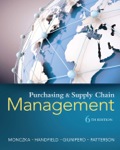
To calculate: The values of
Case summary:
Person BE is a quality engineer at Company ID. The commodity team has been assigned the responsibility of evaluation, negotiating, and selecting suppliers to be used in the company. The suppliers have a major impact on product quality. Person BE received a call regarding a manufacturing problem repeating continuously at a plant. Person BE was focused on identifying the process responsible for the defective component.
The management of supplier quality is an important aspect of any type of business that relies on the suppliers for the provision of goods and services. The activities involved are the management, monitoring, and response to changes in the ability of the supplier to satisfy the needs of the customers with the agreed upon quality.

Want to see the full answer?
Check out a sample textbook solution
Chapter C Solutions
Purchasing and Supply Chain Management
- Sam's Pet Hotel operates 50 weeks per year, 6 days per week, and uses a continuous review inventory system. It purchases kitty litter for $10.50 per bag. The following information is available about these bags: > Demand = 95 bags/week > Order cost = $55.00/order > Annual holding cost = 35 percent of cost > Desired cycle-service level = 80 percent > Lead time = 4 weeks (24 working days) > Standard deviation of weekly demand = 15 bags > Current on-hand inventory is 320 bags, with no open orders or backorders. a. Suppose that the weekly demand forecast of 95 bags is incorrect and actual demand averages only 75 bags per week. How much higher will total costs be, owing to the distorted EOQ caused by this forecast error? The costs will be $ 10.64 higher owing to the error in EOQ. (Enter your response rounded to two decimal places.) b. Suppose that actual demand is 75 bags but that ordering costs are cut to only $13.00 by using the internet to automate order placing. However, the buyer does…arrow_forwardBUS-660 Topic 4: Intege... W Midterm Exam - BUS-66... webassign.net b Answered: The binding c... × W Topic 4 Assignment - BU... how to get more chegg... b My Questions | bartleby + macbook screenshot - G... C Consider the following m... As discussed in Section 8.3, the Markowitz model uses the variance of the portfolio as the measure of risk. However, variance includes deviations both below and above the mean return. Semivariance includes only deviations below the mean and is considered by many to be a better measure of risk. (a) Develop a model that minimizes semivariance for the Hauck Financial data given in the file HauckData with a required return of 10%. Assume that the five planning scenarios in the Hauck Financial Services model are equally likely to occur. Hint: Modify model (8.10)-(8.19). Define a variable d for each 5 - scenario and let d≥ Ŕ – R¸ with d¸ ≥ 0. Then make the objective function: Min 1 5 Σας Let Min s.t. 15 FS = proportion of portfolio invested in the foreign…arrow_forwardOn a daily basis, the van is dispatched from Maplewood Hospital to pickup blood and platelet donations made at its local donation centers. The distances in miles between all locations may be found in the table below. Click the icon to view mileage data for Vampire Van. a. The van travels from the Hospital (A) to (B) to (C) to (D) to (E) and then returns to the Hospital (A). What is the total number of miles that the van must travel using this route? Route ABCDEA requires a total distance of miles. (Enter your response rounded to one decimal place.) More Info Maplewood City Center Westbrook Hospital (A) Donation Site (B) Donation Site (C) Municipal Park Donation Site (D) Valley Hills Donation Site (E) Maplewood 3.1 5.3 3.2 4.4 Hospital (A) City Center 3.1 6.7 2.2 4.3 Donation Site (B) Westbrook 5.3 Donation Site (C) 19 6.7 | 6.2 2.5 Municipal Park 3.2 2.2 6.2 | 4.6 Donation Site (D) Valley Hills 4.4 4.3 2.5 4.6 Donation Site (E) - ☑arrow_forward
