are a couple of different phases to this project. The first phase is moving the core merch transactions and task, purchase ordering, item maintenance, store ordering, to Symphony’s system in 2023. In 2024, inventory task and valuation will be moved and then after that look at Symphony’s warehouse management system to have all supply chain functions and data housed in one system. Recommendations Supply chain is a major function of Save A Lot being a wholesale grocery distributor. Save A Lot’s most important functions in their supply chain are procurement and logistics. Save A Lot has to be able to procure the items their customers want to buy and then once acquired need to be able to ensure they can get the items through the supply chain and ultimately to the end customer. For Save A Lot to continue to grow here are some recommendations that could help to improve the supply chain. One recommendation would be a more integrated supply chain. Save A Lot is working towards this with a recent restructuring that put supply chain and merchandising all under the same team. This should be a help and help to create efficiencies. This change should help to get processes out of the silos and create more of one team doing supply chain than each function working independently. Another recommendation would be to continue to upgrade the information systems. Save A Lot has been working
on old technology company wide so continuing to upgrade so be able to provide better data and help to be
able to track performance measures easier. AS400 systems are old technology that is hard to support so being able to modernize not only allows better data but also is not a failure point. Having people that can support the AS400 if there were any problems is hard to find. The last recommendation would be improved communication throughout the supply chain. With the network optimization that is currently happening, there has been a lack of communication across the functions that has led to some issues in the supply chain. The different teams did not communicate well and there were perishable items that needed moved out of a closing distribution center that logistics and the distribution center was not made of aware
SAVE A LOT SUPPLY CHAIN
9
of and cost the company extra money to get them moved at the last minute. Communication across different functions and teams has to improve in order for the supply chain at Save A Lot to take its next steps. Save A Lot can try to integrate the supply chain by having them all under the same leadership and upgrade the technology but if the different functions still fail to communicate effectively, the supply chain
will not improve.
Conclusion
Save A Lot is a wholesale grocery supplier that can only be successful with a successful supply chain. Save A Lot has ten distribution centers that currently service about nine hundred stores. Save A Lot has a supply chain with the functions of procurement, warehousing, distribution centers, logistics, and
transportation. These different functions have to work together in an integrated supply chain in order for Save A Lot to continue to grow and be successful. The most important recommendation for Save A Lot to get to that integrated supply chain is improved communication across the different functions. Improving the communications will allow Save A Lot to improve its supply chain and be able to grow and service more stores, which in turn will result in more profits.
Your preview ends here
Eager to read complete document? Join bartleby learn and gain access to the full version
- Access to all documents
- Unlimited textbook solutions
- 24/7 expert homework help
SAVE A LOT SUPPLY CHAIN
10
References
About Save A Lot. (2023, February 12). Retrieved from Save A Lot: https://savealot.com/about/
Chopra, S. (2019). Supply Chain Management Strategy, Planning, and Operation. Boston: Pearson Education.
Putnam, H. (2021, August 27). Three Strategies to Build More Sustainable Food Retail Supply Chains. Retrieved from Ratio Institute: https://ratioinstitute.org/three-strategies-to-build-more-
sustainable-food-retail-supply-chains/?
utm_medium=ppc&utm_source=adwords&utm_campaign=supply%20chain&utm_term=grocery
%20supply%20chain&utm_term=grocery%20supply%20chain&utm_campaign=Ratio+Institute
Save A Lot Aims to Update, Expand Core Merch Systems. (2023, February 7). Retrieved from Progressive Grocer: https://progressivegrocer.com/news-briefs?created_1=2023-02-
07T09%3A34%3A48
Save A Lot Completes Wholesale Model Transition. (2022, February 10). Retrieved from Save A Lot: https://savealot.com/news/wholesale-model-transition/
SAVE A LOT HISTORY. (2023, February 25). Retrieved from ZIPPIA: https://www.zippia.com/save-a-
lot-careers-225946/history/
Save A Lot Implements Supply Chain Solution to Minimize Stockouts. (2023, February 7). Retrieved from The Retail Touchpoints Network: https://www.retailtouchpoints.com/topics/supply-chain-
sourcing/save-a-lot-implements-supply-chain-solution-to-minimize-stockouts-symphonyai
Save A Lot Selects SymphonyAI Retail CPG Supply Chain Solutions To Modernize and Expand Its Core Merchandising Systems. (2023, February 7). Retrieved from SymphonyAI: https://www.symphonyretailai.com/save-a-lot-selects-symphonyai-retail-cpg-supply-chain-
solutions/
Related Documents
Recommended textbooks for you
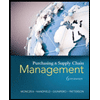
Purchasing and Supply Chain Management
Operations Management
ISBN:9781285869681
Author:Robert M. Monczka, Robert B. Handfield, Larry C. Giunipero, James L. Patterson
Publisher:Cengage Learning
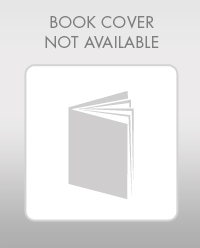
Contemporary Marketing
Marketing
ISBN:9780357033777
Author:Louis E. Boone, David L. Kurtz
Publisher:Cengage Learning
Marketing
Marketing
ISBN:9780357033791
Author:Pride, William M
Publisher:South Western Educational Publishing
Recommended textbooks for you
- Purchasing and Supply Chain ManagementOperations ManagementISBN:9781285869681Author:Robert M. Monczka, Robert B. Handfield, Larry C. Giunipero, James L. PattersonPublisher:Cengage LearningContemporary MarketingMarketingISBN:9780357033777Author:Louis E. Boone, David L. KurtzPublisher:Cengage Learning
- MarketingMarketingISBN:9780357033791Author:Pride, William MPublisher:South Western Educational Publishing
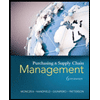
Purchasing and Supply Chain Management
Operations Management
ISBN:9781285869681
Author:Robert M. Monczka, Robert B. Handfield, Larry C. Giunipero, James L. Patterson
Publisher:Cengage Learning
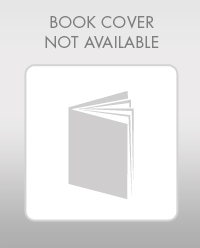
Contemporary Marketing
Marketing
ISBN:9780357033777
Author:Louis E. Boone, David L. Kurtz
Publisher:Cengage Learning
Marketing
Marketing
ISBN:9780357033791
Author:Pride, William M
Publisher:South Western Educational Publishing