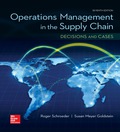
OPERATIONS MANAGEMENT IN THE SUPPLY CHAIN: DECISIONS & CASES (Mcgraw-hill Series Operations and Decision Sciences)
7th Edition
ISBN: 9781259326738
Author: SCHROEDER
Publisher: MCG
expand_more
expand_more
format_list_bulleted
Concept explainers
Textbook Question
Chapter 14, Problem 8P
An electronics retailer carries a particular cellular telephone with the following characteristics:
Average monthly sales = 120 units
Ordering cost = S25 per order
Carrying cost = 35 percent per year
Item cost = S300 per unit
Lead time = 4 days
Standard deviation of daily demand = .2 unit
Working days per year = 250
- a. Determine the EOQ.
- b. Calculate the reorder point for a 92 percent service level, assuming
normally distributed demand. - c. Design a Q system for this item.
- d. What happens to the reorder point when the lead time changes? What happens to the reorder point when the standard deviation of demand changes?
Expert Solution & Answer

Trending nowThis is a popular solution!

Students have asked these similar questions
The Clothing Shack is an online retailer of men's, women's, and children's clothing. The company has
been in business for four years and makes a modest profit from its online sales. However, in an effort
to compete successfully against online retailing heavyweights, the Clothing Shack's marketing
director, Makaya O'Neil, has determined that the Clothing Shack's marketing information systems
need improvement.
Ms. O'Neil feels that the Clothing Shack should begin sending out catalogs to its customers, keep
better track of its customer's buying habits, perform target marketing, and provide a more
personalized shopping experience for its customers. Several months ago, Ms. O'Neil submitted a
systems service request (SSR) to the Clothing Shack's steering committee. The committee
unanimously approved this project. You were assigned to the project at that time and have since
helped your project team successfully complete the project initiation and planning phase. Your team
is now ready to move…
b-1.
Activity
ES
EF
LS
LF
Slack
1
2
3
4
5
6
7
8
9
b-2. Identify the critical activities, and determine the duration of the project.
The critical activities are .
The forecast for each week of a four-week schedule is 50 units. The MPS rule is to schedule production if the projected on-hand
Inventory would be negative without it. Customer orders (committed) are follows:
Week
Customer Order
1
52
35
20
12
Use a production lot size of 75 units and no beginning Inventory. Determine the available-to-promise (ATP) quantities for each period.
Note: Leave no cells blank - be certain to enter "0" wherever required.
Period
ATP
1
2
3
Chapter 14 Solutions
OPERATIONS MANAGEMENT IN THE SUPPLY CHAIN: DECISIONS & CASES (Mcgraw-hill Series Operations and Decision Sciences)
Ch. 14.S - eXcel Suppose that for problem 1 in the chapter,...Ch. 14.S - Prob. 2PCh. 14.S - For problem 2 in the chapter, suppose the Grinell...Ch. 14.S - A producer of electronic parts wants to take...Ch. 14 - Identify the different types of inventories (raw...Ch. 14 - Why are stockout costs difficult to determine?...Ch. 14 - What is the difference between a requirements...Ch. 14 - Compare and contrast the management of finished...Ch. 14 - For a given service level, why does a P system...Ch. 14 - Under what circumstances might CPFR be useful, and...
Ch. 14 - Prob. 7DQCh. 14 - What is the appropriate role of inventory turnover...Ch. 14 - Suppose you are managing a chain of retail...Ch. 14 - The Always Fresh Grocery Store carries a...Ch. 14 - The Grinell Machine Shop makes a line of metal...Ch. 14 - The local Toyota dealer has to decide how many...Ch. 14 - Prob. 4PCh. 14 - The famous Widget Company sells widgets at the...Ch. 14 - Prob. 6PCh. 14 - Prob. 7PCh. 14 - An electronics retailer carries a particular...Ch. 14 - An electronics retailer carries a particular...Ch. 14 - The local Toyota dealer has to decide how many...Ch. 14 - The Suregrip Tire Company carries a certain type...Ch. 14 - The Suregrip Tire Company carries a certain type...Ch. 14 - eXcel 13. The Cover-up Drapery Company carries...Ch. 14 - Suppose you are the supplier of the Cover-up...