- The Harvey Motorcycle Company produces three models: the Tiger, a sure-footed dirt bike; the LX2000, a nimble cafe racer; and the Golden, a large interstate tourer. The month's master production schedule calls for the production of 32 Goldens, 31 LX2000s, and 38 Tigers per 10-hour shift. What average cycle time is required for the assembly line to achieve the production quota in 10 hours? 0.099 hours per motorcycle. (Enter your response rounded to three decimal places.) If mixed-model scheduling is used, how many of each model will be produced before the production cycle is repeated? The greatest common divisor of the production requirements is Therefore, the Harvey Motorcycle Company will produce Goldens, LX2000s, and Tigers. (Enter your responses as integers.)arrow_forwardThe Harvey Motorcycle Company produces three models: the Tiger, a sure-footed dirt bike; the LX2000, a nimble cafe racer; and the Golden, a large interstate tourer. The month's master production schedule calls for the production of 32 Goldens, 31 LX2000s, and 38 Tigers per 10-hour shift. What average cycle time is required for the assembly line to achieve the production quota in 10 hours? hours per motorcycle. (Enter your response rounded to three decimal places.)arrow_forwardThe binding constraints for this problem are the second and third constraints are binding. Min x1 + 2x2 s.t. x1 + x2 ≤ 300 2x1 + x2 ≥ 400 2x1 + 5x2 ≥750 X1, X220 (a) Keeping the second objective function coefficient fixed at 2, over what range can the first objective function coefficient vary before there is a change in the optimal solution point? The first objective coefficient can from a low of to a high of (b) Keeping the first objective function coefficient fixed at 1, over what range can the second objective function coefficient vary before there is a change in the optimal solution point? The second objective coefficient can from a low of to a high of (c) If the objective function becomes Min 1.5x₁ + 2x2, what will be the optimal values of x1 and x2? x1 = X2 = What is the value of the objective function at the minimum? (d) If the objective function becomes Min 7x₁ + 6x2, what constraints will be binding? (Select all that apply.) First Constraint Second Constraint Third Constraint…arrow_forward
- [-16.66 Points] DETAILS MY NOTES CAMMIMS16 4.E.008. 0/1 Submissions Used A linear programming computer package is needed. ASK YOUR TEACHER PRACTICE ANOTHER The Clark County Sheriff's Department schedules police officers for 8-hour shifts. The beginning times for the shifts are 8:00 a.m., noon, 4:00 p.m., 8:00 p.m., midnight, and 4:00 a.m. An officer beginning a shift at one of these times works for the next 8 hours. During normal weekday operations, the number of officers needed varies depending on the time of day. The department staffing guidelines require the following minimum number of officers on duty: Time of Day 8:00 A.M. Noon Noon - 4:00 P.M. Minimum Officers Time of Day on Duty 4 7 4:00 P.M. - 8:00 P.M. 11 8:00 P.M. Midnight 6 Midnight 4:00 A.M. 4:00 A.M. -8:00 A.M. 3 7 Determine the number of police officers that should be scheduled to begin the 8-hour shifts at each of the six times (8:00 a.m., noon, 4:00 p.m., 8:00 p.m., midnight, and 4:00 a.m.) to minimize the total number…arrow_forwarddiscuss in detail the benefits of working in a teamarrow_forwardExplain why some people resist working in a team.arrow_forward
- Discuss the Open Systems Approach to Teamworkarrow_forwarddiscuss team development stagesarrow_forwardLearning Activity 6: Canadian Business This Year Read the following webpage: The Business Development Bank of Canada. (2023). Canadian economic outlook for 2024: Shifting into neutral. https://www.bdc.ca/en/articles- tools/blog/canadian-economic-outlook-for-2024- shifting-into-neutral "Despite persistently high inflation and rising. interest rates, the news was generally better than expected for the Canadian economy in 2023" (BDC Blog 2024). Discussion Question: In your view, what are the most pressing problems for Canadian companies or consumers in 2024? Explain your answer using current examples of companies or consumer concerns.arrow_forward
- Purchasing and Supply Chain ManagementOperations ManagementISBN:9781285869681Author:Robert M. Monczka, Robert B. Handfield, Larry C. Giunipero, James L. PattersonPublisher:Cengage LearningMarketingMarketingISBN:9780357033791Author:Pride, William MPublisher:South Western Educational PublishingContemporary MarketingMarketingISBN:9780357033777Author:Louis E. Boone, David L. KurtzPublisher:Cengage Learning
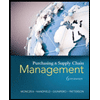
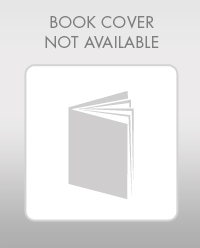