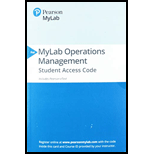
Concept explainers
a)
To evaluate: Plan C for the given information
Introduction: The aggregate plan is the output of sales and operations planning. The major concern of aggregate planning is the production time and quantity for the intermediate future. Aggregate planning would encompass a time prospect of approximately 3 to 18 months.
a)

Answer to Problem 10P
The Plan C has been evaluated. The total cost of Plan C is $104,000.
Explanation of Solution
Given information:
Production for all the months is 1,300 units. Ending inventory in June is 300 units. Overtime cost is $50 per unit. Demand requirement from July to December is given as follows:
Period | Demand | Production (units) |
June | ||
July | 1,000 | 1,300 |
August | 1,200 | 1,300 |
September | 1,400 | 1,300 |
October | 1,800 | 1,300 |
November | 1,800 | 1,300 |
December | 1,800 | 1,300 |
Evaluate the cost of the plan:
Plan C | |||||
Period | Demand | Production (units) | Subcontract (units) | Ending inventory | Extra cost |
June | 300 | ||||
July | 1,000 | 1,300 | 600 | $15,000 | |
August | 1,200 | 1,300 | 700 | $17,500 | |
September | 1,400 | 1,300 | 600 | $15,000 | |
October | 1,800 | 1,300 | 100 | $2,500 | |
November | 1,800 | 1,300 | 400 | 0 | $24,000 |
December | 1,800 | 1,300 | 500 | 0 | $30,000 |
Total | $104,000 |
Note: Production is given as 1,300 units. Ending inventory for June is given as 300 units. If the production is more than or equal to the demand, then there would be inventory. If the demand is more, then there would be stock out.
Calculate ending inventory or subcontract for July:
It is calculated by adding the production and ending inventory of previous month and subtract the result from the demand. Ending inventory for July is 600.
Calculate ending inventory or subcontract for August:
It is calculated by adding the production and ending inventory of previous month and subtract the result from the demand. Ending inventory for August is 700.
Calculate ending inventory or subcontract for September:
It is calculated by adding the production and ending inventory of previous month and subtract the result from the demand. Ending inventory for September is 600.
Even though the demand is high, as there is enough ending inventory in previous month, there would be inventory rather than subcontract.
Calculate the ending inventory or subcontract for October:
It is calculated by adding the production and ending inventory of previous month and subtract the result from the demand. Ending inventory for October is 100.
Even though the demand is high, as there is enough ending inventory in previous month, there would be inventory rather than subcontract.
Calculate ending inventory or subcontract for November:
As the demand is more than the production and there is no enough ending inventory, there would be subcontract.
It is calculated by adding production and ending inventory and the result should be subtracted with the demand. Hence, the subcontract units for November is 400 units.
As the value is in negative, it would be subcontract.
Calculate ending inventory or subcontract for December:
As the demand is more than the production and there is no enough ending inventory, there would be subcontract.
It is calculated by adding production and ending inventory and the result should be subtracted with the demand. Hence, the subcontract units for December is 500 units.
As the value is in negative, it would be subcontract.
Calculate extra cost for July:
It is calculated by multiplying ending inventory units and inventory holding cost. Inventory holding cost is given as $25 per unit. Hence, extra cost for July is $15,000
Calculate extra cost for August:
It is calculated by multiplying ending inventory units and inventory holding cost. Inventory holding cost is given as $25 per unit. Hence, extra cost for August is $17,500
Calculate extra cost for September:
It is calculated by multiplying ending inventory units and inventory holding cost. Inventory holding cost is given as $25 per unit. Hence, extra cost for September is $15,000
Calculate extra cost for October:
It is calculated by multiplying ending inventory units and inventory holding cost. Inventory holding cost is given as $25 per unit. Hence, extra cost for October is $2,500
Calculate extra cost for November:
It is calculated by multiplying ending inventory units and inventory holding cost. Inventory holding cost is given as $60 per unit. Hence, extra cost for November is $24,000
Calculate extra cost for December:
It is calculated by multiplying ending inventory units and inventory holding cost. Inventory holding cost is given as $60 per unit. Hence, extra cost for December is $30,000
Calculate total cost of Plan C:
It is calculated by adding the extra costs of all the periods.
Hence, the total cost for Plan C is $104,000.
b)
To determine: Evaluate plan D for the given information
Introduction: The aggregate plan is the output of sales and operations planning. The major concern of aggregate planning is the production time and quantity for the intermediate future. Aggregate planning would encompass a time prospect of approximately 3 to 18 months.
b)

Answer to Problem 10P
The Plan D has been evaluated. The total cost of Plan D is $93,800.
