Kelpies Furniture Company Assignment 1 Case (1)
pdf
keyboard_arrow_up
School
Accounting Institute Seminar *
*We aren’t endorsed by this school
Course
ACCT 3311
Subject
Business
Date
Nov 24, 2024
Type
Pages
8
Uploaded by ElderKuduMaster744
1
MANU9DA Business Analytics
Assignment 1
Autumn 2023
Division of Management, Work and Organisation
Quality Diagnosis at
The Kelpies Furniture Scotland
IntroducƟon
The Kelpies Furniture Scotland (KFS) is a family-run business that started in 2007 from a workshop near Stirling
with only 5 staff producing innovative products from recycled wood and locally sourced fabrics. It has evolved
into a business with over 200 staff focusing on serving niche market segments for upmarket customised
contemporary furniture with strong ethical credentials.
It also maintains a full design and manufacturing
capability inhouse. When the company’s demand driven steady growth required an expansion of workshop
space a second site, about 20 miles away at Saline in Fife was chosen. Compared to available Stirling facilities,
the new site offered the right workspace for a much lower rental cost. Both locations run the same production
processes and can make any of the furniture products in the range. The company’s CEO however still
anticipates eventually being in one location for all operational activities in Stirling by 2025. The Fife expansion
2
increased production capacity by 200%. Workstations were added for each process in the production lines,
increasing from the 2 initial workstation per process to 6. The new facility also provided a much bigger
warehouse area to store finished product, providing flexibility in production planning.
The CEO and the management team were initially concerned about the scale of the expansion and the future
robustness of the demand to justify this growth investment. Now, they also experiencing what the production
manager calls “growing pains”, with issues of staff wellbeing including absenteeism, quality problems as well as
persistent demand concerns.
Product characterisƟc and demand
The special made-to-order products are popular among customers in the UK, Europe, and emerging markets
in the Asia region. There are 4 product lines in its current catalogue with high levels of customisation of fit and
finish for each of the 4 model types, including sub-frames made from a range of wood or metal materials.
The demand has improved post-Covid19, with all models showing a strong market attraction with the modern
design utilising innovative materials that emphasises sustainable production methods and high environment
standards. All designs have a copyrights and patents registered in UK and Europe. In early April this year, KFS
won a “Made in Scotland Award” for the category “Manufacturer of the Year” in recognition for the most
outstanding business for ethical supply chain practices in Scotland. This commitment to excellence was
instrumental in a sales surge and increased profitability between November 2021 and December 2022.
Since winning the award, the company has experienced increase sales enquiries and higher awareness of the
brand internationally through the positive publicity across social media.
The most popular and expensive furniture is Model 1 which uses sustainable cushion filling with recycled
materials including wool and feathers, plus hand-stitched upholstery before it is carefully completed in the
finishing station. The lowest cost range is Model 4, since it does not require any use of wood materials or
creative work at the upholstery’s station. Other options of the models as presented in Table 1.
Model
Material - Wood
Material -Metal
Cushion &
Upholstery
Metal Work
1
Yes
Yes
Yes
Yes
2
Yes
Yes
Yes
-
3
Yes
-
Yes
-
4
-
Yes
-
Yes
Table 1: Available models and specifications
3
ProducƟon process
Figure 1 illustrated the standard production process for each 4 models. The process begins as soon as
possible after an order is received from customer, however there can be delays since orders are placed online
and often during company holiday shutdowns. Each item is given a unique order number, linking to details on
model type and specification of materials.
Figure 1: The Process flow of production line
Order
Cuƫng &
Sizing
Planning &
Moulding
Joineries
Assembly
Fixing
Metal
Work
Cushion &
Upholstery
Finishing
Despatch
Packaging
Quality
Check
Rework
IniƟal
Treatment
Your preview ends here
Eager to read complete document? Join bartleby learn and gain access to the full version
- Access to all documents
- Unlimited textbook solutions
- 24/7 expert homework help
4
Manpower and Work PaƩern
The company has a diverse range of manpower needs, each with specialized skills and responsibilities. The
majority are employed in the production processes. Key categories of production staff:
Upholsterers
are considered the key craŌ-workers in the company. Responsible for covering and padding
furniture frames with materials like fabric, leather, foam, and baƫng. They sew, staple, and glue upholstery
materials to achieve the desired look and comfort specified by customers.
Assemblers
put together various furniture components, including frames, legs, and hardware, to create the
final product.
Finishers
apply stains, paints, and protecƟve coaƟngs to the furniture to enhance its appearance and
durability.
