OPERATIONS MANAGEMENT CUSTOM ACCESS
11th Edition
ISBN: 9780135622438
Author: KRAJEWSKI
Publisher: PEARSON EDUCATION (COLLEGE)
expand_more
expand_more
format_list_bulleted
Concept explainers
Question
Chapter C, Problem 14P
Summary Introduction
Interpretation:The production level and the sales that need to be achieved in reaching the highest profits are to be calculated.
Concept Introduction:The production level and the sales should be decided based on the
Expert Solution & Answer

Want to see the full answer?
Check out a sample textbook solution
Students have asked these similar questions
What do you feel is the most effective way to communicate with families? Describe how you have used this/these technique(s).
PP.52 A manufacturer of solid state drives (SSDs) has projected the next six months of demand to be as shown the table below:
Supply/Demand Info
Beginning
Jan
Feb
Mar
Apr
May
Jun
Forecast (demand)
53,800
53,400
51,000
63,800
49,200
59,000
Regular production
Overtime production
Subcontract production
Ending inventory
4,000
Hired employees
Fired employees
Total employees
190
Cost variables are as follows:
Cost Variables
Labor cost/hour
$16
Overtime cost/unit
$39
Subcontracting cost/unit
$35
Holding cost/unit/month
$14
Hiring cost/employee
$3,100
Firing cost/employee
$5,500
Here is some additional relevant (capacity) information:
Capacity Information
Total labor hours/SSD
4
Regular production units/employee/month
200…
Discuss how a human resource professional can better gain the confidence of senior management and, thereby, become a key participant/player in the organization’s future.
Chapter C Solutions
OPERATIONS MANAGEMENT CUSTOM ACCESS
Knowledge Booster
Learn more about
Need a deep-dive on the concept behind this application? Look no further. Learn more about this topic, operations-management and related others by exploring similar questions and additional content below.Similar questions
- PP.63 Jupiter, a large candy company, is having great success with its "Swan" family of candy bars. Due to a number of factors they like to plan their production at least six months into the future. The table below contains their demand projections (in tons) for April through September: Supply/Demand Info Beginning Apr May Jun Jul Aug Sep Predicted Sales 45,500 45,100 51,900 52,800 47,900 47,200 Regular production Overtime production Subcontract production Ending inventory 14,400 Hired employees Fired employees Total employees 423 Cost variables are as follows: Cost Variables Labor cost/hour $13 Overtime cost/ton $30 Subcontracting cost/ton $28 Holding cost/ton/month $14 Hiring cost/employee $3,700 Firing cost/employee $5,800 Here is some additional…arrow_forwardWhat are the responsibilities and duties of a consultant for a local company who is considering expanding its operations to international markets? How can a local Agriculture and Food Processing company successfully enter international markets?arrow_forwardWhat is an example of how someone would explain how their past personal and professional experience makes you a quality candidate for a teaching position at an Elementary School as a K-6 Teacher?arrow_forward
- I need answer typing clear urjent no chatgpt used pls i will give 5 Upvotes.arrow_forwardHow can a local tourism and hospitality company successfully enter international markets?arrow_forwardHow was Circuit City Company collapsed? And what was the sequence of time and events or problems? How to solve the issues, and could you help identify positions or titles. Sanitize all names and use only fictitious data. What is synthesize the qualitative research methodology of Case Study research? Please give some examples. How to use the practical of Lean Six Sigma to develop a business-facing DMAIC-based case studyarrow_forward
- BUSINESS MODEL CANVAS: U.S ARMY key partners: Key activities: Key Resources: Value Propositions: Buy-in & Support: Deployment: Benficiaries: Mission budget/cost: Mission Achievement/ Impact factors: Please at least 4 for each categoryarrow_forwardhow you would best conduct a performance evaluation meeting with a subordinate (where an employee would receive their performance evaluation from their supervisor). Importantly, detail how a supervisor can best gain the concurrence from an employee on the evaluation itself, and to ensure that the employee’s performance will be modified as a result of appraisal meeting.arrow_forwardI need answer typing clear urjent no chatgpt used pls i will give 5 Upvotes.arrow_forward
- assume that you are police commander which leads and supervises the department’s internal affairs division. Your goal is to reduce civilian complainants against personnel in the department. Using what you have learned and at least three scholarly sources, document two changes you see the department can implement, whether it be training, planning, mitigating, and resolving, to improve police/community relations.arrow_forwardNess Engineering is a private limited company mainly engaged in the continuous production and assembly of domestic products. The annual turnover is $900,000,000. The largest area of expenditure is raw materials and components where the annual spend is approximately $450,000,000. The Managing Director, Bill, considers that profit margins are too small and has asked you to suggest how profitability might be increased. Bill suggests that this might be done by appointing additional sales staff and by an advertising campaign, which would, hopefully, increase turnover and thereby reduce overhead cost per item. You find that purchasing is little more than a post-office function. Specifications are received from the design or user departments and sent either to supplies designated by the directors or to the supplier providing the cheapest quotation. The company does, in fact, deal with many suppliers and issues many orders for low-cost items. All purchasing is done by manual means. None of the…arrow_forwardThe oasis outpost of Abu Ilan, in the heart of the Negev desert, has a population of 20 Bedouin tribesmen and 20 Farima tribesmen. El Kamin, a nearby oasis, has a population of 32 Bedouins and 8 Farima. A lost Israeli soldier, accidentally separated from his army unit, is wandering through the desert and arrives at the edge of one of the oases. The soldier has no idea which oasis he has found, but the first person he spots at a distance is a Bedouin. 1. What is the probability that he wandered into Abu Ilan? 2. What is the probability that he is in El Kamin?arrow_forward
arrow_back_ios
SEE MORE QUESTIONS
arrow_forward_ios
Recommended textbooks for you
- Purchasing and Supply Chain ManagementOperations ManagementISBN:9781285869681Author:Robert M. Monczka, Robert B. Handfield, Larry C. Giunipero, James L. PattersonPublisher:Cengage LearningPractical Management ScienceOperations ManagementISBN:9781337406659Author:WINSTON, Wayne L.Publisher:Cengage,
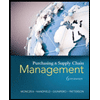
Purchasing and Supply Chain Management
Operations Management
ISBN:9781285869681
Author:Robert M. Monczka, Robert B. Handfield, Larry C. Giunipero, James L. Patterson
Publisher:Cengage Learning
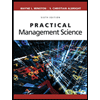
Practical Management Science
Operations Management
ISBN:9781337406659
Author:WINSTON, Wayne L.
Publisher:Cengage,
Single Exponential Smoothing & Weighted Moving Average Time Series Forecasting; Author: Matt Macarty;https://www.youtube.com/watch?v=IjETktmL4Kg;License: Standard YouTube License, CC-BY
Introduction to Forecasting - with Examples; Author: Dr. Bharatendra Rai;https://www.youtube.com/watch?v=98K7AG32qv8;License: Standard Youtube License