Orbital Industries of Canada, Inc. manufactures a variety of materials and equipment for the aerospace industry. A team of R & D engineers in the firm’s Winnipeg plant has developed a new material that will be useful for a variety of purposes in orbiting satellites and spacecraft. Tradenamed Ceralam, the material combines some of the best properties of both ceramics and laminated plastics. Ceralam is already being used for a variety of housings in satellites produced in three different countries. Ceralam sheets are produced in an operation called rolling, in which the various materials are rolled together to form a multilayer laminate. Orbital Industries sells many of these Ceralam sheets just after the rolling operation to aerospace firms worldwide. However, Orbital also processes many of the Ceralam sheets further in the Winnipeg plant. After rolling, the sheets are sent to the molding operation, where they are formed into various shapes used to house a variety of instruments. After molding, the sheets are sent to the punching operation, where holes are punched in the molded sheets to accommodate protruding instruments, electrical conduits, and so forth. Some of the molded and punched sheets are then sold. The remaining units are sent to the dipping operation, in which the molded sheets are dipped in a special chemical mixture to give them a reflective surface.
During the month of March, the following products were manufactured at the Winnipeg plant. The direct-material costs also are shown.
The costs incurred in producing the various Ceralam products in the Winnipeg plant during March are shown in the following table. Manufacturing
Orbital Industries of Canada uses operation costing for its Ceralam operations in the Winnipeg plant.
Required:
- 1. Prepare a table that includes the following information for each of the four operations.
- Total conversion costs.
- Units manufactured.
- Conversion cost per unit.
- 2. Prepare a second table that includes the following information for each product (i.e., rolled Ceralam sheets, nonreflective Ceralam housings, and reflective Ceralam housings).
- Total
manufacturing costs . - Units manufactured.
- Total cost per unit.
- Total
- 3. Prepare
journal entries to record the flow of all manufacturing costs through the Winnipeg plant’s Ceralam operations during March. (Ignore the journal entries to record sales revenue.) - 4. Build a spreadsheet: Construct an Excel spreadsheet to solve requirements 1 and 2 above. Show how the solution will change if the following data change: the cost of direct material used in dipping was $45,000 and the overhead application rate is 200% of direct-labor cost.

Want to see the full answer?
Check out a sample textbook solution
Chapter 4 Solutions
MANAGERIAL ACCOUNTING (PRINT UPGRADE)
- A computer consulting company uses job costing system and has a pre-determined overhead rate of $24 per direct labor hour. This amount is based on an estimated overhead of $23,000 and 2,000 estimated Direct Labor hours. In addition, Selling, General, and Administrative (SG&A) costs for the period totaled $155,000. Total units produced during the period were 1,250,000. Job # 175 incurred direct material costs of $60 and three direct labor hours costing of $83 per hour. What is the total cost of Job # 175? Don't Use Aiarrow_forwardWhat are inventory errors? What inventory method does Airbnb use?arrow_forwardWhat is the amount of gain or loss recorded on the sale of this vehicle for this financial accounting question?arrow_forward
- Please provide solution this financial accounting questionarrow_forwardcan you please solve thisarrow_forwardRolles Company has a contribution margin ratio of 27%. The company is considering a proposal that will increase sales by $130,000. What increase in profit can be expected assuming total fixed costs increase by $25,000?arrow_forward
- Managerial Accounting: The Cornerstone of Busines...AccountingISBN:9781337115773Author:Maryanne M. Mowen, Don R. Hansen, Dan L. HeitgerPublisher:Cengage LearningCornerstones of Cost Management (Cornerstones Ser...AccountingISBN:9781305970663Author:Don R. Hansen, Maryanne M. MowenPublisher:Cengage LearningAccounting Information SystemsAccountingISBN:9781337619202Author:Hall, James A.Publisher:Cengage Learning,
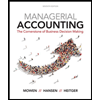
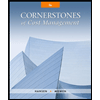
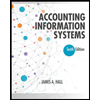