Quality control inspectors
examine finished furniture to ensure it meets design and quality standards. They
idenƟfy defects, imperfecƟons, or misalignments and may perform minor adjustments or repairs.
Designers and engineers
are responsible for creaƟng furniture designs and prototypes. They use computer-
aided design (CAD) to develop detailed plans and specificaƟons. Most designers are also effecƟvely
ProducƟon Managers
when overseeing the manufacturing process, coordinate workflow, and manage
producƟon schedules for their designs. This involves evaluaƟng the iniƟal treatment of the materials to
ensure they are appropriately and accurately applied in accordance to the company sustainability policies
(non-polluƟng) and workforce safety. Their role is supported by
Supervisors
, who provide direct supervision
to producƟon workers, ensuring tasks are completed efficiently and safely, and dealing with any issues
affecƟng producƟon flow.
Currently both locations have a similar working pattern with morning and afternoon shifts from Monday to Friday.
This may change in the future, since the CEO has asked the HR Director to look at the possibility of introducing
new working hours to improve actual production while maintaining the work-life balance ethos of KFS. The
company shuts down during festive periods such as Christmas, New Year and Easter.
The three new proposed shifts are shown in Table 2.
Current
New Shifts Option 1
New Shifts Option
2
New Shifts
Option 3
Operating
Day
Monday - Friday
Monday - Friday
Monday - Sunday
Monday - Saturday
Operating
Time
Morning shift:
7am – 2pm
Morning shift:
7am – 3pm
Morning shift:
7am – 3pm
Day shift:
9am-5pm
Afternoon shift:
2pm -9pm
Afternoon shift:
3pm -11pm
Afternoon shift:
3pm -9pm
Night shifts:
11pm – 7am
Table 2: Current and proposed new work pattern.
A survey was launched to get feedback from staff on the preference of new shifts arrangement (see KFS
data.xlsx).
5
ProducƟon, quality, and space concerns
The value proposition of the business is aligned with the KFS mission in providing high quality product and
services that place environment and social impacts as its core principle. Therefore, inspection is carried out to
check for any defects, imperfections, or misalignments. Quality control measures are vital
to ensure the furniture
meets both design specification and high safety standards.
The data provided by the production manager (see KFS data.xlsx) details the production of 1021 furniture orders
between 2021 and 2022. As advised by the quality control inspectors, the quality score of furniture produced
should reach 70 and over to avoid rework regardless of model or type of materials used. Any small defaults can
be rectified or fixed at the quality check or finishing section. The latest mean quality score is 81 but there is
much variability around this score. All major defaults will be labelled ‘Reject’ and send back to “Rework”, which
will cause disruption to the production plans and dispatch time as the same process will be repeated. It’s has
been accepted as basic feature of working with natural materials, and rework rates of up to 5% have been
accounted for in the pricing of the products, but recent data suggests this reworking has more than doubled.
This is worrying data from the quality perspective. The data also revealed the scale of the customer complaints
- categorised into 5 types (table 3).
Code
Complaint Type
Action
1
No Complaint
-
2
Less Complaint
No action required
3
Slightly High Complaint
Minor fixing at finishing station
4
High Complaint
Significant but not major fixing at
finishing station
5
Very High Complaint
Major rework and repeat production
process
Table 3: Category of complaints
It’s also noted that the space problems are becoming an issue when the demand is growing. The storage units
are limited and currently sharing storage spaces between Fife and Stirling. This has increased operational cost.
Furthermore, the lease at Fife premises is coming to run out in 2025. Each station has a capacity of 2
workstations except for quality check and packaging which only have one.
6
Management Review
On the last monthly meeting, the directors of the company have raised some concerns ideas for making some
changes to improve the productivity, quality and demand. Their comments recorded from the meeting are as
follows:
ProducƟon Director
– “Our production finally getting busy after Covid with every model showing a good lift in
the number of orders. However, our current methods for ‘initial treatment, cutting and moulding’ seems to be
taking too much time compared to the other process steps. We should consider installing a new laser treatment
machine that can reduce the treatment process from current average time to 2 hours for both materials. Finance
seems agreed with this idea. We need more people to reduce the quality inspection time and ensure all process
methods are appropriately followed. Well, the recent training scheme seems have improve the quality score and
thank you to HR for organising this. I supposed we should look at other approaches as well other than new
machines and training if we want to increase production by 30% to meet the forecasted demand.”
