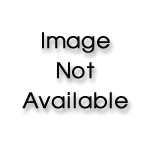
MyLab Operations Management with Pearson eText -- Access Card -- for Operations Management: Processes and Supply Chains
12th Edition
ISBN: 9780134742366
Author: Lee J. Krajewski, Manoj K. Malhotra, Larry P. Ritzman
Publisher: PEARSON
expand_more
expand_more
format_list_bulleted
Concept explainers
Textbook Question
Chapter 9, Problem 7P
Southern Markets, Inc. is considering the use of ABC analysis to focus on the most critical SKUs in its inventory. Currently, there are approximately 20,000 different SKUs with a total dollar usage of $10,000,000 per year.
- What would you expect to be the number of SKUs and the total annual dollar usage for A items, B items, and C items at Southern Markets, Inc.?
- The following table provides a random sample of the unit values and annual demands of eight SKUs. Categorize these SKUs as A, B, and C items.
Expert Solution & Answer

Want to see the full answer?
Check out a sample textbook solution
Students have asked these similar questions
I need answer typing clear urjent no chatgpt used pls i will give 5 Upvotes.with diagram
not use ai please
provide scholarly reseach and references for the following
1. explain operational risks and examples of such risk faced by management at financial institutions
2. discuss the importance of establishing an effective risk management policy at financial institutions to manage operational risk, giving example of a risk management strategy used by financial institutions to mitigate such risk.
3. what is the rold of the core principles of effective bank supervision as it relates to operational risk, in the effective management of financial institutions.
Chapter 9 Solutions
MyLab Operations Management with Pearson eText -- Access Card -- for Operations Management: Processes and Supply Chains
Ch. 9 - What is the relationship between inventory and the...Ch. 9 - Suppose that a large discount retailer with a lot...Ch. 9 - Will organizations ever get to the point where...Ch. 9 - A part is produced in lots of 1,000 units. It is...Ch. 9 - Prince Electronics, a manufacturer of consumer...Ch. 9 - Terminator, Inc. manufactures a motorcycle part in...Ch. 9 - Ruby-Star Incorporated is considering two...Ch. 9 - Haley Photocopying purchases paper from an...Ch. 9 - Prob. 6PCh. 9 - Southern Markets, Inc. is considering the use of...
Ch. 9 - New Wave Shelving’s inventory manager would like...Ch. 9 - Yellow Press, Inc. buys paper in 1,500-pound rolls...Ch. 9 - Babble, Inc. buys 400 blank cassette tapes per...Ch. 9 - At Dot Com, a large retailer of popular books,...Ch. 9 - Leaky Pipe, a local retailer of plumbing supplies,...Ch. 9 - Sam’s Cat Hotel operates 52 weeks per year, 6...Ch. 9 - Consider again the kitty litter ordering policy...Ch. 9 - In a Q system, the demand rate for strawberry ice...Ch. 9 - Petromax Enterprises uses a continuous review...Ch. 9 - In a continuous review inventory system, the lead...Ch. 9 - In a two-bin inventory system, the demand for...Ch. 9 - You are in charge of inventory control of a highly...Ch. 9 - Your firm uses a continuous review system and...Ch. 9 - A company begins a review of ordering policies for...Ch. 9 - Prob. 22PCh. 9 - The Farmer’s Wife is a country store...Ch. 9 - Prob. 24PCh. 9 - Prob. 25PCh. 9 - Prob. 26PCh. 9 - In a P system, the lead time for a box of...Ch. 9 - Suppose that Sam’s Cat Hotel in Problem 13 uses...Ch. 9 - Your firm uses a periodic review system for all...Ch. 9 - Using the same information as in Problem 21,...Ch. 9 - Wood County Hospital consumes 1,000 boxes of...Ch. 9 - A golf specialty wholesaler operates 50 weeks per...Ch. 9 - What is the EOQ and what is the lowest total cost?Ch. 9 - What is the annual cost of holding inventory at...Ch. 9 - Prob. 3AMECh. 9 - Prob. 4AMECh. 9 - Prob. 5AMECh. 9 - Prob. 6AMECh. 9 - Comment on the sensitivity of the EOQ model to...Ch. 9 - Consider the pressures for small versus large...Ch. 9 - Prob. 2VCCh. 9 - The Marker Maker© product recently experienced an...Ch. 9 - Put yourself in Sue McCaskey’s position and...Ch. 9 - By how much do your recommendations for these two...
