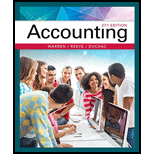
Concept explainers
Accounting for materials costs
In papermaking operations for companies such as International Paper Company, wet pulp is fed into paper machines, which press and dry pulp into a continuous sheet of paper. The paper is formed at very high speeds (60 mph). Once the paper is formed, the paper is rolled onto a reel at the hack end of the paper machine. One of the characteristics of papermaking is the creation of “broke" paper. Broke is paper that fails to satisfy quality standards and is therefore rejected for final shipment to customers. Broke is recycled hack to the beginning of the process by combining the recycled paper with virgin (new) pulp material. The combination of virgin pulp and recycled broke is sent to the paper machine for papermaking. Broke is fed into this recycle process continuously from all over the facility.
In this industry, it is typical to charge the papermaking operation with the cost of direct materials, which is a mixture of virgin materials and broke. Broke has a much lower cost than does virgin pulp. Therefore, the more broke in the mixture, the lower the average cost of direct materials to the department. Papermaking managers frequently comment on the importance of broke for keeping their direct materials costs down
a. How do you react to this accounting procedure?
b. What “hidden costs” are not considered when accounting for broke as described?

Trending nowThis is a popular solution!

Chapter 20 Solutions
Accounting
- Gale Corporation owns 15% of the common stock of Troy Enterprises and uses the fair-value method to account for this investment. Troy reported net income of $140,000 for 2022 and paid dividends of $80,000 on November 1, 2022. How much income should Gale recognize on this investment in 2022? a. $21,000 b. $12,000 c. $33,000 d. $9,500 e. $60,000arrow_forwardHow much income should Mason investments recognize on this investment in 2024 on these financial accounting question?arrow_forwardPresented below is the trial balance of Sandhill Corporation at December 31, 2020. Debit Credit Cash $289,100 Sales Revenue $11,907,000 Debt Investments (trading) (at cost, $218,000) 225,400 Cost of Goods Sold 7,056,000 Debt Investments (long-term) 439,040 Equity Investments (long-term) 407,680 Notes Payable (short-term) 132,300 Accounts Payable 668,360 Selling Expenses 2,940,000 Investment Revenue 93,100 Land 382,200 Buildings 1,528,800 Dividends Payable 199,920 Accrued Liabilities 141,120 Accounts Receivable 638,960 Accumulated Depreciation–Buildings 223,440 Allowance for Doubtful Accounts 37,240 Administrative Expenses 1,323,000 Interest Expense 310,660 Inventory 877,100 Gain 117,600 Notes Payable (long-term) 1,323,000 Equipment 882,000 Bonds Payable 1,470,000 Accumulated Depreciation–Equipment 88,200 Franchises 235,200 Common Stock ($5 par) 1,470,000 Treasury Stock 281,260 Patents 287,140 Retained Earnings 114,660 Paid-in Capital in Excess of Par 117,600 Totals $18,103,540 Debit…arrow_forward
- Aram's taxable income before considering capital gains and losses is $85,000. Determine Aram's taxable income and how much of the income will be taxed at ordinary rates in each of the following alternative scenarios (assume Aram files as a single taxpayer). Aram sold a capital asset that he owned for more than one year for a $3,750 gain, a capital asset that he owned for more than one year for a $550 loss, a capital asset that he owned for six months for a $450 gain, and a capital asset he owned for two months for a $2,400 loss. What is taxable income and incomed taxed at ordinary rates?arrow_forwardMarc and Mikkel are married and file a joint tax return. Marc and Mikkel earned salaries this year of $64,200 and $13,200, respectively. In addition to their salaries, they received interest of $354 from municipal bonds and $600 from corporate bonds. Marc contributed $2,600 to a traditional individual retirement account, and Marc paid alimony to a prior spouse in the amount of $1,600 (under a divorce decree effective June 1, 2017). Marc and Mikkel have a 10-year-old adopted son, Mason, who lived with them throughout the entire year. Thus, Marc and Mikkel are allowed to claim a $2,000 child tax credit for Mason. Marc and Mikkel paid $6,200 of expenditures that qualify as itemized deductions, and they had a total of $2,596 in federal income taxes withheld from their paychecks during the year.What is the total amount of Marc and Mikkel's deductions from AGI?arrow_forwardPlease give me true answer this financial accounting questionarrow_forward
- Can you please give me correct solution this general accounting question?arrow_forwardMichael McDowell Co. establishes a $108 million liability at the end of 2025 for the estimated site-cleanup costs at two of its manufacturing facilities. All related closing costs will be paid and deducted on the tax return in 2026. Also, at the end of 2025, the company has $54 million of temporary differences due to excess depreciation for tax purposes, $7.56 million of which will reverse in 2026. The enacted tax rate for all years is 20%, and the company pays taxes of $34.56 million on $172.80 million of taxable income in 2025. McDowell expects to have taxable income in 2026. Assuming that the only deferred tax account at the beginning of 2025 was a deferred tax liability of $5,400,000, draft the income tax expense portion of the income statement for 2025, beginning with the line "Income before income taxes." (Hint: You must first compute (1) the amount of temporary difference underlying the beginning $5,400,000 deferred tax liability, then (2) the amount of temporary differences…arrow_forwardHi experts please answer the financial accounting questionarrow_forward
- Managerial AccountingAccountingISBN:9781337912020Author:Carl Warren, Ph.d. Cma William B. TaylerPublisher:South-Western College PubFinancial And Managerial AccountingAccountingISBN:9781337902663Author:WARREN, Carl S.Publisher:Cengage Learning,Principles of Cost AccountingAccountingISBN:9781305087408Author:Edward J. Vanderbeck, Maria R. MitchellPublisher:Cengage Learning
- Cornerstones of Cost Management (Cornerstones Ser...AccountingISBN:9781305970663Author:Don R. Hansen, Maryanne M. MowenPublisher:Cengage LearningPrinciples of Accounting Volume 2AccountingISBN:9781947172609Author:OpenStaxPublisher:OpenStax College
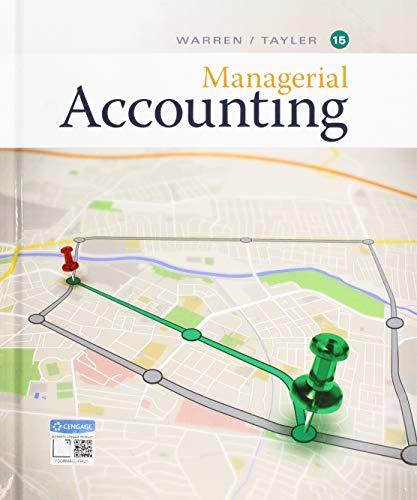
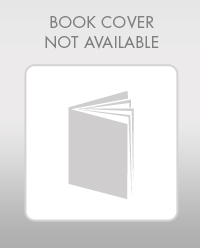
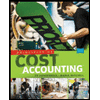
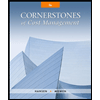