HR Director
– “Our People Strategy is incorporating our ethos in promoting work-life balance. The idea of new
shifts pattern may jeopardise what we are currently doing. Perhaps we should investigate issues of absenteeism
including lateness and unauthorised leaves if we want to improve productivity. We are keen to find out how
analysis of the HR data can support us to explore and diagnose these issues.
Finance Director
– “Buying a new machine maybe a good step for improving production, but it is expensive.
The capital investment is much higher than any other workstation to date and we are not sure if both locations
need it – they seem to perform at different quality of outputs with the same methods.”
MarkeƟng Director
– “The latest marketing campaign has clearly worked to bring in new customers, and they
love Model 1. But our customer relationship’s email inboxes also full of complaints. We should consider focusing
more on the highest sales models and drop Model 3 and 4 from the production. The complaints email folder
might be a lot less busy as a result.
Your preview ends here
Eager to read complete document? Join bartleby learn and gain access to the full version
- Access to all documents
- Unlimited textbook solutions
- 24/7 expert homework help
7
OpƟons
The latest productivity report highlighted on possible measures for quality improvement.
a)
SXL-2 CuƩer
is a new laser machine that can be used for wood and metal. Laser treatment for wood
allows for versatile and precise methods for a range of applications, including engraving, cutting,
marking, and surface treatment. The use of a laser in woodworking offers significant advantages over
traditional techniques, such as high-precision, speed, and greatly reduced material waste. The latest
version can also be used for cutting and scribing metals. The machine is expected to reduce up to 4
hours of average work-time for each of the first three production processes, reduce 2 hours from
inspection time and improving the quality average score up to 90.
b) A recent customer survey provides critical feedback, highlight the volume and nature of customer
complaints. By opting to discontinue Model 3 and 4, production line space could be freed up to
potentially allow an increase of 40% sales on Models 1 and 2; and reduce the amount of complaints.
c)
It’s estimated that the 24-hours shifts will provide a production increase of 22% but create challenging
conditions to staff who have caring responsibilities.
8
Assignment Tasks
KFS management has asked a group of analysts to explore the current state of the business operation and
develop some proposals for change, with particular focus on the issues related to staff absenteeism, quality and
demand.
They have provided company data in the file “
KFS data.xlxs
”.
Advice
You may want to consider forming some basic queries from a read through of the case, such as:
Do the issues of absenteeism depend on staff characteristics?
Does demand and quality dependent on product characteristics?
Does facility location contribute to quality issue or more?
In developing your report, you are asked to demonstrate a range of statistical tests, including at least one
each of:
a parametric test
a t-test
a non-parametric test
Submission and Notes
This assignment accounts for 50% of the module marks.
A Management Report is due by
12 noon, Tuesday 7th November 2023
Your assignment must be submitted electronically via
Canvas by only one person from each group.
Word limit: 1500 (+/- 10%) of Management Report (format style). You will be shown over the course of
the module how to structure a management report. You will be expected to follow the layout provided.
All reports go through Turnitin on submission. It is imperative that the work you submit is your own. If
there is any proof of copying or plagiarism this is a serious academic matter, and you may be called to
an academic integrity meeting.
It is the individual responsibility of each student/group to ensure that there is a low similarity index
score.
A high similarity index score must be investigated and rectified by the student/group prior to final
submission
of
the
assignment.
Information
on
how
to
use
TurnItIn
can
be
found
at:
http://www.plagiarism.stir.ac.uk/moreinfo.php
Related Documents
Recommended textbooks for you
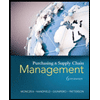
Purchasing and Supply Chain Management
Operations Management
ISBN:9781285869681
Author:Robert M. Monczka, Robert B. Handfield, Larry C. Giunipero, James L. Patterson
Publisher:Cengage Learning
Marketing
Marketing
ISBN:9780357033791
Author:Pride, William M
Publisher:South Western Educational Publishing
Recommended textbooks for you
- Purchasing and Supply Chain ManagementOperations ManagementISBN:9781285869681Author:Robert M. Monczka, Robert B. Handfield, Larry C. Giunipero, James L. PattersonPublisher:Cengage LearningMarketingMarketingISBN:9780357033791Author:Pride, William MPublisher:South Western Educational Publishing
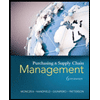
Purchasing and Supply Chain Management
Operations Management
ISBN:9781285869681
Author:Robert M. Monczka, Robert B. Handfield, Larry C. Giunipero, James L. Patterson
Publisher:Cengage Learning
Marketing
Marketing
ISBN:9780357033791
Author:Pride, William M
Publisher:South Western Educational Publishing