Additional Business Textbook Solutions
Find more solutions based on key concepts
Assume you are a CFO of a company that is attempting to race additional capital to finance an expansion of its ...
Financial Accounting, Student Value Edition (5th Edition)
How did the recession of 2007-2009 compare with other recessions since the Great Depression in terms of length?...
Foundations of Financial Management
Place the letter of the appropriate accounting cost in Column 2 in the blank next to each decision category in ...
Fundamentals of Cost Accounting
The flowchart for the process at the local car wash. Introduction: Flowchart: A flowchart is a visualrepresenta...
Principles of Operations Management: Sustainability and Supply Chain Management (10th Edition)
Fundamental and Enhancing Characteristics. Identify whether the following items are fundamental characteristics...
Intermediate Accounting (2nd Edition)
The Warm and Toasty Heating Oil Company used to deliver heating oil by sending trucks that printed out a ticket...
Essentials of MIS (13th Edition)
Knowledge Booster
Learn more about
Need a deep-dive on the concept behind this application? Look no further. Learn more about this topic, operations-management and related others by exploring similar questions and additional content below.Similar questions
- Please show all units, work, and steps needed to solve this problem I need answer typing clear urjent no chatgpt used pls i will give 5 Upvotes.arrow_forwardIM.82 A distributor of industrial equipment purchases specialized compressors for use in air conditioners. The regular price is $50, however, the manufacturer of this compressor offers quantity discounts per the following discount schedule: Option Plan Quantity Discount A 1 - 299 0% B 300 - 1,199 0.50% C 1,200+ 1.50% The distributor pays $56 each time it places an order with the manufacturer. Holding costs are negligible (none) but they do earn 10% annual interest on all cash balances (meaning there will be a financial opportunity cost when they put cash into inventory). Annual demand is expected to be 10,750 units. When there is no quantity discount (Option Plan A, the first row of the schedule listed above), what is the adjusted order quantity? (Display your answer to the nearest whole number.) 491 Based on your answer to the previous question, and based on the annual demand as stated above, what will be the annual ordering costs? (Display your answer to the…arrow_forwardExcel Please. The workload of many areas of banking operations varies considerably based on time of day. A variable capacity can be achieved effectively by employing part-time personnel. Because part-timers are not entitled to all the fringe benefits, they are often more economical than full-time employees. Other considerations, however, may limit the extent to which part-time people can be hired in a given department. The problem is to find an optimal workforce schedule that would meet personnel requirements at any given time and also be economical. Some of the factors affecting personnel assignments are listed here: The bank is open from 9:00am to 7:00pm. Full-time employees work for 8 hours (1 hour for lunch included) per day. They do not necessarily have to start their shift when the bank opens. Part-time employees work for at least 4 hours per day, but less than 8 hours per day and do not get a lunch break. By corporate policy, total part-time personnel hours is limited…arrow_forward
- IM.84 An outdoor equipment manufacturer sells a rugged water bottle to complement its product line. They sell this item to a variety of sporting goods stores and other retailers. The manufacturer offers quantity discounts per the following discount schedule: Option Plan Quantity Price A 1 - 2,399 $5.50 B 2,400 - 3,999 $5.20 C 4,000+ $4.50 A large big-box retailer expects to sell 9,700 units this year. This retailer estimates that it incurs an internal administrative cost of $225 each time it places an order with the manufacturer. Holding cost for the retailer is $55 per case per year. (There are 40 units or water bottles per case.) Based on this information, and not taking into account any quantity discount offers, what is the calculated EOQ (in units)? (Display your answer to the nearest whole number.) Number Based on this information, sort each quantity discount plan from left to right by dragging the MOST preferred option plan to the left, and the LEAST preferred…arrow_forwardIn less than 150 words, what is an example of what your reflection of core values means to you and your work: Commitment, Perseverance, Community, Service, Pride?arrow_forwardPrepare a report on the following: Part 1: Discuss the role of the corporate secretary in facilitating effective governance in a limited liability company. Include the relationships with directors, shareholders, and other officers. Part 2: Compare and contrast two characteristics of different business entities (sole trader, partnership, and limited liability company). Use examples to recommend the most appropriate type of business entity for the scenario below: Scenario Background Alex, Taylor, and Jordan plan to collaborate to launch a tech startup focused on developing and selling innovative software solutions. Each individual brings unique skills and resources to the venture: Alex: A skilled software developer with technical expertise and a vision for the product. Taylor: A marketing professional with extensive connections in the technology industry, aiming to drive sales and build the brand. Jordan: An investor willing to contribute significant financial resources but…arrow_forward
