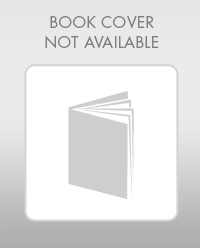
Concept explainers
Terminator, Inc. manufactures a motorcycle part in lots of 250 units. The raw materials cost for the part is $150, and the value added in manufacturing 1 unit from its components is $300, for a total cost per completed unit of $450. The lead time to make the part is 3 weeks, and the annual demand is 4,000 units. Assume 50 working weeks per year.
- How many units of the part are held, on average, as cycle inventory? What is its value?
- How many ii nit S of the part are held, on average, as pipeline inventory? What is its value?

Want to see the full answer?
Check out a sample textbook solution
Chapter 9 Solutions
Operations Management: Processes And Supply Chains (12th Global Edition) - Does Not Include Mylab Operations Management
Additional Business Textbook Solutions
Operations Management, Binder Ready Version: An Integrated Approach
OPERATIONS MANAGEMENT IN THE SUPPLY CHAIN: DECISIONS & CASES (Mcgraw-hill Series Operations and Decision Sciences)
Operations and Supply Chain Management 9th edition
Business in Action (8th Edition)
Operations Management
Loose-leaf for Operations Management (The Mcgraw-hill Series in Operations and Decision Sciences)
- Bhatti Company produces plastic photo frames. Two departments, molding and finishing, are involved in the manufacturing. The molding department fills the molds with hot liquid plastic that is left to cool and then opens them. The finishing department removes the plastic frame from the mold and strips the edges of the frames of extra plastic. The following information is available for the month of January: January 1 Quantity (pounds) January 31 Quantity (pounds) Work-in-Process Inventory Cost Cost Molding department Finishing department None None 5,000 $ 15,000 2,000 The WIP Inventory in the finishing department is estimated to be 40% complete for conversion both at the beginning and end of January. Costs of production for January follow: Direct Costs of Production Materials Conversion Molding department Finishing department $ 450,000 $ 90,000 80,290 The molding department started 50,000 pounds of product in January. The firm uses the FIFO method of process costing. Required: 1. Prepare…arrow_forwardConsider the following information. PART X Gross Requirements Scheduled Receipts Projected On-Hand Inventory 100 Q = 60, LT= 3 weeks, Safety Stock = 5 1 70 70 PART X Gross Requirements Scheduled Receipts Projected On-Hand Inventory 100 Planned Order Releases 1 70 70 100 2 0 > X WEEK 3 40 Compute the planned order releases and projected on-hand inventory for component part X. Round your answers to the nearest whole number. If your answer is zero, enter "0". 2 0 4 0 100 WEEK 3 40 5 160 60 4 0 40 0 X 5 160 Check My Work -60 0arrow_forwardFast pleasearrow_forward
- Owen Conner works part-time packaging software for a local distribution company in Indiana. The annual i xed cost is $10,000 for this process, direct labor is $3.50 per package, and material is $4.50 per package. The selling price will be $12.50 per package. How much revenue do we need to take in before breaking even? What is the break-even point in units?arrow_forwardPranuec Company mai Tactures, assembles, and rebunds material handing equipment used Tn war ses and uistr iters. One product, called a Liftmaster, is assembled from four components: a frame, a motor, two supports, and a metal strap. Frandec's production schedule calls for 6000 Liftmasters to be made next month. Frandec purchases the motors from an outside supplier, but the frames, supports, and straps may be either manufactured by the company or purchased from an outside supplier. Manufacturing and purchase costs per unit are shown. Component Manufacturing Cost Purchase Cost Frame $39.00 $52.00 Support $12.50 $16.00 Strap $7.50 $8.50 Three departments are involved in the production of these components. The time (in minutes per unit) required to process each component in each department and the available capacity (in hours) for the three departments are as follows: Department Component Cutting Milling Shaping Frame 3.6 2.3 3.2 Support 1.4 1.8 2.7 Strap 0.9 1.8 Capacity (hours) 370 430…arrow_forwardDraw a simple bill-of-materials (BOM) for a smart phone given the following requirements: (a) clearly label the end item and each component, (b) the BOM must contain no more than ten items, (c) the BOM must contain at least three levels (you may count the end-item level zero).arrow_forward
- Draw an approximate bill-of-materials (BOM) for a kid’s toy of your choice following these requirements: I would like to use the Jollibee plush Bee toy. (a) clearly label the end item and each component, (b) the BOM must contain no more than 20 items, (c) the BOM must contain at least three levels (you may count the end-item level zero).arrow_forwardJulia Martin is the production manager of a ready to wear manufacturing outfit. A decision needs to be made about the type of clothing material or fabric to be used to make a shirt. The fabric that has been used in the previous production cost P 40 per yard but it is not available currently. Similar material from another supplier will cost P 50 per yard. Required: Identify all costs that you can see in the Julia Martin problem. Explain simply why you classified it as such.arrow_forwardA-Plus Printing Setup fee: $20 Each poster: $0.10 Print More Setup fee: $55 Each poster: $0.05 Complete the table to see how much it would cost for different numbers of posters. After completing the table, what do you notice? the table is in the imagearrow_forward
- I understand that as per the calculations, the gross requirement for week 3 is 50 (25*2) (Item A's order releases), week 5 is 190 (20*2) + (150*1) (Item A's order releases + Item B's order releases), and week 6 is 300 (150*2) (Item A's order releases). But I want to know why do we do it that way because If I have a similar question do I always multiply item A's order release for week 3 by 2, week 5 (Item A's order releases x 2 + Item B's order releases x 1), and and week 6 (Item A's order releases x 2 ) I want to understand why we do that so I can anwser a similar question I don't understand why we do that have way just that you did it that wayarrow_forwardPlease see image for instructions. I need to find the Net requirement for all.arrow_forwardUse the quantity model for production orders.arrow_forward
- Practical Management ScienceOperations ManagementISBN:9781337406659Author:WINSTON, Wayne L.Publisher:Cengage,Operations ManagementOperations ManagementISBN:9781259667473Author:William J StevensonPublisher:McGraw-Hill EducationOperations and Supply Chain Management (Mcgraw-hi...Operations ManagementISBN:9781259666100Author:F. Robert Jacobs, Richard B ChasePublisher:McGraw-Hill Education
- Purchasing and Supply Chain ManagementOperations ManagementISBN:9781285869681Author:Robert M. Monczka, Robert B. Handfield, Larry C. Giunipero, James L. PattersonPublisher:Cengage LearningProduction and Operations Analysis, Seventh Editi...Operations ManagementISBN:9781478623069Author:Steven Nahmias, Tava Lennon OlsenPublisher:Waveland Press, Inc.
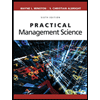
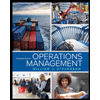
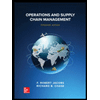
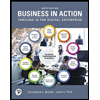
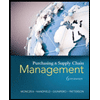
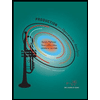