Explanation of Solution
Given information:
Production for all the months is 1,300 units. Ending inventory in June is 300 units. Overtime cost is $50 per unit. Demand requirement from July to December is given as follows:
Period | Demand | Production (units) |
June | ||
July | 1,000 | 1,300 |
August | 1,200 | 1,300 |
September | 1,400 | 1,300 |
October | 1,800 | 1,300 |
November | 1,800 | 1,300 |
December | 1,800 | 1,300 |
Evaluate the cost of the plan:
Plan D | |||||||
Period | Demand | Regular production (units) | Overtime production (units) | Ending inventory | Sub-contract (units) | Idle time (units) | Extra cost |
June | |||||||
July | 1,000 | 1,300 | 180 | 120 | $11,700 | ||
August | 1,200 | 1,300 | 180 | 100 | $10,500 | ||
September | 1,400 | 1,300 | 80 | $2,000 | |||
October | 1,800 | 1,300 | 260 | 0 | 160 | $20,000 | |
November | 1,800 | 1,300 | 260 | 0 | 240 | $24,800 | |
December | 1,800 | 1,300 | 260 | 0 | 240 | $24,800 | |
Total | $93,800 |
Note: Production is given as 1,300 units. If the production is more than or equal to the demand, then there would be inventory. If the demand is more, then there would be stock out. Maximum overtime units allowed is 260 units (20% of production)
Calculate ending inventory or subcontract for July:
It is calculated by adding the production and ending inventory of previous month and subtract the result from the demand. Ending inventory for July is 180.
It is given that the ending inventory should not exceed 180 units. Hence, the ending inventory would be 180 units and remaining units of 300 (120 units) would be in idle time.
Calculate ending inventory or subcontract for August:
It is calculated by adding the production and ending inventory of previous month and subtract the result from the demand. Ending inventory for August is 180.
It is given that the ending inventory should not exceed 180 units. Hence, the ending inventory would be 180 units and remaining units of 280 (100 units) would be in idle time.
Calculate ending inventory or subcontract for September:
It is calculated by adding the production and ending inventory of previous month and subtract the result from the demand. Ending inventory for September is 80.
Calculate the ending inventory or subcontract for October:
It is calculated by adding the production and ending inventory of previous month and subtract the result from the demand. Subcontract for October is 160.
As the value is in negative, it would be subcontract. Overtime production should not exceed 260 units. Hence, 260 units would be production in overtime production and 160 units (remaining from 420) would be produced in subcontract.
Calculate the ending inventory or subcontract for November:
It is calculated by adding the production and ending inventory of previous month and subtract the result from the demand. Subcontract for November is 240.
As the value is in negative, it would be subcontract. Overtime production should not exceed 260 units. Hence, 260 units would be production in overtime production and 240 units (remaining from 500) would be produced in subcontract.
Calculate the ending inventory or subcontract for December:
It is calculated by adding the production and ending inventory of previous month and subtract the result from the demand. Subcontract for December is 240.
As the value is in negative, it would be subcontract. Overtime production should not exceed 260 units. Hence, 260 units would be production in overtime production and 240 units (remaining from 500) would be produced in subcontract.
Calculate extra cost for July:
It is calculated by adding the multiple of ending inventory units and inventory holding cost and the multiple of idle time and idle time cost. Inventory holding cost is given as $25 per unit and idle time per unit is $60. Hence, extra cost for July is $11,700.
Calculate extra cost for August:
It is calculated by adding the multiple of ending inventory units and inventory holding cost and the multiple of idle time and idle time cost. Inventory holding cost is given as $25 per unit and idle time per unit is $60. Hence, extra cost for August is $10,500.
Calculate extra cost for September:
It is calculated by adding the multiple of ending inventory units and inventory holding cost and the multiple of idle time and idle time cost. Inventory holding cost is given as $25 per unit and idle time per unit is $60. Hence, extra cost for September is $2,000.
Calculate extra cost for October:
It is calculated by adding the multiple of overtime units and overtime cost per unit and subcontract units and subcontract cost per unit. Overtime cost per unit is $40 per unit and subcontract cost is $60 per unit. Hence, extra cost for October is $20,000.
Calculate extra cost for November:
It is calculated by adding the multiple of overtime units and overtime cost per unit and subcontract units and subcontract cost per unit. Overtime cost per unit is $40 per unit and subcontract cost is $60 per unit. Hence, extra cost for November is $24,800.
Calculate extra cost for December:
It is calculated by adding the multiple of overtime units and overtime cost per unit and subcontract units and subcontract cost per unit. Overtime cost per unit is $40 per unit and subcontract cost is $60 per unit. Hence, extra cost for December is $24,800.
Calculate total cost of Plan D:
It is calculated by adding the extra costs of all the periods.
Hence, the total cost for Plan D is $93,800.
Total cost for Plan D is preferable when compare with Plan C. However, Plan D with the total cost of $93,800 is preferable than other plans.
Want to see more full solutions like this?