- Problem 1 (20 Points) Davison Electronics manufactures three LED television monitors, identified as Model A, Model B, and Model C. Davison Electronics four manufacturing plants. Each model has its lowest possible production cost when produced at Plant 1. However, Plant 1 does not have the capacity to handle the total production of all three models. As a result, at least some of the production must be routed to the other manufacturing plants. The following table shows the minimum production requirements for next month, the plant capacities in units per month, and the production cost per unit at each plant: Model Production Cost per Unit Minimum Production Requirements Plant 1 Plant 2 Plant 3 Plant 4 A $25 $28 $37 $34 48,000 B $26 $35 $36 $41 75,000 C $20 $31 $26 $23 60,000 Production Capacity 65,000 50,000 32,000 43,000 Davison’s objective is to determine the cost-minimizing production plan. Without…arrow_forwardSECTION B: TOPIC STRUCTURE CAPSTONE PROJECT TOPIC SUBMISSION TEMPLATE SECTION A: STUDENT DETAILS Student number Title (Mr/Miss/Ms/Mrs) Surname First name/s Title of research Date and year of registration Work Home Contact details Cell Region Date submitted Email 1.1 Title Insert title of the research. Choose a title that captures the essence of your proposed project. 1.2 Background to the Problem This section will be used to create the readers' interest. It can include a specific description of the topic that is to be investigated. A brief preview of the topic and the foundation of the problem should also be given. The researcher can achieve this through building up a detailed background of circumstances that lead to the problem being examined. Therefore, the background helps the reader understand the specific problem addressed by the researcher. This section should not include the background/history of the organisation. The background to the problem should not be more than ½ a page.…arrow_forwardDoes Nike Corporation's emphasis on lean operations help the Vietnamese workforce that still earns $150.00 minimum wage a month since 2014?arrow_forward
- Information Security Innovation within a Contemporary Business Environment All organisations using computers need to consider the security of information they keep. Many organisations utilise Websites for their core business functions and this results in monetary transactions being carried out on the Websites.arrow_forwardPlease help with a complete research report on the topic below: "Information Security Innovation within a Contemporary Business Environment " The format of the report should follow this below.arrow_forward7. Wireless Infrastructure in the Cloud Wireless devices have changed the way organisations and their customers interact. Wireless enabled devices have driven the mindset that wireless networks must be ubiquitous, fast, and constantly available. These are demands that have traditionally put organisations and their user communities in direct conflict with their IT departments, as constructing and maintaining wireless infrastructures are typically time-consuming, complex, and costly endeavours.arrow_forward
arrow_back_ios
SEE MORE QUESTIONS
arrow_forward_ios
Recommended textbooks for you
- Purchasing and Supply Chain ManagementOperations ManagementISBN:9781285869681Author:Robert M. Monczka, Robert B. Handfield, Larry C. Giunipero, James L. PattersonPublisher:Cengage LearningMarketingMarketingISBN:9780357033791Author:Pride, William MPublisher:South Western Educational Publishing
- Practical Management ScienceOperations ManagementISBN:9781337406659Author:WINSTON, Wayne L.Publisher:Cengage,
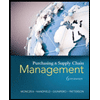
Purchasing and Supply Chain Management
Operations Management
ISBN:9781285869681
Author:Robert M. Monczka, Robert B. Handfield, Larry C. Giunipero, James L. Patterson
Publisher:Cengage Learning
Marketing
Marketing
ISBN:9780357033791
Author:Pride, William M
Publisher:South Western Educational Publishing
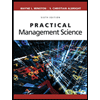
Practical Management Science
Operations Management
ISBN:9781337406659
Author:WINSTON, Wayne L.
Publisher:Cengage,
Inventory Management | Concepts, Examples and Solved Problems; Author: Dr. Bharatendra Rai;https://www.youtube.com/watch?v=2n9NLZTIlz8;License: Standard YouTube License, CC-BY