Knowledge Booster
Learn more about
Need a deep-dive on the concept behind this application? Look no further. Learn more about this topic, operations-management and related others by exploring similar questions and additional content below.Similar questions
- Prepare a master schedule given this information: The forecast for each week of an eight-week schedule is 60 units. The MPS rule is to schedule production if the projected on-hand Inventory would be negative without it. Customer orders (committed) are as follows: Week Customer Orders 1 2 36 28 4 1 Use a production lot size of 85 units and no beginning inventory. Note: In the ATP row, enter a value of 0 (zero) in any periods where ATP should not be calculated. Leave no cells blank - be certain to enter "0" wherever required. June July 1 2 3 4 5 8 7 8 Forecast 60 60 60 60 60 60 60 60 Customer Orders 38 28 4 1 0 0 0 0 Projected On-Hand Inventory MPS ATParrow_forwardSales of tablet computers at Marika Gonzalez's electronics store in Washington, D.C., over the past 10 weeks are shown in the table below: Week 1 2 3 4 5 6 7 8 9 10 Demand 21 21 27 38 25 30 35 24 25 30 a) The forecast for weeks 2 through 10 using exponential smoothing with a = 0.50 and a week 1 initial forecast of 21.0 are (round your responses to two decimal places): Week 1 2 3 4 5 6 7 8 9 10 Demand 21 21 27 38 25 30 35 24 25 30 Forecast 21.0 21 21 24 31 28 29 32 28 26.50 b) For the forecast developed using exponential smoothing (a = 0.50 and initial forecast 21.0), the MAD = |||||sales (round your response to two decimal places).arrow_forwardSales of tablet computers at Marika Gonzalez's electronics store in Washington, D.C., over the past 10 weeks are shown in the table below: Week Demand 1 2 3 4 5 6 7 8 9 10 21 21 27 38 25 30 35 24 25 30 a) The forecast for weeks 2 through 10 using exponential smoothing with a = 0.50 and a week 1 initial forecast of 21.0 are (round your responses to two decimal places): Week 1 2 3 4 5 Demand 21 21 27 38 Forecast 21.0 ☐ G ☐ ☐ 6 7 25 30 35 ∞ ☐ 8 9 10 24 25 30arrow_forward
- Each machine costs $3 Million. Building the room with all its attendant safety protection and other ancillary costs increases the spending by an additional $2.0 million dollars per MRI suite. Each machine can perform 2000 scans per year. Each reading of an MRI scan by a radiologist, along with other per-scan-related costs, is $500 per scan. The machine will last five years. Don’t worry about discount rates for this problem Graph the total costs over 5 years as a function of sales for 0-3000 patients annually. Hint: you may need to add a second MRI at some point. Suppose that you want to make a profit of $500 per scan at a target volume of 1000 patients per year, and you purchase only one machine. Superimpose the total revenue curve on top of the total cost curve in (1).arrow_forwardI need the answer to requirement C.arrow_forwardImagine you are Susan Kim and are faced with a difficult choice to either follow the orders she was given, or refusing to do so. Using each lens determine what the ethical response would be. Suppot your answer with materials from readings and lectures. For example, using Universalism what would the ethical response be? Do the same for all four lenses.arrow_forward
- Answer all these questions, selecting any company of your choice. Choose a specific type of food company. Select a specific product. Develop all the inputs that are part of the process. Develop the transformation process in a graphic (diagram, etc.). Develop all the outputs or finished products that are part of the process. Describe all the processes involved in one line of production in any manufacturing facility. Also describing how good management is the center of any part of a production company.arrow_forwardUsing exponential smoothing with α =0.2, forecast the demand for The initial forecast for January is 2000 tons. Calculate the capacity utilization for June, July and Discuss the implications of underutilized or over utilized capacity for Green Harvestarrow_forwardIn organizational development when results are improving but relationships are declining, what leadership style is appropriate? directing delegating supporting coachingarrow_forward
- What is the first thing a leader should do when moving through a cultural change? conduct an assessment comparing the practices to other high-performing organizations learn about the current organizational culture continue to monitor key metrics define expectationsarrow_forwardThe third change leadership strategy, Collaborate on Implementation, is designed to address what type of concerns? impact concerns personal concerns refinement concerns collaboration concernsarrow_forwardIf team members are concerned with specifics such as their tasks, contingency plans, resources, and timeline, what concerns do they have? implementation concerns impact concerns refinement concerns personal concernsarrow_forward
arrow_back_ios
SEE MORE QUESTIONS
arrow_forward_ios
Recommended textbooks for you
- Purchasing and Supply Chain ManagementOperations ManagementISBN:9781285869681Author:Robert M. Monczka, Robert B. Handfield, Larry C. Giunipero, James L. PattersonPublisher:Cengage LearningMarketingMarketingISBN:9780357033791Author:Pride, William MPublisher:South Western Educational Publishing
- Contemporary MarketingMarketingISBN:9780357033777Author:Louis E. Boone, David L. KurtzPublisher:Cengage LearningPractical Management ScienceOperations ManagementISBN:9781337406659Author:WINSTON, Wayne L.Publisher:Cengage,Foundations of Business (MindTap Course List)MarketingISBN:9781337386920Author:William M. Pride, Robert J. Hughes, Jack R. KapoorPublisher:Cengage Learning
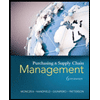
Purchasing and Supply Chain Management
Operations Management
ISBN:9781285869681
Author:Robert M. Monczka, Robert B. Handfield, Larry C. Giunipero, James L. Patterson
Publisher:Cengage Learning
Marketing
Marketing
ISBN:9780357033791
Author:Pride, William M
Publisher:South Western Educational Publishing
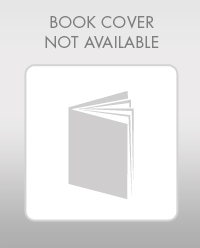
Contemporary Marketing
Marketing
ISBN:9780357033777
Author:Louis E. Boone, David L. Kurtz
Publisher:Cengage Learning
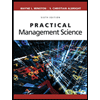
Practical Management Science
Operations Management
ISBN:9781337406659
Author:WINSTON, Wayne L.
Publisher:Cengage,
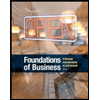
Foundations of Business (MindTap Course List)
Marketing
ISBN:9781337386920
Author:William M. Pride, Robert J. Hughes, Jack R. Kapoor
Publisher:Cengage Learning
Inventory Management | Concepts, Examples and Solved Problems; Author: Dr. Bharatendra Rai;https://www.youtube.com/watch?v=2n9NLZTIlz8;License: Standard YouTube License, CC-BY