Chapter 13 Solutions
EBK PRINCIPLES OF OPERATIONS MANAGEMENT
- Do you feel there is anything positive about rework?arrow_forwardDo you think technology can achieve faster setup times? How would it be implemented in the hospital workforce?arrow_forwardIn your experience or opinion, do you think process changes like organizing workspaces make a bigger difference, or is investing in technology usually the better solution for faster setups?arrow_forward
- Have you seen rework done in your business, and what was done to prevent that from occurring again?arrow_forwardResearch a company different than case studies examined and search the internet and find an example of a business that had to rework a process. How was the organization affected to rework a process in order to restore a good flow unit? Did rework hurt a process or improve the organization's operational efficiency? • Note: Include a reference with supportive citations in the discussion reply in your post.arrow_forwardSetup time is very important in affecting a process and the capacity of a process. How do you reduce setup time? Give examples of reducing setup time. Please Provide a referenecearrow_forward
- Do you think TPS was successful? If so, how? Are there other companies that have used TPS? If so, give examples. Please provide a referencearrow_forwardGiven the significant impact on finances, production timelines, and even equipment functionality, as you pointed out, what do you believe is the most effective single strategy a company can implement to significantly reduce the occurrence of rework within their operations?arrow_forwardDurban woman, Nombulelo Mkumla, took to social media last week to share how she discovered the rodent.In a lengthy Facebook post, she said she purchased the loaf of bread from a local shop after work on August 27.For the next days, Mkumla proceeded to use slices of bread from the load to make toast."Then, on the morning of August 31, I took the bread out of the fridge to make toast and noticed something disgusting andscary. I took a picture and sent it to my friends, and one of them said, 'Yi mpuku leyo tshomi' [That's a rat friend]“."I was in denial and suggested it might be something else, but the rat scenario made sense - it's possible the rat got into thebread at the factory, and no one noticed," Mkumla said.She went back to the shop she'd bought the bread from and was told to lay a complaint directly with the supplier.She sent an email with a video and photographs of the bread.Mkumla said she was later contacted by a man from Sasko who apologised for the incident.According to…arrow_forward
- PepsiCo South Africa says the incident where a woman discovered part of a rodent in her loaf of bread, is anisolated occurrence.Durban woman, Nombulelo Mkumla, took to social media last week to share how she discovered the rodent.In a lengthy Facebook post, she said she purchased the loaf of bread from a local shop after work on August 27.For the next days, Mkumla proceeded to use slices of bread from the load to make toast."Then, on the morning of August 31, I took the bread out of the fridge to make toast and noticed something disgusting andscary. I took a picture and sent it to my friends, and one of them said, 'Yi mpuku leyo tshomi' [That's a rat friend]“."I was in denial and suggested it might be something else, but the rat scenario made sense - it's possible the rat got into thebread at the factory, and no one noticed," Mkumla said.She went back to the shop she'd bought the bread from and was told to lay a complaint directly with the supplier.She sent an email with a video and…arrow_forwardDurban woman, Nombulelo Mkumla, took to social media last week to share how she discovered the rodent.In a lengthy Facebook post, she said she purchased the loaf of bread from a local shop after work on August 27.For the next days, Mkumla proceeded to use slices of bread from the load to make toast."Then, on the morning of August 31, I took the bread out of the fridge to make toast and noticed something disgusting andscary. I took a picture and sent it to my friends, and one of them said, 'Yi mpuku leyo tshomi' [That's a rat friend]“."I was in denial and suggested it might be something else, but the rat scenario made sense - it's possible the rat got into thebread at the factory, and no one noticed," Mkumla said.She went back to the shop she'd bought the bread from and was told to lay a complaint directly with the supplier.She sent an email with a video and photographs of the bread.Mkumla said she was later contacted by a man from Sasko who apologised for the incident.According to…arrow_forwardRead the project statement and answer ALL of the questions that follow PROJECT STATEMENT The African Integrated High-Speed Railway Network (AIHSRN). African nations are preparing to invest billions in a significant overhaul of their rail infrastructure as part of an ambitious plan for the continent. One of the key projects underway is the African Integrated High-Speed Railway Network (AIHSRN), which aims to connect Africa's capital cities and major commercial centres with a high-speed railway network to enhance continental trade and competition. This network will span 2,000 km (1,243 miles) and connect 60 cities, including Nairobi, Lagos, Cairo, and Dakar. It will improve access to essential markets, enhance economic cooperation, and encourage regional collaboration. The plan is poised to revolutionise intra-African trade by reducing travel times and lowering transportation costs, making trade between African nations more competitive. The trains will be capable of reaching speeds of up…arrow_forward
- MarketingMarketingISBN:9780357033791Author:Pride, William MPublisher:South Western Educational PublishingPractical Management ScienceOperations ManagementISBN:9781337406659Author:WINSTON, Wayne L.Publisher:Cengage,Purchasing and Supply Chain ManagementOperations ManagementISBN:9781285869681Author:Robert M. Monczka, Robert B. Handfield, Larry C. Giunipero, James L. PattersonPublisher:Cengage Learning
- Foundations of Business (MindTap Course List)MarketingISBN:9781337386920Author:William M. Pride, Robert J. Hughes, Jack R. KapoorPublisher:Cengage Learning
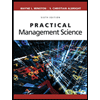
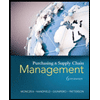
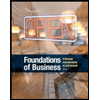